汽车车身轻量化的关键工艺制造
2019-01-11 09:38:13· 来源:橡塑技术与装备
近年来,在我国汽车市场逐渐实现高速发展后,人们对汽车的要求已不再仅限于功能之上,对汽车的整体车身也有着较高的要求。以客户群当前的需求来看,汽车车身轻量化是目前广大客户群所追求的,车身轻量化不仅能够有效减轻车身的自重,还能
近年来,在我国汽车市场逐渐实现高速发展后,人们对汽车的要求已不再仅限于功能之上,对汽车的整体车身也有着较高的要求。以客户群当前的需求来看,汽车车身轻量化是目前广大客户群所追求的,车身轻量化不仅能够有效减轻车身的自重,还能实现节能减排,使汽车保持轻量化的同时达到环保的目的。这也要求着当前汽车市场需改变发展战略,改变市场方向,并利用工艺制造技术及轻量化材料来打造符合客户群需求的汽车市场,以此提高汽车市场的整体发展速度。
一、汽车车身轻量化的关键工艺制造技术控制及研究
1.采用轻量化制造材料
材料是打造轻量化车身的重要组成之一,在车身材料选择上,其需选择安全系数高、优质的工艺性能以及低经济等特点材料。选择轻量化制造材料能够有效减轻车身的整体重量,使汽车制造能达到轻量化目的。从我国汽车市场当前现有的轻量化材料来看,其主要包括高强度钢、铝合金、铝镁金等。高强度钢:钢铁一直是汽车生产环节中最常用的一项制造材料,在相同的强度标准下,高强度钢能够削减钢板的厚度,使汽车车身达到轻量化目的。根据强度等级划分,钢可分为低、高、超高三种强度钢。这三种不同等级强度的钢材料在经过汽车生产多年后,发现高强度钢是汽车车身实现轻量化最有效的一项材料,这也表明,在我国未来多年后,钢铁材料仍会是我国汽车生产的主要材料之一,并在汽车的不同组成构件中也会有十分普遍的应用。铝合金:铝合金材料的密度是钢铁材料的1/3,也是目前汽车生产商运用最普遍的轻型材料。
铝合金材料在性能上与高强度钢材质相比,具有导热性能佳、耐腐蚀性强等特点,但在强度上弱于高强度钢,但是,通过一定的制造技术,能够完全满足于汽车轻量化生产要求。另外,铝合金材料能够更耐得住外部撞击,对汽车整体的安全系数更具有保障。另外,铝合金材料还包括了变形铝合金以及铸造铝合金,铸造铝合金是其中使用最广泛的一项材料,主要占据车身的78%左右,在汽车车身的多个部位都有着重要的应用。镁合金:镁合金分别占据着铝和钢的2/3 以及1/4,是在汽车车身材料中质量最轻的一项有色金属,该材料还具备很高的轻度及钢度,具有显著的轻量化效果。另外,镁合金还具备良好的散热功能,是当下我国汽车生产市场最具发展潜力的一项轻量化材料。
2.轻量化关键工艺制造技术
轻量化工艺制造技术主要分为热成形技术与激光拼焊技术。首先,热成形技术是利用热冲压高强钢板材加热于奥氏体在接近温度上,然后进行一段时间的保温工作,使其均匀奥氏体化,再将其快速转移至具备冷却系统的模具当中进行冲压,再对其开展保压与冷却工作,使该奥氏体能够转化为板条状马氏体,提高该材料的整体强热成形的主要工艺技术如图1所示。
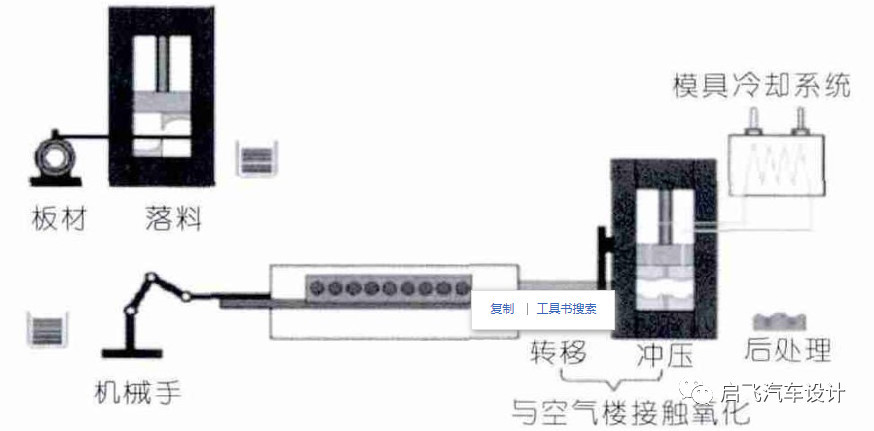
图1 热成形技术原理
按照原理来说,高强度钢在常温环境下其形状塑造范围十分狭窄,并且成形较差,容易使材质出现开裂现象,材质回弹机率大,无法应对当前汽车碰撞所需的安全系数。而热成形工艺制造技术则是根据刚强度钢制造技术所具备的种种缺陷而发展起来的更完善的一项新型制造技术,该技术能够使高强度钢经过产热冲压后,将其材质的抗拉强度提升至1700MPa以上,使汽车车身整体重量得到减轻的同时,提高了车身的强度与钢度,使车身整体更耐撞击,也具备更高的安全性。
当前,热成形工艺主要分为两大类型:第一是直接成形工艺制造技术。该工艺制造技术是指对板材进行直接冲压,较为广泛应用于汽车结构简单的零件。第二是间接成形工艺制造技术,该技术在板材加热前对其进行预先成形制造,再将其放于模具当中进行快速冲压,较为广泛应用于结构复杂的汽车零件。
另外,热成形所采用的板材主要分为无镀层与有镀层两种类型,无镀层在应用热成形工艺制造技术时,需增加后续加工环节,在后续加工中进行喷丸处理,以此清除板材表面的氧化层。热成形是当前汽车生产中的新型制造工艺,该工艺与传统的冷冲压技术相比,热成形主要具备了五大优势:
(1热成形工艺制造技术具备回弹小的优势,其能够有效提高零件大小尺寸的精准度,这是传统制造技术无法达到的。
(2热成形工艺制造技术能够降低汽车各个零件的整体厚度,并有效提高零件的自身强度对汽车车身轻量化的生产十分有利。
(3热成形使板材在高温环境下能够具备更优质的塑性,使汽车十分复杂的组成零件不容易出现损坏现象。
(4热成形制造技术在使用时能够使板材变形抗力降低,减少了成形成本的支出。
(5在应用热成形后,板材的整体强度能够在原基础上大力的提高,其表面硬度也会有效提高。
热成形工艺制造技术在未来的应用趋势上,其主要面临的问题是技术的提升与工艺的改进上,由于热成形工艺在我国发展起步较晚,目前在生产上还未形成有可观的规模,无法应对当前我国汽车热冲压所需的大规模产量,虽然我国当前已有部分热成形的生产产业,但这些产业的还未有自主知识产权。
激光拼焊工艺制造技术,该技术工艺是在20世纪时期起步,在当时该技术的应用主要是为了完善钢板宽度不足问题,在伴随我国汽车生产业实现了高速发展后,激光拼焊制工艺制造技术在越来越多的国家得到了广泛的推崇与应用,并成为了目前世界上应用最广泛的一项制造技术,该技术能够有效满足当前汽车零件的设计要求,并根据不同材质及厚度的零件来将其通过焊接方式组成一个完整零件,再将其冲压成所需零件形状,减少资源耗能。与传统技术工艺相比,该技术能够有效发挥不同板材的优势,提高车身整体材质的强度,并通过减少零件数量,来达到降低成本的目的。另外,激光焊接通过对接工艺,能够消除搭接缝,使汽车车身能够有效提高抗腐蚀系数。虽然该技术工艺目前在我国汽车生产生产领域中得到了广泛应用,但由于成型技术还尚未成熟,还难以找到适用于激光拼焊板材质,因此,激光拼焊板当前还只仅限于用于不同钢板与铝板的焊接,而在其它材料上的用途十分稀少。
二、结束语
目前,我国在汽车车身轻量化的材料上,已经出现了明显的多元化应用趋势,单一的车身材料已无法满足当前车身所需的强度及刚度,因此,在汽车车身的未来发展中,其轻量化材料会实现多种材料的组合制造,并在车身工艺制造技术上,会主要控制工艺材料的使用量,并开发可回收材料,使汽车车身达到轻量化要求的同时也具备低耗能的优势,有效提高材料的利用率,利用各项技术提高车身的安全系数,完善传统工艺的不足之处,以此实现汽车车身轻量化的生产目标。
举报 0
收藏 0
分享 123
-
旭化成首战全球供应链管理大赛斩获佳绩
2025-03-03 -
旭化成授权斯尔邦高纯度碳酸盐生产技术,助力二
2024-12-13 -
华为尊界S800的座椅会有什么亮点?
2024-11-27 -
博世最新宣布裁员7000人
2024-11-06
编辑推荐
最新资讯
-
华为、地平线、大众、东风、起亚等引
2025-04-24 08:27
-
全球产业链聚沪 共探双碳新路径 SNEC
2025-04-18 18:05
-
柯马签订具有约束力的协议收购 Autom
2025-04-17 13:01
-
高效协同新范式:比亚迪叉车领创智能
2025-04-17 10:04
-
埃马克德国总部迎来中国社科院工业经
2025-04-15 09:40