康耐视In-Sight 7802视觉系统帮助博世解决汽车电机绕线检测问题
2021-11-08 12:08:38· 来源:汽车制造网
客户:博世汽车部件有限公司 行业:汽车零部件 解决方案:康耐视In-Sight 7802视觉系统挑战 ▪ 未到达相机的拍摄角度拍照,会造成拟合的检测区域缩小,影响对于铜线伸出比例的判断; ▪ 表面凹坑出现在弯钩出,会影响弯钩的铜线有无判断
客户:博世汽车部件有限公司
行业:汽车零部件
解决方案:康耐视In-Sight® 7802视觉系统
挑战
▪ 未到达相机的拍摄角度拍照,会造成拟合的检测区域缩小,影响对于铜线伸出比例的判断;
▪ 表面凹坑出现在弯钩出,会影响弯钩的铜线有无判断;
▪ 首线过短无法通过blob宽度判断;
效果
▪ 检测高效,可准确地验证各种绕线缺陷;
▪ 操作简捷,初学者上手快,产品稳定性强;
▪ 良品率提高到97%,生产效率和经济效益明显改观;
博世集团是全球领先的技术和服务供应商,在全球拥有约400000名员工,集团在2019财政年度创造了777亿欧元的销售业绩。博世业务划分为四个业务领域,涵盖汽车与智能交通技术、工业技术、消费品以及能源与建筑技术领域。作为全球领先的汽车技术和服务供应商,博世将车辆技术专业知识与硬件、软件和服务相结合,提供完整的出行解决方案。其中,博世汽车部件有限公司主要提供汽车零配件研发制造和售后服务,其产品线涉及汽车电子驱动和起动机/发电机、底盘系统控制装置、汽车电子设备、火花塞等。
汽车电机绕线检测不稳定,很难精确定位
电机是汽车上的重要部件,而电机绕线是电机的关键工艺。任何缠绕不准确的地方都会对电机效率产生负面影响,且难以发现。因此,在电机生产过程中,必须对电机绕线进行缺陷检测,以保证最后成品的质量达到要求。
在博世的汽车电机产线中,应用了大量的视觉技术来检测电机绕线的质量。但是,在生产过程中,博世的生产工程师们发现一系列的检测难题,传统视觉技术难以应对。
1)绕线机的剪线方式是通过应力扯断,会造成回缩现象,从而导致首线过短无法通过blob宽度判断。
2)工件在夹具上经过绕线机绕线,绕线完后会回摆到拍照位置。由于设备的不稳定性,导致每次回摆的角度不一致,在视野内的位置会存在一定的高低偏差。未到达相机的拍摄角度拍照,会造成拟合的检测缩小,影响对于铜线伸出比例的判断。
3)在相机拍照时,回摆还未结束,造成相机的图像焦距不清晰。绕线挂钩表面凹痕会影响铜线斑点的宽度判断,而单根铜线的像素仅30左右。如果表面有其它的凹坑就会超过正常的范围。
4)检测时还需要对弯钩处的铜线进行判断,如果前面的工艺不稳定,就会导致弯钩处有电木未清理干净,影响检测判断。
5)若两根铜线同时存在一个检测框内,而另一个检测框没有铜线。此时通过拟合工具拟合斑点最大外接矩形,若是两根铜线并在一起,则无法去判断产品是否合格。
“这些诸如铜线表面亮度反光、铜线绕线不规则、旋转角度未到达相机拍摄位置等因素都会造成检测的不稳定。”博世的生产工程师指出,“如果问题得不到解决,将无法满足检测要求,我们需要人工进行处理,这就直接影响产线的生产效率。”
性能卓越的康耐视In-Sight 7802视觉系统
面对这些技术挑战,博世需要一家能提供算法功能齐备和完整解决方案的视觉技术供应商,来帮助解决检测难题。
“我们寻找解决方案提供商时,考虑的最重要因素是供应商的过往项目案例、公司实力、售后服务的响应速度、产品的价格及质量和履行约定及守信能力。”博世的生产工程师表示,“经过调研和同行推荐,我们认为康耐视公司作为全球领先的机器视觉厂商,其强大的技术能力和丰富的设备部署经验,能为博世的检测难题提供解决方法。而且,博世与康耐视公司合作已达10年之久,公司的很多产线上都应用了康耐视产品,我们彼此都很了解和信任。”
于是,博世就联系上了康耐视,并把相关技术需求进行了沟通交流。在接到博世的咨询后,康耐视就第一时间派出工程师团队到现场进行考察。根据调研结果,康耐视推荐了In-Sight 7802视觉解决方案,并提供了检测验证方案。优化后的检测方案如下:
1)由于工件位置可能存在的偏差会改变图案模型区域,从而使得到的坐标产生偏差,造成检测不稳定。于是就放弃传统的FindPatterns图案定位方式,选择边定位的方式。分别以工件上两条高对比度的边定位X轴Y轴,最终达到精确定位的效果。此定位方法可不受工件整体左右、上下移动的影响。
2)建立自定义区域分布在挂钩外侧,当有铜线伸出进入外部检测区域时,检测工具即可判断铜线不良,也可调整外部区域增加稳定性。
3)若两个斑点分别存在于两个检测框之内,两个区域内分别可以找到对应斑点,则判断存在挂钩,通过视觉计算工具就可计算出两斑点之间最远的距离。当只存在一个挂钩时,该挂钩位于另一个检测框之间,即A,B检测区域。依旧能找到A,B两点,且距离阈值也在正常值,这时可通过斑点之间的最远距离,判断此时存在几个挂钩。只有一根铜线时,两斑点的最远距离会远小于两根铜线存在时的值,合理设置铜线最远距离阈值,即可准确判断此种情况。
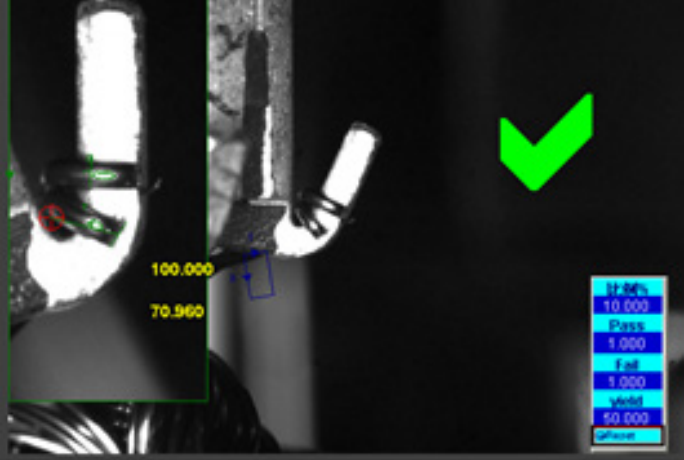
图1 通过对检测区域的精准定位,选取不同的斑点工具检 测是否存在斑点判断挂钩A,B有无及长度比例是否10%
4)若两根铜线同时存在同一个检测框内时,另一个检测框则没有铜线。此时通过拟合工具拟合斑点最大外接矩形。如果两根铜线并在一起,外接矩形面积将远大于一根铜线存在时的面积,此时即可判断产品合格,在可视化界面可设置阈值。
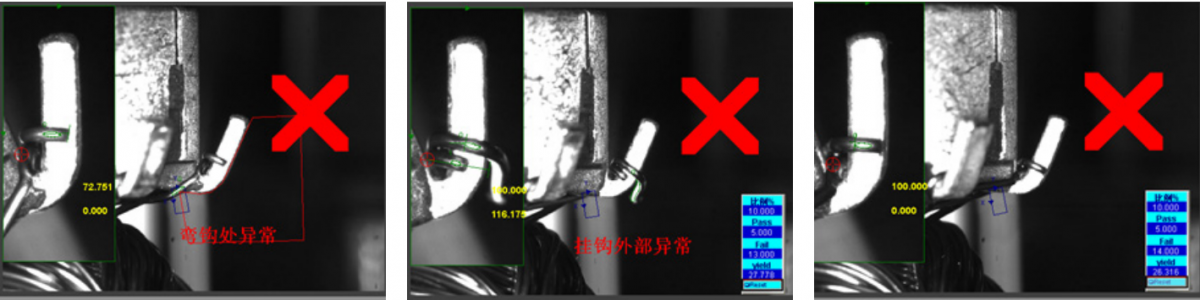
图2 弯钩检测不合格 图3 铜线超出挂钩,检测不合格 图4 缺失一根铜线,检测不合格
按照康耐视的方案,博世就安排了现场验证。当看到测试结果时,博世的生产工程师惊喜地发现,凭借康耐视强大的In-Sight 7802视觉系统,原来困扰他们的诸多检测难题不但得到成功解决,而且还实现了产品的质量追溯。
而卓越的PatMax® 图像匹配技术作为康耐视In-Sight 7802视觉系统的最主要检测工具,给博世的生产工程师们留下了深刻的印象。
“PatMax只需简单设置就可以轻松完成工作,凭借极快的采集和行业领先的视觉工具,In-Sight 7802 能够执行快速、精确的检测,可准确地验证各种绕线缺陷。”博世的生产负责人表示,“In-Sight 7802是全功能的强大视觉系统,它的出色表现赢得了我们的认可,于是决定选择该方案来解决电机绕线检测问题。”
良品率提升到97%,经济效益显著
目前,依靠康耐视的In-Sight 7802视觉系统,博世的电机绕线检测稳定性大为提高。而且In-Sight Explorer简洁易用的界面,并配合合适的光源,从而达到了超高的检测合格率。博世很快就实现了电机绕线的高效检测,不但节省了人力而且大幅度提升了生产速度。“良品率从原先的86%提高到97%,并直接带动了生产效率的增长。”博世的生产负责人算了一笔账,表明投资In-Sight 7802视觉系统让经济效益得到明显改观,“每天由于消除未绕线而节省的成本估计为100美元,每年总计10万美元。加上降低产品召回所节省的成本,以及处理消费者投诉的成本,公司每年将节省20万美元!”

图5 现场图片
通过一段时间的实际运行,In-Sight 7802视觉系统的操作简捷性,让博世的生产工程师们交口称赞。“ 它不用编程,只需要简单的拖拉工具,就可以实现检测。且强大的工具库可以满足大部分的项目需求,软件操作简单,还提供案例教程使初学者上手快。产品的稳定性极好,在十分恶劣的环境也可以稳定工作。”
而康耐视技术团队的高水平服务,更是给博世留下了深刻的印象。“在与康耐视合作期间,有一次晚上 11点,由于设备不稳定出现检测问题,当时生产十分紧急。为了及时解决问题,我们就打电话联系了康耐视。”博世的生产工程师感慨地回忆说,“康耐视马上就连夜安排了技术服务人员进厂调试,解决了火烧眉睫的检测问题。康耐视团队的高度服务意识和爱岗敬业态度真是令人钦佩。”
“基于康耐视先进视觉系统的质量管控措施得到了我们的高度认可,”博世的生产负责人最后指出,“ 如今汽车的需求量越来越大,汽车器件产量和质量都至关重要,采用康耐视先进视觉系统后,我们同时解决了这两大问题,还降低了生产成本,保证了高质量的产品品质和对客户的承诺。康耐视为公司提供了不可估量的价值,是值得信赖的合作伙伴!”
行业:汽车零部件
解决方案:康耐视In-Sight® 7802视觉系统
挑战
▪ 未到达相机的拍摄角度拍照,会造成拟合的检测区域缩小,影响对于铜线伸出比例的判断;
▪ 表面凹坑出现在弯钩出,会影响弯钩的铜线有无判断;
▪ 首线过短无法通过blob宽度判断;
效果
▪ 检测高效,可准确地验证各种绕线缺陷;
▪ 操作简捷,初学者上手快,产品稳定性强;
▪ 良品率提高到97%,生产效率和经济效益明显改观;
博世集团是全球领先的技术和服务供应商,在全球拥有约400000名员工,集团在2019财政年度创造了777亿欧元的销售业绩。博世业务划分为四个业务领域,涵盖汽车与智能交通技术、工业技术、消费品以及能源与建筑技术领域。作为全球领先的汽车技术和服务供应商,博世将车辆技术专业知识与硬件、软件和服务相结合,提供完整的出行解决方案。其中,博世汽车部件有限公司主要提供汽车零配件研发制造和售后服务,其产品线涉及汽车电子驱动和起动机/发电机、底盘系统控制装置、汽车电子设备、火花塞等。
汽车电机绕线检测不稳定,很难精确定位
电机是汽车上的重要部件,而电机绕线是电机的关键工艺。任何缠绕不准确的地方都会对电机效率产生负面影响,且难以发现。因此,在电机生产过程中,必须对电机绕线进行缺陷检测,以保证最后成品的质量达到要求。
在博世的汽车电机产线中,应用了大量的视觉技术来检测电机绕线的质量。但是,在生产过程中,博世的生产工程师们发现一系列的检测难题,传统视觉技术难以应对。
1)绕线机的剪线方式是通过应力扯断,会造成回缩现象,从而导致首线过短无法通过blob宽度判断。
2)工件在夹具上经过绕线机绕线,绕线完后会回摆到拍照位置。由于设备的不稳定性,导致每次回摆的角度不一致,在视野内的位置会存在一定的高低偏差。未到达相机的拍摄角度拍照,会造成拟合的检测缩小,影响对于铜线伸出比例的判断。
3)在相机拍照时,回摆还未结束,造成相机的图像焦距不清晰。绕线挂钩表面凹痕会影响铜线斑点的宽度判断,而单根铜线的像素仅30左右。如果表面有其它的凹坑就会超过正常的范围。
4)检测时还需要对弯钩处的铜线进行判断,如果前面的工艺不稳定,就会导致弯钩处有电木未清理干净,影响检测判断。
5)若两根铜线同时存在一个检测框内,而另一个检测框没有铜线。此时通过拟合工具拟合斑点最大外接矩形,若是两根铜线并在一起,则无法去判断产品是否合格。
“这些诸如铜线表面亮度反光、铜线绕线不规则、旋转角度未到达相机拍摄位置等因素都会造成检测的不稳定。”博世的生产工程师指出,“如果问题得不到解决,将无法满足检测要求,我们需要人工进行处理,这就直接影响产线的生产效率。”
性能卓越的康耐视In-Sight 7802视觉系统
面对这些技术挑战,博世需要一家能提供算法功能齐备和完整解决方案的视觉技术供应商,来帮助解决检测难题。
“我们寻找解决方案提供商时,考虑的最重要因素是供应商的过往项目案例、公司实力、售后服务的响应速度、产品的价格及质量和履行约定及守信能力。”博世的生产工程师表示,“经过调研和同行推荐,我们认为康耐视公司作为全球领先的机器视觉厂商,其强大的技术能力和丰富的设备部署经验,能为博世的检测难题提供解决方法。而且,博世与康耐视公司合作已达10年之久,公司的很多产线上都应用了康耐视产品,我们彼此都很了解和信任。”
于是,博世就联系上了康耐视,并把相关技术需求进行了沟通交流。在接到博世的咨询后,康耐视就第一时间派出工程师团队到现场进行考察。根据调研结果,康耐视推荐了In-Sight 7802视觉解决方案,并提供了检测验证方案。优化后的检测方案如下:
1)由于工件位置可能存在的偏差会改变图案模型区域,从而使得到的坐标产生偏差,造成检测不稳定。于是就放弃传统的FindPatterns图案定位方式,选择边定位的方式。分别以工件上两条高对比度的边定位X轴Y轴,最终达到精确定位的效果。此定位方法可不受工件整体左右、上下移动的影响。
2)建立自定义区域分布在挂钩外侧,当有铜线伸出进入外部检测区域时,检测工具即可判断铜线不良,也可调整外部区域增加稳定性。
3)若两个斑点分别存在于两个检测框之内,两个区域内分别可以找到对应斑点,则判断存在挂钩,通过视觉计算工具就可计算出两斑点之间最远的距离。当只存在一个挂钩时,该挂钩位于另一个检测框之间,即A,B检测区域。依旧能找到A,B两点,且距离阈值也在正常值,这时可通过斑点之间的最远距离,判断此时存在几个挂钩。只有一根铜线时,两斑点的最远距离会远小于两根铜线存在时的值,合理设置铜线最远距离阈值,即可准确判断此种情况。
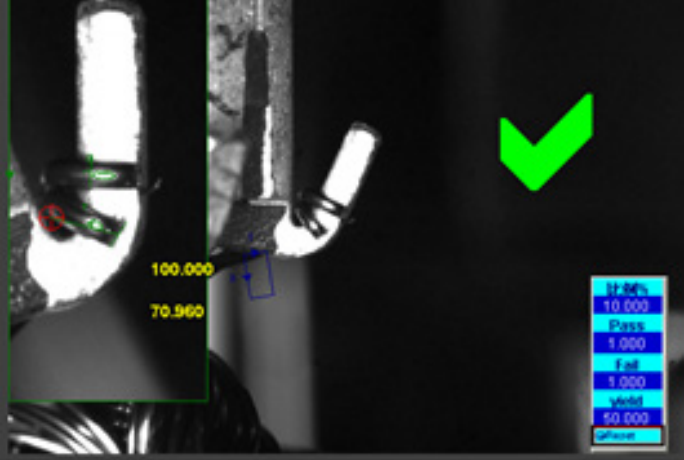
图1 通过对检测区域的精准定位,选取不同的斑点工具检 测是否存在斑点判断挂钩A,B有无及长度比例是否10%
4)若两根铜线同时存在同一个检测框内时,另一个检测框则没有铜线。此时通过拟合工具拟合斑点最大外接矩形。如果两根铜线并在一起,外接矩形面积将远大于一根铜线存在时的面积,此时即可判断产品合格,在可视化界面可设置阈值。
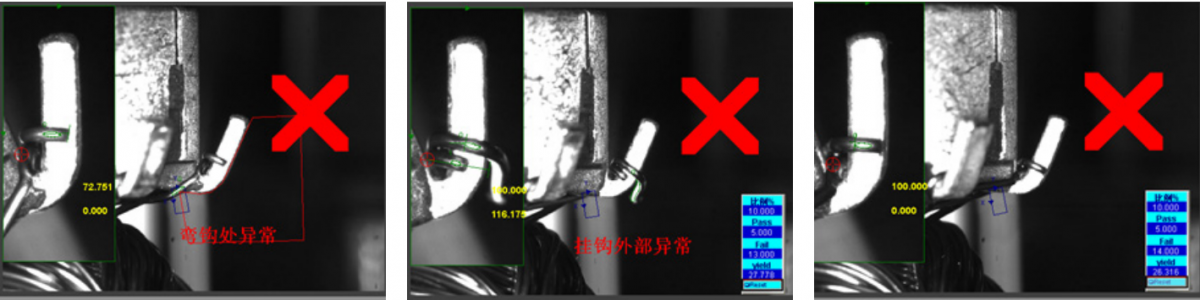
图2 弯钩检测不合格 图3 铜线超出挂钩,检测不合格 图4 缺失一根铜线,检测不合格
按照康耐视的方案,博世就安排了现场验证。当看到测试结果时,博世的生产工程师惊喜地发现,凭借康耐视强大的In-Sight 7802视觉系统,原来困扰他们的诸多检测难题不但得到成功解决,而且还实现了产品的质量追溯。
而卓越的PatMax® 图像匹配技术作为康耐视In-Sight 7802视觉系统的最主要检测工具,给博世的生产工程师们留下了深刻的印象。
“PatMax只需简单设置就可以轻松完成工作,凭借极快的采集和行业领先的视觉工具,In-Sight 7802 能够执行快速、精确的检测,可准确地验证各种绕线缺陷。”博世的生产负责人表示,“In-Sight 7802是全功能的强大视觉系统,它的出色表现赢得了我们的认可,于是决定选择该方案来解决电机绕线检测问题。”
良品率提升到97%,经济效益显著
目前,依靠康耐视的In-Sight 7802视觉系统,博世的电机绕线检测稳定性大为提高。而且In-Sight Explorer简洁易用的界面,并配合合适的光源,从而达到了超高的检测合格率。博世很快就实现了电机绕线的高效检测,不但节省了人力而且大幅度提升了生产速度。“良品率从原先的86%提高到97%,并直接带动了生产效率的增长。”博世的生产负责人算了一笔账,表明投资In-Sight 7802视觉系统让经济效益得到明显改观,“每天由于消除未绕线而节省的成本估计为100美元,每年总计10万美元。加上降低产品召回所节省的成本,以及处理消费者投诉的成本,公司每年将节省20万美元!”

图5 现场图片
通过一段时间的实际运行,In-Sight 7802视觉系统的操作简捷性,让博世的生产工程师们交口称赞。“ 它不用编程,只需要简单的拖拉工具,就可以实现检测。且强大的工具库可以满足大部分的项目需求,软件操作简单,还提供案例教程使初学者上手快。产品的稳定性极好,在十分恶劣的环境也可以稳定工作。”
而康耐视技术团队的高水平服务,更是给博世留下了深刻的印象。“在与康耐视合作期间,有一次晚上 11点,由于设备不稳定出现检测问题,当时生产十分紧急。为了及时解决问题,我们就打电话联系了康耐视。”博世的生产工程师感慨地回忆说,“康耐视马上就连夜安排了技术服务人员进厂调试,解决了火烧眉睫的检测问题。康耐视团队的高度服务意识和爱岗敬业态度真是令人钦佩。”
“基于康耐视先进视觉系统的质量管控措施得到了我们的高度认可,”博世的生产负责人最后指出,“ 如今汽车的需求量越来越大,汽车器件产量和质量都至关重要,采用康耐视先进视觉系统后,我们同时解决了这两大问题,还降低了生产成本,保证了高质量的产品品质和对客户的承诺。康耐视为公司提供了不可估量的价值,是值得信赖的合作伙伴!”
举报 0
收藏 0
分享 103
-
柯马签订具有约束力的协议收购 Automha
2025-04-17 -
高效协同新范式:比亚迪叉车领创智能搬运革新
2025-04-17 -
高歌猛进,奔赴“双碳”——比亚迪叉车助力轮胎
2025-04-10 -
果栗智造磁悬浮技术赋能汽车制造:破解行业痛点
2025-04-03
编辑推荐
最新资讯
-
全球产业链聚沪 共探双碳新路径 SNEC
2025-04-18 18:05
-
柯马签订具有约束力的协议收购 Autom
2025-04-17 13:01
-
高效协同新范式:比亚迪叉车领创智能
2025-04-17 10:04
-
埃马克德国总部迎来中国社科院工业经
2025-04-15 09:40
-
埃马克这项全新应用即将在CIMT惊艳首
2025-04-15 09:37