某车型顶盖天窗废料再利用的实施
2018-08-09 12:03:37· 来源:锻造与冲压
大量的研究资料和奇瑞公司多年的开发经验显示,在整个汽车开发过程中,冲压成本几乎占到汽车白车身成本的60%;影响冲压成本的各要素中的板材费用约占62%,即板料成本能达到汽车白车身成本的36%;整车材料利用率每提升1%,整车的材料工艺消耗将减少约6 ~ 8kg,单车成本最少也能降低35 元。冲压生产过程中材料利用率控制越来越受到汽车厂的重视。
大量的研究资料和奇瑞公司多年的开发经验显示,在整个汽车开发过程中,冲压成本几乎占到汽车白车身成本的60%;影响冲压成本的各要素中的板材费用约占62%,即板料成本能达到汽车白车身成本的36%;整车材料利用率每提升1%,整车的材料工艺消耗将减少约6 ~ 8kg,单车成本最少也能降低35 元。冲压生产过程中材料利用率控制越来越受到汽车厂的重视。
冲压材料利用率涉及面比较广,车身整体造型及分缝、产品新结构、冲压工艺、冲压模面设置、卷料的规格选择,调试阶段及生产阶段的精细化提升等都将影响材料利用率。除以上常用的技术方案以外,近些年我们也不断尝试从其他途径提升材料的利用率,例如废料的再次利用。我们通过模具改造、冲压生产线的简单改造,成功的将某车型的顶盖天窗部位的废料再利用,取得了良好的经济效益。
顶盖天窗部位废料再利用的提出
该车型顶盖有两种不同配置,一种为普通型不带天窗车型,一种为大天窗车型。目前销售的车辆中有90% 以上为大天窗车型。该天窗部位废料尺寸为1065mm×810mm,重量达到4.73kg。按照现有工艺,两次修边(相对于冲孔)得到多块尺寸相对较小的废料,直接滑落到冲压线废料道中,最后打包作为废料处理,如图1 所示。
通过优化该车型的修边模具,将该部位废料切成一整块,通过机械手端拾器将废料从模具中取出收集。收集后的废料在同一车型的尺寸较小,材料牌号接近且厚度一致的零件上使用,以实现废料的最大利用。
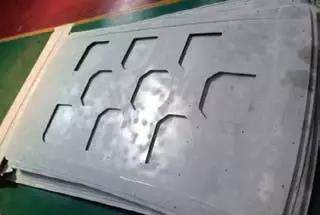
图1 原有天窗修边及废料状况
天窗废料再利用的有效实施
废料收集后的再利用
通过在同一车型中排查,确认左/ 右侧围外板后部连接板拉延序坯料尺寸为1070mm×800mm,选择此件进行废料利用,材料利用率相对较高。并经过AutoForm 分析,采用天窗部位的废料进行拉延,分析结果良好,与原有板料结果一致,如图2 所示。
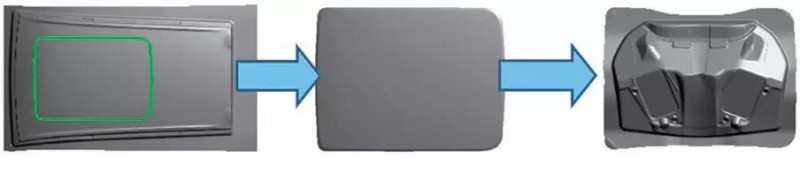
图2 天窗废料使用的制件确认
析结果良好,与原有板料结果一致,如图2 所示。
实物调试验证
为进一步确认该板料能直接用于选择制件的生产,该部位废料通过激光切割后,进行冲压验证,效果良好,如图3 所示。
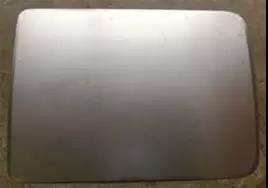
图3 废料利用调试验证
天窗废料整体修边的模具方案确认
顶盖天窗处废料整体形状为圆弧形,修边后废料会有一定程度的回弹,尺寸会略大于理论数据,导致卡料,无法通过自动化吸盘将废料从模具中取出。为了确保顶盖天窗废料能够顺利脱离刃口,必须保证冲孔后废料与刃口有一定间隙。根据翻边角度的理论测算(图4),结合模具镶块强度及模具行程等因素考虑,最终确定该废料折边后与下模刃口间隙约0.8mm。AutoForm 软件中分析,废料折边过程未发生起皱,成形过程较好。
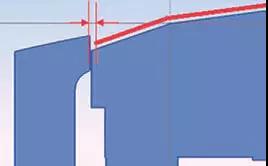
图4 废料取件避让的理论分析
模具的开发及实物体现
为保证现有车型的生产,不能在现有模具上进行改造,经过详细的经济效益分析(表1),认为重新开发一套顶盖OP20 模具也能取得较好的经济效益。经过几个月开发、调试,新开发修边模具已经替代原有OP20 模具,并对原有冲压生产的端拾器进行改造,新增废料收集机构(后期天窗废料也可使用)等,正式投入生产后,运行效果良好,废料实物为图5 所示。
表1 详细的经济效益分析
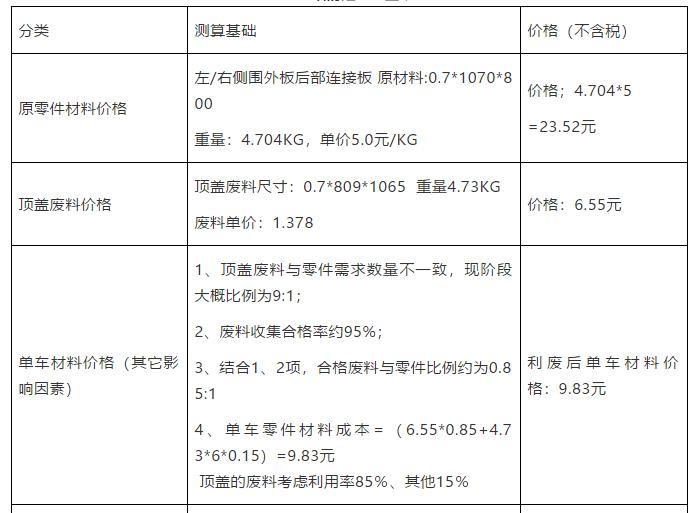
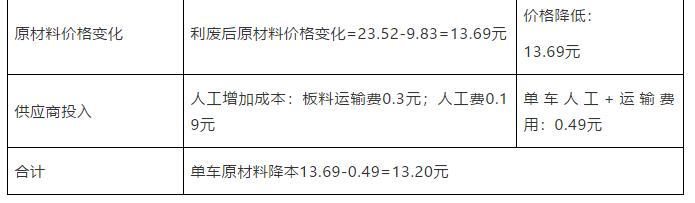
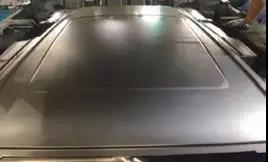
图5 废料实物情况
结束语
汽车市场的竞争日益激烈,汽车价格将很大程度的影响着消费者的选择。如何在保证质量的前提下,降低汽车的开发成本,提供更有竞争力的产品,是每一个汽车企业必须重点解决的课题。我公司通过对某车型天窗废料再利用的实施,取得了良好的经济效益,并已将此工艺标准化,在后期项目中进行推广。
冲压材料利用率涉及面比较广,车身整体造型及分缝、产品新结构、冲压工艺、冲压模面设置、卷料的规格选择,调试阶段及生产阶段的精细化提升等都将影响材料利用率。除以上常用的技术方案以外,近些年我们也不断尝试从其他途径提升材料的利用率,例如废料的再次利用。我们通过模具改造、冲压生产线的简单改造,成功的将某车型的顶盖天窗部位的废料再利用,取得了良好的经济效益。
顶盖天窗部位废料再利用的提出
该车型顶盖有两种不同配置,一种为普通型不带天窗车型,一种为大天窗车型。目前销售的车辆中有90% 以上为大天窗车型。该天窗部位废料尺寸为1065mm×810mm,重量达到4.73kg。按照现有工艺,两次修边(相对于冲孔)得到多块尺寸相对较小的废料,直接滑落到冲压线废料道中,最后打包作为废料处理,如图1 所示。
通过优化该车型的修边模具,将该部位废料切成一整块,通过机械手端拾器将废料从模具中取出收集。收集后的废料在同一车型的尺寸较小,材料牌号接近且厚度一致的零件上使用,以实现废料的最大利用。
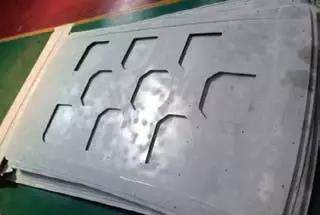
图1 原有天窗修边及废料状况
天窗废料再利用的有效实施
废料收集后的再利用
通过在同一车型中排查,确认左/ 右侧围外板后部连接板拉延序坯料尺寸为1070mm×800mm,选择此件进行废料利用,材料利用率相对较高。并经过AutoForm 分析,采用天窗部位的废料进行拉延,分析结果良好,与原有板料结果一致,如图2 所示。
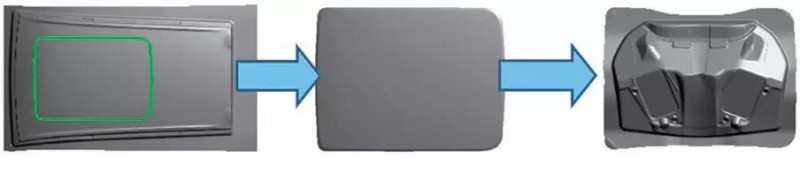
图2 天窗废料使用的制件确认
析结果良好,与原有板料结果一致,如图2 所示。
实物调试验证
为进一步确认该板料能直接用于选择制件的生产,该部位废料通过激光切割后,进行冲压验证,效果良好,如图3 所示。
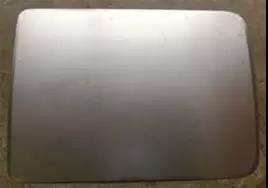
图3 废料利用调试验证
天窗废料整体修边的模具方案确认
顶盖天窗处废料整体形状为圆弧形,修边后废料会有一定程度的回弹,尺寸会略大于理论数据,导致卡料,无法通过自动化吸盘将废料从模具中取出。为了确保顶盖天窗废料能够顺利脱离刃口,必须保证冲孔后废料与刃口有一定间隙。根据翻边角度的理论测算(图4),结合模具镶块强度及模具行程等因素考虑,最终确定该废料折边后与下模刃口间隙约0.8mm。AutoForm 软件中分析,废料折边过程未发生起皱,成形过程较好。
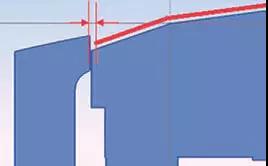
图4 废料取件避让的理论分析
模具的开发及实物体现
为保证现有车型的生产,不能在现有模具上进行改造,经过详细的经济效益分析(表1),认为重新开发一套顶盖OP20 模具也能取得较好的经济效益。经过几个月开发、调试,新开发修边模具已经替代原有OP20 模具,并对原有冲压生产的端拾器进行改造,新增废料收集机构(后期天窗废料也可使用)等,正式投入生产后,运行效果良好,废料实物为图5 所示。
表1 详细的经济效益分析
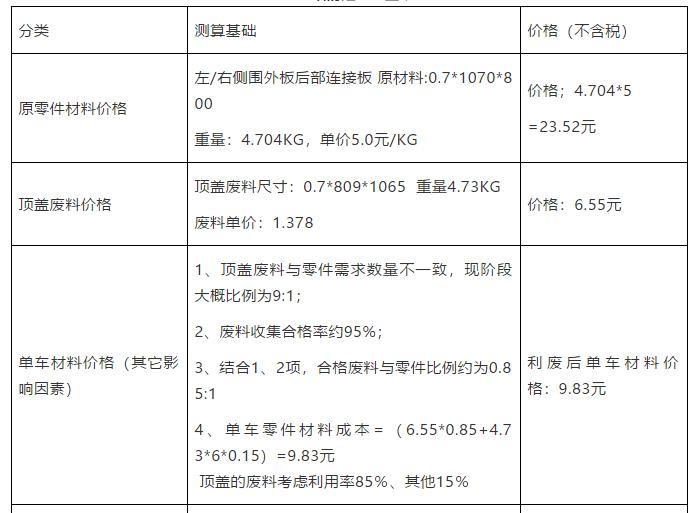
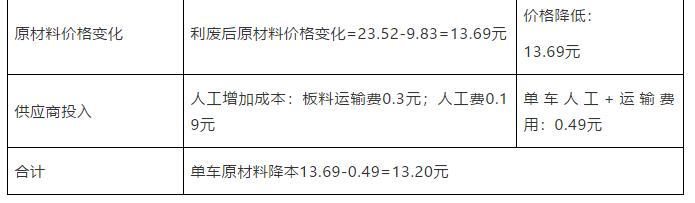
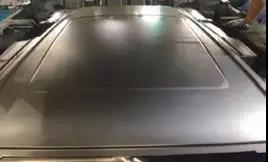
图5 废料实物情况
结束语
汽车市场的竞争日益激烈,汽车价格将很大程度的影响着消费者的选择。如何在保证质量的前提下,降低汽车的开发成本,提供更有竞争力的产品,是每一个汽车企业必须重点解决的课题。我公司通过对某车型天窗废料再利用的实施,取得了良好的经济效益,并已将此工艺标准化,在后期项目中进行推广。
举报 0
收藏 0
分享 95
-
冲压技术在电机叠片制造的应用
2024-09-06 -
车身零部件包边质量控制要点
2024-09-05 -
轻量化技术——热汽胀形工艺技术解析
2024-09-04 -
高强板车身件冲压技术
2024-09-02
最新资讯
-
全球产业链聚沪 共探双碳新路径 SNEC
2025-04-18 18:05
-
柯马签订具有约束力的协议收购 Autom
2025-04-17 13:01
-
高效协同新范式:比亚迪叉车领创智能
2025-04-17 10:04
-
埃马克德国总部迎来中国社科院工业经
2025-04-15 09:40
-
埃马克这项全新应用即将在CIMT惊艳首
2025-04-15 09:37