汽车轻量化关键技术的发展现状及前景
2018-08-20 11:36:37· 来源:锻造与冲压
随着社会的快速发展,汽车保有量越来越多,给人们出行带来方便快捷。目前,节能、环保、安全和智能都成为汽车发展的新动向。与此同时,能源和环境是当今世界面临的两大问题,两者都与汽车产业发展息息相关,制造出“低能耗”、“低排放”甚至“零排放”的汽车是汽车行业及政府等部门都需要思考的问题。
随着社会的快速发展,汽车保有量越来越多,给人们出行带来方便快捷。目前,节能、环保、安全和智能都成为汽车发展的新动向。与此同时,能源和环境是当今世界面临的两大问题,两者都与汽车产业发展息息相关,制造出“低能耗”、“低排放”甚至“零排放”的汽车是汽车行业及政府等部门都需要思考的问题。
在采用相同动力系统和传动系统的前提下,乘用车的整车质量每减少10%,燃油消耗就可降低6%~8%。巴斯夫公司统计结果表明,汽车每减重100kg,每百公里油耗可降低0.3~0.6L、二氧化碳排放可减少5g/km。相较于汽车的动力系统和传动系统的技术改革,轻量化是降低能耗、减少排放的最为有效的措施之一。在《中国制造2025》中关于汽车发展的整体规划中也强调了“轻量化仍然是重中之重”,“轻量化”已然成为国家的重要战略,越来越多的研究机构和汽车行业将其研究工作的重点放在汽车轻量化上。
汽车轻量化实现的途径
汽车轻量化即在汽车保证其基本的使用性能要求、安全性要求和其成本控制要求的前提下,从结构、材料、工艺等方面,应用新设计、新材料、新技术来实现对汽车整体的减重,以完成汽车向“低能耗”、“低排放”的转变。
目前,实现汽车轻量化主要有三种途径:⑴结构优化,使部件薄壁化、中空化、小型化或复合化;⑵新材料的使用,如高强度钢、铝、镁合金及一些非金属材料的使用;⑶工艺的改进,主要包括成形技术和连接技术。
轻量化结构设计
从车身结构方面实现轻量化,主要有整体车身的拓扑优化设计、尺寸形状再优化。拓扑优化为基于经验目标函数的宏观优化,尺寸形状再优化和材料布局优化则为局部的调整细化。
拓扑优化设计是在给定的空间范围内,通过不停地迭代,重新规划材料的分布和连接方式,将车身整体中的冗余部分去掉,使部分零部件薄壁化、中空化,完成宏观层面的拓扑优化。拓扑优化是数学运算方法和有限元分析的有效结合。
尺寸形状优化是在确定了车身结构参数和材料分布的前提下展开的,主要对各个桁架结构进行横截面积、几何尺寸以及节点位置寻求最优解,在达到保证基本刚度要求的前提下车身重量最小。尺寸优化是建立在数学模型之上得到的最优解,可作为拓扑优化的进一步完善和提高。
轻量化材料的使用
轻质新材料的应用是汽车实现轻量化的关键。为实现轻量化,世界各大汽车生产商和材料生产厂家一直致力于轻量化材料的研发,轻量化材料应用的多少已经成为衡量汽车生产技术和新材料开发水平的重要标准之一。目前用于汽车轻量化的新材料主要分为金属材料和非金属材料。
金属材料
金属材料主要是高强度钢和轻质合金。使用高强钢、铝合金、镁合金,车体重量可分别减轻15%~25%、40%~50%和55%~60%。目前,高强度钢主要被应用于汽车结构件、安全件、前后保险杠等部位;铝合金主要应用在车身结构材料的替换上;镁合金主要应用在零部件上,其中包括壳体类与支架类零部件。
高强度钢具有强度高、质量轻、成本低等特点,有助于汽车的轻量化,而且能够提高安全性。所以,汽车用高强度钢已成为颇具竞争性的轻量化材料。就目前的工业发展状况来看,车辆的主要部分如悬架、底盘和车身结构需要高强度钢的应用较多。这些部位的高强度钢,大多是在原有材料的基础上,添加不同成分的合金,从而提高了合金钢的强度和韧性。
铝及铝合金是目前应用较为成熟的轻量化金属材料,其优势为低密度、高轻度、高弹性、高抗冲击性能、易着色等。在当前汽车制造中,已大量的使用在汽车轮毂、动力系统及悬架系统等零部件中,近年来奥迪、捷豹路虎、福特等都使用了全铝式的车身结构,铝合金已经成为了一种比较理想的轻量化材料,未来随着成形技术和连接技术的发展,铝合金的使用会越来越广泛。
镁及镁合金具有密度低、质量轻、比强度优于铝合金和钢等优势,但由于其高温疲劳性能较差和抗蠕变能力弱,限制了其在汽车上的应用,目前主要应用在壳体类和支架类零件上,如仪表盘、变速箱体、转向支架、刹车支架等。我国镁含量储备大,但是从镁合金的生产、成形等方面都需要加大研究投入,将其转化为我国的产业优势。

图1 奥迪A8全铝车身
非金属材料
随着汽车轻量化进程的飞速发展,非金属制品的应用范围也在不断扩大,其中使用最为广泛的是塑料制品,碳纤维作为新型材料也逐步进入了汽车产业中。
塑料的应用已经从内饰扩展到零件和构件上,“以塑代钢”已经成为一种趋势。国外很多汽车产业发达地区已经将塑料制品的用量作为衡量汽车发展的重要指标。
碳纤维复合材料是目前最主要的车用复合材料,具有密度小、耐腐蚀、比强度和比刚度高等特点,主要应用在汽车的结构件上,如汽车车身、底盘等,能在保证强度和刚度的前提下,大量减轻汽车重量。但碳纤维的生产成本高是制约其在汽车工业应用和推广的一个主要原因。目前,碳纤维复合材料主要应用于一些小批量生产的高档轿车和赛车中。
轻量化工艺
为了实现全面减重的目的,在结构优化设计和新材料使用的情况下,仍需要研究开发更先进的生产制造工艺,以满足新结构和新材料的需求。轻量化工艺主要是新材料的零部件在生产过程中的连接技术和成形技术。当前应用较为广泛的有板材锁铆连接、粉末注射成形和内高压成形等。
锁铆连接技术
传统的板材连接方式如点焊,表面前处理过程复杂、生产成本较高、生产效率较低,无法满足轻量化车身对板材连接的要求。而锁铆连接技术在连接轻质材料如铝合金、镁合金等材料上具有很大优势,在连接异种材质或表面有镀层的板料时,其优势更加显著。锁铆连接在连接前无需预冲孔、工艺步骤简单、生产效率高,在轻量化车身制造上具有广阔的发展前景,在汽车车身连接中占据很重要的地位。
锁铆连接是将铆钉在外力的作用下,穿透第一层材料,并在底层材料中进行流动和延展形成一个互相镶嵌的塑性变形过程,具有较高的抗拉强度和抗剪强度。目前锁铆连接技术在汽车行业的发展主要受限于汽车行业用的相关锁铆连接设备的发展水平较低。
粉末注射成形
粉末注射成形是传统粉末冶金工艺与现代塑料注射成形工艺相结合的一项新型近净成形技术。其可以得到致密度高、力学性能良好、表面粗糙度小的零件;同时能够大量制备具有高性能的复杂形状零件;生产效率较高,可以有效地降低成本,加速汽车轻量化发展的步伐,具有巨大的技术和经济优势。目前已被大量应用在汽车轻量化上,主要包括汽车动力传输零件、涡轮增压器、燃油喷油器、安全气囊传感器嵌入件、压力传感器、电动门锁组合零件等。
内高压成形
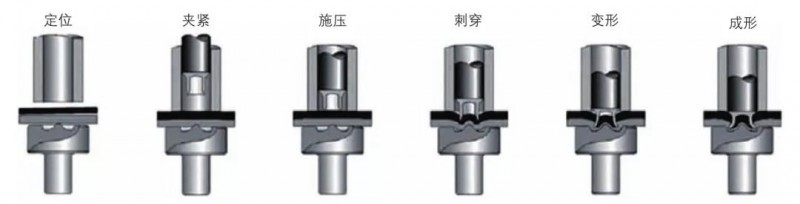
图2 锁铆连接的工艺过程
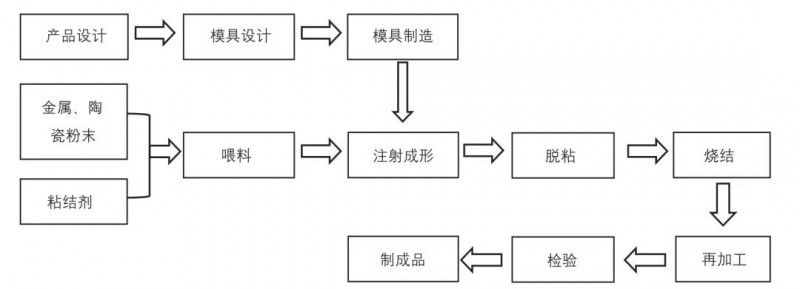
图3 粉末注射成形工艺流程
内高压成形又称充液成形、液压成形,是始于20世纪初的一种软模成形技术。该工艺尤其适用于形状复杂、尺寸多变、外观质量要求高、批量不大的大型板材零件的生产,使复杂形状板材零件的生产简单化、柔性化,实现零件的快速制造,并且大幅度降低模具费用。
根据原材料形状的不同可分成两类,即板材和管材。板材液压成形主要是车身的覆盖件;管材液压成形主要应用于汽车复杂异形截面的管件零件,如曲轴、凸轮轴、排气管道、支架梁等。
日本丰田在20世纪90年代初已建立了2条以3000t设备为核心的充液拉深生产线,专门生产高档车的翼子板,并进行模具开发;Amino2002年成立北美分公司,并建立了以3000t设备为核心的充液拉深成形生产线,专门研制开发铝合金车身覆盖件充液拉深成形技术及模具,以减少零件连接数量,满足多品种、小批量、个性化车型对整体覆盖件成形的需求,提升汽车品质;德国Schuler公司除了生产充液拉深设备外,还给主机厂和零部件厂提供批量生产用模具。而我国目前轿车车身铝合金充液拉深零件模具开发还处于空白,这成为牵制铝合金在汽车工业应用的另一关键因素。
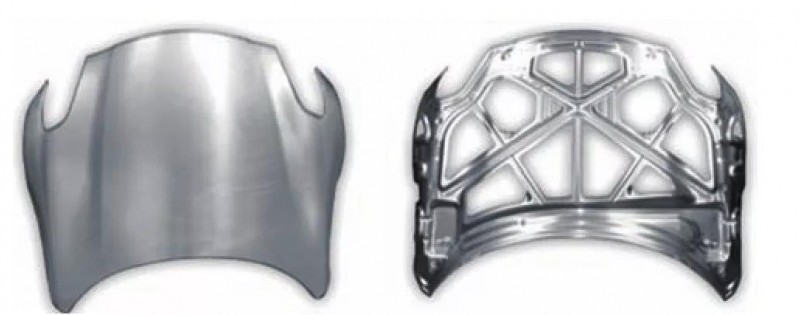
图4 内高压板材成形示例
结束语
汽车工业作为我国经济发展的重要支柱产业之一,其发展势头不容小觑,面临当前世界能源和环境的危机,汽车轻量化已然成为汽车行业可持续发展的必经之路。现阶段我国轻量化技术的应用与国际先进水平尚有差距,轻量化结构设计、新材料的使用以及新工艺的研发,三者之间息息相关,互相制约,综合平衡发展才能促进整个轻量化的进展。
在采用相同动力系统和传动系统的前提下,乘用车的整车质量每减少10%,燃油消耗就可降低6%~8%。巴斯夫公司统计结果表明,汽车每减重100kg,每百公里油耗可降低0.3~0.6L、二氧化碳排放可减少5g/km。相较于汽车的动力系统和传动系统的技术改革,轻量化是降低能耗、减少排放的最为有效的措施之一。在《中国制造2025》中关于汽车发展的整体规划中也强调了“轻量化仍然是重中之重”,“轻量化”已然成为国家的重要战略,越来越多的研究机构和汽车行业将其研究工作的重点放在汽车轻量化上。
汽车轻量化实现的途径
汽车轻量化即在汽车保证其基本的使用性能要求、安全性要求和其成本控制要求的前提下,从结构、材料、工艺等方面,应用新设计、新材料、新技术来实现对汽车整体的减重,以完成汽车向“低能耗”、“低排放”的转变。
目前,实现汽车轻量化主要有三种途径:⑴结构优化,使部件薄壁化、中空化、小型化或复合化;⑵新材料的使用,如高强度钢、铝、镁合金及一些非金属材料的使用;⑶工艺的改进,主要包括成形技术和连接技术。
轻量化结构设计
从车身结构方面实现轻量化,主要有整体车身的拓扑优化设计、尺寸形状再优化。拓扑优化为基于经验目标函数的宏观优化,尺寸形状再优化和材料布局优化则为局部的调整细化。
拓扑优化设计是在给定的空间范围内,通过不停地迭代,重新规划材料的分布和连接方式,将车身整体中的冗余部分去掉,使部分零部件薄壁化、中空化,完成宏观层面的拓扑优化。拓扑优化是数学运算方法和有限元分析的有效结合。
尺寸形状优化是在确定了车身结构参数和材料分布的前提下展开的,主要对各个桁架结构进行横截面积、几何尺寸以及节点位置寻求最优解,在达到保证基本刚度要求的前提下车身重量最小。尺寸优化是建立在数学模型之上得到的最优解,可作为拓扑优化的进一步完善和提高。
轻量化材料的使用
轻质新材料的应用是汽车实现轻量化的关键。为实现轻量化,世界各大汽车生产商和材料生产厂家一直致力于轻量化材料的研发,轻量化材料应用的多少已经成为衡量汽车生产技术和新材料开发水平的重要标准之一。目前用于汽车轻量化的新材料主要分为金属材料和非金属材料。
金属材料
金属材料主要是高强度钢和轻质合金。使用高强钢、铝合金、镁合金,车体重量可分别减轻15%~25%、40%~50%和55%~60%。目前,高强度钢主要被应用于汽车结构件、安全件、前后保险杠等部位;铝合金主要应用在车身结构材料的替换上;镁合金主要应用在零部件上,其中包括壳体类与支架类零部件。
高强度钢具有强度高、质量轻、成本低等特点,有助于汽车的轻量化,而且能够提高安全性。所以,汽车用高强度钢已成为颇具竞争性的轻量化材料。就目前的工业发展状况来看,车辆的主要部分如悬架、底盘和车身结构需要高强度钢的应用较多。这些部位的高强度钢,大多是在原有材料的基础上,添加不同成分的合金,从而提高了合金钢的强度和韧性。
铝及铝合金是目前应用较为成熟的轻量化金属材料,其优势为低密度、高轻度、高弹性、高抗冲击性能、易着色等。在当前汽车制造中,已大量的使用在汽车轮毂、动力系统及悬架系统等零部件中,近年来奥迪、捷豹路虎、福特等都使用了全铝式的车身结构,铝合金已经成为了一种比较理想的轻量化材料,未来随着成形技术和连接技术的发展,铝合金的使用会越来越广泛。
镁及镁合金具有密度低、质量轻、比强度优于铝合金和钢等优势,但由于其高温疲劳性能较差和抗蠕变能力弱,限制了其在汽车上的应用,目前主要应用在壳体类和支架类零件上,如仪表盘、变速箱体、转向支架、刹车支架等。我国镁含量储备大,但是从镁合金的生产、成形等方面都需要加大研究投入,将其转化为我国的产业优势。

图1 奥迪A8全铝车身
非金属材料
随着汽车轻量化进程的飞速发展,非金属制品的应用范围也在不断扩大,其中使用最为广泛的是塑料制品,碳纤维作为新型材料也逐步进入了汽车产业中。
塑料的应用已经从内饰扩展到零件和构件上,“以塑代钢”已经成为一种趋势。国外很多汽车产业发达地区已经将塑料制品的用量作为衡量汽车发展的重要指标。
碳纤维复合材料是目前最主要的车用复合材料,具有密度小、耐腐蚀、比强度和比刚度高等特点,主要应用在汽车的结构件上,如汽车车身、底盘等,能在保证强度和刚度的前提下,大量减轻汽车重量。但碳纤维的生产成本高是制约其在汽车工业应用和推广的一个主要原因。目前,碳纤维复合材料主要应用于一些小批量生产的高档轿车和赛车中。
轻量化工艺
为了实现全面减重的目的,在结构优化设计和新材料使用的情况下,仍需要研究开发更先进的生产制造工艺,以满足新结构和新材料的需求。轻量化工艺主要是新材料的零部件在生产过程中的连接技术和成形技术。当前应用较为广泛的有板材锁铆连接、粉末注射成形和内高压成形等。
锁铆连接技术
传统的板材连接方式如点焊,表面前处理过程复杂、生产成本较高、生产效率较低,无法满足轻量化车身对板材连接的要求。而锁铆连接技术在连接轻质材料如铝合金、镁合金等材料上具有很大优势,在连接异种材质或表面有镀层的板料时,其优势更加显著。锁铆连接在连接前无需预冲孔、工艺步骤简单、生产效率高,在轻量化车身制造上具有广阔的发展前景,在汽车车身连接中占据很重要的地位。
锁铆连接是将铆钉在外力的作用下,穿透第一层材料,并在底层材料中进行流动和延展形成一个互相镶嵌的塑性变形过程,具有较高的抗拉强度和抗剪强度。目前锁铆连接技术在汽车行业的发展主要受限于汽车行业用的相关锁铆连接设备的发展水平较低。
粉末注射成形
粉末注射成形是传统粉末冶金工艺与现代塑料注射成形工艺相结合的一项新型近净成形技术。其可以得到致密度高、力学性能良好、表面粗糙度小的零件;同时能够大量制备具有高性能的复杂形状零件;生产效率较高,可以有效地降低成本,加速汽车轻量化发展的步伐,具有巨大的技术和经济优势。目前已被大量应用在汽车轻量化上,主要包括汽车动力传输零件、涡轮增压器、燃油喷油器、安全气囊传感器嵌入件、压力传感器、电动门锁组合零件等。
内高压成形
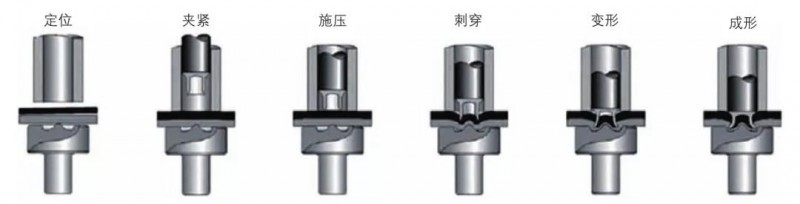
图2 锁铆连接的工艺过程
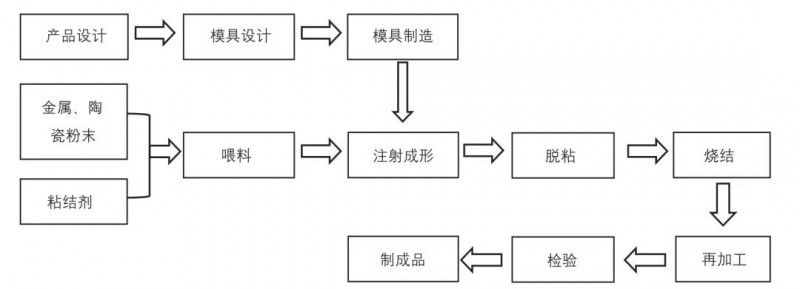
图3 粉末注射成形工艺流程
内高压成形又称充液成形、液压成形,是始于20世纪初的一种软模成形技术。该工艺尤其适用于形状复杂、尺寸多变、外观质量要求高、批量不大的大型板材零件的生产,使复杂形状板材零件的生产简单化、柔性化,实现零件的快速制造,并且大幅度降低模具费用。
根据原材料形状的不同可分成两类,即板材和管材。板材液压成形主要是车身的覆盖件;管材液压成形主要应用于汽车复杂异形截面的管件零件,如曲轴、凸轮轴、排气管道、支架梁等。
日本丰田在20世纪90年代初已建立了2条以3000t设备为核心的充液拉深生产线,专门生产高档车的翼子板,并进行模具开发;Amino2002年成立北美分公司,并建立了以3000t设备为核心的充液拉深成形生产线,专门研制开发铝合金车身覆盖件充液拉深成形技术及模具,以减少零件连接数量,满足多品种、小批量、个性化车型对整体覆盖件成形的需求,提升汽车品质;德国Schuler公司除了生产充液拉深设备外,还给主机厂和零部件厂提供批量生产用模具。而我国目前轿车车身铝合金充液拉深零件模具开发还处于空白,这成为牵制铝合金在汽车工业应用的另一关键因素。
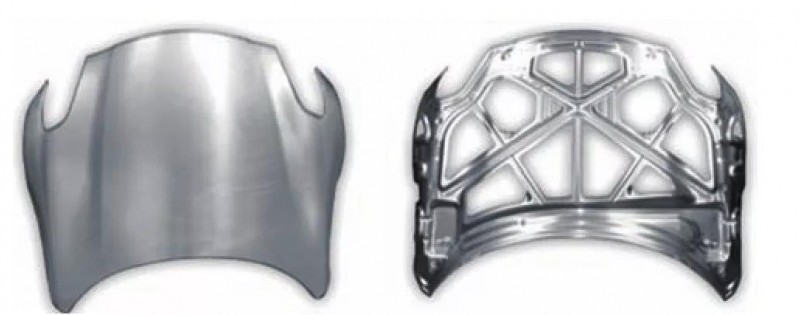
图4 内高压板材成形示例
结束语
汽车工业作为我国经济发展的重要支柱产业之一,其发展势头不容小觑,面临当前世界能源和环境的危机,汽车轻量化已然成为汽车行业可持续发展的必经之路。现阶段我国轻量化技术的应用与国际先进水平尚有差距,轻量化结构设计、新材料的使用以及新工艺的研发,三者之间息息相关,互相制约,综合平衡发展才能促进整个轻量化的进展。
- 下一篇:汽车冲压模具开发过程及管控探析
- 上一篇:测量柔性支架的搭建方法
编辑推荐
最新资讯
-
全球产业链聚沪 共探双碳新路径 SNEC
2025-04-18 18:05
-
柯马签订具有约束力的协议收购 Autom
2025-04-17 13:01
-
高效协同新范式:比亚迪叉车领创智能
2025-04-17 10:04
-
埃马克德国总部迎来中国社科院工业经
2025-04-15 09:40
-
埃马克这项全新应用即将在CIMT惊艳首
2025-04-15 09:37