ABB喷涂机器人的降级模式与节距控制
2018-08-08 14:47:45· 来源:现代涂料与涂装
现在各大汽车整车厂的涂装车间普遍采用机器人进行车身外部喷涂,相对于以前的人工喷涂和往复机式喷涂,机器人喷涂具有喷涂范围大、灵活性好、质量好、速度快、效率高、节省材料等特点。喷涂机器人是先进而复杂的机电一体化设备,发生故障时,如果预计处理时间较长或者暂时难以解决,就要考虑是否旁路这台故障机器人,改由其它机器人分担故障机器人的工作,继续维持生产,生产结束之后再处理该机器人的问题,这种在个别机器人故障时的应急生产方式就是降级模式。降级模式下还要控制好车体间的节距,减少停线,保证产能和质量。
ABB喷涂机器人的降级模式与节距控制
谢巨龙
(长安福特汽车有限公司哈尔滨分公司 哈尔滨 150060)
0 引言
现在各大汽车整车厂的涂装车间普遍采用机器人进行车身外部喷涂,相对于以前的人工喷涂和往复机式喷涂,机器人喷涂具有喷涂范围大、灵活性好、质量好、速度快、效率高、节省材料等特点。喷涂机器人是先进而复杂的机电一体化设备,发生故障时,如果预计处理时间较长或者暂时难以解决,就要考虑是否旁路这台故障机器人,改由其它机器人分担故障机器人的工作,继续维持生产,生产结束之后再处理该机器人的问题,这种在个别机器人故障时的应急生产方式就是降级模式。降级模式下还要控制好车体间的节距,减少停线,保证产能和质量。
1 全自动降级模式
要实现全自动的降级模式,需要编写和调试相应的控制程序、喷涂轨迹和喷涂参数,相当于增加一种车型,难度和工作量都较大,整车厂自行修改比较困难,最好在生产线规划和建设时向专业承包商提出喷涂生产线要具备降级模式的要求,专业承包商如ABB等公司可以提供相应的解决方案。
2 ABB机器人喷涂线介绍
2.1 ABB机器人喷涂线的标准配置
目前ABB主推的喷涂机器人型号是6.0系统的 5500,对采用3C1B涂装工艺、JPH为33的跟踪式轿车喷涂生产线,要配置18台外喷机器人(本例中的内部喷涂由人工完成),在双链式传送带两侧交错分布。18台机器人从工艺上分为中涂、色漆和清漆3个站,其中中涂站机器人配置为4台,每侧2台;色漆站机器人配置为8台,每侧4台;清漆站机器人配置为6台,每侧3台。中涂站喷一遍漆,色漆站相当于2个中涂站,喷两遍漆。清漆站类似于2个降级模式的中涂站,侧面喷2遍漆,顶面喷一遍漆。每站都配有1台控制喷涂机器人的PLC(简称喷涂PLC),它们在传送带的主传动轴上都接有各自的编码器,编码器信号同时连也接到机器人,用来跟踪传送带上载有车身的滑橇的位置,各喷涂PLC与站内机器人和传送带PLC之间通过网络进行数据交换。
2.2 ABB机器人喷涂线的部分术语和数据
ABB机器人喷涂线的部分术语和数据见表1所列。
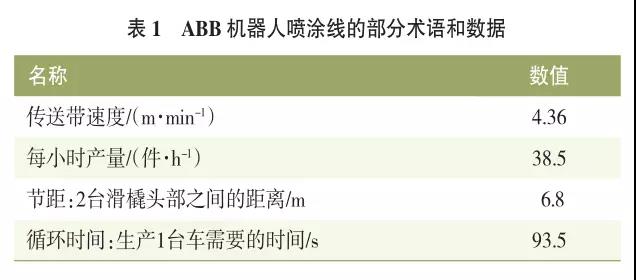
2.3 正常生产模式
在传送带(双链式)速度为4.36米/分、最小节距稳定在6.8米的情况下,ABB机器人喷涂线每小时最多可以生产38.5台车,单车运行周期时间为93.5秒,这个周期时间是已经包含了换色清洗动作的最短时间。计算如下:
每小时产量JPH=4.36×60/6.8=38.5台/小时
循环时间Cycle time=3600/38.5=93.5秒
2.4 降级生产模式
如果某站的4台机器人中有1台故障而且短期难以修复时,可暂时将其打到安全位置并设为旁路不用,传送带速度维持不变,其对面的机器人改喷全部水平面(顶面),其它2台改喷全部的垂直面(侧面)。
在上述喷涂生产线配置情况下,在1台机器人被旁路时,每站的降级模式最多有如下3种:
1、 站内任意一侧第1台机器人降级
2、 站内任意一侧第2台机器人降级
3、 站内任意一侧第3台机器人降级
中涂站和色漆站都只有2种降级模式,6台机器人的清漆站有3种降级模式。
降级模式下工作的机器人需要分担故障机器人的工作,喷涂更多的面积,花费更多的时间,再加上换色清洗的时间,单车运行周期时间会超过上述的93.5秒。如果换色清洗尚未完成时,新来的下一台车体已经到达预设的开始喷涂位置,正在忙于换色清洗的机器人就来不及回来喷涂该车了,这就涉及到车身节距控制问题。
3 节距控制
3.1 节距过近时的传送带暂停等待程序
正常模式和降级模式下,都可能发生换色尚未完成时下一台车体已到达预设启动喷涂位置导致机器人来不及喷涂的情况,为了避免这种情况,需要在下一台车体到达开始喷涂位置之前暂停传送带,等待换色完成后再启动传送带。ABB 5500机器人程序在启动喷涂位置之前预设了传送带暂停等待换色完成的位置,这些预设位置数据保存在cnvpos.ndx文件中,包括正常模式和3种降级模式下的4种位置数据,比相应模式下的开始喷涂位置提前一段距离(50mm)。换色尚未完成时,机器人程序会把C1position数值(车身从外部同步启动信号开始的前进位置计数器值)与cnvpos.ndx文件中的相应数值进行比较,从而决定是否停线等待。
下面是代号为PR RR2的中涂右侧2号机器人的cnvpos.ndx文件的实际内容:
Program Index
| ____ InitialWait Position for Conveyor
| |
1,2350,1650,1850,1800
2,2350,1950,1750,1800
3,1800,1800,1800,1800
第一列为程序号,对应不同的车型。
第二列是正常生产时新来的下一台车体等待换色完成的位置数据,单位是mm,比正常开始喷涂的位置2400mm提前了50mm。
后面3列是降级时等待换色完成的位置数据,分别对应站内对面的左侧第1台机器人降级、左右第2台机器人降级和左右第3台机器人降级的情况,只有清漆站有第3台机器人降级的情况。从上面的数值可以看到,降级时的位置数值比正常生产时的数值要小,表示要比正常生产时提前等待,不同的车型或者不同的降级模式下,数值可能不一样。
3.2 降级模式下的节距控制实例
上面的例子中,PR RR2机器人车型程序号为1时,在对面PR RL2机器人故障后被旁路时采用第2种降级模式,等待换色完成的位置为1850mm,比正常的2350mm要提前500mm。线速4.36m/min时,500mm的距离对应的传送带运行时间=500mm/(4360mm/60s)=6.88s,约7秒钟,就是说两台车之间需要增加节距500mm或者延时7秒钟,否则在车体连续的情况下,传送带会因后车等待前车换色清洗完成而停线。
实际降级模式也验证了这一点,在中涂左侧PR RL2机器人故障后,将其打到安全位置并旁路,开启降级模式,由于最初传送带没有降级时的节距调整功能,车身节距维持6800mm不变,导致每次换色清洗都会停线,当时换色情况也比较多,传送带频繁停止和启动很难让人满意,既对设备不利,也影响喷涂质量,还可能引起车体(滑橇)在传送带上的滑移,导致车身与机器人碰撞等更严重的问题。只好临时修改传送带入口送车滚床的送车程序,在其它条件都满足的情况下,延时一段时间再送车来增加节距,经验证,延时小于7秒时换色清洗仍会停线,7秒以上可以连续运行。
3.3 降级模式下的节距控制的改进
上述降级模式实例中增加的延时延长了每一台车的周期时间,包括不需要换色的车体,导致生产时间延长和能源浪费,这也是我们不希望的,因此考虑加以改进,实现降级时的节距自动调节功能,即换色车之间增加节距,同色车之间不增加节距,这样可以保证降级时传送带连续运行,避免不必要的停线。
要实现降级时的节距自动调节功能,需要喷涂机与传送带密切配合。在本例改进方案中,我们要求喷涂PLC向传送带PLC发送各喷涂站的降级信号、具体降级模式和需要增加的节距数值(或者对应的时间),传送带PLC需要根据各站具体降级情况,以及本台准备送入喷房的车体的颜色与上台车相比是否变化来选择适当的节距增量,最大限度减少降级模式对生产的影响。以中涂左侧PR RL2机器人旁路后的降级模式为例,中涂PLC向传送带发送站降级信号为1、发送降级模式为2、发送节距增量为500,传送带PLC收到降级信号后,就要比较本台准备送入喷房的车体的中涂颜色与上台车相比是否变化来插入适当的节距增量。同理,色漆站降级时就要比较色漆颜色是否变化,清漆站降级时就要比较清漆颜色是否变化。当换色情况不频繁时,也可以使用简化的方法增加降级时的节距,就是喷涂PLC只向传送带发送具体站降级信号,传送带PLC插入换色需要的最大节距,从本例的18台机器人的全部cnvpos.ndx文件中,查到最大节距增量为700mm,采用定时器增加节距时延时10秒即可。
4 结语
降级模式下自动调节车身节距,可以最大限度保证跟踪式喷涂线传送带的连续运行,得到降级模式下的最大产能和最好质量,特别是对颜色变化频繁的喷涂生产线更加重要,在项目前期规划和建设时要向承包商提出相关要求,并在项目实施过程中完成这项自动化功能。
(详情见《现代涂料与涂装》2018-7)
谢巨龙
(长安福特汽车有限公司哈尔滨分公司 哈尔滨 150060)
0 引言
现在各大汽车整车厂的涂装车间普遍采用机器人进行车身外部喷涂,相对于以前的人工喷涂和往复机式喷涂,机器人喷涂具有喷涂范围大、灵活性好、质量好、速度快、效率高、节省材料等特点。喷涂机器人是先进而复杂的机电一体化设备,发生故障时,如果预计处理时间较长或者暂时难以解决,就要考虑是否旁路这台故障机器人,改由其它机器人分担故障机器人的工作,继续维持生产,生产结束之后再处理该机器人的问题,这种在个别机器人故障时的应急生产方式就是降级模式。降级模式下还要控制好车体间的节距,减少停线,保证产能和质量。
1 全自动降级模式
要实现全自动的降级模式,需要编写和调试相应的控制程序、喷涂轨迹和喷涂参数,相当于增加一种车型,难度和工作量都较大,整车厂自行修改比较困难,最好在生产线规划和建设时向专业承包商提出喷涂生产线要具备降级模式的要求,专业承包商如ABB等公司可以提供相应的解决方案。
2 ABB机器人喷涂线介绍
2.1 ABB机器人喷涂线的标准配置
目前ABB主推的喷涂机器人型号是6.0系统的 5500,对采用3C1B涂装工艺、JPH为33的跟踪式轿车喷涂生产线,要配置18台外喷机器人(本例中的内部喷涂由人工完成),在双链式传送带两侧交错分布。18台机器人从工艺上分为中涂、色漆和清漆3个站,其中中涂站机器人配置为4台,每侧2台;色漆站机器人配置为8台,每侧4台;清漆站机器人配置为6台,每侧3台。中涂站喷一遍漆,色漆站相当于2个中涂站,喷两遍漆。清漆站类似于2个降级模式的中涂站,侧面喷2遍漆,顶面喷一遍漆。每站都配有1台控制喷涂机器人的PLC(简称喷涂PLC),它们在传送带的主传动轴上都接有各自的编码器,编码器信号同时连也接到机器人,用来跟踪传送带上载有车身的滑橇的位置,各喷涂PLC与站内机器人和传送带PLC之间通过网络进行数据交换。
2.2 ABB机器人喷涂线的部分术语和数据
ABB机器人喷涂线的部分术语和数据见表1所列。
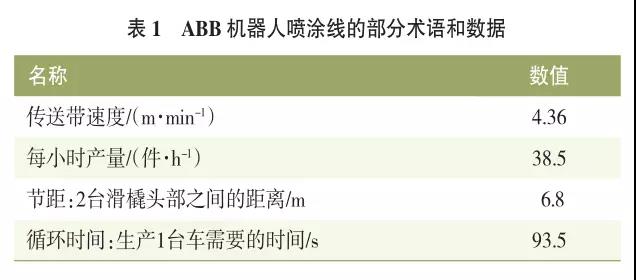
2.3 正常生产模式
在传送带(双链式)速度为4.36米/分、最小节距稳定在6.8米的情况下,ABB机器人喷涂线每小时最多可以生产38.5台车,单车运行周期时间为93.5秒,这个周期时间是已经包含了换色清洗动作的最短时间。计算如下:
每小时产量JPH=4.36×60/6.8=38.5台/小时
循环时间Cycle time=3600/38.5=93.5秒
2.4 降级生产模式
如果某站的4台机器人中有1台故障而且短期难以修复时,可暂时将其打到安全位置并设为旁路不用,传送带速度维持不变,其对面的机器人改喷全部水平面(顶面),其它2台改喷全部的垂直面(侧面)。
在上述喷涂生产线配置情况下,在1台机器人被旁路时,每站的降级模式最多有如下3种:
1、 站内任意一侧第1台机器人降级
2、 站内任意一侧第2台机器人降级
3、 站内任意一侧第3台机器人降级
中涂站和色漆站都只有2种降级模式,6台机器人的清漆站有3种降级模式。
降级模式下工作的机器人需要分担故障机器人的工作,喷涂更多的面积,花费更多的时间,再加上换色清洗的时间,单车运行周期时间会超过上述的93.5秒。如果换色清洗尚未完成时,新来的下一台车体已经到达预设的开始喷涂位置,正在忙于换色清洗的机器人就来不及回来喷涂该车了,这就涉及到车身节距控制问题。
3 节距控制
3.1 节距过近时的传送带暂停等待程序
正常模式和降级模式下,都可能发生换色尚未完成时下一台车体已到达预设启动喷涂位置导致机器人来不及喷涂的情况,为了避免这种情况,需要在下一台车体到达开始喷涂位置之前暂停传送带,等待换色完成后再启动传送带。ABB 5500机器人程序在启动喷涂位置之前预设了传送带暂停等待换色完成的位置,这些预设位置数据保存在cnvpos.ndx文件中,包括正常模式和3种降级模式下的4种位置数据,比相应模式下的开始喷涂位置提前一段距离(50mm)。换色尚未完成时,机器人程序会把C1position数值(车身从外部同步启动信号开始的前进位置计数器值)与cnvpos.ndx文件中的相应数值进行比较,从而决定是否停线等待。
下面是代号为PR RR2的中涂右侧2号机器人的cnvpos.ndx文件的实际内容:
Program Index
| ____ InitialWait Position for Conveyor
| |
1,2350,1650,1850,1800
2,2350,1950,1750,1800
3,1800,1800,1800,1800
第一列为程序号,对应不同的车型。
第二列是正常生产时新来的下一台车体等待换色完成的位置数据,单位是mm,比正常开始喷涂的位置2400mm提前了50mm。
后面3列是降级时等待换色完成的位置数据,分别对应站内对面的左侧第1台机器人降级、左右第2台机器人降级和左右第3台机器人降级的情况,只有清漆站有第3台机器人降级的情况。从上面的数值可以看到,降级时的位置数值比正常生产时的数值要小,表示要比正常生产时提前等待,不同的车型或者不同的降级模式下,数值可能不一样。
3.2 降级模式下的节距控制实例
上面的例子中,PR RR2机器人车型程序号为1时,在对面PR RL2机器人故障后被旁路时采用第2种降级模式,等待换色完成的位置为1850mm,比正常的2350mm要提前500mm。线速4.36m/min时,500mm的距离对应的传送带运行时间=500mm/(4360mm/60s)=6.88s,约7秒钟,就是说两台车之间需要增加节距500mm或者延时7秒钟,否则在车体连续的情况下,传送带会因后车等待前车换色清洗完成而停线。
实际降级模式也验证了这一点,在中涂左侧PR RL2机器人故障后,将其打到安全位置并旁路,开启降级模式,由于最初传送带没有降级时的节距调整功能,车身节距维持6800mm不变,导致每次换色清洗都会停线,当时换色情况也比较多,传送带频繁停止和启动很难让人满意,既对设备不利,也影响喷涂质量,还可能引起车体(滑橇)在传送带上的滑移,导致车身与机器人碰撞等更严重的问题。只好临时修改传送带入口送车滚床的送车程序,在其它条件都满足的情况下,延时一段时间再送车来增加节距,经验证,延时小于7秒时换色清洗仍会停线,7秒以上可以连续运行。
3.3 降级模式下的节距控制的改进
上述降级模式实例中增加的延时延长了每一台车的周期时间,包括不需要换色的车体,导致生产时间延长和能源浪费,这也是我们不希望的,因此考虑加以改进,实现降级时的节距自动调节功能,即换色车之间增加节距,同色车之间不增加节距,这样可以保证降级时传送带连续运行,避免不必要的停线。
要实现降级时的节距自动调节功能,需要喷涂机与传送带密切配合。在本例改进方案中,我们要求喷涂PLC向传送带PLC发送各喷涂站的降级信号、具体降级模式和需要增加的节距数值(或者对应的时间),传送带PLC需要根据各站具体降级情况,以及本台准备送入喷房的车体的颜色与上台车相比是否变化来选择适当的节距增量,最大限度减少降级模式对生产的影响。以中涂左侧PR RL2机器人旁路后的降级模式为例,中涂PLC向传送带发送站降级信号为1、发送降级模式为2、发送节距增量为500,传送带PLC收到降级信号后,就要比较本台准备送入喷房的车体的中涂颜色与上台车相比是否变化来插入适当的节距增量。同理,色漆站降级时就要比较色漆颜色是否变化,清漆站降级时就要比较清漆颜色是否变化。当换色情况不频繁时,也可以使用简化的方法增加降级时的节距,就是喷涂PLC只向传送带发送具体站降级信号,传送带PLC插入换色需要的最大节距,从本例的18台机器人的全部cnvpos.ndx文件中,查到最大节距增量为700mm,采用定时器增加节距时延时10秒即可。
4 结语
降级模式下自动调节车身节距,可以最大限度保证跟踪式喷涂线传送带的连续运行,得到降级模式下的最大产能和最好质量,特别是对颜色变化频繁的喷涂生产线更加重要,在项目前期规划和建设时要向承包商提出相关要求,并在项目实施过程中完成这项自动化功能。
(详情见《现代涂料与涂装》2018-7)
编辑推荐
最新资讯
-
全球产业链聚沪 共探双碳新路径 SNEC
2025-04-18 18:05
-
柯马签订具有约束力的协议收购 Autom
2025-04-17 13:01
-
高效协同新范式:比亚迪叉车领创智能
2025-04-17 10:04
-
埃马克德国总部迎来中国社科院工业经
2025-04-15 09:40
-
埃马克这项全新应用即将在CIMT惊艳首
2025-04-15 09:37