汽车冲压件工艺参数优化及回弹控制
2018-08-14 16:30:58· 来源:锻压技术
针对汽车冲压件的回弹问题, 研究了某汽车后地板零件的回弹控制问题。首先借助数值模拟软件Auto Form建立汽车后地板零件冲压成形的全流程的有限元模型, 然后采用工艺参数优化和回弹补偿相结合来共同控制该零件的回弹。工艺参数优化借助了Auto Form的西格玛优化模块, 优化目标为最小回弹量, 优化得到最优组的压边力为798 k N, 摩擦系数为0.14。然后采用回弹补偿策略对拉延工序的模具进行回弹补偿, 当回弹补偿循环迭代2次后, 零件的回弹满足尺寸公差要求。最后进行了模具加工和试模验证。实验结果表明将工
摘要
针对汽车冲压件的回弹问题, 研究了某汽车后地板零件的回弹控制问题。首先借助数值模拟软件Auto Form建立汽车后地板零件冲压成形的全流程的有限元模型, 然后采用工艺参数优化和回弹补偿相结合来共同控制该零件的回弹。工艺参数优化借助了Auto Form的西格玛优化模块, 优化目标为最小回弹量, 优化得到最优组的压边力为798 k N, 摩擦系数为0.14。然后采用回弹补偿策略对拉延工序的模具进行回弹补偿, 当回弹补偿循环迭代2次后, 零件的回弹满足尺寸公差要求。最后进行了模具加工和试模验证。实验结果表明将工艺参数优化和回弹补偿相结合的方法能够有效地控制冲压零件的回弹。
一、有限元模型
汽车后地板是汽车生产中的典型薄板类零件, 该零件的生产批量大、尺寸精度要求高、模具开发成本高。有限元软件可以在模具开发前期来预测零件的成形缺陷和回弹量, 此外有限元软件还可以根据预测的回弹量来对模具进行回弹补偿, 从而有效降低模具开发成本。
以某汽车后地板为研究对象, 该零件的成形工艺流程为拉延、切边、冲孔、翻边。在板料冲压成形分析软件Auto Form中建立汽车后地板的全流程的有限元模型如图1所示, 模型中包括拉延工序、切边工序和翻边工序。拉延工序采用倒装的单动拉延工艺, 拉延工序成形工具包括凹模、压边圈和凸模。翻边工序的成形工具有托料器、压料器和翻边工具。
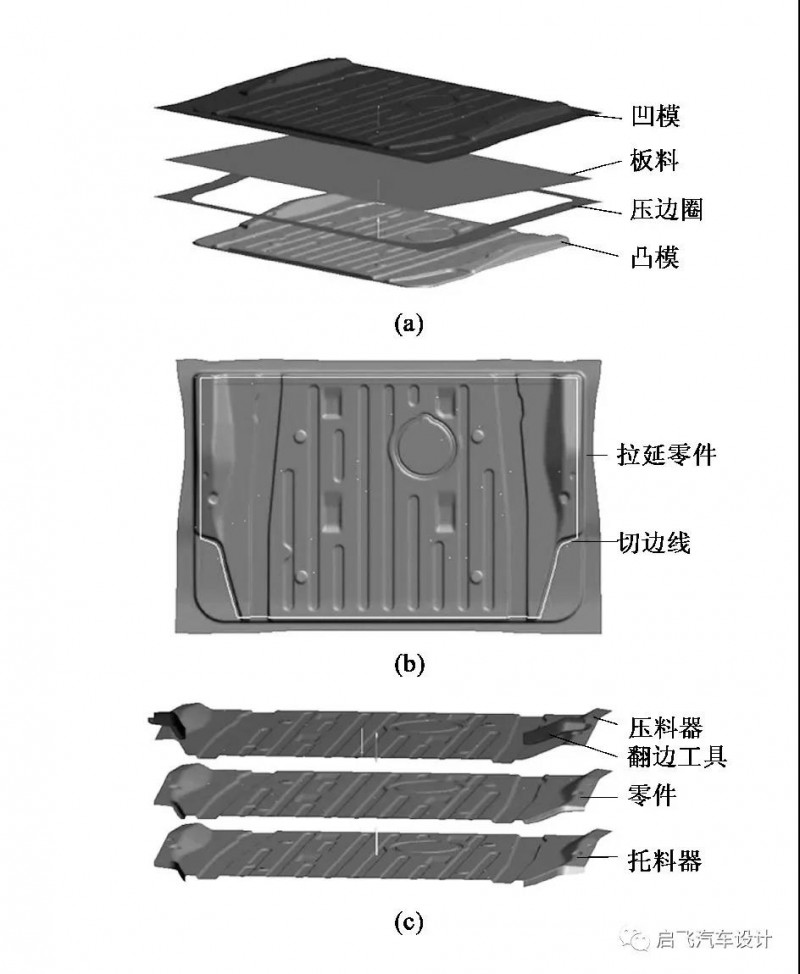
图1 汽车后地板有限元模型 (a) 拉延工序 (b) 切边工序 (c) 翻边工序
该零件的材料为宝钢材料DC03钢, 材料厚度为0.7 mm。表1为数值模拟中材料的力学性能。Auto Form中有两种单元类型:膜单元和壳单元, 为了提高数值模拟的计算精度, 在有限元模型中选择单元类型为弹塑性壳单元。成形模拟中板料一般设置为5层, 为了准确预测零件成形后的回弹量, 在模拟中设置板料为11层。
表1 DC03钢的材料力学性能
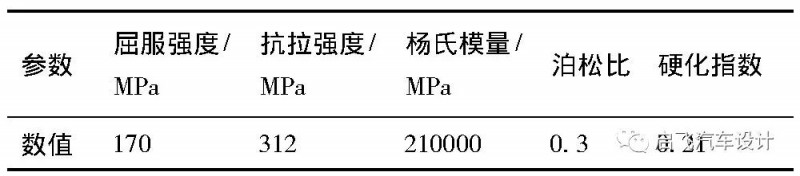
二、工艺参数优化
零件回弹的影响因素较多, 包括材料参数和成形工艺参数。而当零件的材料确定后, 材料参数已确定, 不能进行更改, 因此, 为了降低成形后零件的回弹量, 对汽车后地板的成形工艺参数进行优化, 确定回弹量较小的工参数。
在对汽车冲压件的回弹控制中, 得出影响零件回弹的主要工艺参数有压边力、模具间隙、摩擦系数。对于汽车后地板模具开发中, 最后凸凹要完全闭合, 因此, 在对汽车后地板的工艺参数优化中主要考虑了成形过程中的压边力和摩擦系数。
工艺参数优化借助Auto Form的西格玛优化模块 (RE:Performance Analysis Design) , 该模块用于冲压工艺参数优化。优化分析的设计变量见表2。优化分析中优化目标为零件的回弹量, 进行30组模拟, 得到的模拟结果见图2, 由图2可知, 第24组为回弹最小的模拟组, 因此, 将该模拟组的参数作为最优参数组合, 即最优组的压边力为798k N, 摩擦系数为0.14。优化后的零件的回弹分布如图3所示, 图3中采用椭圆圈出的区域A~D为该零件回弹较大的4个区域, 其中零件的最大回弹量为1.78 mm。
表2 优化分析的设计变量
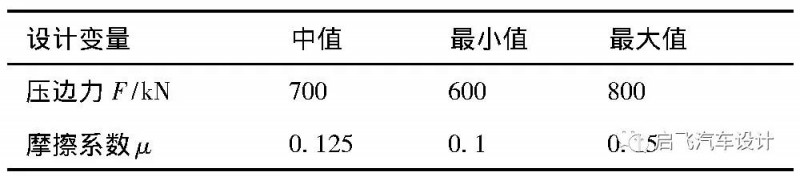
三、回弹补偿
采用工艺参数优化只能减小零件的回弹, 但不能完全控制零件的回弹量。因此, 接下来采用回弹补偿方法来进一步控制回弹。对拉延工序的模具进行补偿, 回弹补偿方法如图4所示, 将拉延模模面分为3个区域, 切边线以内区域定义为直接补偿区域, 压料面部分定义为固定补偿区域, 压料面和切边线之间区域定义为过渡补偿区域。采用Auto Form软件进行回弹补偿, 当回弹补偿循环迭代2次后, 成形后零件的回弹满足尺寸公差要求。第1次回弹补偿后, 零件的回弹相对于未补偿时回弹量有所降低, 图3中4个椭圆区域A~D的最大回弹量分别为1.28, 1.14, 1.21和0.96 mm。第2次回弹补偿后的零件的回弹分布如图5所示, 4个椭圆区域A~D的最大回弹量分别为0.68, 0.63, 0.62和0.45mm。图6为回弹补偿前后的模面, 可以看出零件的型面补偿主要在零件区域和过渡补偿区域, 压料面在补偿前后未发生变化。
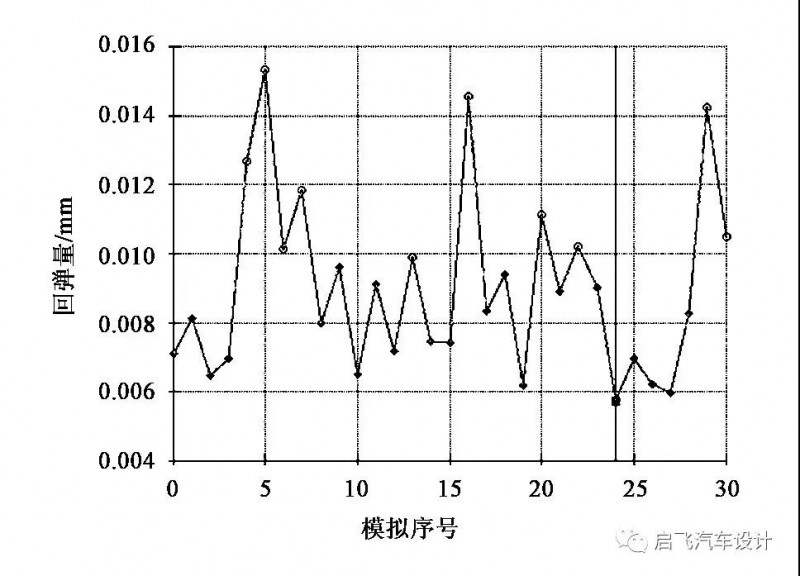
图2 优化分析的回弹结果
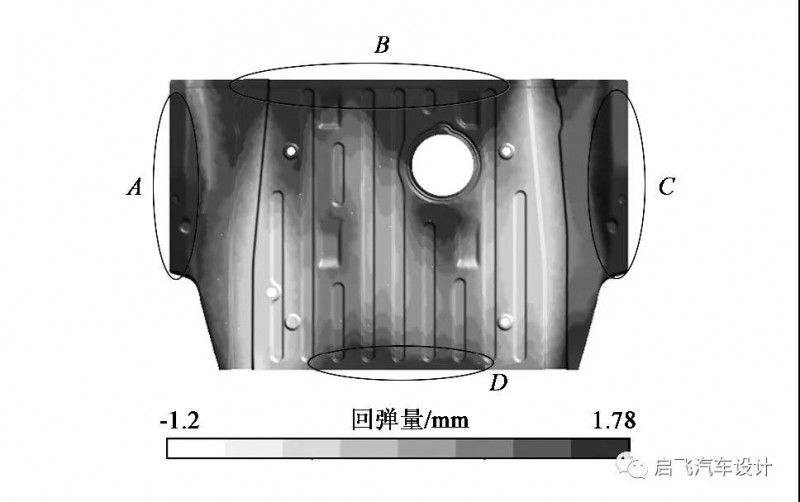
图3 优化后的零件的回弹分布
四、实验验证
为验证数值模拟结果进行了模具加工和试模实验, 得到试模零件如图7所示。由图7可知, 该零件成形充分, 无成形缺陷。采用模具检具对零件进行检查, 重点测量图3所示的4个椭圆区域, 得到椭圆区域A~D的最大回弹量分别为1.20, 0.96, 1.14和0.66 mm。由于零件的允许最大偏差为±0.7 mm, 因此, 还需要对超出区域进行试模修改, 通过再一次对模具型面进行修改加工, 最终得到零件的回弹偏差满足零件尺寸要求。虽然本文提出的方法没有达到一次控制零件的回弹, 但相对于传统回弹补偿方法, 能缩短试模调试时间, 降低模具成本。
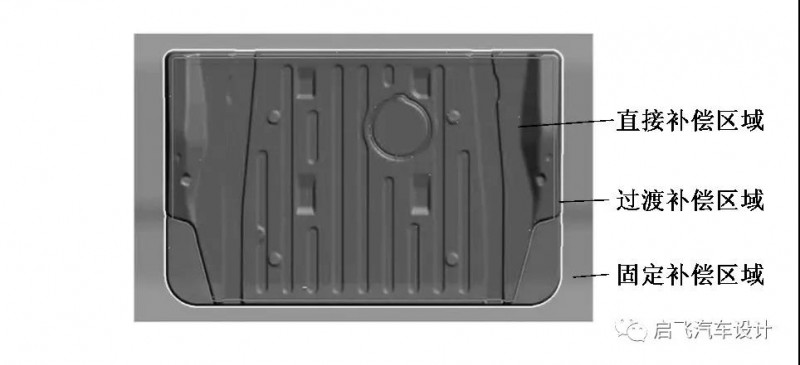
图4 回弹补偿策略
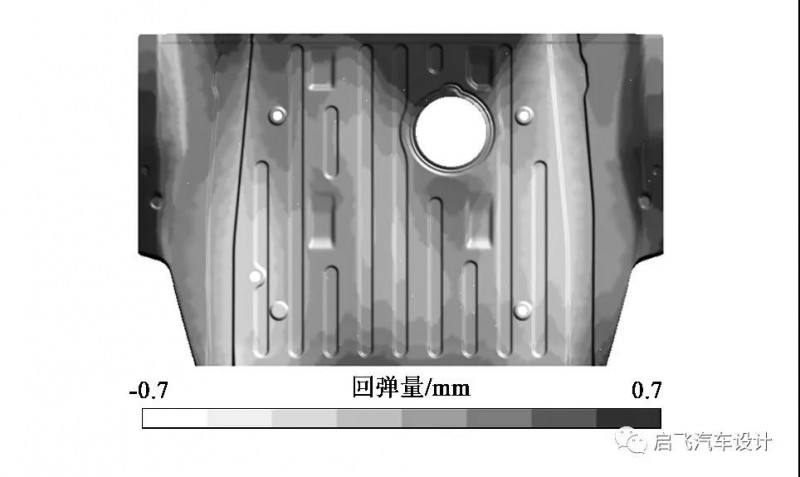
图5 第2次回弹补偿后的零件的回弹分布
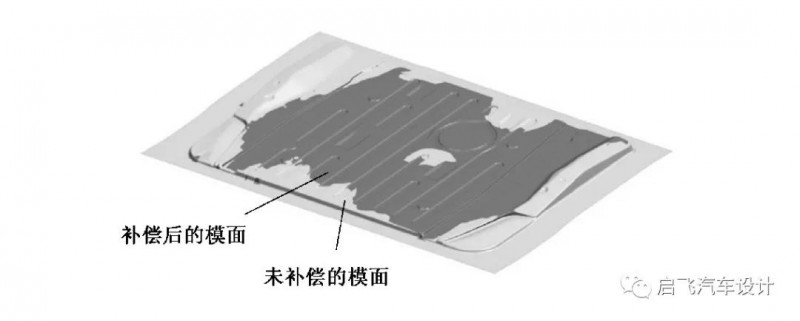
图6 回弹补偿前后的模面
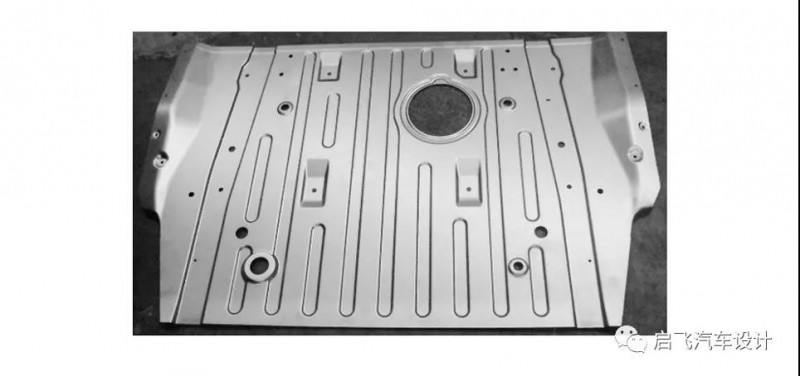
图7 试模零件
五、结论
(1) 针对汽车冲压件的回弹问题, 借助数值模拟软件Auto Form建立汽车后地板零件冲压成形的全流程的有限元模型, 然后采用工艺参数优化和回弹补偿来控制该零件的回弹。
(2) 工艺参数优化中得到最优组的压边力为798 k N, 摩擦系数为0.14。采用回弹补偿策略对拉延模具进行回弹补偿, 当回弹补偿循环迭代两次后成形后零件的回弹满足尺寸公差要求。
(3) 实验结果表明将工艺参数优化和回弹补偿相结合的方法能够有效地控制零件的回弹, 缩短试模调试时间, 降低模具成本。
作者:苟春梅; 吴民; 董静; 孙华伟
针对汽车冲压件的回弹问题, 研究了某汽车后地板零件的回弹控制问题。首先借助数值模拟软件Auto Form建立汽车后地板零件冲压成形的全流程的有限元模型, 然后采用工艺参数优化和回弹补偿相结合来共同控制该零件的回弹。工艺参数优化借助了Auto Form的西格玛优化模块, 优化目标为最小回弹量, 优化得到最优组的压边力为798 k N, 摩擦系数为0.14。然后采用回弹补偿策略对拉延工序的模具进行回弹补偿, 当回弹补偿循环迭代2次后, 零件的回弹满足尺寸公差要求。最后进行了模具加工和试模验证。实验结果表明将工艺参数优化和回弹补偿相结合的方法能够有效地控制冲压零件的回弹。
一、有限元模型
汽车后地板是汽车生产中的典型薄板类零件, 该零件的生产批量大、尺寸精度要求高、模具开发成本高。有限元软件可以在模具开发前期来预测零件的成形缺陷和回弹量, 此外有限元软件还可以根据预测的回弹量来对模具进行回弹补偿, 从而有效降低模具开发成本。
以某汽车后地板为研究对象, 该零件的成形工艺流程为拉延、切边、冲孔、翻边。在板料冲压成形分析软件Auto Form中建立汽车后地板的全流程的有限元模型如图1所示, 模型中包括拉延工序、切边工序和翻边工序。拉延工序采用倒装的单动拉延工艺, 拉延工序成形工具包括凹模、压边圈和凸模。翻边工序的成形工具有托料器、压料器和翻边工具。
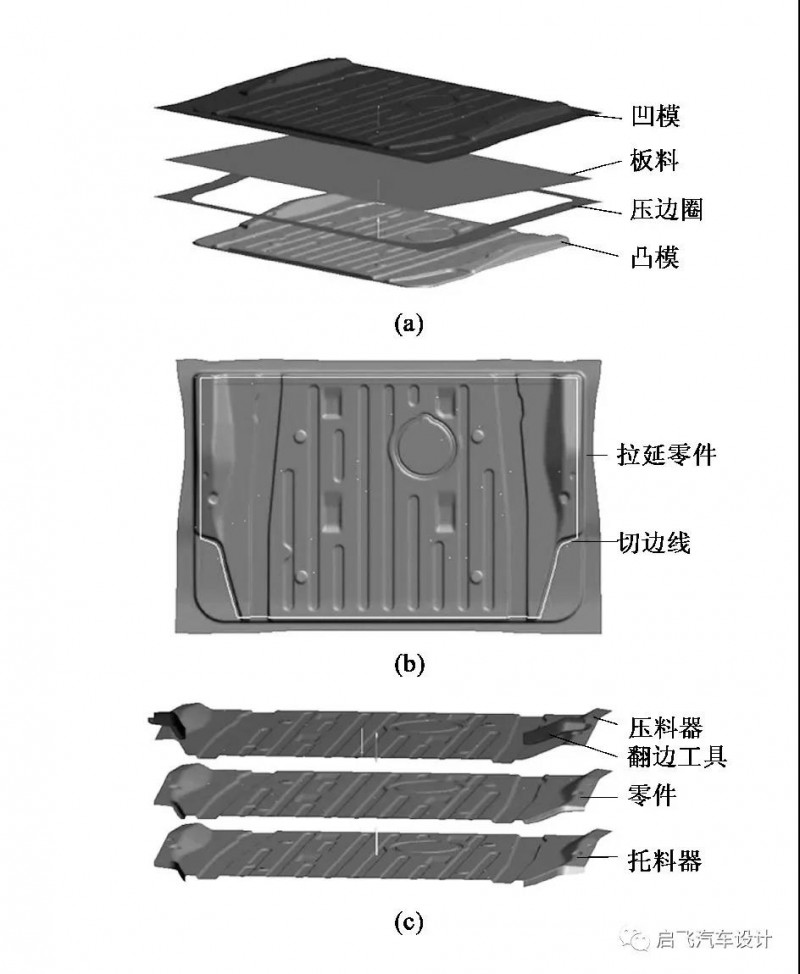
图1 汽车后地板有限元模型 (a) 拉延工序 (b) 切边工序 (c) 翻边工序
该零件的材料为宝钢材料DC03钢, 材料厚度为0.7 mm。表1为数值模拟中材料的力学性能。Auto Form中有两种单元类型:膜单元和壳单元, 为了提高数值模拟的计算精度, 在有限元模型中选择单元类型为弹塑性壳单元。成形模拟中板料一般设置为5层, 为了准确预测零件成形后的回弹量, 在模拟中设置板料为11层。
表1 DC03钢的材料力学性能
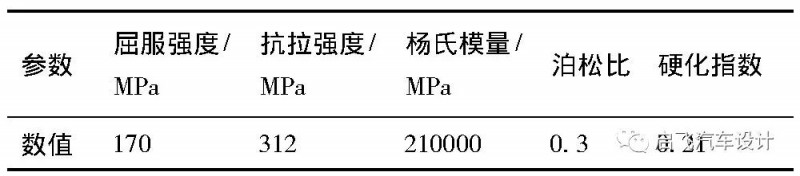
二、工艺参数优化
零件回弹的影响因素较多, 包括材料参数和成形工艺参数。而当零件的材料确定后, 材料参数已确定, 不能进行更改, 因此, 为了降低成形后零件的回弹量, 对汽车后地板的成形工艺参数进行优化, 确定回弹量较小的工参数。
在对汽车冲压件的回弹控制中, 得出影响零件回弹的主要工艺参数有压边力、模具间隙、摩擦系数。对于汽车后地板模具开发中, 最后凸凹要完全闭合, 因此, 在对汽车后地板的工艺参数优化中主要考虑了成形过程中的压边力和摩擦系数。
工艺参数优化借助Auto Form的西格玛优化模块 (RE:Performance Analysis Design) , 该模块用于冲压工艺参数优化。优化分析的设计变量见表2。优化分析中优化目标为零件的回弹量, 进行30组模拟, 得到的模拟结果见图2, 由图2可知, 第24组为回弹最小的模拟组, 因此, 将该模拟组的参数作为最优参数组合, 即最优组的压边力为798k N, 摩擦系数为0.14。优化后的零件的回弹分布如图3所示, 图3中采用椭圆圈出的区域A~D为该零件回弹较大的4个区域, 其中零件的最大回弹量为1.78 mm。
表2 优化分析的设计变量
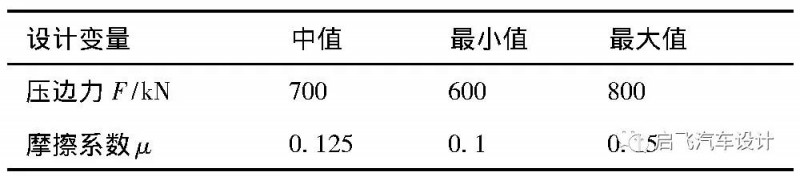
三、回弹补偿
采用工艺参数优化只能减小零件的回弹, 但不能完全控制零件的回弹量。因此, 接下来采用回弹补偿方法来进一步控制回弹。对拉延工序的模具进行补偿, 回弹补偿方法如图4所示, 将拉延模模面分为3个区域, 切边线以内区域定义为直接补偿区域, 压料面部分定义为固定补偿区域, 压料面和切边线之间区域定义为过渡补偿区域。采用Auto Form软件进行回弹补偿, 当回弹补偿循环迭代2次后, 成形后零件的回弹满足尺寸公差要求。第1次回弹补偿后, 零件的回弹相对于未补偿时回弹量有所降低, 图3中4个椭圆区域A~D的最大回弹量分别为1.28, 1.14, 1.21和0.96 mm。第2次回弹补偿后的零件的回弹分布如图5所示, 4个椭圆区域A~D的最大回弹量分别为0.68, 0.63, 0.62和0.45mm。图6为回弹补偿前后的模面, 可以看出零件的型面补偿主要在零件区域和过渡补偿区域, 压料面在补偿前后未发生变化。
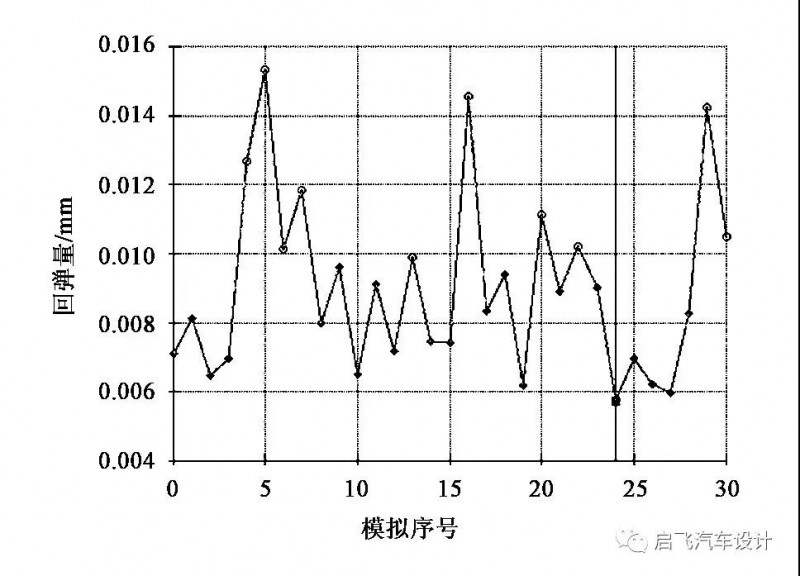
图2 优化分析的回弹结果
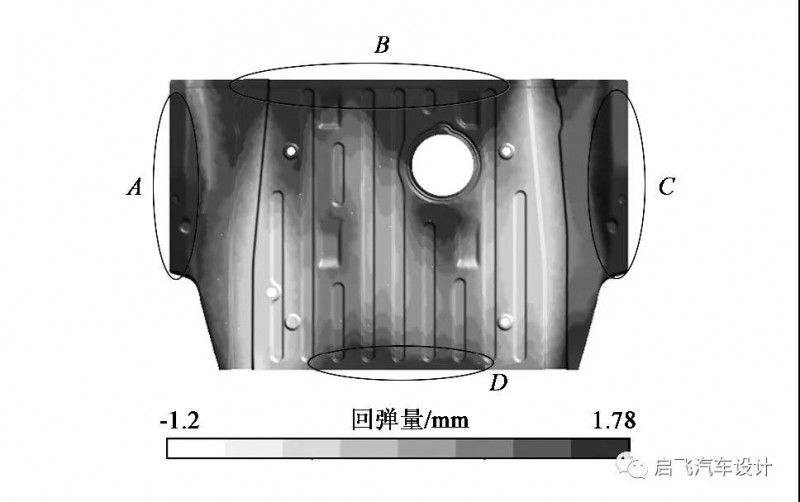
图3 优化后的零件的回弹分布
四、实验验证
为验证数值模拟结果进行了模具加工和试模实验, 得到试模零件如图7所示。由图7可知, 该零件成形充分, 无成形缺陷。采用模具检具对零件进行检查, 重点测量图3所示的4个椭圆区域, 得到椭圆区域A~D的最大回弹量分别为1.20, 0.96, 1.14和0.66 mm。由于零件的允许最大偏差为±0.7 mm, 因此, 还需要对超出区域进行试模修改, 通过再一次对模具型面进行修改加工, 最终得到零件的回弹偏差满足零件尺寸要求。虽然本文提出的方法没有达到一次控制零件的回弹, 但相对于传统回弹补偿方法, 能缩短试模调试时间, 降低模具成本。
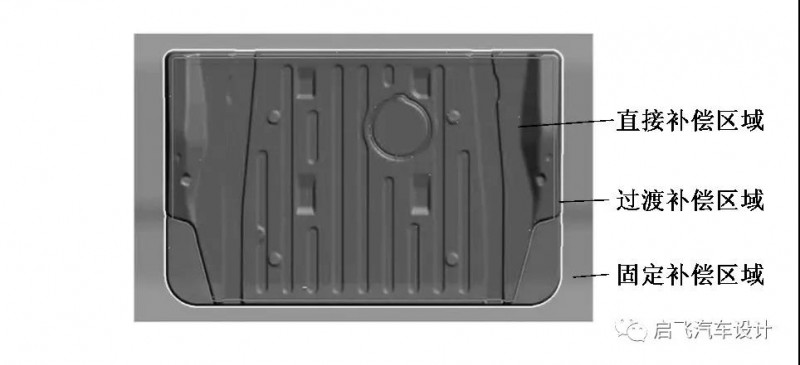
图4 回弹补偿策略
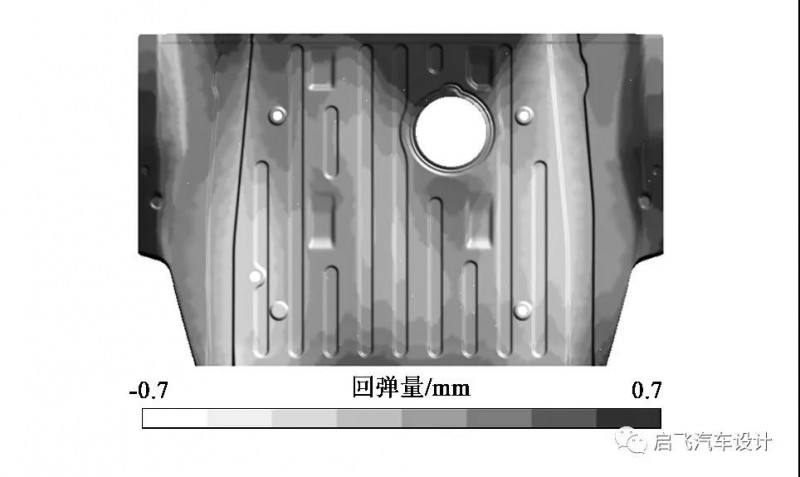
图5 第2次回弹补偿后的零件的回弹分布
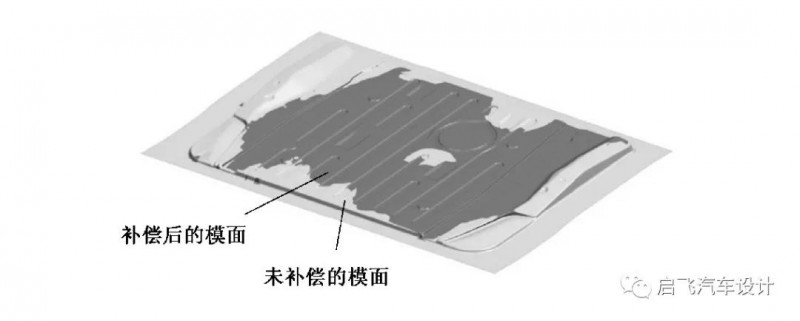
图6 回弹补偿前后的模面
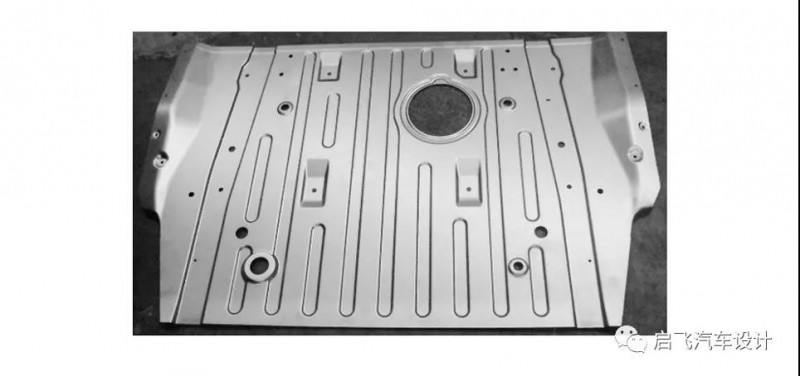
图7 试模零件
五、结论
(1) 针对汽车冲压件的回弹问题, 借助数值模拟软件Auto Form建立汽车后地板零件冲压成形的全流程的有限元模型, 然后采用工艺参数优化和回弹补偿来控制该零件的回弹。
(2) 工艺参数优化中得到最优组的压边力为798 k N, 摩擦系数为0.14。采用回弹补偿策略对拉延模具进行回弹补偿, 当回弹补偿循环迭代两次后成形后零件的回弹满足尺寸公差要求。
(3) 实验结果表明将工艺参数优化和回弹补偿相结合的方法能够有效地控制零件的回弹, 缩短试模调试时间, 降低模具成本。
作者:苟春梅; 吴民; 董静; 孙华伟
最新资讯
-
全球产业链聚沪 共探双碳新路径 SNEC
2025-04-18 18:05
-
柯马签订具有约束力的协议收购 Autom
2025-04-17 13:01
-
高效协同新范式:比亚迪叉车领创智能
2025-04-17 10:04
-
埃马克德国总部迎来中国社科院工业经
2025-04-15 09:40
-
埃马克这项全新应用即将在CIMT惊艳首
2025-04-15 09:37