硬齿面齿轮精加工技术的现状与展望
2018-08-10 10:30:51· 来源:齿轮传动
硬齿面精加工在加工精度和加工效率上取得了一些进步,出现了一些新的工艺方法。本文对国内外硬齿面的滚齿、插齿、剃齿、珩齿以及磨齿的最新工艺方法及装备进行了介绍,尤其是对磨齿加工的成形法和展成法工艺现状进行了详细介绍,指出了硬齿面精加工方法的发展方向。
硬齿面精加工在加工精度和加工效率上取得了一些进步,出现了一些新的工艺方法。本文对国内外硬齿面的滚齿、插齿、剃齿、珩齿以及磨齿的最新工艺方法及装备进行了介绍,尤其是对磨齿加工的成形法和展成法工艺现状进行了详细介绍,指出了硬齿面精加工方法的发展方向。
近年来,各种硬齿面精加工在加工精度和加工效率上都取得了一些进展,同时还出现了一些新的硬齿面精加工方法。
硬齿面滚齿工艺
由于磨齿效率低、成本高,近年来,国外开始研究硬齿面滚齿工艺,采用硬质合金滚刀可以提高加工效率,目前在日本、德国等生产中已有应用。国内近年来也在积极研究硬齿面滚齿工艺,并取得了一些进展,一些工厂生产中已有应用。
北京第二机床厂和济南第一机床厂等一些厂家已采用硬齿面滚齿工艺代替粗磨齿,加工效率比锥面砂轮磨齿机约高5~6倍。硬齿面滚齿工艺要求滚齿机床刚度好、精度高,只有在切齿技术、刀具及机床等几个方面的正确配合下,使切齿过程达到最佳状态,硬齿面滚齿的精度才能达到7级。硬齿面滚齿存在的最大问题是齿形精度较低,加工精度不稳定。其主要原因是:
1)用硬质合金滚刀来加工60HRC 左右的硬齿面,刀具与工件的硬度相差很小,滚刀易磨损,直接影响齿形精度;
2)由于滚齿是一种断续切削过程,滚齿过程伴随着强迫及自激振动、力和热的冲击,常常容易造成硬质合金滚刀崩刃;
3)由于硬质合金滚刀采用负前角,而切削厚度小,工件硬度又高,使得径向切削力很大。从工艺系统分析,滚齿机的刚度虽较强,但刀杆和心轴却是2个刚性薄弱环节,径向的变形对精度影响很大。
硬齿面插齿工艺
国外有的公司将硬质合金插齿刀顶刃磨出较大的负前角,使侧刃有较大的刃倾角,形成刮削加工,也取得了初步成果。不过,要想用硬齿合金插齿刀插制6级精度齿轮是非常困难的。除了存在和硬质合金滚刀、滚齿相类似的问题外,还存在着插齿速度无法增加到与硬质合金刀具相适应的最佳切削速度,往复插齿运动造成振动、插齿机传动链精度不达标等许多问题,使之未能在生产实际中应用。
国内一些工厂在普通插齿工艺基础上,对硬齿面插齿工艺也作了一些研究。目前,可插制48HRC左右的中硬齿面7级精度齿轮,主要采取了以下措施:1)提高机床的刚度和精度,提高传动链精度;2)采用高精度插齿刀(AA 级插齿刀),严格控制刀具的安装偏心;3)提高齿坯和夹具的精度;4)选取合理的进给次数和加工进给量等。
硬齿面剃齿工艺
近年来,日本试验成功用硬质台金剃齿刀加工8级精度、硬度为60 HRC 的齿轮。为使剃齿刀能切入工件的硬齿面,除将剃齿刀上的渐开线螺旋面刃带减至最窄处外,还要把剃齿刀每齿上的刀刃减至l~2个。本来软齿面剃齿的最大优点是刀刃多,有渐开线螺旋面保持稳定啮合,使剃齿效率高,并保证精度。而硬齿合金剃齿刀在结构上的改动,削弱了剃齿的上述2个优点。此外,剃齿的特点是切削厚度很小,而硬质合金的刀刃一般是较钝的,故很难进行剃削加工;因而难于在生产中实际应用。
国内近年来也在研究硬齿面剃齿工艺,目前已能剃削48 HRC 左右的中硬齿面7 级精度齿轮,加工效率很高,其主要采取了以下措施:
1)选择剃削性能好的刀具材料做剃齿刀;
2)提高剃齿刀的制造精度,并采用修形剃齿刀或负变位剃齿刀,不仅减小或消除了剃齿齿形的中凹现象,还能剃削鼓形齿轮;
3)提高热处理前、后齿坯的加工精度,严格控制热处理淬火变形;
4)精细调整机床,提高机床刚度,选择合理的剃削用量等。
珩齿工艺
珩齿是目前高精度硬齿面齿轮加工的主要方法;但是,要把珩齿精度提高到6级,是比较困难的。目前,国内有的工厂已珩出6级精度齿轮。德国的工厂也是利用珩齿生产6级精度齿轮,采用粗、精2次滚齿,并采用修形剃齿刀剃齿,严格控制热处理变形等一系列措施,以保证珩前精度,并使用修形珩轮进行珩齿。
普通珩齿工艺采用的盘形珩轮加工效率很高,1~2 min就能加工1 个齿轮。近年来,日本提出新的珩齿方法———蜗杆珩齿工艺,推出新型蜗杆珩齿机。蜗杆珩齿的工作原理是采用蜗杆形状的珩轮对齿轮齿面进行珩齿,与珩前精度比较,可提高1~2级精度。目前,蜗杆珩齿技术在日本、美国、英国和瑞士等国已有十几项专利发表,多用于汽车变速箱齿轮的制造。国内近年来对蜗杆珩齿工艺组织攻关,进行了很多研究,已由南京第二机床厂和长江机床厂生产蜗杆珩齿机,并开始在生产中应用,精度可达到6~7级,平均生产速度为3~6min/件。一般蜗杆珩轮采用普通磨料,又分为软珩和硬珩2种蜗杆珩轮。近年来试验研究采用电镀金刚石蜗杆珩轮和电镀CBN(立方氮化硼)蜗杆珩轮的珩齿工艺。
国外近年来还发展了内啮合自由珩齿工艺,瑞士已生产出内啮合珩齿机。这种工艺采用内齿圈珩轮加工外齿轮工件,平均单件工时为1~2min,珩后精度可提高2级,一般可达6~7级。如果提高珩前精度,将能珩出更高精度的齿轮。
磨齿工艺
磨齿分为展成磨齿和成形磨齿2大类。一般说来,展成磨齿的效率较低(蜗杆砂轮磨齿除外),磨齿费用较高,机床复杂,价格昂贵,限制了其在生产中的广泛应用,仅在少数精密机械及工具行业使用。而成形磨齿具有机床简单、效率较高、成本较低等优点,但由于过去成形磨齿砂轮修整问题未得到很好解决,也妨碍了成形磨齿工艺在生产中的应用。现在世界各国都在积极研究高精度、高效率、多功能、性能稳定的新型磨齿加工方法和磨齿机。
5.1 展成磨齿
展成磨齿法又可分为单齿分度展成磨齿法和连续展成磨齿法,如图1所示。
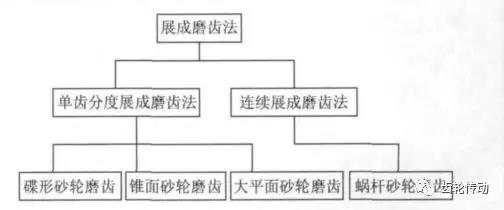
图1 展成法齿轮磨削方法分类
瑞士 Maag磨齿机采用碟形砂轮磨齿,除继续保持高精度的优势外,在结构和磨削方法上有所改进,效率有所提高。为提高加工效率,Maag 公司在磨削方法上由 HSS系列磨齿机的15°/20°的普通磨削法发展到0°磨削法,采用BC机构磨修形齿轮,形成了新的SD 系列。后来 Maag 公司在0°磨削法的基础上,又发展了K磨削法,效率又有所提高。尽管这样,Maag磨齿机的效率仍然很低,磨1 个齿轮常常要耗费几个小时,成本很高,尤其是大规格磨齿机效率更低。
锥面砂轮磨齿机传动链长,而且渐开线齿面是逐点包络出来的,影响加工精度及稳定性,单件工时一般为0.6~3h;但锥面砂轮磨齿机通用性好,在生产中应用得较广。世界上生产锥面砂轮磨齿机声誉较高的是德国的 Hofler公司和 Niles公司。这2家公司已发展了直径为3500 mm 的磨齿机系列产品。
大平面砂轮磨齿机传动链短,结构比较简单,加工精度也较高;但加工效率很低,多用来加工剃齿刀和插齿刀等齿轮刀具以及精度较高的齿轮。各国相关厂家都在生产这种磨齿机,但多年来在结构和性能上没有太大的发展。
在各种磨齿方法中,蜗杆砂轮磨齿机的效率最高,一般10多分钟就能磨1个齿轮,适于5~6级齿数>8 mm 或直径>600 mm)的加工,还有待于解决。
近年来,日本还出现了采用电镀CBN(立方氮化硼)蜗杆砂轮的数控蜗杆砂轮磨齿机,砂轮不用修整可连续加工几万个齿轮,用废后换新砂轮,加工效率很高,1 min 左右就能磨1 个齿轮,并能磨修形齿轮。目前,我国各种形式的展成磨齿机都已有生产,但产品尺寸系列还不够齐全。
5.2 成形磨齿
为了解决大批量齿轮的高效经济磨齿问题,近年来世界上许多国家(如前面提到的瑞士 Maag 公司以及德国、日本、英国、美国等)又在积极研究成形磨齿工艺。成形磨齿所达到的精度与展成磨齿相媲美,且生产率还要高好多倍(但仍低于蜗杆砂轮磨齿),强力高效磨削应用于成形磨齿,效率还将进一步提高。成形磨齿一般适于5~6级精度齿轮的批量生产,还特别适合于模数大、齿致少、宽度大的齿轮和各种修形齿轮的加工。
成形磨齿要解决的第1个问题是创造通用的成形砂轮修整器,为此近年来发表了不少这方面的专利和成果,如图2所示。国外成形磨齿机多采用靠模四杆机构修整器;但这种修整器的精度稳定性较差,靠模数量多,调整麻烦。由于准确渐开线修整器结构一般较复杂,影响精度,又发展了许多种近似渐开线修整方法。单金刚石笔修整砂轮时很难解决金刚笔磨损对修整齿形精度的影响;因此又发展了金刚滚轮修整法。由于成形金刚滚轮制造复杂、价格很贵,国外又发展了金刚砂带压轮法。近年来,国内外又研制出了数控成形砂轮修整器,采用三坐标闭环系统,以保证精度并能自动调节补偿金刚石笔磨损;但这种装置复杂、昂贵,尚未正式应用于生产。
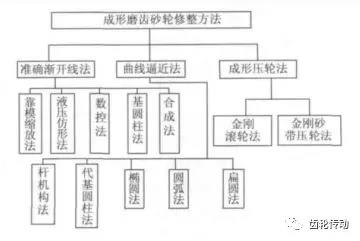
图2 成形磨齿砂轮修整方法分类
硬齿面齿轮精加工技术的未来发展
随着数控技术的出现,硬齿面齿轮的精加工设备在机床的成形运动设计方面,原有的形成齿轮渐开线轮廓的内联系传动链是通过机械机构实现的。数控技术使得机床的每个运动都加入一个伺服电动机,通过数控机床的CNC系统,向每个伺服电动机发送脉冲指令,每个伺服电动机得到指令后,通过电动机旋转带动滚珠丝杠实现机床运动,这样就消除了原有的、形成齿轮渐开线轮廓的、内联系传动链的机械机构误差,使机床运动精度得到提高。新的数控滚齿机、插齿机、剃齿机以及磨齿机将得到广泛应用。
近年来,各种硬齿面精加工在加工精度和加工效率上都取得了一些进展,同时还出现了一些新的硬齿面精加工方法。
硬齿面滚齿工艺
由于磨齿效率低、成本高,近年来,国外开始研究硬齿面滚齿工艺,采用硬质合金滚刀可以提高加工效率,目前在日本、德国等生产中已有应用。国内近年来也在积极研究硬齿面滚齿工艺,并取得了一些进展,一些工厂生产中已有应用。
北京第二机床厂和济南第一机床厂等一些厂家已采用硬齿面滚齿工艺代替粗磨齿,加工效率比锥面砂轮磨齿机约高5~6倍。硬齿面滚齿工艺要求滚齿机床刚度好、精度高,只有在切齿技术、刀具及机床等几个方面的正确配合下,使切齿过程达到最佳状态,硬齿面滚齿的精度才能达到7级。硬齿面滚齿存在的最大问题是齿形精度较低,加工精度不稳定。其主要原因是:
1)用硬质合金滚刀来加工60HRC 左右的硬齿面,刀具与工件的硬度相差很小,滚刀易磨损,直接影响齿形精度;
2)由于滚齿是一种断续切削过程,滚齿过程伴随着强迫及自激振动、力和热的冲击,常常容易造成硬质合金滚刀崩刃;
3)由于硬质合金滚刀采用负前角,而切削厚度小,工件硬度又高,使得径向切削力很大。从工艺系统分析,滚齿机的刚度虽较强,但刀杆和心轴却是2个刚性薄弱环节,径向的变形对精度影响很大。
硬齿面插齿工艺
国外有的公司将硬质合金插齿刀顶刃磨出较大的负前角,使侧刃有较大的刃倾角,形成刮削加工,也取得了初步成果。不过,要想用硬齿合金插齿刀插制6级精度齿轮是非常困难的。除了存在和硬质合金滚刀、滚齿相类似的问题外,还存在着插齿速度无法增加到与硬质合金刀具相适应的最佳切削速度,往复插齿运动造成振动、插齿机传动链精度不达标等许多问题,使之未能在生产实际中应用。
国内一些工厂在普通插齿工艺基础上,对硬齿面插齿工艺也作了一些研究。目前,可插制48HRC左右的中硬齿面7级精度齿轮,主要采取了以下措施:1)提高机床的刚度和精度,提高传动链精度;2)采用高精度插齿刀(AA 级插齿刀),严格控制刀具的安装偏心;3)提高齿坯和夹具的精度;4)选取合理的进给次数和加工进给量等。
硬齿面剃齿工艺
近年来,日本试验成功用硬质台金剃齿刀加工8级精度、硬度为60 HRC 的齿轮。为使剃齿刀能切入工件的硬齿面,除将剃齿刀上的渐开线螺旋面刃带减至最窄处外,还要把剃齿刀每齿上的刀刃减至l~2个。本来软齿面剃齿的最大优点是刀刃多,有渐开线螺旋面保持稳定啮合,使剃齿效率高,并保证精度。而硬齿合金剃齿刀在结构上的改动,削弱了剃齿的上述2个优点。此外,剃齿的特点是切削厚度很小,而硬质合金的刀刃一般是较钝的,故很难进行剃削加工;因而难于在生产中实际应用。
国内近年来也在研究硬齿面剃齿工艺,目前已能剃削48 HRC 左右的中硬齿面7 级精度齿轮,加工效率很高,其主要采取了以下措施:
1)选择剃削性能好的刀具材料做剃齿刀;
2)提高剃齿刀的制造精度,并采用修形剃齿刀或负变位剃齿刀,不仅减小或消除了剃齿齿形的中凹现象,还能剃削鼓形齿轮;
3)提高热处理前、后齿坯的加工精度,严格控制热处理淬火变形;
4)精细调整机床,提高机床刚度,选择合理的剃削用量等。
珩齿工艺
珩齿是目前高精度硬齿面齿轮加工的主要方法;但是,要把珩齿精度提高到6级,是比较困难的。目前,国内有的工厂已珩出6级精度齿轮。德国的工厂也是利用珩齿生产6级精度齿轮,采用粗、精2次滚齿,并采用修形剃齿刀剃齿,严格控制热处理变形等一系列措施,以保证珩前精度,并使用修形珩轮进行珩齿。
普通珩齿工艺采用的盘形珩轮加工效率很高,1~2 min就能加工1 个齿轮。近年来,日本提出新的珩齿方法———蜗杆珩齿工艺,推出新型蜗杆珩齿机。蜗杆珩齿的工作原理是采用蜗杆形状的珩轮对齿轮齿面进行珩齿,与珩前精度比较,可提高1~2级精度。目前,蜗杆珩齿技术在日本、美国、英国和瑞士等国已有十几项专利发表,多用于汽车变速箱齿轮的制造。国内近年来对蜗杆珩齿工艺组织攻关,进行了很多研究,已由南京第二机床厂和长江机床厂生产蜗杆珩齿机,并开始在生产中应用,精度可达到6~7级,平均生产速度为3~6min/件。一般蜗杆珩轮采用普通磨料,又分为软珩和硬珩2种蜗杆珩轮。近年来试验研究采用电镀金刚石蜗杆珩轮和电镀CBN(立方氮化硼)蜗杆珩轮的珩齿工艺。
国外近年来还发展了内啮合自由珩齿工艺,瑞士已生产出内啮合珩齿机。这种工艺采用内齿圈珩轮加工外齿轮工件,平均单件工时为1~2min,珩后精度可提高2级,一般可达6~7级。如果提高珩前精度,将能珩出更高精度的齿轮。
磨齿工艺
磨齿分为展成磨齿和成形磨齿2大类。一般说来,展成磨齿的效率较低(蜗杆砂轮磨齿除外),磨齿费用较高,机床复杂,价格昂贵,限制了其在生产中的广泛应用,仅在少数精密机械及工具行业使用。而成形磨齿具有机床简单、效率较高、成本较低等优点,但由于过去成形磨齿砂轮修整问题未得到很好解决,也妨碍了成形磨齿工艺在生产中的应用。现在世界各国都在积极研究高精度、高效率、多功能、性能稳定的新型磨齿加工方法和磨齿机。
5.1 展成磨齿
展成磨齿法又可分为单齿分度展成磨齿法和连续展成磨齿法,如图1所示。
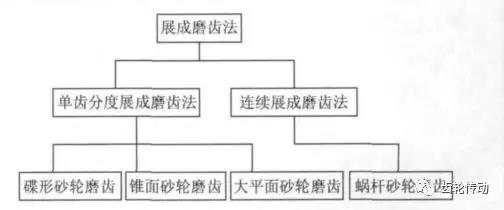
图1 展成法齿轮磨削方法分类
瑞士 Maag磨齿机采用碟形砂轮磨齿,除继续保持高精度的优势外,在结构和磨削方法上有所改进,效率有所提高。为提高加工效率,Maag 公司在磨削方法上由 HSS系列磨齿机的15°/20°的普通磨削法发展到0°磨削法,采用BC机构磨修形齿轮,形成了新的SD 系列。后来 Maag 公司在0°磨削法的基础上,又发展了K磨削法,效率又有所提高。尽管这样,Maag磨齿机的效率仍然很低,磨1 个齿轮常常要耗费几个小时,成本很高,尤其是大规格磨齿机效率更低。
锥面砂轮磨齿机传动链长,而且渐开线齿面是逐点包络出来的,影响加工精度及稳定性,单件工时一般为0.6~3h;但锥面砂轮磨齿机通用性好,在生产中应用得较广。世界上生产锥面砂轮磨齿机声誉较高的是德国的 Hofler公司和 Niles公司。这2家公司已发展了直径为3500 mm 的磨齿机系列产品。
大平面砂轮磨齿机传动链短,结构比较简单,加工精度也较高;但加工效率很低,多用来加工剃齿刀和插齿刀等齿轮刀具以及精度较高的齿轮。各国相关厂家都在生产这种磨齿机,但多年来在结构和性能上没有太大的发展。
在各种磨齿方法中,蜗杆砂轮磨齿机的效率最高,一般10多分钟就能磨1个齿轮,适于5~6级齿数>8 mm 或直径>600 mm)的加工,还有待于解决。
近年来,日本还出现了采用电镀CBN(立方氮化硼)蜗杆砂轮的数控蜗杆砂轮磨齿机,砂轮不用修整可连续加工几万个齿轮,用废后换新砂轮,加工效率很高,1 min 左右就能磨1 个齿轮,并能磨修形齿轮。目前,我国各种形式的展成磨齿机都已有生产,但产品尺寸系列还不够齐全。
5.2 成形磨齿
为了解决大批量齿轮的高效经济磨齿问题,近年来世界上许多国家(如前面提到的瑞士 Maag 公司以及德国、日本、英国、美国等)又在积极研究成形磨齿工艺。成形磨齿所达到的精度与展成磨齿相媲美,且生产率还要高好多倍(但仍低于蜗杆砂轮磨齿),强力高效磨削应用于成形磨齿,效率还将进一步提高。成形磨齿一般适于5~6级精度齿轮的批量生产,还特别适合于模数大、齿致少、宽度大的齿轮和各种修形齿轮的加工。
成形磨齿要解决的第1个问题是创造通用的成形砂轮修整器,为此近年来发表了不少这方面的专利和成果,如图2所示。国外成形磨齿机多采用靠模四杆机构修整器;但这种修整器的精度稳定性较差,靠模数量多,调整麻烦。由于准确渐开线修整器结构一般较复杂,影响精度,又发展了许多种近似渐开线修整方法。单金刚石笔修整砂轮时很难解决金刚笔磨损对修整齿形精度的影响;因此又发展了金刚滚轮修整法。由于成形金刚滚轮制造复杂、价格很贵,国外又发展了金刚砂带压轮法。近年来,国内外又研制出了数控成形砂轮修整器,采用三坐标闭环系统,以保证精度并能自动调节补偿金刚石笔磨损;但这种装置复杂、昂贵,尚未正式应用于生产。
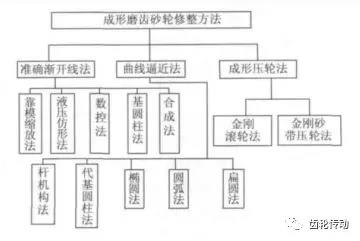
图2 成形磨齿砂轮修整方法分类
硬齿面齿轮精加工技术的未来发展
随着数控技术的出现,硬齿面齿轮的精加工设备在机床的成形运动设计方面,原有的形成齿轮渐开线轮廓的内联系传动链是通过机械机构实现的。数控技术使得机床的每个运动都加入一个伺服电动机,通过数控机床的CNC系统,向每个伺服电动机发送脉冲指令,每个伺服电动机得到指令后,通过电动机旋转带动滚珠丝杠实现机床运动,这样就消除了原有的、形成齿轮渐开线轮廓的、内联系传动链的机械机构误差,使机床运动精度得到提高。新的数控滚齿机、插齿机、剃齿机以及磨齿机将得到广泛应用。
- 下一篇:康耐视Vidi套件 让汽车“艳压群芳”的AI解决方案
- 上一篇:瓦尔特涡轮罩精密刀具
编辑推荐
最新资讯
-
全球产业链聚沪 共探双碳新路径 SNEC
2025-04-18 18:05
-
柯马签订具有约束力的协议收购 Autom
2025-04-17 13:01
-
高效协同新范式:比亚迪叉车领创智能
2025-04-17 10:04
-
埃马克德国总部迎来中国社科院工业经
2025-04-15 09:40
-
埃马克这项全新应用即将在CIMT惊艳首
2025-04-15 09:37