铝合金在汽车轻量化中的应用:仿真引领汽车设计
2018-12-03 09:22:37· 来源:Fields COMSOL 作者:Sarah
近年来,随着汽车制造商和消费者环保意识的提升,汽车正向着轻量化的方向发展。当车身重量减少 10%,汽车的燃油效率可以提高约 8%。为了实现轻量化设计目标,制造商需要将传统的车体结构材料和车身材料(例如结构钢)与更轻质的材料结合
近年来,随着汽车制造商和消费者环保意识的提升,汽车正向着轻量化的方向发展。当车身重量减少 10%,汽车的燃油效率可以提高约 8%。为了实现轻量化设计目标,制造商需要将传统的车体结构材料和车身材料(例如结构钢)与更轻质的材料结合在一起。铝(图 1)的密度只有钢的三分之一,具有耐候性强、回收利用率高、易于加工成型、防撞性强等优点,因此成为了极具潜力的汽车轻量化材料。
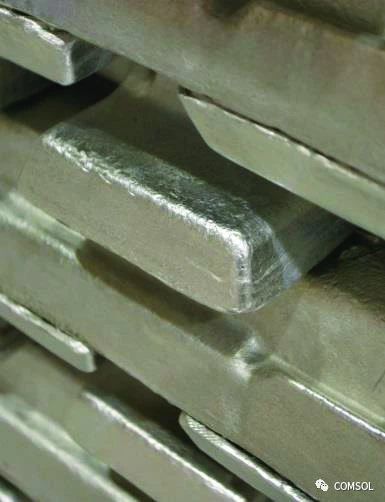
图 1. 高压压铸(high-pressure die casting)的铝合金。
然而,开发混合使用钢与铝合金材料的汽车困难重重,其中包括:如何开发低成本的量产技术;如何在部分零件中用铝质材料替代原有材料,实现多材料装配;如何降低因电解质(如洒在道路上的除冰盐)导致的相互接触的异种金属间产生电偶腐蚀的风险(图 2)。
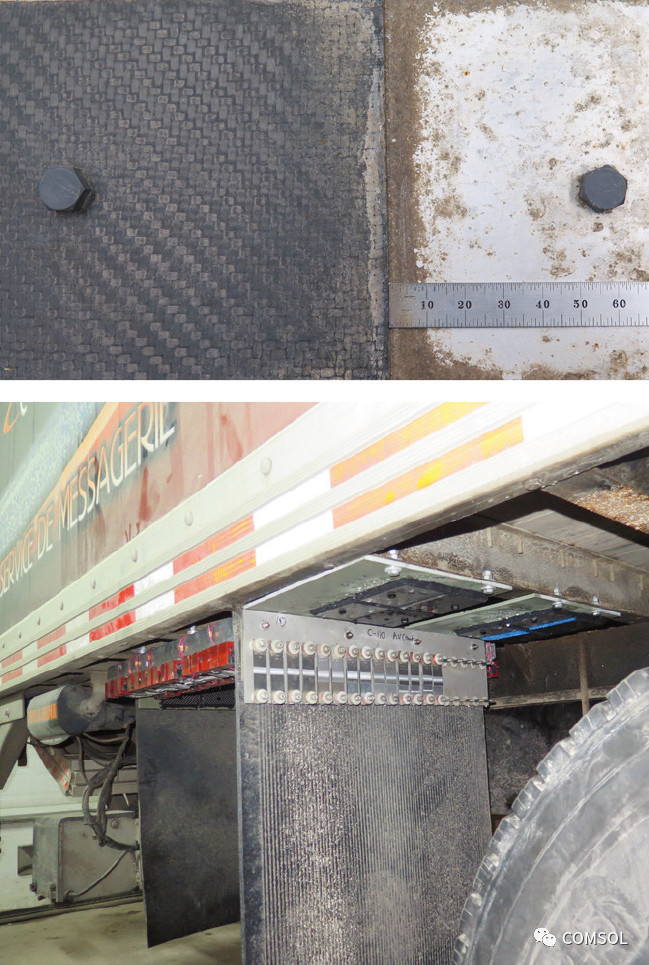
图 2.上:经过一年在役暴露实验后,由碳纤维增强聚合物(carbon-fiber-reinforcedpolymer,简称 CFRP)和6000系列铝合金制成的多材料叠加式装配制成的车身上的电偶腐蚀情况。下:用于车辆运行测试的汽车样件常见安装方式。
Danick Gallant 是加拿大国家研究院(NRC)汽车和地面运输研究中心(Automotive and Surface Transportation Research Center)的技术主管,负责腐蚀控制技术以及耐腐蚀部件和装配的研发工作。在工业领域的应用中,单焊缝连接会涉及多种腐蚀问题,例如缝隙腐蚀和电偶腐蚀(图 3),这就给汽车行业带来了巨大的挑战。NRC 及其合作伙伴 ALTec 多客户铝技术研发合作集团(图 4),共同致力于推动铝合金在轻量化设计中的应用,并为运输行业提供针对上述问题的技术支持和解决方案。
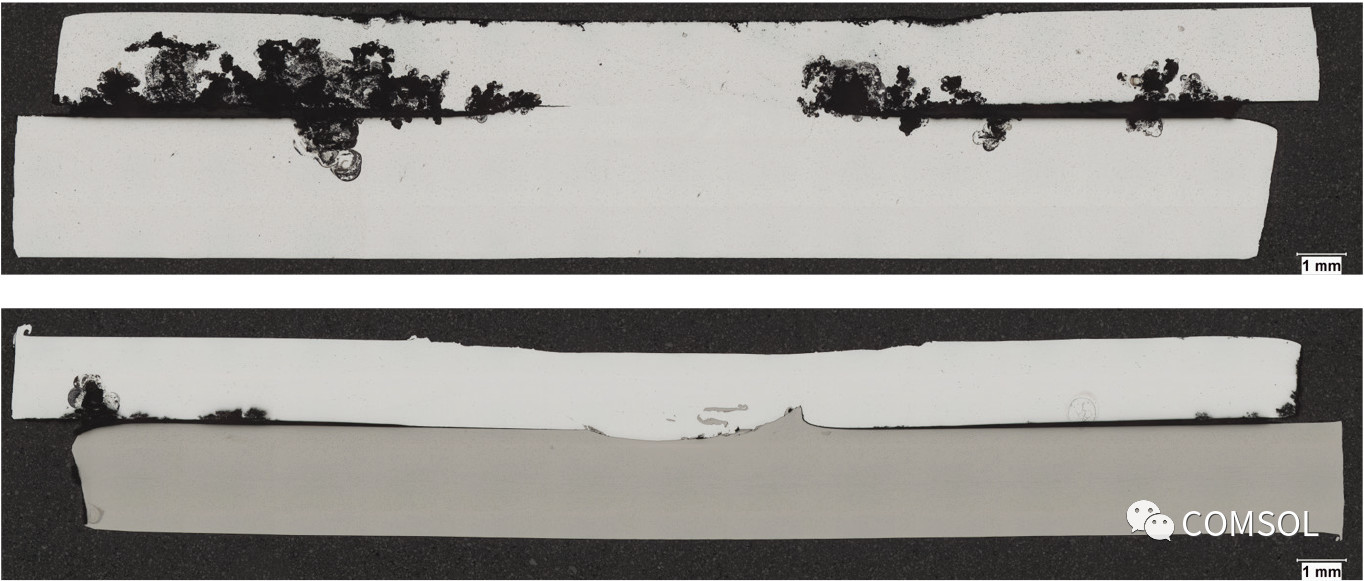
图 3.车辆经过 10 万公里的公路行驶后,车轮和挡泥板之间经搅拌摩擦焊接(friction-stir welded,简称 FSW)而成的多材料装配剖视图。上:在 AA7000 系列与 AA6000 系列的 FSW 装配中,缝隙腐蚀为主要的腐蚀方式。下:在 AA5000 系列与不锈钢 300 系列的 FSW 装配中,电偶腐蚀为主要的腐蚀方式。
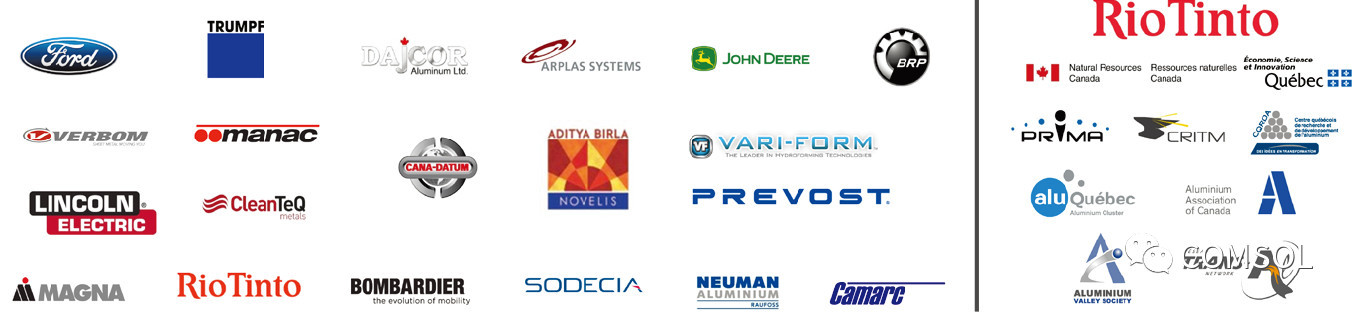
图 4. ALTec 多客户铝技术研发合作集团的成员公司(左)和合作伙伴(右)(截止日期 2018 年 3 月 19 日)。
虽然 ALTec 成员公司拥有各自不同的核心业务,但每个公司都高度重视腐蚀控制的相关项目。装配腐蚀问题的预测能力对于铝板产品制造商而言是至关重要的,只有充分了解腐蚀情况,才能确保产品以正确的方式进行使用,保证可靠性等指标达到预期要求。这对于汽车制造商而言也同样重要,它关乎着汽车能否性能出色,经受住时间的考验。
消除电偶腐蚀
汽车设计工程师可以利用一些通用方法来延缓电偶腐蚀的发生,其中包括:
(1)避免出现大阴极小阳极;(2)遵守电偶腐蚀兼容性图表;(3)避免异种金属之间的任何直接接触;(4)对两种不同的接触材料进行喷涂,或只喷涂阴极。然而上述方法对于实际应用却并没有太大的意义,因为在真实条件下应用这些方法几乎是不可能的。举例来说,如果安装了机械紧固件,那么金属与金属之间必定存在接触,而机械紧固件在异种材料装配中有着极其广泛的应用。
物理测试可以揭示复杂系统的行为特性,因此仍然是必不可少的环节,它包括路面测试、循环腐蚀和电化学测试。检查车载部件的测试既耗时又昂贵,而标准的循环腐蚀测试常常容易高估电偶腐蚀的风险。此外,如果材料还具有复杂的几何结构,电化学测试便更加难以提供准确的结果。
研究人员发现,将物理测试和多物理场仿真分析结合使用,可以在制造物理样机之前解决设计难题,加速耐腐蚀设计的开发进程。
多材料装配的腐蚀建模
根据由 COMSOL Multiphysics® 软件得到的在役、循环腐蚀和电化学测试信息,Gallant 及其团队创建了灵活、易用的数学模型,可对腐蚀行为进行预测。Gallant 解释说:“为了创建能反映真实动态过程的虚拟样机,我们利用一组安装在汽车上的传感器对模型进行了校准。”团队借助模型获取了高质量的数据,并采用先进的数据分析程序和机器学习模型从数据中提取了所需的信息和知识。模型中包含车底的表面温度、润湿时间、成分、汽车表面沉积的除冰盐的电导率、车辆速度和 GPS 定位在内的每一组数据。
在项目启动初期,Gallant 考虑过好几款不同的腐蚀仿真软件。他在尝试过程中发现,许多常见的软件虽然允许用户控制输入,但是隐藏了内部的计算过程,就像是不支持修改的“黑匣子”,而 COMSOL® 软件则支持用户指定和控制模型的所有属性。“COMSOL 软件具有强大的腐蚀建模功能,同时支持从其他软件中导入几何模型,这给予了我们有力的支持。通过对不同的电偶组合进行测试,我们可以在制作物理样机之前,充分了解需要调整的几何参数。”Gallant 解释说。
Gallant 与团队成员构建了由十多种材料和涂层构成的复杂装配(图 5),并将其作为面向NRC潜在客户的研究案例和实验室演示材料。由为期四天的实验室腐蚀试验得到的腐蚀破坏测试结果与仿真结果高度吻合,充分说明了使用 COMSOL Multiphysics 软件建立的NRC腐蚀模型可以准确预测复杂多材料装配的腐蚀情况。
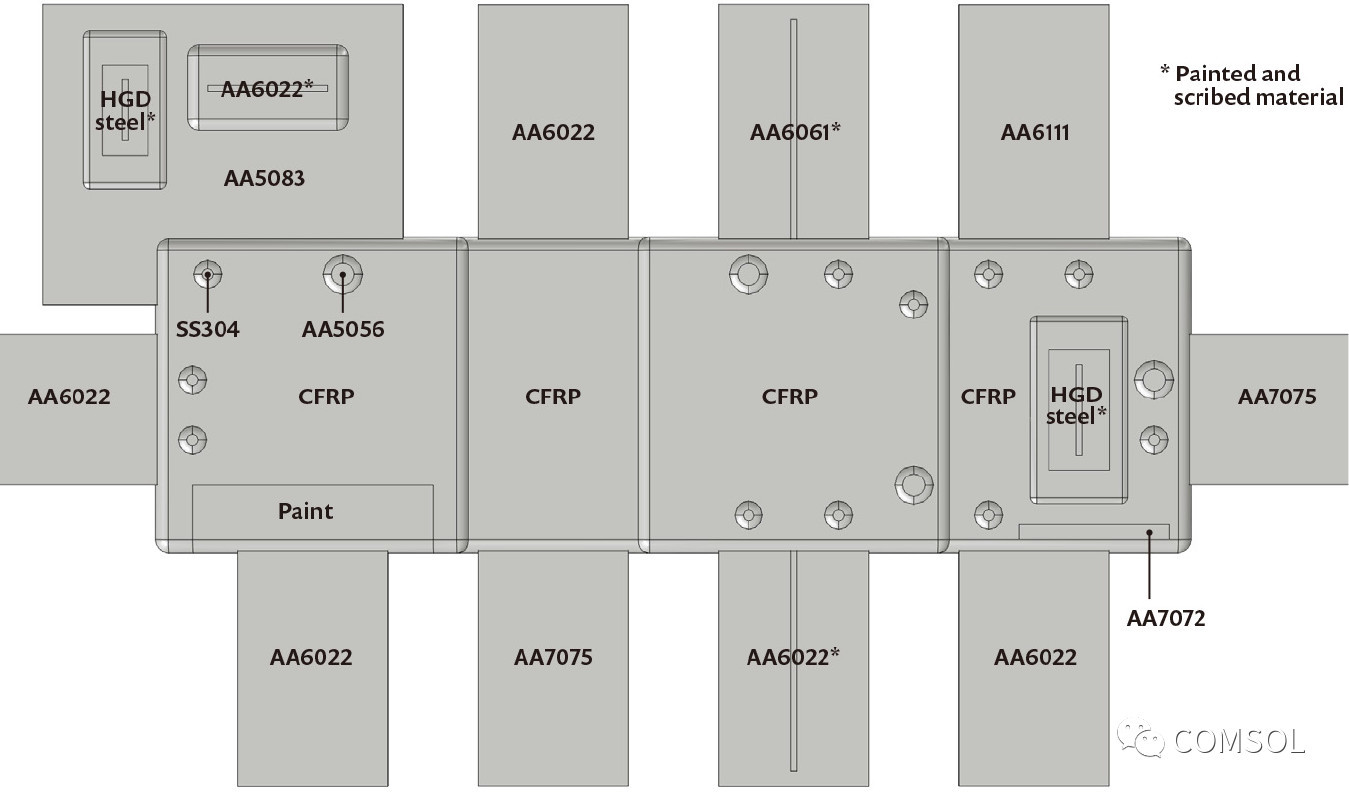
图 5. 多材料装配展示了利用腐蚀仿真发现不合理设计的重要性。图注: Painted and scribed material - 涂刻材料
团队通过 COMSOL Multiphysics 软件研究了实验室腐蚀暴露试验中牺牲阳极的厚度损失随时间的变化(图 6)。实验结果和仿真结果高度吻合。从实验数据和仿真结果均可看出,因左侧为尺寸较大且更为活跃的铝部件,铝铆钉左侧的溶解过程受到了抑制(图 7)。右侧为惰性碳纤维增强复合材料,致使铆钉右侧受到了腐蚀。团队据此再次证实了仿真准确反映实验结果的能力。
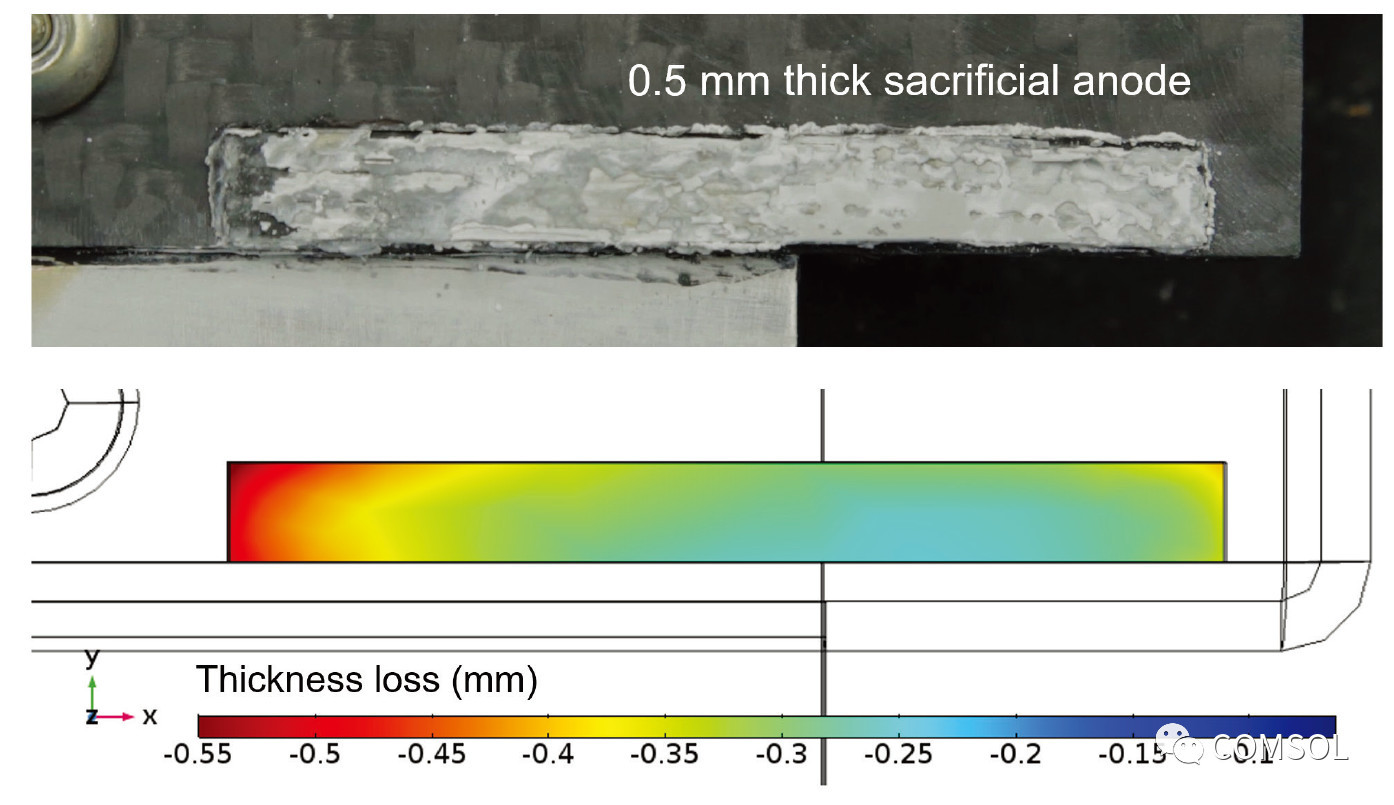
图 6. 利用瞬态分析(下)计算牺牲部件在实验室腐蚀暴露试验(上)期间的厚度损失。 图注:0.5 毫米厚牺牲阳极
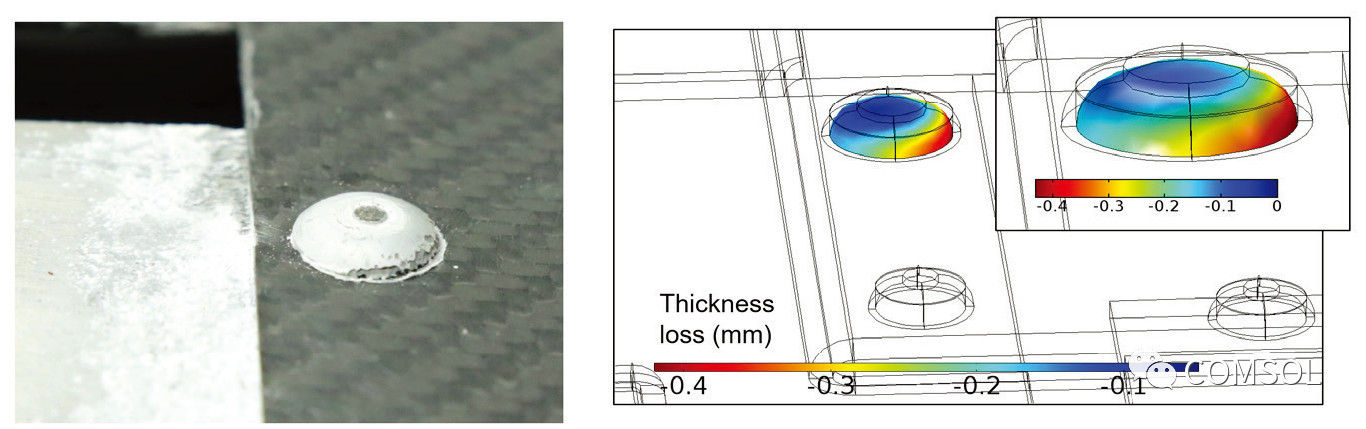
图 7. 利用瞬态分析(右)研究铝铆钉的溶解过程(左)。
仿真 App 助力前沿设计
在创建数值模型后,Gallant 又使用 COMSOL Multiphysics 软件中的“App 开发器”工具开发了一个可与同事们共享的仿真App。利用公司内安装的 COMSOL Server™ 产品(图 8),他可以通过网页浏览器快速部署仿真 App、管理用户、应用定制品牌,并根据需要分享更新。同事和客户可随时随地通过网页浏览器登录,访问这些仿真 App。
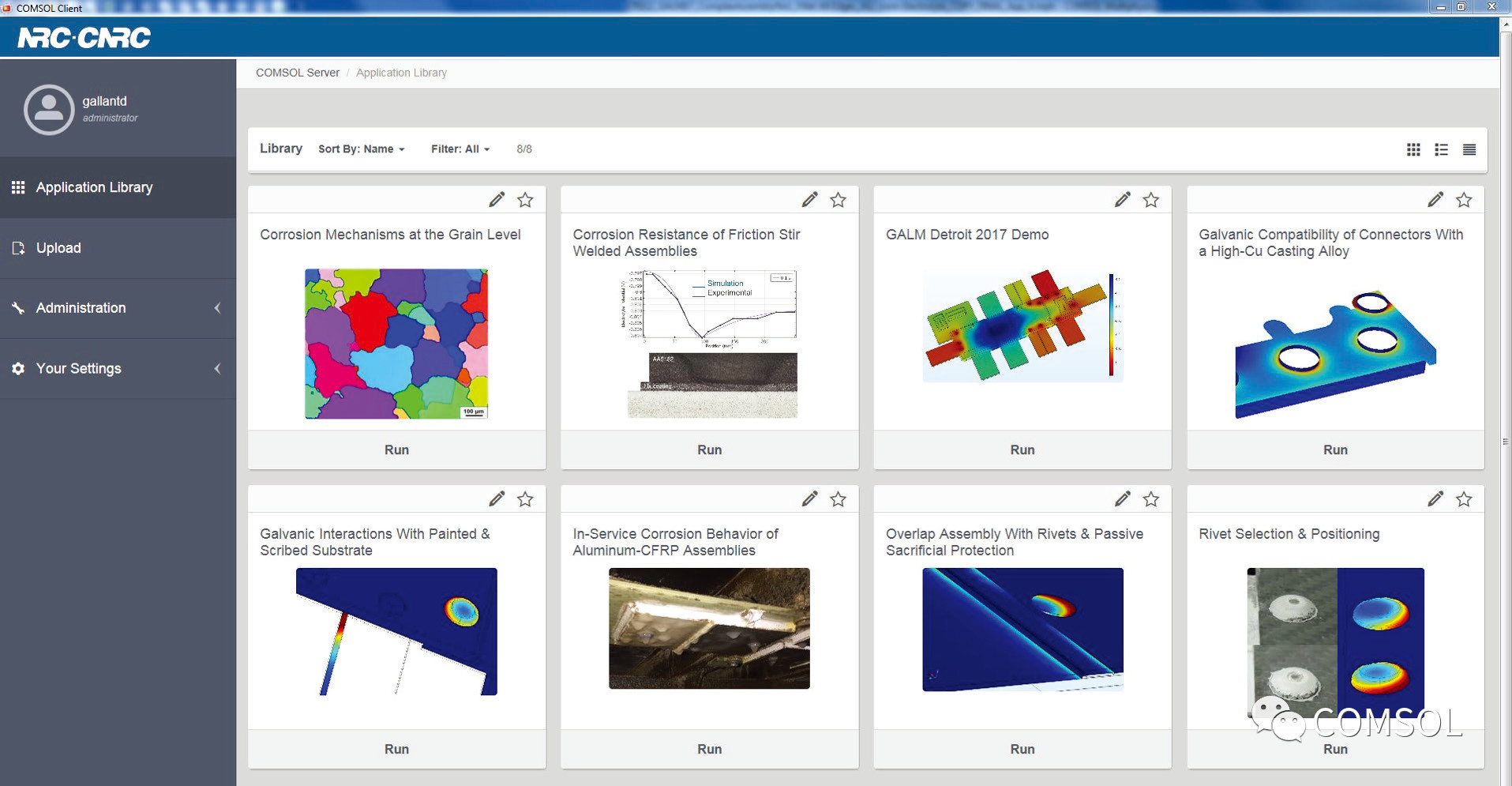
图 8. 通过网页浏览器访问显示 NRC 商标的 COMSOL Server™ 视图。
图 9 显示了专门计算多材料复杂装配的电偶腐蚀现象的仿真 App,使用者可以选择装配组件,并定义电解质厚度、对流和温度。在仿真 App 运行期间,用户可以生成电解质电位、电流密度和电极厚度变化的可视化绘图。利用由 NRC 编写的 MATLAB® 或 RStudio® 脚本,用户还可以导出定制的结果报告,以便进一步分析数据,并按照客户提出的规格进行调整。
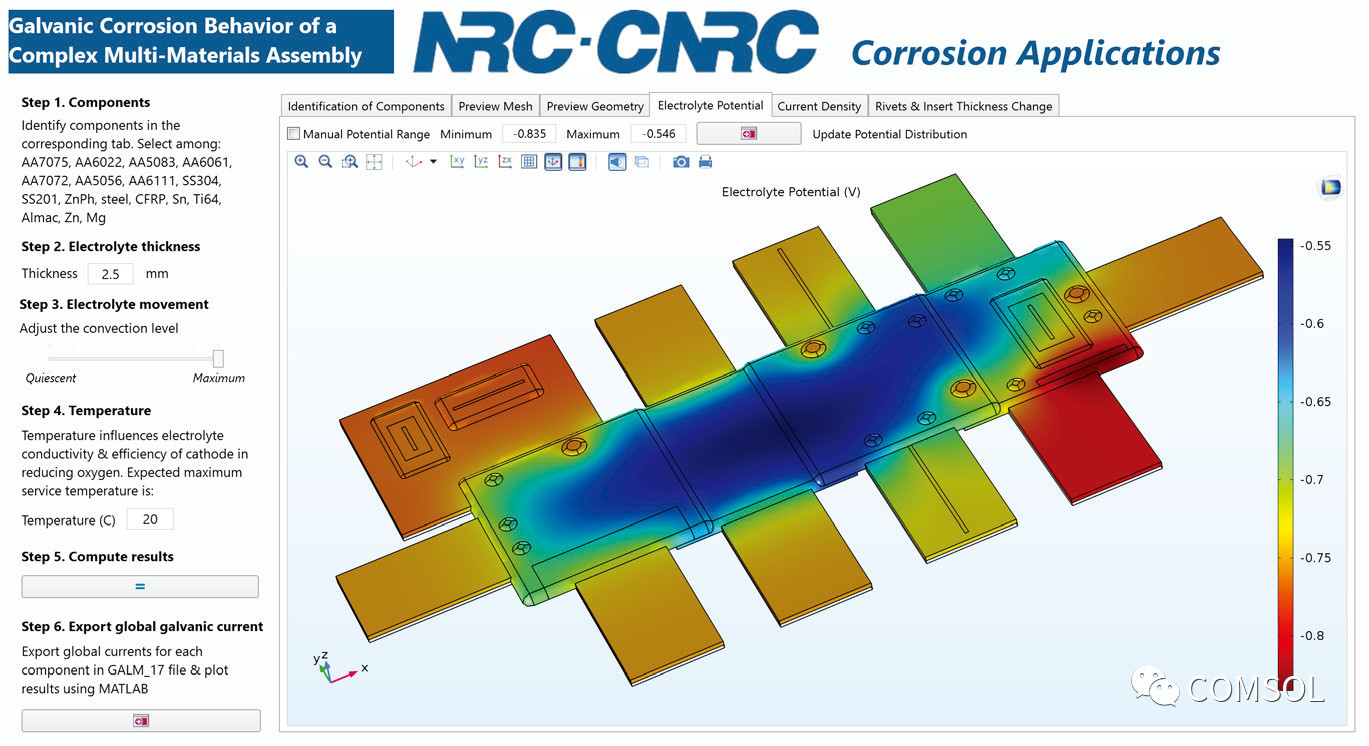
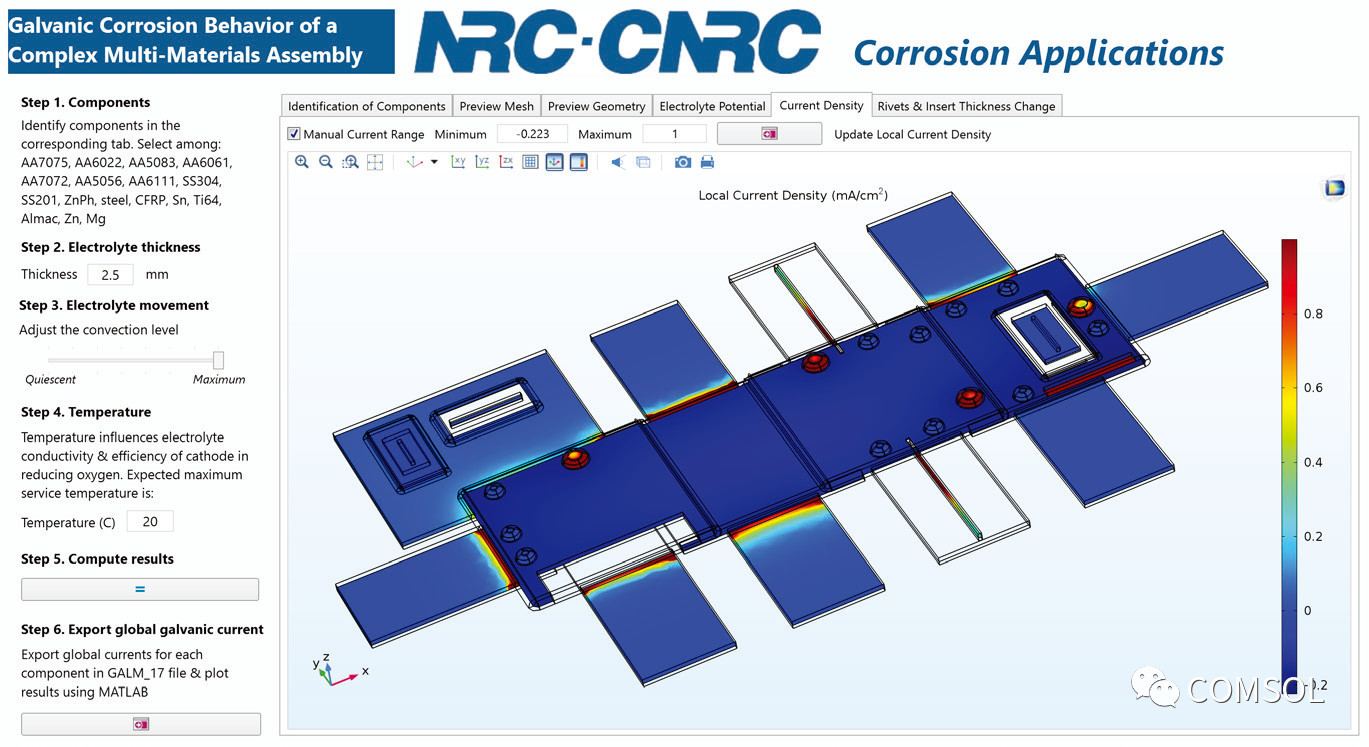
图 9. 用于分析复杂多材料装配电偶腐蚀行为的仿真 App。上:整个装配中的电解质电位。下:整个装配中的电流密度。
不仅如此,仿真 App 还加强了负责整车性能开发的工程师与腐蚀工程师之间的沟通协作。使用仿真 App 之前,如果改变几何结构或更换材料的做法不是常规操作,或者造价更高,开发整车性能的工程师往往会选择避免这些改变,因为他们无法清晰预见这些变化带来的好处。全面部署仿真 App 后,腐蚀工程师可以为设计人员提供更详实的理论依据,并明确指出腐蚀产生的位置和原因。
“我们的下一阶段目标是让 ALTec 成员能够在仿真 App 中选择汽车的装配位置,这款专业的预测工具可以帮助他们更加准确地表征模型中的电解质。COMSOL Server 开启了近乎无限的可能性,卓越的灵活性使其能够轻松适应客户的具体需求。”Gallant 评论道。
在轻量化设计中独占鳌头
多物理场仿真和仿真 App 降低了在设计进程中选择合适材料和几何结构的难度,为推动铝材料在新型轻量化设计中的应用提供了有力的支持。加拿大国家研究院的研究团队及其行业合作伙伴将不懈地致力于铝合金制造业的技术革新,推进铝合金在汽车轻量化设计中的应用,进而为整个汽车行业的发展做出贡献。
举报 0
收藏 0
分享 105
-
比亚迪发布2024年ESG报告 以技术创新驱动可持续
2025-03-26 -
旭化成精细化工(南通)新工厂竣工
2025-03-18 -
新品上市|FLIR Si2x系列防爆声学成像仪,引领
2025-03-13 -
Spectrum推出可由以太网控制的超高速GHz数字化
2025-03-12
编辑推荐
最新资讯
-
从4S店到修理厂:FLIR ONE Pro USB-C
2025-03-28 16:05
-
比亚迪发布2024年ESG报告 以技术创新
2025-03-26 16:44
-
电装中国:以“技术+生态”双引擎驱
2025-03-24 19:07
-
杜尔中国海外项目-Stellantis 集团摩
2025-03-20 11:59
-
3D扫描仪新品 | KSCAN-X 重新定义工
2025-03-20 11:58