机器人滚边质量缺陷的仿真分析与改善措施
2019-03-11 22:47:12· 来源:文/王强 锻造与冲压
根据某车型后背门总成零件在滚边过程中出现的外观质量缺陷,应用CAE仿真分析的方法对机器人滚边工艺过程进行模拟分析,提出了质量改进方案并验证有效,对后续车型机器人滚边质量的改进过程提供了指导方法。机器人滚边工艺主要指汽车门、
根据某车型后背门总成零件在滚边过程中出现的外观质量缺陷,应用CAE仿真分析的方法对机器人滚边工艺过程进行模拟分析,提出了质量改进方案并验证有效,对后续车型机器人滚边质量的改进过程提供了指导方法。
机器人滚边工艺主要指汽车门、盖等开闭件的内外板合装采用的一种连接工艺,即应用工业机器人持滚边工具端将外板零件分序向内折弯包裹内板零件,以获得一定的连接强度并保证总成制件的尺寸及外观质量,如图1所示。本文主要结合一汽轿车某车型后背门总成制件在滚边过程中产生的表面波浪缺陷,简述了机器人滚边的工艺过程,并利用有限元分析软件对在不同滚边角度下制件压合边弯曲变形情况进行分析,最终获得最优的滚边压合角度,改进产品外观质量。

图1 机器人滚边工位
缺陷描述
机器人滚边过程中会产生各种类型缺陷,对此应分析缺陷的具体类型,并针对不同类型缺陷找出解决问题的办法。本文所述某车型后背门压合总成,滚边压合后上边缘边存在严重的波浪缺陷,白车身AUDIT评审为B类缺陷,整车油漆后缺陷同样可见,严重影响整车外观质量,如图2所示。
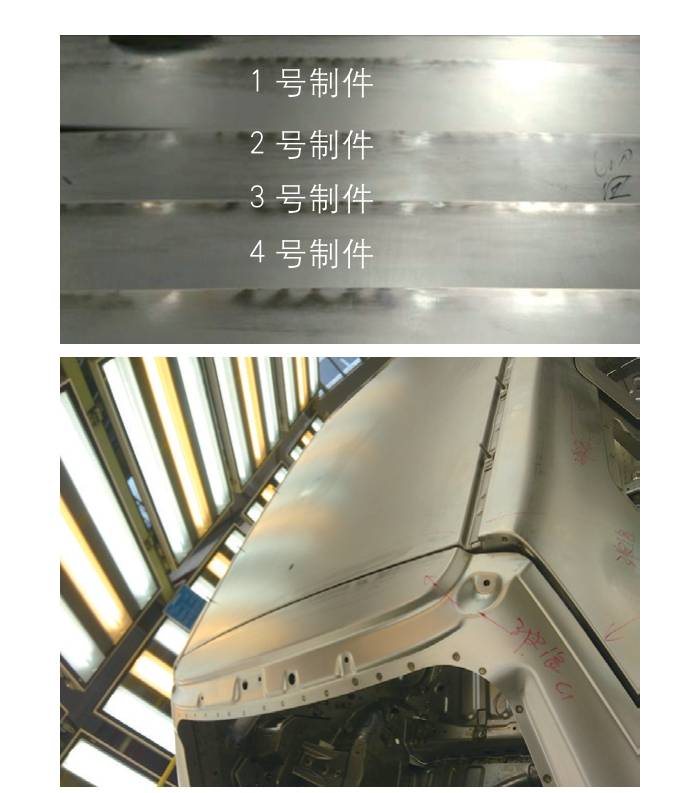
图2 后背门总成上边缘波浪缺陷及白车身评审结果
其评价方法为:⑴白车身评审者使用油石在制件表面沿固定方向反复轻摩擦,观察表面即可看出缺陷;⑵观察者在灯光隧道区,观察车门在灯带下的反光情况即可看出缺陷。
滚边工艺过程
根据后背门外板冲压工艺规划,外板上边缘翻边角度为120°,压合采用三序滚边成形工艺,后背门上边缘具体滚边序数及滚边角度如表1所示,分别完成120°~65°第一序滚边、65°~30°第二序滚边、30°~0°第三序滚边,通过三序滚边,最终完成边部压实。其中,第一序滚边和第二序滚边为预翻边,第三序滚边为终翻边。
在实际滚边过程中发现,预翻边工序中外板翻边波浪已经产生,第一序及第二序滚边后压合边波浪较大,如图3所示。分析原因可能是预翻边的角度过大(第一序滚边角度大于50°),翻边区域进行大角度滚边时,较大变形量产生的内应力无法释放,造成波浪起皱。此时,应考虑减小滚边角度,合理分配每一序滚边的变形量,减小滚边波浪的产生。
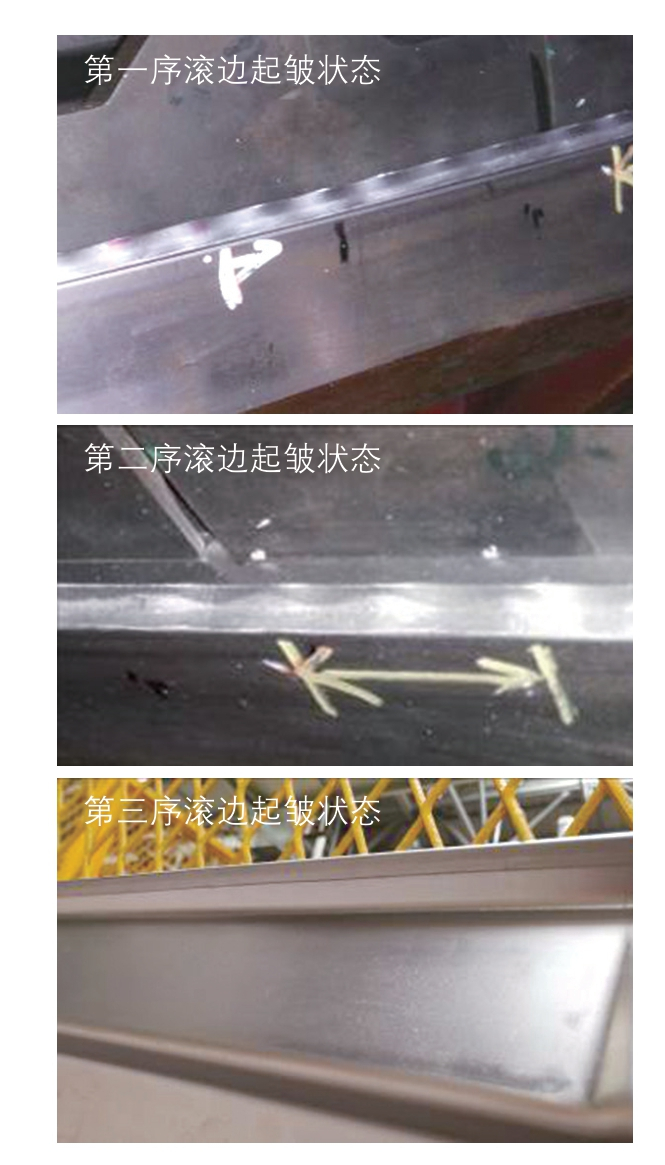
图3 外板各工序翻边波浪缺陷
滚边仿真模型建立及角度优化
滚边CAE仿真模型建立
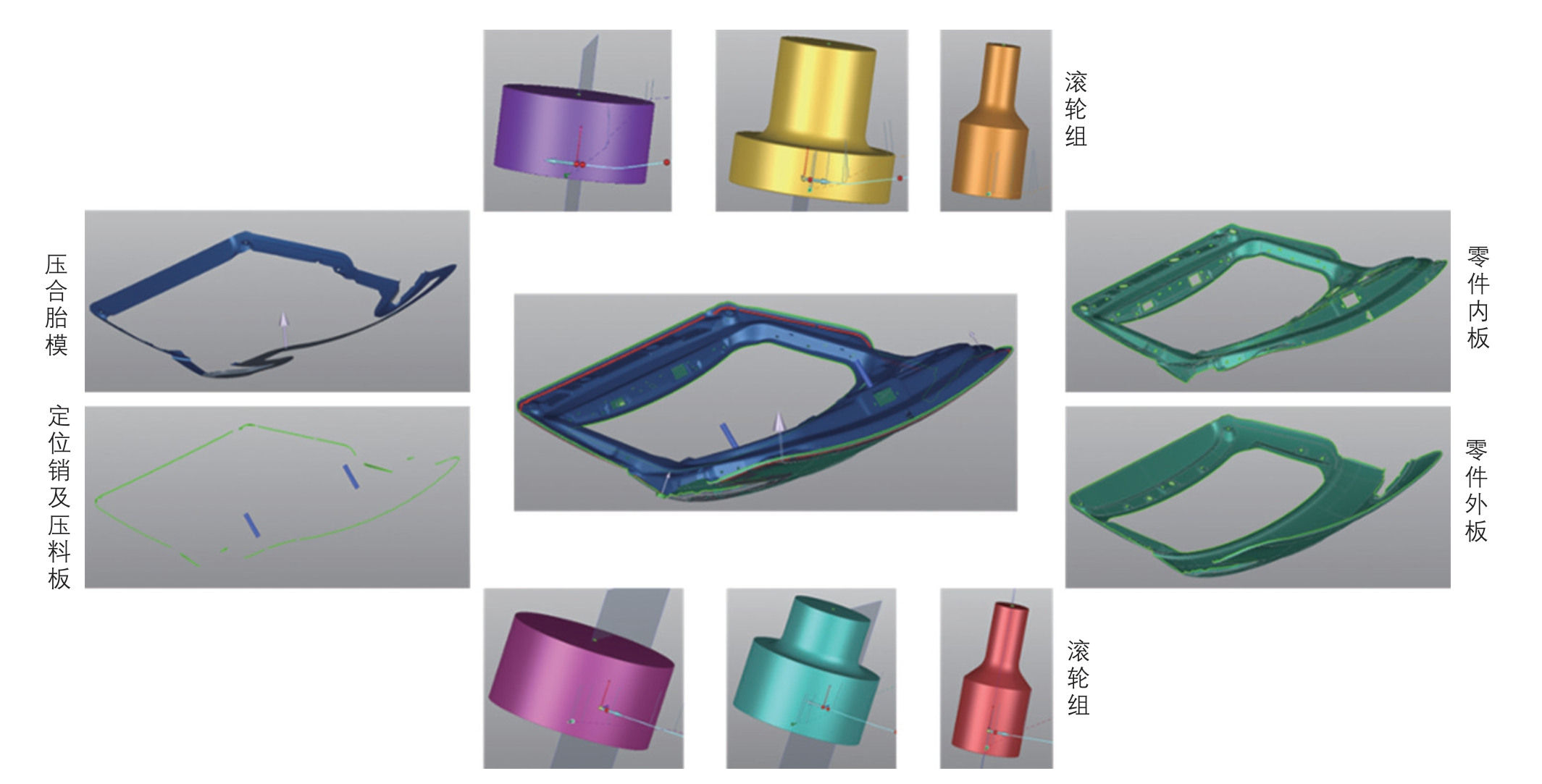
图4 滚边压合仿真理论模型建立
Auto Form软件广泛应用于金属板材成形的工艺仿真优化,Auto Form R6版本新加入了Hem Planner模块,为滚边成形仿真提供了一个很方便的工具。根据实际生产情况,使用Auto Form模拟软件建立压合仿真模型,如图4所示。将后背门外板冲压成形后产品数据导入软件,材料设置为H180,材料厚度t=0.7mm,胎模型面在软件中根据产品型面生成,胎模型面支撑宽度100mm,后背门内板冲压成形后产品数据导入软件,材料设置为St16,材料厚度t=0.65mm,压料板压料型面从模具结构图中提取型面导入,总压料力大小设置为2500N。内板定位销根据定位孔位置及直径在软件中生成,滚轮组根据实际滚轮尺寸在软件中直接生成,采用三序滚边成形工艺。本模型仅考虑滚边压合中翻边成形的应力应变,不考虑冲压成形后残余应力、应变及零件回弹等。
滚边CAE模拟分析及角度优化
滚边压合仿真理论模型建立完成后,利用Auto Form软件进行滚边压合模拟分析,将三序压合角度设置为表1所示的实际生产滚边角度,分析结果如图5所示。结果显示第一序及第二序滚边后翻边波浪较大,与实际滚边后翻边状态基本一致。第三序滚边后压合边内沿起皱较大,存在较大的残余应力,最终将导致零件外表面形成波浪,影响后背门总成及整车外观质量。
表1 后背门上边缘各工序滚边角度

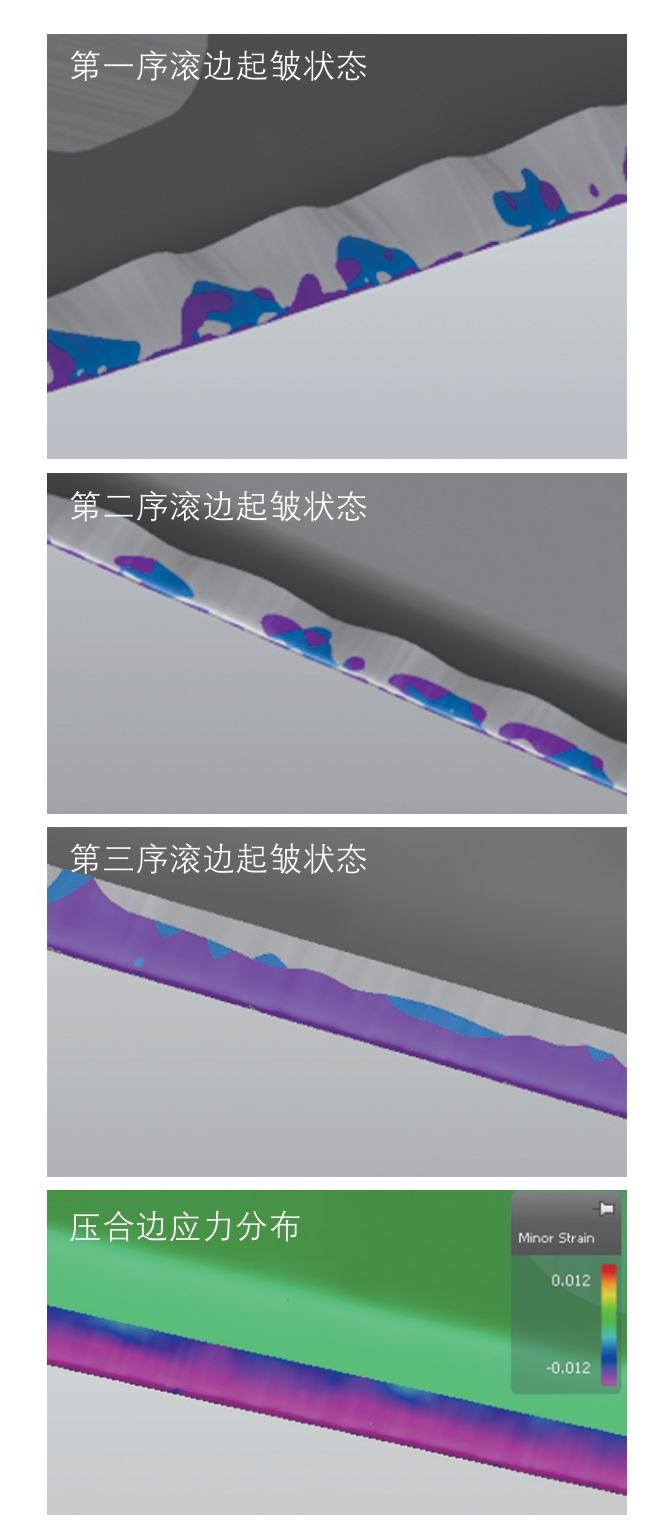
图5 原始滚边角度仿真分析结果
根据原始滚边角度滚边仿真分析结果,对后背门上边缘滚边角度进行优化,重新分配三序滚边角度,具体角度分配如表2所示。利用Auto Form软件建立滚边压合仿真模型,分别对10组滚边角度分配进行模拟分析。
表2 后背门上边缘滚边角度优化
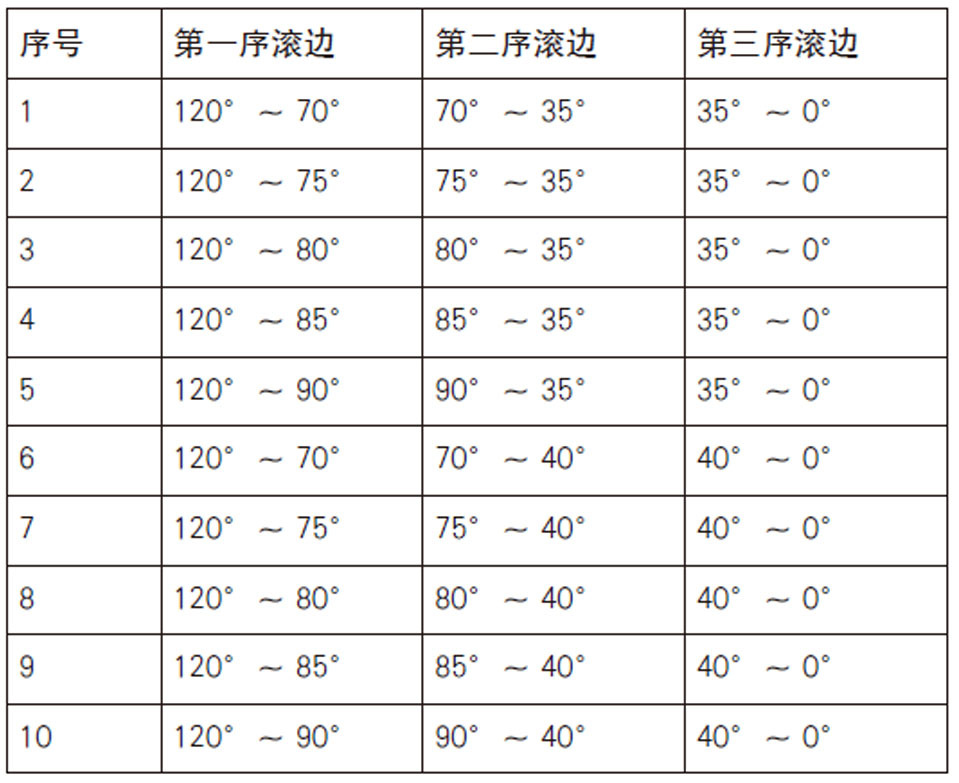
模拟分析结果表明,当后背门上边缘滚边角度选取三序滚边角度分别为120°~85°、85°~40°、40°~0°组合时,每一序滚边压合后的翻边波浪较小,翻边质量明显优于其他角度滚边状态,最终滚边后压合边起皱及残余应力都较原滚边压合角度明显减轻,如图6所示。
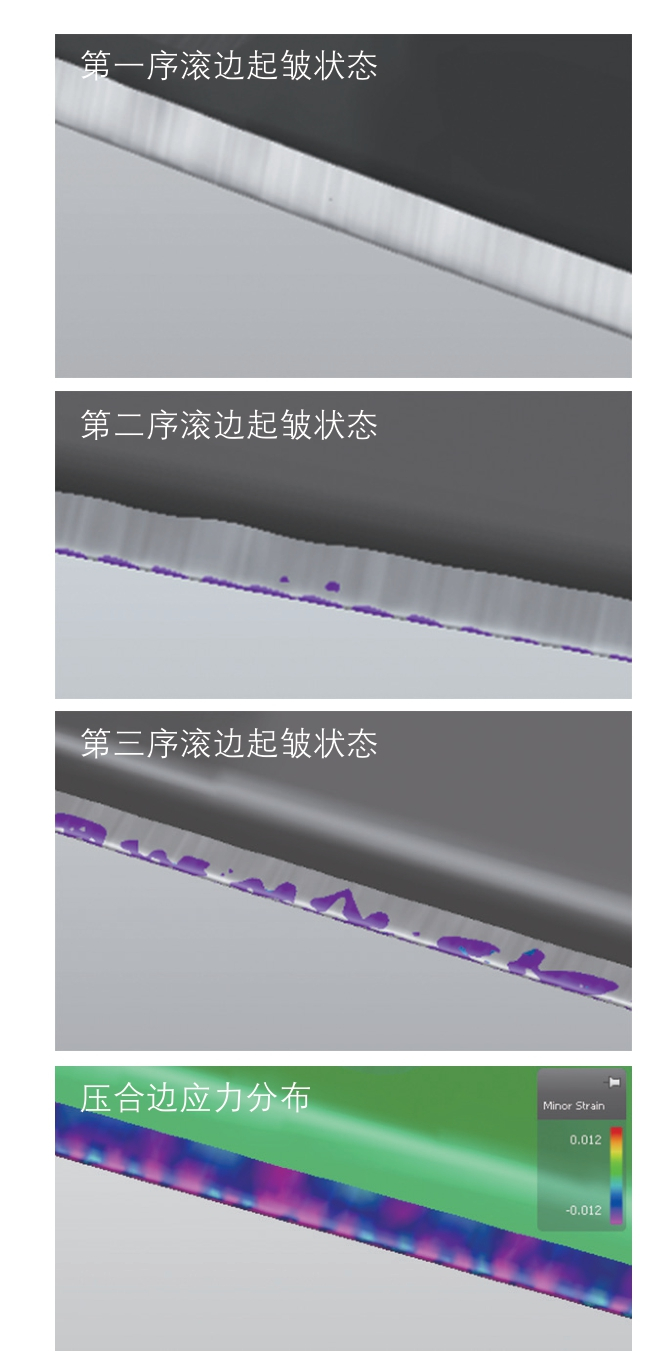
图6 优化滚边角度后滚边仿真分析结果
滚边角度优化结果验证
根据优化滚边角度模拟分析结果,通过调整机器人工具端角度,采用最优的120°~85°、85°~40°、40°~0°滚边压合角度进行滚边压合,生产结果表明:第一序、第二序滚边后翻边表面波浪明显减轻,终压合后制件总成表面波浪缺陷也得到大幅度优化,实际生产结果如图7、图8所示。
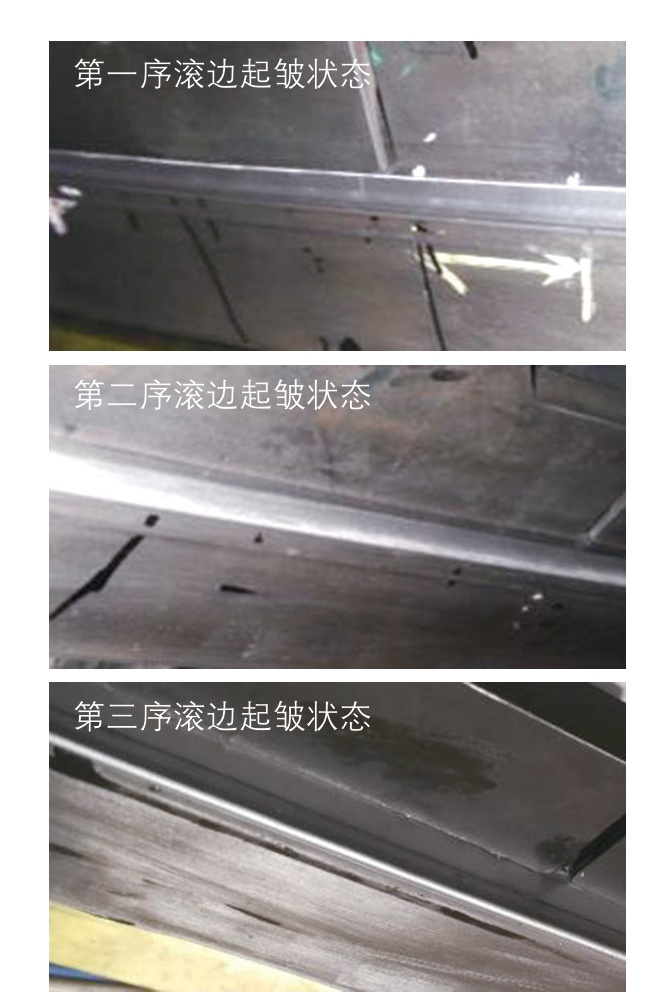
图7 优化滚边角度后实际生产调试结果
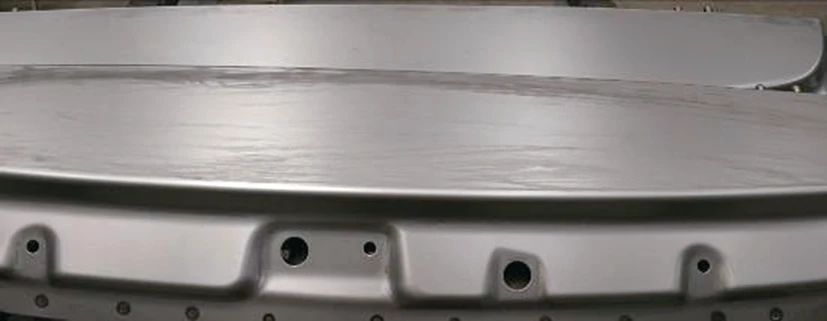
图8 优化滚边角度后压合总成状态
最终后背门上边缘表面波浪缺陷优化至白车身AUDIT评审C类项,漆后整车表面质量不扣分,满足整车评审质量要求,整改效果明显。
结束语
本文采用CAE仿真分析与现场实际生产相结合的方法,通过对机器人滚边压合典型质量缺陷的案例研究表明,滚边压合角度对制件表面质量的影响很大,合理分配每一序滚边的角度,可以明显优化表面波浪缺陷,提升制件及整车外观质量,为今后生产中此一类问题的解决提供了参考方法。
——摘自《锻造与冲压》2019年第4期
- 下一篇:混合动力乘用车发动机的发展历程与研究现状II
- 上一篇:碳纤维材料助力电动车轻量化
举报 0
收藏 0
分享 110
-
2024海康机器人行业解决方案系列发布会
2024-10-14 -
2024年机器人行业5大发展趋势
2024-07-29 -
AMTS | 以智驭新,协作创造汽车行业新质生产力
2025-02-17 -
汽车制造新范式,AMR赋能汽车工业智造新蓝图
2024-06-20
编辑推荐
最新资讯
-
全球产业链聚沪 共探双碳新路径 SNEC
2025-04-18 18:05
-
柯马签订具有约束力的协议收购 Autom
2025-04-17 13:01
-
高效协同新范式:比亚迪叉车领创智能
2025-04-17 10:04
-
埃马克德国总部迎来中国社科院工业经
2025-04-15 09:40
-
埃马克这项全新应用即将在CIMT惊艳首
2025-04-15 09:37