镁合金铸件在汽车工业中的应用与研究状况
2018-09-08 10:32:02· 来源:第一压铸网
为了提高汽车的燃油效率和降低其废气排放,减轻汽车的重量至关重要。为了达到这一目的,用镁合金来制造合适的汽车零部件似乎是一种显而易见的明智之举。作为一种最轻的结构金属,镁比钢轻75%,比铝轻33%左右。01 前沿研究表明,约75%的油
为了提高汽车的燃油效率和降低其废气排放,减轻汽车的重量至关重要。为了达到这一目的,用镁合金来制造合适的汽车零部件似乎是一种显而易见的明智之举。作为一种最轻的结构金属,镁比钢轻75%,比铝轻33%左右。
01 前沿
研究表明,约75%的油耗与汽车整车质量有关, 减轻汽车整车质量可以有效降低油耗及排放。减轻整车质量,还可以明显减小动力传动负荷,可在较低的牵引负荷下达到更好的操控性能。在保证汽年零部件强度和刚度要求下尽可能选用质量较轻的材料,是汽车轻量化的重要途径之一。镁合金是当前常用金属结构材料中最轻的,而且储量丰富,因而成为汽车减重以提高其燃油经济性和可操控性的首选材料。
02 镁合金用于汽车工业的优势
镁合金部件应用于汽车工业中主要有如下优势:
质量轻,其密度只有铝合金的2/3;
比强度高于铝合金和铸铁,略低于比强度最 高的纤维增强塑料,有一定的承载能力;
比刚度与其他几种材料基本相同,可以取代铝合金和钢部件;
具有良好的铸造性能和尺寸稳定性,易于加工,废品率低;
具有良好的阻尼系数,减振量大于铝合金和铸铁,用于制造壳体可以降低噪声,用于制造座椅、轮圈可以减小振动,从而提高汽车的安全性和舒适性;
抗电磁干扰及屏蔽性好,减少噪声;
对环境污染小,可重复利用。
03 国内外镁合金汽车零部件的应用概况
3.1 国外应用概况
德国大众汽车公司是最早在汽车上大规模应用镁合金的汽车公司,早在20世纪30年代,大众汽车就开始使用镁合金,特别是90年代以来,德国在镁合金领域一直处于世界领先地位;奔驰汽车公司最早将镁合金压力铸造件应用于汽车座支架,奥迪汽车公司第一个推出镁合金压力铸造仪表板。近年来,帕萨特、奥迪A4和奥迪A6等汽车的齿轮箱壳体使用AZ91D镁合金,与铝合金部件相比减重25%。
美国在1948~1962年间,采用压力铸造生产了数百万件镁合金铸件供汽车使用。美国的福特、通用和克莱斯勒等汽车公司在过去的十几年里一直致力于镁合金汽车铸件如转向柱架、离合 器壳体、进气管、离合器片、汽缸盖、座架、滤油器壳体等的开发和应用,替代效果明显,大大促进了镁合金的发展。
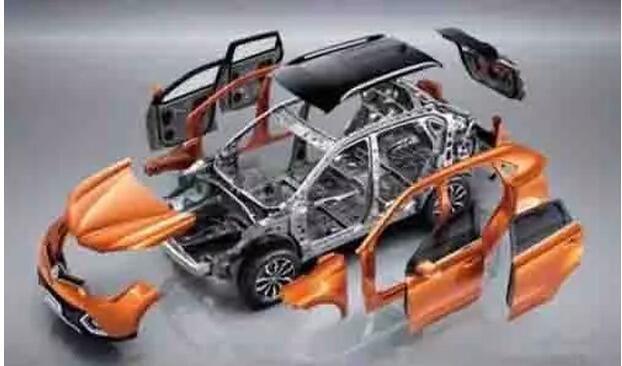
日本开发出镁合金低压力铸造造装置,由此, 经过研究相继开发了一系列镁合金压力铸造产 品,如丰田汽车公司首先制造出镁合金汽车轮毂、转向轴系统、凸轮罩等零部件,目前,日本的各家汽车公司都生产和应用了大量镁合金壳体类压力铸造件。
3.2 国内应用概况
在我国采用铸造镁合金已有30多年的历史, 但最初主要用于航空航天工业的壳体、机轮和机座等,在汽车行业起步较晚,目前仅近百家企业从事镁合金压力铸造件的生产和研究。上汽、一 汽、东风汽车公司及长安汽车在研究和开发镁合 金在汽车领域应用方面发挥了重要作用。
20世纪90年代初,上汽在国内最早将镁合金 应用在汽车上,首次在桑塔纳轿车上采用镁合金变 速器壳盖、壳体和离合器外壳。目前,其镁合金 汽车变速器外壳生产和应用技术已经十分成熟,镁合金电机壳体铸件正在电动汽车上进行装车试验。
一汽开发了高性能镁合金,可用于制造高温负载条件下的汽车动力系统部件,还成功开发出脚踏板、气缸罩盖、增压器壳体、转向盘、传动箱罩 盖等镁合金压力铸造件,并已应用于生产。
东风汽车公司结合我国汽车零部件压力铸造生产企业设备现状,开发了镁合金冷室压力铸造 工艺生产汽车零部件的全套技术。
长安汽车在国家科技支撑计划的支持下,完成了以镁合金变速器壳体、油底壳和气缸盖罩为 代表的大型复杂镁合金压力铸造件的设计、分析、模具开发制造和样件生产,成功开发出国内第一 个镁合金座椅并装车通过法规试验验证,并联合重庆大学开发了挤压力铸造造镁合金汽车轮毂。
3.3 典型零件
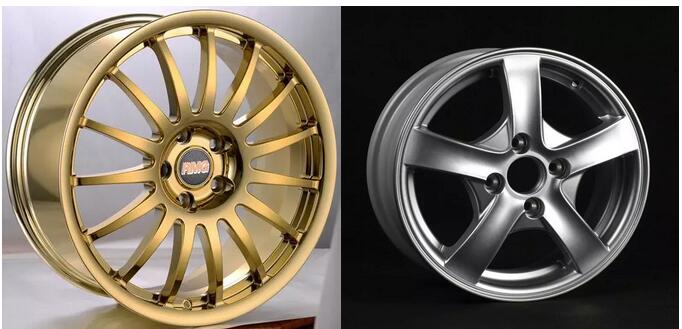
目前,镁合金在汽车上应用的零部件有100多 种,可分为两类:
壳体类,如离合器壳体、阀盖、阀板、变速器 壳体、仪表板、曲轴箱、发动机前盖、气缸箱、仪表 板、过滤器壳体等,这类件不仅可以减轻整车质 量,而且由于镁合金的阻尼衰减能力强,可以降低 汽车运行时的噪声;
支架类,如转向支架、转向盘、灯托架、制动 器、离合器踏板托架、制动支架、座椅框架、车镜支 架、分配支架和轮毂等,这类件有很好的抗冲击韧 性,大大提高了汽车行驶过程中的平稳性和安全性。
随着镁合金汽车零部件的开发,镁合金在汽 车上的应用有如下特点,由体积小的零件过渡到体积大的零件;由结构简单件过渡到复杂件;由简单受力件过渡到适应特殊性能要求的件;由分件 组合向过渡到集成化设计。
04 铸造工艺方式
目前,在汽车中镁型材、变形镁合金的应用较少(平均用镁量不到3 kg),主要应用的都是铸件 (单车达到30~40 kg),压力铸造生产的镁合金约占车用镁合金总量的80%。
4.1 压力铸造
从国内、外的研究应用情况看,镁合金的铸造成型方法较多,当前汽车零部件大多采用压力铸 造工艺进行生产。采用压力铸造工艺生产的铸件 具有轮廓清晰、表面质量高、尺寸精确稳定、加工 余量小,组织细密、强度和硬度较高等特点。另外,利用压力铸造工艺可以生产形状复杂的薄壁 铸件,生产效率高。
在镁合金压力铸造中,镁合金的比热容小、填充铸模型腔速度快,弥散状态的金属流与模型腔内的空气高度混合,气体来不及排出,最终在压力 铸造件内形成气孔、浇不足、冷隔等缺陷。镁合金压力铸造件一般不能进行热处理强化,为了消 除这些缺陷,提高压力铸造件的质量,近年来美国、日本等相继开发出了真空压力铸造、充氧压力铸造、挤压力铸造造、半固态触变注射成形和铸锻 双控成形等新工艺。
4.2 真空压力铸造
镁合金真空压力铸造是利用真空技术把模型 腔中的空气抽空,同时辅助降低模型腔中的气压, 使得充填成型和合金熔液中的气体排出,使合金熔 液在压力作用下充填模型腔,并在压力下凝固而获 得致密件。真空压力铸造件不仅可消除表面气 孔、疏松,提高表面质量,还能改善铸件致密度、解 决涂料脱皮、电镀起泡及盲孔缺料等工艺难题。近 年来,随着镁合金真空压力铸造工艺日益精良,铸 件壁厚最低可达1.5mm,真空度≦80kPa,充填时间 大大减小,铸件强度和韧性都得到相应提高。
4.3 充氧压力铸造
镁合金的充氧压力铸造是充分利用熔化状态的镁合金易与氧气或其他活性气体发生反应的特 点,在金属液充填压力铸造模型腔前充入活性气体置换模穴内的空气,当镁熔液压入模型腔时,活 性气体与其反应生成金属氧化物颗粒弥散分布在铸件中,从而消除铸件内的气体。充氧压力铸造 能够减少甚至消除压力铸造件的气孔,细化铸件组织,从而提高铸件致密度和力学性能,并使其可进行热处理强化。日本轻金属株式会社用充氧压 力铸造法成批生产了AM60镁合金汽车轮毂,比铝 轮毂质量减轻15%。
4.4 挤压力铸造
利用高压使镁熔液低速挤入模型腔内,凝固和微小的塑性变形之后得到铸件的方法就是挤压力 铸造。利用该工艺所得到的铸件具有很高的致密 度、优良的力学性能及较高的尺寸精度等,对铸件 的疏松、气孔等缺陷有很好的改善作用。此外, 得到的铸件还可以直接进行热处理工艺,以获取更 细小的组织晶粒。重庆大学蒋德平、龙思远对镁合 金轮毂做了一系列研究,采用挤压力铸造的镁合金 轮毂具有良好的力学性能,工艺流程更短,生产效 率也更高。由于挤压力铸造的压力可以改变镁 合金的固溶度和熔点,科研人员开发了一些适合于 挤压力铸造的镁合金体系,如英国的HTMI镁合金, 在180 ℃下具有优异的强度和抗蠕变性能。
4.5 半固态触变注射成形
镁合金的触变注射成形是一种充分利用注塑成形原理让金属半固态触变成形工艺。模具和成 形材料与压力铸造工艺相似,工艺过程则接近于 注塑成形工艺。该工艺不但可使铸件组织致密、 凝固收缩小、成形温度低和尺寸精度高,还具有操 作简单、安全、效率高和环保等一系列优点,适 合形状复杂、致密度高、薄壁和高性能零件的生 产。触变注射成形技术是目前唯一用于镁合金工 业生产的半固态成形技术,具有巨大的应用潜力。
4.6 铸锻双控成形
镁合金的铸锻双控成形集合了液态压力铸造和锻造的优点,在成形过程中,可同时实现铸件 形状、尺寸和使用性能的精确控制。实质就是在压力铸造基础上,待模型腔中的液态金属还未完全凝固时,立即施加一个变形力,打碎已经凝固的枝晶组织,进行细晶强化,使制件的力学性能得到显著 提高,既解决了压力铸造件毛坯缩孔和疏松的缺陷,又解决了锻造不能生产复杂高精度零件的缺 点,主要用于生产形状复杂和强度要求高的汽车零 部件。
05 存在问题与发展趋势
镁合金的耐蚀性较差,存在高温蠕变性,强度不高等缺点,另外,镁合金低温工作能力及屈服 极限有限,高性能的镁合金有待于研究开发。目前镁合金的基础数据积累还不够,没有系统的力 学性能测试,在腐蚀、热膨胀及模具设计等方面的数据也不够,使得汽车零部件的设计难度增大,成本增加。
与镁合金快速发展相适应的新型铸造技术、 技术人员、设备配备不足。近年来,真空压力铸造 技术、充氧压力铸造技术、挤压力铸造等一系列新 型铸造技术发展起来,使得镁合金性能得到了很 大提高。如镁合金的连续铸轧技术具有很好的应用前景,而目前国内的研究大多数还在实验室内, 很少有工业化生产。另外,这些新型技术属于汽 车生产商的机密技术,无法在汽车领域广泛应用 推广。镁合金铸造是一个系统工程,它集设计、制造及研究为一身,需要镁合金铸造工作者具有更全面的知识、经验及研究开发能力。新的铸造技术要有新型的设备来与其匹配,以生产出性能更 好的铸件,扩大镁合金的应用范围。但是新型设备投资、运行的成本较高,可以对现有设备进行改 进,以降低其生产成本、减少生产周期,最终扩大镁合金在汽车行业的应用范围。
北美镁战略联盟计划到2020年车用镁平均质量约达158 kg。我国按照目前车用镁平均质量3 kg、年 增长20%计算,到2020年与北美仍有很大差距。 要想缩小这种差距,今后的主要发展方向为:
提高镁合金的材料性能。
镁合金耐蚀性较差,对于暴露在外特别是沿海地区的汽车底盘和行走系统零部件,应能满足使用环境对耐蚀性的要求,高耐蚀镁合金的研究成为镁合金发展重要方向;目前广泛使用的商业镁合金,如AZ91D,在120 ℃以上温度工作时因析出相的分解和软化,使 其抗蠕变性能较差,对于工作温度超过130 ℃的高 性能齿轮箱和曲轴箱,现有的镁合金很难满足使用要求。高耐热镁合金开发与应用是将来镁合金 在汽车工业应用的重要领域;在汽车部件轻量化 的同时,其安全可靠性非常重要,重要的车内部件如转向盘、转向盘立柱、座椅骨架和车门框等,除 了要满足成型性要求,更重要的是材料要具有高 强韧性,能减振并使零件受重击时不断裂,应用较多的如 AM60,AM50 其合金塑性较好,但强度偏低,并且铸造流动性和耐蚀性不理想,具有更高强 度和韧性,又具有优良铸造流动性的镁合金应该 大力发展。
新型铸造技术、高技能人才及新型设备将成为镁合金铸造发展三要素。
01 前沿
研究表明,约75%的油耗与汽车整车质量有关, 减轻汽车整车质量可以有效降低油耗及排放。减轻整车质量,还可以明显减小动力传动负荷,可在较低的牵引负荷下达到更好的操控性能。在保证汽年零部件强度和刚度要求下尽可能选用质量较轻的材料,是汽车轻量化的重要途径之一。镁合金是当前常用金属结构材料中最轻的,而且储量丰富,因而成为汽车减重以提高其燃油经济性和可操控性的首选材料。
02 镁合金用于汽车工业的优势
镁合金部件应用于汽车工业中主要有如下优势:
质量轻,其密度只有铝合金的2/3;
比强度高于铝合金和铸铁,略低于比强度最 高的纤维增强塑料,有一定的承载能力;
比刚度与其他几种材料基本相同,可以取代铝合金和钢部件;
具有良好的铸造性能和尺寸稳定性,易于加工,废品率低;
具有良好的阻尼系数,减振量大于铝合金和铸铁,用于制造壳体可以降低噪声,用于制造座椅、轮圈可以减小振动,从而提高汽车的安全性和舒适性;
抗电磁干扰及屏蔽性好,减少噪声;
对环境污染小,可重复利用。
03 国内外镁合金汽车零部件的应用概况
3.1 国外应用概况
德国大众汽车公司是最早在汽车上大规模应用镁合金的汽车公司,早在20世纪30年代,大众汽车就开始使用镁合金,特别是90年代以来,德国在镁合金领域一直处于世界领先地位;奔驰汽车公司最早将镁合金压力铸造件应用于汽车座支架,奥迪汽车公司第一个推出镁合金压力铸造仪表板。近年来,帕萨特、奥迪A4和奥迪A6等汽车的齿轮箱壳体使用AZ91D镁合金,与铝合金部件相比减重25%。
美国在1948~1962年间,采用压力铸造生产了数百万件镁合金铸件供汽车使用。美国的福特、通用和克莱斯勒等汽车公司在过去的十几年里一直致力于镁合金汽车铸件如转向柱架、离合 器壳体、进气管、离合器片、汽缸盖、座架、滤油器壳体等的开发和应用,替代效果明显,大大促进了镁合金的发展。
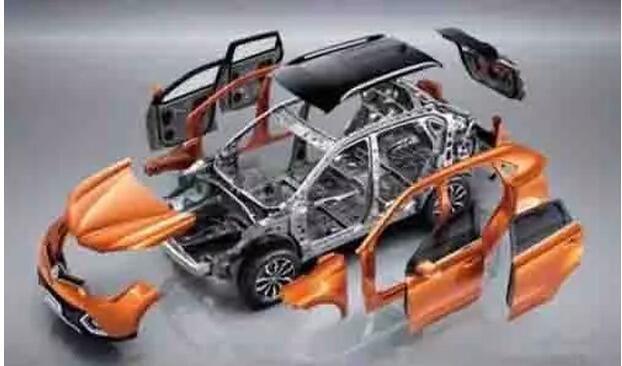
日本开发出镁合金低压力铸造造装置,由此, 经过研究相继开发了一系列镁合金压力铸造产 品,如丰田汽车公司首先制造出镁合金汽车轮毂、转向轴系统、凸轮罩等零部件,目前,日本的各家汽车公司都生产和应用了大量镁合金壳体类压力铸造件。
3.2 国内应用概况
在我国采用铸造镁合金已有30多年的历史, 但最初主要用于航空航天工业的壳体、机轮和机座等,在汽车行业起步较晚,目前仅近百家企业从事镁合金压力铸造件的生产和研究。上汽、一 汽、东风汽车公司及长安汽车在研究和开发镁合 金在汽车领域应用方面发挥了重要作用。
20世纪90年代初,上汽在国内最早将镁合金 应用在汽车上,首次在桑塔纳轿车上采用镁合金变 速器壳盖、壳体和离合器外壳。目前,其镁合金 汽车变速器外壳生产和应用技术已经十分成熟,镁合金电机壳体铸件正在电动汽车上进行装车试验。
一汽开发了高性能镁合金,可用于制造高温负载条件下的汽车动力系统部件,还成功开发出脚踏板、气缸罩盖、增压器壳体、转向盘、传动箱罩 盖等镁合金压力铸造件,并已应用于生产。
东风汽车公司结合我国汽车零部件压力铸造生产企业设备现状,开发了镁合金冷室压力铸造 工艺生产汽车零部件的全套技术。
长安汽车在国家科技支撑计划的支持下,完成了以镁合金变速器壳体、油底壳和气缸盖罩为 代表的大型复杂镁合金压力铸造件的设计、分析、模具开发制造和样件生产,成功开发出国内第一 个镁合金座椅并装车通过法规试验验证,并联合重庆大学开发了挤压力铸造造镁合金汽车轮毂。
3.3 典型零件
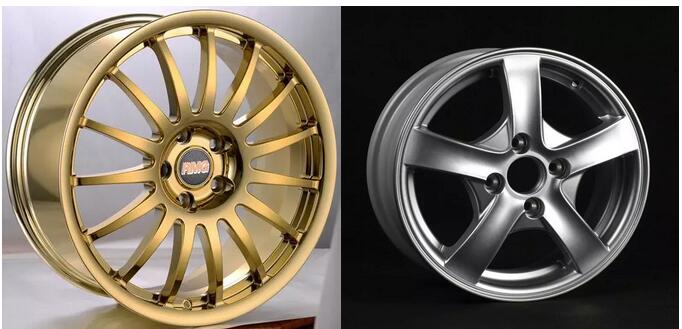
目前,镁合金在汽车上应用的零部件有100多 种,可分为两类:
壳体类,如离合器壳体、阀盖、阀板、变速器 壳体、仪表板、曲轴箱、发动机前盖、气缸箱、仪表 板、过滤器壳体等,这类件不仅可以减轻整车质 量,而且由于镁合金的阻尼衰减能力强,可以降低 汽车运行时的噪声;
支架类,如转向支架、转向盘、灯托架、制动 器、离合器踏板托架、制动支架、座椅框架、车镜支 架、分配支架和轮毂等,这类件有很好的抗冲击韧 性,大大提高了汽车行驶过程中的平稳性和安全性。
随着镁合金汽车零部件的开发,镁合金在汽 车上的应用有如下特点,由体积小的零件过渡到体积大的零件;由结构简单件过渡到复杂件;由简单受力件过渡到适应特殊性能要求的件;由分件 组合向过渡到集成化设计。
04 铸造工艺方式
目前,在汽车中镁型材、变形镁合金的应用较少(平均用镁量不到3 kg),主要应用的都是铸件 (单车达到30~40 kg),压力铸造生产的镁合金约占车用镁合金总量的80%。
4.1 压力铸造
从国内、外的研究应用情况看,镁合金的铸造成型方法较多,当前汽车零部件大多采用压力铸 造工艺进行生产。采用压力铸造工艺生产的铸件 具有轮廓清晰、表面质量高、尺寸精确稳定、加工 余量小,组织细密、强度和硬度较高等特点。另外,利用压力铸造工艺可以生产形状复杂的薄壁 铸件,生产效率高。
在镁合金压力铸造中,镁合金的比热容小、填充铸模型腔速度快,弥散状态的金属流与模型腔内的空气高度混合,气体来不及排出,最终在压力 铸造件内形成气孔、浇不足、冷隔等缺陷。镁合金压力铸造件一般不能进行热处理强化,为了消 除这些缺陷,提高压力铸造件的质量,近年来美国、日本等相继开发出了真空压力铸造、充氧压力铸造、挤压力铸造造、半固态触变注射成形和铸锻 双控成形等新工艺。
4.2 真空压力铸造
镁合金真空压力铸造是利用真空技术把模型 腔中的空气抽空,同时辅助降低模型腔中的气压, 使得充填成型和合金熔液中的气体排出,使合金熔 液在压力作用下充填模型腔,并在压力下凝固而获 得致密件。真空压力铸造件不仅可消除表面气 孔、疏松,提高表面质量,还能改善铸件致密度、解 决涂料脱皮、电镀起泡及盲孔缺料等工艺难题。近 年来,随着镁合金真空压力铸造工艺日益精良,铸 件壁厚最低可达1.5mm,真空度≦80kPa,充填时间 大大减小,铸件强度和韧性都得到相应提高。
4.3 充氧压力铸造
镁合金的充氧压力铸造是充分利用熔化状态的镁合金易与氧气或其他活性气体发生反应的特 点,在金属液充填压力铸造模型腔前充入活性气体置换模穴内的空气,当镁熔液压入模型腔时,活 性气体与其反应生成金属氧化物颗粒弥散分布在铸件中,从而消除铸件内的气体。充氧压力铸造 能够减少甚至消除压力铸造件的气孔,细化铸件组织,从而提高铸件致密度和力学性能,并使其可进行热处理强化。日本轻金属株式会社用充氧压 力铸造法成批生产了AM60镁合金汽车轮毂,比铝 轮毂质量减轻15%。
4.4 挤压力铸造
利用高压使镁熔液低速挤入模型腔内,凝固和微小的塑性变形之后得到铸件的方法就是挤压力 铸造。利用该工艺所得到的铸件具有很高的致密 度、优良的力学性能及较高的尺寸精度等,对铸件 的疏松、气孔等缺陷有很好的改善作用。此外, 得到的铸件还可以直接进行热处理工艺,以获取更 细小的组织晶粒。重庆大学蒋德平、龙思远对镁合 金轮毂做了一系列研究,采用挤压力铸造的镁合金 轮毂具有良好的力学性能,工艺流程更短,生产效 率也更高。由于挤压力铸造的压力可以改变镁 合金的固溶度和熔点,科研人员开发了一些适合于 挤压力铸造的镁合金体系,如英国的HTMI镁合金, 在180 ℃下具有优异的强度和抗蠕变性能。
4.5 半固态触变注射成形
镁合金的触变注射成形是一种充分利用注塑成形原理让金属半固态触变成形工艺。模具和成 形材料与压力铸造工艺相似,工艺过程则接近于 注塑成形工艺。该工艺不但可使铸件组织致密、 凝固收缩小、成形温度低和尺寸精度高,还具有操 作简单、安全、效率高和环保等一系列优点,适 合形状复杂、致密度高、薄壁和高性能零件的生 产。触变注射成形技术是目前唯一用于镁合金工 业生产的半固态成形技术,具有巨大的应用潜力。
4.6 铸锻双控成形
镁合金的铸锻双控成形集合了液态压力铸造和锻造的优点,在成形过程中,可同时实现铸件 形状、尺寸和使用性能的精确控制。实质就是在压力铸造基础上,待模型腔中的液态金属还未完全凝固时,立即施加一个变形力,打碎已经凝固的枝晶组织,进行细晶强化,使制件的力学性能得到显著 提高,既解决了压力铸造件毛坯缩孔和疏松的缺陷,又解决了锻造不能生产复杂高精度零件的缺 点,主要用于生产形状复杂和强度要求高的汽车零 部件。
05 存在问题与发展趋势
镁合金的耐蚀性较差,存在高温蠕变性,强度不高等缺点,另外,镁合金低温工作能力及屈服 极限有限,高性能的镁合金有待于研究开发。目前镁合金的基础数据积累还不够,没有系统的力 学性能测试,在腐蚀、热膨胀及模具设计等方面的数据也不够,使得汽车零部件的设计难度增大,成本增加。
与镁合金快速发展相适应的新型铸造技术、 技术人员、设备配备不足。近年来,真空压力铸造 技术、充氧压力铸造技术、挤压力铸造等一系列新 型铸造技术发展起来,使得镁合金性能得到了很 大提高。如镁合金的连续铸轧技术具有很好的应用前景,而目前国内的研究大多数还在实验室内, 很少有工业化生产。另外,这些新型技术属于汽 车生产商的机密技术,无法在汽车领域广泛应用 推广。镁合金铸造是一个系统工程,它集设计、制造及研究为一身,需要镁合金铸造工作者具有更全面的知识、经验及研究开发能力。新的铸造技术要有新型的设备来与其匹配,以生产出性能更 好的铸件,扩大镁合金的应用范围。但是新型设备投资、运行的成本较高,可以对现有设备进行改 进,以降低其生产成本、减少生产周期,最终扩大镁合金在汽车行业的应用范围。
北美镁战略联盟计划到2020年车用镁平均质量约达158 kg。我国按照目前车用镁平均质量3 kg、年 增长20%计算,到2020年与北美仍有很大差距。 要想缩小这种差距,今后的主要发展方向为:
提高镁合金的材料性能。
镁合金耐蚀性较差,对于暴露在外特别是沿海地区的汽车底盘和行走系统零部件,应能满足使用环境对耐蚀性的要求,高耐蚀镁合金的研究成为镁合金发展重要方向;目前广泛使用的商业镁合金,如AZ91D,在120 ℃以上温度工作时因析出相的分解和软化,使 其抗蠕变性能较差,对于工作温度超过130 ℃的高 性能齿轮箱和曲轴箱,现有的镁合金很难满足使用要求。高耐热镁合金开发与应用是将来镁合金 在汽车工业应用的重要领域;在汽车部件轻量化 的同时,其安全可靠性非常重要,重要的车内部件如转向盘、转向盘立柱、座椅骨架和车门框等,除 了要满足成型性要求,更重要的是材料要具有高 强韧性,能减振并使零件受重击时不断裂,应用较多的如 AM60,AM50 其合金塑性较好,但强度偏低,并且铸造流动性和耐蚀性不理想,具有更高强 度和韧性,又具有优良铸造流动性的镁合金应该 大力发展。
新型铸造技术、高技能人才及新型设备将成为镁合金铸造发展三要素。
举报 0
收藏 0
分享 136
-
冲压技术在电机叠片制造的应用
2024-09-06 -
车身零部件包边质量控制要点
2024-09-05 -
轻量化技术——热汽胀形工艺技术解析
2024-09-04 -
高强板车身件冲压技术
2024-09-02
最新资讯
-
思看科技受邀出席第三届联合国教科文
2025-04-27 13:29
-
聚势谋远,智领新程——五菱柳机以硬
2025-04-27 13:22
-
聚势求新、智驱未来——五菱工业底盘
2025-04-27 13:22
-
向轻量化、智能化迈进,助力建设国家
2025-04-27 13:21
-
五菱工业:以“中国智造”领跑绿色未
2025-04-27 13:21