房车转向节前臂弯曲工艺优化与模具装置研发及应用
2018-09-12 09:15:21· 来源:锻造与冲压 作者:夏巨谌
房车转向节是自驾旅游用车的核心零部件,轮廊尺寸大,结构极其复杂。针对目前采用分体制造存在的诸多问题,提出了整体模锻成形的工艺方案,并对其关键工序弯曲成形工艺进行了优化与专用模具装置开发。结果表明,所提方案合理先进,实现了
房车转向节是自驾旅游用车的核心零部件,轮廊尺寸大,结构极其复杂。针对目前采用分体制造存在的诸多问题,提出了整体模锻成形的工艺方案,并对其关键工序弯曲成形工艺进行了优化与专用模具装置开发。结果表明,所提方案合理先进,实现了以整体模锻取代分体制造,所生产的房车转向节满足了美国客户的技术要求。
房车是集交通、餐饮和住宿于一体的专用汽车。近年来,自驾旅游在美国和欧洲等发达国家发展迅速,近两年来我国人民因改革开放生活水平大幅提高,节假日和双休日私家车车主和亲朋好友自驾游发展迅猛,对房车的需求不断增长,由此,带动了房车制造所需一些关键零部件的发展。
三环锻造有限公司是汽车转向节专业化生产企业,年产各种汽车转向节系列产品1000多种,200万件,超过100万吨,除国内东风、一汽外,国外客户有戴姆勒奔驰公司、荷兰DAF公司、印度塔塔和利兰公司、美国TRP等公司,国际业务已占公司销售总额的25%以上。因产品质量好,供货准时,可满足客户特殊要求,因此,2016年,美国某知名公司要求为其生产房车A223型转向节,并主动提供了研发费用。
房车转向节结构特点
常用汽车转向节和房车A223型转向节锻件如图1所示。A223型转向节锻件二维图如图2所示。其锻件的复杂系数为S=V锻/V包=0.075≤0.16,这表示该型转向节为最复杂的枝杈类锻件。它与常用载重车的转向节的最大差别就是一个直线前臂特别长,另一个稍短的前臂与杆部及直线长臂的轴线方向成90°弯曲。
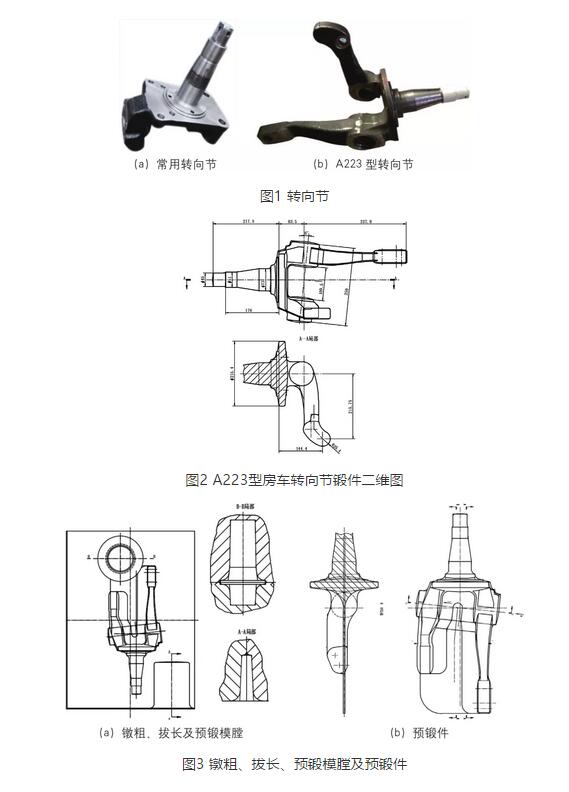
目前,这种房车转向节锻件的生产,国内尚为空白,现有工艺是将前臂与杆部和法兰分开锻造经机加工后采用螺栓连接为一体。不难看出,分体制造存在的突出问题是,不仅材料利用率低,加热能耗高,生产效率低,产品性能差,而且很难实现轻量化。
房车转向节整体模锻工艺简介
公司接到订单后,立即同华中科技大学夏巨谌教授及其课题组合作进行研发,针对房车转向节结构特点及分体制造存在的诸多问题。经过分析并参考公司生产异形转向节锻件的经验,制定了如下整体模锻工艺方案:下料→加热→第一次制坯局部镦粗→第二次制坯杆部拔长→预锻→终锻→切边→(加热)→弯曲及校正。
第一次制坯局部镦粗是采用闭式镦粗工艺,对坯料上对应于转向节法兰盘的位置将其局部镦粗,其中间局部镦粗及镦粗模具如图3(a)中B-B局部剖视图所示;第二次拔杆制坯是将局部镦粗所成形出的工件,对应于转向节杆部的一段进行拔长,如图3(a)中A-A局部剖视图所示;预锻是将经过两道制坯的工件在预锻模膛中成形为将弯曲前臂沿轴线伸直成与直线长臂平行的叉形件,预锻模膛如图3(a)中间俯视图所示,所成形的预锻件如图3(a)所示;终锻是将预锻件通过终锻模膛成形为具有两个直前臂的锻件,这相当于一般模锻生产的最后成形;切边后的锻件如图4(a)实线所示。弯曲成形是将切边后的锻件长度较短的前臂在专用装置上弯曲成形,得到最终锻件。
弯曲成形机理及工艺优化研究
弯曲成形机理:弯曲成形分为自由弯曲成形和强制弯曲成形两种,自由弯曲成形时在坯料的中线形成中性层,中性层以内产生压应变和压应力,中性层以外产生拉应变和拉应力。本文研究的房车转向节前臂弯曲是在模膛内强制弯曲成形,弯曲臂在弯曲前的初始状态如图4(a)实线所示,弯曲后的状态如图4(a)虚线所示。
如上所述,图4所示弯曲是前臂在上、下凹模对应的模膛内发生弯曲。前臂左端与法兰相连,弯曲圆心紧靠法兰,弯曲主要发生在垂直轴线的右边,且完全是拉伸变形,即自前臂的下面至上面均为拉伸变形,相应的应力也为拉伸应力,两者的分布规律如图4(b)所示;选择Z轴为圆柱体的轴向坐标,则变形体内的应力与应变状态如图4(c)所示,由图可知,沿切向为拉应力σθ,沿轴向σz和径向σρ均为压应力;其应变的方向与应力的方向相同。
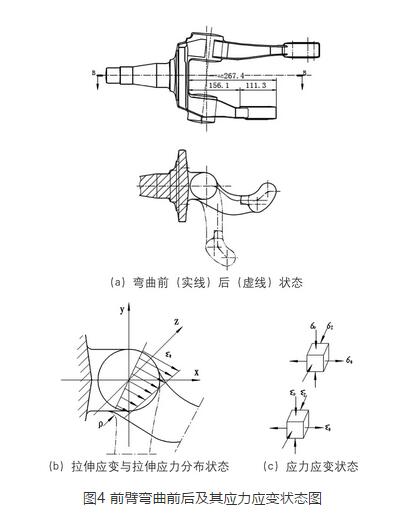
由上面的分析可知,前臂弯曲成形的实质是近似纯拉伸成形。因此,以此为基础,分析得到前臂弯曲前的形状和尺寸的优化设计方法。
优化方法及步骤:
⑴采用UG或PRO/E软件对A223转向节锻件进行三维实体造型,在计算出整个锻件体积的同时,也分别计算出被弯曲的前臂及已成形的端部的体积V臂、V端,进而得到弯曲前杆部的体积V杆=V臂-V端;
⑵因弯曲成形是在模膛内闭式弯曲成形,其特点是杆部宽度保持不变、高度减小、长度大幅延伸的近似于拉伸伸长成形,所以弯曲成形前的直杆(预弯杆)较弯曲成形后的杆部其截面增大而长度缩短,为了预弯杆顺利放入弯曲模膛,取预弯杆的宽度B杆=B弯-(1~1.5)mm,B弯为弯曲模膛宽度,即宽度B杆已知,因圆台纵坐标至右端与法兰盘相连接部分的高度与弯曲后对应高度相等,右端高度与前端左边高度相等,所以弯曲前的前臂杆部为宽度(B杆)、左端及右端横截面的高度及体积(V杆)均已知的左高右低且底面为平面的梯形,进而可求出预弯杆部的长度L杆。至此,可得到预弯杆部的形状及主要尺寸,如图2(a)实线图形及标注所示。
由锻件工步图(未示出)上的标注可知,前臂杆部弯曲前、后的长度分别为l0=101.1mm、l1=154.9mm,其伸长量为Δl=l1-l0=53.8mm,相应的伸长变形程度为εF=(Δl/l0)×100%=53.2%。锻件材料为42CrMo,弯曲时工件温度为900~1000℃,其允许最大变形程度[εF]≤80%~85%。由εF<[εF]表明,其弯曲工艺设计合理安全。
弯曲专用模具装置研制
基本结构:图5所示为笔者提出的专用弯曲模具装置,其基本结构由模架、上凹模提升及压紧机构、凸凹模工作部分所组成。模架由下模板、中模板、上模板和下导柱、下压环、下导套、上导套、上导柱及上压环等组成;下导套与上导套固定在中模板上,下导柱、上导柱分别固定在下模板和上模板上,四组导柱、导套分布在模板的四角;上凹模提升及压紧机构由四组法兰筒及拉杆和四组活塞杆及油缸组成,其连接与固定方式如图5所示;凸凹模工作部分由凸模及凸模座、上凹模和下凹模组成,凸模与凸模座用两个柱销连接,凸模座固定在上模板的凹坑中,上凹模固定在中模板下面,下凹模固定下模板上;此外,还有顶杆。该装置安装在通用液压机上使用。按照图5所示基本结构及原理研制出的专用模具装置照片如图6所示。
工作过程及原理:
⑴操作液压机使滑块带动上模板及固定在上模板上的所有零件上行,当上行至法兰筒的底部同拉杆的圆柱头部接触时,带动中模板及固定在其上的所有零件一起上行至上限位置;同时,随着活塞杆上行,将低压油吸入油缸下腔;
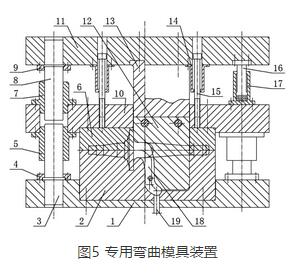
1-下模板 2-下凹模 3-下导柱 4-下压环 5-下导套6-上凹模 7-上导套 8-上导柱 9-上压环 10-中模板11-上模板 12-凸模 13-凸模座 14-法兰筒 15-拉杆16-活塞杆 17-油缸 18-工件 19-顶杆
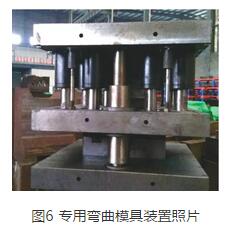
⑵将已切边的锻件放入下凹模中;
⑶操作液压机滑块及与其固定及连接在一起的所有零件下行,当下行至上凹模与下凹模相碰时,中模板及其固定与连接在一起的零件均处于静止状态,随着滑块继续下行,活塞杆压缩油缸下腔的油液,由高压液流阀产生的油压通过上凹模将锻件的杆部、法兰及长前臂压紧,同时凸模迫使短前臂向下弯曲成形并同时对杆部法兰和直长臂进行校正;
⑷校正弯曲成形结束时,滑块带动上模板及其固定在上面的所有零件一起向上回程,回程过程与第一步相同,在回程的同时,下顶出器通过顶杆将锻件从下凹模中顶出,一个工作循环结束。
工艺试验及生产应用
锻件材料为42CrMo,坯料尺寸为φ125mm×458 mm,采用公司现有的中频感应加热炉、5t模锻锤、10t模锻锤、800t曲柄压力机和630t四立柱通用液压机为试验和小批量生产设备,将制坯及预锻模、终锻模、冲模及图5所示弯曲专用模具装置分别安装在对应的设备上使用。试验完全按照前述工艺流程进行,试验中采用水基石墨润滑剂进行喷雾式润滑,试验所得A223房车转向节锻件并经初步机加工的产品如图1(b)所示,达到了美国客户的技术标准和要求,并已开始小批量供货。
所试验出的锻件经光学快速精密测量完全达到美国用户的技术标准。已经进行了小批量生产供用户使用。
目前正在设计并建立中频感应加热炉→辊锻机制坯→1600t数控电动螺旋压力机预锻→2500t数控电动螺旋压力机终锻→800t曲柄压力机切边→630t液压机校正及弯曲成形,采用机器人操作的全自动化生产线,将实现大批量生产,以满足国内外迅速增长的市场需求。
采用整体模锻技术生产A223房车转向节同分体制造然后采用螺栓连接为一体的技术生产转向节比较:材料利用率由约45%提高到70%以上;节约加热能耗35%以上;生产效率提高4~5倍,产品力学性能大为提高。
结论
⑴针对A223房车转向节的结构特点,所研发的整体模锻关键技术及模具装置同现有的分体制造技术生产转向节锻件比较,具有节材、节能、提高生产效率和产品质量的突出优点,这对具有弯曲前臂转向节的整体模锻具有推广应用价值。
⑵正在建立的全自动化生产线,为房车转向节这类复杂枝杈类零件整体模锻批量生产奠定了坚实基础。
本文节选自《锻造与冲压》2018.17期。
房车是集交通、餐饮和住宿于一体的专用汽车。近年来,自驾旅游在美国和欧洲等发达国家发展迅速,近两年来我国人民因改革开放生活水平大幅提高,节假日和双休日私家车车主和亲朋好友自驾游发展迅猛,对房车的需求不断增长,由此,带动了房车制造所需一些关键零部件的发展。
三环锻造有限公司是汽车转向节专业化生产企业,年产各种汽车转向节系列产品1000多种,200万件,超过100万吨,除国内东风、一汽外,国外客户有戴姆勒奔驰公司、荷兰DAF公司、印度塔塔和利兰公司、美国TRP等公司,国际业务已占公司销售总额的25%以上。因产品质量好,供货准时,可满足客户特殊要求,因此,2016年,美国某知名公司要求为其生产房车A223型转向节,并主动提供了研发费用。
房车转向节结构特点
常用汽车转向节和房车A223型转向节锻件如图1所示。A223型转向节锻件二维图如图2所示。其锻件的复杂系数为S=V锻/V包=0.075≤0.16,这表示该型转向节为最复杂的枝杈类锻件。它与常用载重车的转向节的最大差别就是一个直线前臂特别长,另一个稍短的前臂与杆部及直线长臂的轴线方向成90°弯曲。
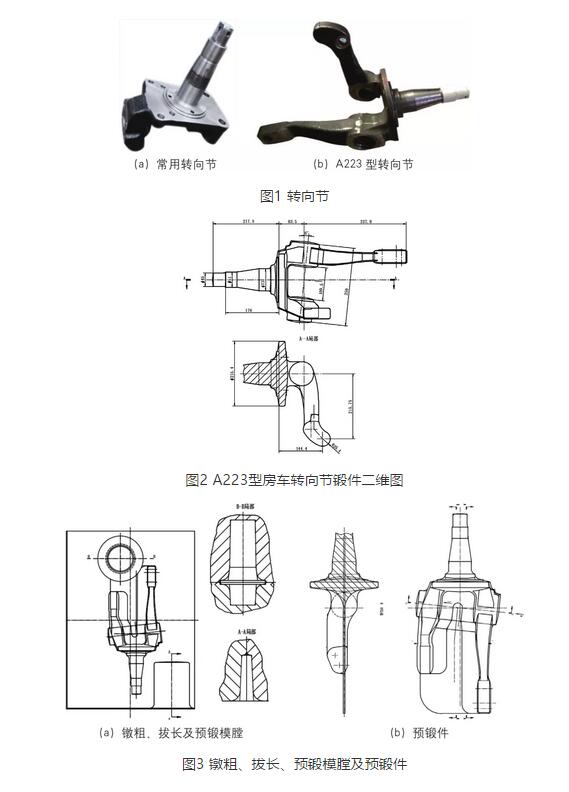
目前,这种房车转向节锻件的生产,国内尚为空白,现有工艺是将前臂与杆部和法兰分开锻造经机加工后采用螺栓连接为一体。不难看出,分体制造存在的突出问题是,不仅材料利用率低,加热能耗高,生产效率低,产品性能差,而且很难实现轻量化。
房车转向节整体模锻工艺简介
公司接到订单后,立即同华中科技大学夏巨谌教授及其课题组合作进行研发,针对房车转向节结构特点及分体制造存在的诸多问题。经过分析并参考公司生产异形转向节锻件的经验,制定了如下整体模锻工艺方案:下料→加热→第一次制坯局部镦粗→第二次制坯杆部拔长→预锻→终锻→切边→(加热)→弯曲及校正。
第一次制坯局部镦粗是采用闭式镦粗工艺,对坯料上对应于转向节法兰盘的位置将其局部镦粗,其中间局部镦粗及镦粗模具如图3(a)中B-B局部剖视图所示;第二次拔杆制坯是将局部镦粗所成形出的工件,对应于转向节杆部的一段进行拔长,如图3(a)中A-A局部剖视图所示;预锻是将经过两道制坯的工件在预锻模膛中成形为将弯曲前臂沿轴线伸直成与直线长臂平行的叉形件,预锻模膛如图3(a)中间俯视图所示,所成形的预锻件如图3(a)所示;终锻是将预锻件通过终锻模膛成形为具有两个直前臂的锻件,这相当于一般模锻生产的最后成形;切边后的锻件如图4(a)实线所示。弯曲成形是将切边后的锻件长度较短的前臂在专用装置上弯曲成形,得到最终锻件。
弯曲成形机理及工艺优化研究
弯曲成形机理:弯曲成形分为自由弯曲成形和强制弯曲成形两种,自由弯曲成形时在坯料的中线形成中性层,中性层以内产生压应变和压应力,中性层以外产生拉应变和拉应力。本文研究的房车转向节前臂弯曲是在模膛内强制弯曲成形,弯曲臂在弯曲前的初始状态如图4(a)实线所示,弯曲后的状态如图4(a)虚线所示。
如上所述,图4所示弯曲是前臂在上、下凹模对应的模膛内发生弯曲。前臂左端与法兰相连,弯曲圆心紧靠法兰,弯曲主要发生在垂直轴线的右边,且完全是拉伸变形,即自前臂的下面至上面均为拉伸变形,相应的应力也为拉伸应力,两者的分布规律如图4(b)所示;选择Z轴为圆柱体的轴向坐标,则变形体内的应力与应变状态如图4(c)所示,由图可知,沿切向为拉应力σθ,沿轴向σz和径向σρ均为压应力;其应变的方向与应力的方向相同。
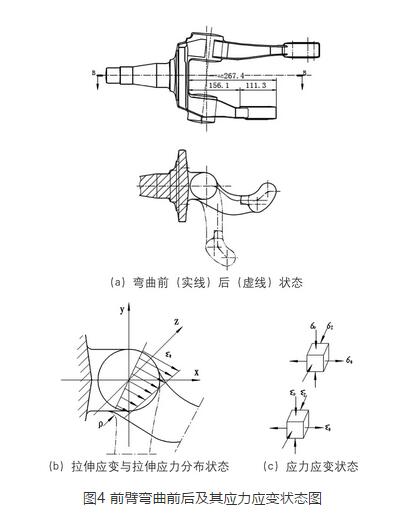
由上面的分析可知,前臂弯曲成形的实质是近似纯拉伸成形。因此,以此为基础,分析得到前臂弯曲前的形状和尺寸的优化设计方法。
优化方法及步骤:
⑴采用UG或PRO/E软件对A223转向节锻件进行三维实体造型,在计算出整个锻件体积的同时,也分别计算出被弯曲的前臂及已成形的端部的体积V臂、V端,进而得到弯曲前杆部的体积V杆=V臂-V端;
⑵因弯曲成形是在模膛内闭式弯曲成形,其特点是杆部宽度保持不变、高度减小、长度大幅延伸的近似于拉伸伸长成形,所以弯曲成形前的直杆(预弯杆)较弯曲成形后的杆部其截面增大而长度缩短,为了预弯杆顺利放入弯曲模膛,取预弯杆的宽度B杆=B弯-(1~1.5)mm,B弯为弯曲模膛宽度,即宽度B杆已知,因圆台纵坐标至右端与法兰盘相连接部分的高度与弯曲后对应高度相等,右端高度与前端左边高度相等,所以弯曲前的前臂杆部为宽度(B杆)、左端及右端横截面的高度及体积(V杆)均已知的左高右低且底面为平面的梯形,进而可求出预弯杆部的长度L杆。至此,可得到预弯杆部的形状及主要尺寸,如图2(a)实线图形及标注所示。
由锻件工步图(未示出)上的标注可知,前臂杆部弯曲前、后的长度分别为l0=101.1mm、l1=154.9mm,其伸长量为Δl=l1-l0=53.8mm,相应的伸长变形程度为εF=(Δl/l0)×100%=53.2%。锻件材料为42CrMo,弯曲时工件温度为900~1000℃,其允许最大变形程度[εF]≤80%~85%。由εF<[εF]表明,其弯曲工艺设计合理安全。
弯曲专用模具装置研制
基本结构:图5所示为笔者提出的专用弯曲模具装置,其基本结构由模架、上凹模提升及压紧机构、凸凹模工作部分所组成。模架由下模板、中模板、上模板和下导柱、下压环、下导套、上导套、上导柱及上压环等组成;下导套与上导套固定在中模板上,下导柱、上导柱分别固定在下模板和上模板上,四组导柱、导套分布在模板的四角;上凹模提升及压紧机构由四组法兰筒及拉杆和四组活塞杆及油缸组成,其连接与固定方式如图5所示;凸凹模工作部分由凸模及凸模座、上凹模和下凹模组成,凸模与凸模座用两个柱销连接,凸模座固定在上模板的凹坑中,上凹模固定在中模板下面,下凹模固定下模板上;此外,还有顶杆。该装置安装在通用液压机上使用。按照图5所示基本结构及原理研制出的专用模具装置照片如图6所示。
工作过程及原理:
⑴操作液压机使滑块带动上模板及固定在上模板上的所有零件上行,当上行至法兰筒的底部同拉杆的圆柱头部接触时,带动中模板及固定在其上的所有零件一起上行至上限位置;同时,随着活塞杆上行,将低压油吸入油缸下腔;
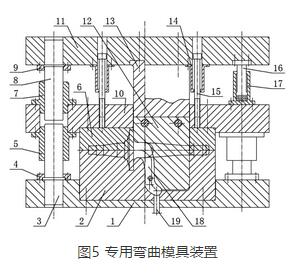
1-下模板 2-下凹模 3-下导柱 4-下压环 5-下导套6-上凹模 7-上导套 8-上导柱 9-上压环 10-中模板11-上模板 12-凸模 13-凸模座 14-法兰筒 15-拉杆16-活塞杆 17-油缸 18-工件 19-顶杆
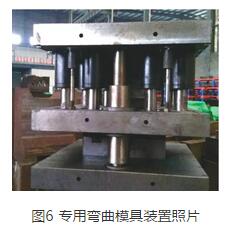
⑵将已切边的锻件放入下凹模中;
⑶操作液压机滑块及与其固定及连接在一起的所有零件下行,当下行至上凹模与下凹模相碰时,中模板及其固定与连接在一起的零件均处于静止状态,随着滑块继续下行,活塞杆压缩油缸下腔的油液,由高压液流阀产生的油压通过上凹模将锻件的杆部、法兰及长前臂压紧,同时凸模迫使短前臂向下弯曲成形并同时对杆部法兰和直长臂进行校正;
⑷校正弯曲成形结束时,滑块带动上模板及其固定在上面的所有零件一起向上回程,回程过程与第一步相同,在回程的同时,下顶出器通过顶杆将锻件从下凹模中顶出,一个工作循环结束。
工艺试验及生产应用
锻件材料为42CrMo,坯料尺寸为φ125mm×458 mm,采用公司现有的中频感应加热炉、5t模锻锤、10t模锻锤、800t曲柄压力机和630t四立柱通用液压机为试验和小批量生产设备,将制坯及预锻模、终锻模、冲模及图5所示弯曲专用模具装置分别安装在对应的设备上使用。试验完全按照前述工艺流程进行,试验中采用水基石墨润滑剂进行喷雾式润滑,试验所得A223房车转向节锻件并经初步机加工的产品如图1(b)所示,达到了美国客户的技术标准和要求,并已开始小批量供货。
所试验出的锻件经光学快速精密测量完全达到美国用户的技术标准。已经进行了小批量生产供用户使用。
目前正在设计并建立中频感应加热炉→辊锻机制坯→1600t数控电动螺旋压力机预锻→2500t数控电动螺旋压力机终锻→800t曲柄压力机切边→630t液压机校正及弯曲成形,采用机器人操作的全自动化生产线,将实现大批量生产,以满足国内外迅速增长的市场需求。
采用整体模锻技术生产A223房车转向节同分体制造然后采用螺栓连接为一体的技术生产转向节比较:材料利用率由约45%提高到70%以上;节约加热能耗35%以上;生产效率提高4~5倍,产品力学性能大为提高。
结论
⑴针对A223房车转向节的结构特点,所研发的整体模锻关键技术及模具装置同现有的分体制造技术生产转向节锻件比较,具有节材、节能、提高生产效率和产品质量的突出优点,这对具有弯曲前臂转向节的整体模锻具有推广应用价值。
⑵正在建立的全自动化生产线,为房车转向节这类复杂枝杈类零件整体模锻批量生产奠定了坚实基础。
本文节选自《锻造与冲压》2018.17期。
举报 0
收藏 0
分享 96
-
冲压技术在电机叠片制造的应用
2024-09-06 -
车身零部件包边质量控制要点
2024-09-05 -
轻量化技术——热汽胀形工艺技术解析
2024-09-04 -
高强板车身件冲压技术
2024-09-02
最新资讯
-
全球产业链聚沪 共探双碳新路径 SNEC
2025-04-18 18:05
-
柯马签订具有约束力的协议收购 Autom
2025-04-17 13:01
-
高效协同新范式:比亚迪叉车领创智能
2025-04-17 10:04
-
埃马克德国总部迎来中国社科院工业经
2025-04-15 09:40
-
埃马克这项全新应用即将在CIMT惊艳首
2025-04-15 09:37