福特重新设计碳纤维悬架组件
2018-08-30 22:20:11· 来源:汽车制造网 作者:徐婷
福特(Ford)、华威制造集团(WMG)、汽车技术公司(Autotech)和GRM咨询公司(GRM Consulting)已经开发出一种用于C级车辆的复合式后悬架转向节。
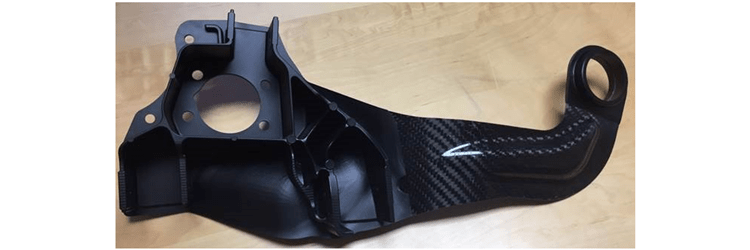
福特(Ford)、华威制造集团(WMG)、汽车技术公司(Autotech)和GRM咨询公司(GRM Consulting)已经开发出一种用于C级车辆的复合式后悬架转向节。
根据福特的说法,新的后悬架转向节采用独特的碳纤维配置和定制的制造工艺相结合,与目前的钢构件相比,重量减少了50%。该项目中引入的加工技术据说是同类产品中首创的,整个周期不到5分钟。这一零件的设计已经完成,目前正在进行零件的制造试验,以开发全面的大规模生产过程。
协作是至关重要的
全球汽车行业都在推动更严格的目标,以满足日益增长的排放严格要求,减轻对化石燃料消耗的担忧以及满足客户对行驶里程更长的电动汽车的需求。福特的全球研究和先进工程集团与英国的底盘工程公司合作,重新设计了一种系列钢制悬架部件,使其能够作为轻质复合材料部件制造。这种非簧载组件的重量节省提高了弹簧和阻尼器的有效性,从而提高了乘客的舒适性和驾驶员的操控性。新开发的复合零件被证明适合于高性能C级车。
这一为期两年的项目——复合轻型汽车悬架系统(CLASS),由Innovate UK参与资助。
WMG利用其对材料性能的广泛知识和最先进的制造单元,使底盘制造商Autotech能够设计出满足所需功能要求的组件。GRM咨询公司为赛车行业的碳纤维结构开发预测工具,通过减少物理测试的数量,为项目做出了重大贡献。
设计方法
在项目进行的过程中,复合材料部分的设计从单一材料部分发展到多材料设计。初步研究表明,单材料薄板模塑复合材料(SMC)可实现复合材料轻量化转向节。然而,对SMC样品的严格内部测试突出了两个缺陷,即较长的固化时间和缺乏满足负载要求的机械性能。这些问题导致设计工程团队启用了一个多材料系统,其中预制层提供了所需的机械性能,并且SMC的共同成型能够实现复杂的几何轮廓。这种技术已经在学术界和航天工业中提出,但是对汽车应用的要求是不同的,这个项目很可能是这种技术在汽车行业的第一次实施。这是有可能的,因为全球范围内的预制生产成本正在降低。将单/双轴预浸料与SMC相结合的方法表明,复合材料能够满足大多数机械强度目标。经过广泛的模拟和实验工作,最终完成了设计,包括OEM耐久性和NVH目标的优化。
创新的制造技术
目前,已经开发了一种能够大批量生产高强度、刚性和复杂形状的悬架转向节的模压成型技术。这将是完全自动化的,制造试验生产用于物理测试评估的演示部件的一个周期时间低于5分钟。在压力机的帮助下,预切预浸料在模具中按要求的形状预先成形。然后将预成形件转移到压型压力机中。该压缩模压工具是由一家英国的工具制造商制造的,其特点是传感器可以跟踪SMC流,监测工艺参数,并研究预浸料和SMC树脂的固化。SMC由53%重量分数和15k长丝数碳纤维组成,预浸料是一种织物,其重量分数为60%,丝数为12k,均由Mitsubishi Rayon提供。在制造该部件之前,一流的候选碳纤维材料是在美国迪尔伯恩的福特研究与创新中心成型的。这有助于优化工艺参数,从而获得最大的机械性能和几何精度。
经验教训
实现项目的成本目标是最大的挑战,但所获得的经验帮助工程师了解如何在成本、性能和重量之间取得最佳平衡。该项目一开始的目标是开发一个100% SMC复合转向节。随着工程的进展,工程师了解到低成本复合材料无法提供所需的机械刚度特性,因此必须在材料选择上更具创造性,以确保生产过程可以保持在周期内,同时满足该项目开始时制定的目标。
编辑推荐
最新资讯
-
全球产业链聚沪 共探双碳新路径 SNEC
2025-04-18 18:05
-
柯马签订具有约束力的协议收购 Autom
2025-04-17 13:01
-
高效协同新范式:比亚迪叉车领创智能
2025-04-17 10:04
-
埃马克德国总部迎来中国社科院工业经
2025-04-15 09:40
-
埃马克这项全新应用即将在CIMT惊艳首
2025-04-15 09:37