强化研磨加工最佳工艺参数的实验研究
2018-09-10 19:23:02· 来源:《工具技术》 作者:陶建华
强化研磨加工是一种集“强化塑性加工”和“研磨微切削”为一体的金属表面冷加工方法,是一种多工艺结合的复合加工工艺。其在轴承加工方面具有明显的效果,具备较好的理论和技术的可行性。为此,可将强化研磨工艺应用于模具钢表面加工以提高表面质量,延长模具的使用寿命,通过单变量试验的方法,得出喷头移动速度、喷射压力和喷射距离等主要加工参数对模具钢表面质量的影响,获得最佳工艺参数。
模具是工业生产制造中不可或缺的基础工艺装备,其生产制件具有的高复杂性、高一致性和高生产率是其他加工制造工艺无法比拟的。模具广泛用于制造领域,但是,60%的模具都存在着早期失效的问题,其中表面质量问题占了绝大部分。现阶段,模具中主要采用热处理和喷丸处理来提高模具的表面硬度以延长使用寿命,但是由于热处理依赖操作人员的经验,所以造成模具质量良莠不齐,喷丸处理虽然可以明显提高模具的表面硬度及表面压应力,但是对于降低表面粗糙度的效果不佳。因此,模具行业的发展需要一种既能提高模具表面强度又能保证模具表面粗糙度的加工方法,强化研磨加工工艺在这种有利条件下发展出来的一种新型加工方法。
强化研磨加工是一种集“强化塑性加工”和“研磨微切削”为一体的金属表面冷加工方法,是一种多工艺结合的复合加工工艺。其在轴承加工方面具有明显的效果,具备较好的理论和技术的可行性。为此,可将强化研磨工艺应用于模具钢表面加工以提高表面质量,延长模具的使用寿命,通过单变量试验的方法,得出喷头移动速度、喷射压力和喷射距离等主要加工参数对模具钢表面质量的影响,获得最佳工艺参数。
1 实验设备与条件
采用自行搭建的数控强化研磨平台,其整体结构见图1。该实验平台的实现原理:空气压缩机压缩空气至储气罐,储气罐具有稳定气压的功能,将恒定的气压由气管引导至喷头,运用虹吸原理将钢丸和研磨液的混合物吸出,经过喷头时与高压空气混合形成固液气三相混合射流喷射至模具表面,从而进行强化加工。
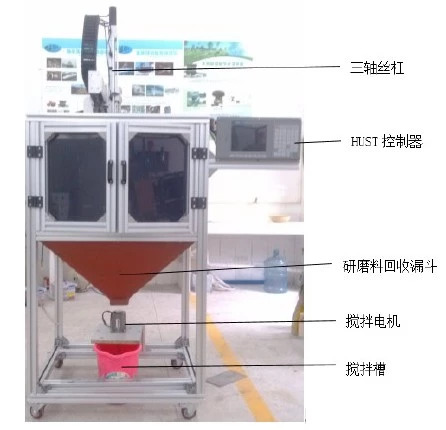
图1 强化研磨数控平台
强化研磨料的成分及配比见表1,采用单变量试验法,分成三组模具钢试样,其中每组试样包含两块模具钢,1#、2#、3#模具钢为未打磨,4#、5#、6#模具钢为经过砂纸打磨。其中1#与4#模具钢为一组,控制变量为喷射压力;2#与5#模具钢为一组,控制变量为喷头移动速度;3#与6#模具钢为一组,控制变量为喷射距离。
表1 强化研磨料成分及配比
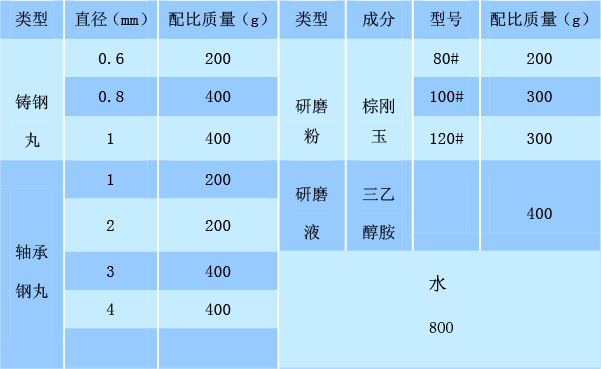
2 工艺参数与表面粗糙度对比分析
对每组样件采用相同的加工工艺,实验后采用TIME3230粗糙度测试仪对加工表面进行表面粗糙度测量,其数值可精确到纳米级,每条加工工艺均采用一定距离的10个点,舍弃最大值与最小值后求平均值,从而确保数据的准确性。将测量后的数据绘制成图表,由图可见,强化研磨工艺对降低模具表面粗糙度具有显著效果。
(1)喷射压力与表面粗糙度的关系
根据实验数据的平均值,绘制1#和4#模具钢在不同喷射压力下的表面粗糙度规律曲线(见图2);随着喷射压力由0逐渐增大时,4#模具钢的表面粗糙度先随着喷射压力逐渐升高,当喷射压力到达0.4MPa后,4#模具钢的表面粗糙度又逐渐降低。两条表面粗糙度规律曲线在喷射压力的0.5-0.6MPa区间是一个比较接近且变化缓慢的区域,趋于稳定。由此可知,针对初始表面形貌各不相同的模具钢,随着喷射压力的提高,模具钢的表面粗糙度都会趋向于1.5-1.6μm的区间。
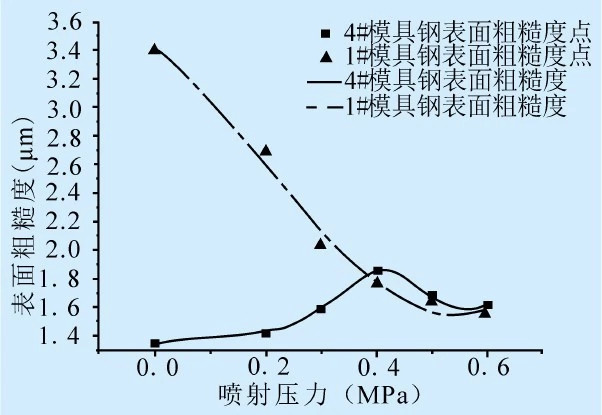
图2 喷射压力与表面粗糙度的规律曲线
(2)喷头移动速度与表面粗糙度的关系
根据实验数据的平均值,绘制2#和5#模具钢在不同喷头移动速度下的表面粗糙度规律曲线(见图3)。当喷头移动速度控制在10mm/min左右时,两条表面粗糙度规律曲线均在接近的一个区间,因此,模具钢的表面粗糙度在不同移动速度下能够达到的表面粗糙度是1.5-1.6μm。
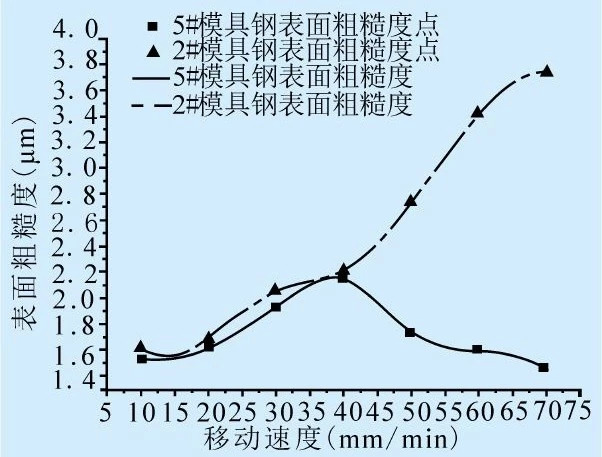
图3 喷头移动速度与表面粗糙度规律曲线
(3)喷射距离与表面粗糙度的关系
根据实验数据的平均值,绘制3#和6#模具钢在不同喷射距离下表面粗糙度规律曲线(见图4)。当喷射距离控制在10mm时,模具钢的表面粗糙度可降低到1.5-1.6μm。综上所述,针对初始形貌不同的模具钢,强化研磨加工所能够达到的精度是1.5-1.6μm。
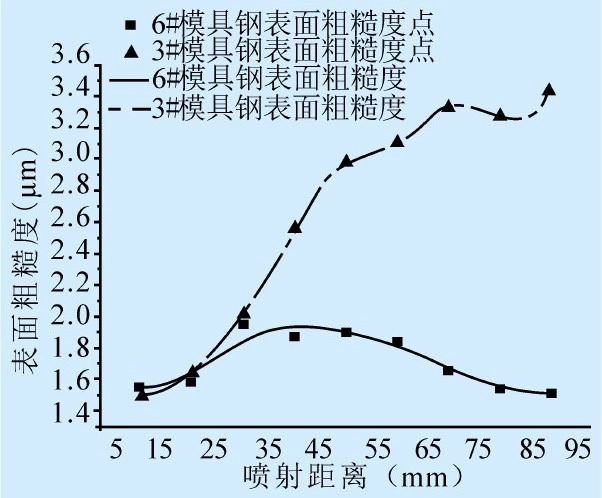
图4 喷射距离与表面粗糙度的规律曲线
第一组对比试验中,考虑在喷射压力0.5-0.6MPa之间时,表面粗糙度变化比较缓和,同时喷射压力越大能耗势必也会越大,因此在此选择0.5MPa作为较优的喷射压力。第二组实验中,喷头移动速度在10-20mm/min之间时,模具钢的表面粗糙度变化不大,但是考虑到加工速度越小,加工一块平面时所需的时间越大,其加工效率也就越低,因此选择20mm/min作为一个较优的的加工速度。第三组实验中,喷射距离为10-20mm时,模具钢表面粗糙度变化比较平缓,但是由于扩散作用的存在,20mm的喷射距离喷射到模具钢表面时,其加工范围较大,因此加工相同模具钢时,其用数控加工所需用的步数会越小,效率也就越高,在此组实验中选择20mm为较优的加工参数。
综合以上因素,当确定喷头直径8mm、喷射角度45°时,各组的比较理想的加工参数是:①喷射压力0.5MPa,喷头移动速度50mm/min,喷射距离45mm;②喷射压力0.4MPa,喷射速度10mm/min,喷射距离45mm;③喷射压力0.4MPa,喷头移动速度50mm/min,喷射距离10mm。
3 工艺参数与表面硬度的对比分析
采用压入硬度作为衡量模具钢表面硬度标准,采用JMTT数字洛氏硬度计进行硬度测量。对每组模具钢进行硬度测量,每一个工艺参数选择10个点进行测量,去除最大值和最小值,其余8个数值取平均值作为测量的硬度值。将实验后测得的数据,采用平均值绘制各参数之间的影响曲线。
由图5、图6和图7可知,强化研磨工艺加工不同表面形貌的模具钢时,模具钢表面硬度均可由加工前的50HRC提升至53-54HRC之间。试验分析可知,当喷射压力越大、喷头移动速度越慢、喷射距离越短时,模具钢表面塑性硬化层达到一定厚度后,要继续增厚硬化层会越来越困难,因此表面硬度的增加也越来越平缓。
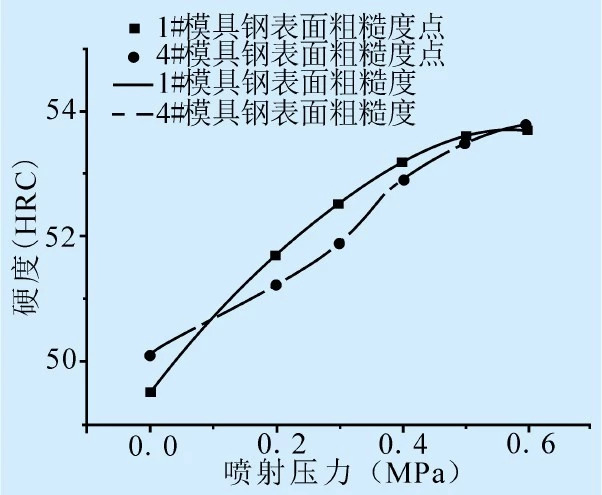
图5 喷射压力与表面硬度规律曲线
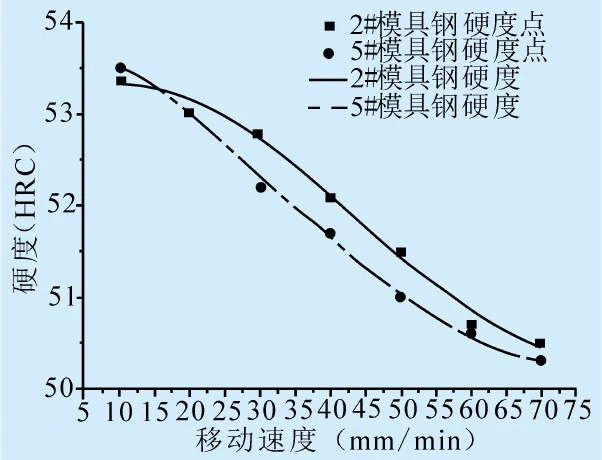
图6 喷头移动速度与表面硬度规律曲线
综合考虑加工能耗和加工效率,喷射压力不宜过大,能耗太大,损耗也会越大;喷射距离与移动速度不宜过小,过小所需的加工时间就越大,因此,每一组较优的加工参数为:①喷射压力0.5MPa,喷头移动速度50mm/min,喷射距离45mm;②喷射压力0.4MPa,喷头移动速度10mm/min,喷射距离45mm;③喷射压力0.4MPa,喷头移动速度50mm/min,喷射距离10mm。
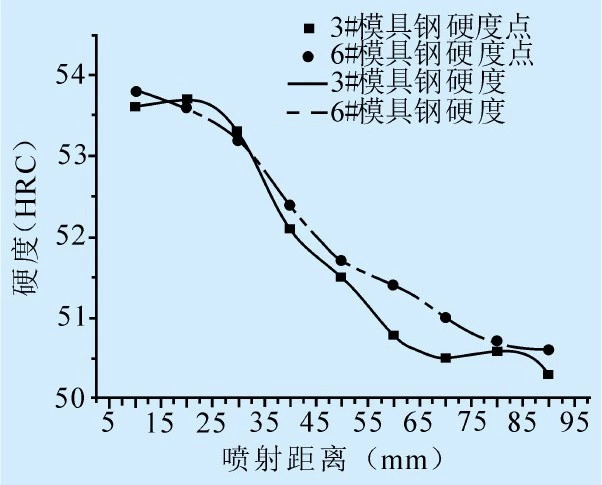
图7 喷射距离与表面硬度规律曲线
小结
根据六组对比实验分析,综合能耗因素和加工效率的影响,在确定喷头形状、喷嘴为8mm、喷射角度确定的情况下,使用以上三组加工参数加工45#模具钢时,所加工后的钢板表面粗糙度均可达到1.5-1.6μm,表面硬度由原来的50HRC均提升至53-54HRC。
根据能耗因素,在单位时间内,喷射压力越小,能耗越低,第二、三组加工参数为最优参数。但是由于第二组喷头移动速度为10mm/min,所以加工同一块模具钢所需的时间是第一组的5倍,整体的能耗并不会低于第一组。而第三组工艺参数的喷射距离为10mm,喷射范围比第一组小很多,因此加工同一块模具钢所需的步数会更多,加工时间也会更长,相比之下能耗也不会低于第一组。同时,从加工效率而言,第一组喷头移动速度和喷射距离都是最大的,因此在加工同一块模具钢时所需时间也最短。
综上所述,在喷头形式确定、喷嘴直径8mm、喷射角度45°时,对45#模具钢强化研磨加工的最佳工艺参数为:喷射压力0.5MPa,喷头移动速度50mm/min,喷射距离45mm。
强化研磨加工是一种集“强化塑性加工”和“研磨微切削”为一体的金属表面冷加工方法,是一种多工艺结合的复合加工工艺。其在轴承加工方面具有明显的效果,具备较好的理论和技术的可行性。为此,可将强化研磨工艺应用于模具钢表面加工以提高表面质量,延长模具的使用寿命,通过单变量试验的方法,得出喷头移动速度、喷射压力和喷射距离等主要加工参数对模具钢表面质量的影响,获得最佳工艺参数。
1 实验设备与条件
采用自行搭建的数控强化研磨平台,其整体结构见图1。该实验平台的实现原理:空气压缩机压缩空气至储气罐,储气罐具有稳定气压的功能,将恒定的气压由气管引导至喷头,运用虹吸原理将钢丸和研磨液的混合物吸出,经过喷头时与高压空气混合形成固液气三相混合射流喷射至模具表面,从而进行强化加工。
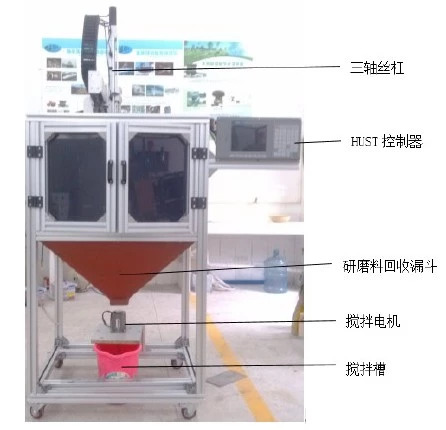
图1 强化研磨数控平台
强化研磨料的成分及配比见表1,采用单变量试验法,分成三组模具钢试样,其中每组试样包含两块模具钢,1#、2#、3#模具钢为未打磨,4#、5#、6#模具钢为经过砂纸打磨。其中1#与4#模具钢为一组,控制变量为喷射压力;2#与5#模具钢为一组,控制变量为喷头移动速度;3#与6#模具钢为一组,控制变量为喷射距离。
表1 强化研磨料成分及配比
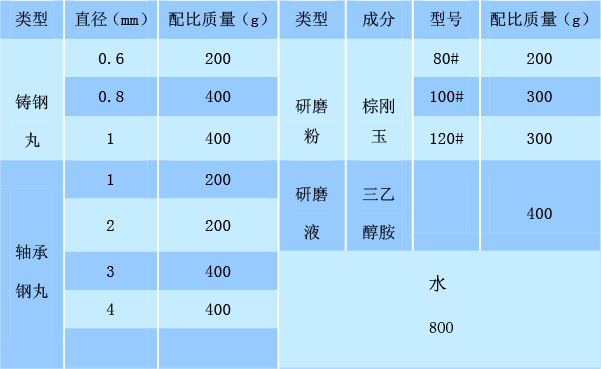
2 工艺参数与表面粗糙度对比分析
对每组样件采用相同的加工工艺,实验后采用TIME3230粗糙度测试仪对加工表面进行表面粗糙度测量,其数值可精确到纳米级,每条加工工艺均采用一定距离的10个点,舍弃最大值与最小值后求平均值,从而确保数据的准确性。将测量后的数据绘制成图表,由图可见,强化研磨工艺对降低模具表面粗糙度具有显著效果。
(1)喷射压力与表面粗糙度的关系
根据实验数据的平均值,绘制1#和4#模具钢在不同喷射压力下的表面粗糙度规律曲线(见图2);随着喷射压力由0逐渐增大时,4#模具钢的表面粗糙度先随着喷射压力逐渐升高,当喷射压力到达0.4MPa后,4#模具钢的表面粗糙度又逐渐降低。两条表面粗糙度规律曲线在喷射压力的0.5-0.6MPa区间是一个比较接近且变化缓慢的区域,趋于稳定。由此可知,针对初始表面形貌各不相同的模具钢,随着喷射压力的提高,模具钢的表面粗糙度都会趋向于1.5-1.6μm的区间。
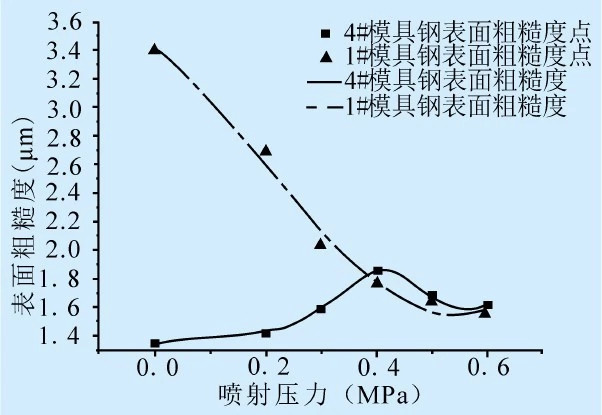
图2 喷射压力与表面粗糙度的规律曲线
(2)喷头移动速度与表面粗糙度的关系
根据实验数据的平均值,绘制2#和5#模具钢在不同喷头移动速度下的表面粗糙度规律曲线(见图3)。当喷头移动速度控制在10mm/min左右时,两条表面粗糙度规律曲线均在接近的一个区间,因此,模具钢的表面粗糙度在不同移动速度下能够达到的表面粗糙度是1.5-1.6μm。
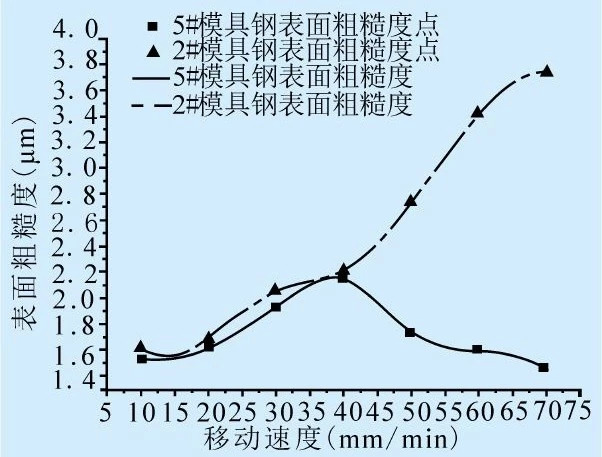
图3 喷头移动速度与表面粗糙度规律曲线
(3)喷射距离与表面粗糙度的关系
根据实验数据的平均值,绘制3#和6#模具钢在不同喷射距离下表面粗糙度规律曲线(见图4)。当喷射距离控制在10mm时,模具钢的表面粗糙度可降低到1.5-1.6μm。综上所述,针对初始形貌不同的模具钢,强化研磨加工所能够达到的精度是1.5-1.6μm。
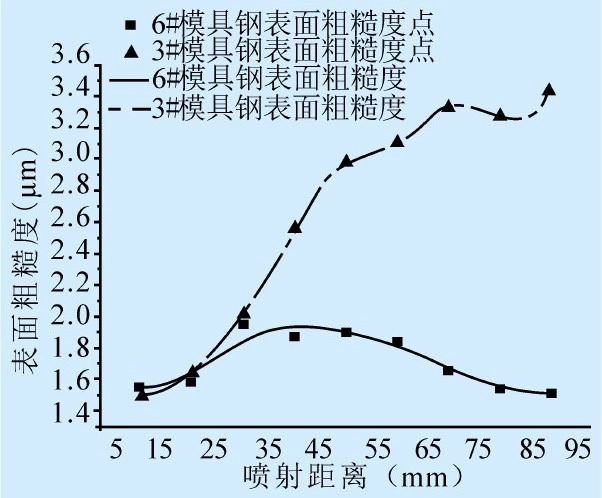
图4 喷射距离与表面粗糙度的规律曲线
第一组对比试验中,考虑在喷射压力0.5-0.6MPa之间时,表面粗糙度变化比较缓和,同时喷射压力越大能耗势必也会越大,因此在此选择0.5MPa作为较优的喷射压力。第二组实验中,喷头移动速度在10-20mm/min之间时,模具钢的表面粗糙度变化不大,但是考虑到加工速度越小,加工一块平面时所需的时间越大,其加工效率也就越低,因此选择20mm/min作为一个较优的的加工速度。第三组实验中,喷射距离为10-20mm时,模具钢表面粗糙度变化比较平缓,但是由于扩散作用的存在,20mm的喷射距离喷射到模具钢表面时,其加工范围较大,因此加工相同模具钢时,其用数控加工所需用的步数会越小,效率也就越高,在此组实验中选择20mm为较优的加工参数。
综合以上因素,当确定喷头直径8mm、喷射角度45°时,各组的比较理想的加工参数是:①喷射压力0.5MPa,喷头移动速度50mm/min,喷射距离45mm;②喷射压力0.4MPa,喷射速度10mm/min,喷射距离45mm;③喷射压力0.4MPa,喷头移动速度50mm/min,喷射距离10mm。
3 工艺参数与表面硬度的对比分析
采用压入硬度作为衡量模具钢表面硬度标准,采用JMTT数字洛氏硬度计进行硬度测量。对每组模具钢进行硬度测量,每一个工艺参数选择10个点进行测量,去除最大值和最小值,其余8个数值取平均值作为测量的硬度值。将实验后测得的数据,采用平均值绘制各参数之间的影响曲线。
由图5、图6和图7可知,强化研磨工艺加工不同表面形貌的模具钢时,模具钢表面硬度均可由加工前的50HRC提升至53-54HRC之间。试验分析可知,当喷射压力越大、喷头移动速度越慢、喷射距离越短时,模具钢表面塑性硬化层达到一定厚度后,要继续增厚硬化层会越来越困难,因此表面硬度的增加也越来越平缓。
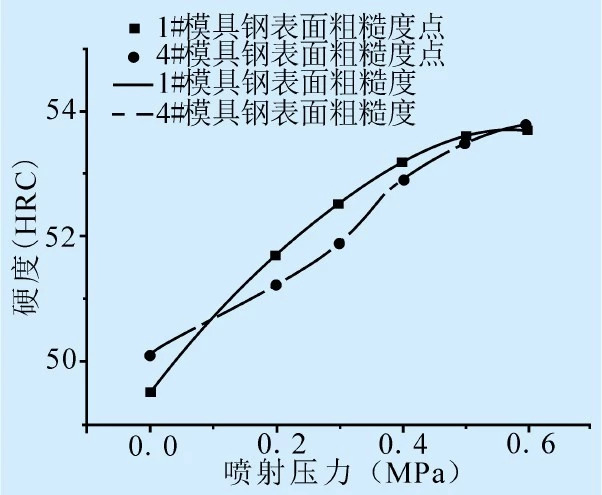
图5 喷射压力与表面硬度规律曲线
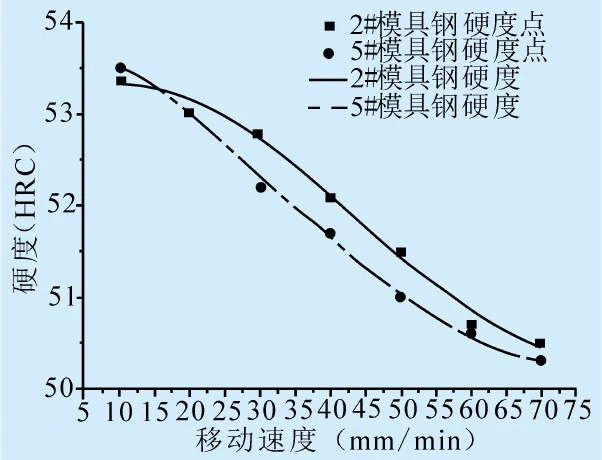
图6 喷头移动速度与表面硬度规律曲线
综合考虑加工能耗和加工效率,喷射压力不宜过大,能耗太大,损耗也会越大;喷射距离与移动速度不宜过小,过小所需的加工时间就越大,因此,每一组较优的加工参数为:①喷射压力0.5MPa,喷头移动速度50mm/min,喷射距离45mm;②喷射压力0.4MPa,喷头移动速度10mm/min,喷射距离45mm;③喷射压力0.4MPa,喷头移动速度50mm/min,喷射距离10mm。
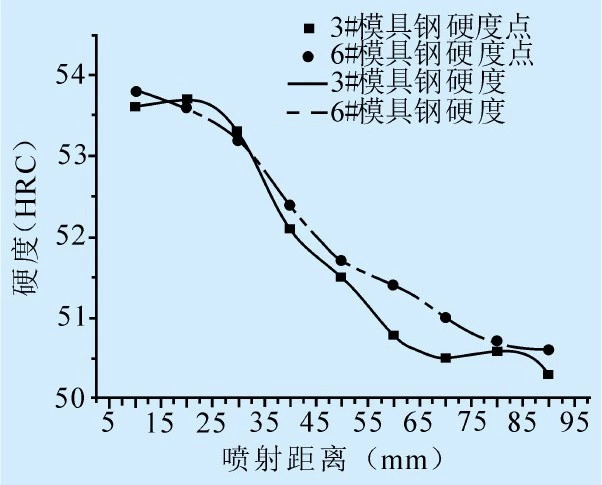
图7 喷射距离与表面硬度规律曲线
小结
根据六组对比实验分析,综合能耗因素和加工效率的影响,在确定喷头形状、喷嘴为8mm、喷射角度确定的情况下,使用以上三组加工参数加工45#模具钢时,所加工后的钢板表面粗糙度均可达到1.5-1.6μm,表面硬度由原来的50HRC均提升至53-54HRC。
根据能耗因素,在单位时间内,喷射压力越小,能耗越低,第二、三组加工参数为最优参数。但是由于第二组喷头移动速度为10mm/min,所以加工同一块模具钢所需的时间是第一组的5倍,整体的能耗并不会低于第一组。而第三组工艺参数的喷射距离为10mm,喷射范围比第一组小很多,因此加工同一块模具钢所需的步数会更多,加工时间也会更长,相比之下能耗也不会低于第一组。同时,从加工效率而言,第一组喷头移动速度和喷射距离都是最大的,因此在加工同一块模具钢时所需时间也最短。
综上所述,在喷头形式确定、喷嘴直径8mm、喷射角度45°时,对45#模具钢强化研磨加工的最佳工艺参数为:喷射压力0.5MPa,喷头移动速度50mm/min,喷射距离45mm。
举报 0
收藏 0
分享 107
-
埃马克德国总部迎来中国社科院工业经济研究所代
2025-04-15 -
埃马克这项全新应用即将在CIMT惊艳首秀!
2025-04-15 -
[转载] 机床巨头埃马克:百年跌宕再出发
2025-03-31 -
赋能电动未来,埃马克重庆技术日展示尖端制造技
2025-03-03
编辑推荐
最新资讯
-
全球产业链聚沪 共探双碳新路径 SNEC
2025-04-18 18:05
-
柯马签订具有约束力的协议收购 Autom
2025-04-17 13:01
-
高效协同新范式:比亚迪叉车领创智能
2025-04-17 10:04
-
埃马克德国总部迎来中国社科院工业经
2025-04-15 09:40
-
埃马克这项全新应用即将在CIMT惊艳首
2025-04-15 09:37