复合精冲成形装备研发及应用
2018-12-05 21:59:52· 来源:华林,刘艳雄 锻造与冲压
精冲压力机是专为完成精冲工艺而设计制造的精冲装备,它必需充分满足精冲工艺的特定要求。精冲成形是零件在精冲力、压边力和反顶力共同作用下实现剪切分离的工艺,因此必须能同时提供三种单独的作用力。随着复合精冲的发展,精冲机还需提
精冲压力机是专为完成精冲工艺而设计制造的精冲装备,它必需充分满足精冲工艺的特定要求。精冲成形是零件在精冲力、压边力和反顶力共同作用下实现剪切分离的工艺,因此必须能同时提供三种单独的作用力。随着复合精冲的发展,精冲机还需提供第四、第五力,甚至第六、第七力。另外精冲机还需要满足冲裁速度可调、机架刚度高、导向精度高、滑块重复定位精度高以及具有灵敏可靠的模具保护装置等特点。

图1 KHF全自动精冲成形生产线
1-开卷 2-校平 3-精冲机主机
为了提高生产效率,精冲已向着全自动生产方向发展。本项目组和黄石华力锻压设备有限公司合作研发的典型KHF1000型全自动精冲生产线如图1所示。全自动生产流程主要包括开卷-校平-复合精冲工序。由于精冲材料一般为卷料,因此首先要进行开卷。板料卷曲后会发生弯曲塑性变形,为了保证精冲零件的平面度,板料需要校平,然后通过精冲机的自动送料系统将条料送进。在自动送进系统中含有条料自动润滑系统,条料的上下两面会被涂抹润滑油。涂有润滑油的条料进入模具型腔后,滑块上行,模具闭合,在模具中进行精冲成形。在一次精冲成形结束后,模具打开,高压气体将零件及废料吹出到传送带上,将零件及废料运送到料箱,或者通过机械手将零件和废料取出。剩余的条料废料在每隔一定冲次后由废料剪剪断,获得一定长度的废料,便于回收处理。
全自动液压精冲机
总体结构
图2所示为KHF1200型全自动液压式精冲机主机三维立体结构简图。KHF1200型精冲机是国内吨位最大的全自动液压精冲机。该精冲机采用下传动式,主油缸布置在机架的下部,压边油缸布置在精冲机的上方,反顶油缸嵌入主冲压油缸的内部,这种布置使精冲机结构紧凑。同时为了满足滑块的快速工进和快速回程,主滑块下还设计有快速闭合油缸。快速缸体积小、运行速度快。精冲过程中,快速闭合油缸首先推动滑块快速上行,位移传感器检测到滑块运行到设定位置后进行废料检测。如果不存在废料,滑块继续上行进行冲裁,此时主油缸开始工作,提供大的冲裁力。同时压边缸和反顶缸的活塞被传力杆顶着往后退,压边缸和反顶缸为背压缸,活塞后退过程中能稳定的提供压边力和反顶力。
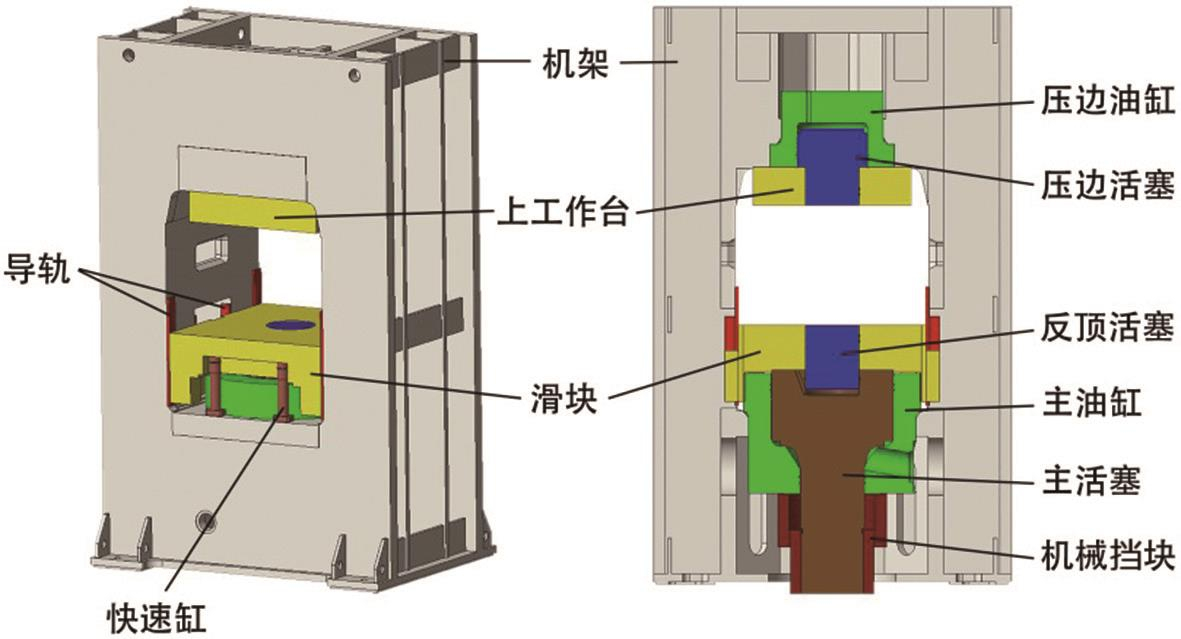
图2 KHF1200型液压精冲机主机三维立体结构简图
该精冲机具有双重导向,第一重导向为主油缸的活塞与缸体之间的导向,第二重导向为主滑块与机架上的导轨导向。目前应用最多的为八面导轨导向,具有很强的抗偏载能力,因此导致了结构复杂,对加工精度要求非常高。对于精冲工艺,要求滑块具有高的重复定位精度,液压式精冲机上设计有限位块,限位块限制主油缸活塞向上运行的上死点。限位块位置可通过伺服电机驱动螺母旋转进行调节。
为了实现全自动精冲,精冲机上还配有送料机构,送料机构送进步距误差不能超过0.1mm,否则由于误差累计,在级进复合精冲成形时导致零件不能精确定位,损坏零件和模具。目前送料结构一般采用伺服电机驱动,此外精冲机上还配有废料剪,当条料送进到设定距离后自动将废料剪断,便于废料的收集。
机械部分设计
精冲机机架通常采用厚板焊接的整体框架式结构,其加工流程为:首先将不同厚度(通常为20~400mm)的钢板焊接在一起,然后进行整体去应力退火,最后进行整体数控精加工,保证机架的尺寸精度。这种结构的机架具有较高的强度和刚度,并且可以为滑块提供间隙可调的平面导向结构,导向精度高、抗偏载能力强,可以满足精冲的工艺要求。此外机架经拓扑优化和尺寸优化后,可以达到节省材料、减轻重量且便于制造的目的。
KHF型精冲机导向采用油缸与滑块双重导向机构。主油缸采用导向带滑动导向,在油缸和活塞之间设置导向带,起导向作用的同时也防止了活塞与油缸直接接触造成的磨损;主滑块采用八面导向结构,具有很强的抗偏载能力,确保偏载作用下精冲零件的成形精度。KHF型液压式精冲机抗偏载性能测试结果如表1所示,这种导向结构形式复杂,其液压缸滑块环形导轨和滑块平面导轨应严格对中且间隙要均匀,加工精度要求极高。
表1 KHF型液压式精冲机抗偏载性能测试结果
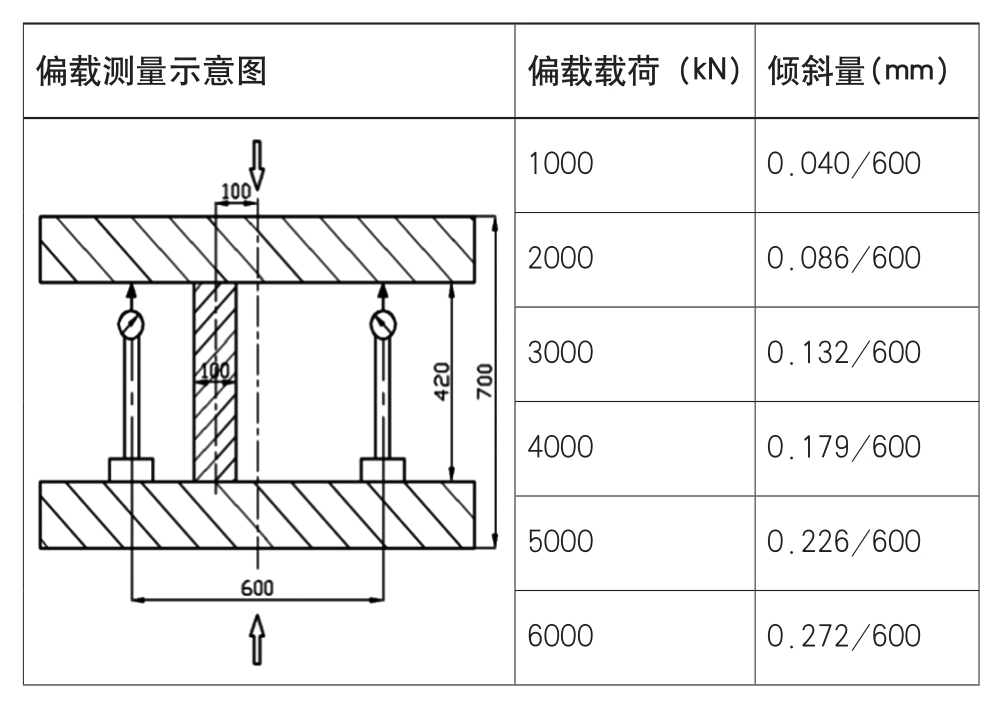
高性能节能液压系统设计
传统液压精冲机为保证冲压效率,其快速合开模回路及主冲压回路均常采用比例-伺服阀控制系统,然而阀控系统低效率、高能耗等缺点在液压精冲机上尤为突出。为改善液压精冲机高能耗问题以及实现低碳制造,对传统精冲机液压系统进行了改进。本项目组提出了一种多蓄能器混合液压控制系统,其中快速合开模回路采用比例-伺服阀控制系统,主冲压回路采用伺服电机-泵控制系统,且在两个回路中安装多个液压蓄能器,分别起到储蓄能量、压力补偿与能量回收的作用。该混合液压控制系统同时具有阀控液压系统响应快、伺服电机泵控制效率高的优点,液压蓄能器的合理利用使其系统能量的利用效率进一步提高。改进前与改进后系统性能、能耗及利用效率分别如图3和图4所示。
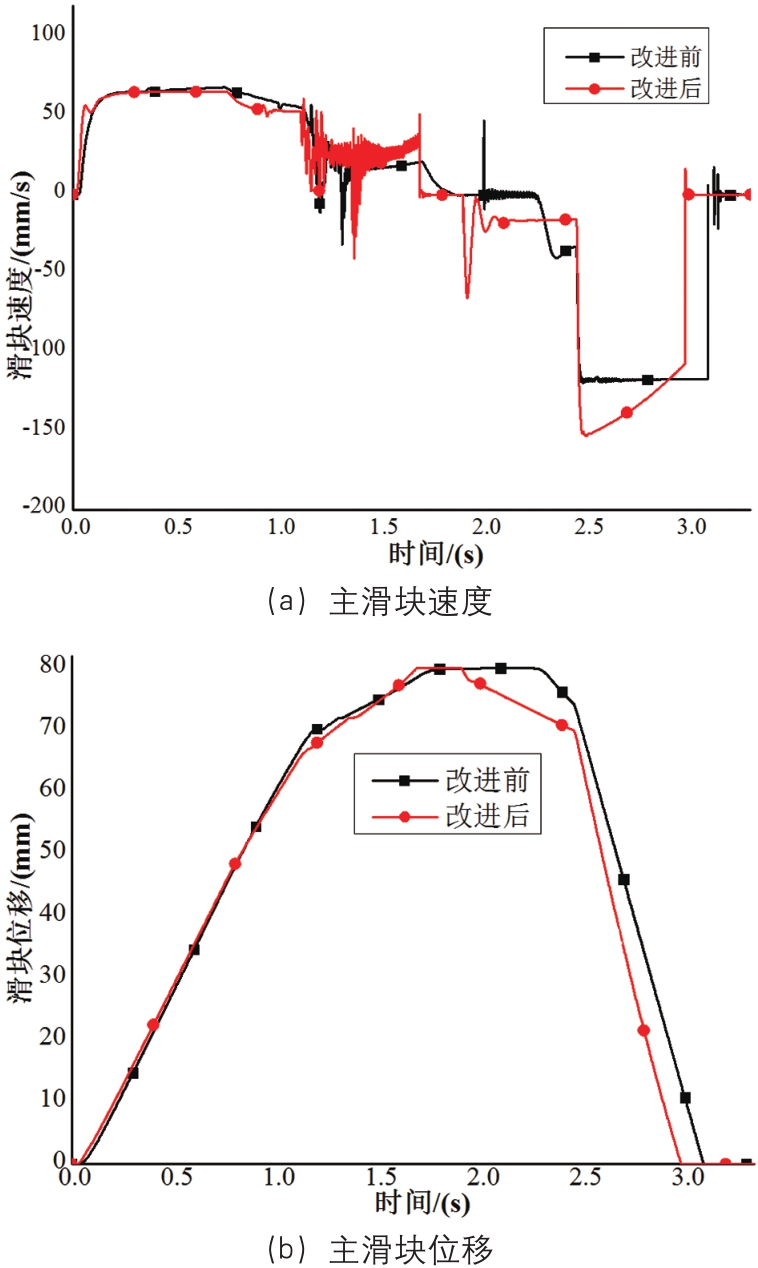
图3 优化前后的精冲机液压系统性能对比
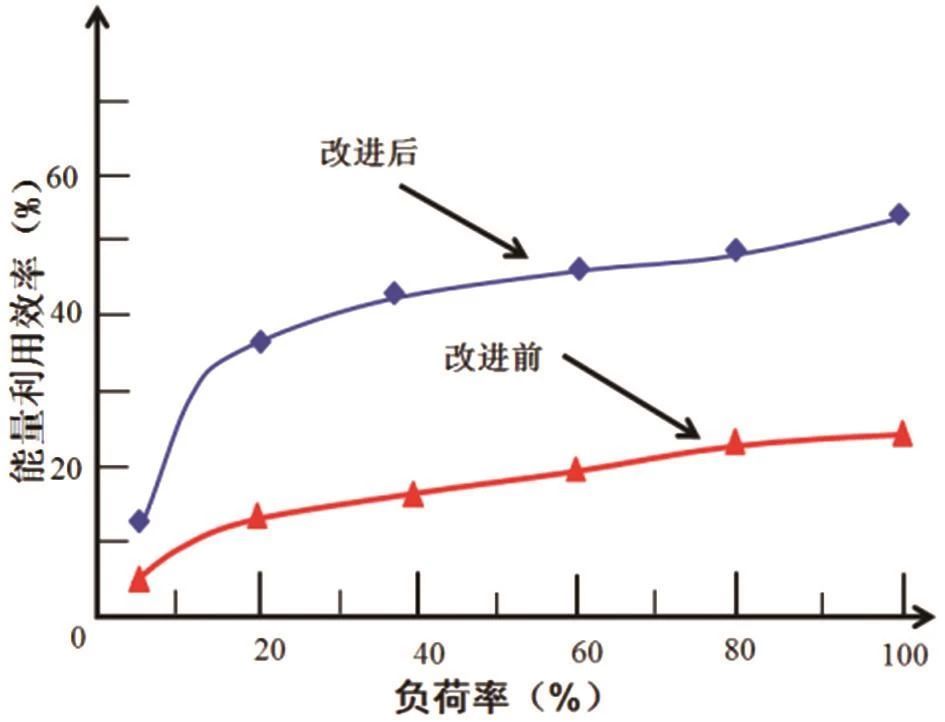
图4 不同负荷率下精冲机液压系统能量利用率
图3 中,对液压系统改进后,其精冲机滑块在快上、检测、冲压阶段响应速度几乎相同,而对卸压及快返阶段改进后,系统滑块响应运动速度明显加快,导致工作循环周期减小,进一步提高了精冲机工作效率。另外整机的液压系统振动非常小,在复合精冲成形过程中,竖立放置的硬币可以保持不倒。
图4中,当负荷率较小时(<10%),改进后与改进前液压系统能量利用率相差不大,然而随着负荷率升高,改进后的液压系统相比改进前能量利用率平均提高25%。以一台650t液压精冲机为例,其功率为145kW,冲频30次/min,16小时/天,300天/年,电费1.2元/度,阀控系统能量利用效率25%,泵控系统能量利用效率50%。则生产同批量产品,泵控系统比阀控系统每年多节约电能为:E=(145-145×25%/50%)×16×300=348000kW·h。每年多节约:348000kW·h×1.2元/kW·h=417600元。
为了满足复合精冲多力系要求,精冲机需要提供第四、第五力,其结构原理图如图5所示。精冲机的主油缸提供精冲力与精冲运动,反顶油缸提供精冲反顶力和反顶运动,压边油缸提供压边力和压边运动。至于第四、第五力,则是根据零件成形特征,在模具中设计挤压油缸和挤压反顶油缸,其液压力源来自精冲机的液压系统。在精冲机液压系统中设计有第四力、第五力的液压油路,只需通过油管将模具上的液压油缸和精冲机上的液压油路连接起来即可。随着精冲零件结构越来越复杂,力系数量要求越来越多,第六、第七力系全自动液压精冲机也已经研发了出来。
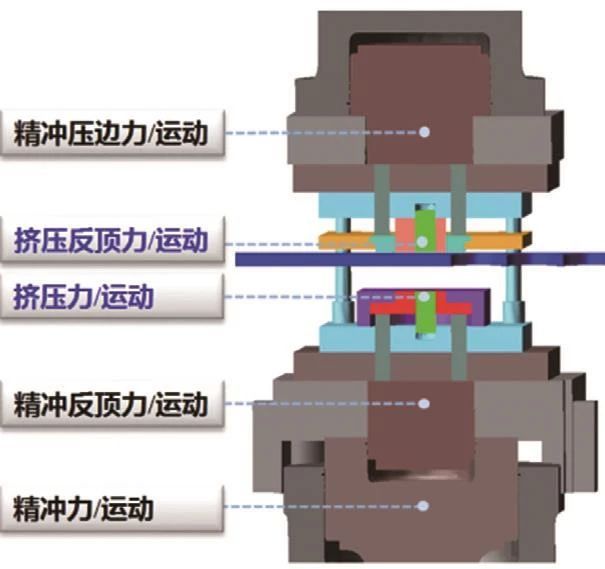
图5 复合精冲多力系结构原理图
高速机械伺服精冲机
为了实现高速精冲,本项目组还研发了机械伺服高速精冲机。其最大精冲成形力为3200kN,最大压边力为1600kN,最大反顶力为800kN,滑块最大行程为70mm,冲压频率最高为220次/min,冲裁板料厚度为0.5~10mm,各参数指标处于国际领先水平。
该精冲机主传动采用曲柄肘杆结构,为双伺服电机驱动,其运动原理图如图6所示。其中伺服电机1快速转动,实现精冲机主滑块的快速上行,当主滑块快速上行到预备冲裁位置时,伺服电机2开始工作,提供足够大的主冲裁力,实现慢速精冲,精冲完成后,伺服电机1再次高速运转实现快速回程。采用双伺服电机能够有效避免单电机功率过大现象,可节约能源和制造成本,同时能够高速平稳的实现精冲成形。
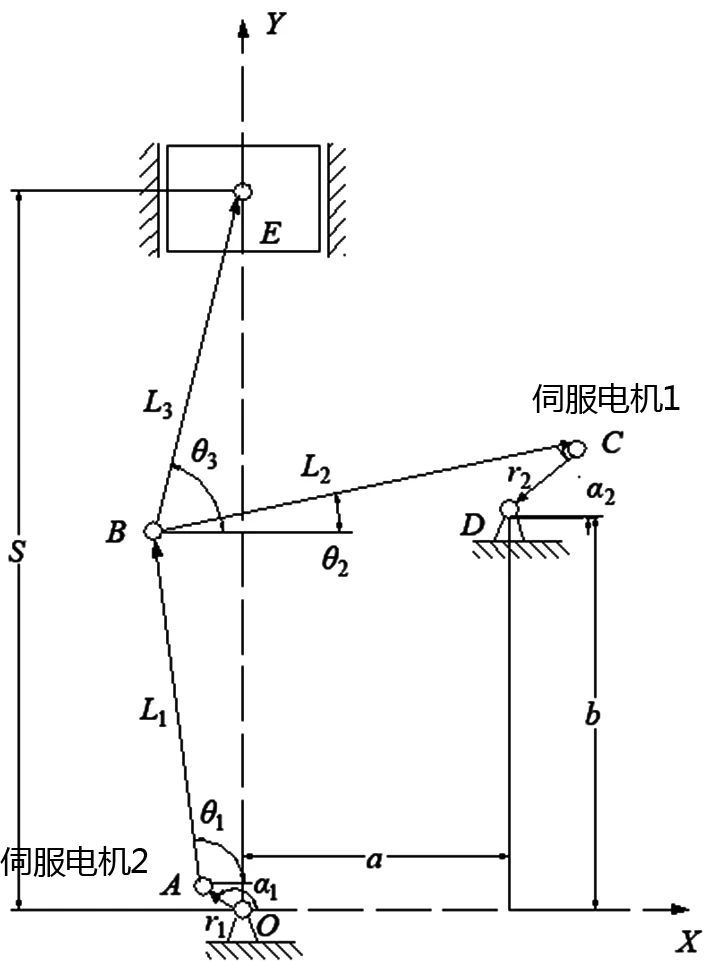
图6 双伺服电机曲柄肘杆结构
目前在精冲过程中常采用恒定压边力及顶出力,为了实现智能精冲,压边力及顶出力在精冲过程中智能可调,并对传统液压精冲机压边及反顶系统进行升级改造。反顶力液压系统如图7所示。

图7 智能伺服反顶缸液压系统图
与传统反顶缸液压系统相比,本系统采用比例溢流插装阀替换普通电磁溢流插装阀。通过调节比例溢流阀溢流压力值,能实现精冲过程中顶出力的伺服可调。根据研究表明压边力主要在精冲的初始阶段,此时剪切变形区的压应力较大。随着精冲行程的增加,剪切变形区压应力逐渐减小。因此在精冲初期可以适当减小压边力和反顶力,随着行程的增加再逐渐增加压边力和反顶力。这种设计一方面可以减小能耗,另一方面对于高强度难变形材料,动态调整压边力和反顶力,可以实现其全光亮带的精冲成形。
结束语
精冲装备作为精冲成形工艺的保证,其性能直接决定了复合精冲零部件的质量,也反映了国家高端装备的发展水平。本项目组和黄石华力锻压设备有限公司合作研发的KHF系列精冲机整体性能达到了国际先进水平,后续将继续研发更高速度、更高精度的复合精冲机。
本文节选自《锻造与冲压》2018年第22期。
- 下一篇:Festo为你开启数字化转型之门!
- 上一篇:案例 | 5分钟更换机床中心架
举报 0
收藏 0
分享 74
-
冲压技术在电机叠片制造的应用
2024-09-06 -
车身零部件包边质量控制要点
2024-09-05 -
轻量化技术——热汽胀形工艺技术解析
2024-09-04 -
高强板车身件冲压技术
2024-09-02
最新资讯
-
旭化成微电子开始批量生产用于环保发
2025-04-24 16:00
-
华为、地平线、大众、东风、起亚等引
2025-04-24 08:27
-
全球产业链聚沪 共探双碳新路径 SNEC
2025-04-18 18:05
-
柯马签订具有约束力的协议收购 Autom
2025-04-17 13:01
-
高效协同新范式:比亚迪叉车领创智能
2025-04-17 10:04