分享 | 带你了解汽车结构件的压铸技术
2019-06-10 22:13:38· 来源:旺材汽车轻量化
1. 前言由于性能及品质要求高,汽车结构件大多采用铁或钢质材料,通过其他制造工艺生产。汽车轻量化的要求,这类铸件正在向轻合金转化。采用压铸工艺生产结构件不但可以缩短生产周期,还可达到精近化,省去大量的机加工序,节约成本,但
1. 前言
由于性能及品质要求高,汽车结构件大多采用铁或钢质材料,通过其他制造工艺生产。汽车轻量化的要求,这类铸件正在向轻合金转化。采用压铸工艺生产结构件不但可以缩短生产周期,还可达到精近化,省去大量的机加工序,节约成本,但压铸工艺生产难度大。布勒公司针对汽车结构件特点和多年的专业经验,开发了 Structual结构件压铸工艺。布勒 Structural 结构件压铸工艺主要涉及压铸机、压铸模具、合金材料、合金液处理、真空应用、工艺优化等因素。生产实践证明,正确处置上述工艺因素,完全可以在通用压铸机上生产出合格的结构件。
2. 结构件的特征和要求
汽车结构件指的是汽车中的承载件或受力件,与汽车安全性密切相关。在汽车车身中,许多结构件装在车身结构的节点上并与其他构件连接形成抗变形的高强度框架,这类结构件通常具有尺寸大、壁薄、结构复杂等特征。
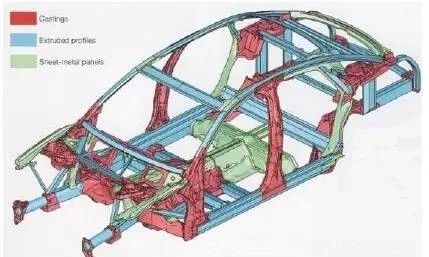
图1是AudiA8轿车铝合金车身,其中红色部位系铝合金压铸结构件。由于在行驶中要保证汽车可靠的安全性,对这类压铸件的机械性能要求高,韧性相关的结构件一般要求抗拉强度≥180MPa,伸长率≥10%;强度相关的结构件,一般要求抗拉强度≥210MPa,伸长率≥7%。为获得高性能,结构件往往需要热处理。如果与其它构件连接,还需要良好的焊接性或铆接性。显然,常规的压铸工艺无法满足汽车结构件的生产要求,结构件的压铸生产需要进行新的工艺开发。
3. 布勒 Structural 结构件压铸工艺要素
布勒 Structual 结构件压铸工艺为压铸工厂生产汽车结构件提供了完整的技术和工艺解决方案,在欧洲压铸厂的实际生产中获得广泛应用。布勒 Structural 结构件压铸工艺涉及的主要工艺措施或因素包括合金、模具、真空、浇注、喷涂及挤压等几个方面,以下进行分别介绍。
3.1 压铸合金
传统的标准压铸合金不能满足汽车结构件的要求。目前欧洲常用于结构件压铸的铝合金主要是Silafont-36、Magsimal-59和Castasil-37,这些合金通常称为高韧性合金。与传统的标准压铸铝合金相比,这些合金都严格控制了 Fe 含量,一般控制在 0.2%以下。其意义是避免合金中产生针状的 AlFeSi 相,该相会恶化合金的强度、延展性及疲劳性能,在铸件受力状态下还可能诱发裂纹。Silafont-36合金将Si含量控制在共晶点附近,保持了良好的铸造性能和充型能力,并通过提高Mn 含量防止因 Fe 铁含量降低而导致的粘模现象。镁含量对该合金的机械性能影响显著,通过调节镁含量可调整合金的机械性能。Silafont-36合金的屈服强度和延伸率与热处理制度密切相关。在 T6 热处理状态下,合金的屈服强度可达210-280MPa,延伸率可达 7-14%。
Masgsinal-59 合金降低了Si含量,提高了Mg含量,适当的 Si/Mg 比例改善了合金的铸造性能和补缩性能。该合金的主要特点是铸态下的机械性能就很高,壁厚在 2-4mm 的情况下,拉伸强度可达310-340,屈服强度可达160-220MPa,延伸率可达 12-18,往往不用热处理即能满足结构件的机械性能要求。但该合金的机械性能与铸件壁厚密切相关,所以特别情况下需要进行 T5或类似的时效处理予以改善。
Castasil-37是近年出现的新型压铸铝合金,具有耐长期时效的能力,主要应用目标是在较高温度下工作的零部件,保证在整个使用期内具有稳定的性能。Castasil-37合金也将Si含量控制在共晶点附近,具有良好的铸造和充型性能。合金的机械性能主要受Si、Mn、Mo及Sr等元素的影响,Sr的作用主要是改善Si在合金中的形态,但过量Sr会增加合金的吸气倾向。在2-3mm壁厚的情况下,铸态下合金的拉伸强度可达260-300,屈服强度可达120-150MPa,延伸率可达10-14。
3.2 模具设计
模具设计要注意以下几点:(1)首先要正确设计浇注系统,合理选定浇注系统位置、充型方向以及各部分的尺寸,保证良好的充型顺序和流态。(2)模具的排气口要设置在型腔最后充填的位置,保证抽真空持续至充型结束。此外,在铸件的重要部位、液流汇合或容易产生紊流的部位也应设置排气口,减小这些部位产生缺陷的可能性。(3)应对排气道面积进行仔细校核,真空通道面积足够,保证排气畅通。(4)模具密封性影响真空的形成,必须保证模具密封良好。(5)要仔细分析模具的热平衡,合理设计冷却/加热管道,这是生产中对模具温度进行有效控制的前提条件。(6)在模具制造之前,最好进行充型及凝固方面的模拟,由此可获得压铸过程信息,有助于模具的改进。
3.3 合金熔化和处理
对于一般用途,Silafont-36 和 Castasil-37 合金无需特别处理便可用于压铸生产。但如果生产高品质要求的铸件,应注意以下几点:(1)采用高纯电解金属配制的合金,熔化过程中避免金属杂质污染,尤其是Fe、Zn和 Cu,Castasil-37 合金控制杂质还包括 Mg。(2)快速熔化,防止金属液氧化及偏析现象。氧化物和硬夹杂对铸件的铸造性能和机械性能都有不利影响。(3)为保证合金的高延展性,尽可能在炉内使用叶片旋转除氢和净化。(4)控制 Sr 的熔损,过多熔损会影响合金的延展性,但 Sr 含量增高会增加合金的吸氢倾向。Silafont-36 合金还应控制 Mg 的熔损,Mg 的熔损会影响合金的强度。(5)不可过热,合金熔化温度不超过 780oC。否则,加重合金吸气及氧化,Sr和Mg 的熔损增加。氧化显著影响Masgsinal-59 合金的延展性。快速熔化后使用叶片进行深度净化,合金的优势才能保持。一般情况下,无需熔盐、变质剂或碱性稀土等加入熔液中。如果使用回炉料,氩气或氮气旋转除气工序则是必需的。
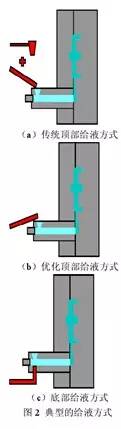
3.4 给液(浇注)方式
给液方式指的是金属液浇入或输入压室的方式,图 2 是几种典型的给液方式。试验表明给液方式对铸件的延伸率有明显影响。传统的顶部给液方式容易造成金属液之间的冲击、溅液、氧化及卷气,会造成铸件基体组织缺陷,降低延伸率。底部给液方式减少了合金液的扰动及热损失,降低了合金液氧化、产生浮渣微粒以及吸气的可能性,因而铸件基体夹杂和缺陷减少,有利于提高铸件的延伸率。但底部给液方式必需对压铸机进行局部修改,要使用专门的压室和模具,压铸机可能失去通用性。如果采取优化的给液管长度、给液管加热、平稳给液等特别措施,优化顶部给液方式也同样能达到提高铸件延伸率的目的,而不用对压铸机和压室进行改动,压铸生产转化方便。
3.5 脱模剂及喷涂工艺
脱模剂或润滑剂可产生气体进入铸件,增加铸件中的含气量。在采用真空工艺时,脱模剂或润滑剂的挥发则是铸件中气体的重要来源。在选用脱模剂或润滑剂时,要经过验证,选用发气性低和挥发性好的产品。其次,要选用先进的喷涂设备,具备高动态特性,喷涂参数可调。尽可能减少喷涂量,保证快速喷涂和精确喷涂。喷涂目的主要是保护模具表面和冷却模具热节,模具的整体温度控制尽可能由模具内部的加热/冷却管道完成。在结构件压铸生产中,要对喷涂时间、喷涂角度和范围,喷吹距离等因素进行优化,在型腔中不可有残留水分,使进入铸件的气体最少。
3.6 真空工艺
真空充型是结构件压铸重要的工艺措施,采用真空工艺应注意以下几点:
(1)及时启动真空系统,冲头封住浇料口后立即开始抽真空。
(2)真空系统功率足够,抽真空快速。
(3)压室充满前必须达到要求的真空度,否则影响效果。
(4)尽量延长抽真空时间,真空阀尽可能的迟闭合。
试验结果表明,型腔内的绝对压力在300mbar 以上时,对铸件的延伸率影响不大。当型腔内的绝对压力达到 150mbar 以下,铸件的延伸率才随真空度的提高而明显增加。真空度对铸件的表面质量也有明显影响,铸件的表面质量随真空度提高而改善,如图 3 所示。铸件中的气泡随真空度增加而减少,但气泡不是影响铸件延伸率的主导因素。高真空还可以增大压铸工艺窗,使压铸工艺宽松。但高真空对真空设备性能要求高,会导致真空工艺成本增加。双回路真空系统对结构件压铸非常有效,图4(a)是双回路真空系统原理图,图 4(b)是布勒配套的 Vacu2 双回路真空系统。
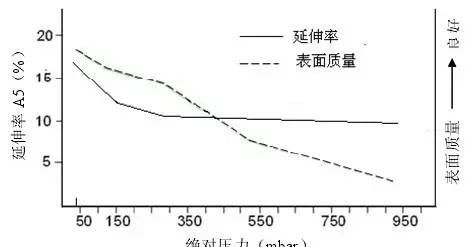
双回路真空系统中一个回路的抽气口设置在压室的上端,主要用于压室内的空气抽出。当压射冲头前行封住浇料口时,压室抽真空启动,在冲头即将封住抽气口的瞬间关闭。另一个回路设置与传统的真空工艺基本相同,主要用于型腔内的空气抽出。双回路真空系统可以加速抽真空的速度,有利于获得稳定的高品质铸件。采用嵌入特殊钢环(或铜环)的压射冲头可减小冲头与压室之间的间隙,增加密封性。
3.7 压铸机及压铸工艺优化
压铸工艺对生产合格的汽车结构件十分重要,正确的选择压射模式、压射参数等有利于减少压铸件中的缺陷。压铸件中的气体有相当一部分来自金属液在压室中的预充填阶段,所以应充分注意优化慢压射阶段的压射模式,避免金属液在压室中卷入气体。应正确选用脱模剂和润滑剂,优化喷涂工艺。压铸机性能稳定,要有灵活的编程模式和实时控制系统,保证整个压铸过程合理及工艺参数偏差最小。对模具温度应进行精确控制,通过冷却水分配器,监控各个冷却回路的流量及温度,形成要求的温度分布。良好的模具设计,恰当的压铸工艺,理想的充型模式,可以保证铸件品质优良,减轻对真空度的依赖。此外,在重要部位或厚壁部位还可以使用挤压销,减小缩松或增加密度。使用金属液前沿传感器,准确知道金属液的流程,可以优化充填模式。
4. 压铸结构件及应用
使用布勒压铸机及 Structual 结构件压铸工艺,汽车结构件压铸在欧洲已形成规
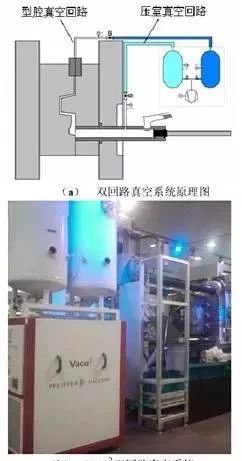
模生产能力。本节介绍布勒公司在今年 GIFA 展览会上展出的一些压铸结构件。这些结构件目前已装入许多车型上,大大减轻了车体重量,改进了车身结构,满足汽车应用要求。
图 5 是 B 形支架,装于车身中部、前后门之间。压铸 B 形支架尺寸稳定性高,热处理后具有很高的屈服强度和延伸率。
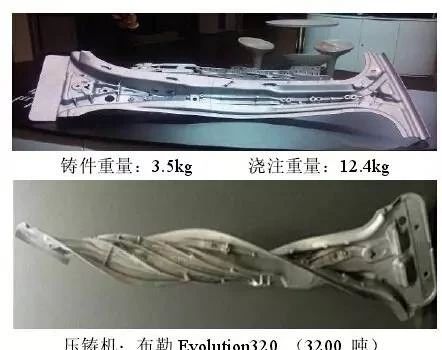
图 6 是铝合金车门框架压铸件。用铝合金压铸结构代替原钢板结构,整套车门可减轻重量约40kg,减重效果明显。压铸车门框架还具有非常好的刚性,可以使用焊接、铆接及拴接等技术,改善装配精度。图 7 是前轮减震器上盖压铸件,装在汽车前端,承受非常大的动载荷。该件壁厚仅 3mm,体现了压铸件的最佳性能。图 8 及图 9分别是纵向构件和悬挂臂,装于车身下部,承载较高载荷,对强度和延伸性要求高。图 10 是镁合金中间控制板,装于车内部中间位置。镁合金的中控板压铸件壁厚仅为 2mm 左右,尺寸精度高,装配方便,大幅减轻了构件的重量。
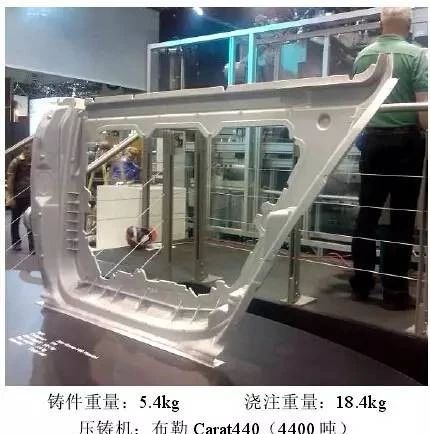
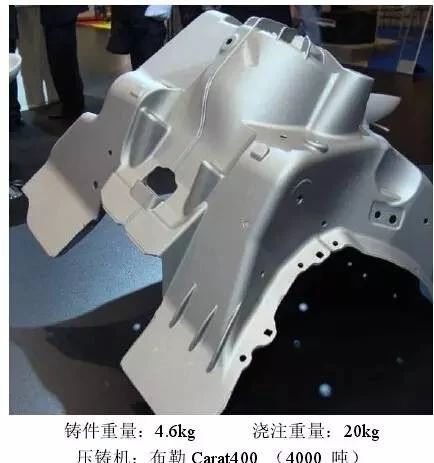
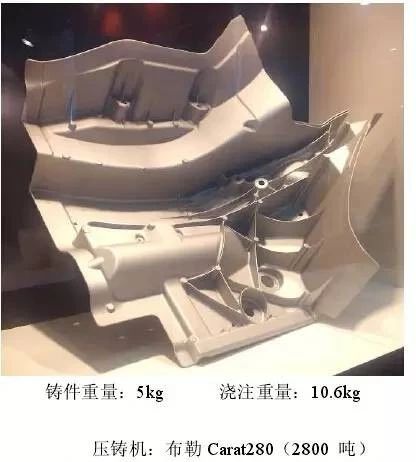
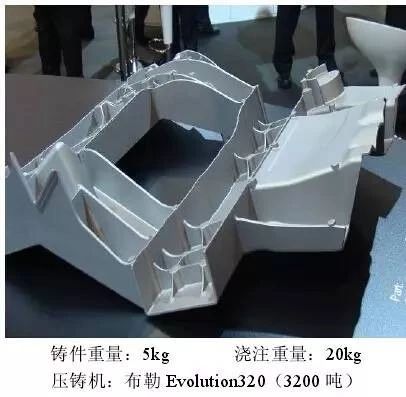
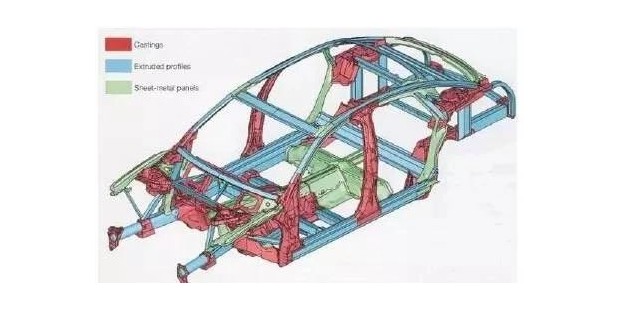
5. 结束语
汽车结构件具有很高的强度和韧性要求。布勒 Structual 结构件压铸工艺采用通用压铸机,配合辅助的工艺措施及优化的工艺因素,实现了压铸汽车结构件的工业化生产。由压铸工艺生产的汽车结构件可以进行热处理、焊接、铆接及粘合连接等,品质及性能完全符合要求。压铸汽车结构件在欧洲已进入汽车市场,并逐步由高档车向中低档车普及,应用范围日渐扩大。结构件的压铸成功,标志着压铸工艺水平又达到了一个新的高度。目前汽车结构件压铸的利润空间较大,中国压铸业也应积极进行技术开发和跟进,共享压铸技术进步成果
举报 0
收藏 0
分享 129
-
冲压技术在电机叠片制造的应用
2024-09-06 -
车身零部件包边质量控制要点
2024-09-05 -
轻量化技术——热汽胀形工艺技术解析
2024-09-04 -
高强板车身件冲压技术
2024-09-02
最新资讯
-
全球产业链聚沪 共探双碳新路径 SNEC
2025-04-18 18:05
-
柯马签订具有约束力的协议收购 Autom
2025-04-17 13:01
-
高效协同新范式:比亚迪叉车领创智能
2025-04-17 10:04
-
埃马克德国总部迎来中国社科院工业经
2025-04-15 09:40
-
埃马克这项全新应用即将在CIMT惊艳首
2025-04-15 09:37