汽车轻量化材料、工艺、成本、水平、技术路线汇总
2018-07-02 13:00:37· 来源:汽车工艺师
乘用车白车身包括下部车身、上部车身骨架、车门、发动机罩盖、行李箱盖、翼子板等部件,是发动机、变速器、传动系统、制动系统、悬架系统、排气系统、电气系统及内饰件的安装基础,并通过其相应的结构设计满足成员的安全性要求。车身轻量化的目的在于保证车身结构抗撞性、刚度、强度以及NVH性能前提下,减轻身上骨架质量,同时不提高汽车车身制造成本来增强整车产品的市场竞争力。
乘用车白车身包括下部车身、上部车身骨架、车门、发动机罩盖、行李箱盖、翼子板等部件,是发动机、变速器、传动系统、制动系统、悬架系统、排气系统、电气系统及内饰件的安装基础,并通过其相应的结构设计满足成员的安全性要求。车身轻量化的目的在于保证车身结构抗撞性、刚度、强度以及NVH性能前提下,减轻身上骨架质量,同时不提高汽车车身制造成本来增强整车产品的市场竞争力。
轻质材料
车身上应用的不断扩大的高强、轻质材料主要为高强度钢与超高强度钢、铝合金、镁合金工程塑料以及符合材料等。
高强度钢
高强度钢主要应用于前防撞梁,A、B、C柱加强件,门槛梁,车门防撞梁和车顶横梁等关键部位,并且因公比例逐渐扩大。欧美部分车身车身高强度钢应用比例已超过60%,如奥迪A3、宝马3系、凯迪拉克ATS、福特蒙迪欧等;日系车型高强度钢占比也超过50%,如英菲尼迪Q50、本田思域等;
铝合金
铝合金已由发动机罩向翼子板、行李厢盖及车门上逐渐延伸,部分高端车已实现全部铝合金车身;
镁合金
镁合金已经从方向盘骨架、座椅骨架向转向支撑、传动系壳体零件上发展;
纤维增强复合材料
纤维增强复合材料已开始应用于前段模块、后尾门、进气歧管等零部件;碳纤维复合材料已由跑车、豪华车向中高端车和电动车应用扩展。如图某轿车带四门两盖的车身结构。
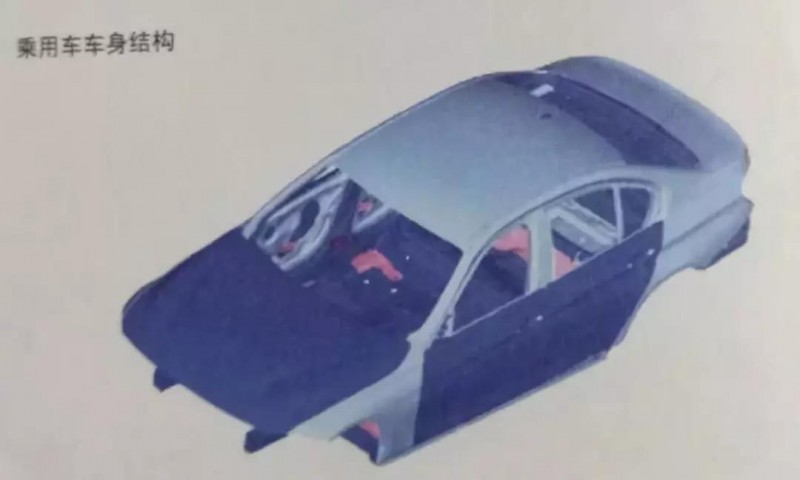
结构优化设计
在结构优化设计方面,车型开发前期,对车身结构做出更合理的设计规划更为重要。目前多材料车身结构轻量化设计正在向着搭建参数化设计平台(如图),应用拓扑优化、尺寸优化、形貌优化、多目标优化以及结构-材料-性能一体化优化设计方向发展。
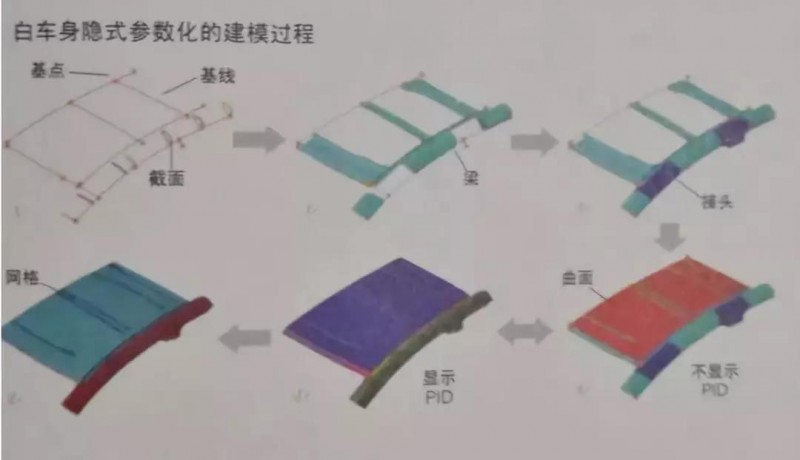
一、材料应用
1、高强度钢
高强度钢主要应用在车上内外板以及车上结构件,同时高强度钢可以有效提升车身被动安全性。先进刚度刚在汽车超轻钢车身、先进概念车上应用,在减重、节能、提高安全性、降低排放发面应用前景良好。虽然在成型中面临回弹等问题挑战,但相比于其他替代材料,高强度钢还是性价比最好、最具吸引力的材料。
2、铝合金
铝合金的应用始于20世纪90年代,以奥迪汽车推推出的全铝空间框架车身为代表。提出了奥迪全铝车身框架概念(ASF),推出相应车身Audi100、第一代Audi A8、A2.除奥迪其他公司也推出了全铝车身,如捷豹XJ、新路虎揽胜、奔驰S级车等如图所示。
变形铝合金在车身零件级结构件的应用方面发展比较快,如应用日益广发的铝合金行李箱盖、发动机舱罩盖、后背门、保险杠横梁等,随着凝固铝合金、粉末冶金铝合金、超塑性铝合金、铝基复合材料和泡沫铝材等新材料的开发应用,未来铝合金在汽车应用范围将进一步扩大,并将呈现铸件、型材、板材并举的局面,预计未来铝将成为仅次于钢的第二大汽车用材料。
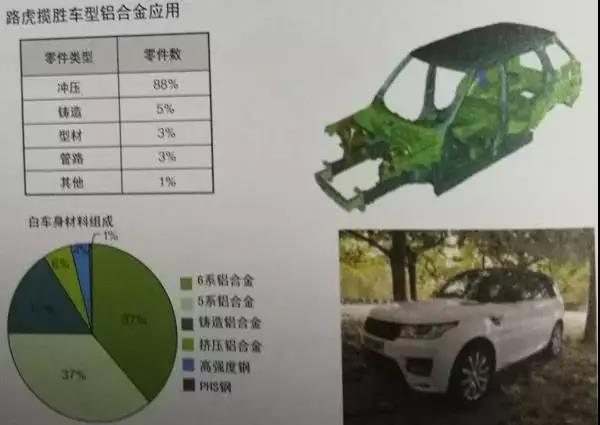
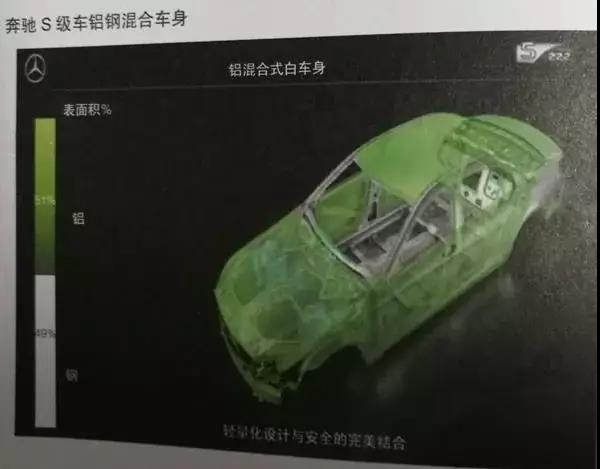
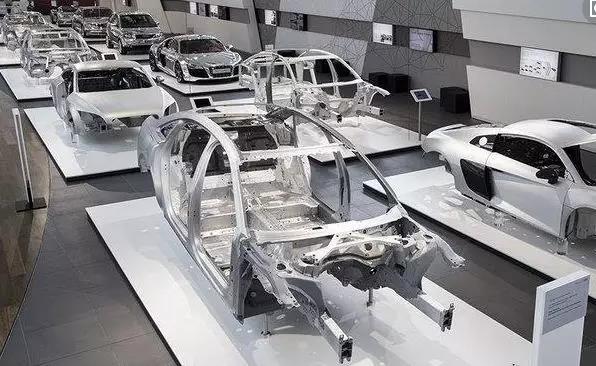
奥迪A8全铝车身
3、镁合金
目前镁合金在车身上主要集中在方向盘骨架。仪表盘骨架、座椅骨架等零部件上,在白车身结构件上还没有量产应用。目前仅有克莱斯勒某车型上做过尝试,如图。由于镁合金耐腐性和成型方面限制,目前尚未得到广泛应用。
4、复合材料
汽车工业复合材料技术首先应用于保险杠,而后用与生产变截面弹簧钢板以代替钢板,之后又用与生产四门两盖。复合材料大规模应用是在20世纪80年代中期以后。1990年福特、克莱斯勒相继开发出复合材料。
复合材料具有许多金属材料无法比拟的优点:密度低、比强高、比模高;材料性能具有可设计性;制品结构设计自由度大,易实现集成化、模块化设计;抗腐蚀性好、耐久性能好,隔声降噪;可采用多种成型工艺,模具成本低;A级表面,可免喷涂等工序;投资少,生产周期短。目前,汽车轻量化发展需求迫切,从成本性能发展综合考虑,可用于车身结构件的复合材料以树脂基碳纤维增强复合材料为首选。可以应用于发动机舱罩盖、翼子板、车顶、行李箱、门板、底盘灯结构件中。
随着车用复合材料技术的发展,现已广发的应用在跑车、豪华车上,于铝合金构件比,复合材料可以减重50%左右,目前车上碳纤维已从单向丝、双向编制物,发展到多轴中空的碳纤维预制体,可获得多种形状结构的汽车部件,如图宝马I3电动汽车复合材料应用。
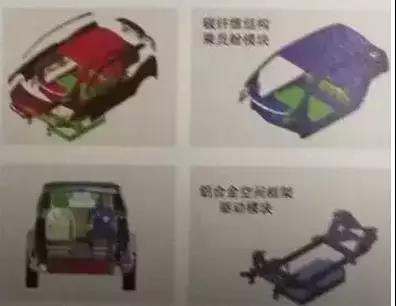
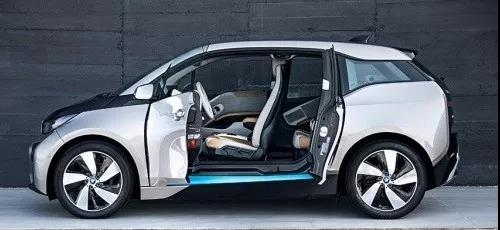
二、制造工艺
1、热成形
精度高、成形性能好,广泛应用于生产高强度汽车保险杠,车门防撞杆,A、B、C柱加强件,车顶框架,中通道等安全件和结构件。目前该技术在国外发展很快,美国通用、福特德国大众等在用该项技术制造高强度冲压件。中国一汽红旗H7车身下部也规模化使用热成形技术,如图:
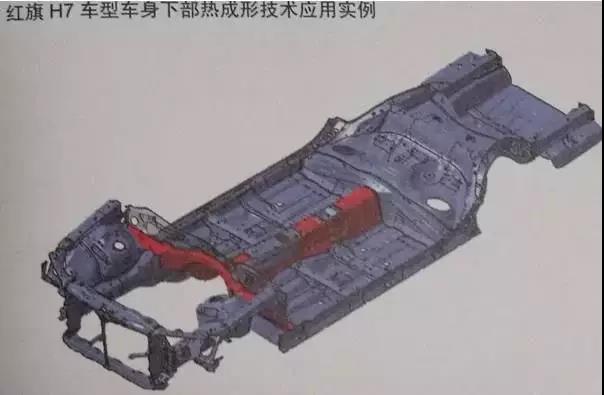
2、激光拼焊
1985年奥迪成功采用全球第一块激光拼焊板。20世纪90年代,欧美、日本各大汽车企业开始大规模使用激光拼焊技术。近年来该项技术在全球新型钢制车身设计和制造商应用广泛。如图中国一汽H7车身使用激光焊接的典型结构件。
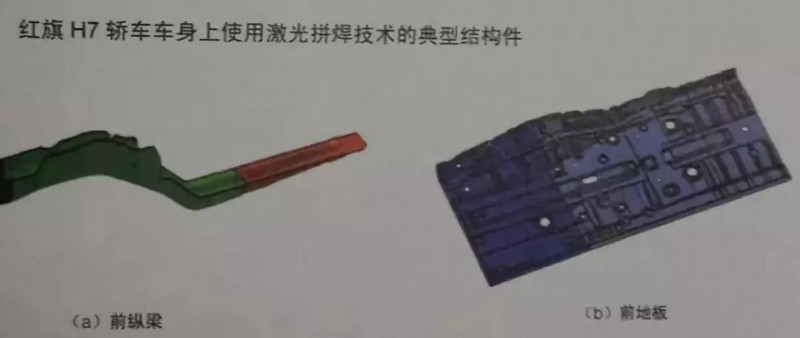
利用激光焊接技术可以减少汽车零部件数量、减轻车身重量、提高原材料利用率、提高结构功能、增加产品设计灵活性。
3、差厚板
差厚板是在激光焊接之后,为解决激光拼焊板存在的问题而出现的,生产过程如图

差厚板可以代替激光拼焊板,从而更好的实现轻量化。但不完全代替激光拼焊板,因为激光拼焊除了焊接不同厚度板料还可以焊接不同材料、强度的板焊接在一起,差厚板不能实现这一功能。
三、成本估计
高强度钢与其他轻质材料比,价格低、经济性好,广泛的应用可提高车是安全性。高强度钢可以减薄材料,所以与普通钢板相比可以做大成本不大幅增加,约为普通钢板的1.5倍。
铝合金密度2.68g/cm³,仅为钢板的1/3。考虑到使用铝材需要增加厚度及截面,可以减重30%~50%,与钢板相比,一般铝板件成本将增加2-5倍。
碳纤维复合材料密度1.5 g/cm³,不及钢的1/5。碳纤维复合材料应用到车门、发动机舱罩盖、行李箱盖能够减重50%以上,其材料成本相对钢板增加5倍以上。
四、轻量化水平
国内汽车轻量化产业未形成规模,产业链不够完整,与国外差距较大。国际主流车型高强度钢车身占比60%以上,强度级别780MPa、980MPa的钢在车身构件上已相当普遍。高强度钢可以在不降低安全性与舒适性前提下,零件减重20~30%。
国外或者国内合资高端车型部分零部件应用轻质材料,工程塑料零部件相对钢制部件可以减重30%~35%,铝合金零部件相对钢制零部件也减重30%~50%,镁合金零部件相对钢制零部件可以减重40%~55%,碳纤维复合材料零部件相对钢制零部件可减重40%~60%。
五、车身轻量化技术路径
国外车身轻量化路径如下图所示:
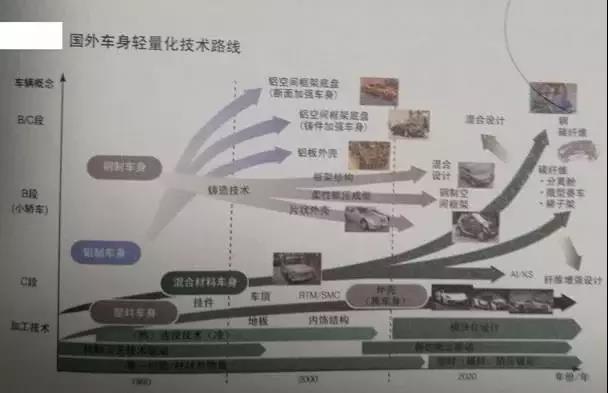
借鉴国外技术可以探索我国车身轻量化技术发展路线
1、 短期
目标:加大刚强度钢和超高强度钢应用比例,合理减薄钢板厚度,广泛应用先进成形技术和链接技术,达到预计的轻量化目标。
途径:采用高强度钢、超高强度钢、工程塑料,适量应用镁铝合金及复合材料,进行车身结构参数优化设计,欧皇钢板厚度断面形状、尺寸,广泛应用激光焊接、热成形工艺及先进连接技术。
2、 中期
目标:掌握铝镁合金、复合材料特性及连接技术,结构-材料-性能一体化轻量化多目标协同优化设计方法,所需与国外技术水平差距。
路径:扩大铝镁合金、复合材料在车身上的应用比例、零部件数量,根据材料性能优化设计铝镁合金与纤维增强复合材料零部件结构,充分发挥材料本身性能优势。
3、 长期
目标:逐渐掌握碳纤维复合材料特性、零部件设计方法、高效制造工艺、性能控制方法和连接技术,逐渐赶超汽车工业发达国家汽车轻量化技术水平。
途径:熟练应用钢铝混合车身设计、制造与连接技术,逐渐掌握碳纤维复合材料零部件结构设计。高效制造、性能调控和连接技术,扩大碳纤维复合材料在汽车上的应用比例。
以下是我国汽车关键零部件制造技术路线图:
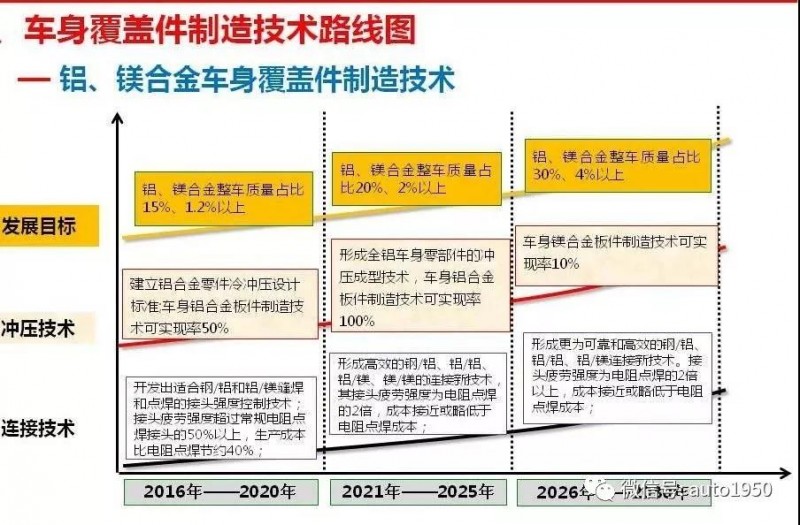
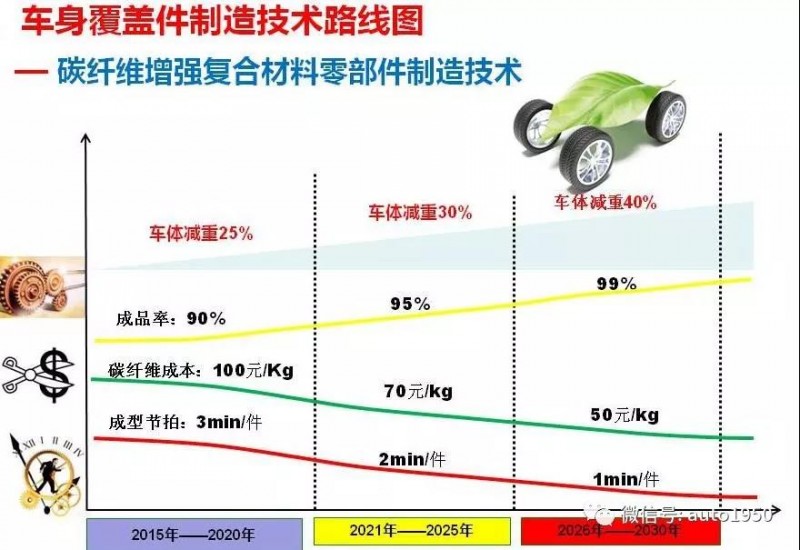
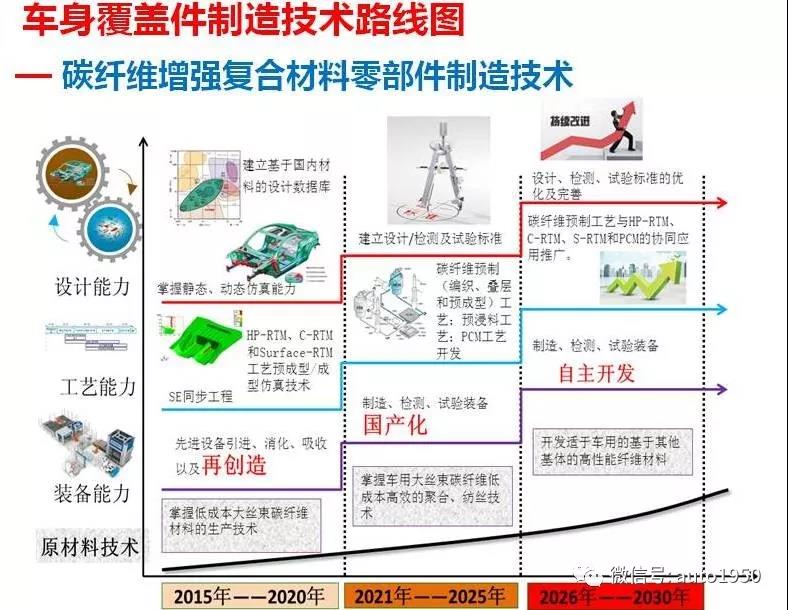
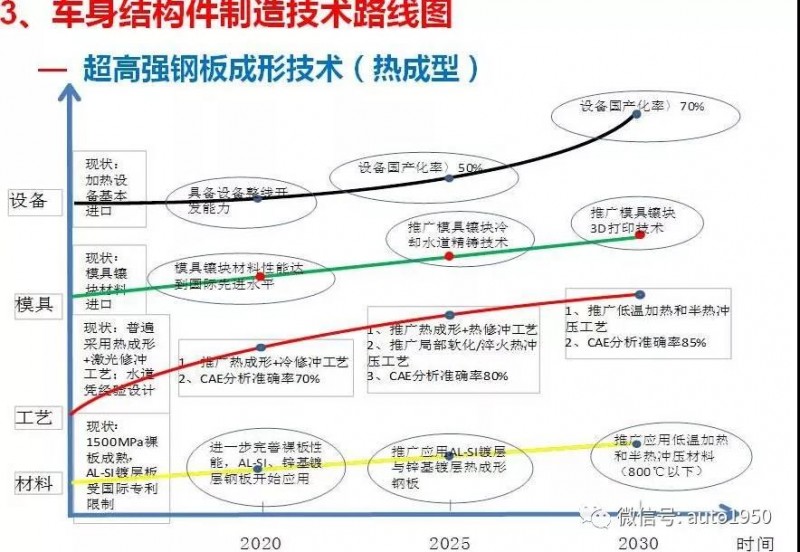
汽车工艺师整理、资料来源:快资讯、东风邹恒琪在第六届中国汽车先进技术与制造高峰论坛上的演讲
轻质材料
车身上应用的不断扩大的高强、轻质材料主要为高强度钢与超高强度钢、铝合金、镁合金工程塑料以及符合材料等。
高强度钢
高强度钢主要应用于前防撞梁,A、B、C柱加强件,门槛梁,车门防撞梁和车顶横梁等关键部位,并且因公比例逐渐扩大。欧美部分车身车身高强度钢应用比例已超过60%,如奥迪A3、宝马3系、凯迪拉克ATS、福特蒙迪欧等;日系车型高强度钢占比也超过50%,如英菲尼迪Q50、本田思域等;
铝合金
铝合金已由发动机罩向翼子板、行李厢盖及车门上逐渐延伸,部分高端车已实现全部铝合金车身;
镁合金
镁合金已经从方向盘骨架、座椅骨架向转向支撑、传动系壳体零件上发展;
纤维增强复合材料
纤维增强复合材料已开始应用于前段模块、后尾门、进气歧管等零部件;碳纤维复合材料已由跑车、豪华车向中高端车和电动车应用扩展。如图某轿车带四门两盖的车身结构。
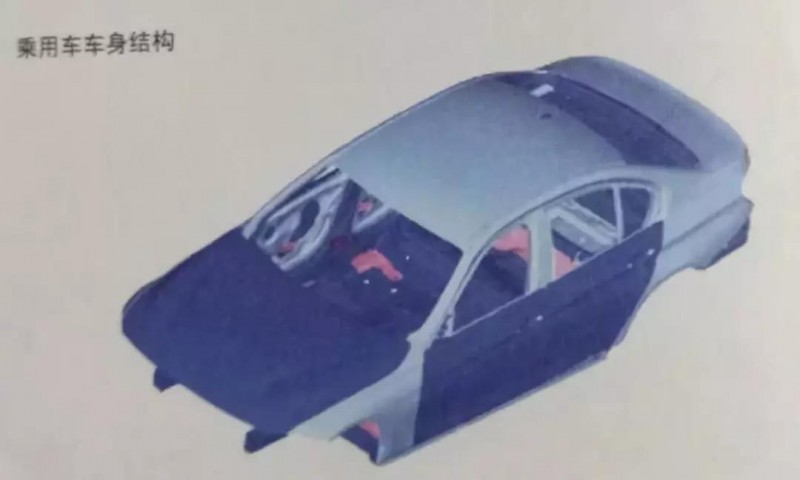
结构优化设计
在结构优化设计方面,车型开发前期,对车身结构做出更合理的设计规划更为重要。目前多材料车身结构轻量化设计正在向着搭建参数化设计平台(如图),应用拓扑优化、尺寸优化、形貌优化、多目标优化以及结构-材料-性能一体化优化设计方向发展。
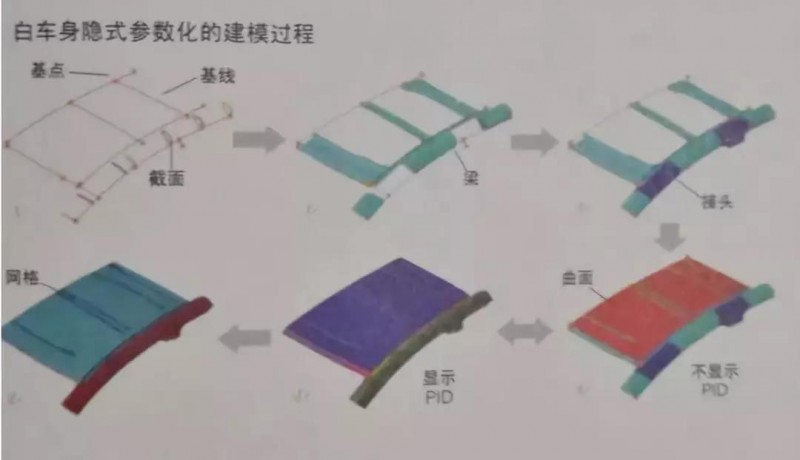
一、材料应用
1、高强度钢
高强度钢主要应用在车上内外板以及车上结构件,同时高强度钢可以有效提升车身被动安全性。先进刚度刚在汽车超轻钢车身、先进概念车上应用,在减重、节能、提高安全性、降低排放发面应用前景良好。虽然在成型中面临回弹等问题挑战,但相比于其他替代材料,高强度钢还是性价比最好、最具吸引力的材料。
2、铝合金
铝合金的应用始于20世纪90年代,以奥迪汽车推推出的全铝空间框架车身为代表。提出了奥迪全铝车身框架概念(ASF),推出相应车身Audi100、第一代Audi A8、A2.除奥迪其他公司也推出了全铝车身,如捷豹XJ、新路虎揽胜、奔驰S级车等如图所示。
变形铝合金在车身零件级结构件的应用方面发展比较快,如应用日益广发的铝合金行李箱盖、发动机舱罩盖、后背门、保险杠横梁等,随着凝固铝合金、粉末冶金铝合金、超塑性铝合金、铝基复合材料和泡沫铝材等新材料的开发应用,未来铝合金在汽车应用范围将进一步扩大,并将呈现铸件、型材、板材并举的局面,预计未来铝将成为仅次于钢的第二大汽车用材料。
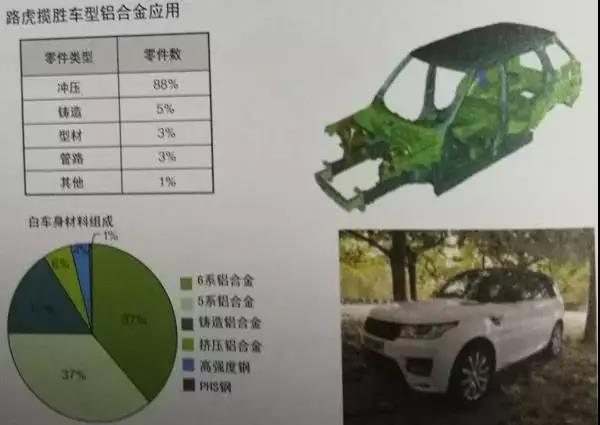
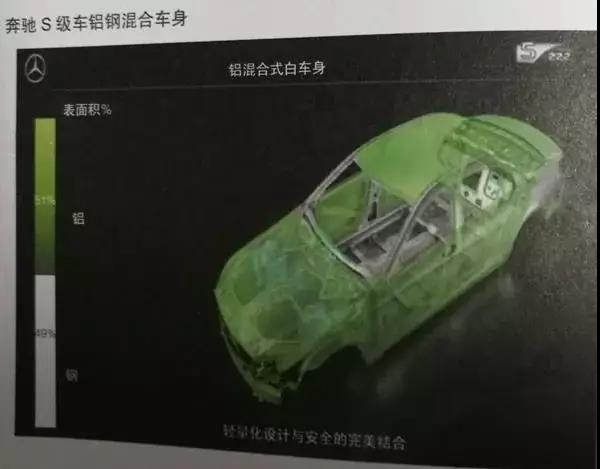
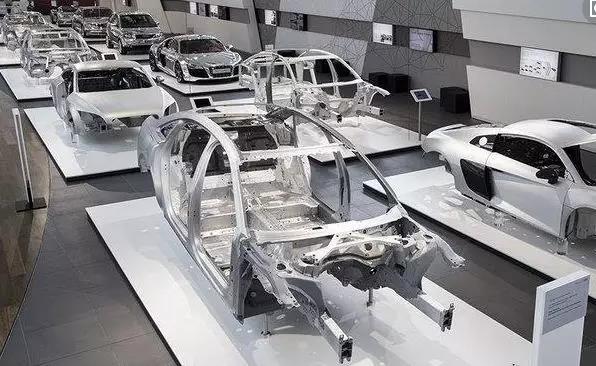
奥迪A8全铝车身
3、镁合金
目前镁合金在车身上主要集中在方向盘骨架。仪表盘骨架、座椅骨架等零部件上,在白车身结构件上还没有量产应用。目前仅有克莱斯勒某车型上做过尝试,如图。由于镁合金耐腐性和成型方面限制,目前尚未得到广泛应用。
4、复合材料
汽车工业复合材料技术首先应用于保险杠,而后用与生产变截面弹簧钢板以代替钢板,之后又用与生产四门两盖。复合材料大规模应用是在20世纪80年代中期以后。1990年福特、克莱斯勒相继开发出复合材料。
复合材料具有许多金属材料无法比拟的优点:密度低、比强高、比模高;材料性能具有可设计性;制品结构设计自由度大,易实现集成化、模块化设计;抗腐蚀性好、耐久性能好,隔声降噪;可采用多种成型工艺,模具成本低;A级表面,可免喷涂等工序;投资少,生产周期短。目前,汽车轻量化发展需求迫切,从成本性能发展综合考虑,可用于车身结构件的复合材料以树脂基碳纤维增强复合材料为首选。可以应用于发动机舱罩盖、翼子板、车顶、行李箱、门板、底盘灯结构件中。
随着车用复合材料技术的发展,现已广发的应用在跑车、豪华车上,于铝合金构件比,复合材料可以减重50%左右,目前车上碳纤维已从单向丝、双向编制物,发展到多轴中空的碳纤维预制体,可获得多种形状结构的汽车部件,如图宝马I3电动汽车复合材料应用。
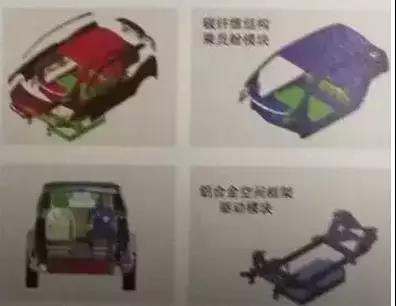
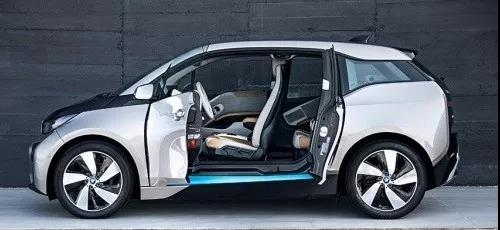
二、制造工艺
1、热成形
精度高、成形性能好,广泛应用于生产高强度汽车保险杠,车门防撞杆,A、B、C柱加强件,车顶框架,中通道等安全件和结构件。目前该技术在国外发展很快,美国通用、福特德国大众等在用该项技术制造高强度冲压件。中国一汽红旗H7车身下部也规模化使用热成形技术,如图:
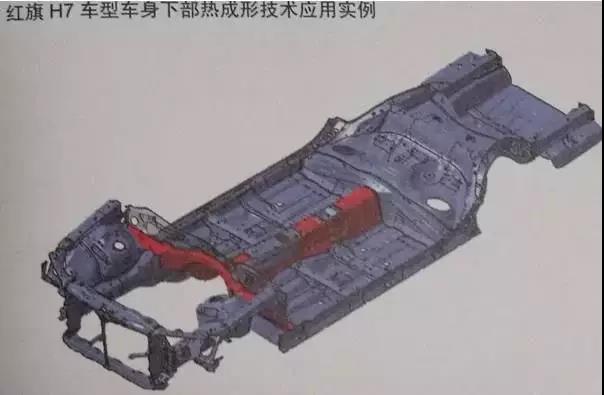
2、激光拼焊
1985年奥迪成功采用全球第一块激光拼焊板。20世纪90年代,欧美、日本各大汽车企业开始大规模使用激光拼焊技术。近年来该项技术在全球新型钢制车身设计和制造商应用广泛。如图中国一汽H7车身使用激光焊接的典型结构件。
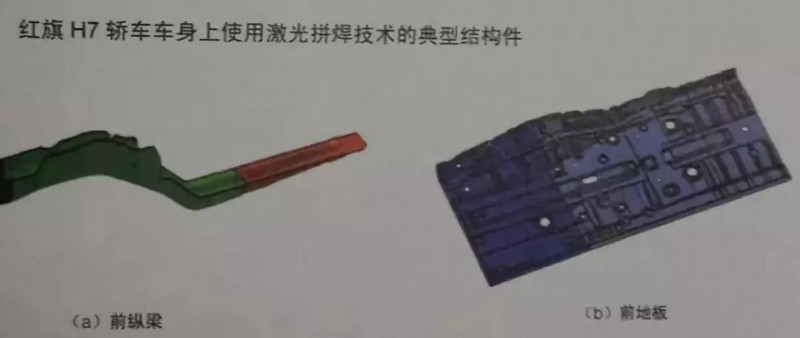
利用激光焊接技术可以减少汽车零部件数量、减轻车身重量、提高原材料利用率、提高结构功能、增加产品设计灵活性。
3、差厚板
差厚板是在激光焊接之后,为解决激光拼焊板存在的问题而出现的,生产过程如图

差厚板可以代替激光拼焊板,从而更好的实现轻量化。但不完全代替激光拼焊板,因为激光拼焊除了焊接不同厚度板料还可以焊接不同材料、强度的板焊接在一起,差厚板不能实现这一功能。
三、成本估计
高强度钢与其他轻质材料比,价格低、经济性好,广泛的应用可提高车是安全性。高强度钢可以减薄材料,所以与普通钢板相比可以做大成本不大幅增加,约为普通钢板的1.5倍。
铝合金密度2.68g/cm³,仅为钢板的1/3。考虑到使用铝材需要增加厚度及截面,可以减重30%~50%,与钢板相比,一般铝板件成本将增加2-5倍。
碳纤维复合材料密度1.5 g/cm³,不及钢的1/5。碳纤维复合材料应用到车门、发动机舱罩盖、行李箱盖能够减重50%以上,其材料成本相对钢板增加5倍以上。
四、轻量化水平
国内汽车轻量化产业未形成规模,产业链不够完整,与国外差距较大。国际主流车型高强度钢车身占比60%以上,强度级别780MPa、980MPa的钢在车身构件上已相当普遍。高强度钢可以在不降低安全性与舒适性前提下,零件减重20~30%。
国外或者国内合资高端车型部分零部件应用轻质材料,工程塑料零部件相对钢制部件可以减重30%~35%,铝合金零部件相对钢制零部件也减重30%~50%,镁合金零部件相对钢制零部件可以减重40%~55%,碳纤维复合材料零部件相对钢制零部件可减重40%~60%。
五、车身轻量化技术路径
国外车身轻量化路径如下图所示:
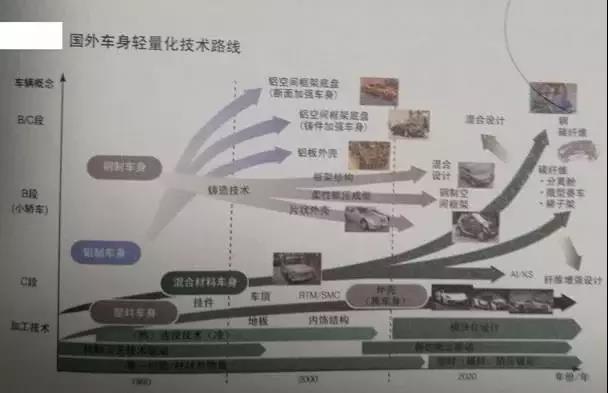
借鉴国外技术可以探索我国车身轻量化技术发展路线
1、 短期
目标:加大刚强度钢和超高强度钢应用比例,合理减薄钢板厚度,广泛应用先进成形技术和链接技术,达到预计的轻量化目标。
途径:采用高强度钢、超高强度钢、工程塑料,适量应用镁铝合金及复合材料,进行车身结构参数优化设计,欧皇钢板厚度断面形状、尺寸,广泛应用激光焊接、热成形工艺及先进连接技术。
2、 中期
目标:掌握铝镁合金、复合材料特性及连接技术,结构-材料-性能一体化轻量化多目标协同优化设计方法,所需与国外技术水平差距。
路径:扩大铝镁合金、复合材料在车身上的应用比例、零部件数量,根据材料性能优化设计铝镁合金与纤维增强复合材料零部件结构,充分发挥材料本身性能优势。
3、 长期
目标:逐渐掌握碳纤维复合材料特性、零部件设计方法、高效制造工艺、性能控制方法和连接技术,逐渐赶超汽车工业发达国家汽车轻量化技术水平。
途径:熟练应用钢铝混合车身设计、制造与连接技术,逐渐掌握碳纤维复合材料零部件结构设计。高效制造、性能调控和连接技术,扩大碳纤维复合材料在汽车上的应用比例。
以下是我国汽车关键零部件制造技术路线图:
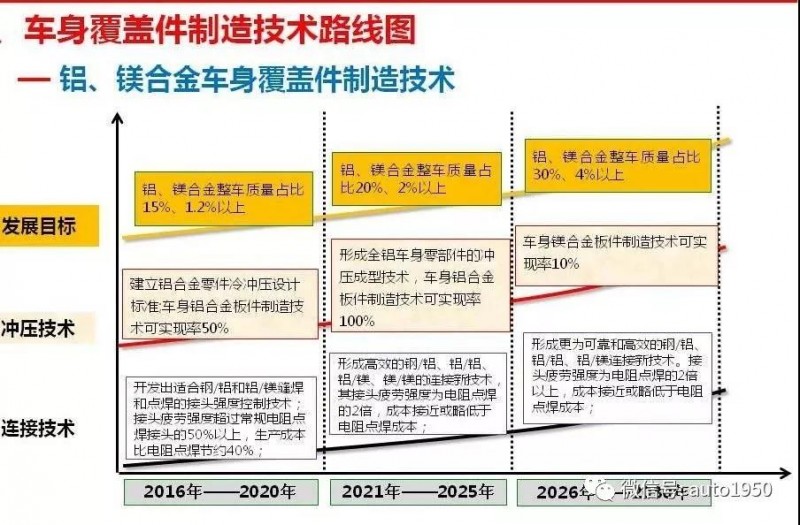
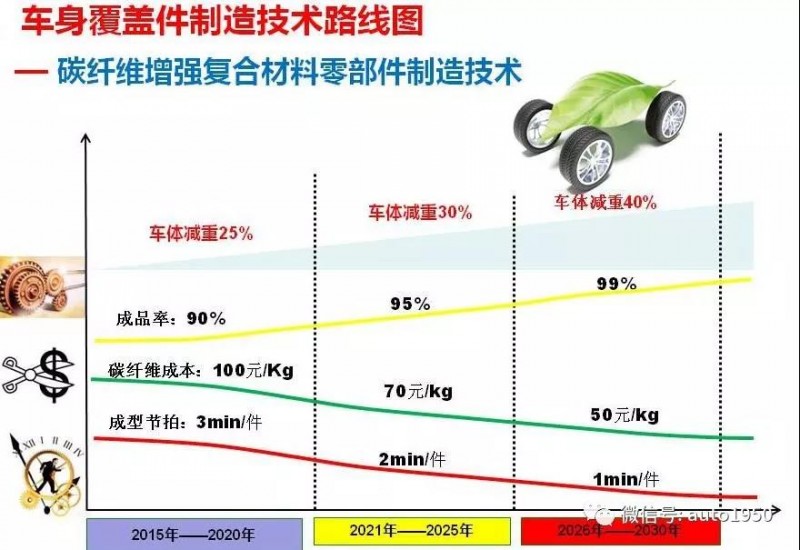
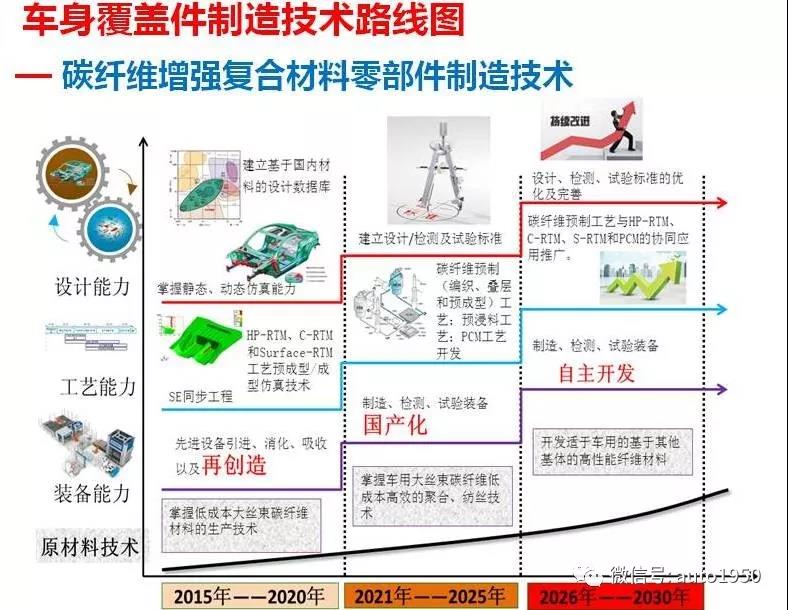
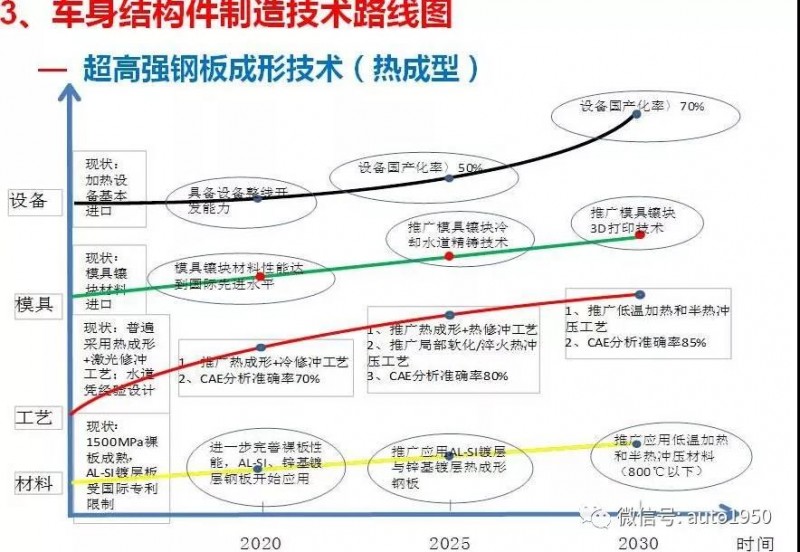
汽车工艺师整理、资料来源:快资讯、东风邹恒琪在第六届中国汽车先进技术与制造高峰论坛上的演讲
编辑推荐
最新资讯
-
全球产业链聚沪 共探双碳新路径 SNEC
2025-04-18 18:05
-
柯马签订具有约束力的协议收购 Autom
2025-04-17 13:01
-
高效协同新范式:比亚迪叉车领创智能
2025-04-17 10:04
-
埃马克德国总部迎来中国社科院工业经
2025-04-15 09:40
-
埃马克这项全新应用即将在CIMT惊艳首
2025-04-15 09:37