汽车覆盖件冲压生产车间的规划及设计
覆盖件冲压生产具有规模化、成批生产、多品种化的特点;冲压车间、冲压设备和冲压生产线一次性投资大,但适应产品发展变化的通用性较强,产品换型只需模具变化,设备可以通用。冲压生产是一项规模效益递增型的产业,冲压车间规划要立足于长远和未来发展。对于整车厂来说,覆盖件冲压生产车间的规划与设计显得尤为重要。
概述
覆盖件冲压生产具有规模化、成批生产、多品种化的特点;冲压车间、冲压设备和冲压生产线一次性投资大,但适应产品发展变化的通用性较强,产品换型只需模具变化,设备可以通用。冲压生产是一项规模效益递增型的产业,冲压车间规划要立足于长远和未来发展。对于整车厂来说,覆盖件冲压生产车间的规划与设计显得尤为重要。
覆盖件冲压生产工艺流程
卷料→开卷剪切或落料(包括开卷、清洗、校平、剪切或落料、堆垛)→冲压成形(包括拆垛、清洗、涂油、板料对中、上料、冲压成形、取件)→检验→装入工位器具→入库,如图1所示。
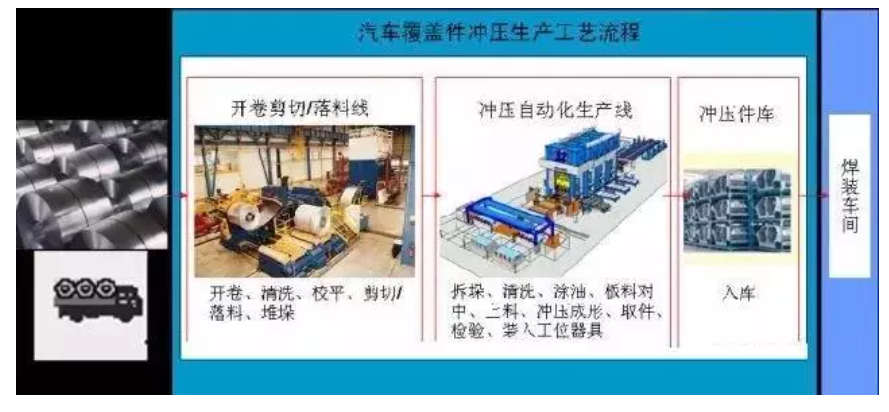
主要规划内容
汽车覆盖件冲压车间规划的主要内容包括冲压车间工艺设计分析、生产设备及生产线选择、辅助设备(线)选择、总图设计、车间平面布置及功能区域设计、厂房设计等。
规划原则
汽车覆盖件冲压车间规划是汽车整车厂四大工艺工厂规划的重要内容之一,应遵循“精益化”的设计原则,高质量、高效率、低投入。采用经济、合理、实用、与生产纲领和生产批量相适应的先进技术,采用高性价比的工艺装备。
规划前提确定
产品类型:轿车或卡车大中型覆盖件和关键梁类结构件;
生产纲领:以10万辆/年生产纲领为例;400辆/天;
工作制度:250天/年,2班/天,16h;
产品种类及内外制冲压件确定:整车厂一般以生产白车身大型内外覆盖件及关键梁类结构件为主,此类件为内制件。其它件由外部供应商协作生产,此类件为外制件。
内制件的确定原则
(1)车身的核心零部件;
(2)高附加值的零部件;
(3)车身外表面覆盖件;
(4)堆垛、运输较困难的大中型内覆盖件;
(5)尺寸精度要求高的关键梁类结构件。
覆盖件冲压车间工艺设计分析
以整车厂只生产内制件为设计前提,规划整车厂的冲压车间。
汽车覆盖件冲压生产线分类及主要生产零件
(1)单机联线冲压生产线分类,见表1。
表1 单机联线冲压生产线分类(仅供参考)
序号 |
分类 |
参考标准 |
主要生产零件 |
备注 |
1 |
超大型线 |
工作台长度>4260mm (5000t≤压机吨位≤9000t) |
侧围、顶盖、车门内外板(一模四件)等 |
自动化线 |
2 |
大型线 |
3270mm<工作台长度≤4260mm (3000t≤压机吨位<5000t) |
翼子板、发动机罩板、行李箱盖板、车门内外板(一模双件)等 |
自动化线 |
3 |
中型线 |
2650mm<工作台长度≤3270mm (1600t≤压机吨位<3000t) |
门槛、B柱、左右前纵梁、铰链加强板、顶盖加强梁等 |
自动化线 或手工线 |
4 |
小型线 |
工作台长度≤2650mm (315t≤压机吨位<1600t) |
加强板、铰链、横梁、减震器支座等 |
自动化线 或手工线 |
注:工作台长度为垂直于送料方向。
(2)多工位压力机线分类,见表2。
表2 多工位压力机线分类(仅供参考)
序号 |
分类 |
参考标准 |
主要生产零件 |
备注 |
1 |
超大型线 |
工位间距>2200mm |
侧围、顶盖、车门、翼子板等(一模双件) |
自动化线 |
2 |
大型线 |
1800mm<工位间距≤2200mm |
翼子板、发动机盖、后盖,门内板、门外板等 |
自动化线 |
3 |
中型线 |
1200mm<工位间距≤1800mm |
门槛、铰链加强板,B柱,车顶框架等 |
自动化线 |
4 |
小型线 |
工位间距≤1200mm |
加强板,横梁,铰链等 |
自动化线 |
注:表中是按照多工位压机工位中心至工位中心的最大工位间距分类。
冲压件工艺设计
典型件工艺:以轿车侧围外板为例:开卷落料→拉延成形→修边冲孔→修边成形冲孔→修边成形冲孔→检验→装入工位器具。
按照冲压线分类并根据零件结构特点、零件大小和工艺特点,大型内外覆盖件规划在超大型或大型冲压生产线上生产,关键梁类结构件规划在中小型多工位压力机或中型冲压线上生产。
覆盖件冲压车间生产线负荷计算及影响因素
每h冲程次数GSPH(Gross Strokes Per Hour)
生产线年冲程总数与年运行时间的比值,即年平均每h冲程次数。
生产线负荷计算公式
需求冲程数:冲压线承担的车型所需求的冲程数,需求冲程数=生产线模具组数(冲程/辆)×年生产纲领(包括备品数);
产能冲程数:冲压线所能提供的有效冲程数,产能冲程数=每h冲程次数×年工作天数×每天工作时间;
上述冲压生产线负荷计算公式可用于已建工厂实际生产线的负荷平衡和生产能力计算,也可以用于新建冲压车间时计算所需要冲压生产线数量及一条冲压线所承担的品种数或模具组数。
对冲压生产来说,提高h冲程次数GSPH、缩短换模时间ADCT,对提高冲压线的生产能力具有重要意义。
影响每h冲程次数GSPH主要因素
平均换模时间ADCT;品种数(模具组数);管理方面停台时间;模具和设备故障时间;工序数多少;冲压线固有属性(设计能力、额定能力)。
影响换模时间ADCT的主要因素
快速换模系统(模具自动夹紧或手动夹紧);首台压机形式(单动、双动);模具闭合高度;移动工作台形式(一字型、T字型、单、双工作台);设备、模具状态;联线调试及首件确认时间;工序数多少等。
覆盖件冲压车间设备及生产线选择
根据生产纲领和生产规模,结合所要生产品种的特点、质量要求、投资、成本,以及覆盖件各种冲压设备和冲压线的形式和特点等因素,选择经济、合理、实用、与生产纲领和生产批量相适应的冲压车间工艺设备和冲压生产线形式。
各种形式汽车覆盖件冲压线对比分析
几种主要形式的覆盖件冲压生产线的对比分析见表3。
表3 冲压线对比分析表
通过分析可以看出,机器人线和机械手线适合于对传统压力机线的改造,机器人线由于投资少,灵活性和柔性好,适合于一般生产规模的生产线选用,随着机器人技术的不断发展,机器人冲压线的生产效率也会越来越高。
由于大型多工位冲压生产线投资较大、生产线柔性差、维修维护费用高、维修复杂、对模具要求较高、模具复杂等特点,适合于较大规模的生产。
目前,单臂式和双臂式快速横杆式机械手自动化冲压线是比较好的冲压自动化解决方案,特别是单臂式快速横杆式机械手自动化冲压线,投资适中,效率较高、柔性较好,以较高的性价比,在国内各大自主体系整车厂中广泛采用。
汽车覆盖件冲压生产线设备组合和配置
(1)压力机吨位及工作台面选择。
根据所生产的零件大小不同,特别是以轿车整体侧围为代表,综合考虑一模双件或一模四件工艺、冲压成形力、冲压工序数、压力机结构形式等因素,超大型压力机生产线一般首台压机为1600~2400t,后续压力机吨位一般为首台压力机的二分之一左右,一般为800~1200t,压力机数量一般为4~6台。压力机工作台面可根据整体侧围模具大小,车门、翼子板一模多件模具大小选择,一般为4500mm×2400mm左右。
(2)冲压生产线设备组合。
表4是超大型和大型压力机生产线设备组合比较,超大型和大型压力机生产线设备的组合一般有7种方式。
1)首台多连杆双动压力机,后面配3~5台偏心传动单动机械压力机,拉延后的零件需要翻转180度,再送到下序,影响整线生产节拍,生产效率低,已逐渐被取代。
2)首台多连杆传动单动机械压力机,带数控拉深垫,后面配3~5台偏心传动单动机械压力机,投资适中,较为实用。
3)首台多连杆传动单动机械压力机,带数控拉深垫,后面配3~5台多连杆传动单动机械压力机,带数控拉深垫,投资较大,部分功能过剩。
4)首台液压机,带数控拉深垫,后面配3~5台偏心传动单动机械压力机,混合压力机生产线,投资少,但生产效率较低。
5)4~6台液压机生产线,带数控拉深垫。投资少,但效率低,适合中小批量生产。
6)4~6台伺服压力机生产线,效率高,冲压件质量好,节能环保,投资较大,是冲压生产线的发展趋势。
7)大型多工位压力机生产线,效率高,投资大,对模具要求高,国内较少采用,是冲压生产线的发展趋势
表4 超大型和大型压力机生产线设备组合比较
冲压车间总图设计
冲压车间总图设计以物流流向为主线,遵循”一个流”的设计原则,冲压车间位置一般与焊装车间相邻,与焊装车间组成联合厂房,冲压与焊装车间之间一般设置冲压件库。冲压、焊装、涂装、总装四大工艺车间的位置关系如图2所示。
图2 冲压车间位置
覆盖件冲压车间工艺平面布置及厂房设计选择
开卷落料(剪切)车间
(1)开卷落料(剪切)车间工艺平面布置及功能区域。
开卷落料(剪切)车间功能区域一般划分为卷料存放区、开卷线生产作业区、毛坯周转存放区、模具存放区等。平面布置如图3所示,根据需要可布置一条开卷剪切线、一条开卷落料线等工艺设备,布置天车、转运车、毛坯翻转机等辅助设备。
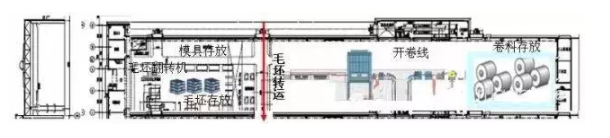
(2)开卷落料(剪切)车间与冲压车间平面布置方式。
如果整车厂冲压件毛坯自制,开卷落料(剪切)线在冲压厂房内的布置主要有两种方式,一种是开卷落料(剪切)线厂房与冲压线厂房平行布置,均为横跨,如图4所示。另一种是与冲压生产线厂房垂直布置,如图5所示,即冲压线厂房为横跨,开卷落料(剪切)线厂房为纵跨。
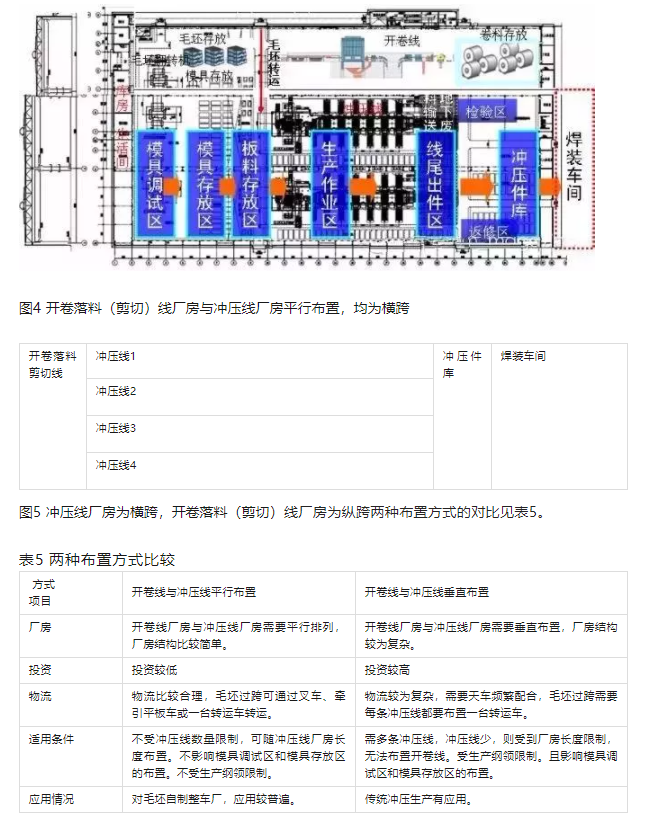
通过对比,冲压车间开卷线与冲压线平行布置,开卷落料(剪切)线厂房与冲压线厂房平行布置,均为横跨的布置方式较为合理。
另外,覆盖件毛坯准备也可以通过组建合资或独资的毛坯加工配送公司,与钢厂形成战略合作伙伴关系,在整车厂附近建设,或与整车厂冲压车间建设联合厂房,规划开卷剪切线和开卷落料线,形成规模化生产和专业化生产,形成毛坯的区域性供应。国内很多汽车和钢铁企业已广泛采用这种方式。
(3)开卷落料(剪切)车间厂房。
开卷落料(剪切)车间厂房宽度一般为24~30m,长度按功能区域确定。
冲压车间
(1)冲压车间工艺平面布置及功能区域
覆盖件冲压车间的功能区域一般划分为模具调试维修区、模具存放区、板料存放区、生产作业区(生产线)、线尾出件区、检验区、冲压件返修区、冲压件库等。冲压车间一般与焊装车间相邻形成联合厂房,两者之间布置冲压件库,冲压车间的工艺平面布置及功能区域示意见图6。
图6 冲压车间工艺平面布置及功能区域
1)模具调试维修区:用于模具的日常维护、维修、保养和调试。模修区的布置有两种方式:
一种是与冲压线布置在同一跨内的一端,靠近模具存放区,要考虑模具上下模打开后的占地面积和调试材料的存放面积,这种布置方式可以根据模修量大小,模修量大的需要每条冲压线一端都要布置模修区,如图6所示。模修量小的,可以布置在模具维修量大的生产线一跨内,一般与最大吨位的生产线在一跨厂房内。
另一种是布置在与冲压线跨平行的独立一跨内,即与冲压线跨平行的横跨,几条冲压线的模具共用模具调试维修区,各条线内需要维修的模具通过过跨转运车转运到模修区内,如图7所示。
根据需要,模具调试维修区一般配有调试压力机、研配压力机、模具清洗机、天车、转运车及部分机加设备和焊接设备。设置用于气动或电动维修工具用的压缩空气接头和动力插座。附近设置模具、设备备件库。调试压力机与冲压线首台压力机的设备参数基本一致,研配压力机一般为200~300t的液压机。模具维修区的起重设备(天车)按大于最大模具重量配置,并且带有副钩,副钩的吨位要大于最大模具的上模重量。
图7 冲压车间工艺平面布置及功能区域(模修区独立一跨,横向布置)
2)模具存放区:用于模具的存放,大型模具一般直接存放在地坪上,下面垫枕木或加防护层的钢轨,存放高度一般不超过2层,模具运输采用电动平板车和起重机,起重机采用地面遥控形式。
3)板料存放区:用于冲压件毛坯的存放,毛坯放在平板料盘上,可以直接存放在地坪上,也可以采用料棚存放。车间内毛坯运输采用叉车或起重机。
4)生产作业区(生产线):冲压生产线的生产区域。
5)线尾出件区:线尾成品件的百检、将成品件装入工位器具的区域,下件输送带布置方式有“一”字型布置和“T”型布置两种。
6)检验区:用于冲压件的检验,一般为频次抽检,外观百检一般在线完成。
7)冲压件返修区:用于不合格冲压件的返修,一般设置在与冲压车间相邻的冲压件库房内。
8)冲压件库:冲压件的存放区域,采用工位器具多层存放。一般布置在冲压车间与焊装车间相连接的位置,厂房高度一般与焊装车间的高度一致。冲压件的运输采用叉车。
(2)冲压车间面积。
按使用功能划分,冲压车间面积一般划分为生产面积、辅助面积和生活面积三类。
1)生产面积是指直接用于实现工艺过程的生产部门所占的面积,主要包括:
生产线和全部生产设备所占用的面积;
生产设备之间小通道(不包括主要通道);
工人操作时占用的面积;
生产过程中必须占用的面积(如冲压件检验地、冲压件返修地等);
生产设备周围待加工的毛坯、材料、半成品等占用的面积。
2)辅助面积是指不直接用于实现工艺过程的生产辅助部门所占的面积,主要包括:
车间内辅助部门所占用的面积;
车间主要通道面积;
各种库房和存放地。
3)生活面积主要包括车间办公室、会议室、更衣室、淋浴间、厕所等。
(3)冲压车间厂房。
布置超大型线厂房跨(宽)度一般为30m,大型线厂房跨(宽)度一般为24m,长度按功能区域确定。独立一跨布置的模具维修调试区跨(宽)度一般为24m。离线式清洗涂油线一般与中小型多工位压力机线(主要用于关键梁类结构件生产)布置在同一跨厂房内,厂房跨(宽)度一般为24m。
结束语
汽车覆盖件冲压生产车间是整车生产厂四大生产工艺车间或五大工艺车间(包括树脂成形)之一,其规划与设计应遵循“精益、紧凑、实用”的原则,追求“高质量、高效率、低投入”。许多企业将冲压车间的工艺平面布置形成标准化、模块化,工艺设备选择形成标准化、平台化,厂房及车间面积精益紧凑,物流便捷顺畅,为企业的汽车生产提供了重要保障。
-
冲压技术在电机叠片制造的应用
2024-09-06 -
车身零部件包边质量控制要点
2024-09-05 -
轻量化技术——热汽胀形工艺技术解析
2024-09-04 -
高强板车身件冲压技术
2024-09-02
最新资讯
-
旭化成微电子开始批量生产用于环保发
2025-04-24 16:00
-
华为、地平线、大众、东风、起亚等引
2025-04-24 08:27
-
全球产业链聚沪 共探双碳新路径 SNEC
2025-04-18 18:05
-
柯马签订具有约束力的协议收购 Autom
2025-04-17 13:01
-
高效协同新范式:比亚迪叉车领创智能
2025-04-17 10:04