汽车涂装中应用高固工艺的优势分析
2018-07-19 14:00:16· 来源:汽车实用技术杂志社
汽车高固含技术并不是一个新名词,但真正具有稳定的施工高固含技术问世尚不足十年。经过实践验证,新的高固含技术在VOC排放上接近水性漆的水平,在碳排放和施工要求上又具备原来普通溶剂型涂料的优势,是节能环保涂料技术方面的新选择。为了适应部分原有生产线的环保改造需求,我们在福特3C1B高固含技术的基础上,陆续开发应用了一些新的高固含工艺技术,如3C2B色漆清漆高固含、3C2B色漆高固含等,并在研讨配套2K清漆和免中涂的高固含技术。本文重点从汽车高固含技术和水性漆的比较、汽车高固含工艺技术的最新发展、国家政策对高固
作者:盛宏志
单位:奇瑞捷豹路虎汽车公司
引言
汽车高固含技术并不是一个新名词,但真正具有稳定的施工高固含技术问世尚不足十年。经过实践验证,新的高固含技术在VOC排放上接近水性漆的水平,在碳排放和施工要求上又具备原来普通溶剂型涂料的优势,是节能环保涂料技术方面的新选择。为了适应部分原有生产线的环保改造需求,我们在福特3C1B高固含技术的基础上,陆续开发应用了一些新的高固含工艺技术,如3C2B色漆清漆高固含、3C2B色漆高固含等,并在研讨配套2K清漆和免中涂的高固含技术。本文重点从汽车高固含技术和水性漆的比较、汽车高固含工艺技术的最新发展、国家政策对高固含技术态度的变化等方面进行阐述,使得行业能够对汽车高固含技术的进一步研讨推广。
1汽车高固含技术和水性漆的比较
1.1 VOC排放量的比较
3C2B中低固含溶剂型涂料中色漆施工固含平均在20%-30%之间,其单车VOC产生量占整个涂装工序近一半。
表1 某传统溶剂型3C2B汽车涂装生产线VOC分布情况
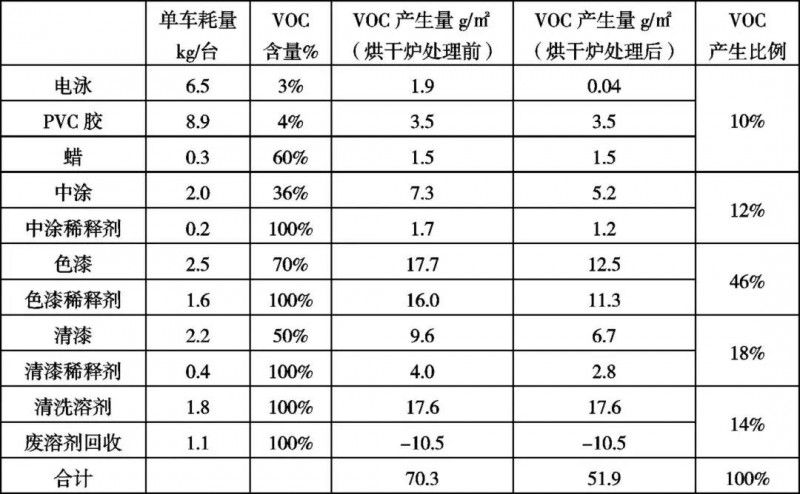
色漆涂料随着固含升高、用量减少,按施工固含反算,当施工固含在50%左右的时候,单车VOC和水性漆基本相当。
实际应用中发现高固含施工中油漆吐出量减少会使得上漆率提升10%左右、水性漆由于加电困难油漆利用率会降低10%左右。
下表是两家国际品牌涂料公司在我公司高固含色漆机器人实际喷涂的结果:
表2 高固含和中低固溶剂色漆机器人外表面单车喷涂比较

从上表可以看出,采用高固色漆,相比普通溶剂涂料浪费(即环境有害物)减少了50-70%,而水性漆,大约也是将普通溶剂涂料中60%左右的溶剂用水替代(图1),即同样内加电的情况下减少约60%的环境有害物。
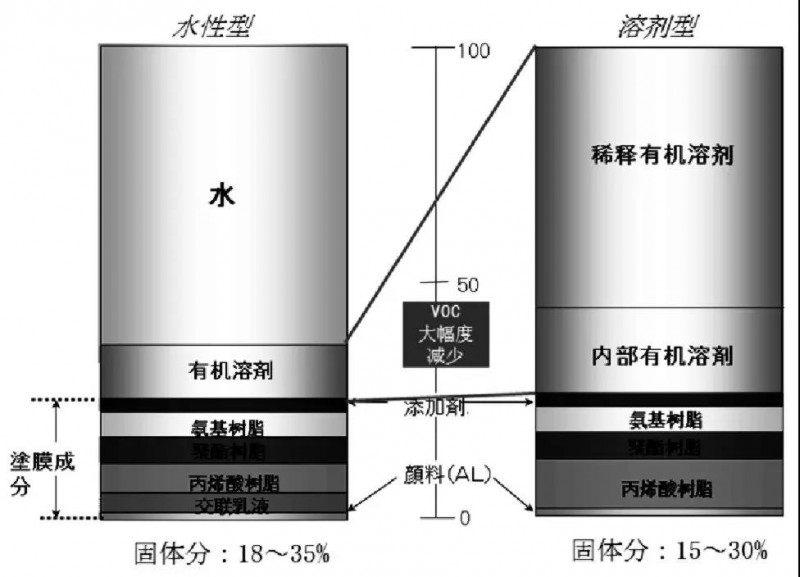
图1 普通溶剂涂料和水性漆施工状态成分对比
除了色漆涂料,中涂、清洗溶剂等对高固含和水性漆生产线VOC排放的比较结果也有影响。下表是国内几条外表面采用机器人,内表面采用人工喷涂的汽车涂装生产线VOC对比。
表3 不同工艺的生产线VOC排放量对比数据
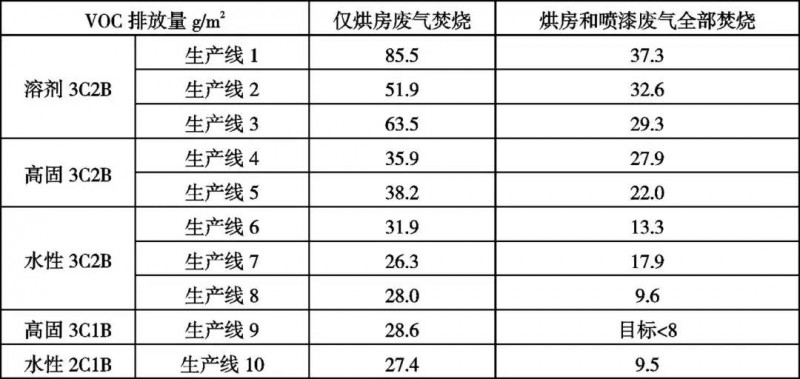
整体来说,在采用同样工序和机器人外喷、人工内喷的情况下,高固含相对水性漆VOC排放略高,如果内外喷均采用机器人静电喷涂,高固则可能具有VOC排放的优势。
1.2 单车碳排放
高固含和普通溶剂漆施工窗口基本相当,而水性漆因为水分预烘干需求(图2)和较为严格的施工窗口(图3),动能消耗较大,相应地碳排放也较多,福特公司有案例显示其它条件基本相同的情况下,高固含工艺比同工序水性工艺二氧化碳排放可以减少34%。
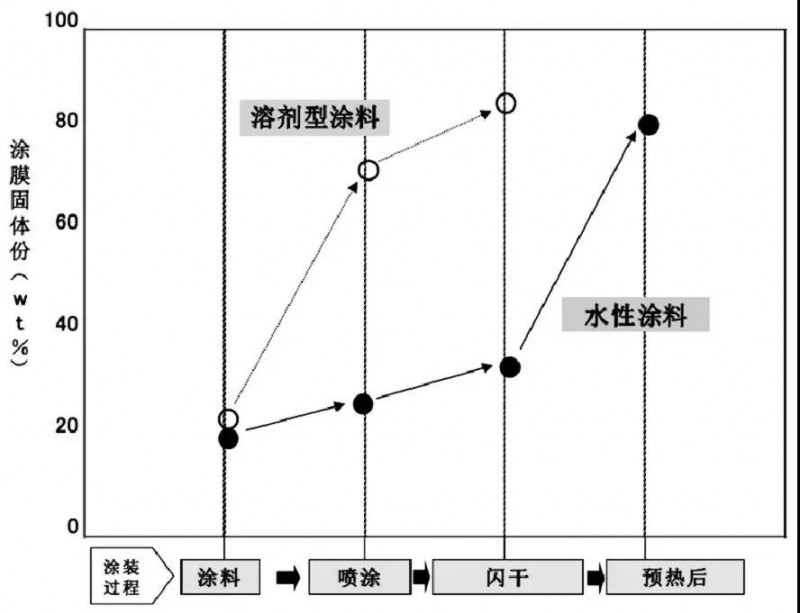
图2 水性漆必须借助预烘干才能达到湿膜固体分要求
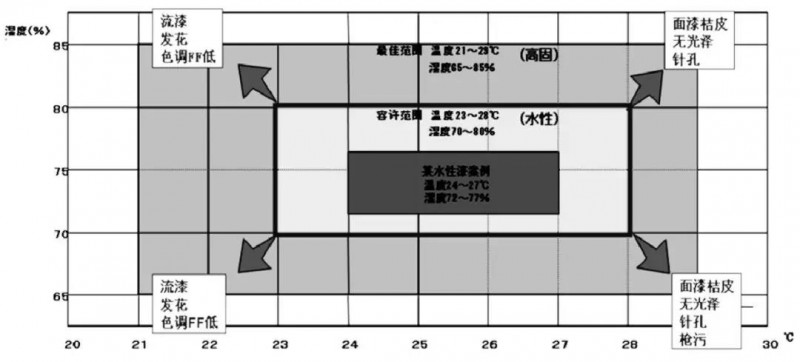
图3 水性漆和高固含的施工窗差异
1.3 废水废渣废溶剂后处理的影响
水性漆的核心优势是与水相融,这同时在后处理方面,也形成了一些对应的劣势(图4)。一方面前述上漆率的差异导致水性漆废物同比产生量更大,另一方面因为过喷漆雾难以从水中分离出来,以及表面活性剂的影响,喷涂循环水中的有机物含量高、泡沫多、气味大,循环水和污水难以处理,在监管不到位的情况下会形成很大的公害。随着干式喷漆漆雾分离技术的不断成熟,水性漆的后处理难题有望得到解决。
同理,水性清洗溶剂其中的溶剂也难以分离,目前均需花费较高的危费处理费用,而溶解涂料的清洗溶剂较为容易提炼出可以二次利用的产品,因此在部分地区溶剂型涂料的清洗溶剂可以作为商品卖给有处理资质的单位,建议法规支持清洗溶剂的回收利用。
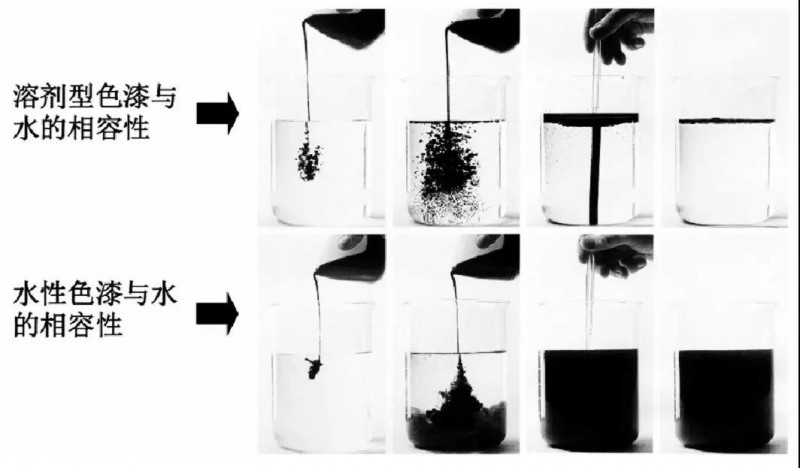
图4 因为树脂差异和表面活性剂等因素,水性漆完全分散溶解在水中
2几种高固含工艺的比较
2.1 环保法规对应情况
3C2B工艺中,仅仅色漆采用高固含,加上普通溶剂漆中涂原漆固含60%和清漆原漆固含50%左右的行业普遍情况,多数涂装线就可以达到2016年11月1日颁布实施《 涂装行业清洁生产评价指标体系》VOC部分三级指标(表4)。
表4 《涂装行业清洁生产评价指标体系》VOC部分
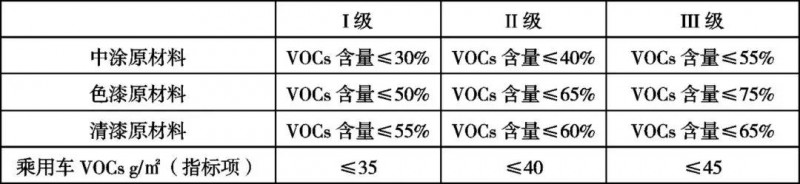
在此基础上若寻求更好地控制VOC排放、提升经济性或外观性能,除了研究提升有效物料利用率、减少无效物料的使用外,可以根据情况选择方案采用清漆切换高固、紧凑高固、配套2K的高固、免中涂高固等技术,根据中国涂料工业协会涂料行业标准牵头制定的《汽车用高固含体分溶剂型涂料》T/CNCIA 01001-2016(表5),参考表3数据,可以对应达到表4中VOC部分二级或一级指标。
表5 《汽车用高固含体分溶剂型涂料》施工固含部分
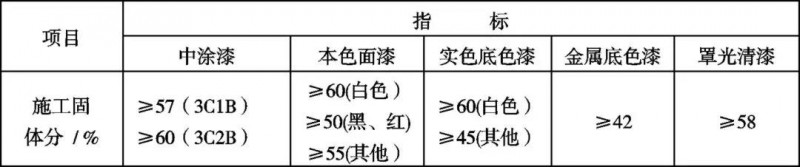
2.2 改造和运行成本
原有乘用车溶剂型涂装生产线,多采用3C2B方式,有的受原有工艺和布局的限制难以改造为3C1B工艺,如没有PVC烘干、中涂和面漆的位置难以相连等等,这需要根据生产线的情况具体分析。总体而言,不改变原有3C2B布局的改造成本和风险最低,改造为3C1B的难度要根据具体情况,但投资肯定更高,而清漆系统改造为2K清漆,也是一笔不小的投资。
在运行成本上,3C2B溶剂漆的中涂具有较大价格优势,现阶段3C2B色漆高固含还是最为经济的方案。随着3C1B高固含工艺的不断普及、高固含清漆和2K清漆的大量应用,加上紧凑工艺在效和能耗上的优势,未来3C1B高固含和3C1B高固含+2K清漆的运行成本有可能达到甚至低于3C2B高固含工艺 。
现阶段由3C2B传统溶剂涂装工艺改造为各类高固含工艺的比较如表6:
表6 五种高固含涂装工艺改造比较(在3C2B溶剂涂装工艺基础上)
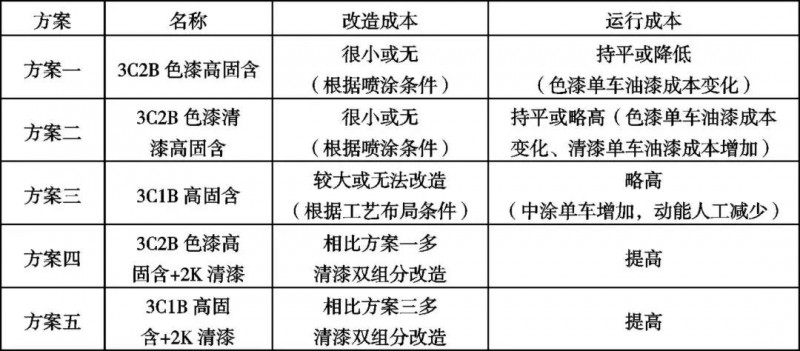
当然,如果考虑改造水性漆,目前行业已经有多个实际案例,这样的改造投资往往上亿、需要两三个月停产改造和一段时期的爬坡、运行成本也会明显提升,其改造和运行代价远远大于高固含方案。
2.3 外观性能比较
随着这几年的研究开发,我们也逐步积累了一些各类高固工艺的外观数据(参见表7),这些数据和我们构想的方向基本相同,即3C2B高固含工艺外观较好,在紧凑的3C1B高固含中最好配套2K清漆。
表7 某颜色不同高固含涂装工艺外观试验数据
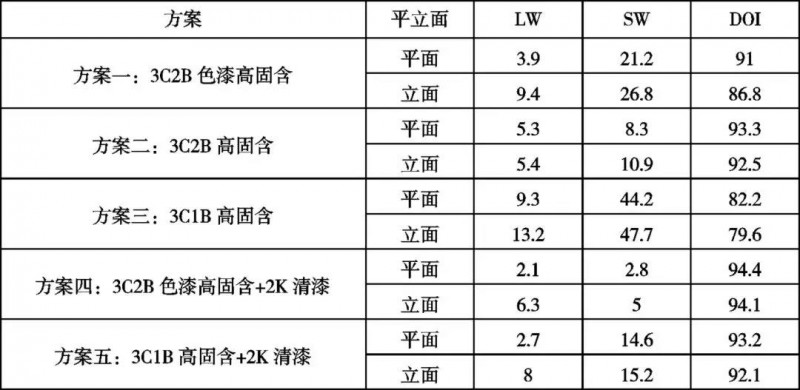
注:不同颜色、不同样本会有一定差异,本表只是根据标准符合性和趋势性验证。
因为提升外观的需要,尤其高性价比的万华国产异氰酸酯2K清漆固化剂的成熟,最近几年2K清漆的应用在国内迅速普及。当然,一些高固体系色漆和2K清漆的配套性研究,也会是一个长期的新难题。
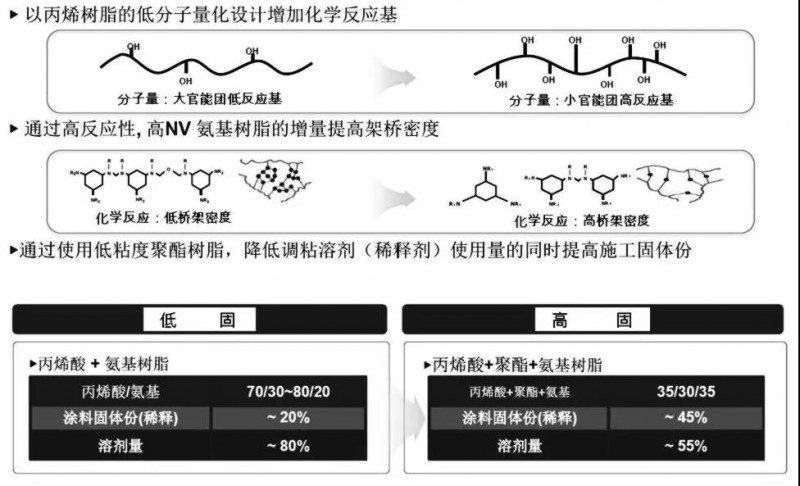
图5 立邦高固含汽车漆技术的原理
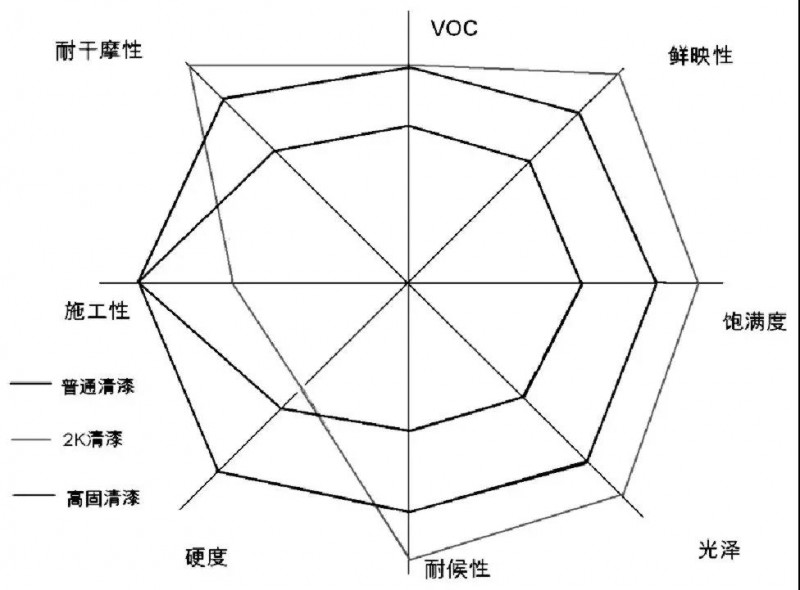
图6 普通清漆、2K清漆、高固清漆外观性能差异示意
外观和性能的差异,除了配套性和涂层厚度等,主要差异取决于清漆。各家同类清漆产品的开发机理不尽相同,如立邦高固含采用低分子量丙烯树脂+ 低粘度聚酯树脂+高NV氨基树脂(见图5),PPG高固含采用聚酯+丙烯酸体系,艾仕德高固含采用硅氧烷+丙烯酸体系,但总体来说,高固含清漆相比普通单组分清漆,VOC上有一定优势,施工性能
相当或略好,在外观和性能上有所提升;2K清漆和高固含清漆VOC基本相当,在车辆使用中更关注的目视外观、耐磨性、耐溶剂等方面表现更好,参考部分油漆材料供应商和主机厂的资料绘制的三种产品大致差异示意见图6。
3高固含调试的要点
汽车高固含作为一个新技术,尤其在替代原有普通溶剂漆时,需要注意一些技术方面的差异。
高固含表干性能与中低固体分油漆不同,低固体分色漆在湿碰湿工艺时,需要表干,而高体分油漆不会表干。为了增加对流挂的控制,油漆必选表现为在剪切力作用下的假塑性,在高剪切力下粘度降低,以及剪切力屈服点,即在某一剪切力之下表现为高的剪切力,为了能使油漆具备剪切变稀以及剪切压力的屈服点,高分子微胶的加入使得高固体分色漆具备了这样的性能。这种表现有一点类似水性涂料,因此水性涂料的一些缺点在高固涂料上也会有不同程度的反映,如容易因表面张力问题导致缩孔。另外,高固含改造多直接配套原有材料,高固含清漆跟原有中涂接触可能产生抽缩等不良反应,跟原有PVC胶条接触可能产生油漆开裂或发粘的情况。
因此,采用高固含涂料,需要按照施工要求核查设备是否需要改造,在实验室和调试中要研究验证配套关系。高档的溶剂型汽车涂装线施工条件较好,基本可以满足高固含涂料施工的要求(参见表8),只不过原有溶剂型涂料经过多年实践在实际应用中可能要求十分宽泛,比如温湿度、压缩空气含油量大幅突破产品技术要求也能施工,高固含涂料目前还达不到。在原有的PVC胶配套上,要注意塑化剂等迁移材料的控制,和阻隔迁移材料的适当添加。
表8 高固含涂料施工参数控制
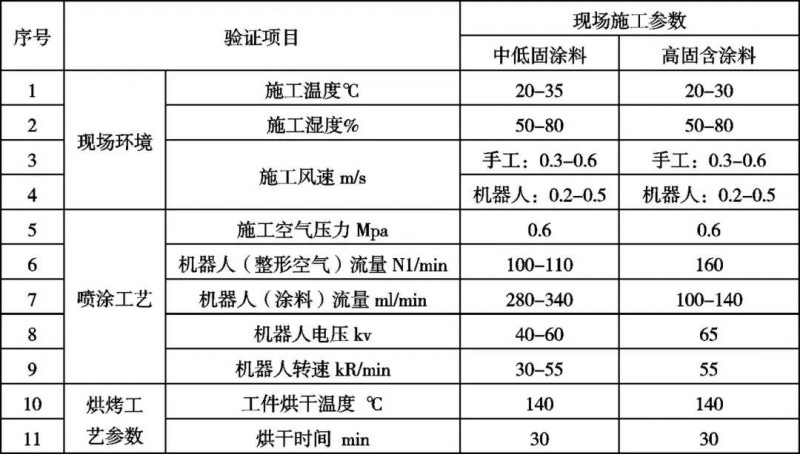
4总结
在高固含工艺成功实践应用的基数上,经过努力推动,高固含在汽车涂装法规上逐渐被认可,新颁布的《涂装行业清洁生产评价指标体系》已经体现了对汽车高固含涂装工艺技术的支撑。2016年12月26日环境保护部办公厅印发执行的《汽车整车制造建设项目环境影响评价文件审批原则》提出:大气污染防治重点区域内新建、扩建汽车项目,改建项目水性、高固含份、粉末、紫外光固化涂料等低挥发性有机物含量涂料的使用比例达到50%以上。这是建设项目环评法规中首次明确支持在改扩建中采用高固含含工艺。在更加严格的发达地区地方政策方面,也有对汽车涂装高固含工艺十分支持的,如《浙江省挥发性有机物深化治理与减排工作方案(2017-2020)》(征求意见稿),将高固含定义为和水性漆一样“含有VOC的非溶剂型涂料”,作为汽车制造业首要推荐的环保涂料升级方案。随着法规的支持和技术的完善,汽车高固含涂装技术必将和水性漆技术相互竞争促进,共同承担起汽车涂装行业节能减排的重任。
单位:奇瑞捷豹路虎汽车公司
引言
汽车高固含技术并不是一个新名词,但真正具有稳定的施工高固含技术问世尚不足十年。经过实践验证,新的高固含技术在VOC排放上接近水性漆的水平,在碳排放和施工要求上又具备原来普通溶剂型涂料的优势,是节能环保涂料技术方面的新选择。为了适应部分原有生产线的环保改造需求,我们在福特3C1B高固含技术的基础上,陆续开发应用了一些新的高固含工艺技术,如3C2B色漆清漆高固含、3C2B色漆高固含等,并在研讨配套2K清漆和免中涂的高固含技术。本文重点从汽车高固含技术和水性漆的比较、汽车高固含工艺技术的最新发展、国家政策对高固含技术态度的变化等方面进行阐述,使得行业能够对汽车高固含技术的进一步研讨推广。
1汽车高固含技术和水性漆的比较
1.1 VOC排放量的比较
3C2B中低固含溶剂型涂料中色漆施工固含平均在20%-30%之间,其单车VOC产生量占整个涂装工序近一半。
表1 某传统溶剂型3C2B汽车涂装生产线VOC分布情况
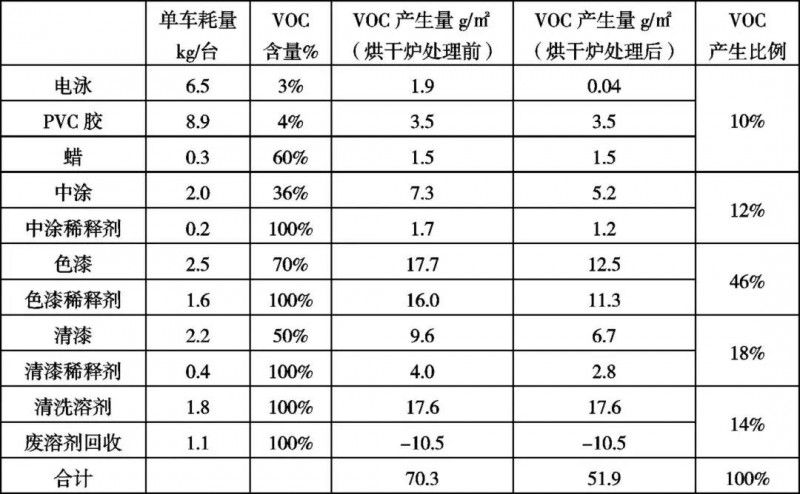
色漆涂料随着固含升高、用量减少,按施工固含反算,当施工固含在50%左右的时候,单车VOC和水性漆基本相当。
实际应用中发现高固含施工中油漆吐出量减少会使得上漆率提升10%左右、水性漆由于加电困难油漆利用率会降低10%左右。
下表是两家国际品牌涂料公司在我公司高固含色漆机器人实际喷涂的结果:
表2 高固含和中低固溶剂色漆机器人外表面单车喷涂比较

从上表可以看出,采用高固色漆,相比普通溶剂涂料浪费(即环境有害物)减少了50-70%,而水性漆,大约也是将普通溶剂涂料中60%左右的溶剂用水替代(图1),即同样内加电的情况下减少约60%的环境有害物。
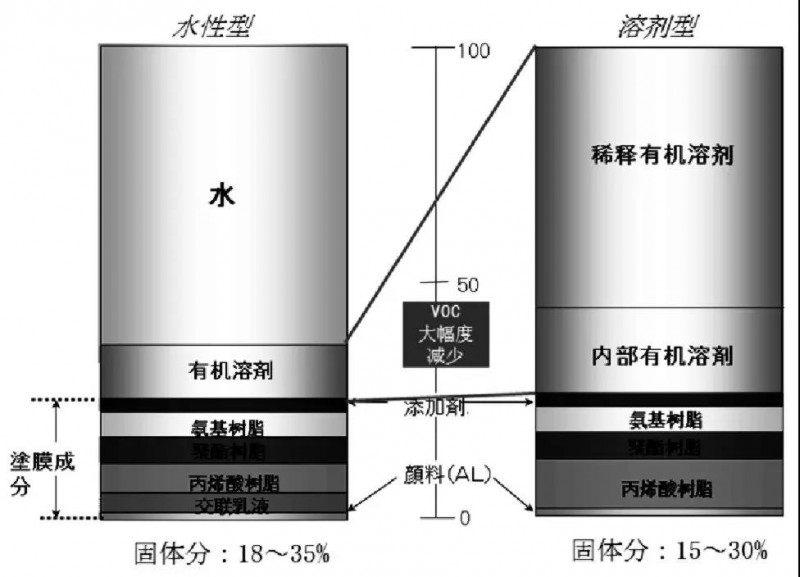
图1 普通溶剂涂料和水性漆施工状态成分对比
除了色漆涂料,中涂、清洗溶剂等对高固含和水性漆生产线VOC排放的比较结果也有影响。下表是国内几条外表面采用机器人,内表面采用人工喷涂的汽车涂装生产线VOC对比。
表3 不同工艺的生产线VOC排放量对比数据
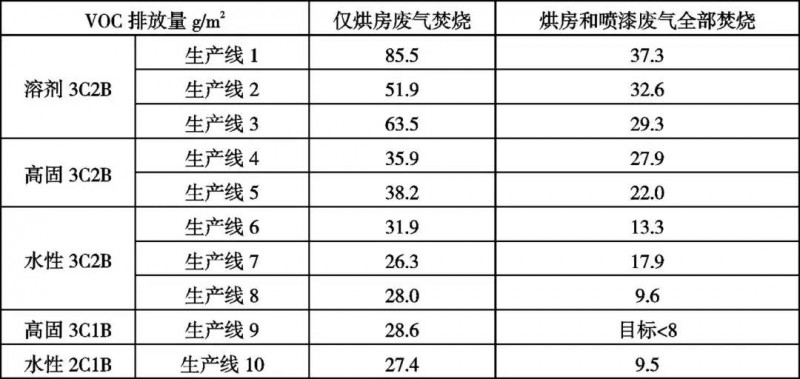
整体来说,在采用同样工序和机器人外喷、人工内喷的情况下,高固含相对水性漆VOC排放略高,如果内外喷均采用机器人静电喷涂,高固则可能具有VOC排放的优势。
1.2 单车碳排放
高固含和普通溶剂漆施工窗口基本相当,而水性漆因为水分预烘干需求(图2)和较为严格的施工窗口(图3),动能消耗较大,相应地碳排放也较多,福特公司有案例显示其它条件基本相同的情况下,高固含工艺比同工序水性工艺二氧化碳排放可以减少34%。
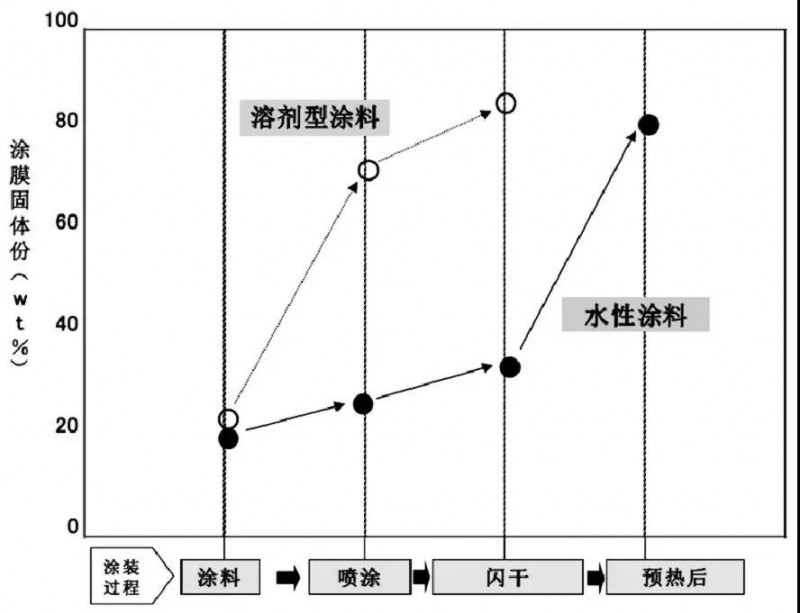
图2 水性漆必须借助预烘干才能达到湿膜固体分要求
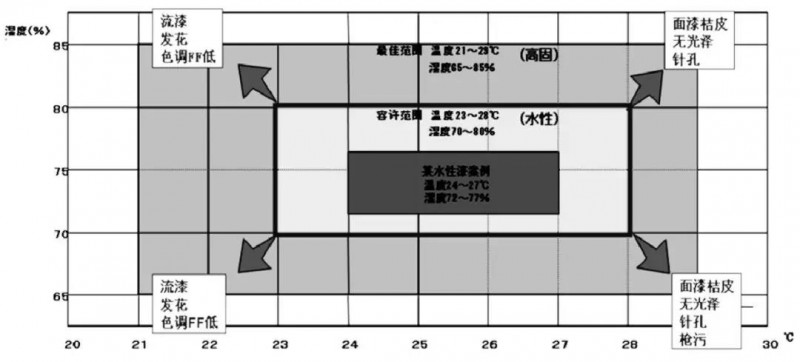
图3 水性漆和高固含的施工窗差异
1.3 废水废渣废溶剂后处理的影响
水性漆的核心优势是与水相融,这同时在后处理方面,也形成了一些对应的劣势(图4)。一方面前述上漆率的差异导致水性漆废物同比产生量更大,另一方面因为过喷漆雾难以从水中分离出来,以及表面活性剂的影响,喷涂循环水中的有机物含量高、泡沫多、气味大,循环水和污水难以处理,在监管不到位的情况下会形成很大的公害。随着干式喷漆漆雾分离技术的不断成熟,水性漆的后处理难题有望得到解决。
同理,水性清洗溶剂其中的溶剂也难以分离,目前均需花费较高的危费处理费用,而溶解涂料的清洗溶剂较为容易提炼出可以二次利用的产品,因此在部分地区溶剂型涂料的清洗溶剂可以作为商品卖给有处理资质的单位,建议法规支持清洗溶剂的回收利用。
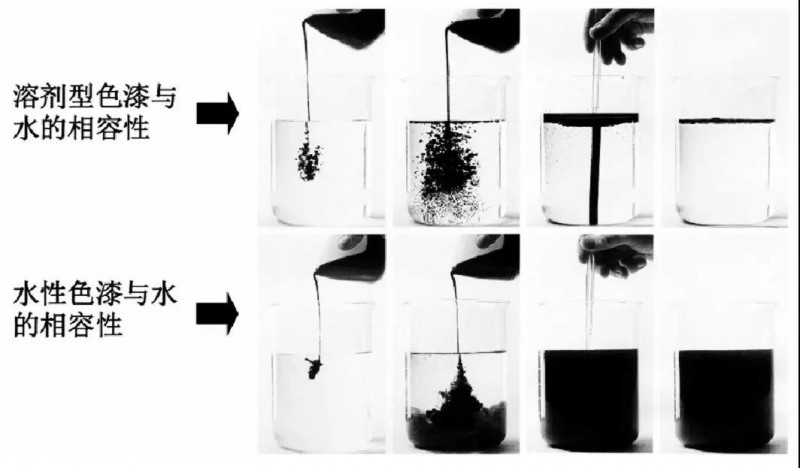
图4 因为树脂差异和表面活性剂等因素,水性漆完全分散溶解在水中
2几种高固含工艺的比较
2.1 环保法规对应情况
3C2B工艺中,仅仅色漆采用高固含,加上普通溶剂漆中涂原漆固含60%和清漆原漆固含50%左右的行业普遍情况,多数涂装线就可以达到2016年11月1日颁布实施《 涂装行业清洁生产评价指标体系》VOC部分三级指标(表4)。
表4 《涂装行业清洁生产评价指标体系》VOC部分
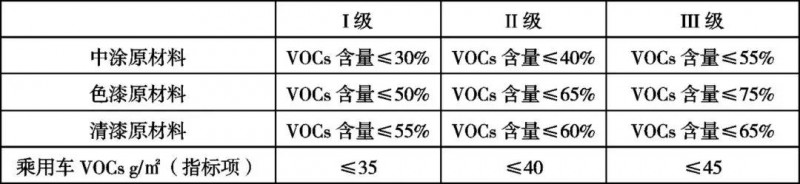
在此基础上若寻求更好地控制VOC排放、提升经济性或外观性能,除了研究提升有效物料利用率、减少无效物料的使用外,可以根据情况选择方案采用清漆切换高固、紧凑高固、配套2K的高固、免中涂高固等技术,根据中国涂料工业协会涂料行业标准牵头制定的《汽车用高固含体分溶剂型涂料》T/CNCIA 01001-2016(表5),参考表3数据,可以对应达到表4中VOC部分二级或一级指标。
表5 《汽车用高固含体分溶剂型涂料》施工固含部分
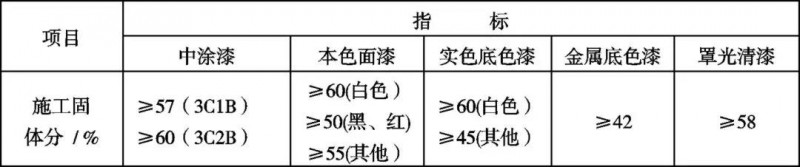
2.2 改造和运行成本
原有乘用车溶剂型涂装生产线,多采用3C2B方式,有的受原有工艺和布局的限制难以改造为3C1B工艺,如没有PVC烘干、中涂和面漆的位置难以相连等等,这需要根据生产线的情况具体分析。总体而言,不改变原有3C2B布局的改造成本和风险最低,改造为3C1B的难度要根据具体情况,但投资肯定更高,而清漆系统改造为2K清漆,也是一笔不小的投资。
在运行成本上,3C2B溶剂漆的中涂具有较大价格优势,现阶段3C2B色漆高固含还是最为经济的方案。随着3C1B高固含工艺的不断普及、高固含清漆和2K清漆的大量应用,加上紧凑工艺在效和能耗上的优势,未来3C1B高固含和3C1B高固含+2K清漆的运行成本有可能达到甚至低于3C2B高固含工艺 。
现阶段由3C2B传统溶剂涂装工艺改造为各类高固含工艺的比较如表6:
表6 五种高固含涂装工艺改造比较(在3C2B溶剂涂装工艺基础上)
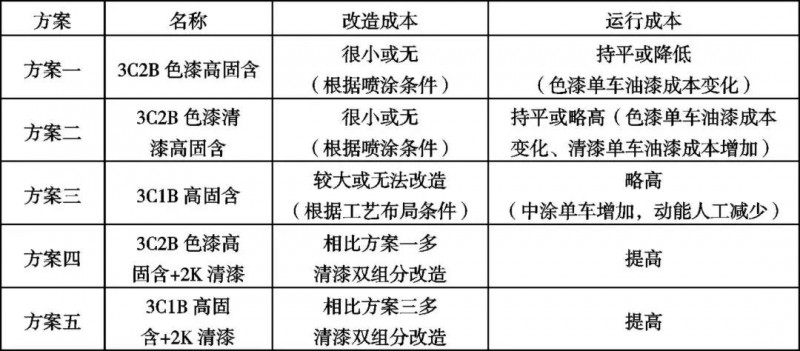
当然,如果考虑改造水性漆,目前行业已经有多个实际案例,这样的改造投资往往上亿、需要两三个月停产改造和一段时期的爬坡、运行成本也会明显提升,其改造和运行代价远远大于高固含方案。
2.3 外观性能比较
随着这几年的研究开发,我们也逐步积累了一些各类高固工艺的外观数据(参见表7),这些数据和我们构想的方向基本相同,即3C2B高固含工艺外观较好,在紧凑的3C1B高固含中最好配套2K清漆。
表7 某颜色不同高固含涂装工艺外观试验数据
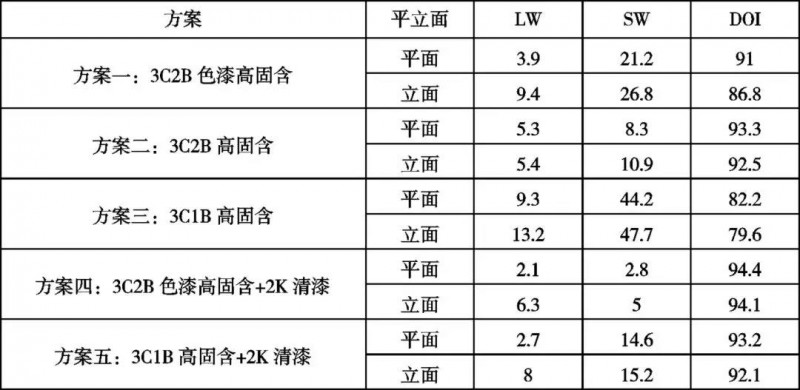
注:不同颜色、不同样本会有一定差异,本表只是根据标准符合性和趋势性验证。
因为提升外观的需要,尤其高性价比的万华国产异氰酸酯2K清漆固化剂的成熟,最近几年2K清漆的应用在国内迅速普及。当然,一些高固体系色漆和2K清漆的配套性研究,也会是一个长期的新难题。
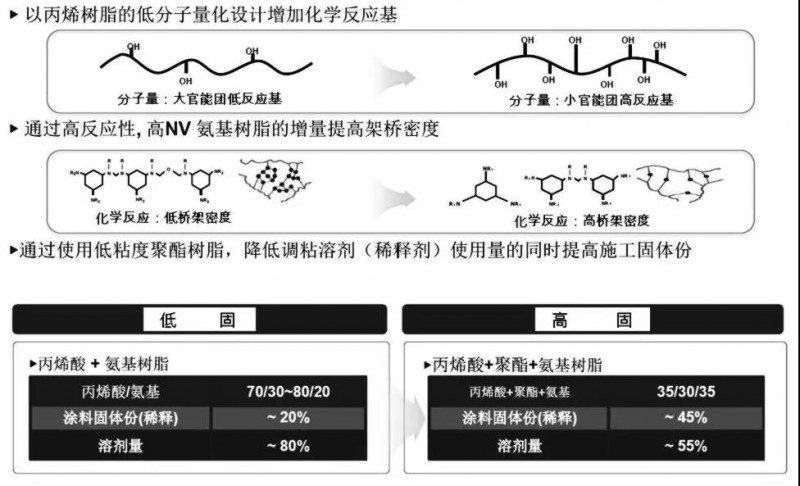
图5 立邦高固含汽车漆技术的原理
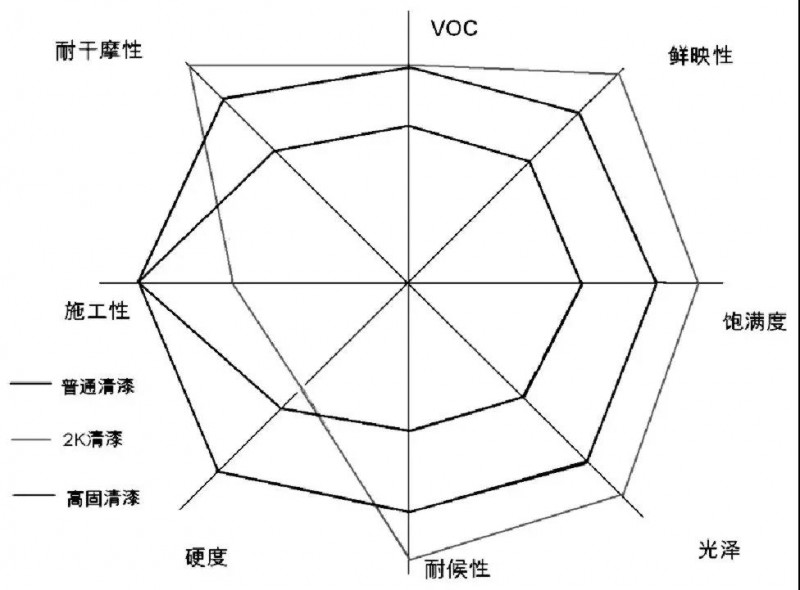
图6 普通清漆、2K清漆、高固清漆外观性能差异示意
外观和性能的差异,除了配套性和涂层厚度等,主要差异取决于清漆。各家同类清漆产品的开发机理不尽相同,如立邦高固含采用低分子量丙烯树脂+ 低粘度聚酯树脂+高NV氨基树脂(见图5),PPG高固含采用聚酯+丙烯酸体系,艾仕德高固含采用硅氧烷+丙烯酸体系,但总体来说,高固含清漆相比普通单组分清漆,VOC上有一定优势,施工性能
相当或略好,在外观和性能上有所提升;2K清漆和高固含清漆VOC基本相当,在车辆使用中更关注的目视外观、耐磨性、耐溶剂等方面表现更好,参考部分油漆材料供应商和主机厂的资料绘制的三种产品大致差异示意见图6。
3高固含调试的要点
汽车高固含作为一个新技术,尤其在替代原有普通溶剂漆时,需要注意一些技术方面的差异。
高固含表干性能与中低固体分油漆不同,低固体分色漆在湿碰湿工艺时,需要表干,而高体分油漆不会表干。为了增加对流挂的控制,油漆必选表现为在剪切力作用下的假塑性,在高剪切力下粘度降低,以及剪切力屈服点,即在某一剪切力之下表现为高的剪切力,为了能使油漆具备剪切变稀以及剪切压力的屈服点,高分子微胶的加入使得高固体分色漆具备了这样的性能。这种表现有一点类似水性涂料,因此水性涂料的一些缺点在高固涂料上也会有不同程度的反映,如容易因表面张力问题导致缩孔。另外,高固含改造多直接配套原有材料,高固含清漆跟原有中涂接触可能产生抽缩等不良反应,跟原有PVC胶条接触可能产生油漆开裂或发粘的情况。
因此,采用高固含涂料,需要按照施工要求核查设备是否需要改造,在实验室和调试中要研究验证配套关系。高档的溶剂型汽车涂装线施工条件较好,基本可以满足高固含涂料施工的要求(参见表8),只不过原有溶剂型涂料经过多年实践在实际应用中可能要求十分宽泛,比如温湿度、压缩空气含油量大幅突破产品技术要求也能施工,高固含涂料目前还达不到。在原有的PVC胶配套上,要注意塑化剂等迁移材料的控制,和阻隔迁移材料的适当添加。
表8 高固含涂料施工参数控制
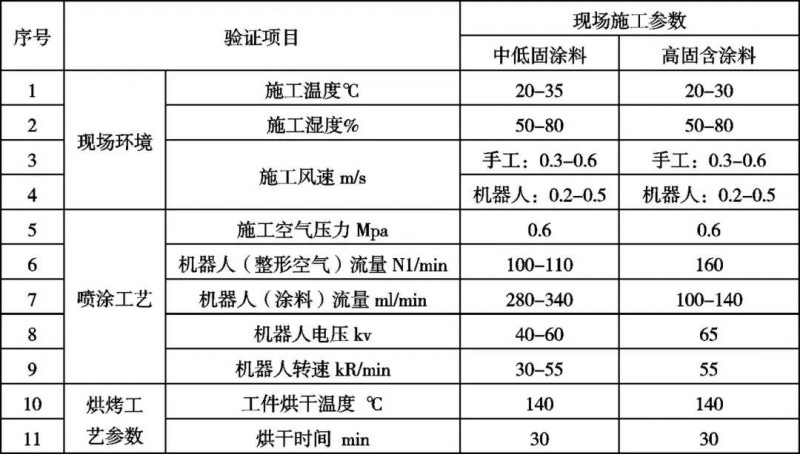
4总结
在高固含工艺成功实践应用的基数上,经过努力推动,高固含在汽车涂装法规上逐渐被认可,新颁布的《涂装行业清洁生产评价指标体系》已经体现了对汽车高固含涂装工艺技术的支撑。2016年12月26日环境保护部办公厅印发执行的《汽车整车制造建设项目环境影响评价文件审批原则》提出:大气污染防治重点区域内新建、扩建汽车项目,改建项目水性、高固含份、粉末、紫外光固化涂料等低挥发性有机物含量涂料的使用比例达到50%以上。这是建设项目环评法规中首次明确支持在改扩建中采用高固含含工艺。在更加严格的发达地区地方政策方面,也有对汽车涂装高固含工艺十分支持的,如《浙江省挥发性有机物深化治理与减排工作方案(2017-2020)》(征求意见稿),将高固含定义为和水性漆一样“含有VOC的非溶剂型涂料”,作为汽车制造业首要推荐的环保涂料升级方案。随着法规的支持和技术的完善,汽车高固含涂装技术必将和水性漆技术相互竞争促进,共同承担起汽车涂装行业节能减排的重任。
编辑推荐
最新资讯
-
旭化成微电子开始批量生产用于环保发
2025-04-24 16:00
-
华为、地平线、大众、东风、起亚等引
2025-04-24 08:27
-
全球产业链聚沪 共探双碳新路径 SNEC
2025-04-18 18:05
-
柯马签订具有约束力的协议收购 Autom
2025-04-17 13:01
-
高效协同新范式:比亚迪叉车领创智能
2025-04-17 10:04