专利创新成果融入标准,实现中国汽车热冲压钢的追赶和超越 —《汽车用高韧性热镀铝硅合金镀层热冲压钢板技术要求》解读
2021-06-05 11:11:51· 来源:中国汽车工程学会标准
2021年4月,中国汽车工程学会正式发布《汽车用高韧性热镀铝硅合金镀层热冲压钢板技术要求》(T/CSAE 179-2021),这是第一项专利权人承诺基于FRAND原则以合理费率进行专利许可的CSAE标准,开启了专利创新成果融入团体标准的创新实践。而
2021年4月,中国汽车工程学会正式发布《汽车用高韧性热镀铝硅合金镀层热冲压钢板技术要求》(T/CSAE 179-2021),这是第一项专利权人承诺基于FRAND原则以合理费率进行专利许可的CSAE标准,开启了专利创新成果融入团体标准的创新实践。而随着该标准的推广实施,新技术应用预计将为企业钢材成本每吨节省1000元。
导读
——缘起——
汽车用户对铝硅镀层热冲压钢绝不陌生,在汽车轻量化和提高安全性的大背景下,它在各个车型上的使用比例很频繁地出现在车型安全性能介绍中,是衡量车辆被动安全的黄金标尺之一。因此,各个汽车企业均有意识的逐年提高铝硅镀层热冲压钢在车身上的用量,据不完全统计,2020年仅国内铝硅镀层热冲压钢的需求量就将达到60万吨以上,预测2025年需求量则上升到150万吨以上。
铝硅镀层热冲压钢的原创来源于欧洲,其镀层的结构设计,热冲压的规范以及后续汽车应用上的焊接涂装等方方面面早已在先驱者的多年积累之下形成了逻辑严密的闭环,并形成了全方位的专利保护。基于此,全国乃至全球的铝硅镀层热冲压钢供给是被一二家国外钢铁公司控制的。各个国内车企和他们的零部件供应商不得不承受高昂的钢板价格,国内钢铁公司在无法澄清专利问题之前也没有能力合法合规地进入各车企的采购名单。
——破局——
东北大学联合育材堂(苏州)材料科技有限公司(以下简称育材堂)从研究现有铝硅镀层热冲压钢的弯曲韧性偏低的问题入手,发现了物理上的机理,提出了简单但有效的解决方案,形成一系列韧性明显改善的铝硅镀层热冲压钢的科技创新成果并获得相关专利。这种高韧性铝硅镀层热冲压钢技术得到了行业上下游企业的广泛关注,而育材堂也积极探讨与各方企业的合作模式,以合理的费率将这套专利技术许可给多家钢铁公司生产,并与合作伙伴一起推动在零部件和汽车企业的应用。
为更大范围地分享高韧性铝硅镀层技术带来的红利,东北大学联合育材堂于2019年在中国汽车工程学会提出标准立项申请,联合20余家行业上下游企业共同成立标准工作组,完成了T/CSAE 179-2021《汽车用高韧性热镀铝硅合金镀层热冲压钢板技术要求》。希望通过新标准的建立,系统梳理钢铁企业,热冲压零部件供应商以及汽车公司的铝硅镀层钢板板及零件的生产管控,促进高韧性铝硅镀层热冲压零件的品质提升,扩大其在国内外车型上的应用,从而提升国内汽车行业热冲压材料的应用技术水平。
——探索——
专利技术融入标准,通过标准实施实现创新技术快速推广应用,获得合理经济回报反哺科技创新,这种以合理许可费率进行标准必要专利许可的模式在中国汽车领域属于首创。该模式的建立使得上游的钢铁公司不用付出高额的研发费用即可将技术转化为生产,而新技术带来的性能改善以及成本下降也大大缓解了零部件厂和汽车企业的原材料采购压力。
标准解读:
此次工作组提出的新标准,显然不是众多汽车企业对多年来铝硅镀层热冲压钢使用经验的总结,更不是对现有铝硅镀层热冲压钢标准的一个补缺。此标准标题中的“高韧性”三个字开宗明义的表明,这是一个对现有铝硅镀层热冲压钢的升级宣告。
既然是升级,那大家自然都想知道:升的什么级,升级有什么用,怎么升的级。因此,我们试图通过解读这个标准来回答以下的几个问题:
a)当我们谈论韧性的时候,我们到底在谈论什么?
开门见山的说,这里的韧性是想描述一种汽车零件抵抗变形破坏的能力,或者说在断裂之前零件能发生局部变形的能力,即“断裂应变”的大小。我们应该知道,材料的受力状态不同,断裂应变是完全不同的。例如,在我们熟悉的单向拉伸实验中,试样处于“单向拉伸”(uniaxial tension)的受力状态,是被“拉断”的。
然而,汽车在发生碰撞时,零件几乎不可能是被拉断的,他们大多处于被“折弯”的状态,接近于力学描述的“平面应变”(Plane Strain)的受力状态,也即是说零件是被“折断”的。因此,为正确评价汽车零件抵抗变形破坏的能力,我们需要对不同受力状态下材料的等效断裂应变进行测定。其中,不同的受理状态可以用力学概念“应力三轴度”的数值来表达。下图所示的就是材料的等效应变Y随应力三轴度X变化的曲线。通常情况下,对于高强度钢,我们得到的,几乎总是一条形似字母W的曲线。
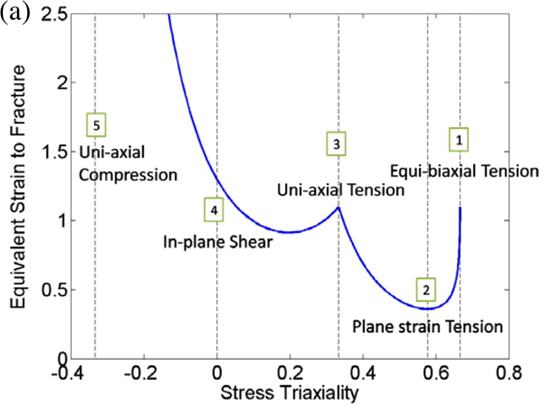
图1:材料等效断裂应变曲线,来源:M. Kõrgesaar et al. International Journal of Solids andStructures, Volume 51, Issues 21–22, 15October 2014, Pages 3752-3761
通过上图可知,我们可以清楚的看到,单向拉伸(uniaxial tension)对应的断裂应变总是位于W曲线的中间高峰上,而平面应变(Plane Strain)对应的断裂应变则落到了W右侧的谷底,要低很多。也就是说,对同一种材料,折断总比拉断更容易(似乎我们天生就知道折断树枝比拉断树枝容易);投射到汽车应用上,产生两件值得思考的事情:
1)对于材料开发者和生产者,片面追求提高热冲压钢的单向拉伸总伸长率,不一定有多大意义;
2)对于材料使用者,如果用单向拉伸总伸长率好坏来评判零件抵抗折弯破坏的能力,是严重高估了,其结果当然是碰撞安全的隐患。
正是基于我们对于热冲用钢断裂应变上的理解,我们发布了新标准。从标准正文的表7中可以看到,新标准中的“总伸长率”并没有显著提升,还是大家熟悉的味道。因此,如果你期待在热冲压状态或烘烤状态下,材料的伸长率能达到10%,你恐怕要失望了。正如我们强调的,我们要的高韧性并不是体现在总伸长率上,而是体现在平面应变状态下的高断裂应变。
平面断裂应变并不容易测量,因此,德国汽车工业协会标准VDA238-100中提供了一个十分好用的近似方法:通过搭建平板三点弯实验获得一个较理想的平面应变条件,并通过测试材料三点弯后的最大弯曲角进而判断材料平面断裂应变的高低。而平面断裂应变可以通过最大弯曲角求得,求得方法见下图。这种方法简单,好用,从而使得VDA最大弯曲角成为工程上表征韧性最理想的性能指标。
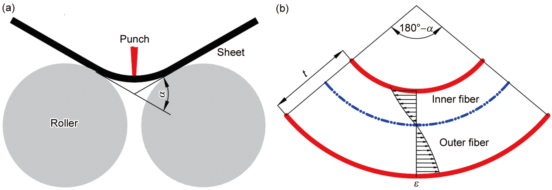
图2:VDA 238-100 弯曲示意图与弯曲过程中的厚度方向应变的分布,来源:易红亮等. 金属学报,第56卷,第4期,2020.04:429~443
b)高韧性的“高”是相对什么韧性而言的?
近年来,越来越多的汽车企业意识到高韧性热冲压钢的重要性,并在自家的标准中提出了对VDA最大弯曲角的要求。如东风汽车标准中提到,当板厚≥1mm时,其轧向和垂直轧向方向的VDA最大弯曲角要不低于70°。BMW则一直要求所有热冲压钢(包括无镀层,铝硅镀层以及锌基镀层等)的VDA最大弯曲角均需达到60°以上。而通用汽车则在2019年之前的热冲压钢材料标准也仅要求VDA最大弯曲角需达到50°以上,并在2019年6月发布的GM全球材料标准GMW14400中对VDA最大弯曲角进行了升级,增加了牌号为HS1300T/950Y-MS-IB的材料规范,要求铝硅镀层热冲压钢的VDA最大弯曲角须达到60°以上,其中“IB”正是Improved Bendability(提升弯曲韧性)的缩写,展示了通用汽车在此领域的前瞻性。
结合汽车企业的需求,新标准中的表10则给出了不同板厚下,高韧性铝硅镀层热冲压钢板在热冲压态和烘烤态的VDA最大弯曲角要求。与现有铝硅镀层热冲压钢比较,通过VDA最大弯曲角的提升,平面断裂应变将有显著的提升(见下图),进而提高了零件抵抗变形破坏的能力以及整车碰撞安全性能。
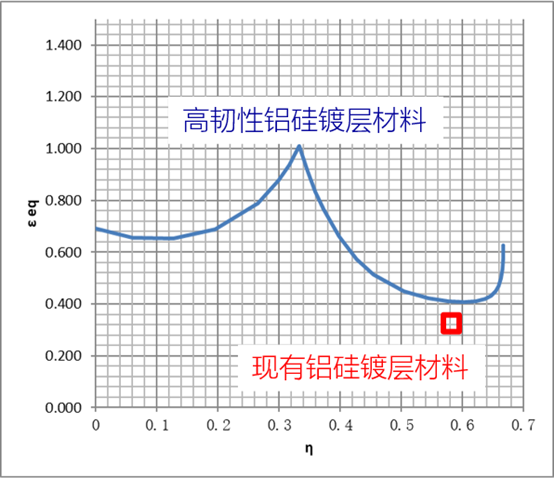
图3:高韧性铝硅镀层热冲压钢的等效断裂应变曲线
c)新标准的高韧性是通过什么获得的?
新标准中的表1至表3分别展示了新材料规范的基板化学成分、非金属夹杂物以及性能要求,显然,基板材料仍为传统的22MnB5,即获取高韧性的秘密不是来自于基板的材料突破。
直觉上,我们很难相信材料整体的韧性改善是镀层的优化导致的,但事实就是这样。先简单说说为何现有铝硅镀层热冲压钢无法突破60°甚至是55°的VDA最大弯曲角门槛。铝硅镀层在热冲压的奥氏体化加热过程中,是会和基体的钢发生相互扩散以及复杂的金属间化合反应,而镀层与基板之间的界面会在该过程中向钢一端推移,形象的说,镀层在加热过程中变厚了。通过显微观察发现,镀层增厚之后,镀层与基板之间的界面靠近镀层一侧为富铝的铁素体,另一侧为几乎不含铝的富碳马氏体,由于界面的推移,未推移前的马氏体中本来均匀分布的碳被“挤压”出来并堆积在界面靠近基体上,形成薄薄的一层高碳马氏体。而高碳马氏体韧性不好是通识,其断裂应变大约只有基体里正常马氏体的1/10。在折弯的受力状态下,这层薄薄的高碳马氏体层又处在应变最大的表面区域,怎能不断?
显然,克服这个问题的关键,在于降低碳在界面上的堆积。怎么降低?在可能的工程方法中,最优美最简单的莫过于减少界面的推移,即镀层的厚度减薄。基于此,新标准中的表5和表8分别规范了热冲压前后高韧性铝硅镀层热冲压钢的镀层厚度,即“钢厂交货状态”(热冲压之前)的单面镀层厚度典型值为10微米以及“热冲压平板或零件”(热冲压之后)的单面镀层厚度典型值为16微米。也就是说,按照新标准的指导,对比热冲压前后的镀层状态,界面的推移距离只有6微米,界面推移效果显著弱于现有铝硅镀层热冲压钢。
新标准规范的高韧性铝硅镀层热冲压钢常被简称为“薄镀层”材料。对比现有产品,这的确是最显著的区别,也是标准中容易被观测和执行的特征。但其内涵,不在于镀层本身有多“薄”,而在于界面推移有多“远”。通过铝硅镀层厚度减薄这一简单有效的办法,热冲压加热过程中镀层与基板直接的界面推移受到限制,高碳马氏体的生成得到控制,最终热冲压零件的韧性将得到显著改善,并将直接贡献于车身轻量化以及整车碰撞安全性提升上。因此,有理由相信,高韧性铝硅镀层热冲压钢将成为未来车身用材发展的一个重要方向,实现在汽车热成形钢领域国人对国际领先技术的追赶和超越。
—标准解读文字来源于东北大学 周澍
导读
——缘起——
汽车用户对铝硅镀层热冲压钢绝不陌生,在汽车轻量化和提高安全性的大背景下,它在各个车型上的使用比例很频繁地出现在车型安全性能介绍中,是衡量车辆被动安全的黄金标尺之一。因此,各个汽车企业均有意识的逐年提高铝硅镀层热冲压钢在车身上的用量,据不完全统计,2020年仅国内铝硅镀层热冲压钢的需求量就将达到60万吨以上,预测2025年需求量则上升到150万吨以上。
铝硅镀层热冲压钢的原创来源于欧洲,其镀层的结构设计,热冲压的规范以及后续汽车应用上的焊接涂装等方方面面早已在先驱者的多年积累之下形成了逻辑严密的闭环,并形成了全方位的专利保护。基于此,全国乃至全球的铝硅镀层热冲压钢供给是被一二家国外钢铁公司控制的。各个国内车企和他们的零部件供应商不得不承受高昂的钢板价格,国内钢铁公司在无法澄清专利问题之前也没有能力合法合规地进入各车企的采购名单。
——破局——
东北大学联合育材堂(苏州)材料科技有限公司(以下简称育材堂)从研究现有铝硅镀层热冲压钢的弯曲韧性偏低的问题入手,发现了物理上的机理,提出了简单但有效的解决方案,形成一系列韧性明显改善的铝硅镀层热冲压钢的科技创新成果并获得相关专利。这种高韧性铝硅镀层热冲压钢技术得到了行业上下游企业的广泛关注,而育材堂也积极探讨与各方企业的合作模式,以合理的费率将这套专利技术许可给多家钢铁公司生产,并与合作伙伴一起推动在零部件和汽车企业的应用。
为更大范围地分享高韧性铝硅镀层技术带来的红利,东北大学联合育材堂于2019年在中国汽车工程学会提出标准立项申请,联合20余家行业上下游企业共同成立标准工作组,完成了T/CSAE 179-2021《汽车用高韧性热镀铝硅合金镀层热冲压钢板技术要求》。希望通过新标准的建立,系统梳理钢铁企业,热冲压零部件供应商以及汽车公司的铝硅镀层钢板板及零件的生产管控,促进高韧性铝硅镀层热冲压零件的品质提升,扩大其在国内外车型上的应用,从而提升国内汽车行业热冲压材料的应用技术水平。
——探索——
专利技术融入标准,通过标准实施实现创新技术快速推广应用,获得合理经济回报反哺科技创新,这种以合理许可费率进行标准必要专利许可的模式在中国汽车领域属于首创。该模式的建立使得上游的钢铁公司不用付出高额的研发费用即可将技术转化为生产,而新技术带来的性能改善以及成本下降也大大缓解了零部件厂和汽车企业的原材料采购压力。
标准解读:
此次工作组提出的新标准,显然不是众多汽车企业对多年来铝硅镀层热冲压钢使用经验的总结,更不是对现有铝硅镀层热冲压钢标准的一个补缺。此标准标题中的“高韧性”三个字开宗明义的表明,这是一个对现有铝硅镀层热冲压钢的升级宣告。
既然是升级,那大家自然都想知道:升的什么级,升级有什么用,怎么升的级。因此,我们试图通过解读这个标准来回答以下的几个问题:
a)当我们谈论韧性的时候,我们到底在谈论什么?
开门见山的说,这里的韧性是想描述一种汽车零件抵抗变形破坏的能力,或者说在断裂之前零件能发生局部变形的能力,即“断裂应变”的大小。我们应该知道,材料的受力状态不同,断裂应变是完全不同的。例如,在我们熟悉的单向拉伸实验中,试样处于“单向拉伸”(uniaxial tension)的受力状态,是被“拉断”的。
然而,汽车在发生碰撞时,零件几乎不可能是被拉断的,他们大多处于被“折弯”的状态,接近于力学描述的“平面应变”(Plane Strain)的受力状态,也即是说零件是被“折断”的。因此,为正确评价汽车零件抵抗变形破坏的能力,我们需要对不同受力状态下材料的等效断裂应变进行测定。其中,不同的受理状态可以用力学概念“应力三轴度”的数值来表达。下图所示的就是材料的等效应变Y随应力三轴度X变化的曲线。通常情况下,对于高强度钢,我们得到的,几乎总是一条形似字母W的曲线。
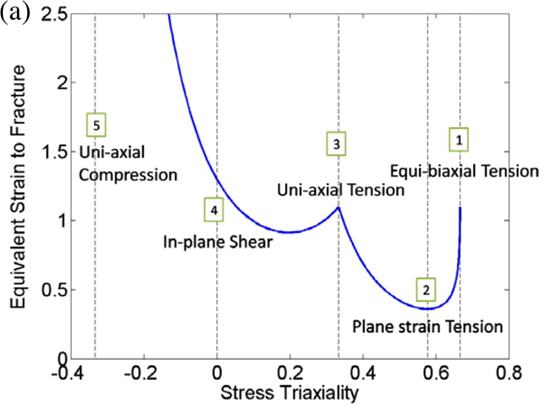
图1:材料等效断裂应变曲线,来源:M. Kõrgesaar et al. International Journal of Solids andStructures, Volume 51, Issues 21–22, 15October 2014, Pages 3752-3761
通过上图可知,我们可以清楚的看到,单向拉伸(uniaxial tension)对应的断裂应变总是位于W曲线的中间高峰上,而平面应变(Plane Strain)对应的断裂应变则落到了W右侧的谷底,要低很多。也就是说,对同一种材料,折断总比拉断更容易(似乎我们天生就知道折断树枝比拉断树枝容易);投射到汽车应用上,产生两件值得思考的事情:
1)对于材料开发者和生产者,片面追求提高热冲压钢的单向拉伸总伸长率,不一定有多大意义;
2)对于材料使用者,如果用单向拉伸总伸长率好坏来评判零件抵抗折弯破坏的能力,是严重高估了,其结果当然是碰撞安全的隐患。
正是基于我们对于热冲用钢断裂应变上的理解,我们发布了新标准。从标准正文的表7中可以看到,新标准中的“总伸长率”并没有显著提升,还是大家熟悉的味道。因此,如果你期待在热冲压状态或烘烤状态下,材料的伸长率能达到10%,你恐怕要失望了。正如我们强调的,我们要的高韧性并不是体现在总伸长率上,而是体现在平面应变状态下的高断裂应变。
平面断裂应变并不容易测量,因此,德国汽车工业协会标准VDA238-100中提供了一个十分好用的近似方法:通过搭建平板三点弯实验获得一个较理想的平面应变条件,并通过测试材料三点弯后的最大弯曲角进而判断材料平面断裂应变的高低。而平面断裂应变可以通过最大弯曲角求得,求得方法见下图。这种方法简单,好用,从而使得VDA最大弯曲角成为工程上表征韧性最理想的性能指标。
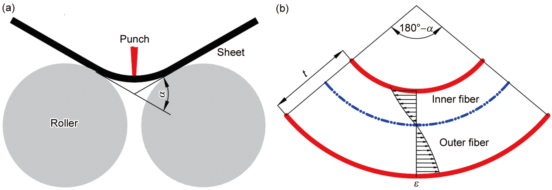
图2:VDA 238-100 弯曲示意图与弯曲过程中的厚度方向应变的分布,来源:易红亮等. 金属学报,第56卷,第4期,2020.04:429~443
b)高韧性的“高”是相对什么韧性而言的?
近年来,越来越多的汽车企业意识到高韧性热冲压钢的重要性,并在自家的标准中提出了对VDA最大弯曲角的要求。如东风汽车标准中提到,当板厚≥1mm时,其轧向和垂直轧向方向的VDA最大弯曲角要不低于70°。BMW则一直要求所有热冲压钢(包括无镀层,铝硅镀层以及锌基镀层等)的VDA最大弯曲角均需达到60°以上。而通用汽车则在2019年之前的热冲压钢材料标准也仅要求VDA最大弯曲角需达到50°以上,并在2019年6月发布的GM全球材料标准GMW14400中对VDA最大弯曲角进行了升级,增加了牌号为HS1300T/950Y-MS-IB的材料规范,要求铝硅镀层热冲压钢的VDA最大弯曲角须达到60°以上,其中“IB”正是Improved Bendability(提升弯曲韧性)的缩写,展示了通用汽车在此领域的前瞻性。
结合汽车企业的需求,新标准中的表10则给出了不同板厚下,高韧性铝硅镀层热冲压钢板在热冲压态和烘烤态的VDA最大弯曲角要求。与现有铝硅镀层热冲压钢比较,通过VDA最大弯曲角的提升,平面断裂应变将有显著的提升(见下图),进而提高了零件抵抗变形破坏的能力以及整车碰撞安全性能。
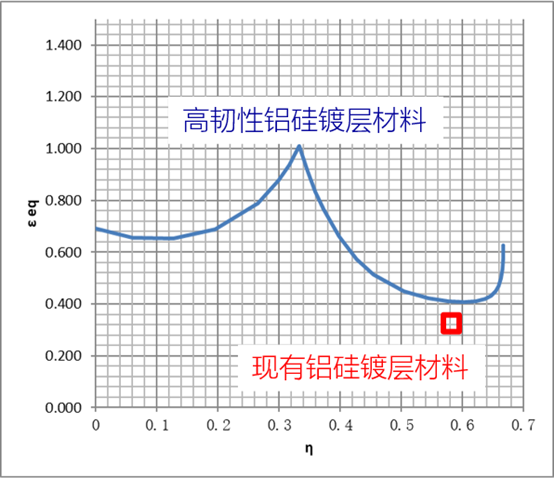
图3:高韧性铝硅镀层热冲压钢的等效断裂应变曲线
c)新标准的高韧性是通过什么获得的?
新标准中的表1至表3分别展示了新材料规范的基板化学成分、非金属夹杂物以及性能要求,显然,基板材料仍为传统的22MnB5,即获取高韧性的秘密不是来自于基板的材料突破。
直觉上,我们很难相信材料整体的韧性改善是镀层的优化导致的,但事实就是这样。先简单说说为何现有铝硅镀层热冲压钢无法突破60°甚至是55°的VDA最大弯曲角门槛。铝硅镀层在热冲压的奥氏体化加热过程中,是会和基体的钢发生相互扩散以及复杂的金属间化合反应,而镀层与基板之间的界面会在该过程中向钢一端推移,形象的说,镀层在加热过程中变厚了。通过显微观察发现,镀层增厚之后,镀层与基板之间的界面靠近镀层一侧为富铝的铁素体,另一侧为几乎不含铝的富碳马氏体,由于界面的推移,未推移前的马氏体中本来均匀分布的碳被“挤压”出来并堆积在界面靠近基体上,形成薄薄的一层高碳马氏体。而高碳马氏体韧性不好是通识,其断裂应变大约只有基体里正常马氏体的1/10。在折弯的受力状态下,这层薄薄的高碳马氏体层又处在应变最大的表面区域,怎能不断?
显然,克服这个问题的关键,在于降低碳在界面上的堆积。怎么降低?在可能的工程方法中,最优美最简单的莫过于减少界面的推移,即镀层的厚度减薄。基于此,新标准中的表5和表8分别规范了热冲压前后高韧性铝硅镀层热冲压钢的镀层厚度,即“钢厂交货状态”(热冲压之前)的单面镀层厚度典型值为10微米以及“热冲压平板或零件”(热冲压之后)的单面镀层厚度典型值为16微米。也就是说,按照新标准的指导,对比热冲压前后的镀层状态,界面的推移距离只有6微米,界面推移效果显著弱于现有铝硅镀层热冲压钢。
新标准规范的高韧性铝硅镀层热冲压钢常被简称为“薄镀层”材料。对比现有产品,这的确是最显著的区别,也是标准中容易被观测和执行的特征。但其内涵,不在于镀层本身有多“薄”,而在于界面推移有多“远”。通过铝硅镀层厚度减薄这一简单有效的办法,热冲压加热过程中镀层与基板直接的界面推移受到限制,高碳马氏体的生成得到控制,最终热冲压零件的韧性将得到显著改善,并将直接贡献于车身轻量化以及整车碰撞安全性提升上。因此,有理由相信,高韧性铝硅镀层热冲压钢将成为未来车身用材发展的一个重要方向,实现在汽车热成形钢领域国人对国际领先技术的追赶和超越。
—标准解读文字来源于东北大学 周澍
举报 0
收藏 0
分享 218
-
冲压技术在电机叠片制造的应用
2024-09-06 -
车身零部件包边质量控制要点
2024-09-05 -
轻量化技术——热汽胀形工艺技术解析
2024-09-04 -
高强板车身件冲压技术
2024-09-02
最新资讯
-
全球产业链聚沪 共探双碳新路径 SNEC
2025-04-18 18:05
-
柯马签订具有约束力的协议收购 Autom
2025-04-17 13:01
-
高效协同新范式:比亚迪叉车领创智能
2025-04-17 10:04
-
埃马克德国总部迎来中国社科院工业经
2025-04-15 09:40
-
埃马克这项全新应用即将在CIMT惊艳首
2025-04-15 09:37