齿轨轮深层渗碳工艺
2018-08-22 14:24:41·
我公司近几年为了提高齿轨轮(见图1)和驱动轮的耐磨性,其渗层深度已由四五年前的2.5~3mm增至3~4mm,经过近几年的应用其效果是明显的,齿轨轮的耐磨性有了很大的提高。但对一些大机组特别是一些地质条件较差的矿井仍然存在齿轨轮耐磨性差的问题,严重影响了我公司在采煤机用户中的声誉。为了进一步提高我公司齿轨轮的耐磨性能,提升我公司采煤机的技术水平,使采煤机齿轨轮不耐磨问题,不再成为影响我公司声誉的因素,从而有效地提高我公司的订货量及经济效益,我们结合现有设备,通过反复试验及工艺改进,最终确定齿轨轮渗碳深度达到
作者:田林、闫雪侠、朱科、张宽,西安煤矿机械有限公司
李治宝,陕西德仕汽车部件(集团)有限责任公司
来源:《金属加工(热加工)》杂志
我公司近几年为了提高齿轨轮(见图1)和驱动轮的耐磨性,其渗层深度已由四五年前的2.5~3mm增至3~4mm,经过近几年的应用其效果是明显的,齿轨轮的耐磨性有了很大的提高。但对一些大机组特别是一些地质条件较差的矿井仍然存在齿轨轮耐磨性差的问题,严重影响了我公司在采煤机用户中的声誉。为了进一步提高我公司齿轨轮的耐磨性能,提升我公司采煤机的技术水平,使采煤机齿轨轮不耐磨问题,不再成为影响我公司声誉的因素,从而有效地提高我公司的订货量及经济效益,我们结合现有设备,通过反复试验及工艺改进,最终确定齿轨轮渗碳深度达到6mm以上的热处理工艺方法。
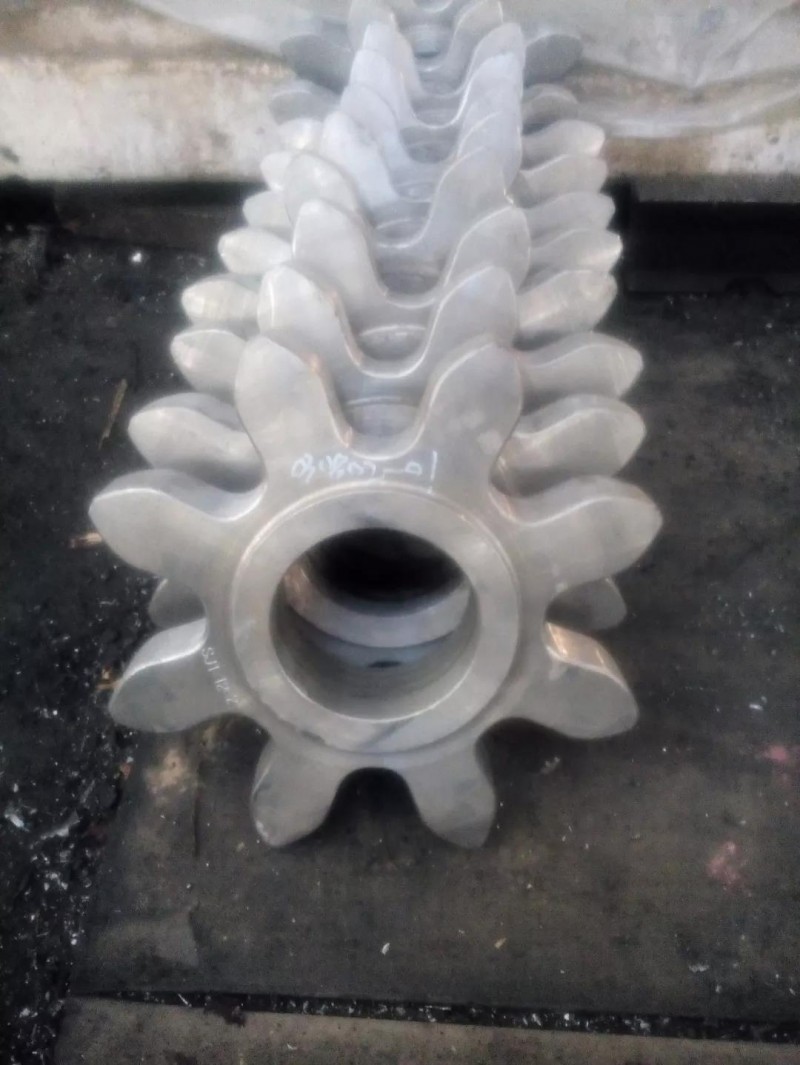
图1 齿轨轮
1.选择试验样本
根据产品C0N040802-01齿轨轮,齿宽68mm,材料为18Cr2Ni4WA,要求齿面渗碳,有效硬化层深度6~7mm,根据此产品的尺寸及精度确定用Φ68mm的棒料进行渗碳试验,材料为18Cr2Ni4WA,具体图样如图2所示。
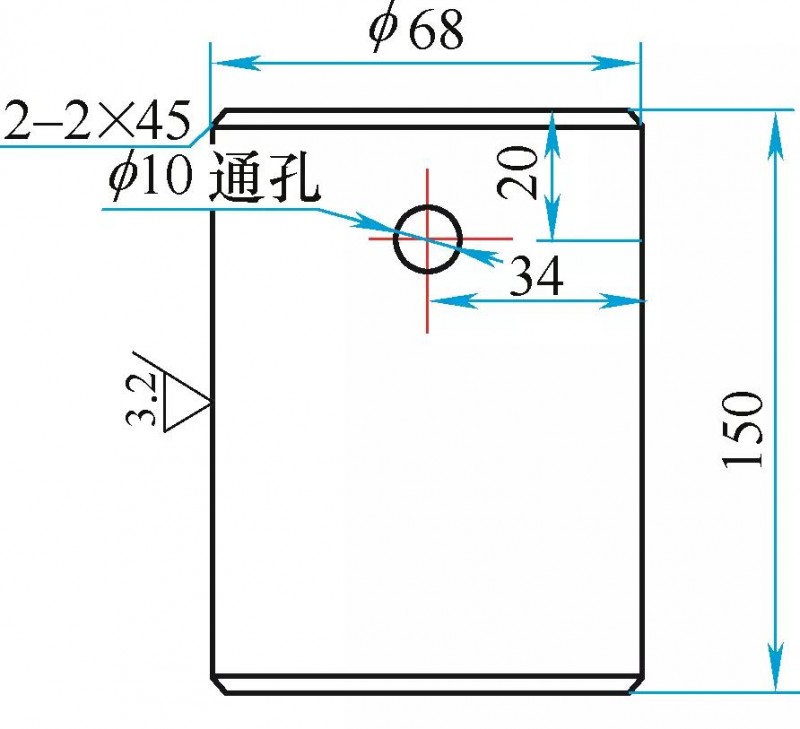
图 2
2.确定工艺路线
为了达到和产品相同的效果,渗碳前采用与高端齿轨轮相同的工艺路线,路线如下:锻造成Φ80mm左右的棒料→930℃正火+670℃高温回火→加工成图2的尺寸及精度→渗碳试验+3次高温回火→取20mm厚、¼圆的金相试样→检测渗碳层深度和碳化物级别。
3.拟定试验方案
现有热处理设备都比较老旧,加热时间过长对设备损坏比较严重,所以我们根据现有设备情况及生产条件,制定出两种试验方案:第一种是三次短时间渗碳;第二种是一次长时间渗碳。
(1)第一种方案
试棒随渗碳层深度3~4mm的产品同炉进行三次渗碳处理。为了检验每次的渗碳层深度,在第一次渗碳时放3根试棒,渗碳完成时取出1根试棒并进行标记,其余2根再进行第二次渗碳,第二次渗碳完成后再取出1根并进行标记,剩下1根进行第三次渗碳并进行标记。3次渗碳完成后的试样进行3次高温回火处理,然后加工出金相试样并进行金相检测。这种方案我们进行了两组试验。三次渗碳工艺参数相同,如表1所示。
表 1

(2)第二种方案
一次长时间渗碳。用一根试棒随产品12100090140齿轨轮一起装炉进行渗碳,渗碳完成后进行3次回火。由于时间原因这种方案我们只进行了一次试验。工艺参数如表2所示。
表 2

4.试验结果
试验中我们将Φ68mm试验用试棒与生产中Φ20mm随炉试样同时装炉,并对渗碳检验结果进行对比。
(1)第一种方案试验结果
第一种方案第一组渗碳完成后取样检验结果如表3所示。
表 3
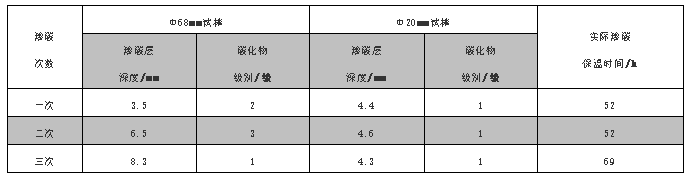
第一种方案第二组渗碳试验完成后取样检验结果如表4所示。
表 4
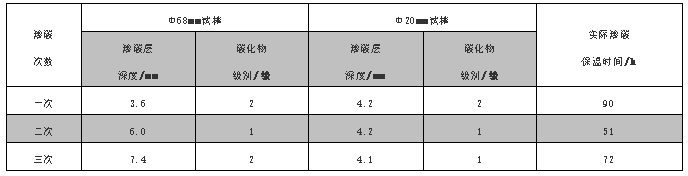
(2)第二种方案试验结果
第二种方案渗碳完成后取样检验结果如表5所示。
表 5

5.结语
本次深层渗碳试验采用两种方案,一种为一次长时间渗碳;一种为2~3次3~4mm短时间渗碳。对试验结果进行分析可得出以下结论:在现有设备条件下,使用三次3~4mm渗碳可以实现深渗层渗碳,经两次3~4mm渗碳基本上可以达到6mm渗层,三次可达到7~8mm渗层,而且碳化物可控制在4级以下。
李治宝,陕西德仕汽车部件(集团)有限责任公司
来源:《金属加工(热加工)》杂志
我公司近几年为了提高齿轨轮(见图1)和驱动轮的耐磨性,其渗层深度已由四五年前的2.5~3mm增至3~4mm,经过近几年的应用其效果是明显的,齿轨轮的耐磨性有了很大的提高。但对一些大机组特别是一些地质条件较差的矿井仍然存在齿轨轮耐磨性差的问题,严重影响了我公司在采煤机用户中的声誉。为了进一步提高我公司齿轨轮的耐磨性能,提升我公司采煤机的技术水平,使采煤机齿轨轮不耐磨问题,不再成为影响我公司声誉的因素,从而有效地提高我公司的订货量及经济效益,我们结合现有设备,通过反复试验及工艺改进,最终确定齿轨轮渗碳深度达到6mm以上的热处理工艺方法。
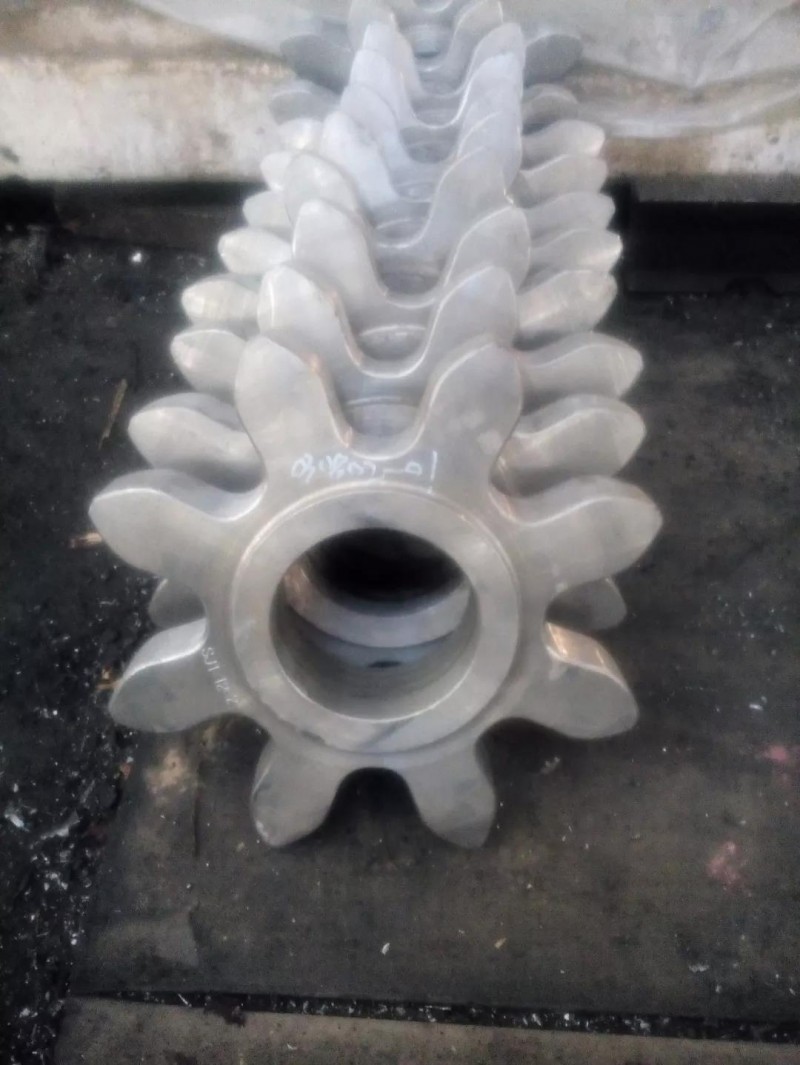
图1 齿轨轮
1.选择试验样本
根据产品C0N040802-01齿轨轮,齿宽68mm,材料为18Cr2Ni4WA,要求齿面渗碳,有效硬化层深度6~7mm,根据此产品的尺寸及精度确定用Φ68mm的棒料进行渗碳试验,材料为18Cr2Ni4WA,具体图样如图2所示。
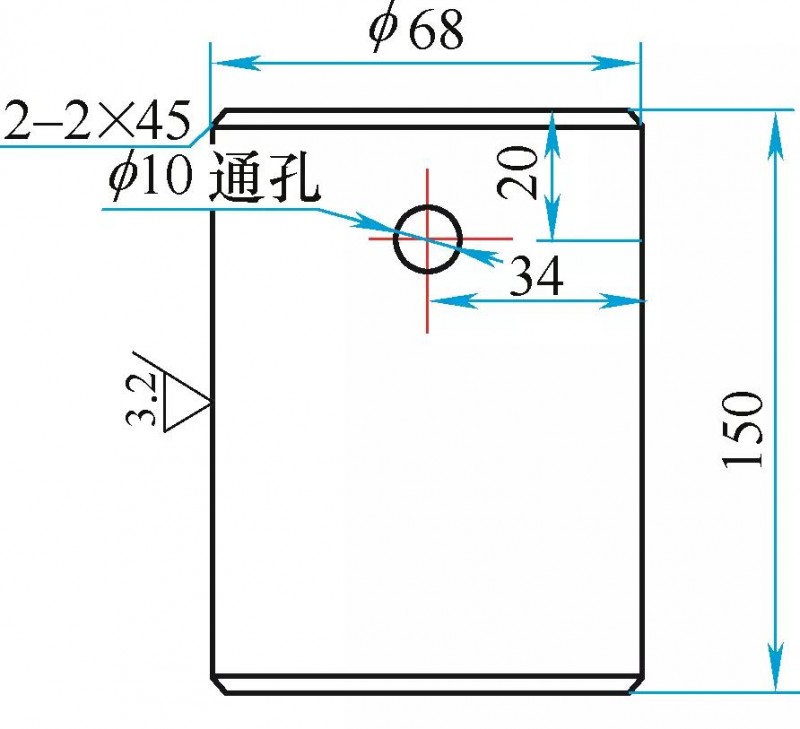
图 2
2.确定工艺路线
为了达到和产品相同的效果,渗碳前采用与高端齿轨轮相同的工艺路线,路线如下:锻造成Φ80mm左右的棒料→930℃正火+670℃高温回火→加工成图2的尺寸及精度→渗碳试验+3次高温回火→取20mm厚、¼圆的金相试样→检测渗碳层深度和碳化物级别。
3.拟定试验方案
现有热处理设备都比较老旧,加热时间过长对设备损坏比较严重,所以我们根据现有设备情况及生产条件,制定出两种试验方案:第一种是三次短时间渗碳;第二种是一次长时间渗碳。
(1)第一种方案
试棒随渗碳层深度3~4mm的产品同炉进行三次渗碳处理。为了检验每次的渗碳层深度,在第一次渗碳时放3根试棒,渗碳完成时取出1根试棒并进行标记,其余2根再进行第二次渗碳,第二次渗碳完成后再取出1根并进行标记,剩下1根进行第三次渗碳并进行标记。3次渗碳完成后的试样进行3次高温回火处理,然后加工出金相试样并进行金相检测。这种方案我们进行了两组试验。三次渗碳工艺参数相同,如表1所示。
表 1

(2)第二种方案
一次长时间渗碳。用一根试棒随产品12100090140齿轨轮一起装炉进行渗碳,渗碳完成后进行3次回火。由于时间原因这种方案我们只进行了一次试验。工艺参数如表2所示。
表 2

4.试验结果
试验中我们将Φ68mm试验用试棒与生产中Φ20mm随炉试样同时装炉,并对渗碳检验结果进行对比。
(1)第一种方案试验结果
第一种方案第一组渗碳完成后取样检验结果如表3所示。
表 3
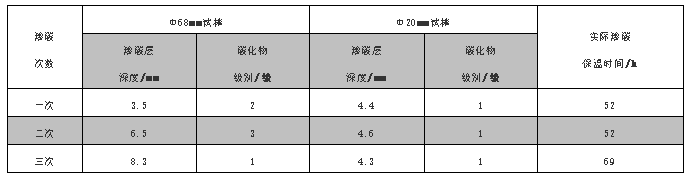
第一种方案第二组渗碳试验完成后取样检验结果如表4所示。
表 4
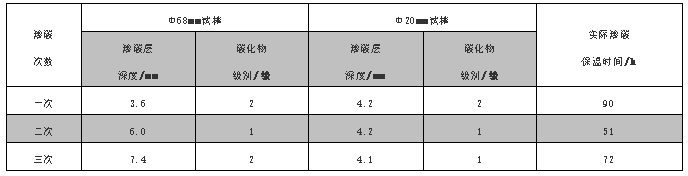
(2)第二种方案试验结果
第二种方案渗碳完成后取样检验结果如表5所示。
表 5

5.结语
本次深层渗碳试验采用两种方案,一种为一次长时间渗碳;一种为2~3次3~4mm短时间渗碳。对试验结果进行分析可得出以下结论:在现有设备条件下,使用三次3~4mm渗碳可以实现深渗层渗碳,经两次3~4mm渗碳基本上可以达到6mm渗层,三次可达到7~8mm渗层,而且碳化物可控制在4级以下。
编辑推荐
最新资讯
-
全球产业链聚沪 共探双碳新路径 SNEC
2025-04-18 18:05
-
柯马签订具有约束力的协议收购 Autom
2025-04-17 13:01
-
高效协同新范式:比亚迪叉车领创智能
2025-04-17 10:04
-
埃马克德国总部迎来中国社科院工业经
2025-04-15 09:40
-
埃马克这项全新应用即将在CIMT惊艳首
2025-04-15 09:37