电池壳第一道次冲压成形模拟分析
2019-01-28 12:42:00· 来源:锻造与冲压 作者:张茜
本文以唐钢自主研发的电池壳钢为对象,采用有限元软件Dynaform对电池壳第一道次冲压过程进行模拟分析,从而确定合理的冲压边界条件,探究材料强度、加工硬化指数、塑性应变比等材料参数对冲压零件壁厚的影响。由于节能和环保的压力,新能
本文以唐钢自主研发的电池壳钢为对象,采用有限元软件Dynaform对电池壳第一道次冲压过程进行模拟分析,从而确定合理的冲压边界条件,探究材料强度、加工硬化指数、塑性应变比等材料参数对冲压零件壁厚的影响。
由于节能和环保的压力,新能源电动车正迅速的从实验室走向商业化和市场化。电动汽车采用电池组作为主要的能量来源。电池组需求量大,零件表面要求高,给钢铁企业带来了新的挑战。一台49座纯电动客车,其电池组由1.8万个电池组成,在电池组中任意一电池壳出现砂孔、冲压开裂、轧制横折纹等问题,均无法满足使用要求,其研发难度之大,让国内很多钢厂望而却步。河钢唐钢起初研发电池壳钢试用生产时,也曾出现拉丝、夹缝等缺陷。因此,本文以某纯电动客车电池组电池为原型,采用Dynaform软件对电池壳第一道次冲压成形过程进行仿真分析,评价影响电池壳冲压成形的关键材料参数。
电池壳冲压成形有限元模型及边界条件设定
研究背景
某电动客车厂生产电池壳时,采用0.5mm厚板料经过落料→6道次变形冲压→整形、切边等工序得到,不同道次零件如图1所示,不同道次零件尺寸见表1。实际生产时,每分钟可得到20个成品电池壳。
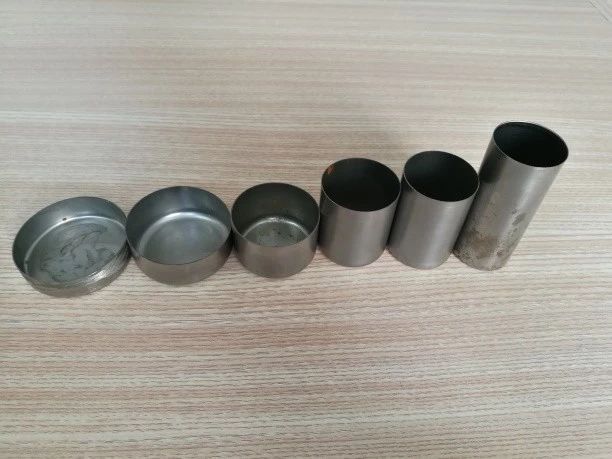
图1 不同道次冲压变形后电池壳(已切边)
几何模型建立
本文以电池壳生产过程中第一道次冲压过程为研究对象,根据不同道次零件尺寸,参照冲压手册中圆筒形件冲压毛坯尺寸计算公式和无凸缘圆筒形拉深件的修边余量经验值表,可以确定初始坯料尺寸为φ104mm。第一道次零件尺寸为φ55mm×27mm,底部外圆角半径为4mm,可得到凹模尺寸,通过Dynaform软件自带的偏置功能偏置模具间隙即可得到凸模尺寸。由于第一道次为不减薄冲压,其模具间隙为(1.1~1.3)t,拟定模具间隙为1.1t得到凸模。各零件的形状如图2所示。
表1 不同道次冲压后得到零件尺寸

表2 唐钢电池壳钢不同方向力学性能
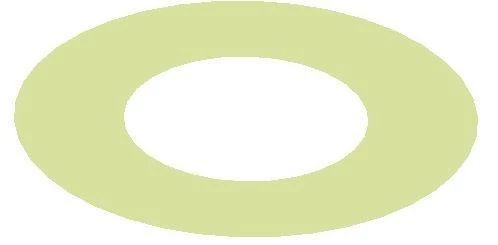
边界条件设定
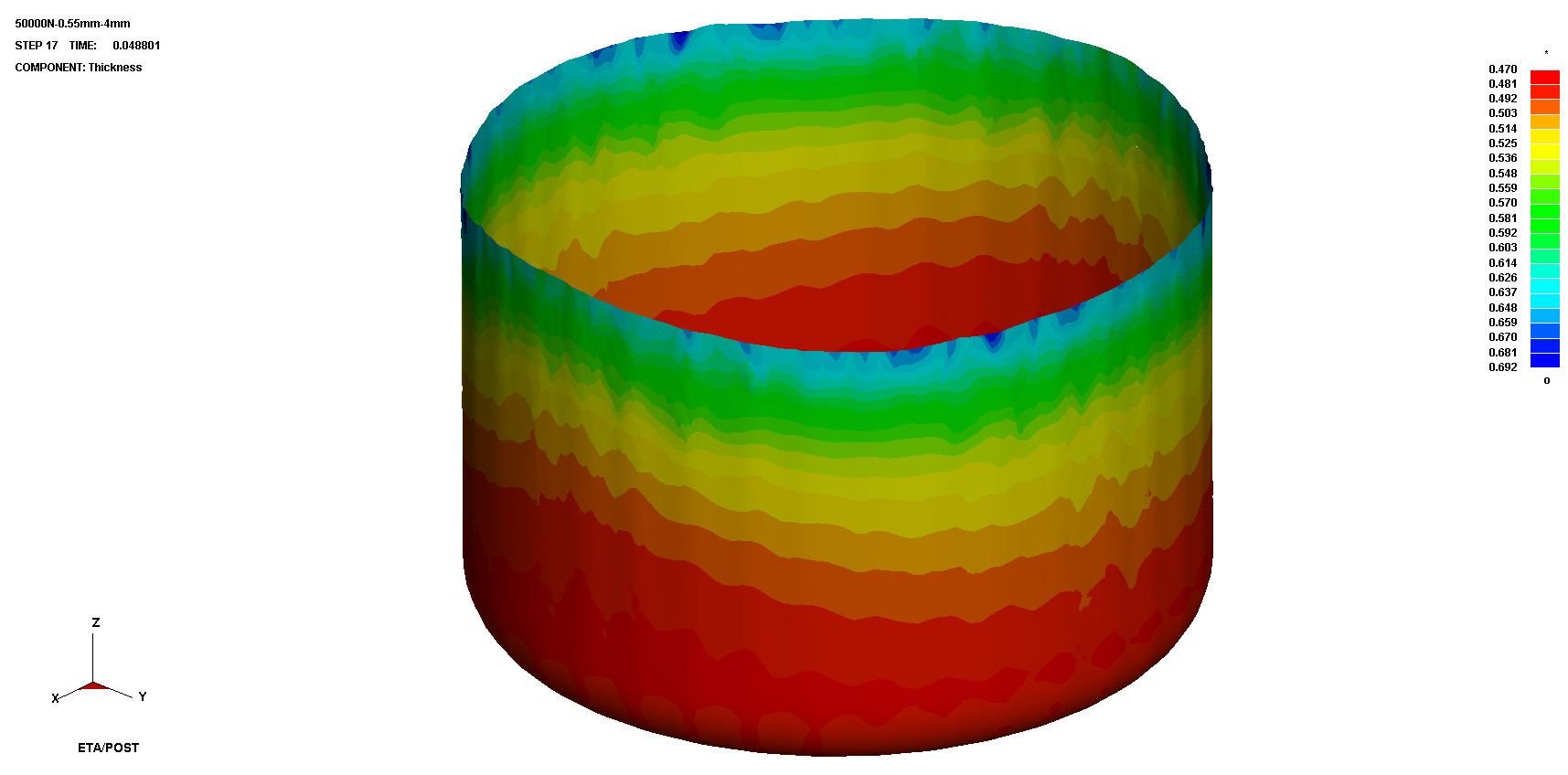
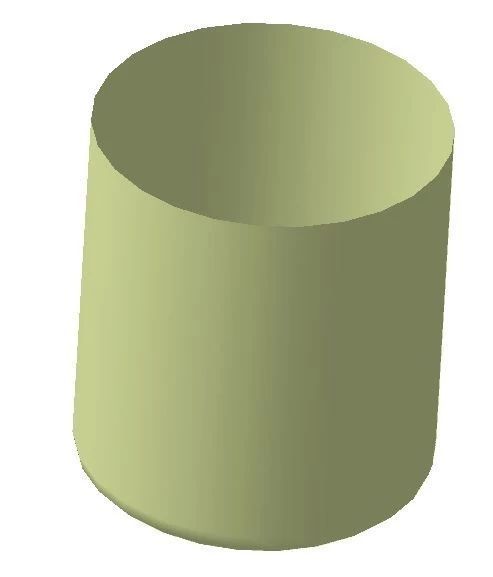
凹模 凸模
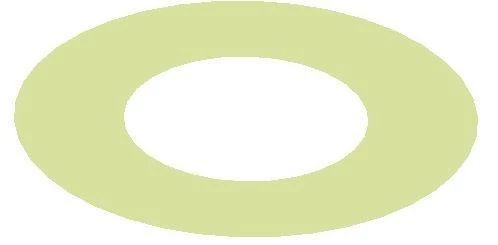
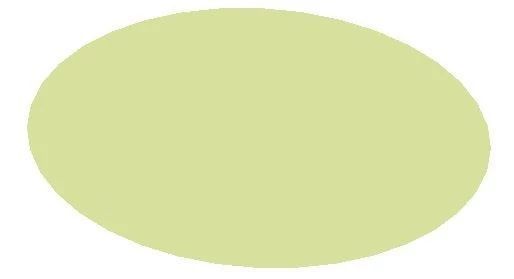
压边圈 板料
图2 各零件形状
采用Dynaform对冲压过程进行模拟,模具单元定义为刚性壳单元,坯料单元选用计算效率较高的Belytschko-Tsay单元(简称BT单元) ,采用自适应网格划分方法将模具和坯料划分为四边形单元和三角形单元。求解格式采用显示动力学算法。本构关系选用Barlat屈服模型(36#),该模型适用于任何薄板金属成形分析,材料参数借鉴唐钢某次生产的电池壳钢力学性能(表2)。
模拟结果分析
凹模上圆角尺寸对冲压成形的影响
根据电池壳钢生产速度可估算出模具冲压速度约为1000mm/s,模具间隙和摩擦系数根据经验分别设定为1.1t和0.08,压边力设定为4000N,在2~10mm范围内调整凹模上圆角尺寸进行模拟分析,模拟结果如图3所示,不同凹模上圆角半径对零件影响如图4所示。
通过模拟可以看出,随着凹模上圆角半径的增加,减薄区域呈现减少的趋势,起皱区域呈现增加的趋势,板料厚度差变小。当凹模圆角半径小于6mm时,厚度变化严重;大于6mm时变化较平缓,但随着圆角半径的增加,起皱区域较大,浪费较多,综合考虑凹模上圆角半径取值为6mm。
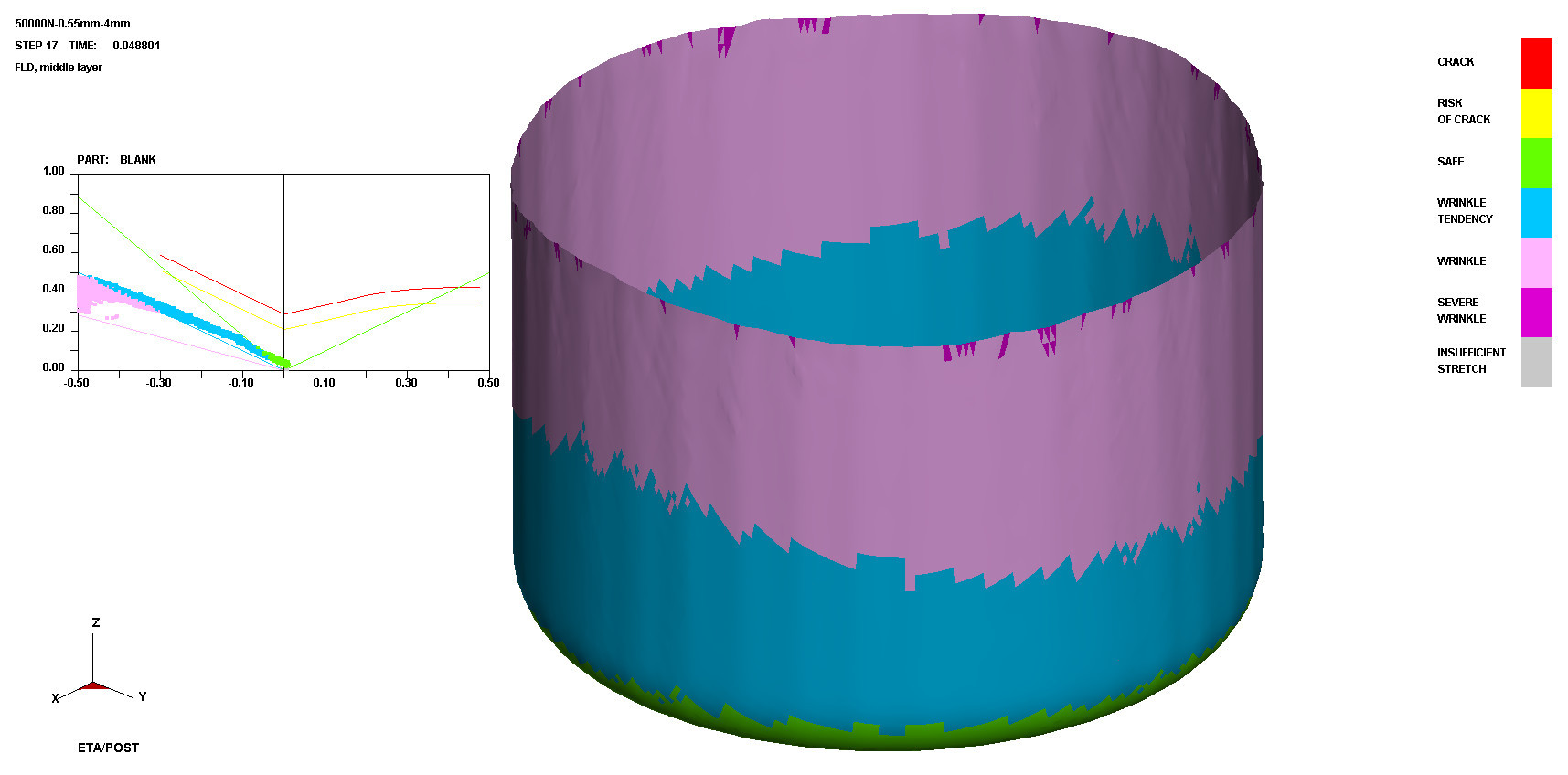
成形性
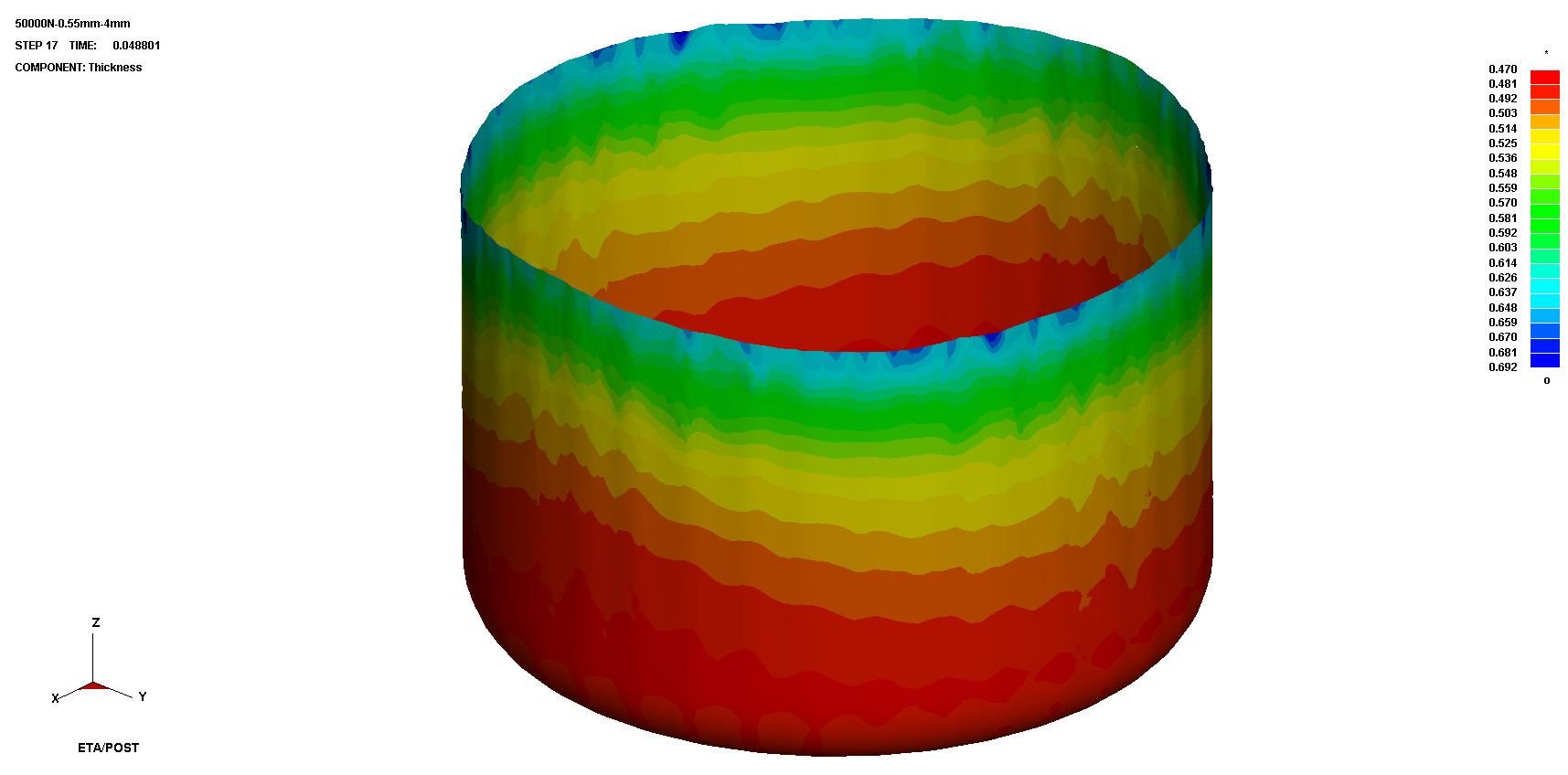
厚度
图3 零件模拟结果
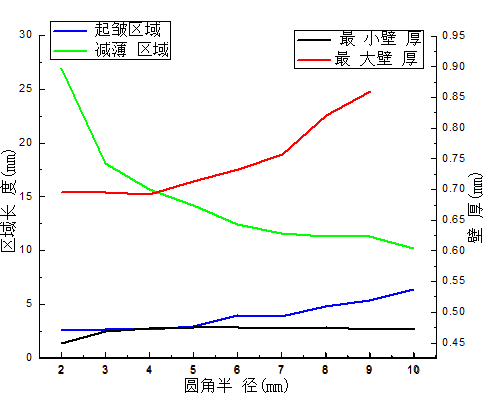
图4 不同凹模上圆角半径对冲压件影响
模具间隙对冲压件的影响
分别采用1.1t、1.2t、1.3t间隙进行冲压过程模拟,模拟结果如图5所示。
通过模拟可以看出,当模具间隙>1.1倍料厚时,继续增大模具间隙,几乎不影响起皱区域,但会略微增大减薄区域长度,整体而言对冲压件厚度无影响。所以,模具间隙设定为1.1t是合理的。
摩擦系数对冲压件的影响
分别用 0.02、0.04、0.06、0.08、0.10、0.12的摩擦系数进行冲压模拟,模拟结果如图6所示。
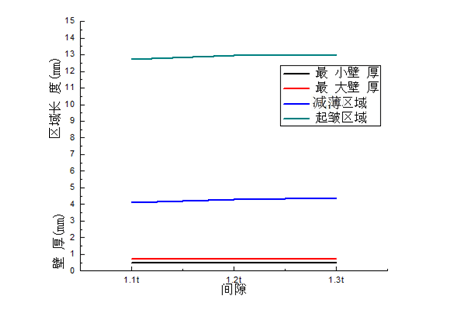
图5 不同模具间隙对冲压件的影响
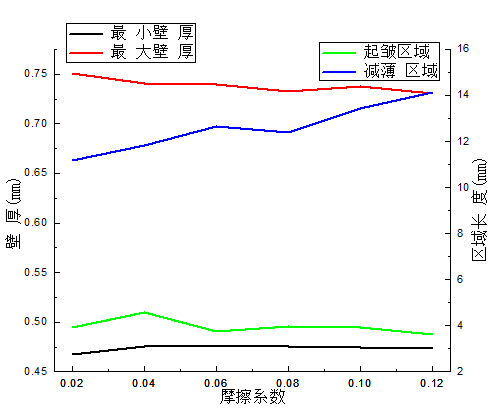
图6 摩擦系数对冲压件的影响
通过模拟可以看出,随着摩擦系数的增加,减薄区域呈现增大趋势,摩擦系数越小,减薄区域越小,但实际生产中模具摩擦系数很难达到非常光滑的程度,结合实际情况及相关文献,将摩擦系数选定为0.08是合理的。
压边力对冲压件的影响
分别采用1000N、1500N、2000N、4000N、6000N、8000N、10000N、12000N的压边力进行冲压过程模拟,模拟结果如图7所示。
通过模拟可以看出,在一定范围内压边力对成形件影响不大,但当压边力小于1500N时,零件起皱非常严重;当压边力为2000~12000N时,对冲压结果几乎无影响。所以采用4000N的压边力进行冲压模拟是合理的,如图8所示。
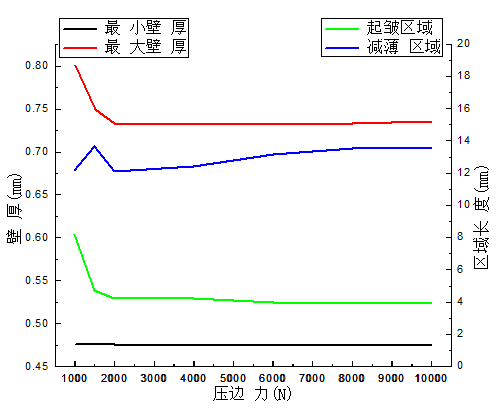
图7 压边力对冲压件的影响
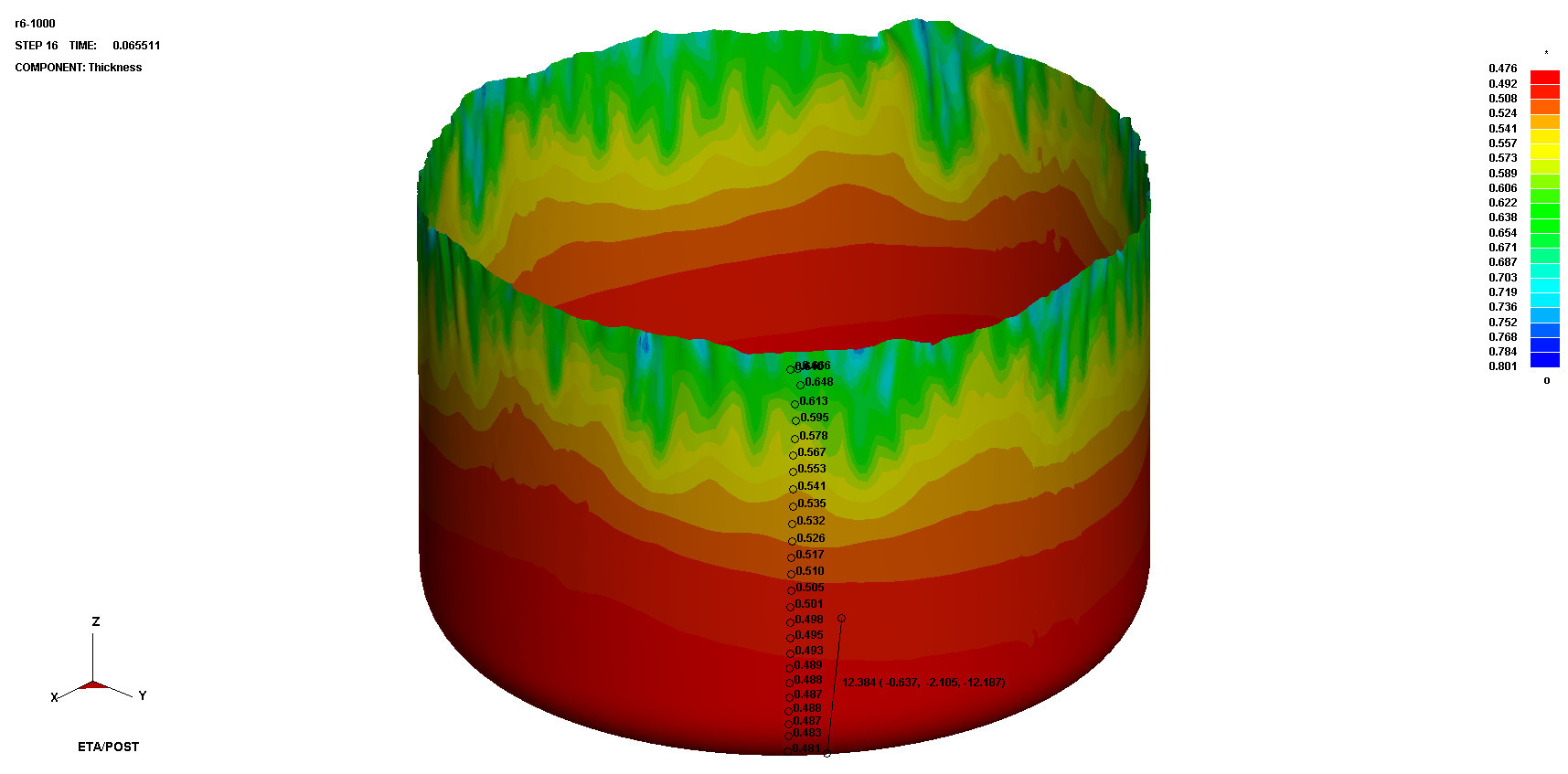
(a)压力边<1500N
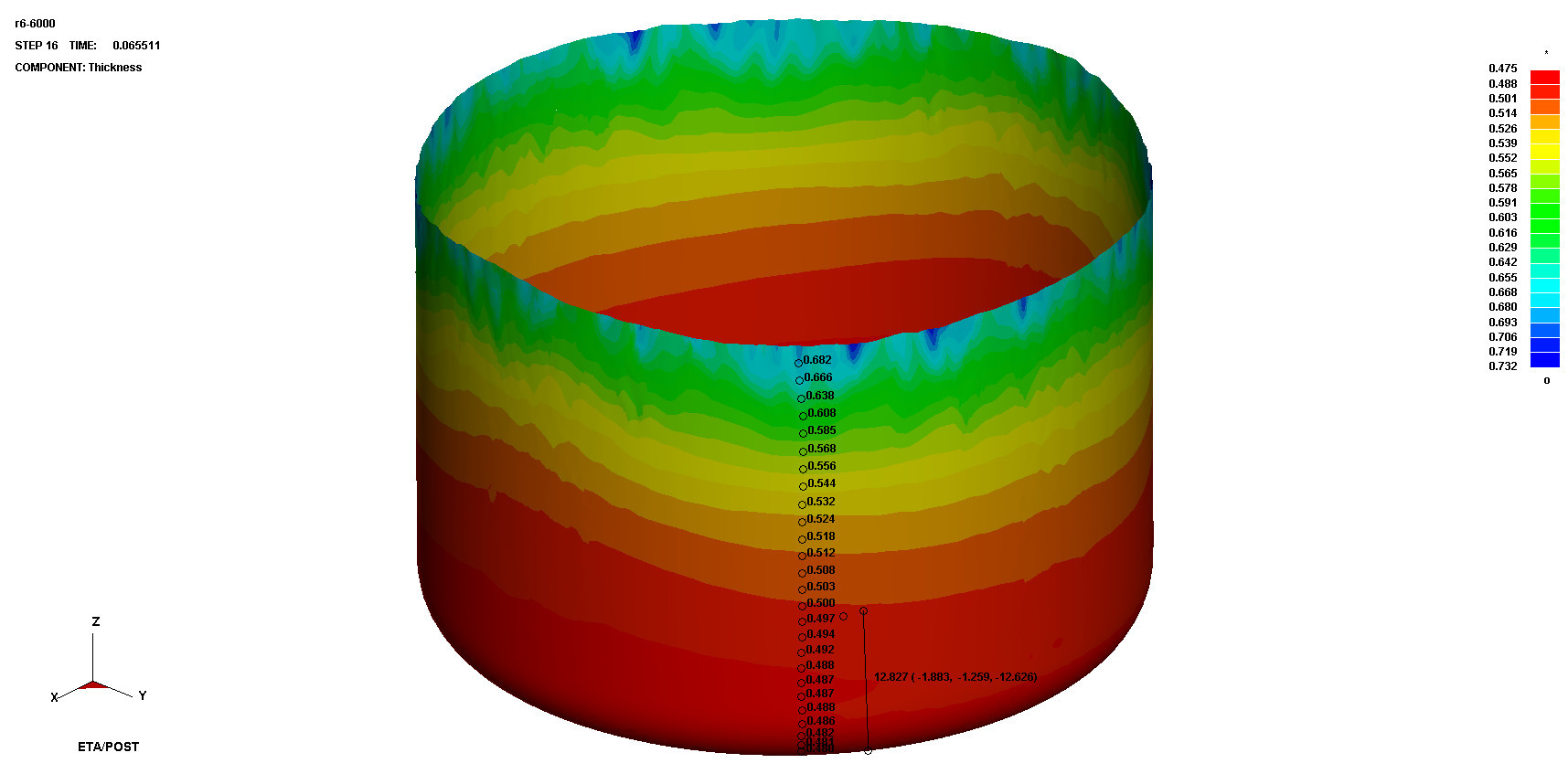
(b)压力边>2000N
图8 不同压边力下零件厚度分布
不同材料参数对冲压结果的影响
⑴屈服强度对冲压件的影响。以原始电池壳钢的力学性能为基准,在保证r值和n值不变的情况下,沿弹性段斜率上下平移调整屈服强度使其在170~240MPa之间进行冲压模拟,模拟结果如图9所示。通过模拟可以看出,在n值和r值不变的前提下,屈服强度波动不影响零件壁厚。
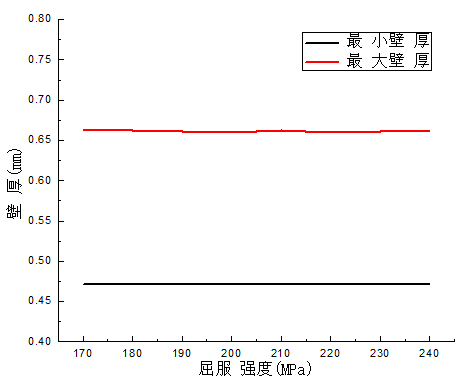
图9 屈服强度对零件壁厚的影响
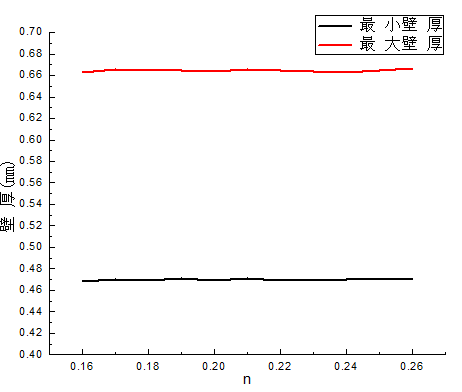
图10 n值对零件壁厚的影响
⑵加工硬化指数n对冲压件影响。采用Krupskowsky law 硬化准则 [σ=K(ε0+ε)n,其中ε0为屈服强度对应的应变值],在0.16~0.26范围内调整n值进行模拟,模拟结果如图10所示。通过模拟可以看出,在一定范围内调整n值不影响零件壁厚。
⑶塑性应变比r对冲压件影响。在保证屈服强度和n值不变情况下,在1.3~2.4范围内调整r值进行模拟,模拟结果如图11所示。通过模拟可以看出,随着r值增加,冲压件最小壁厚基本不变,但最大壁厚值有所降低,上部最厚厚度值减小,冲压件壁厚均匀性更佳。
⑷各向异性差△r对冲压件影响。在不同批次生产的电池壳钢中,选取△r在0~0.3范围内波动的材料参数进行模拟,模拟结果如图12所示。通过模拟可以看出,随着Δr增加,冲压件厚度分布基本不变,但凸耳高度明显增加。
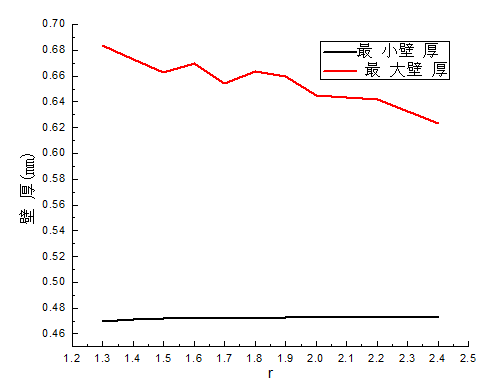
图11 r值对零件壁厚影响
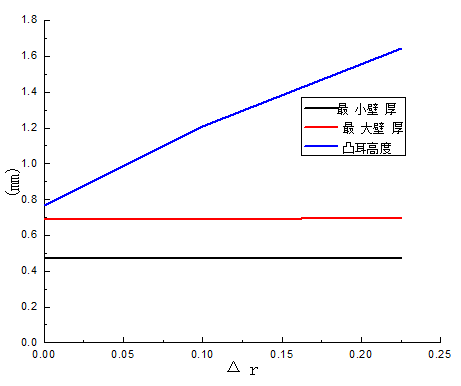
图12 △r对零件壁厚及凸耳的影响
⑸r均值对冲压件的影响。从材料数据库中选取Δr近似、r均值不同的DC01、DC03、DC04进行冲压模拟,不同材料力学性能见表3,模拟结果如图13所示。
通过模拟可以看出,在Δr相近的情况下,随着r均值的增加,最大壁厚明显降低,凸耳明显降低,有利于提高产品壁厚均匀性。
结论
本文结合实际案例,采用Dynaform软件对电池壳冲压成形过程中第一道次进行模拟仿真,在冲压过程中凹模上圆角尺寸、模具间隙、压边力、摩擦系数等外界条件以及材料属性均会对冲压产生影响。
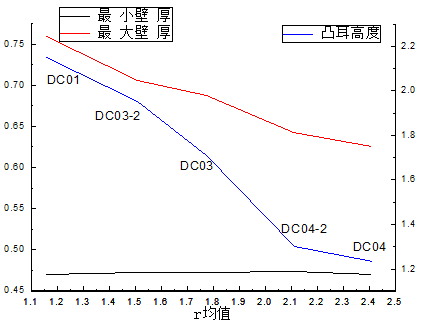
图13 r均值对零件壁厚及凸耳高度的影响
表3 不同材料力学性能
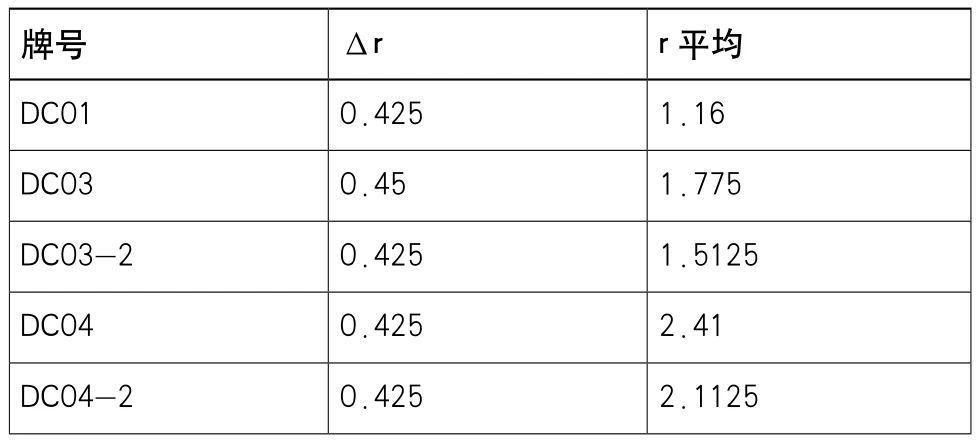
⑴当凹模上圆角半径设定为6mm,模具间隙设定为1.1t,压边力设定为4000N,摩擦系数设定为0.08时,可得到形状良好的成形件。
⑵材料的强度和加工硬化指数n值基本不影响零件壁厚的分布。
⑶材料Δr主要影响零件凸耳高度。Δr越大,凸耳值越大,但对厚度影响不大。
⑷r值主要影响零件最大壁厚,对最小壁厚影响不大。r均值增加可降低零件最大壁厚值,有利于保证产品壁厚均匀性,且会降低凸耳高度。
——来源:《锻造与冲压》 2018年第24期
举报 0
收藏 0
分享 103
-
冲压技术在电机叠片制造的应用
2024-09-06 -
车身零部件包边质量控制要点
2024-09-05 -
轻量化技术——热汽胀形工艺技术解析
2024-09-04 -
高强板车身件冲压技术
2024-09-02
最新资讯
-
比亚迪叉车的智慧演变:从动力革新到
2025-04-02 09:15
-
重磅剧透!首批参展商名单曝光——这
2025-04-01 20:48
-
施耐德电气发布新一代Harmony XVB7模
2025-04-01 18:51
-
[转载] 机床巨头埃马克:百年跌宕再
2025-03-31 12:42
-
从4S店到修理厂:FLIR ONE Pro USB-C
2025-03-28 16:05