汽车信号轮旋压增厚工艺研究及旋轮设计
2019-02-01 15:56:09· 来源:锻造与冲压 作者:周金良,黄彪
信号轮作为汽车发动机里面重要的传动部件,信号轮外齿端厚度是板料厚度的2~3倍,对于其综合性能有着很高的要求。传统工艺主要是通过冲压、拼焊或者锻造后多次机加工获得。采用传统工艺获得的信号轮存在着焊接影响区化学成分不均匀、精度
信号轮作为汽车发动机里面重要的传动部件,信号轮外齿端厚度是板料厚度的2~3倍,对于其综合性能有着很高的要求。传统工艺主要是通过冲压、拼焊或者锻造后多次机加工获得。采用传统工艺获得的信号轮存在着焊接影响区化学成分不均匀、精度较低、零件寿命短、材料利用率低等问题。而采用旋压工艺成形信号轮有诸多优点,比如产品精度高、零件性能优良、材料利用率高等。本文将设计一套信号轮旋压成形模具,通过有限元分析软件SIMUFACT对信号轮多道次旋压增厚成形的过程进行有限元模拟分析,分析成形过程中板坯变形情况、金属流动规律及旋压增厚过程中载荷分布情况,验证所设计旋轮的合理性。
多楔轮旋压成形工艺分析
信号轮的结构特征如图1所示,通过多道次旋压增厚可使原始厚度为2.5mm的板料局部增厚到6mm。板料增厚部位并非两边对称增厚,上半部板料厚度为0.75mm,下半部厚度为1.75mm,考虑后续加工余量两边各加0.5mm,总增厚厚度为6mm,增厚外径加0.5mm,最终上半部板料厚度为1.25mm,下半部厚度为2.25mm。所以在旋轮定位时,应保证板料距旋槽上平面距离和下平面距离比值为5∶9。
图2所示为增厚旋轮局部示意图,旋轮侧面有一个深度为n的旋轮槽,轮槽底端为一个半径为r的圆底,圆底的设计有利于增厚过程中金属的流动,轮槽宽度为m。
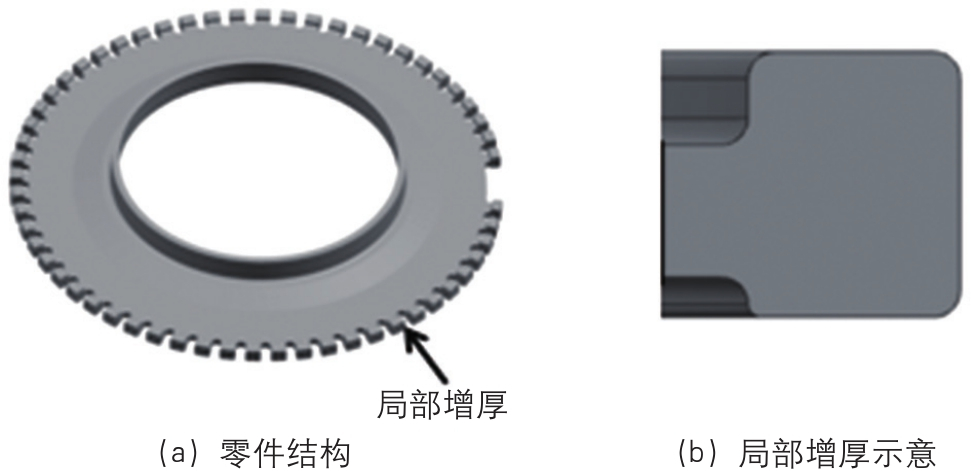
图1 信号轮结构特征示意图
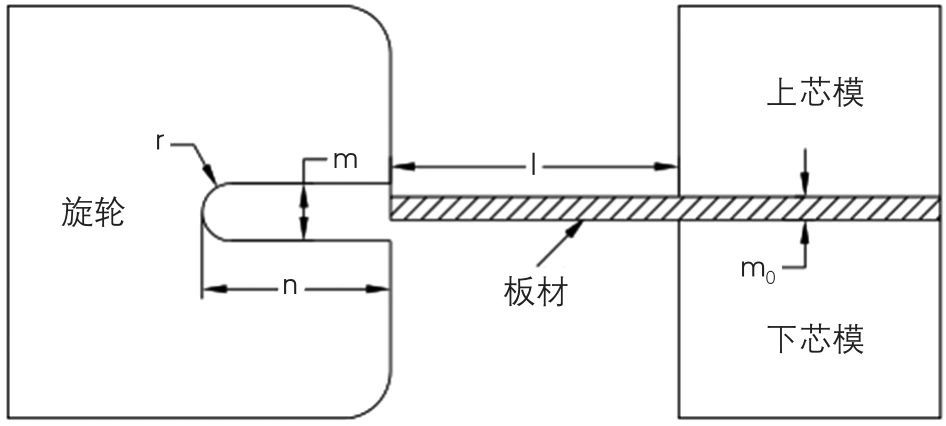
图2 增厚旋轮局部示意图
表1 旋压增厚轮具体参数

根据旋压手册以及工业生产经验,从减少生产道次以及提高材料利用率和零件成品率的角度考虑,信号轮的旋压增厚成形工艺采用三个增厚旋轮依次进给成形,每道次进给旋轮的具体参数如表1所示。
有限元模型建立
采用SIMUFACT有限元分析软件建立如图3所示的板材旋压增厚模型,板材为厚度2.5mm、直径191mm、DD13材料的圆形板材。模拟中定义板材和模具温度为20℃,旋轮与板材之间的摩擦系数为0.05,芯模与板材之间的摩擦系数为0.3,上下芯轴转速为300 r/min,旋轮的进给速度为2mm/s。
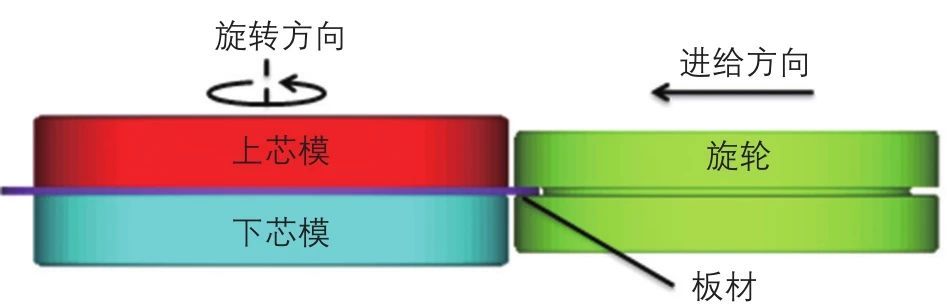
图3 信号轮旋压增厚模型
模拟过程分析
图4 所示为一道次旋压增厚成形过程,可以看出在旋轮与板材接触处的应力最大,应力沿着径向逐渐递减,随着旋轮的进给,板材中的高应力区范围也越来越大。根据成形过程中板材在旋轮进给作用下的变形情况,可以将一道次旋压增厚工艺分为三个阶段:第一阶段是成形初期,板材与旋轮刚接触时发生变形,如图4(a)所示,这时板材的外缘发生塑性变形,板材外缘增厚程度明显,同时板材发生微小的弹性变形;第二阶段是成形中期,此时板材外缘已经完全增厚,随着旋轮的进给,板材主要发生轴向变形,金属逐渐充满整个轮槽,如图4(b)所示。等效应力值随着旋轮的进给呈现增大的趋势,等效应变随着变形程度的增大逐渐累积;第三阶段是成形末期,增厚旋轮达到预定位置,板坯完整成形,如图4(c)所示,且没有产生飞边、卷边等缺陷,整体成形效果良好。
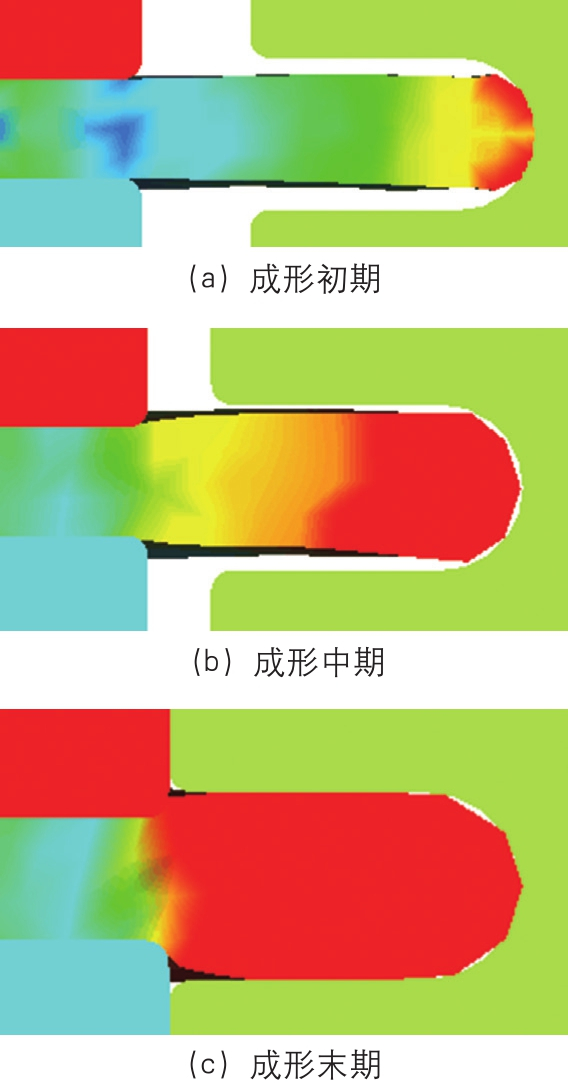
图4 一道次旋压增厚成形过程
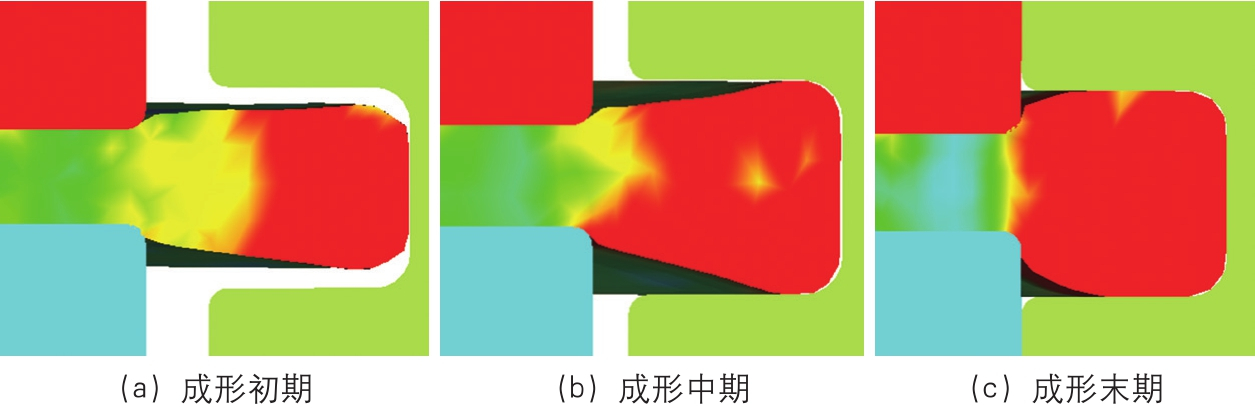
图5 二道次旋压增厚成形过程

图6 三道次旋压增厚成形过程
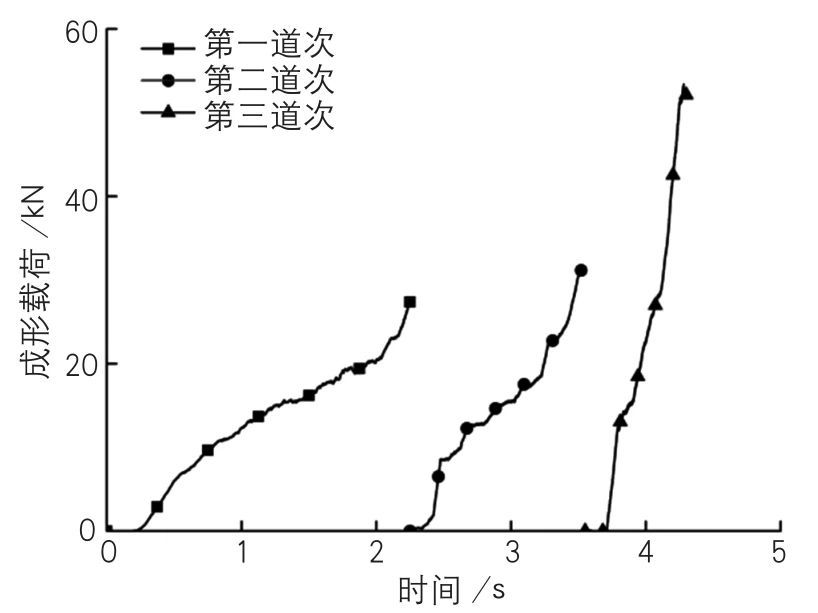
图7 各道次旋压成形过程径向载荷变化
图5所示为二道次旋压增厚成形过程。一道次成形后,旋压增厚轮轮槽相比一道次旋压增厚轮宽度增大但深度减小,旋轮径向进给使板坯金属进一步变形增厚。金属的流动情况与一道次大致相同,板材外缘与旋轮接触先发生增厚,随着旋轮进给,金属主要向轴向流动,发生轴向增厚,并且金属的变形抗力和等效应力值随之变大。从图5(c)可以看出在成形末期时板材的成形效果良好,轮槽内部几乎完全被填充,没有产生飞边、卷边等缺陷。
图6所示为三道次旋压增厚成形过程。整个变形过程与前两个道次类似,图6(c)中板材的成形效果良好,金属填充满旋轮槽,并且没有明显缺陷产生。
通过比较三道次旋压增厚过程中的载荷变化(图7),可以看出前两道次的模具载荷大小几乎一样且明显小于第三道次。0~2.25s为第一道次载荷变化,载荷整体变化趋势均匀平缓,这是因为第一道次成形过程中金属变形程度较小,因此变形抗力较小,所以载荷均匀增大;2.25~3.6s为第二道次载荷变化,当板材外缘完全增厚时,旋轮继续进给且载荷急剧增大,这是因为变形量累积导致金属的变形抗力增大;3.6~4.2s为第三道次载荷变化趋势,由于前两道次的应变累积,此时变形抗力更大,所以在旋轮进给过程中,载荷急剧增加,最大载荷达到50.1kN。
试验验证
信号轮旋压增厚试验是在CDC-4S80多工位旋压机上进行的,所用圆形板坯尺寸为191mm×2.5 mm、旋轮进给速度为1mm/s、摩擦系数0.05、主轴转速300 r/min,旋轮尺寸与表1完全一致。成形后的试验样品成形效果良好,外缘端从2.5mm增厚到了6mm,再经过表面精车外缘端,厚度变成了5mm,达到了模拟预期效果,试验与有限元模拟结果基本一致。
——本文节选自《锻造与冲压》2018年第22期。
举报 0
收藏 0
分享 96
-
冲压技术在电机叠片制造的应用
2024-09-06 -
车身零部件包边质量控制要点
2024-09-05 -
轻量化技术——热汽胀形工艺技术解析
2024-09-04 -
高强板车身件冲压技术
2024-09-02
最新资讯
-
[转载] 机床巨头埃马克:百年跌宕再
2025-03-31 12:42
-
从4S店到修理厂:FLIR ONE Pro USB-C
2025-03-28 16:05
-
比亚迪发布2024年ESG报告 以技术创新
2025-03-26 16:44
-
电装中国:以“技术+生态”双引擎驱
2025-03-24 19:07
-
杜尔中国海外项目-Stellantis 集团摩
2025-03-20 11:59