红旗全新智能工厂,这些技术都是国内首创!
2019-03-29 00:30:18· 来源:汽车工艺师
国内领先的智能工厂多项技术国内首创早在去年1月份,新红旗全新设计语言发布,使其成为各大车展最吸睛和最具话题性的品牌之一。高山飞瀑式的格栅、气贯山河红光闪烁的旗标、振翅飞翔的前大灯、昂首挺胸的腰身、定海神针式的轮标。新红旗
国内领先的“智能工厂”多项技术国内首创
早在去年1月份,新红旗全新设计语言发布,使其成为各大车展最吸睛和最具话题性的品牌之一。
高山飞瀑式的格栅、气贯山河红光闪烁的旗标、振翅飞翔的前大灯、昂首挺胸的腰身、定海神针式的轮标。
新红旗概念模型将这些元素融合在了一起,由此确立了未来几年红旗汽车的造车理念方向:
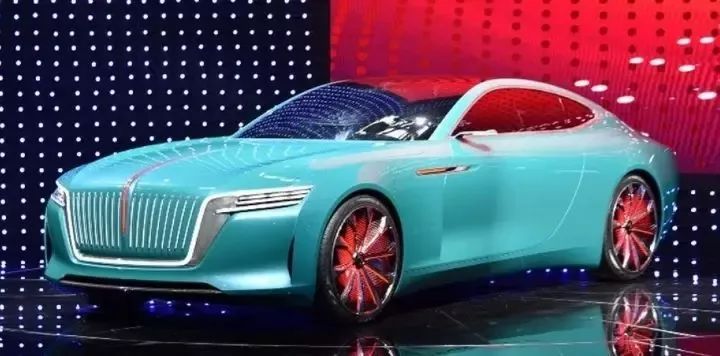
你看这侧面▲
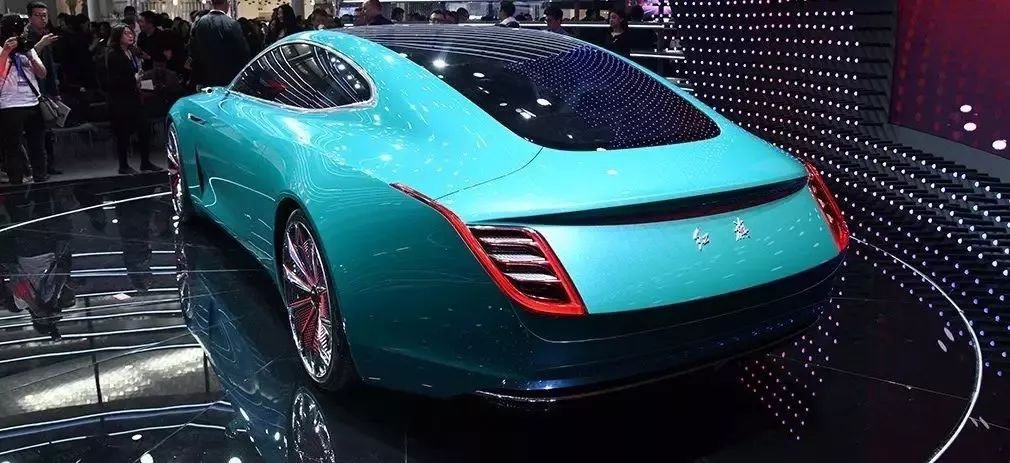
再瞧这腰线▲
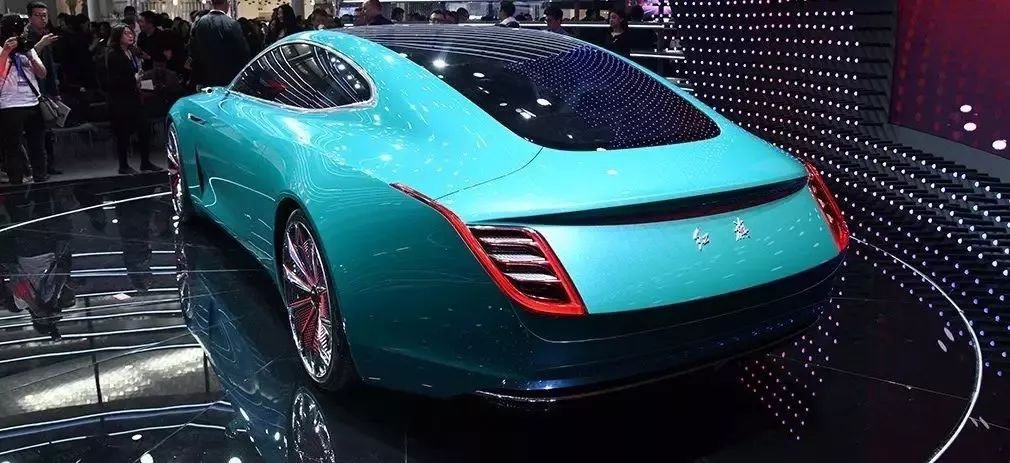
再瞅这屁股▲
新红旗历时7个月打造的全新智能工厂于18年12月落成,立志将概念变为现实。
红旗工厂新H平台总装车间,总建筑面积1.9万平米,设计极限产能10万辆/年,并预留未来发展空间,主要生产红旗H7高级轿车、HS7高端SUV车型。
车间采用L型生产线布局,实现了工位作业空间的最大化,是“柔性化”、“智能化”、“共享化”、“信息化”于一体的现代化车间。
其中,智能工位占全部工位80%以上,更有几项为国内首创。下面,带您走进这座国内领先的“智能工厂”!
工厂细节层层解读
1.实时数据中控系统
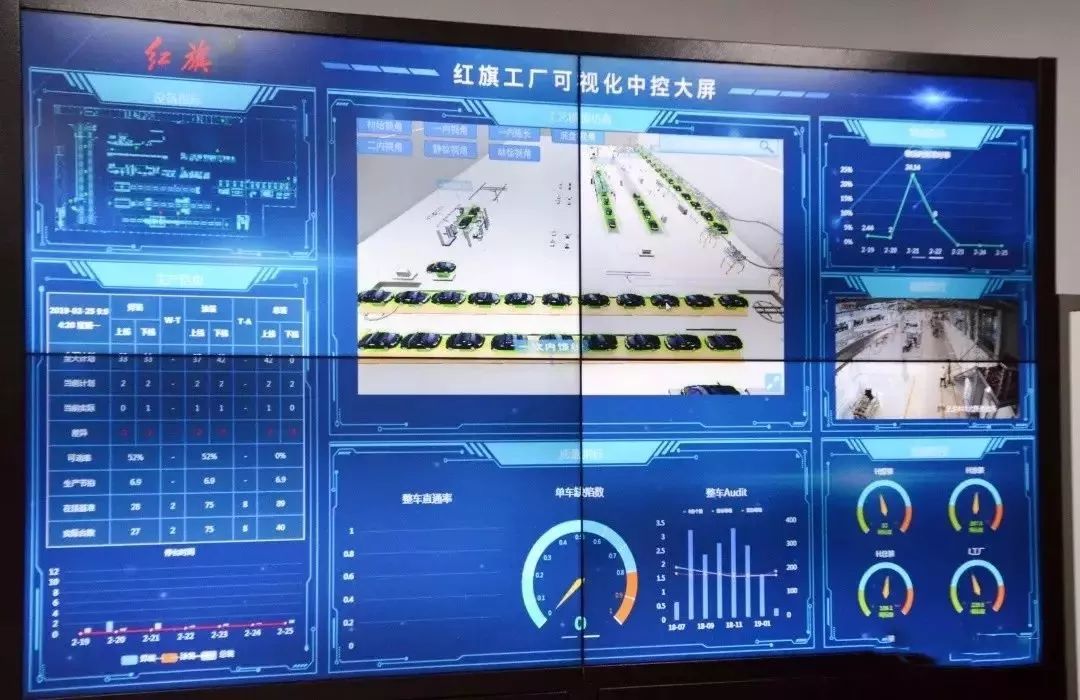
新H平台总装车间设有MES(Manufacturing Execution System)系统,通过可视化中控大屏与手机APP相结合,可实时采集、监控制造过程中车序车型、工艺参数、产品质量、能源消耗情况等信息,并将信息数据存储、分析,实现整个生产环节的全信息化闭环管理。
MES系统下设多个子系统,相互间信息互联互通,配合大数据管理,实现问题可追溯,缺陷“0流出”。
系统还预留了未来与销售订单系统、工艺设计系统等扩展接口,可实现满足客户任意选配需求的定制化生产要求,大幅缩短交付周期,提升用户体验。
2.自适应生产线
新H平台总装车间的自适应生产线,由车身输送AGV、转挂装置、控制系统组成。

自适应生产线▲
AGV(自动导引搬运车)作为输送线搬送车身,可根据车型调整工位间距,根据产量需求扩展生产线调整布局,成功解决了现场空间干涉问题。未来扩展产能,只要增加AGV数量,改变地面行走路线即可,改造不受特构基础、停产周期影响,大幅降低投资与改造周期,属国内首创。
同时,利用可升降吊具、可升降滑板,在一定范围内根据工艺操作需要,可任意调整车身高度,降低员工操作难度,节省工时。
新H总装车间可兼容生产从A到C级,从轿车到SUV、从传统车到新能源汽车的多品种混线生产,为产能扩展打下坚实基础。
3.自动化机器人搬送车身
搬送车身的自动化机器人由六轴载重机器人、视觉定位系统和转运叉臂构成。
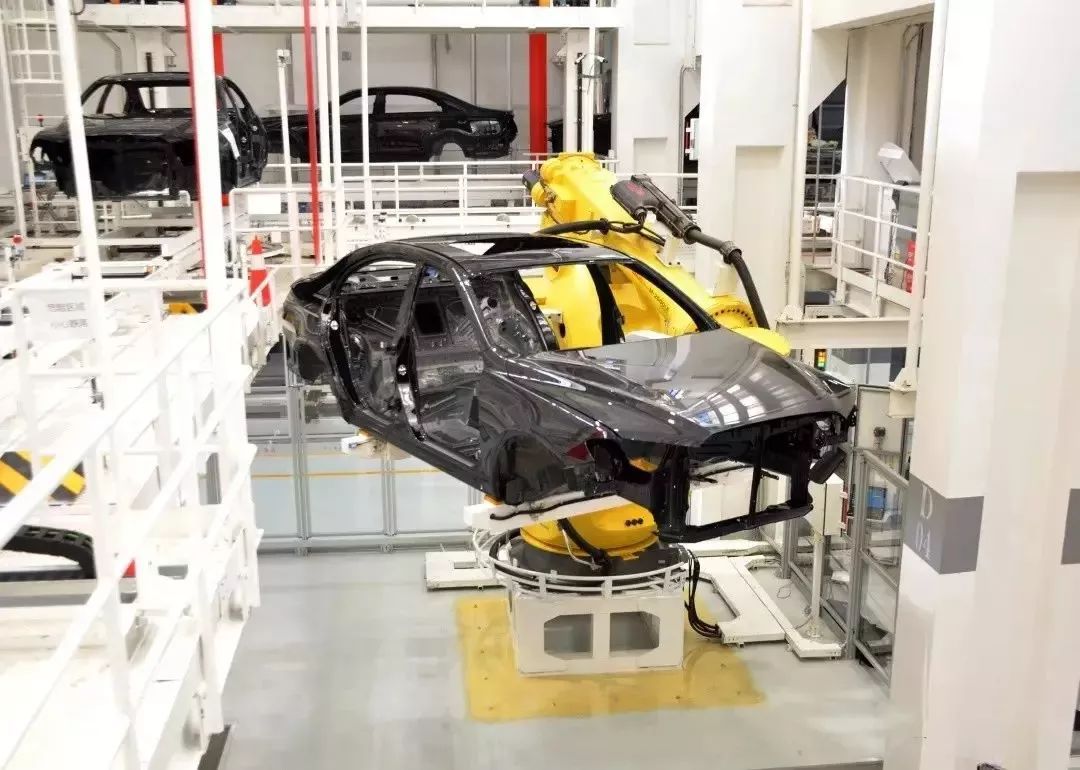
自动化机器人搬送车身▲
该六轴重载机器人,臂展4.2米、负载1.7吨,是国内最大型工业机器人。由于机身涂装是明黄色,因此被工人们亲切的叫做“大黄鸭”。
“大黄鸭”的出现,成功解决了厂房立柱干涉、空间狭小等问题。“大黄鸭”具有精度高、免维护、高适应性、可重复利用等诸多优点,也是传统的升降机转接形式所无法比拟的。
4.全覆盖电动拧紧
新H平台总装车间内共有近100把电动拧紧机,应用密度远高于行业标准,且全部为全球顶级的瑞典阿特拉斯品牌。
通过使用电动拧紧机,充分保证了整车全部重点力矩的拧紧精度,可达5%以内。
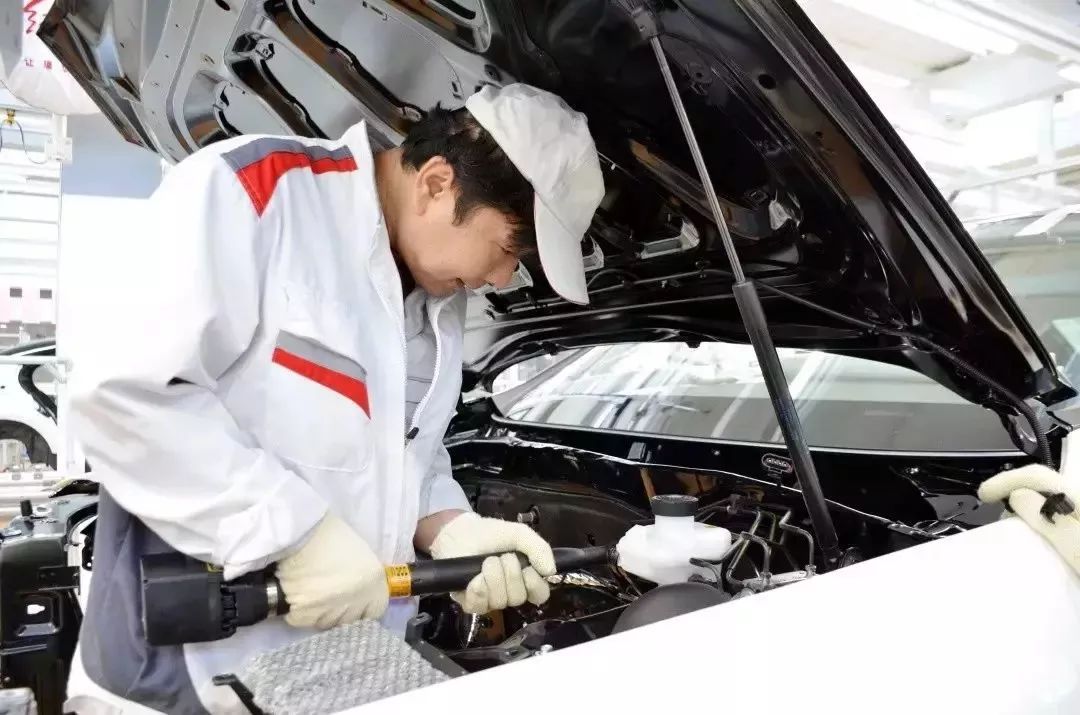
全覆盖电动拧紧▲
每台电动拧紧机都配有MasterPC系统,可实时显示拧紧工艺要求与结果,并将数据结果上传至拧紧联网系统。数据可存储15年,用于后续信息追溯。
5.全自动风挡涂胶装配
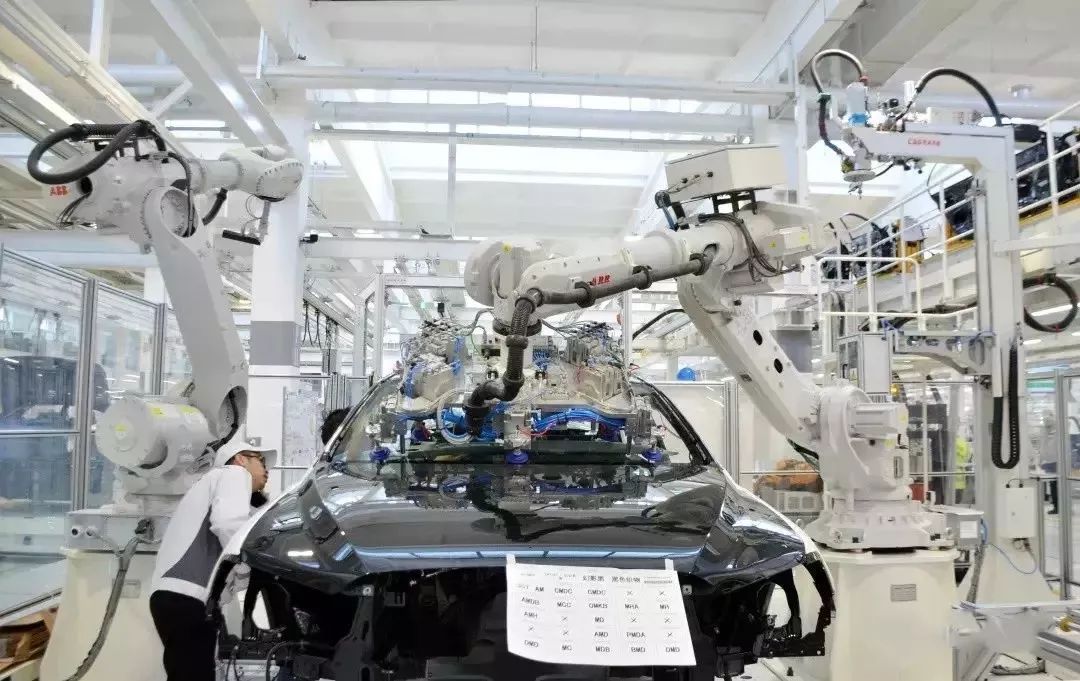
该系统由伺服定量供胶系统、视觉引导及装配机器人、自动玻璃输送台组成。
通过使用该系统,可实现自动供胶、涂胶、定位和装配。自带的扫描系统,便于及时发现并解决短胶等不良现象。
机器人自动装配,具有质量稳定、可靠性高等特点。视觉引导系统,提高了装配速度和装配精度。
6.底盘模块化自动合装
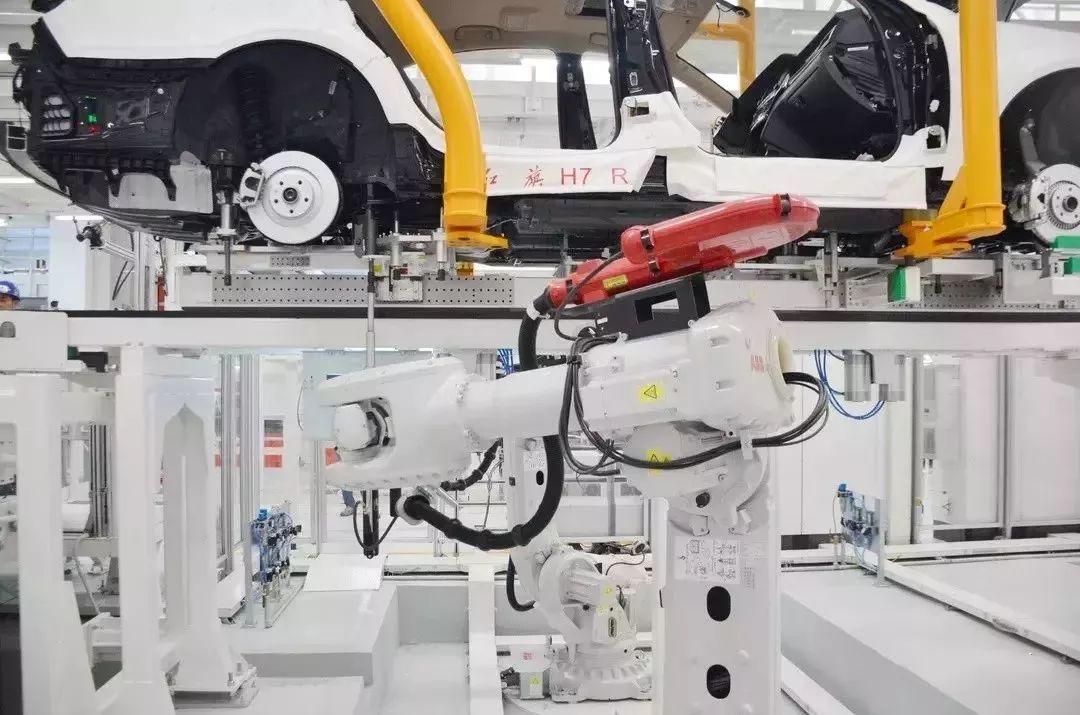
该系统由输送系统、定位托盘、机器人拧紧系统、视觉定位系统、电气控制系统组成。
底盘模块与车身采用整体自动合装工艺,最大程度保证了车身、底盘的装配质量。地面全部拧紧点,均采用机器人自动追踪拧紧。两个机器人工作站,不但可以满足当前车型的工艺需求,对于后续电动车等不同平台的拧紧工艺也能充分适应。视觉拍照定位引导系统的使用,进一步保证了拧紧质量。
整个定位托盘采用双层结构,通过支点切换,在国内首次实现一个托盘兼容两种不同平台底盘,大幅降低设备投资与占地面积。
7.国内首创高精度轮胎装配
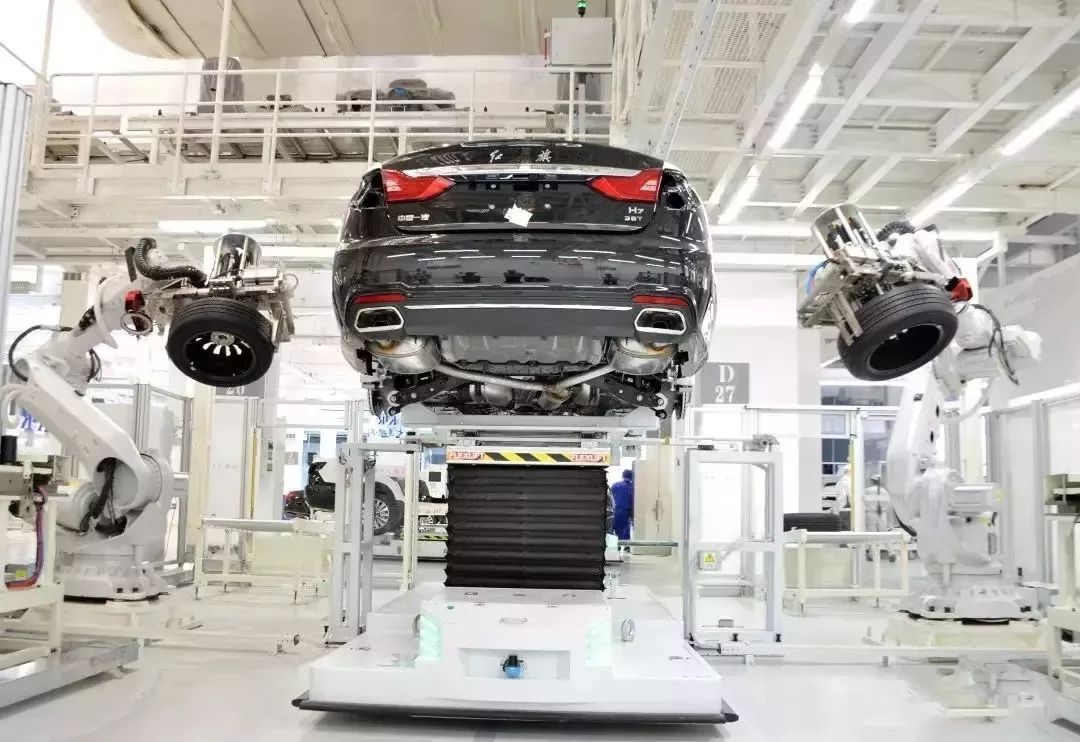
新H平台总装车间的车轮装配,采用全自动设备,由五轴电动拧紧机、物料输送系统、视觉定位系统组成。
通过自动送钉机构,可实现两种螺栓的自动输送、上料;通过安装在夹具上的气动机构,可实现两种车型不同直径分度圆的切换,属国内首创;通过视觉拍照定位装置,能够精确识别拧紧点位置状态,引导机器人对准、拧紧,精度达0.05mm;拧紧结果即时上传拧紧系统,实现信息可控、问题可溯。
轮胎装配采用供货厂家收取生产计划、同步配送的顺引方式,使轮胎从进厂到输送、抓取、定位、拧紧,实现全自动化,节约了时间、空间成本。
8.高精度车身表面间隙测量
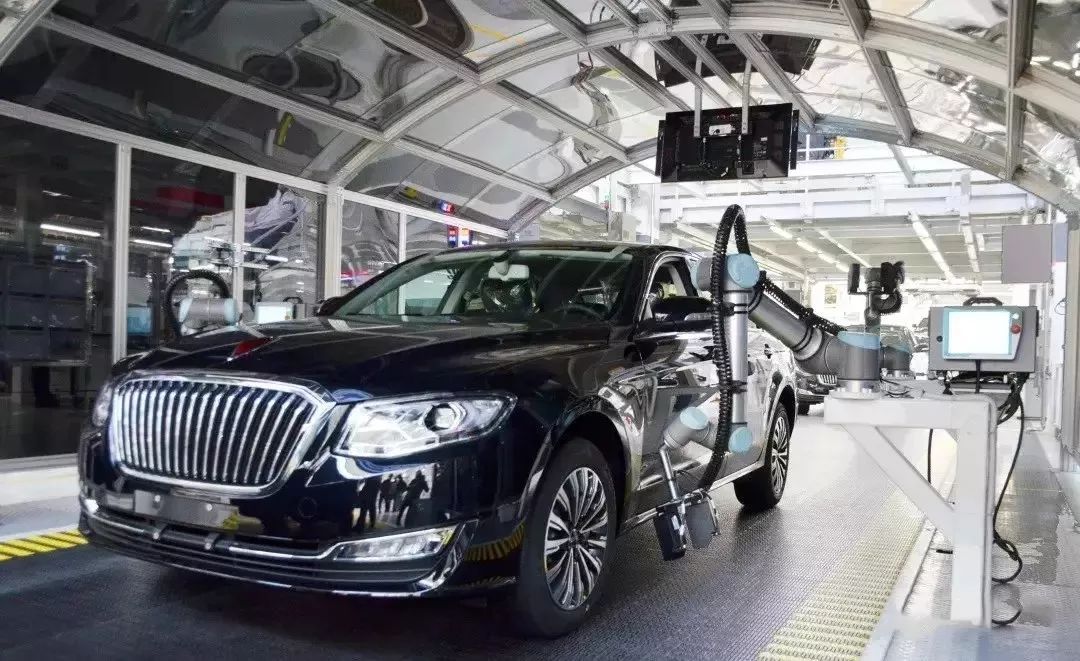
该系统由UR协作机器人、光学测量系统、车身定位系统组成。
通过UR协作机器人与ISRA(德国伊斯拉)光学检测系统的配合,可实现整车主要外观表面间隙、段差自动测量,并将测量结果存储、分析、上传。该组合系统,为国内首创。
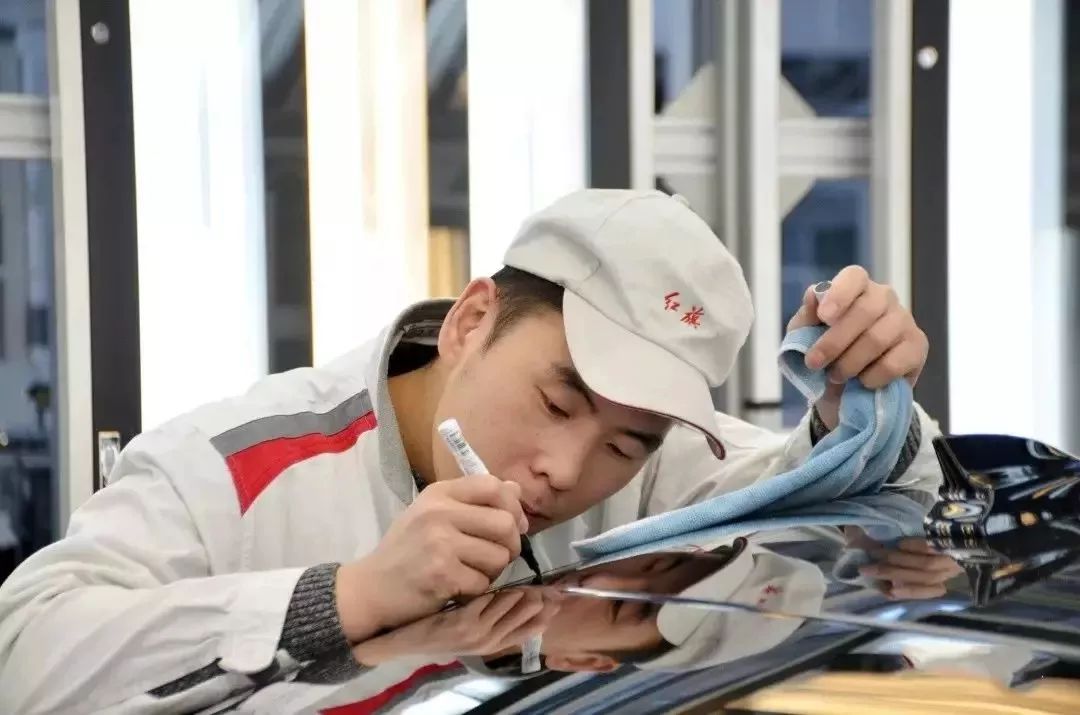
“国内首创”高精度车身表面间隙测量▲
UR协作机器人相比传统工业机器人,能够与检查员协同工作,自带力学传感器、无需安全围栏;ISRA的光学检测系统应用的是LED光源,相比传统的激光光源,精度更高、稳定性更好,且对人眼无伤害。
未来,该系统将与新涂装、焊装等检查设备数据联通,实现车身质量的自动化闭环管理。
9.国内首创全线AGV自动物流
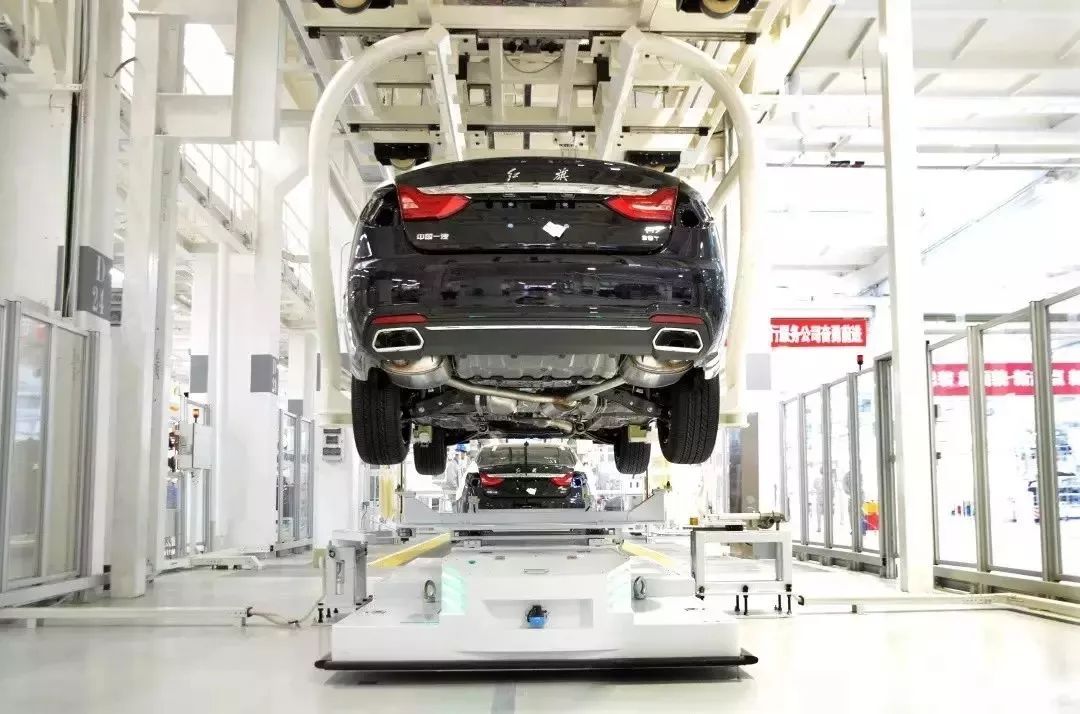
该系统由物料输送AGV、自动转接机构、LES系统、RFID信息识别系统组成。
通过厂内近160台AGV,可完成全部33条运输路线的上线运输;应用LES系统,读取物料配送提前期,指导物流配送节奏;AGV根据系统指示,将零件准时输送到线侧。同时引入的RFID自动识别技术,可自动识别物料配送位置,真正做到智能物流,是国内首个实现全无人配送的总装车间。
10.一体化电气检测系统
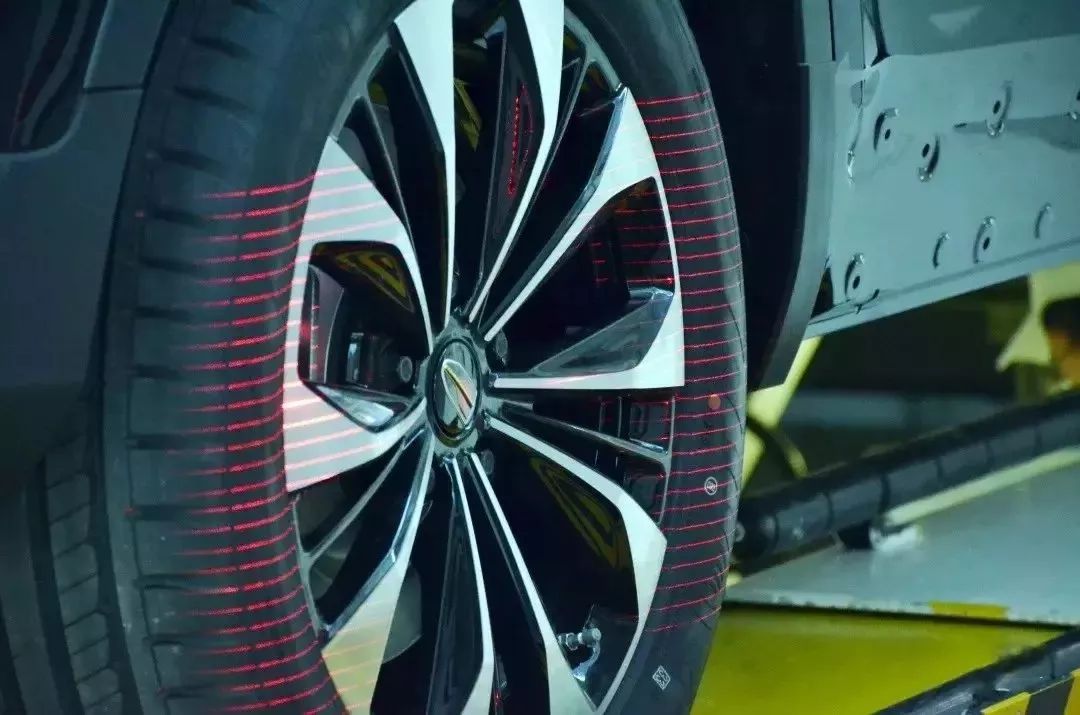
新H平台总装车间的整车电气程序激活写入、功能检测,使用了先进的电检平台系统,可将全部电气功能检测结果,实时共享、存储,用于后续质量追溯与问题分析解决。
电检系统还具有很高的柔性,程序软件的升级、新增车型的检测等工作,只需要修改车型参数等信息即可,无需资金投入和场地改造,大幅缩减了后续的改造周期与成本。
举报 0
收藏 0
分享 122
-
柯马签订具有约束力的协议收购 Automha
2025-04-17 -
高效协同新范式:比亚迪叉车领创智能搬运革新
2025-04-17 -
高歌猛进,奔赴“双碳”——比亚迪叉车助力轮胎
2025-04-10 -
果栗智造磁悬浮技术赋能汽车制造:破解行业痛点
2025-04-03
编辑推荐
最新资讯
-
全球产业链聚沪 共探双碳新路径 SNEC
2025-04-18 18:05
-
柯马签订具有约束力的协议收购 Autom
2025-04-17 13:01
-
高效协同新范式:比亚迪叉车领创智能
2025-04-17 10:04
-
埃马克德国总部迎来中国社科院工业经
2025-04-15 09:40
-
埃马克这项全新应用即将在CIMT惊艳首
2025-04-15 09:37