众泰汽车轻量化技术取得新突破
2018-08-27 18:05:43· 来源:众泰汽车研究院
随着汽车消费的日益普及和环保压力的逐渐加大,轻量化已经成为当今新车研发的焦点和大势所趋,而要达到预期的轻量化目标,轻量化材料以及工艺技术带来的效果最为显著。以碳纤维复合材料为代表的轻量化材料及工艺技术,将大力推动汽车轻量化进程,成为汽车轻量化路上的得力助手。
随着汽车消费的日益普及和环保压力的逐渐加大,轻量化已经成为当今新车研发的焦点和大势所趋,而要达到预期的轻量化目标,轻量化材料以及工艺技术带来的效果最为显著。以碳纤维复合材料为代表的轻量化材料及工艺技术,将大力推动汽车轻量化进程,成为汽车轻量化路上的得力助手。
技术研发:布局轻量化时代
在业内,碳纤维复合材料一直有着汽车轻量化杀手锏之美誉,但由于碳纤维复合材料设计和工程开发难度大,我国在各种碳纤维复合材料铺层设计、连接点CAE设计及验证等方面的数据积累较少,导致碳纤维复合材料的应用成为业内普遍公认的难点。
众泰汽车自成立以来,便非常重视碳纤维复合材料等轻量化材料及零部件研发,并相继开展了以 “碳纤维复合材料混合车身”为主,包括全铝底盘、轻量化座椅等在内的SUV轻量化平台研发项目。截止目前为止,在碳纤维复合材料车身件、大型铝合金前后纵梁的材料、工艺及连接技术方面,众泰汽车已拥有多项自主研发的核心技术,并已申请了20余项专利,其中发明专利占70%,已获得4项授权,硕果累累。

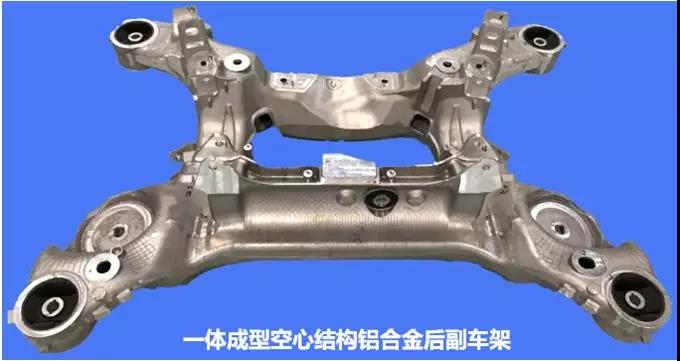
技术突破:开发碳纤维复合材料混合车身
碳纤维复合材料密度通常在1.7g每立方厘米左右,远远低于制造业常用的钢材,其断裂韧性、抗疲劳性、抗蠕变性都高于汽车常用的金属材料,众泰汽车目前研发的SUV平台碳纤维复合材料混合车身,便是一种拥有碳纤维复合材料、铝合金、塑料及钢等多材料混合技术以及先进连接工艺的新型车身。
该车身包含有十余种碳纤维复合材料零部件(翼子板、四门等车身覆盖件以及9种碳纤维复合材料结构件),最大尺寸达1820*1180mm。其中,研发的B柱总成由超高强钢及碳纤维复合材料混合而成,使B柱上部的强度提高,又使下部具有韧性。此外,诸如顶盖前顶梁、中央通道加强板等碳纤维复合材料结构件采用一体化成型设计,减少了零件的数量,使安全性和NVH性能提升。相对于传统钢制件,碳纤维复合材料顶盖前顶梁减重约50%,强度提升173%;碳纤维复合材料门槛边梁外板减重约40%,强度提升高达227%。

技术推进:攻克多项车身轻量化核心技术
在技术层面,众泰汽车基于“材料-性能-工艺”一体化的多零件集成设计方法,研发出既能够满足零件结构性能,还能发挥碳纤维复合材料优势的结构和铺层方案,并通过自主研发的新型连接技术,解决了碳纤维复合材料混合车身中异种材料连接带来的电化学腐蚀问题,以及因热膨胀系数不同在温度变化时易失效等关键问题。众泰汽车在“碳纤维/钢”、“碳纤维/铝”等异种材料连接技术方面实现了核心技术突破。例如,专利技术“超差孔胶铆结构”,即在连接处的碳纤维复合材料零件上开设超差孔用于补偿由于热膨胀系数不同引起的位置公差,该结构有效解决了碳纤维复合材料混合车身在线电泳涂装易开裂的问题,实现了碳纤维复合材料混合车身混合车身在线电泳涂装;采用专利连接技术新型衬套混合连接结构防止异种材料间的电化学腐蚀,并在车身性能试验中经过验证非常有效。
众泰汽车设计研发了可以批量生产的模压碳纤维复合材料混合车身零部件结构,基于复合材料的性能特征及成型特点,结合零部件本身的工况要求和结构特点进行设计,既能充分发挥碳纤维复合材料混合车身的性能优势,又能充分满足性能要求,实现减重的同时性能也得到提升。除此之外,众泰汽车在混合车身上还自主开发了具有梯度缓冲吸能结构的铝合金前后纵梁以及一体成型铝合金减震塔等大型轻量化结构件。
小结
未来,众泰汽车的车身覆盖件制造将以铝合金和碳纤维复合材料混合车身复合材料为重点,逐步掌握轻量化材料制造技术,实现2020年铝合金整车质量占比15%以上,车身减重20%,轻量化系数达到2.8以下;2025年碳纤维复合材料混合车身复合材料在车上使用量达到2%以上,车身重量降低30%的发展目标。
作为自主品牌的中坚力量,众泰汽车一直致力于提升研发技术水平,通过新技术、新材料的运用,打造高品质、高质量的“智美中国车”,在为消费者提供更加节能环保和高性能的优秀汽车产品的同时,也为众泰汽车突破自主品牌第一阵营积蓄力量!
技术研发:布局轻量化时代
在业内,碳纤维复合材料一直有着汽车轻量化杀手锏之美誉,但由于碳纤维复合材料设计和工程开发难度大,我国在各种碳纤维复合材料铺层设计、连接点CAE设计及验证等方面的数据积累较少,导致碳纤维复合材料的应用成为业内普遍公认的难点。
众泰汽车自成立以来,便非常重视碳纤维复合材料等轻量化材料及零部件研发,并相继开展了以 “碳纤维复合材料混合车身”为主,包括全铝底盘、轻量化座椅等在内的SUV轻量化平台研发项目。截止目前为止,在碳纤维复合材料车身件、大型铝合金前后纵梁的材料、工艺及连接技术方面,众泰汽车已拥有多项自主研发的核心技术,并已申请了20余项专利,其中发明专利占70%,已获得4项授权,硕果累累。

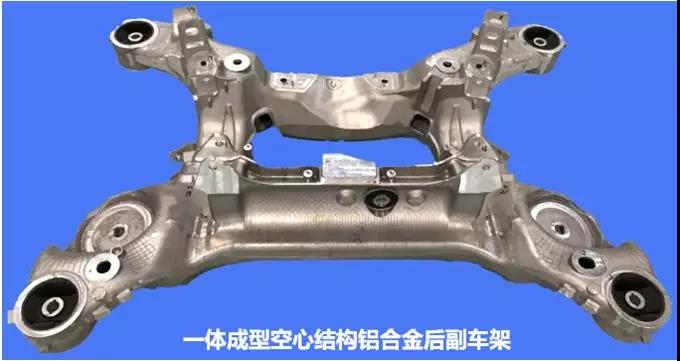
技术突破:开发碳纤维复合材料混合车身
碳纤维复合材料密度通常在1.7g每立方厘米左右,远远低于制造业常用的钢材,其断裂韧性、抗疲劳性、抗蠕变性都高于汽车常用的金属材料,众泰汽车目前研发的SUV平台碳纤维复合材料混合车身,便是一种拥有碳纤维复合材料、铝合金、塑料及钢等多材料混合技术以及先进连接工艺的新型车身。
该车身包含有十余种碳纤维复合材料零部件(翼子板、四门等车身覆盖件以及9种碳纤维复合材料结构件),最大尺寸达1820*1180mm。其中,研发的B柱总成由超高强钢及碳纤维复合材料混合而成,使B柱上部的强度提高,又使下部具有韧性。此外,诸如顶盖前顶梁、中央通道加强板等碳纤维复合材料结构件采用一体化成型设计,减少了零件的数量,使安全性和NVH性能提升。相对于传统钢制件,碳纤维复合材料顶盖前顶梁减重约50%,强度提升173%;碳纤维复合材料门槛边梁外板减重约40%,强度提升高达227%。

技术推进:攻克多项车身轻量化核心技术
在技术层面,众泰汽车基于“材料-性能-工艺”一体化的多零件集成设计方法,研发出既能够满足零件结构性能,还能发挥碳纤维复合材料优势的结构和铺层方案,并通过自主研发的新型连接技术,解决了碳纤维复合材料混合车身中异种材料连接带来的电化学腐蚀问题,以及因热膨胀系数不同在温度变化时易失效等关键问题。众泰汽车在“碳纤维/钢”、“碳纤维/铝”等异种材料连接技术方面实现了核心技术突破。例如,专利技术“超差孔胶铆结构”,即在连接处的碳纤维复合材料零件上开设超差孔用于补偿由于热膨胀系数不同引起的位置公差,该结构有效解决了碳纤维复合材料混合车身在线电泳涂装易开裂的问题,实现了碳纤维复合材料混合车身混合车身在线电泳涂装;采用专利连接技术新型衬套混合连接结构防止异种材料间的电化学腐蚀,并在车身性能试验中经过验证非常有效。
众泰汽车设计研发了可以批量生产的模压碳纤维复合材料混合车身零部件结构,基于复合材料的性能特征及成型特点,结合零部件本身的工况要求和结构特点进行设计,既能充分发挥碳纤维复合材料混合车身的性能优势,又能充分满足性能要求,实现减重的同时性能也得到提升。除此之外,众泰汽车在混合车身上还自主开发了具有梯度缓冲吸能结构的铝合金前后纵梁以及一体成型铝合金减震塔等大型轻量化结构件。
小结
未来,众泰汽车的车身覆盖件制造将以铝合金和碳纤维复合材料混合车身复合材料为重点,逐步掌握轻量化材料制造技术,实现2020年铝合金整车质量占比15%以上,车身减重20%,轻量化系数达到2.8以下;2025年碳纤维复合材料混合车身复合材料在车上使用量达到2%以上,车身重量降低30%的发展目标。
作为自主品牌的中坚力量,众泰汽车一直致力于提升研发技术水平,通过新技术、新材料的运用,打造高品质、高质量的“智美中国车”,在为消费者提供更加节能环保和高性能的优秀汽车产品的同时,也为众泰汽车突破自主品牌第一阵营积蓄力量!
编辑推荐
最新资讯
-
比亚迪叉车的智慧演变:从动力革新到
2025-04-02 09:15
-
重磅剧透!首批参展商名单曝光——这
2025-04-01 20:48
-
施耐德电气发布新一代Harmony XVB7模
2025-04-01 18:51
-
[转载] 机床巨头埃马克:百年跌宕再
2025-03-31 12:42
-
从4S店到修理厂:FLIR ONE Pro USB-C
2025-03-28 16:05