舒勒第九届金属成形技术研讨会在长春成功举办
2018-12-02 10:31:32· 来源:舒勒
2018年11月21-22日,两年一度的舒勒第九届金属成形技术研讨会在长春凯悦酒店成功举办。本届研讨会以汽车轻量化及冲压智能化为主题,集中展示了金属成形领域最新的技术、工艺、解决方案包括舒勒在热成形、激光落料技术以及新能源汽车的电
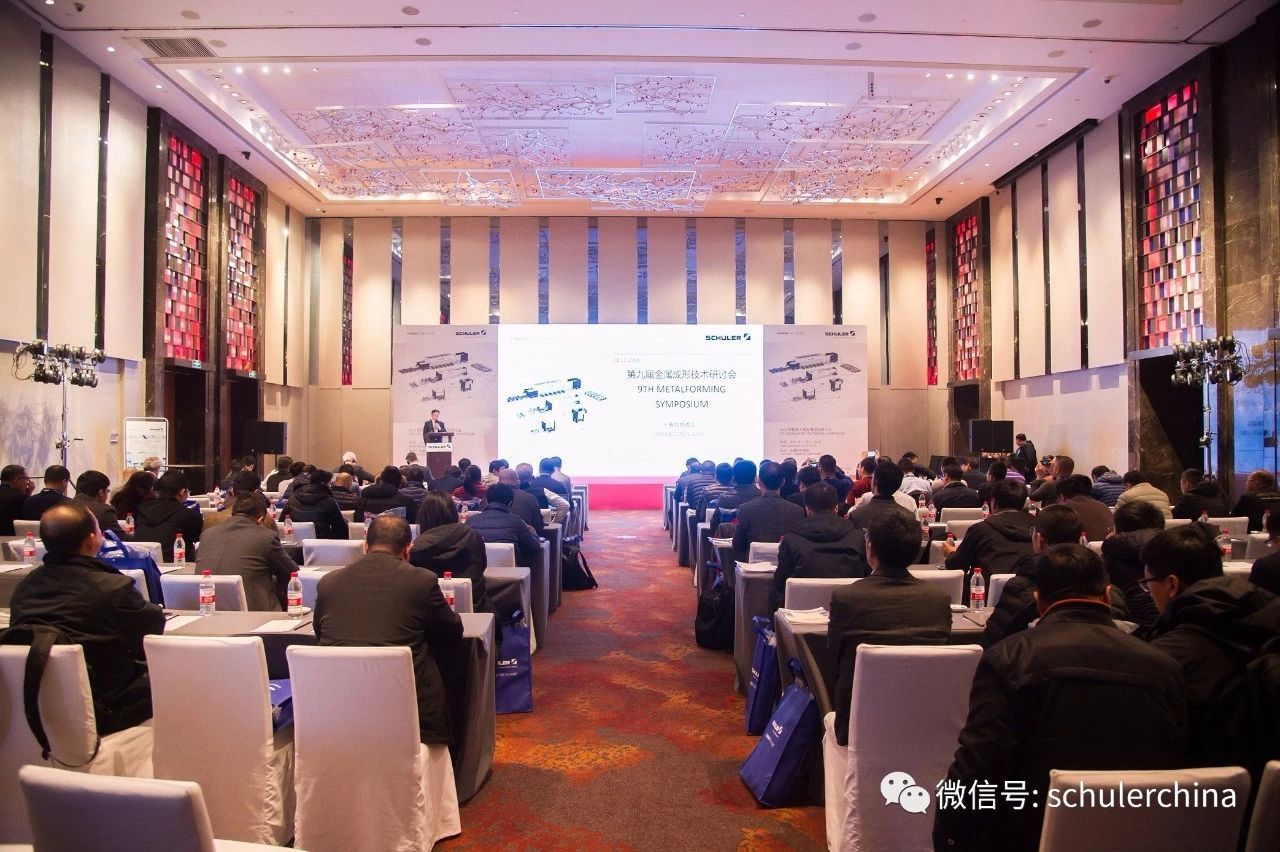
2018年11月21-22日,两年一度的舒勒第九届金属成形技术研讨会在长春凯悦酒店成功举办。本届研讨会以“汽车轻量化及冲压智能化”为主题,集中展示了金属成形领域最新的技术、工艺、解决方案包括舒勒在热成形、激光落料技术以及新能源汽车的电机、电池壳体生产线和智能冲压生产线方面的最新成果。来自全国各大汽车主机厂及其配套供应商的专家和代表一百余人参加了本次会议。
区别于往届研讨会,本次会议的亮点在于来自舒勒中德双方的行业资深销售代表结合中国市场的客户需求,分七个议题向汽车主机厂、零部件配套企业、初创型企业代表展示了舒勒在传统燃油汽车、新能源汽车以及冲压生产线智能化方面的先进技术和研究成果。此外,本次活动还参观了一家主机厂的超现代冲压车间,该冲压车间的高速冲压生产线采用了舒勒最新的整线控制技术和伺服直驱冲压技术(SDT),实现钢铝混合生产。生产节拍达到每分钟18次,可谓行业应用的典范。
会议伊始,舒勒压力机股份有限公司销售副总裁Frank Viola先生首先致欢迎词,对目前舒勒集团的产品、用户、技术创新以及在金属成形行业取得的成绩做了概述。此外, 结合客户现场压机线实际的运行情况,舒勒可以提供实用的虚拟培训,以保证生产的高效运行。在电动车市场领域,舒勒可以为车身、电动机冲片、电池外壳等零部件制造商提供系统解决方案,为客户降低运营成本。
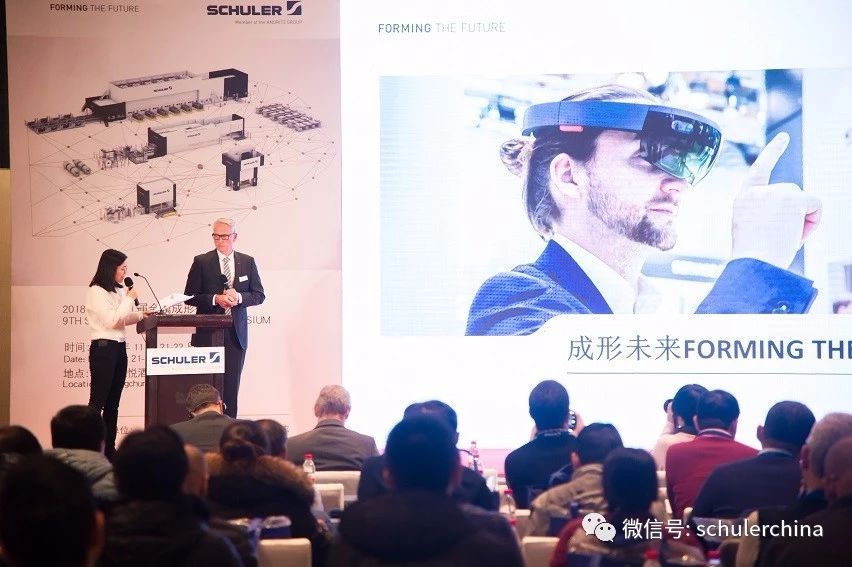
舒勒电驱动-新技术
舒勒电驱动包含新能源汽车电机高速冲Smartline系列以及新能源车用电池壳体技术。随着新能源汽车的快速发展,客户对工艺流程及冲床提出了新的要求,例如更大的长度和刚性、最好的滑块下死点精度、更高的速度以及更好的模具寿命等。舒勒Smartline系列高速冲床在床身,滑块,台面和驱动进行了改进和优化,并且使用舒勒专利技术—动态穿透深度控制系统,确保在变速情况下,滑块能够达到+/-0.01mm的下死点位置精度,同时配合了高刚性高精密的无缝滑块导轨,从而使得在确保最优产品质量的同时把模具使用寿命提高了30%,舒勒创新的自扣控制系统,突破了新能源汽车电机定转子铁芯生产速度的瓶颈,使得生产效率显著提高。整合的交钥匙方案,不会对生产造成任何干涉,同时保证了工艺流程的稳定性。
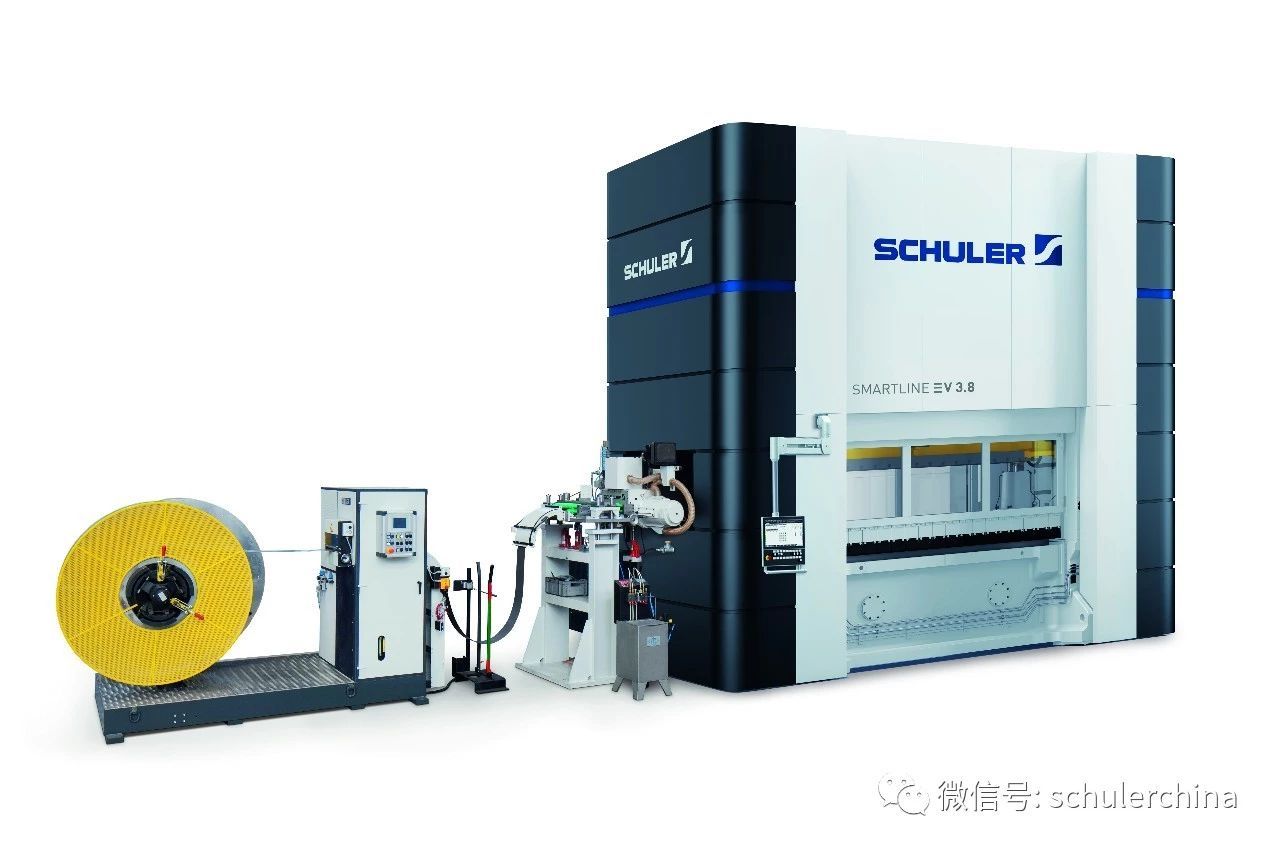
舒勒电池业务可以为所有汽车公司(OEM)和他们的供应商(一级、二级)供应商包括圆柱、方形电池壳体以及锂电池、碳芯电池行业的客户提供服务。通过设计电池壳(壁厚、重量和成本分析)采用冷挤压技术和冲压整形技术、深拉伸和多工位冲压技术、拉伸减薄技术新能源车用电池壳技术,提供单体压力机、整线交钥匙工程以及项目管理服务。舒勒新能源圆柱电池壳体技术是创新地把易拉罐生产技术转换到电池壳体技术上来,生产线达到了每分钟生产2000个壳体的速度,同时由于使用宽的钢卷进行一模多出落料,使得材料利用率最高可达85%。舒勒新能源方形电池壳体技术,巧妙地把铝制气雾罐生产技术转化到电池壳体生产上,带来超凡生产柔性的同时,方形壳体的产出达到120个每分钟,同时从原材料到壳体成品,只产生5%-7%的废料。
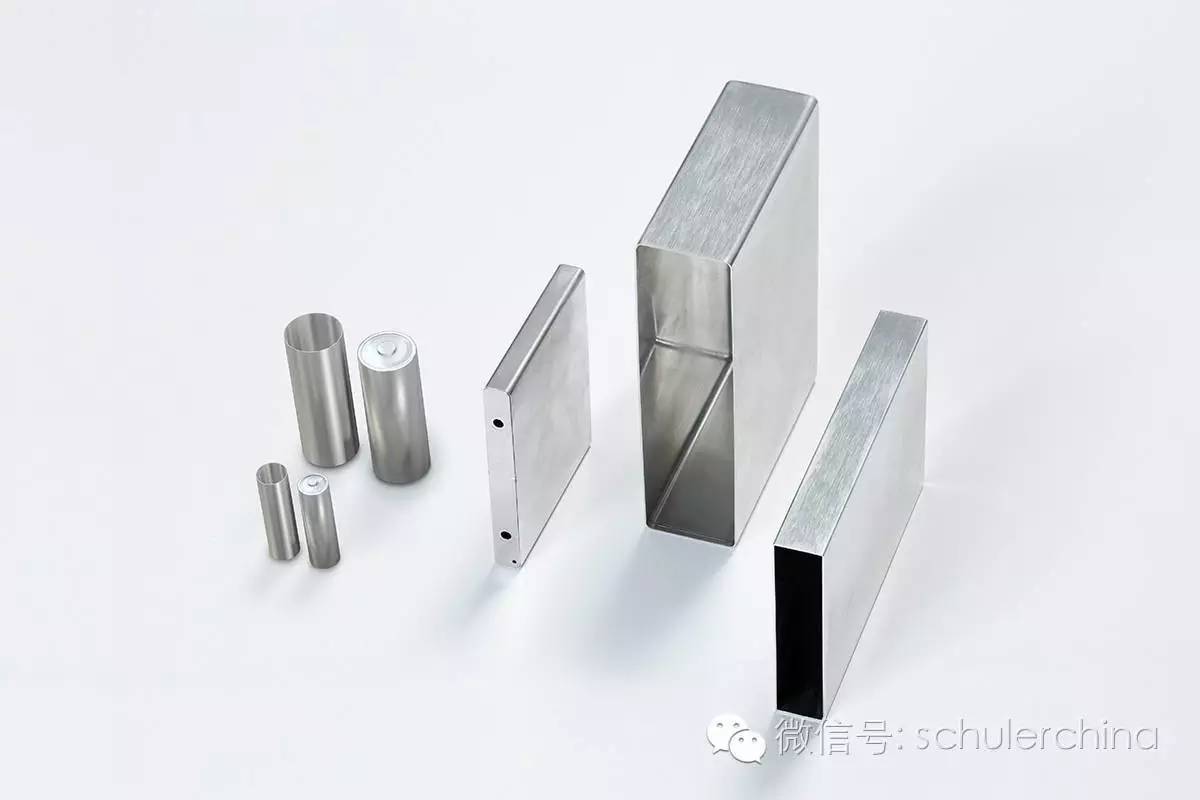
采用舒勒成形技术的汽车轻量化设计
舒勒的轻量化成形技术包括热成形、内高压成形和复合材料成形。由于汽车轻量化材料的工艺加工特性,要求在生产过程中必须使用液压成形技术来提高效率。机械压力机如果长时间在下死点保压的话,会对综合间隙造成不可恢复的磨损。 舒勒PCH FLEX压力机,采用最新的PCHflex拉伸垫技术,高性能液压系统,循环时间最短为8S 7.5冲次/分钟,舒勒环形阀可以实现高速闭合,快速卸压以及快速回程,动态驱动控制保证设备高速工作。
内高压成型产品包含压力机和生产线、零件和工艺、模具设计和制造、内高压成形生产。舒勒最新设计的内高压成形压力机HH-5000to-3.5*2.5m,采用内高压成形常规工艺和支撑压力工艺,可实现一模两腔的生产。适合所有高强钢成形零件,例如:发动机托架、A柱和前挡风边框、副车架后轴和皮卡车架等。
舒勒复合材料技术具有大批量生产的成功经验,通过与合作伙伴Frimo的密切合作,可提供交钥匙的复合材料制造解决方案,包括预成形和预切割、成形、切割、接合和粘结以及零部件组装和自动化整个生产流程。
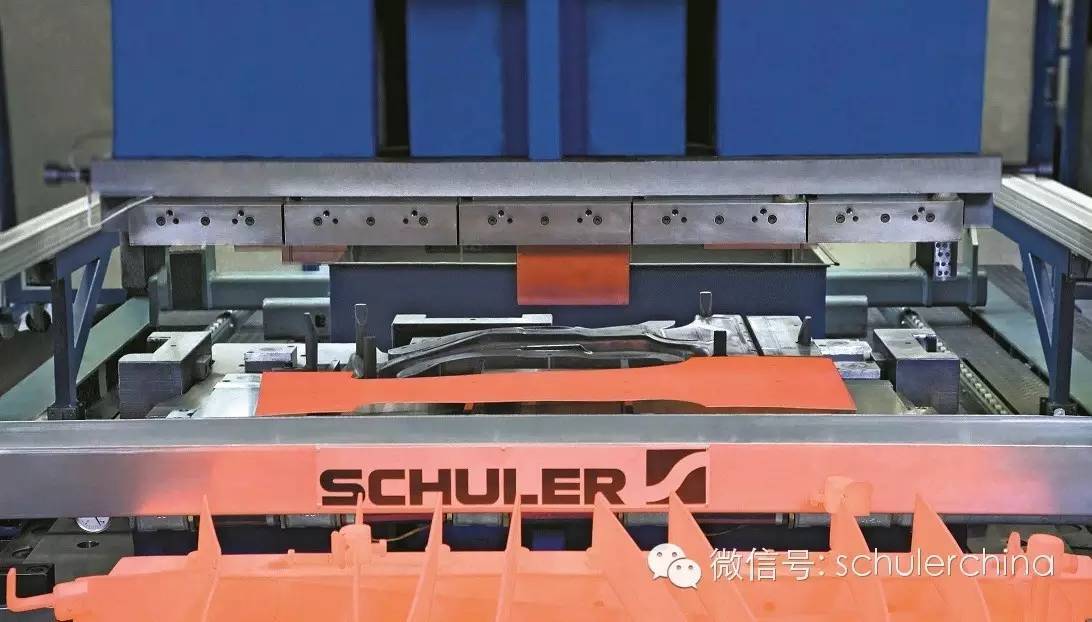
激光落料线:舒勒的动态联动技术实现无模具落料
从2012年全球首条高性能激光落料线诞生到7套设备在全球售出,包括为中国某大型钢铁企业提供的第一条激光落料生产线,舒勒在激光落料领域树立了行业标杆。精确的激光切割技术结合连续的卷材开卷送料,舒勒DynamicFlow(动态联动)技术重新定义了激光落料的速度。
对于车身件的多品种、小批量的生产,激光落料线具有可靠性高、质量好、单件成本低等优点。由于无需模具,省去了模具的存储和维护,激光切割特别适用于需要经常更换产品的生产流程。动态联动技术能够实现高速飞行切割流程,卷料可持续高速开卷落料。同时,也增加了产出,提高了设备的实用性,而且对于铝合金等敏感材料,该工艺可以保证在传输过程中不会对材料表面造成损伤。
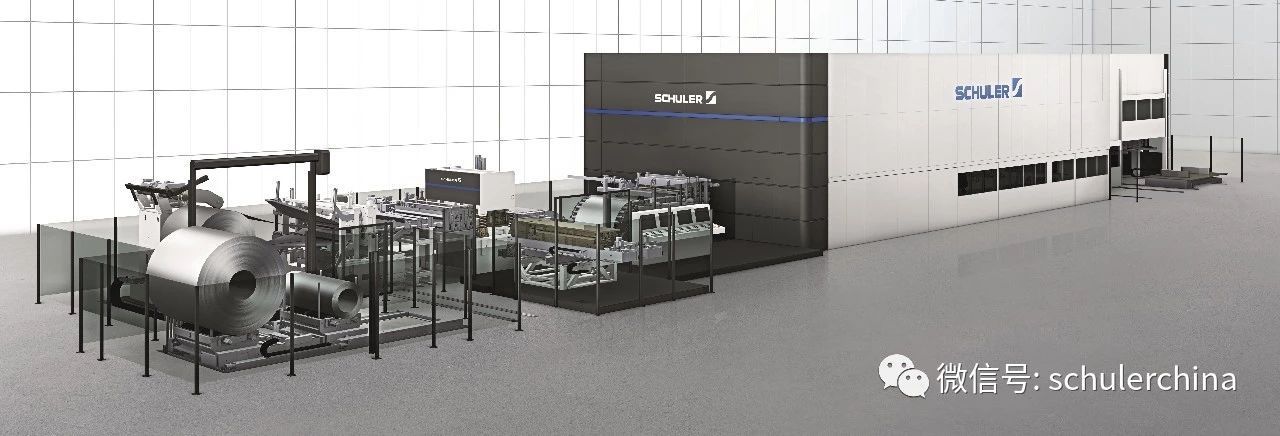
舒勒伺服试模压力机与TST多工位压力机
面对汽车制造领域的设计多元化、型号多样化、混合材料应用、安全性、全球化生产以及可持续发展的诸多挑战,舒勒的组合工艺方案,尽显金属成形优势。舒勒专家在会议中对双伺服压力机和试模压力机技术进行了对比讲解。
与传统的压力机相比,采用双伺服驱动技术(TST)的多工位压力机在提高零部件质量、提高模具寿命、降低噪声排放和降低能耗方面更具优势。在工艺方面,相同冲压力允许更大偏载、更灵活;垂直于物流方向倾斜抗力增加到四倍,零件精度更高,模具闭合更柔和;工作区域视觉效果更好,有利于操作;通过滑块平行度控制,零件质量更高,模具调试更加快捷。
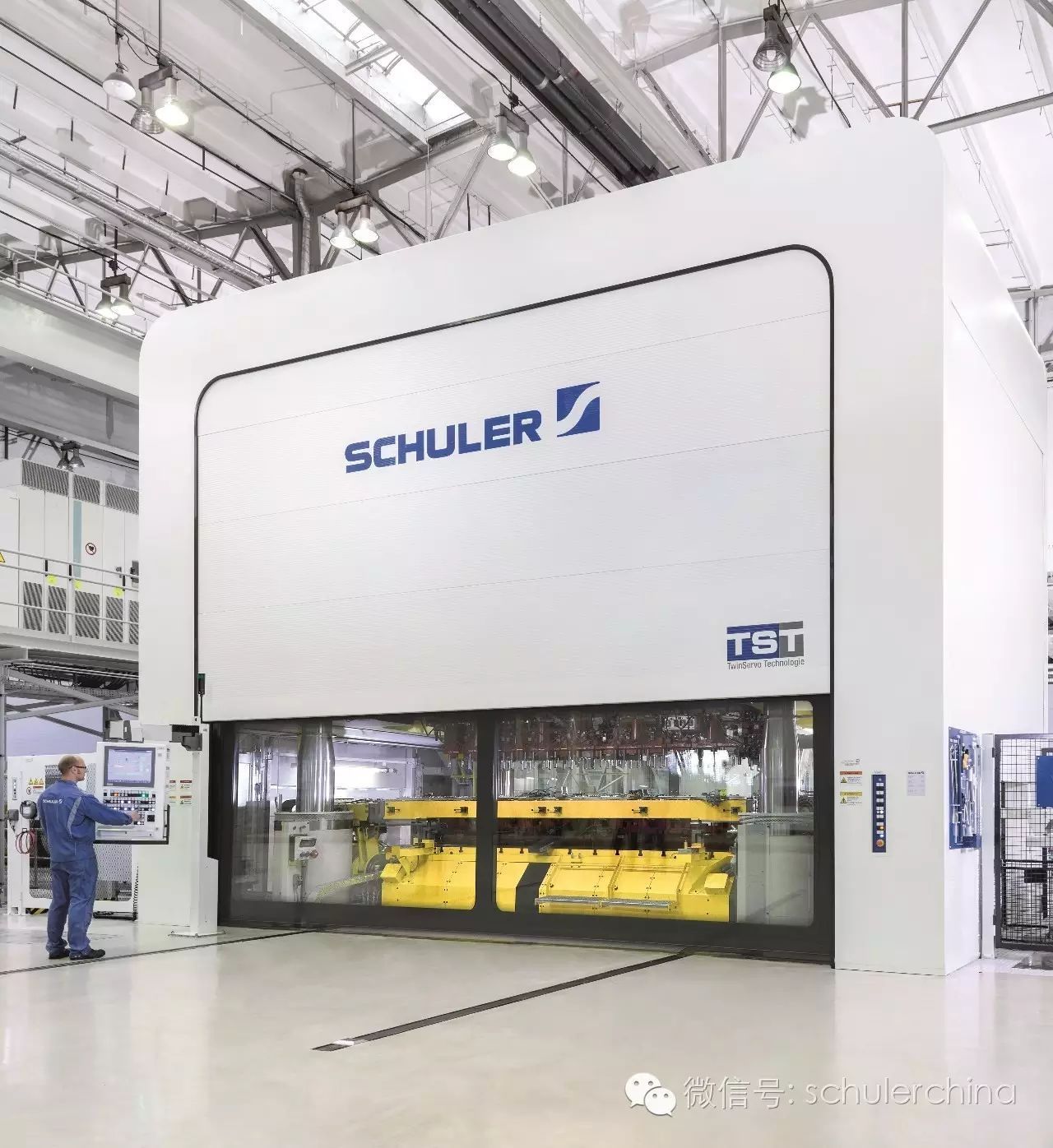
舒勒提供大型串联冲压生产线的最佳解决方案
舒勒大型串联冲压生产线的发展以市场为导向,以客户为中心。从2008年以来舒勒在全球市场陆续推出了以伺服直驱技术(SDT)为核心技术的大型高速自动冲压生产线,生产节拍分别为每分钟20/18/16次,满足了客户不同的工艺和产能要求。舒勒冲压线采用伺服直驱技术,具有速度快、结构紧凑和灵活性强的特点。自2010年首条SDT伺服冲压线投入运行以来,这些设备已经被几乎所有主流汽车制造商官方采用。为更好的满足零部件的不同尺寸以及其他工艺要求,舒勒现提供两种采用伺服直驱技术但规格不同的冲压线:ServoLine L和ServoLineXL。
以SDT伺服冲压线Servo16为例,该冲压线能够实现较高的产能与产品质量,同时缩短模具与端拾器的更换时间,这对于降低零部件的单件成本进而提高工厂的经济效益具有十分重要的意义。
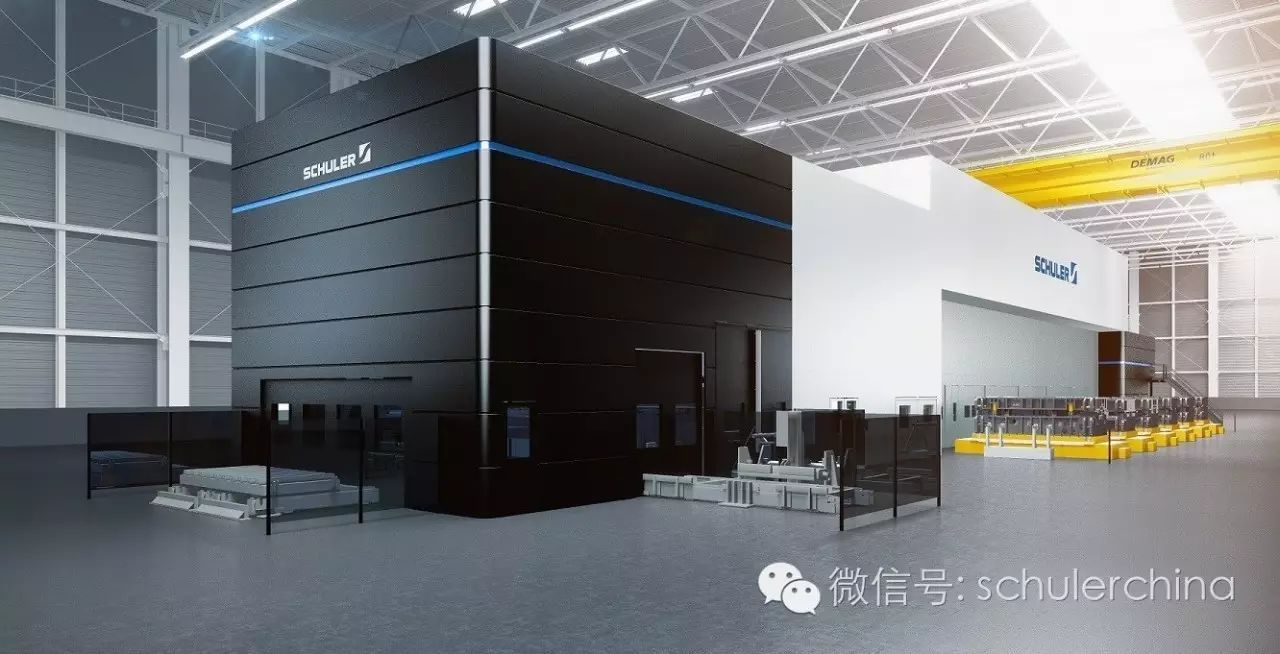
全新自动化+现有冲压线=更高的柔性&更好的性能
舒勒自动化行业专家首先从质量要求提高、更好可靠性、更高灵活性、更高产能、劳动力资源减少、旧备件逐渐退出市场这六方面的市场实际情况来分析客户为什么需要自动化改造。接着对线首解决方案、压机间自动化方案做了重点分析。其中料垛自动上料AGV方案通过拆垛、料片处理、视觉扫描等环节,配合智能物流来实现冲压线自动装箱和自动质检。
对于老旧的人工冲压线设备,自动化已经成为生产效率的瓶颈,而舒勒针对性的对现有的冲压线提供改造方案,通过上料装置、横杆机械手以及线尾系统合理配置,帮助生产线实现较高的产能与提升产品质量,同时缩短模具和端拾器的更换时间,来降低零部件单件的成本,进而提升了冲压车间的经济效率。
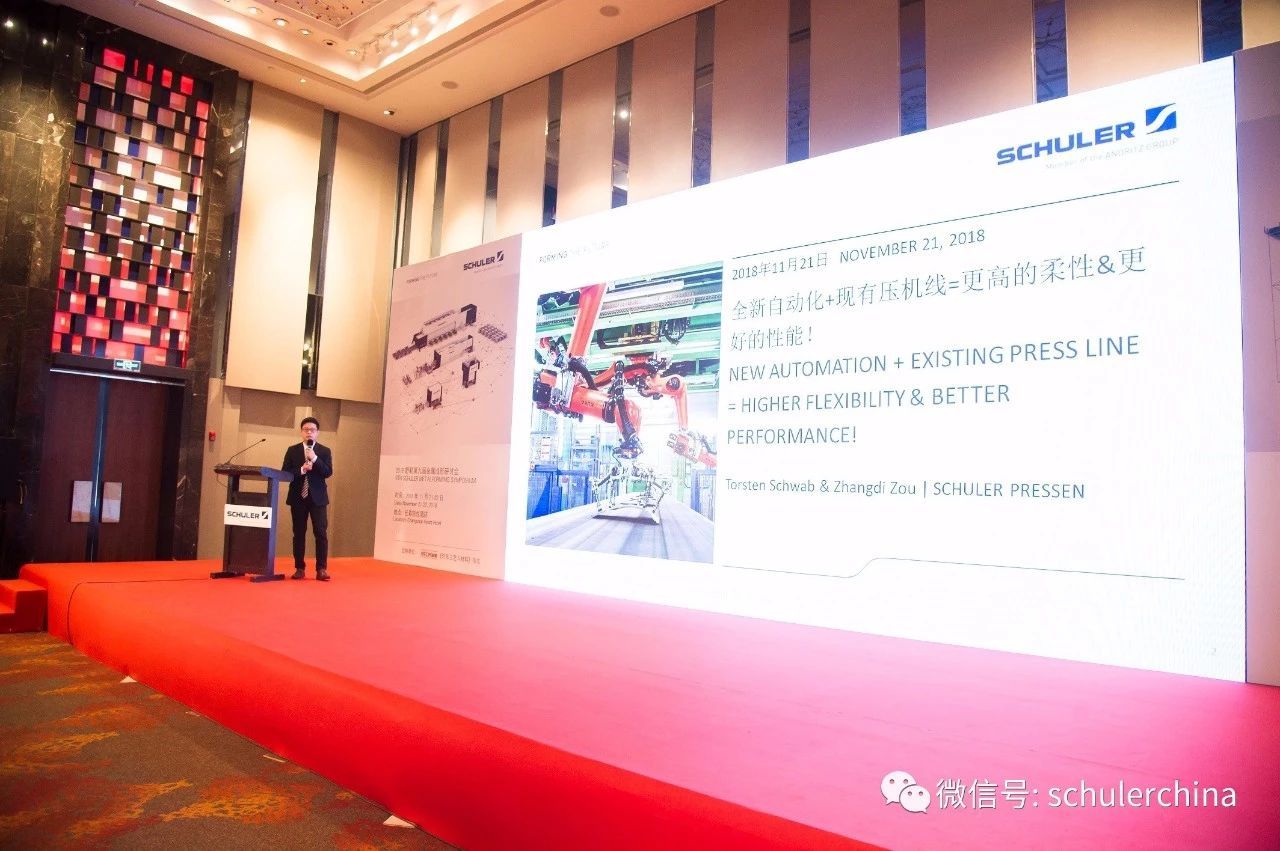
智能冲压车间——舒勒的物联网与工业4.0解决方案
舒勒让成形技术快速驶入了数字化未来,智能数据解决方案可以帮助客户提高生产率和工艺可靠性、延长设备使用寿命、优化能源效率及零件质量的可追溯性、同时增加利润率。此次研讨会中,舒勒专家通过设备监控系统(MMS)、虚拟仿真、DigiSim2.0以及虚拟成形技术学院四个主题分享了舒勒在智能冲压车间实现数字化生产的研究和实践。
首先,成形系统与仿真系统接收提高生产效率所需的数据。设备监控系统(MMS)通过自身的传感器自动收集、记录数据,并将其发送至分析评估系统。接下来,MMS系统利用这些信息进行工艺优化、设备监控、能耗与效率分析以及记录系统状态。最终,这些新数据将再次作为工艺仿真的输入参数。舒勒的设备监控系统能够对压力机运行进行全方位的状态检测和故障预判,避免发生计划外的停机事件。舒勒的成形技术学院虚拟操作培训中心的离线培训,可以让客户员工在操作实际设备前做好充分的准备,避免误操作对设备造成损失。
22日上午,全体与会者应邀参观了一家主机厂的现代化冲压车间,现场目睹了正在高速运营中的舒勒9100吨伺服冲压线以及自动化设备的运行状况。据介绍,该车间运行的舒勒最新投产的两条超大伺服18生产线,采用了最新的整线控制技术和伺服冲压技术,备受参观者的关注。
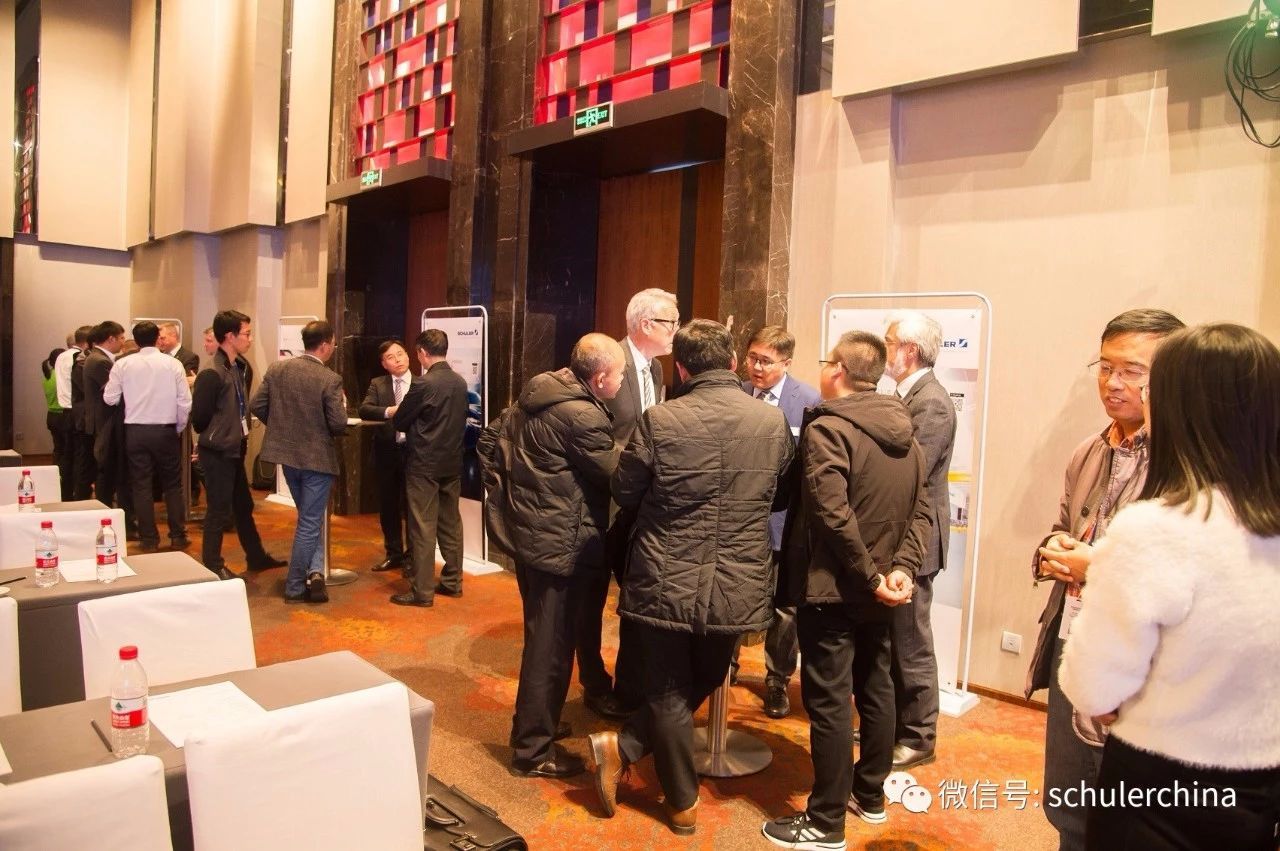
现场讨论环节
最新资讯
-
全球产业链聚沪 共探双碳新路径 SNEC
2025-04-18 18:05
-
柯马签订具有约束力的协议收购 Autom
2025-04-17 13:01
-
高效协同新范式:比亚迪叉车领创智能
2025-04-17 10:04
-
埃马克德国总部迎来中国社科院工业经
2025-04-15 09:40
-
埃马克这项全新应用即将在CIMT惊艳首
2025-04-15 09:37