轿车白车身电阻点焊焊接缺陷的控制
2019-09-09 22:35:34· 来源:江西昌河汽车有限责任公司 作者:沈婵媛
在连接白车身的过程中,电阻点焊是十分关键的一项操作工艺,尽管在焊接时通常会采取多种控制措施,但质量缺陷仍然较为常见,主要是由于焊接参数不合格及设备缺陷所引起的,因此当前最重要的是明确焊接缺陷的类型、特点及原因,并在此基础
在连接白车身的过程中,电阻点焊是十分关键的一项操作工艺,尽管在焊接时通常会采取多种控制措施,但质量缺陷仍然较为常见,主要是由于焊接参数不合格及设备缺陷所引起的,因此当前最重要的是明确焊接缺陷的类型、特点及原因,并在此基础上进行针对性处理,把握好焊接工艺及温度,本文就对此问题进行了详细探讨。
前言
目前,在企业生产中的点焊降飞溅涉及的因素很多,需要协调和处理的技术问题也很多。白车身的焊接以点焊处理为主,焊点大于3000个,与车身强度密切相关,因此需要反复核查焊点总数,确定好焊接参数,由专业人员负责管理,并对各项参数的变化情况进行监控,同时还应选择稳定性达标的焊接设备,有效保障焊接质量。因此,如何在生产中降低点焊飞溅一直是国内各汽车厂努力的目标。
1 点焊质量缺陷
点焊质量缺陷主要包括以下几种类型。第一是漏焊,指的是在焊接时未实现母材与涂层的熔合,主要是因为焊接设备未能触及焊点或焊点处温度较低,没有达到熔合的标准。第二是焊核不足,与焊核及凸台尺寸较小直接相关。第三是虚焊,指工件在焊接处局部融化,但未形成凸台,主要是由于焊件表面热量过低所导致。第四是压痕过深,主要是由于电极压力过高所导致的。存在压痕时会影响焊件的焊接等级,但只要处于工程可接受的范畴内即可,并且工件两侧接受度不同。第五是飞溅,指在焊接时融化金属喷出,如果落在工件表面上则会击穿工件。通常是由于固态金属未能束缚融化金属所引起的。第六是裂纹,指焊件中断,未能形成连接效果,多出现于焊核中心,方向不定。
2 常见的点焊控制手段与办法
2.1焊接员工缺陷识别能力培养
为了让员工更准确地把握焊点表面缺陷的可接受程度,车身车间采用边界样本作为培训工具培训员工。边界样本分为实物边界样本和图示边界样本。边界样本是缺陷可接受的最低质量标准。通过边界样本对员工进行培训,从图示、实物上感知缺陷,以便在生产过程中对缺陷更好地控制。
2.2制作点焊飞溅挡板
飞溅问题是点焊的难题。由于其形成原因较多,上述提供的方法只能减少飞溅的产生,为了减少飞溅对零件表面的影响,可以制作点焊飞溅挡板阻断毛刺测到零件表面的过程,是唯一可行的方法。在进行点焊前碰片吸到被飞溅表面,点焊后再取下来。这种控制方法在轿车生产中常被采用,虽然增加较多人工成本,但确实是一种非常有效的控制办法。
2.3电极头定期修磨
电极头修磨有2种规定,一是定焊点数修磨,一种是定时间修磨。其中定样点数修磨一般预测较准确,在机器人点焊中比较常用,通过对焊点数进行自动计数,达到数量后自动修磨。但在手工点焊中,为了降低成本,一般采用定时修磨,每2h修磨1次。
2.4非破坏检查
焊点非破坏性检查是在生产现场不影响被检查件的性能和完整对其检测缺陷,非破坏检查是对焊点强度进行检查确认的一种方法(如图1)。用专用凿子在距焊点3-6mm处插入一定深度(凿子前端应与被控焊点平齐),上下摆动30°,若焊点不开裂,证明点焊质量良好。通过每班次4次的非破坏检查,及时发现点焊出现脱焊、虚掉的焊钳,并进行修磨,以确保点焊质量。
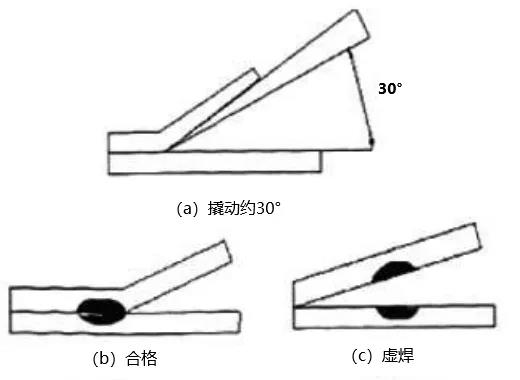
图1 非破坏性检查点焊示意图
2.5焊点破坏性检查
焊点破坏性试验是用强力将焊点拉开,以检验焊点熔核的太小。定期抽查1台白车身,用冲击钻将车身板材钻开,测量焊点熔棱大小,以检验焊点强度。
2.6点焊参数的定期测量
点焊参数可能会随着设备太小、电缆老化、控制系统故障、水气压变化而导致点焊钳终端参数发生变化。所以必须对点焊参数进行定期测量。用于关键焊点的焊钳测量频次为2个星期1次,非关键焊点的点焊参数每季度测量1次。
2.7点焊设备变更验证
在点焊参数变更、搬迁、更换电缆等涉及点焊设备时,必须进行作业更改验证,常见的控制办法为连续进行焊点非破坏性检查,以检查结果来判定参数的合理性。
3 车联网信息安全现状
为了避免出现点焊质量缺陷,可从以下几个方面入手。
3.1焊接设备
在选择焊接设备时需要把握好以下几项要点。第一,设备电流及压力波动幅度不能太大,并且需要做好设备的调试工作,促使设备在焊接时稳定性达标。第二,设备应具有电极对中性特点,如果不对中则会导致电流不够均匀,进而出现飞溅、击穿等多种类型的缺陷。如果问题较为严重,还会损坏电极。第三,控制好电极端头直径,如果直径过大则会降低输入热量,影响电流密度,导致焊核尺寸无法达到标焊接标准,严重时还会出现开焊问题,因此需要严加控制。第四是电极端头表面,如果表面存在缺陷,则会出现偏压问题,影响点焊质量。
3.2焊接操作
在焊接操作时需要控制好以下几项要点。第一是焊钳垂直度。如果焊接时姿势不够标准,则会影响垂直度,进而引发飞溅、击穿等缺陷,并且会使板材变形,导致零件质量无法达到相应标准。第二是点焊点边,同样与操作者的失误有关,飞溅量较大,并且会带走液态金属,导致焊口尺寸过小。第三是焊接分流,与人员操作不规范密切相关,导致焊钳与工件相碰撞。分流时会影响电极两端电流,导致点焊热量无法满足要求,使得焊核缺失。
3.3工艺设计
工艺设计主要包括以下几个方面。第一是焊点过近。通常情况下在焊接时焊点重合的现象较为常见,与设计位置偏差及操作失误相关,导致焊接表面平整度未能达标,容易引发飞溅及击穿等质量缺陷。如果焊点距离过近,则会导致焊接分流,难以保障焊接质量。第二是夹具干涉,如果未能给焊钳留有足够的活动空间,则会导致焊接分流、工件变形、焊点位置出现偏差,因此需要根据焊接情况预留足够的空间。第三是多层板厚度。当接触电阻处于稳定状态时,热量较为集中,中央区域温度较高,而两边板材的热量明显不足,难以与中间区域实现熔合,严重影响焊核尺寸,进而引发开焊缺陷。当出现此种缺陷时调整难度较高,即使定增大电流也无法解决问题,因此应在产品设计阶段进行严格控制,提前消除缺陷。
3.4焊接温度
焊接温度是一项控制重点,包括厂房和冷却水两个方面。通常在焊接过程中会散发出大量的热量,但焊接设备能够承受的温度变化范围相对较广,因此厂房温度无需特别进行控制,但也必须避免温度过低,否则就会影响设备的正常运转。另外,冷却水温度控制在20℃左右最为合适,要满足这样的要求并没有太高的难度,但应避免温度过高,原因在于温度超出规定范围的情况下会导致设备故障,引发飞溅、电极粘连及磨损等不同类型的缺陷,因此需要严格控制温度,并在出现问题时及时对设备进行检修。
4 结语
总而言之,在控制焊接质量的过程中应从设备、工艺、操作方式、温度等多个方面入手,选择性能较好的设备,正确使用各项工艺,合理调控温度,严格控制焊钳垂直度。只有把握好这些因素并严加控制,才能避免出现漏焊、飞溅等类型的缺陷,进而促使白车身的焊接质量更好。
前言
目前,在企业生产中的点焊降飞溅涉及的因素很多,需要协调和处理的技术问题也很多。白车身的焊接以点焊处理为主,焊点大于3000个,与车身强度密切相关,因此需要反复核查焊点总数,确定好焊接参数,由专业人员负责管理,并对各项参数的变化情况进行监控,同时还应选择稳定性达标的焊接设备,有效保障焊接质量。因此,如何在生产中降低点焊飞溅一直是国内各汽车厂努力的目标。
1 点焊质量缺陷
点焊质量缺陷主要包括以下几种类型。第一是漏焊,指的是在焊接时未实现母材与涂层的熔合,主要是因为焊接设备未能触及焊点或焊点处温度较低,没有达到熔合的标准。第二是焊核不足,与焊核及凸台尺寸较小直接相关。第三是虚焊,指工件在焊接处局部融化,但未形成凸台,主要是由于焊件表面热量过低所导致。第四是压痕过深,主要是由于电极压力过高所导致的。存在压痕时会影响焊件的焊接等级,但只要处于工程可接受的范畴内即可,并且工件两侧接受度不同。第五是飞溅,指在焊接时融化金属喷出,如果落在工件表面上则会击穿工件。通常是由于固态金属未能束缚融化金属所引起的。第六是裂纹,指焊件中断,未能形成连接效果,多出现于焊核中心,方向不定。
2 常见的点焊控制手段与办法
2.1焊接员工缺陷识别能力培养
为了让员工更准确地把握焊点表面缺陷的可接受程度,车身车间采用边界样本作为培训工具培训员工。边界样本分为实物边界样本和图示边界样本。边界样本是缺陷可接受的最低质量标准。通过边界样本对员工进行培训,从图示、实物上感知缺陷,以便在生产过程中对缺陷更好地控制。
2.2制作点焊飞溅挡板
飞溅问题是点焊的难题。由于其形成原因较多,上述提供的方法只能减少飞溅的产生,为了减少飞溅对零件表面的影响,可以制作点焊飞溅挡板阻断毛刺测到零件表面的过程,是唯一可行的方法。在进行点焊前碰片吸到被飞溅表面,点焊后再取下来。这种控制方法在轿车生产中常被采用,虽然增加较多人工成本,但确实是一种非常有效的控制办法。
2.3电极头定期修磨
电极头修磨有2种规定,一是定焊点数修磨,一种是定时间修磨。其中定样点数修磨一般预测较准确,在机器人点焊中比较常用,通过对焊点数进行自动计数,达到数量后自动修磨。但在手工点焊中,为了降低成本,一般采用定时修磨,每2h修磨1次。
2.4非破坏检查
焊点非破坏性检查是在生产现场不影响被检查件的性能和完整对其检测缺陷,非破坏检查是对焊点强度进行检查确认的一种方法(如图1)。用专用凿子在距焊点3-6mm处插入一定深度(凿子前端应与被控焊点平齐),上下摆动30°,若焊点不开裂,证明点焊质量良好。通过每班次4次的非破坏检查,及时发现点焊出现脱焊、虚掉的焊钳,并进行修磨,以确保点焊质量。
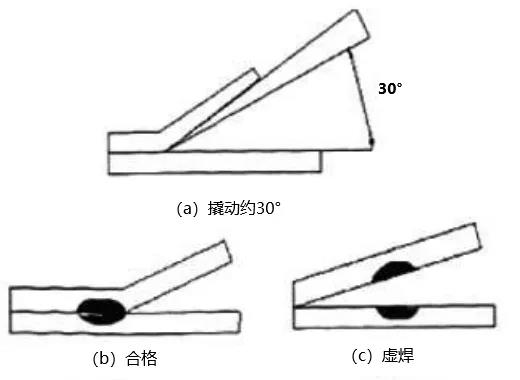
图1 非破坏性检查点焊示意图
2.5焊点破坏性检查
焊点破坏性试验是用强力将焊点拉开,以检验焊点熔核的太小。定期抽查1台白车身,用冲击钻将车身板材钻开,测量焊点熔棱大小,以检验焊点强度。
2.6点焊参数的定期测量
点焊参数可能会随着设备太小、电缆老化、控制系统故障、水气压变化而导致点焊钳终端参数发生变化。所以必须对点焊参数进行定期测量。用于关键焊点的焊钳测量频次为2个星期1次,非关键焊点的点焊参数每季度测量1次。
2.7点焊设备变更验证
在点焊参数变更、搬迁、更换电缆等涉及点焊设备时,必须进行作业更改验证,常见的控制办法为连续进行焊点非破坏性检查,以检查结果来判定参数的合理性。
3 车联网信息安全现状
为了避免出现点焊质量缺陷,可从以下几个方面入手。
3.1焊接设备
在选择焊接设备时需要把握好以下几项要点。第一,设备电流及压力波动幅度不能太大,并且需要做好设备的调试工作,促使设备在焊接时稳定性达标。第二,设备应具有电极对中性特点,如果不对中则会导致电流不够均匀,进而出现飞溅、击穿等多种类型的缺陷。如果问题较为严重,还会损坏电极。第三,控制好电极端头直径,如果直径过大则会降低输入热量,影响电流密度,导致焊核尺寸无法达到标焊接标准,严重时还会出现开焊问题,因此需要严加控制。第四是电极端头表面,如果表面存在缺陷,则会出现偏压问题,影响点焊质量。
3.2焊接操作
在焊接操作时需要控制好以下几项要点。第一是焊钳垂直度。如果焊接时姿势不够标准,则会影响垂直度,进而引发飞溅、击穿等缺陷,并且会使板材变形,导致零件质量无法达到相应标准。第二是点焊点边,同样与操作者的失误有关,飞溅量较大,并且会带走液态金属,导致焊口尺寸过小。第三是焊接分流,与人员操作不规范密切相关,导致焊钳与工件相碰撞。分流时会影响电极两端电流,导致点焊热量无法满足要求,使得焊核缺失。
3.3工艺设计
工艺设计主要包括以下几个方面。第一是焊点过近。通常情况下在焊接时焊点重合的现象较为常见,与设计位置偏差及操作失误相关,导致焊接表面平整度未能达标,容易引发飞溅及击穿等质量缺陷。如果焊点距离过近,则会导致焊接分流,难以保障焊接质量。第二是夹具干涉,如果未能给焊钳留有足够的活动空间,则会导致焊接分流、工件变形、焊点位置出现偏差,因此需要根据焊接情况预留足够的空间。第三是多层板厚度。当接触电阻处于稳定状态时,热量较为集中,中央区域温度较高,而两边板材的热量明显不足,难以与中间区域实现熔合,严重影响焊核尺寸,进而引发开焊缺陷。当出现此种缺陷时调整难度较高,即使定增大电流也无法解决问题,因此应在产品设计阶段进行严格控制,提前消除缺陷。
3.4焊接温度
焊接温度是一项控制重点,包括厂房和冷却水两个方面。通常在焊接过程中会散发出大量的热量,但焊接设备能够承受的温度变化范围相对较广,因此厂房温度无需特别进行控制,但也必须避免温度过低,否则就会影响设备的正常运转。另外,冷却水温度控制在20℃左右最为合适,要满足这样的要求并没有太高的难度,但应避免温度过高,原因在于温度超出规定范围的情况下会导致设备故障,引发飞溅、电极粘连及磨损等不同类型的缺陷,因此需要严格控制温度,并在出现问题时及时对设备进行检修。
4 结语
总而言之,在控制焊接质量的过程中应从设备、工艺、操作方式、温度等多个方面入手,选择性能较好的设备,正确使用各项工艺,合理调控温度,严格控制焊钳垂直度。只有把握好这些因素并严加控制,才能避免出现漏焊、飞溅等类型的缺陷,进而促使白车身的焊接质量更好。
举报 0
收藏 0
分享 160
-
熟背铝合金焊接口诀,秒杀一切焊接难题
2024-07-25 -
激光焊接技术
2024-07-10 -
创想焊缝跟踪系统适配研华宝元机器人自动化焊接
2024-05-23 -
焊装生产线规划及布置概述
2024-05-22
编辑推荐
最新资讯
-
果栗智造磁悬浮技术赋能汽车制造:破
2025-04-03 19:27
-
比亚迪叉车的智慧演变:从动力革新到
2025-04-02 09:15
-
重磅剧透!首批参展商名单曝光——这
2025-04-01 20:48
-
施耐德电气发布新一代Harmony XVB7模
2025-04-01 18:51
-
[转载] 机床巨头埃马克:百年跌宕再
2025-03-31 12:42