汽车电子制动系统行业发展动态
2018-12-26 23:00:28·
(一)电液/气复合制动系统发展现状1.电子液压制动系统(Electro-Hydraulic Brake,EHB)EHB系统是在传统的液压制动器基础上发展而来的。国外多家企业于20世纪90年代就进行了EHB系统的研究并实现了量产,较典型的产品有博世的SBC(Sensot
(一)电液/气复合制动系统发展现状
1.电子液压制动系统(Electro-Hydraulic Brake,EHB)
EHB系统是在传统的液压制动器基础上发展而来的。国外多家企业于20世纪90年代就进行了EHB系统的研究并实现了量产,较典型的产品有博世的SBC(Sensotronic Brake Control)系统、IBS系统,丰田公司的ECB(Electric Brake Control)系统,大陆公司的EVB(Electronic Vacuum Booster)系统等。国内EHB系统尚处于研究阶段,清华大学、同济大学和吉林大学都提出了多种方案,如清华大学2010年提出DEHB系统;国内企业中,亚太、万向、上汽等也在进行相关产品的研发,部分已进入试验验证阶段,还未批量生产(见表11)。
表11 国内外从事相关研究的主要机构
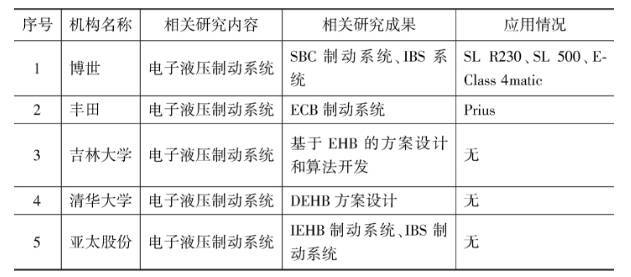
在汽车产业低碳化、信息化及智能化趋势下,EHB系统将面临更多新的需求,特别是国产EHB系统的产业化变得非常迫切。
①制动能量回收的要求:EHB系统在进行制动能量回收上可以实现全解耦,回收效率高。
②智能辅助驾驶主动减速制动的要求:近两年来,国内智能辅助驾驶的主动减速制动功能主要由ESC系统完成,相比ESC系统,EHB(包括IBS)系统因为完全解耦,提供了良好的踏板感觉,同时EHB系统减压速度和控制精度更高,其制动效能更好且控制更加方便,是下一阶段智能辅助驾驶(ADAS)理想的执行系统。亚太股份推出的IEHB系统,要求达到10MPa主动减压时间≤170ms、液压控制精度≤0.1MPa的目标。
③适用于分布式驱动汽车(轮毂电机汽车):轮毂电机技术是电动汽车未来发展的方向,EHB系统和轮毂电机协调控制,可以达到非常高的能量回收效率,在智能驾驶控制上,也会有较大的提升(见图1)。
图1 EHB系统面临的新需求
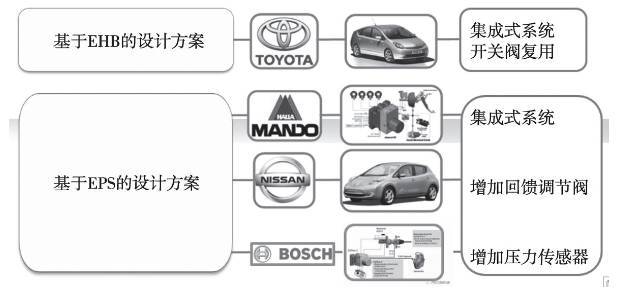
在新需求下,EHB系统需要对回收效率、舒适度、噪音、安全性、快速增压和精确控制进行重点关注和研究。
2.满足制动能量回收的EHB
在城区运行的汽车制动过程中消耗的能量一般占直接驱动汽车运行总能耗的30%~50%,制动能量回收是汽车的一项重要节能措施。针对电动汽车制动能量回馈的要求在原有液压制动系统的基础上研发能量回馈式制动系统,成为当前国际上知名汽车公司和ABS厂家竞相开发的热点。能量回馈式制动系统是决定电动汽车整车制动安全性、制动舒适性、制动能量回收效率的重要因素,成为电动汽车的一项关键共性技术和一种具有核心竞争力的零部件产品。
当前典型的制动能量回收系统主要分为基于与液压控制单元的集成设计、基于与制动主缸的集成设计两类。
(1)基于与液压控制单元的集成设计
基于与液压控制单元的集成设计主要分为基于EHB的设计方案和基于ESP的设计方案(见图2)。
图2 基于与液压控制单元的集成设计的典型制动能量回收系统
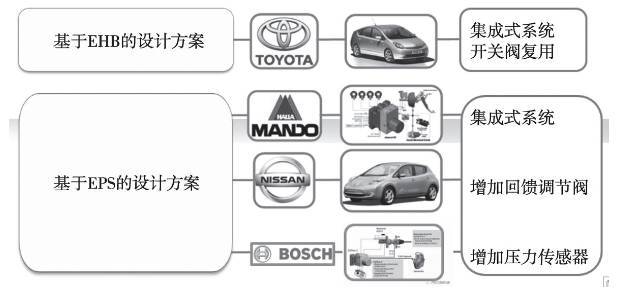
基于EHB的设计方案的代表车型为丰田Prius。该车型搭载丰田公司旗下爱德克斯公司基于电子液压制动(Electric-Hydraulic Brake,EHB)技术路线研制的电控液压制动系统(Electronically Controlled Brake,ECB),是最具代表性的制动能量回收产品,它对比传统的真空助力器有明显的优点,特别是快速反应方面(见图3)。
图3 爱德克斯ECB与传统产品性能对比
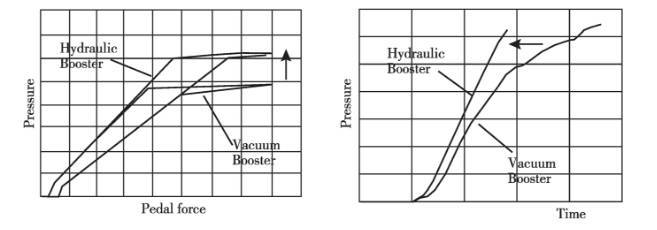
基于ESP的设计方案的代表车型是日产leaf。该车型为了满足制动能量回收的需求,其制动系统采用的是电动控制系统,它和丰田Prius的不同在于采用电机直接加力。该制动系统可在最大限度利用再生制动的同时,使之与摩擦制动配合,确保必要的制动,安装于电机室内驾驶席的前面。
(2)基于与制动主缸的集成设计
基于与制动主缸的集成设计主要分为伺服制动能量回收系统、电控真空助力液压系统及电控推杆能量回收系统,代表产品分别为本田Insight、大陆电控助力液压系统及现代索拉塔(见图4)。
图4 基于与制动主缸的集成设计典型制动能量回收系统
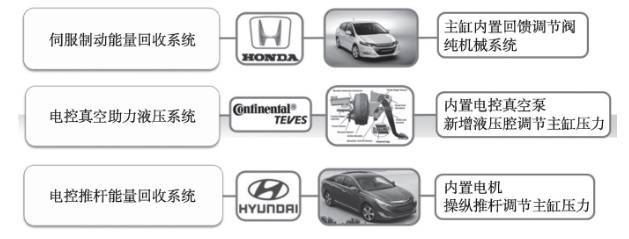
(3)国内制动能量回收系统的进展
基于液压控制单元的集成设计的制动能量回收系统是当前针对新能源汽车制动系统开发的主流方向,目前国内在制动能量回收系统的设计和制造方面已经取得了实质性进展。2011年,由清华大学牵头,联合亚太股份、广州科密、北理工、中科院电工所开发能量回馈式电动汽车制动防抱死系统,主要开发液压EABS和气压EABS产品。2015年,由亚太股份牵头承接国家科技支撑计划课题“电驱动轿车制动能量回收系统研发与产业化”,联合清华大学开始进行EABS的产业化工作和EESC(能量回馈式整车动力学控制系统)的研发,截至2017年,EABS产品已经在北汽C30、广汽A5HEV上完成集成,其对整车能量经济型的改善幅度在20%以上,亚太股份目前已具备3万套EABS的年生产能力;EESC产品在北汽C70轿车上已经完成装车,但仍处于研发阶段。
同时,亚太股份在2016年推出了IEHB系统,该系统是由吉林大学牵头、亚太股份和清华大学参与的国家重点研发计划项目课题,IEHB系统是基于EHB的制动能量回收系统设计方案。国内还有芜湖伯特利、武汉元丰等也在进行基于液压控制单元集成设计的制动能量回收系统的研发。
3.iBooster
机电伺服助力机构iBooster由博世公司开发,其不依赖真空源,可以满足现代制动系统的要求。iBooster可用于所有动力传动系统配置,尤其适用于混合动力车和电动车,且可实现全自动驾驶。通过与ESP © hev相结合,iBooster可实现几乎100%的制动能量回收(高达0.3g的减速度),涵盖公路行驶中所有常见的制动操纵,并使电动车辆的续航里程增加20%(见图5)。
图5 博世iBooster产品
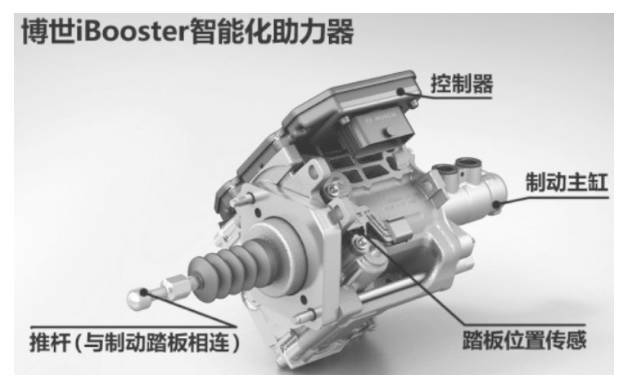
4.商用车电子制动系统EBS
电子制动系统(Electronic Braking System,EBS)集成了电控气压制动系统(Electro-Pneumatic Brake,EPB)、防抱制动系统(Antilock Braking System,ABS)和驱动防滑系统(Anti-Spin Regulator,ASR)三个子功能。
浙江万安科技股份有限公司在国内较早从事EBS系统研发与产业化工作,现为国内多家企业多个车型进行了匹配标定。广州科密和东风科技也在进行相关工作。
(二)电子制动系统技术发展新方向
1.电子驻车制动系统EPB
电子驻车制动系统(Electric Parking Brake,EPB),是一种新型的机电一体化系统,解决了传统汽车驻车系统存在的制动线路长、操作舒适性差、反应慢、安全性能差等问题。与传统的驻车制动系统相比,它用电子元件取代部分机械元件,并通过电线来代替部分制动线路和传动机构,缩短了驻车制动响应时间,提高了驻车制动性能,节省了车辆的质量和设备空间。
EPB分卡钳集成式(Caliper Intergrated Type)和拉索式(Cable Puller Type)两种类型,集成式EPB中,其动力执行机构也分为MOC(Motor on Caliper)、MOD(Motor on Drum),目前主要使用的是MOC,MOD使用很少。电子驻车系统(EPB)产品由美国TRW公司最先提出概念并成功研发,于2001年最先配备在菲亚特中高级轿车Lancia上,随后配备到北美和欧洲地区的许多车型上。德国库斯特(KUESTER)是生产拉索式EPB的企业,其EPB系统曾经占据全球市场一半的份额,但是由于拉索式EPB本身结构的局限性,及性能无法与卡钳集成式相抗衡,正在逐步退出市场。目前参与EPB产品竞争的主要是TRW、Continental、Bosch等几家跨国大公司。
在我国,电子驻车系统起步较晚,2008年才由天合(TRW)廊坊的工厂开始小批量生产。早期我国配置电子驻车系统的都是合资或外资品牌整车厂的高端车型:一汽大众的奥迪、迈腾,上海大众的途观,上海通用的别克等。这些车型的EPB均由天合(TRW)、大陆(Continental)等外资EPB供应商供应。近年来,国内零部件企业(亚太股份、力邦、伯特利等)在EPB研发与产业化上取得了较大的进展,均已开始批量供货。特别值得一提的是国内自主品牌的主流车型上开始装配国内零部件企业的EPB产品,如江铃陆风X5和X7、一汽奔腾X80、一汽森雅R020、众泰T600、一汽红旗等。在功能和可靠性上,国产EPB产品与外资品牌产品差距已经不是特别明显。
随着电动汽车的快速发展,EPB的普及程度越来越高,竞争日趋激烈,如何在不牺牲产品功能、特性、结构的前提下,缩减成本和降低系统复杂性,一直是零部件企业面临的问题。在这样的背景下,遵循德国VDA305-100规范,TRW率先提出了“EPBi”的概念,即集成化电子驻车系统,如图6所示。
图6 EPBi和独立式EPB、ESC结构对比
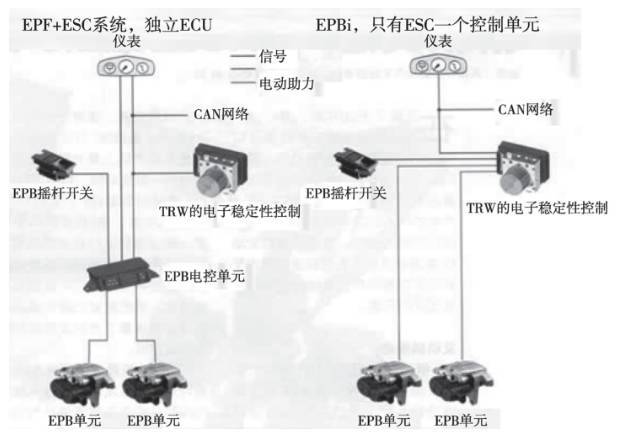
EPB与电子稳定系统的集成可以实现效益的最大化。一方面,EPB和ESC在系统可靠性方面有相似的要求;另一方面,这两个系统能够分享自动监测车辆和制动所需的控制程序和算法的重要部分。因此,可以创造最大的协同效应,提高控制单元中共享的处理器和内存的使用效率。由于取消了EPB控制单元,整车制造商不仅能减轻重量、减少装配工序,还能节省成本和安装空间。
Bosch公司和大陆公司等很快也推出了自己的EPBi产品,并开始在中国市场推广。EPBi产品的推广对国内零部件企业造成了巨大的困扰,其主要体现在以下几个方面。
①部分国内零部件企业并没有自己的ESC产品,无法进行EPBi的整体开发。
②ESC系统的制动安全性要求较高,国内主机厂很少选择国内企业提供ESC产品,导致国内企业的EPBi产品推广难度大。
③EPBi产品需要完全遵循德国VDA305-100规范,国内企业并没有相应的开发经验,在技术能力上天然又开始落后。
④当前情况下,国内企业只能提供EPBi产品的EPB部分模块(包括自身没有ESC产品无法开发EPBi和开发的EPBi得不到主机厂选择的),其用于EPBi集成的EPB部分内容为软件PBC(Parking Brake Controller)模块+动力执行机构,该部分集成到外资企业的ESC中之后形成EPBi产品,因为PBC+动力执行机构是从模块,将会受到外资企业的较大制约,丧失一定的主动权。
在这种情况下,国内零部件企业如亚太股份、芜湖伯特利等在开发符合VDA规范的PBC模块+动力执行机构的同时,也在研究开发EPBi产品,以期望在新趋势下具备整套系统的竞争力。
2.电子机械制动系统EMB
EMB系统以电池为能源、电机为动力装置,是相对传统的液压制动系统,其具备结构简洁、制动响应快、传动效率高、便于集成附加功能、利于环保及易实现智能驾驶等优点。由于去除了备用制动系统,EMB系统需要有很高的可靠性,因此必须采用比EHB系统更可靠的总线协议(TTP/C、Flexray等)。
此外,开发EMB系统还面临很多技术难点,比如:①由于制动能量需求较大,需要开发48V高电压系统;②制动器需要具有更好的耐高温性能,同时质量轻、价格低;③更好的抗干扰能力,抵制车辆运行中遇到的各种干扰信号。EMB由于存在电机、机械方面的技术难题,以及对可靠性要求高和成本等制约因素,一直没有真正得到实际应用。
乘用车方面开展EMB研究的厂家和科研机构较多,如博世、大陆、西门子、德尔福等都进行过大量研究与开发,部分进行了实际装车验证。国内仅有二汽、清华大学、南京航空航天大学在此项目上做了研究。瑞典瀚德公司是全球唯一进行商用车EMB开发的公司,设计了原型样机,并装车进行了验证(见图7)。目前其与浙江万安科技股份有限公司成立了合资公司进行产业化,目标是国内的纯电动客车市场。
图7 瀚德公司的商用车EMB
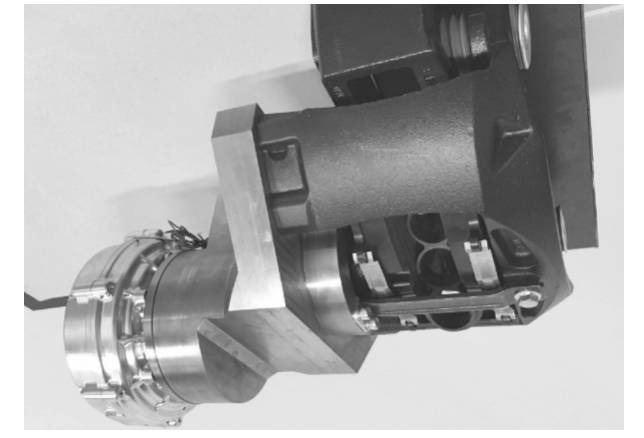
(三)行业问题及建议
由于电控制动系统种类繁多,不同的系统在国内的情况有所差别,但总的来看,问题主要集中在以下方面。
1.关键的原材料和零部件研发能力薄弱
关键的原材料和零部件研发能力偏弱,在高性能电机、轴承、电磁阀等上存在瓶颈。关键原材料如永磁体、轴承材料等研发速度较慢。
2.进入市场困难
由于制动系统安全性要求较高,国内主机厂很难选择国内供应商提供电控制动系统,总是要求供应商有批量装车经验,这样就存在是先有鸡还是先有蛋的问题。
3.行业利润下降
由于国内企业开发的产品在市场上难以形成大批量,导致生产成本普遍比国外厂家高,难以让市场接受。
4.开发投入大,周期长
此类产品系统复杂,安全等级要求高,开发投入十分巨大,一般企业难以承受。再加上市场前景不明,导致很多涉足的企业都是只有投入没有回报。
- 下一篇:浅谈汽车凸轮块精密锻造技术与装备
- 上一篇:矿用汽车齿轮喷丸强化工艺的研究与应用
举报 0
收藏 0
分享 169
-
乘势而上,北汽极狐2025将继续极速前行
2025-01-26 -
北汽蓝谷稳健前行,蓄势新一轮高质量发展
2025-01-26 -
问界M7被鉴定存在“刹车失灵”和“人为修改数据
2024-11-07 -
大众中国计划裁员!
2024-09-24
编辑推荐
最新资讯
-
“锂”想万家——比亚迪叉车在家电行
2025-04-28 10:02
-
全球工业数字化领袖齐聚申城,共绘智
2025-04-28 08:28
-
思看科技受邀出席第三届联合国教科文
2025-04-27 13:29
-
聚势谋远,智领新程——五菱柳机以硬
2025-04-27 13:22
-
聚势求新、智驱未来——五菱工业底盘
2025-04-27 13:22