CAE技术在后纵梁延伸板模具开发中的应用
2019-01-11 10:39:32· 来源:张学文,王冲 锻造与冲压
本文介绍了CAE技术在汽车冲压件开发中的目标和作用,对比了汽车冲压件两种成形工艺的特点及应用条件,介绍了零件冲压工艺及模具的设计原则。通过某车型后纵梁延伸板的模具开发案例,详细阐述了CAE技术在模具设计制造中的实际应用。汽车冲
本文介绍了CAE技术在汽车冲压件开发中的目标和作用,对比了汽车冲压件两种成形工艺的特点及应用条件,介绍了零件冲压工艺及模具的设计原则。通过某车型后纵梁延伸板的模具开发案例,详细阐述了CAE技术在模具设计制造中的实际应用。
汽车冲压件模具在整车的制造环节中占有重要地位,直接影响到新车上市时间和价格,而模具的设计制造离不开有效的板料成形模拟技术。CAE技术是利用计算机有限元模拟对板料冲压成形过程进行仿真分析,通过提高成形裕度,优化零件设计,改善工艺方案,最终实现缩短模具制造周期,提高零件质量的目的。在模具设计阶段,优化冲压工艺方案,消除潜在质量风险;同时判定零件成形的难点和关键区域,制定解决方案,指导现场模具调试。国外大型汽车集团,其模具开发一般都要借助于一种或几种CAE软件,以提高其成功率,确保其制造周期的可控。
汽车冲压件的成形工艺一般分为拉延和压形两种,通过CAE分析可以选择最优的工艺方案。本文以某车型后纵梁延伸板为例,重点讲述了CAE技术在压形模具开发中的实际应用,包括工艺方案确定、成形模拟分析、调试问题解决等,其成功经验对于类似零件的开发具有借鉴和指导意义。
CAE技术的目标和作用
汽车覆盖件模具制造的最大风险来自于冲压工艺的变更和失效,导致模具大量修改,增加模具的调试工作量。板料成形CAE技术是解决此类问题的最佳技术手段,它在缩短模具开发周期、降低模具制造成本、提升零件质量等方面发挥着重要作用。其目的就是在可控的成本范围内,高质量、按时间节点完成模具开发。CAE技术的主要目标和作用如图1所示。
冲压件成形工艺的分类和特点
汽车冲压件成形工艺一般分为拉延和压形两种,在实际生产中,二者的区别主要有以下两点。
⑴拉延工艺特点及适用条件。
拉延是指将板料先成形后切边,拉延成形时有压边圈,板料四周压紧,金属充分流动,不易产生皱褶。拉延后序需要修边冲孔等工序,一般用于中大型覆盖件,零件形状变化剧烈或侧壁强度不均匀。此工艺相对浪费板料,需要更大的成形力,且侧壁回弹和卷曲问题更严重。
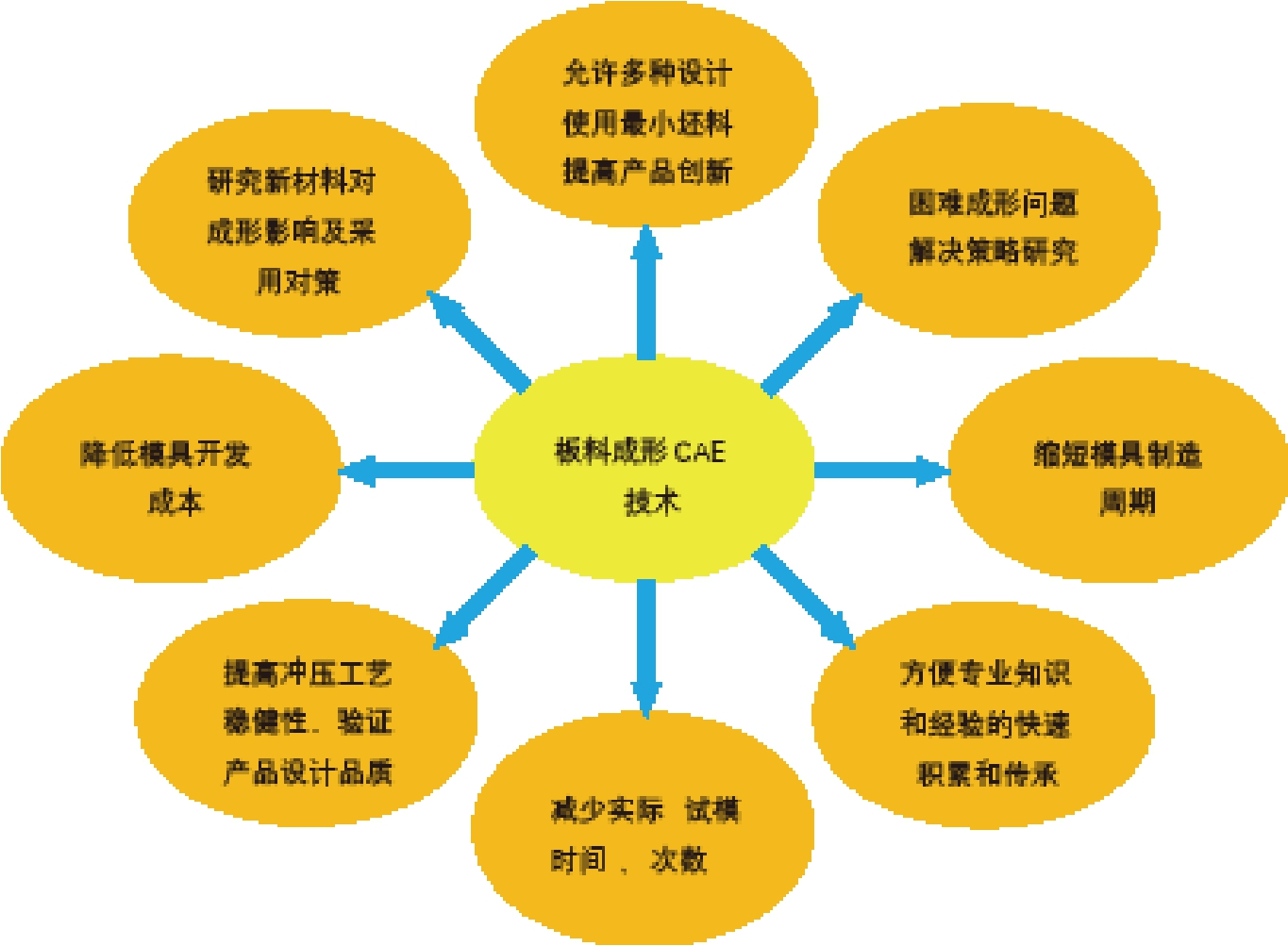
图1 CAE技术的目标和作用
⑵压形工艺特点及适用条件。
压形是指将板料先切边后成形,首先根据零件形状计算出坯料尺寸,然后落料再压形,一般不需要压边圈。其优点在于材料利用率高,但易出现皱褶。一般用于料厚较大的支架、加强板等表面要求不高的冲压件。产品俯视或者正视方向有形状变化导致成形过程中板料有被压缩的趋势,但并不严重时,推荐采用这种工艺。
压形工艺及模具的设计原则
由于压形工艺具有材料利用率高、模具结构简单、侧壁回弹小、机床吨位要求低等优点,一些形状相对简单、表面质量要求不高的内板件,特别是高强钢零件由于延伸率较低,推荐采用此种工艺。在压形工艺制定和模具设计时,必须遵循一定的原则。
压形翻边模的工艺设计准则
⑴考虑翻边或者法兰回弹角度的处理,零件设计应有3°~6°的回弹补偿角。
⑵产品凸模圆角应该尽量小,针对不同的材料强度,R角一般为料厚的1~2倍。
⑶制件形状不均匀时压形会由于残余应力导致回弹或者扭曲,工艺应考虑型面补偿。
⑷坯料线需要零件展开返算得出,一般需经过几轮试模后测量,修改数模重新加工调试。
压形翻边模的模具设计准则
⑴考虑翻边成形的侧向力,镶块应被置于铸件本体内或者设计足够的挡墙。如图2所示。
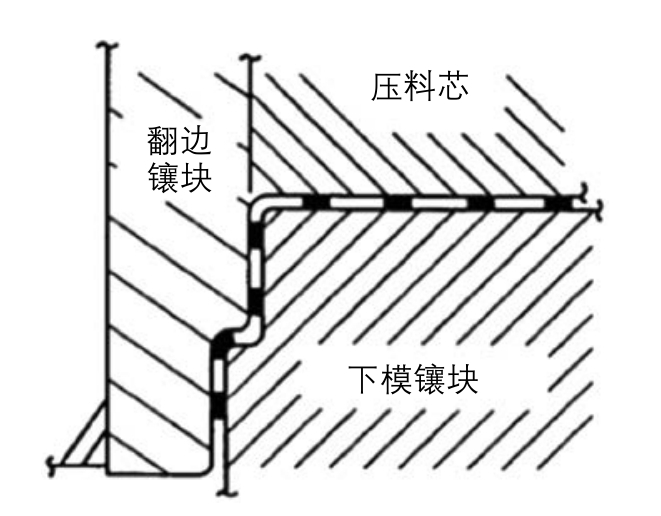
图2 翻边镶块示意图
⑵凸凹模翻边间隙不应超过一个料厚。
⑶可考虑包角翻边以处理回弹,参考图3翻边的回弹处理方法。
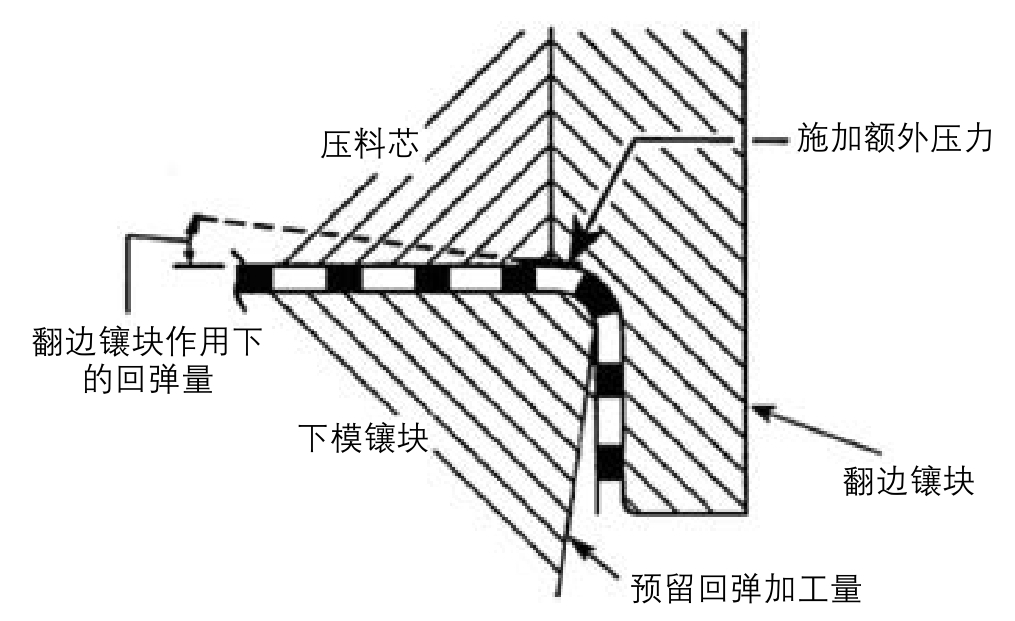
图3 翻边回弹处理示意图
后纵梁延伸板案例分析
以某车型的后纵梁延伸板为例,为满足客户要求,保证零件质量,利用板料成形CAE技术对零件进行了成形模拟分析,并指导模具调试过程,取得了良好的效果。
零件信息
图4为后纵梁延伸板示意图。零件材料:SHP440热轧钢,料厚:1.8mm,尺寸:298mm×137mm×150mm。抗拉强度≥440MPa,屈服强度≥305MPa。零件厚度大、材料强度高、成形困难。
工艺方案确定
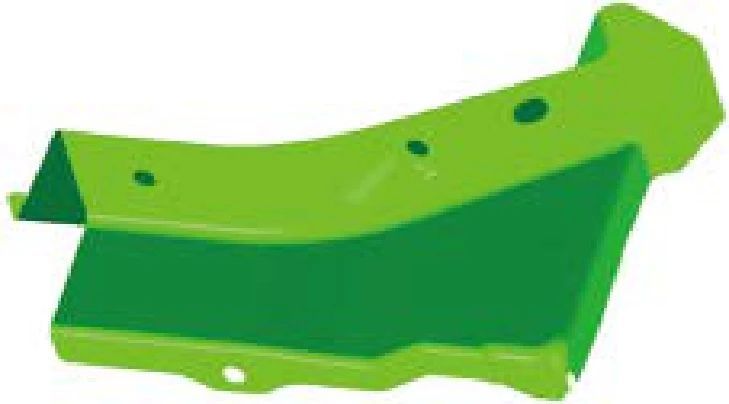
图4 后纵梁延伸板示意图
在冲压工艺方案制定过程中,为降低零件调试风险,首选采用拉延成形、修边、整形、修边冲孔、斜楔冲孔等工序。但是客户要求该零件的材料利用率必须达到60%以上,若按上述工艺生产,利用CAE软件计算出材料利用率还不到40%,这样既不满足客户要求,同时又造成极大的成本浪费。经过反复讨论,最后决定,利用有限元逆算法模拟零件采用压形工艺的可行性。图5采用AUTOFORM软件模拟零件直接成形的结果。
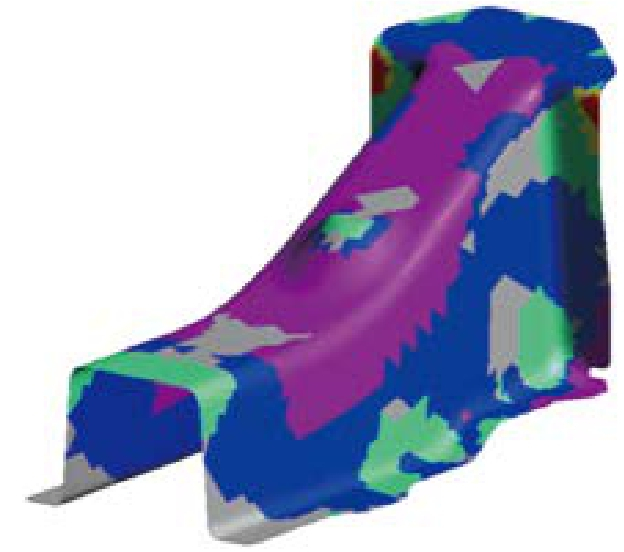
图5 零件直接成形模拟结果示意图
我们从模拟结果可以看出,零件直接成形还存在较严重的起皱缺陷,因此尝试增加整形工序。采用落料、压形、整形、精修边冲孔、斜楔冲孔等工序,相对于拉延成形工艺,模具工序并未增加。零件成形、整形模拟结果如图6、7所示。零件起皱缺陷得到了很大程度的缓解,结果可以接受,确定采用上述工艺方案。结合压形工艺及模具的设计原则进行模具设计制造。
图6 零件成形结果示意图
图7 零件整形结果示意图
指导现场模具调试
采用落料工序的主要风险在于板料展开不准确,可能需要多轮试验以获得坯料边界线,增加模具调试难度。利用FASTAMP有限元逆算法对零件进行展开,有效减少了试模次数。模拟展开结果与实际调试结果比对,坯料线相差不大,图8为零件模拟展开与实际调试坯料线对比情况。
图8 零件模拟展开与实际调试坯料线对比情况
根据所确定的工艺方案,采用模拟展开的坯料线,进行模具调试,其结果如图9、10所示。可以看到,制件没有明显的起皱、开裂或叠料缺陷,焊接面平整,满足零件质量要求。
结束语
图9 成形后制件
图10 整形后制件
冲压成形CAE分析技术的应用为我国汽车和模具行业的发展起到了积极的推动作用。本文通过某车型后纵梁延伸板的模具开发案例,阐述了CAE技术在工程上的成功应用。工艺设计阶段,利用板料成形模拟技术有效解决了零件的工艺问题,同时将材料利用率提高至70%以上,并且简化了模具结构,降低了制造和生产成本。模具调试阶段,利用有限元逆算法准确获取了坯料边界线,降低了车间工人的调整难度,大大减少了现场模具调试工作量,并最终获得了良好的零件状态。掌握冲压CAE技术需要在具体工作中努力思考和探索,不断积累现场模具调试的经验,推动冲压技术水平继续向前发展。
作者简介
张学文,高级工程师,主要从事汽车车身冲压同步工程以及车身冲压件模具开发,主持完成的D310驾驶室模具开发和拼焊板类零件的工艺及模具开发等项目获得东风汽车公司科技进步奖,拥有专利8项。
- 下一篇:详解大功率汽车控制单元模块
- 上一篇:多亏博世力士乐,零误差拧紧不是梦
举报 0
收藏 0
分享 119
-
冲压技术在电机叠片制造的应用
2024-09-06 -
车身零部件包边质量控制要点
2024-09-05 -
轻量化技术——热汽胀形工艺技术解析
2024-09-04 -
高强板车身件冲压技术
2024-09-02
最新资讯
-
全球产业链聚沪 共探双碳新路径 SNEC
2025-04-18 18:05
-
柯马签订具有约束力的协议收购 Autom
2025-04-17 13:01
-
高效协同新范式:比亚迪叉车领创智能
2025-04-17 10:04
-
埃马克德国总部迎来中国社科院工业经
2025-04-15 09:40
-
埃马克这项全新应用即将在CIMT惊艳首
2025-04-15 09:37