电动汽车技术日 | 舒勒为电机与电池壳体的制造提供多种解决方案
2019-05-06 19:56:02· 来源:舒勒
舒勒在德国格平根总部展示了最新研发的高速冲Smartline EV 3.8对更高能源效率的需求以及对新能源汽车的不断探索是该行业的主要创新驱动力。舒勒为电动汽车电机与电池壳体的制造提供多种解决方案。近期,舒勒系统业务部在德国格平根总部展
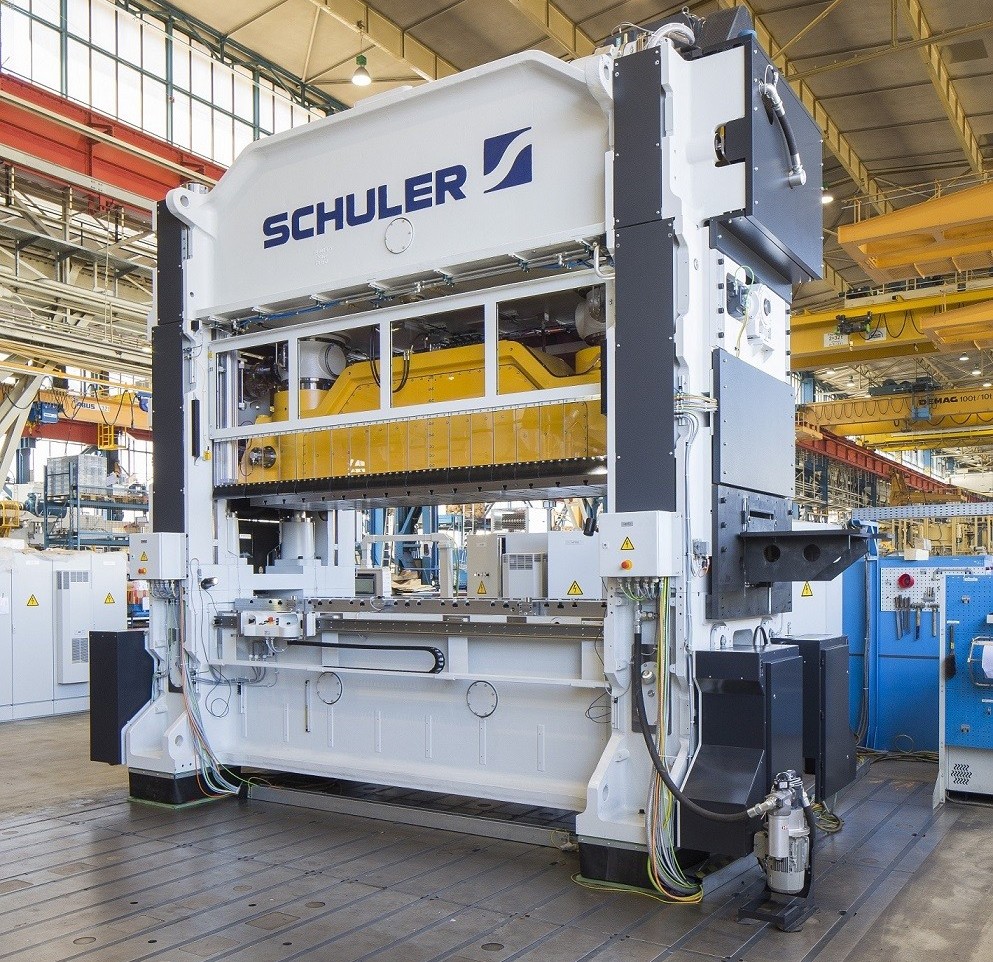
舒勒在德国格平根总部展示了最新研发的高速冲 Smartline EV 3.8
对更高能源效率的需求以及对新能源汽车的不断探索是该行业的主要创新驱动力。舒勒为电动汽车电机与电池壳体的制造提供多种解决方案。近期,舒勒系统业务部在德国格平根总部展示了最新研发的用于自扣电动机铁芯生产的高速冲Smartlin EV3.8,同时舒勒在中国大连的工厂也生产该设备,并提供与电动汽车相关的其他解决方案。
冲片几何形状越来越复杂
在此次舒勒技术日活动上,舒勒的 Simon Schmidt 先生表示,电动汽车现在发展迅猛,汽车制造商纷纷加码电动汽车产业。为了获得更高的电动机效率,电动机冲片的几何形状变得越来越复杂,因此加工所需的模具长度也变得越来越长:“使用双排模具进行加工是目前十分先进的技术。舒勒最新的高速冲 Smartline EV 3.8 工作台长度从 2.7米增加至 3.7 米,能够加工最宽 630 mm 的带料。”
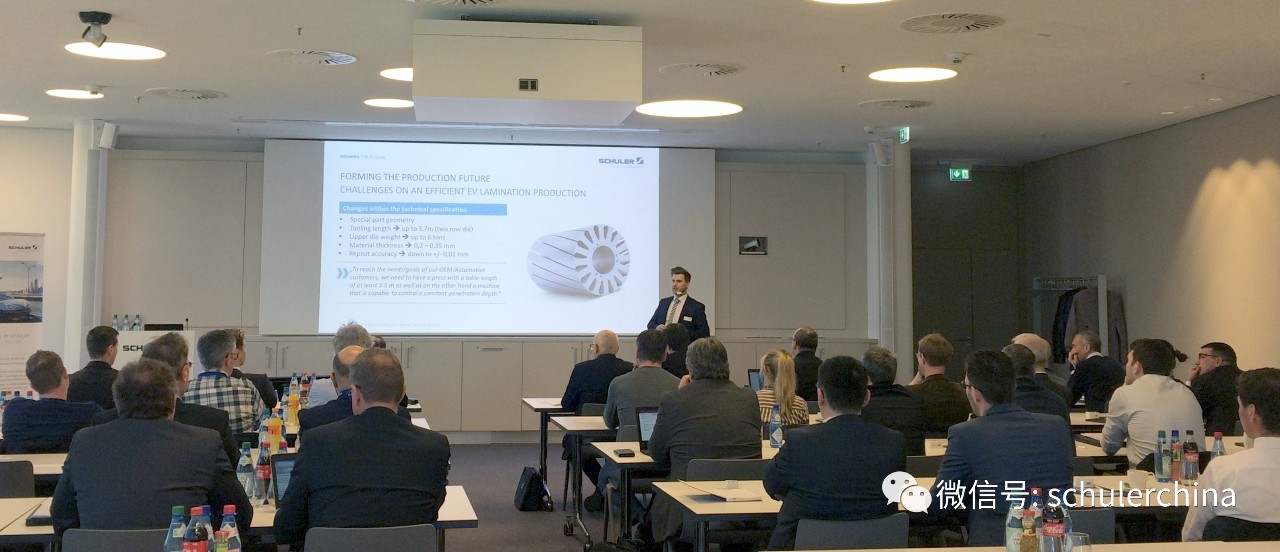
舒勒德国技术日活动现场
同时,材料厚度也减少到了 0.35 mm 甚至 0.2 mm。“按照汽车行业对于电动汽车的新要求,目前的冲片厚度定义在 0.25 mm 到 0.275 mm。因此,压力机供应商必须确保滑块与工作台拥有精准的定位与平行度。”对此,舒勒早在 15 年前就开发出了一套冲裁深度控制装置 (PDC),能够提供完美的滑块定位与位置重复精度。“通过该装置我们可以保证对材料进行精准冲裁,从而实现精准的模内自扣。舒勒的 Smartline 系列设备能够在所有冲裁速度下以 +/-0.01 mm 的精度调节滑块下死点位置。”
SmartlineEV3.8 所配备的 3.7 米长滑块为设备的设计带来了很多挑战。“对于小尺寸的 Smartline 设备,我们曾用激光测量滑块的下降深度,设备会对冲裁深度进行校正,必要时每个行程都会自动校正。”但是对于 3.7 m 长的滑块,就必须要考虑到挠度问题。”现在,舒勒在高级版 的冲裁深度控制系统中,我们把一个应变仪安装到模具的冲头架里,用来代替激光测量:“从而可以保持压力恒定,并可以控制滑块的挠度。无论冲片的形状如何,都能够获得完美的定子和转子叠压效果。”
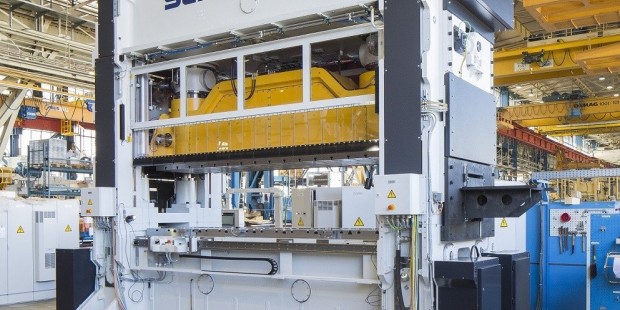
舒勒电动汽车相关业务负责人 Markus Roever先生在展示内部有上千个辊子的滑块导轨
舒勒的目标是凭借 180 年的压力机制造经验,为客户提供可靠、耐用且高精度的设备。Schmidt 先生说道,“我们的设备能够以每分钟 250 冲次的速度全速运行,压力最高可达 3150 kN,上模最大重量达 6 吨。”压力机动态与静态平衡度高,无需特殊的基坑:客户仅需保证基坑的静态承重达到 110 吨即可。“由于动态与静态平衡度高,压力机在全速运行的情况下,在垂直方向的位移小于 1mm。”因此,滑块导轨、压力点、连杆以及主轴承上没有易损件,最大程度地降低了维护成本。
尽管压力机的体积和质量都很大,舒勒仅使用了两个承压点,而非三个:“我们想要确切知道每个压力点上的压力,并确保可以检测到该压力。当有三个承压点时,总会出现较小的偏差,最终出现磨损以及故障只是时间问题。采用两个承压点时,预定义的压力就会达到协调状态,从而将磨损降至最小。同时还能实现滑块的高平行度:我们能够保证从左到右每米的平行度为 0.04 mm。”
得益于 Smartline EV 3.8 采用的高级版 PDC、双压力点设计、四个预张紧滑块导轨以及完美的静态与动态平衡,模具的寿命能够延长 30%。
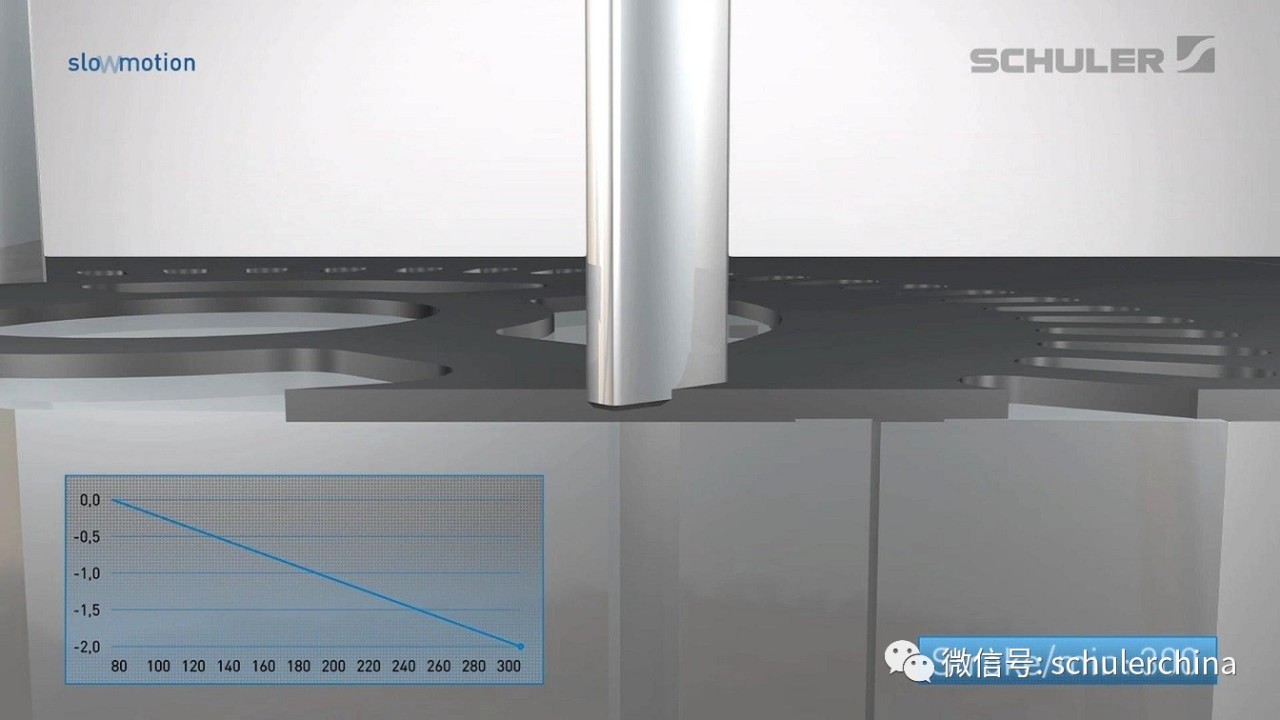
舒勒开发出了一套冲裁深度控制装置 (PDC),保证了滑块相对于工作台的重复位置精度
模具生命周期内完成 1.8 亿冲次
“对于高速钢材料,在模具生命周期内能够完成约 500 万冲次,”模具制造商 AWBEA的 Daniel Kittig 说道。“对于粉末冶金材料,能够实现 3000 万冲次,而对于碳化合金,则能够实现约 1.8 亿冲次,具体取决于工艺条件与材料特性。”在大多数情况下,AWEBA 的模具工程师首先与客户沟通,了解客户的想法。“基于此,我们开始进行设计,同时考量部件的几何形状、尺寸、复杂度以及公差。”
客户要生产的冲片数量是决定采用单排、双排或多排模具的主要因素,但这也取决于压力机的性能:“我们的目标是为客户提供最大程度的灵活性。即可以对工艺和材料问题导致的偏差和变化做出响应。因此我们集成了可调节嵌入功能。”
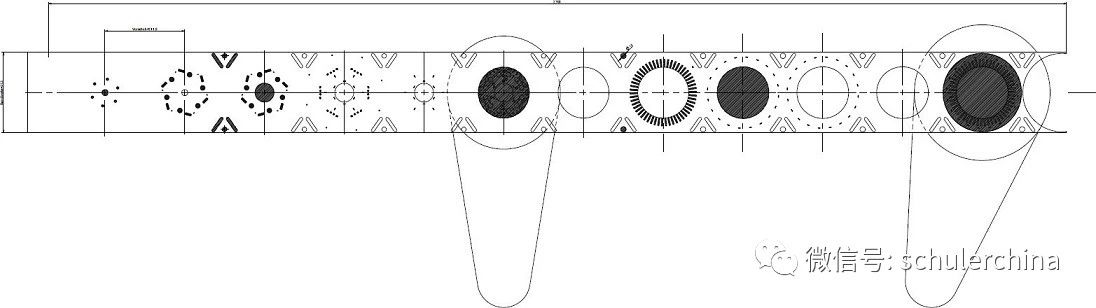
客户要生产的冲片数量是决定采用单排或双排模具的主要因素
每个模具都采用独立的设计。通常,首先通过模具进行预切割,以降低带料的张力。接下来,逐步切割转子的形状,在这个过程中可能需要使用多个不同的工位。“如果仅使用一两个工位,几何形状就会不太稳定。”Kittig 解释道。
在之后的工位中,通过气动冲裁对自扣操作进行分片。用于冲片自扣的压印可以在近轴孔处、成型模之间或近直径处进行:“我们也会在设计中使用黏胶工艺。”
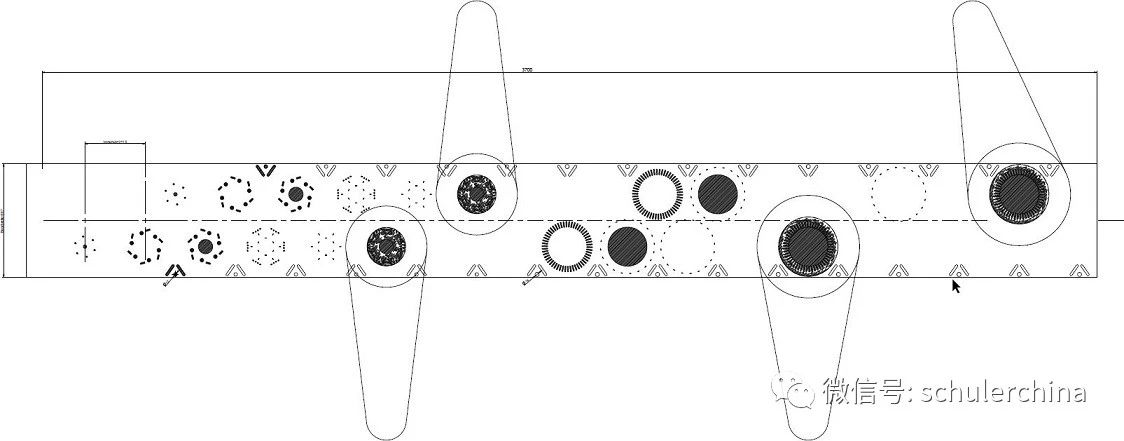
针对更高的产能要求,AWEBA 也开发了双排布局的模具,完美适配舒勒的 Smartline EV 3.8 高速冲
“由于客户的期待产量会越来越高,我们还采用了双排和多排布局,完美适配舒勒的 EV 3.8 压力机,”Kittig 说道。“这样会获得更高的材料利用率。”他说制造这种长度和精度的模具即使对于 AWEBA 也是一个巨大的挑战:“整个模具的精度需要控制在几微米内。”
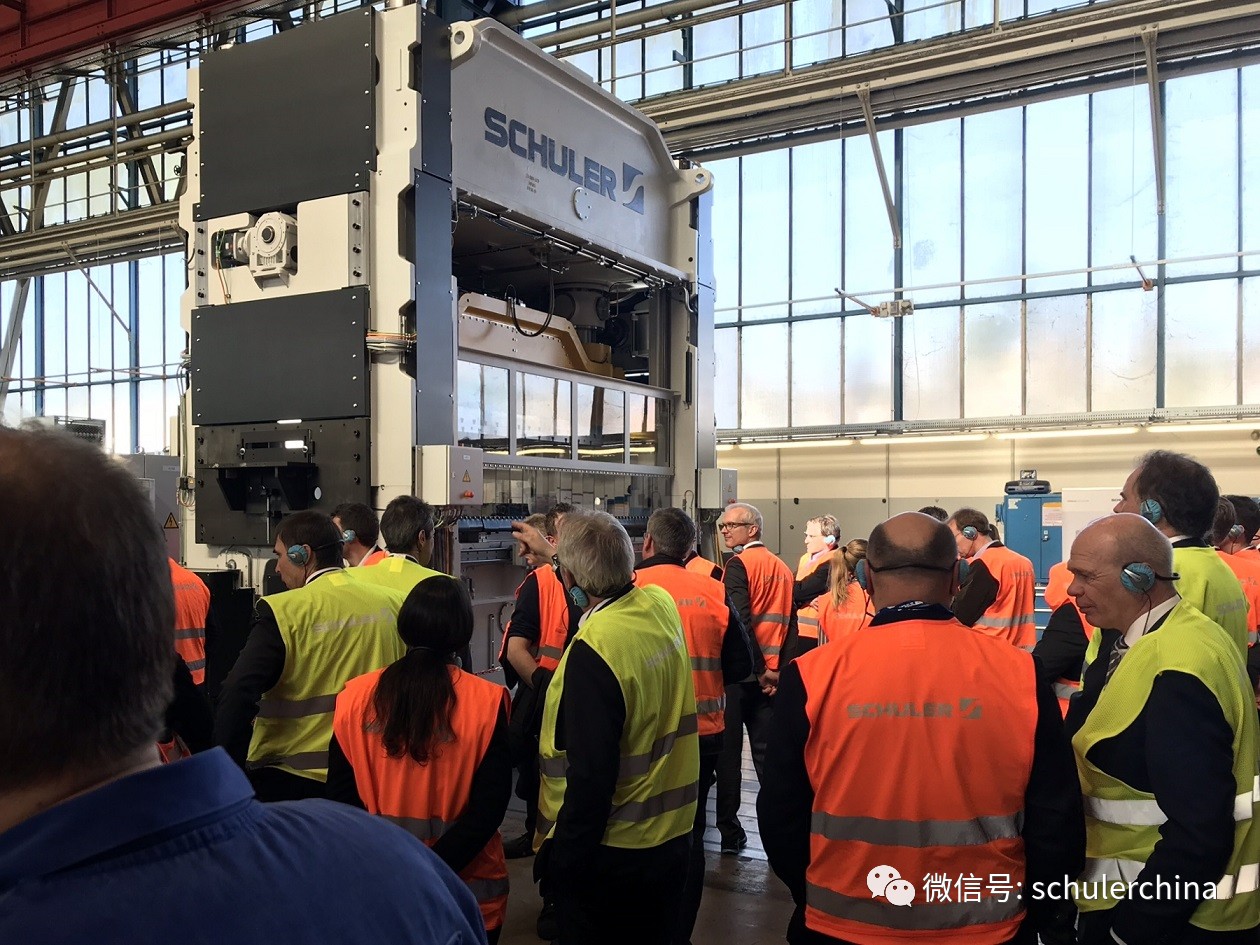
舒勒技术日活动现场参观环节
降低电池壳体的制造成本
电池是导致电动汽车比燃油汽车价格更高的主要原因。但是,从现在的发展规模来看,到 2026 年左右这一情况将会发生改变:彭博公布的统计数据显示,相比 2018 年电池占到总成本的 42%,到那时,这一比例将会降到 24%,电动汽车将比燃油汽车更具经济性。
“对于现今的电动汽车市场,锂离子电池的总需求量为 120 GWH,”舒勒的 Rainer Berkefeld 说道。“而到 2022 年,需求量将会超过 400 GWH,大约相当于需要制造10 亿个电池壳体。”根据 fka 与 Roland Berger 的数据显示,在 2016 年至 2021 年之间,中国的电动汽车电池产能需求为 178 GWH,韩国为 98 GWH,日本为 87 GWH,美国为 74 GWH,德国为 18 GWH。
目前,市场上超过半数的电池采用圆柱形电池壳体(如特斯拉的电动汽车)或方形电池壳体(如丰田、三菱、本田、宝马、大众、奥迪、克莱斯勒、比亚迪、福特等厂商所采用的电池)。虽然圆柱形电池价格更低且商品化更成熟,但是需要复杂的电池管理系统。而方形电池则具有最佳的可扩展性,循环寿命更长,但是生产成本仍然很高。
“舒勒已开发出了一种全自动方形电池生产线,比目前的解决方案生产速度快 5 倍,同时还更节省材料,”Berkefeld先生 说道,“采用的是标准化设备以及在全球汽车和包装行业普遍采用的成熟技术。”原材料采用铝材料块通过冲击挤压制成。当冲头挤压料块时,材料会向相反方向流动。
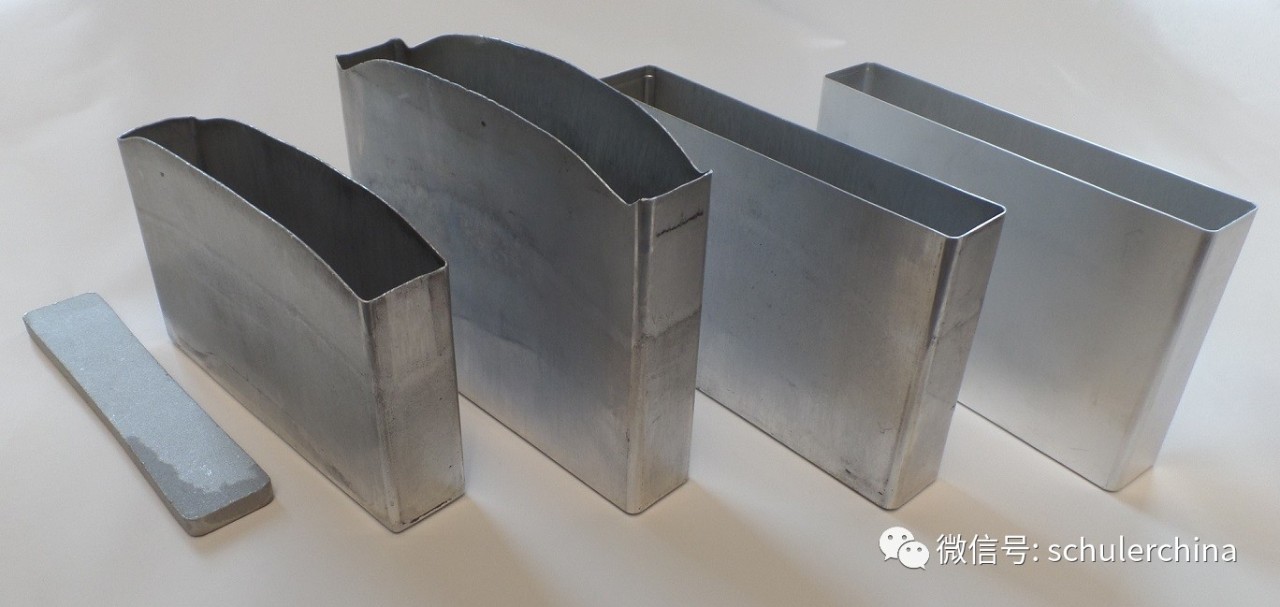
电池壳体原材料采用铝材料块(左)通过冲击挤压制成,并经过成形、处理、切边、清洗等工艺进行加工
之后,从两侧扫描预成形件,以检测裂缝或变形。超出规格的产品将会被移除,以防在接下来的工艺中导致停机。在下一个步骤中,预成形件将会通过四个通道进入到一台300 吨后处理压力机的一模四件模具中。除了变薄拉伸外,还可以集成精冲或整形校准等功能。
然后,将壳体倒置在切边机中。剪切头从内到外以摆动的方式工作,避免内部出现毛刺。在进行清洗、干燥与通过视像检测后,就可以进行使用了。这台高速冲设备目前已在一家大型电池制造商的工厂中投入使用,每年能够生产超过 3000 万个电池壳体。
舒勒同时也提供用于制造电池盖的冲裁压力机。它采用级进模,包含 12 个成形工位,如冲孔、切边、压印与分片等。
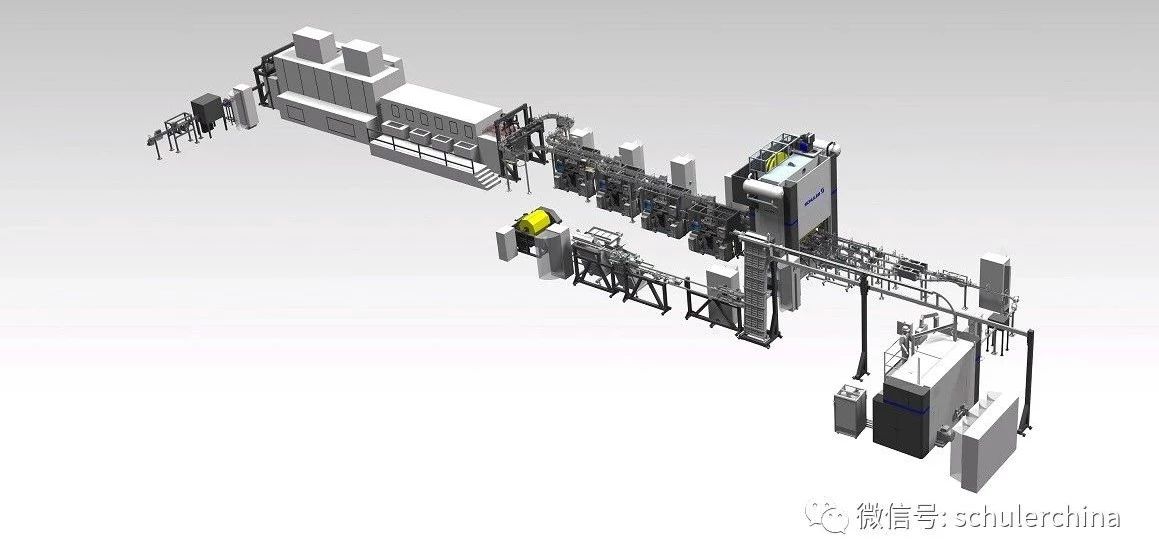
生产线由冲击挤压机(右下)、精冲压力机、切边机、清洗装置和烘干装置组成
举报 0
收藏 0
分享 102
-
冲压技术在电机叠片制造的应用
2024-09-06 -
车身零部件包边质量控制要点
2024-09-05 -
轻量化技术——热汽胀形工艺技术解析
2024-09-04 -
高强板车身件冲压技术
2024-09-02
最新资讯
-
杜尔中国海外项目-Stellantis 集团摩
2025-03-20 11:59
-
3D扫描仪新品 | KSCAN-X 重新定义工
2025-03-20 11:58
-
三维扫描仪新品 | NimbleTrack-CR 极
2025-03-20 11:53
-
浙江省委书记王浩调研思看科技
2025-03-19 08:33
-
旭化成精细化工(南通)新工厂竣工
2025-03-18 10:49