一种汽车零件的精冲复合工艺研究
2018-08-30 10:44:00· 来源:锻造与冲压
随着人类社会的进步与发展,环境、安全等法律法规要求的加严,以及人们对生活品质要求的不断提升,汽车在安全、品质、节能、环保等方面的要求也是越来越高。这些因素促使汽车零部件的加工工艺水平也要不断提升,以满足汽车零部件在结构、规格、性能等方面要求的提高。
随着人类社会的进步与发展,环境、安全等法律法规要求的加严,以及人们对生活品质要求的不断提升,汽车在安全、品质、节能、环保等方面的要求也是越来越高。这些因素促使汽车零部件的加工工艺水平也要不断提升,以满足汽车零部件在结构、规格、性能等方面要求的提高。
精冲作为汽车零部件加工的一种主要生产工艺,也越来越需要通过与其他工艺(拉深、锻造、挤压、折弯、机加工、焊接等)的复合,来满足汽车零部件的生产需求。本文介绍了一种典型的汽车零件的加工工艺,其开发过程是根据客户对产品的要求,最后选择了精冲工艺+ 其他工艺的复合,来实现产品的稳定批量生产。
汽车零件结构分析
该汽车零件原来是由两个零件复合而成,但对零件的加工工艺的要求很高,很难通过单一的加工工艺实现产品的批量生产,后采用一体式零件,如图1 所示。通过综合考虑该汽车零件的结构特点,以及每种加工工艺的优点,最后确认该汽车零件采用成形毛坯+ 精冲+ 机加工的复合工艺。
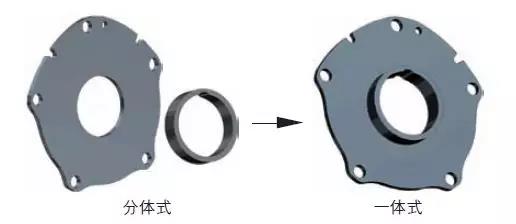
图1 汽车零件结构示意图
原材料分析
该汽车零件可选用A 和B 两种材料,两种不同材料需要不同的工艺进行毛坯成形。从表1 的材料性能可得出A 材料适合锻造的工艺进行毛坯成形,B 材料适合拉深工艺进行毛坯成形。
表1 两种材料的性能对比
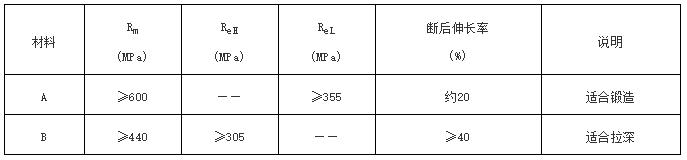
两种工艺加工成形的毛坯,后续都有相应的热处理,以改善成形毛坯的加工性能,保证最后完成品精度的稳定,如表2 所示。
表2 两种毛坯成形工艺的对比
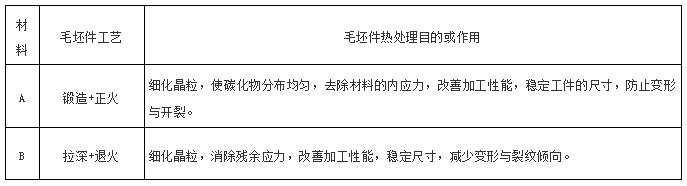
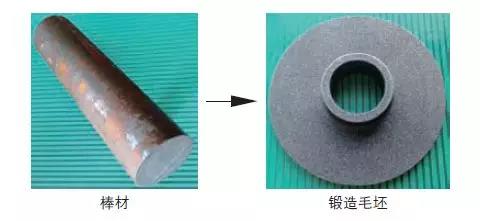
图2 锻造成形示意图
零件加工工艺
毛坯成形
选择A 材料加工时,原材料选用棒材,采用锻造工艺实现毛坯成形,如图2 所示。选择B 材料加工时,原材料选用板材,采用拉深工艺实现毛坯成形,如图3 所示。
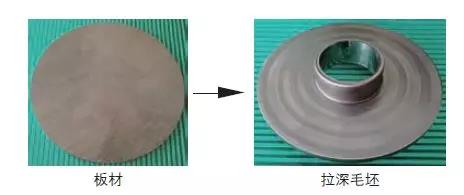
图3 拉深成形示意图
两种毛坯成形工艺,锻造件精度低,后续切削余量大,材料利用率低,成本偏高,且锻造工艺消耗能源大;拉深件对材料性能要求较高,材料利用率高,拉深加工效率高,成本更低,且拉深为冷加工比锻造更环保。
通过以上两种毛坯成形工艺对比,拉深的工艺方案优势更大。厚板经过拉深后,其凸起部R 角比较大,无法满足图纸要求,通过后续校形、挤压的方式,对零件进行整形,减小R 角及改善端部形状,如图4所示。
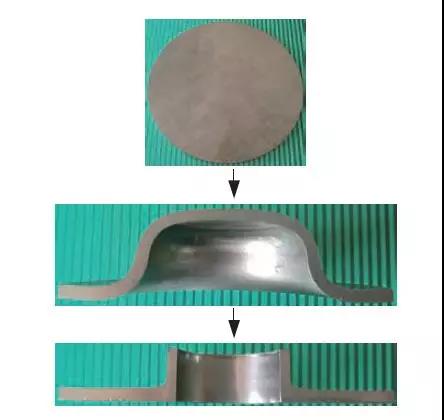
图4 拉深、校形、挤压过程示意图
通过拉深、校形、挤压实现零件毛坯成形后,采用多工位传递模,利用机械手传递系统,实现产品的模内快速传递。设备选用适合厚板拉深、折弯及厚板冲锻复合成形加工的双肘节式精密冲床。
精冲
图5 所示该汽车零件厚度为4.0mm,小孔直径为3.50mm,小孔与外圆的间距为1.25mm。间距小,精冲时,局部塌陷量大,需要设计特殊的模具结构来降低薄壁处的塌陷量,以满足该零件后续的加工要求。
该零件精冲外形及孔后,因其精度要求高,精冲件无法满足图纸要求,需要通过后续的切削加工来保证零件精度。后续机加工时,汽车零件装夹位置如图6 所示,装夹面为精冲的剪切面,所以该部位剪切面的质量会影响到机加工时的装夹精度。
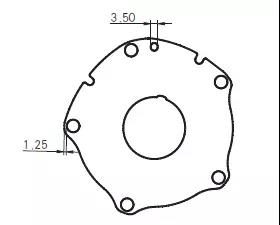
图5 汽车零件简图
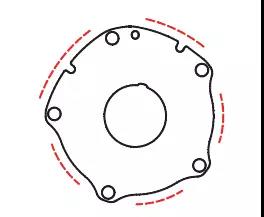
图6 机加工装夹示意图
影响剪切面垂直度的因素有:零件结构、材料厚度(图7)及其机械性能、模具结构、凹模圆角、齿圈及冲压时的压边力和反顶力。因零件的结构及材料由客户指定,精冲工艺设计时,需要通过调整模具结构以及精冲力的大小,来改善剪切面的质量(主要是垂直度)。
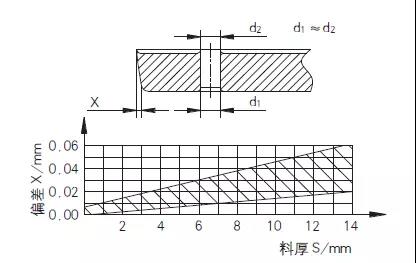
图7 料厚与偏差X 值的关系
的要求,通过对精冲模具结构、模具材料等进行优化改善,大大减小了塌陷量,改善前后塌陷量对比如图8 所示,满足了后续工序的稳定生产。考虑到该零件精冲生产时,是单件上下料,可通过自动上下料系统进行自动化生产。图9 所示的系统能够实现自动上料、自动涂油、冲压后自动下料、零件与废料自动分离等动作,实现了自动冲压,节省了人力成本,保证了生产的稳定性。
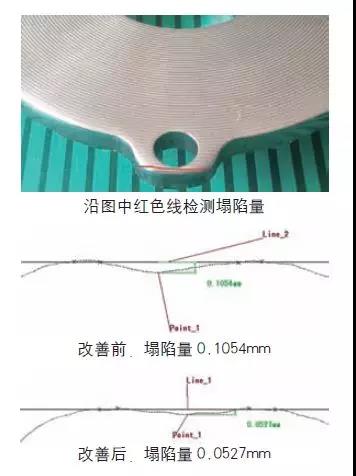
图8 改善前后塌陷量对比示意图
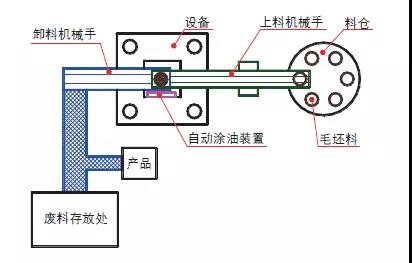
图9 精冲生产自动润滑及上下料示意图
机加工
图10 所示该汽车零件精度要求比较高,精冲件无法满足图面要求,需要后续切削加工工序,以满足其平面度、垂直度、圆柱度、圆度、同轴度等要求。
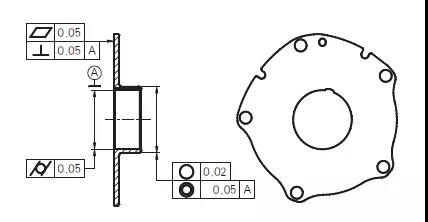
图10 汽车零件机加工简图
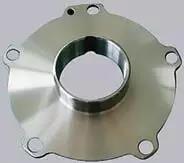
图11 精冲复合工艺生产的汽车零件
结束语
通过精冲工艺与其他工艺的复合加工完成的汽车零件,如图11 所示。不仅轮廓形状精度高、成本低、效率高,而且结合了拉深工艺/ 锻造工艺三维形状成形与高精度机加工工艺的优势。既实现了结构特殊的汽车零部件的加工,又满足了其高精度的要求,实现了批量稳定生产。相信随着汽车行业的发展,会有越来越多的汽车零部件需要复合工艺来满足其高性能、高品质的要求。
精冲作为汽车零部件加工的一种主要生产工艺,也越来越需要通过与其他工艺(拉深、锻造、挤压、折弯、机加工、焊接等)的复合,来满足汽车零部件的生产需求。本文介绍了一种典型的汽车零件的加工工艺,其开发过程是根据客户对产品的要求,最后选择了精冲工艺+ 其他工艺的复合,来实现产品的稳定批量生产。
汽车零件结构分析
该汽车零件原来是由两个零件复合而成,但对零件的加工工艺的要求很高,很难通过单一的加工工艺实现产品的批量生产,后采用一体式零件,如图1 所示。通过综合考虑该汽车零件的结构特点,以及每种加工工艺的优点,最后确认该汽车零件采用成形毛坯+ 精冲+ 机加工的复合工艺。
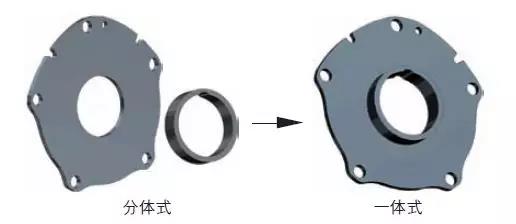
图1 汽车零件结构示意图
原材料分析
该汽车零件可选用A 和B 两种材料,两种不同材料需要不同的工艺进行毛坯成形。从表1 的材料性能可得出A 材料适合锻造的工艺进行毛坯成形,B 材料适合拉深工艺进行毛坯成形。
表1 两种材料的性能对比
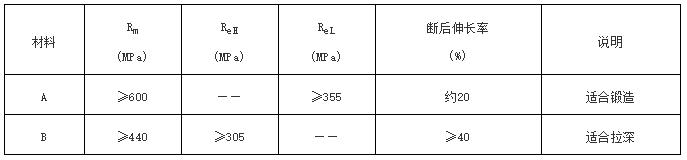
两种工艺加工成形的毛坯,后续都有相应的热处理,以改善成形毛坯的加工性能,保证最后完成品精度的稳定,如表2 所示。
表2 两种毛坯成形工艺的对比
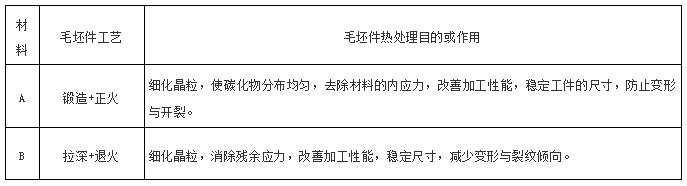
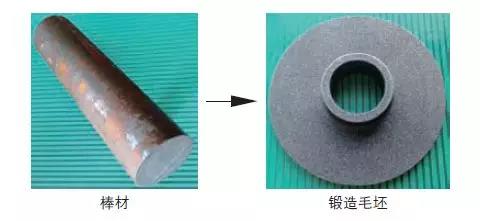
图2 锻造成形示意图
零件加工工艺
毛坯成形
选择A 材料加工时,原材料选用棒材,采用锻造工艺实现毛坯成形,如图2 所示。选择B 材料加工时,原材料选用板材,采用拉深工艺实现毛坯成形,如图3 所示。
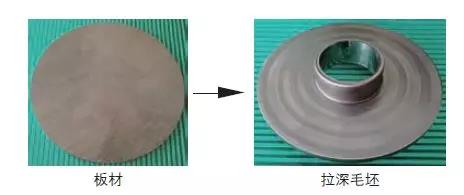
图3 拉深成形示意图
两种毛坯成形工艺,锻造件精度低,后续切削余量大,材料利用率低,成本偏高,且锻造工艺消耗能源大;拉深件对材料性能要求较高,材料利用率高,拉深加工效率高,成本更低,且拉深为冷加工比锻造更环保。
通过以上两种毛坯成形工艺对比,拉深的工艺方案优势更大。厚板经过拉深后,其凸起部R 角比较大,无法满足图纸要求,通过后续校形、挤压的方式,对零件进行整形,减小R 角及改善端部形状,如图4所示。
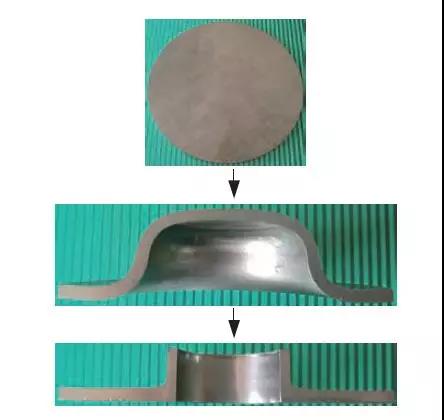
图4 拉深、校形、挤压过程示意图
通过拉深、校形、挤压实现零件毛坯成形后,采用多工位传递模,利用机械手传递系统,实现产品的模内快速传递。设备选用适合厚板拉深、折弯及厚板冲锻复合成形加工的双肘节式精密冲床。
精冲
图5 所示该汽车零件厚度为4.0mm,小孔直径为3.50mm,小孔与外圆的间距为1.25mm。间距小,精冲时,局部塌陷量大,需要设计特殊的模具结构来降低薄壁处的塌陷量,以满足该零件后续的加工要求。
该零件精冲外形及孔后,因其精度要求高,精冲件无法满足图纸要求,需要通过后续的切削加工来保证零件精度。后续机加工时,汽车零件装夹位置如图6 所示,装夹面为精冲的剪切面,所以该部位剪切面的质量会影响到机加工时的装夹精度。
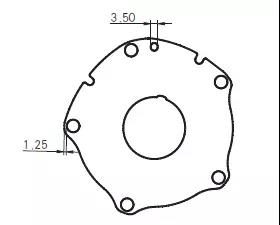
图5 汽车零件简图
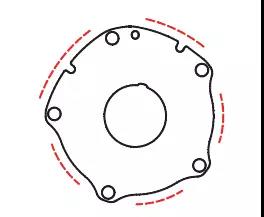
图6 机加工装夹示意图
影响剪切面垂直度的因素有:零件结构、材料厚度(图7)及其机械性能、模具结构、凹模圆角、齿圈及冲压时的压边力和反顶力。因零件的结构及材料由客户指定,精冲工艺设计时,需要通过调整模具结构以及精冲力的大小,来改善剪切面的质量(主要是垂直度)。
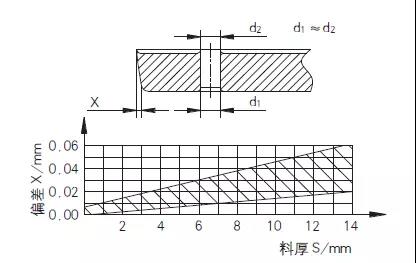
图7 料厚与偏差X 值的关系
的要求,通过对精冲模具结构、模具材料等进行优化改善,大大减小了塌陷量,改善前后塌陷量对比如图8 所示,满足了后续工序的稳定生产。考虑到该零件精冲生产时,是单件上下料,可通过自动上下料系统进行自动化生产。图9 所示的系统能够实现自动上料、自动涂油、冲压后自动下料、零件与废料自动分离等动作,实现了自动冲压,节省了人力成本,保证了生产的稳定性。
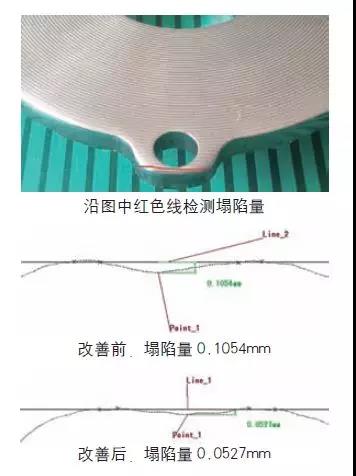
图8 改善前后塌陷量对比示意图
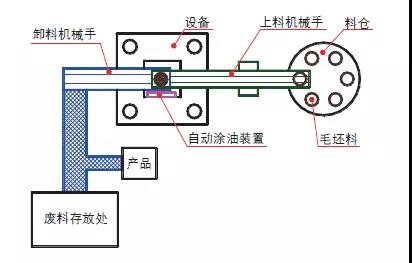
图9 精冲生产自动润滑及上下料示意图
机加工
图10 所示该汽车零件精度要求比较高,精冲件无法满足图面要求,需要后续切削加工工序,以满足其平面度、垂直度、圆柱度、圆度、同轴度等要求。
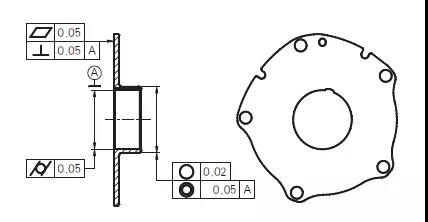
图10 汽车零件机加工简图
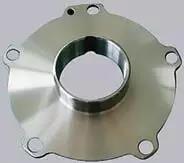
图11 精冲复合工艺生产的汽车零件
结束语
通过精冲工艺与其他工艺的复合加工完成的汽车零件,如图11 所示。不仅轮廓形状精度高、成本低、效率高,而且结合了拉深工艺/ 锻造工艺三维形状成形与高精度机加工工艺的优势。既实现了结构特殊的汽车零部件的加工,又满足了其高精度的要求,实现了批量稳定生产。相信随着汽车行业的发展,会有越来越多的汽车零部件需要复合工艺来满足其高性能、高品质的要求。
最新资讯
-
果栗智造磁悬浮技术赋能汽车制造:破
2025-04-03 19:27
-
比亚迪叉车的智慧演变:从动力革新到
2025-04-02 09:15
-
重磅剧透!首批参展商名单曝光——这
2025-04-01 20:48
-
施耐德电气发布新一代Harmony XVB7模
2025-04-01 18:51
-
[转载] 机床巨头埃马克:百年跌宕再
2025-03-31 12:42