应用于车身的下一代热冲压成形钢设计和工艺
摘要
研究复杂载荷条件下的车身结构是钢材料研发的重中之重。这种方法论使新型超高强度钢和高延展性热成形钢的设计更具针对性。由于最终材料性能是在汽车制造的生产步骤中决定的,因此淬火和分配(Q&P)等新型热冲压工艺可以保证在应用层面获得更好的材料性能。作为潜在新材料设计的一个方案,为了满足特定的车辆碰撞性能要求,开发了一种新的贝氏体化、淬火和碳分配(BQP-)工艺路径。为了进一步提升轻量化潜力,增加强度水平是必要的,但材料延展性通常非常低。一种新的“Sibora”--满足“BQP”路线的钢材料--有望为车身提供更高的碰撞延展性和更大的轻量化能力。
关键词:热冲压成形、钢板、淬火与分配、贝氏体化、轻量化设计、抗碰撞潜力、车身
1、下一代热冲压钢性能潜力研究的方法论
1.1
在过去的十年里,轻量化车身结构已经成为汽车行业的真正创新,新材料生产技术、制造方法和计算方法是其背后的推动力量。减少二氧化碳排放的政策方针和开发新型电动汽车的要求汽车行业付出巨大努力来满足所有需要高安全性能以及保持有吸引力且可以被客户接受的成本水平的车辆将是不久的将来市场决定性作用的角色。由于90%公司的汽车产品仍然采用钢制车身因此钢的设计与创新工艺技术的结合将是至关重要的。在不久的将来,零碳足迹的需求将更加强调生产工艺流程。为了减少热冲压生产线的高能耗,新的工艺路径对于基于全生命周期的新钢材料潜力分析至关重要。对资源高效利用的轻量化设计、批量生产的需求、成本降低和更高安全的要求,将为创新的钢转化为车身应用做出更大的努力。虽然只有在车辆碰撞情况下才能真正看到轻量化结构的未来潜力,但应用仿真模拟工装可以验证其经济性、轻量化和安全程度。通过计算机模拟预测结果的验证有助于在不同的车辆碰撞场景中检测新钢材料新的轻量化潜力。新的超高强度等级可以提供额外的轻量化潜力,但往往受到较差延展性的限制。热冲压成形工艺会显著影响材料性能,通过先进的材料设计和另一种热成形工艺路径的平衡结合,可能会实现新型钢材料的应用开发。作为一种方法论的结果,可以为未来的钢材料研究发展一些有益的性能[1,2,7]。超高强度钢的数量可以随着如图1所示的潜在部件的增加而增加。
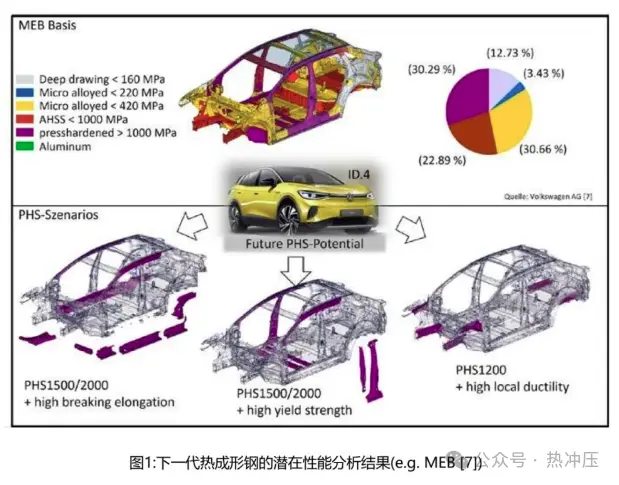
优先应用具有改进的机械性能(如断裂伸长率、屈服强度和局部延展性)的新型热冲压钢等级,随着钢板材厚度的部分减少,优化后的白车身重量减少了数公斤,但在碰撞和NVH(噪声、振动与声振粗糙度)方面,其性能仍与原白车身结构相当。
1、2
新的贝氏体化、淬火和碳分配(BQP-)工艺
淬火和碳分配(Q&P)的概念已成为热成形钢研究的一个重要主题,因为Q&P钢有望实现非常有价值的强度和延展性组合[3]。从经济性角度来看,与常见的先进高强钢以及热成形钢(例如22MnB5)相比,可以用相对低合金含量实现性能的改善。随着关注于工业化应用,这一方面的重要性越来越高,因为它不仅影响成本,而且影响良好的加工性能,适合现有生产线和精益生产线。一个重要方面是焊接能力,以保持材料更好的性能优点。最初的Q&P工艺对传统的热冲压成形工艺进行了延伸,预冷却阶段至低于马氏体起始温度的淬火点(淬火),然后是淬火温度水平(第一步)或高于马氏体起始温度(第二步的加热阶段(分配)。从工业化应用的角度来看,为实现批量生产的要求Q&P工艺的工业化生产需要经济性和可靠的工艺路径是显而易见的[5,6]。到目前为止,Q&P工艺项目的重点是在不同含硅量的条件下,利用Q&P技术对22MnB5钢进行热冲压成形。结果,Si含量为1.5%的合金显示出断裂伸长率的显著提高,而与22MnB5钢相比,观察到其抗拉强度的降低。研究发现这一结果可以在相对较低的碳分配温度下实现[5,6]。
在这项研究工作的基础上,设计了一种新的1900MPa含硅硼合金钢36SiB6并采用单步Q&P工艺路径带一套加热模具[6,8]进行分析。从Q&P工艺路径实施到批量生产中的第一个有希望的结果是寻找到适应现有热冲压成形生产线的其它工艺路径,以实现高强度和高延展性的组合。为了最大限度地提高含硅材料Q&P工艺获得的延展性,使奥氏体稳定并使其具有更高的强度,下一步将在热冲压应用中引入多相设计。其想法是使用Q&P工艺与贝氏体化相结合的方法,在最后部分产生多相分布。其结果是贝氏体、残余奥氏体和马氏体在最终部分的结合。在图2中,主要工艺路径通过时间一温度曲线与传统的热冲压工艺路径进行了比较。该示例中,在高于Ac3温度几分钟的奥氏体化阶段之后,快速预冷至贝氏体起始温度和马氏体起始温度之间的温度。在接下来的贝氏体保温阶段,根据时间和温度的不同,一定量的奥氏体转变为铁素体和贝氏体。贝氏体化阶段的典型温度在380至450°C之间。虽然硅抑制了铁碳化物的形成,但高碳含量也能够稳定奥氏体。下一步是在成形模具中进行最终的成形在该成形模具中,零件被压延至其最终形状,奥氏体迅速转变为马氏体。所提出的BQP工艺路径的最后一步是在150-200C的温度范围内进行20-30分钟的碳分配相阶段。该操作可以与阴极浸涂中的油漆烘焙过程相结合,并导致碳在结构中的重新分布。在配分相后的拉伸试验中,压延的拉伸长度得到了显著提高
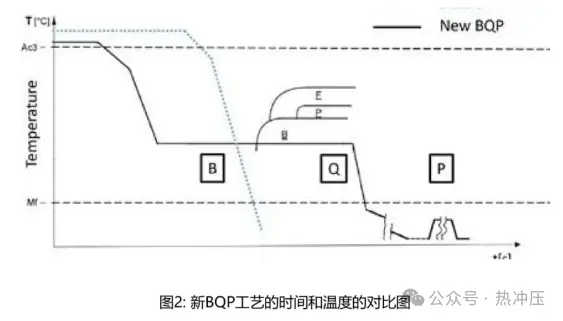
图3显示了新的BQP工艺的流程图,而图4显示了metakus AutomotiveGmbH用于研究的已实现BQP工艺的试验工厂图片。BQP试验工厂的设计与大众汽车集团卡塞尔零部件工厂的现有热冲压成形生产线非常相似,测试结果和经验可作为下一步进行批量化生产应用。与批量化生产的热冲压线的主要区别是,由于不需要生产大批零件,加热炉只有8米长。
2、用于BQP-工艺的新型“Sibora”钢设计
高强度通常是车身结构进一步轻量化的驱动力。因此,1900MPa抗拉强度的钢材可以提供进一步轻量化的潜力。此外,如果增大溃能吸收,大约定义为产品拉伸强度Rm x断裂伸长率At,则1200MPa或1500MPa钢的抗拉强度可以加大其轻量化潜力。36SiB6合金体系在Q&P工艺中显示出先进的延展性,适用于BQP工艺路径的研究。总而言之,研究了具有最大碳和硅含量的另一个合金体系40SiB8,以显示进一步的潜力以及可能的局限性,表1。
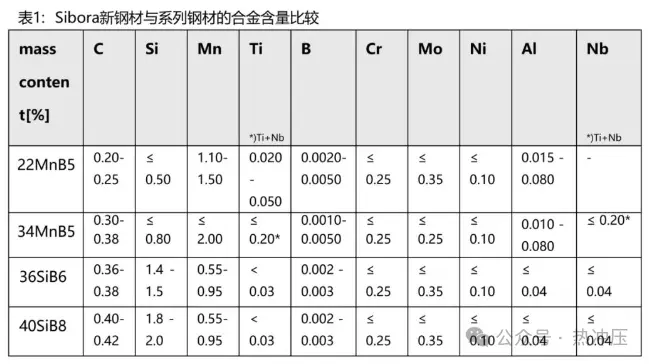
硅和碳是成本相对较低的元素,这是汽车大规模生产成功的重要因素。为了具有稳健的热冲压成形过程,一个方面是避免不均匀的硬相(碳化物)。因此,即使在含Mn的情况下,这些元素的含量也会减少,以便在连续生产的Q&P工艺过程中产生均匀的微观结构[5,6]
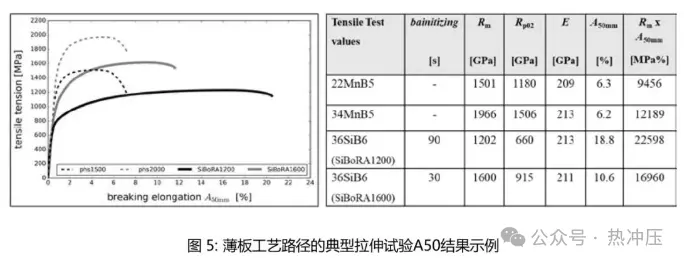
进行了进一步分析,显示出不同工艺参数下的机械性能有所改善,如图5所示。所生产板材的微观结构显示出铁素体-贝氏体、马氏体和残余奥氏体的非常精细的分散织构,马氏体针之间有针状奥氏体组织[8],图6。
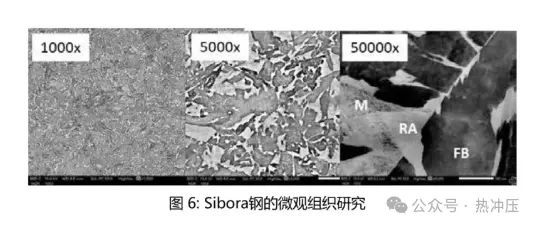
为了更好地进行内部沟通,研究级别被命名为硅硼钢和残余奥氏体“Sibora”钢。
3、作为初步结果的半工业化示范加工
下一步将是将新一代热成形钢应用到批量化生产中。德国奇昊(KirchoffAutomotive)汽车在一条量产线上使用了B柱演示模具进行研究分析。由于“Sibora原型钢材料的板材尺寸有限,因此试制了一个拼焊定制的B柱。“Sibora"--40SiB8级钢设置在部件的顶端,以便使用现有的预冷设施。B柱采用22MnB5钢系列如图7所示。
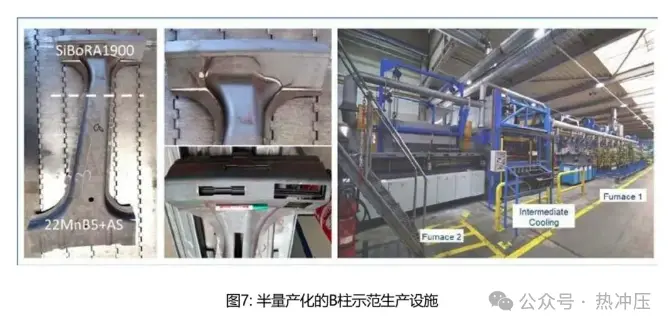
B柱采用不同的工艺参数,贝氏体化时间设定在6s至90s之间。该工艺在没有炉内氛围气体的情况下运行,未涂层的“Sibora”级钢板显示出有粘性和氧化硅层,显然不需要额外的保护。不幸的是,在这种状态下,将需要喷丸进行进一步处理。A3o拉伸,正如从生产的B柱上切下弯曲角试样一样,测试结果如图8所示。
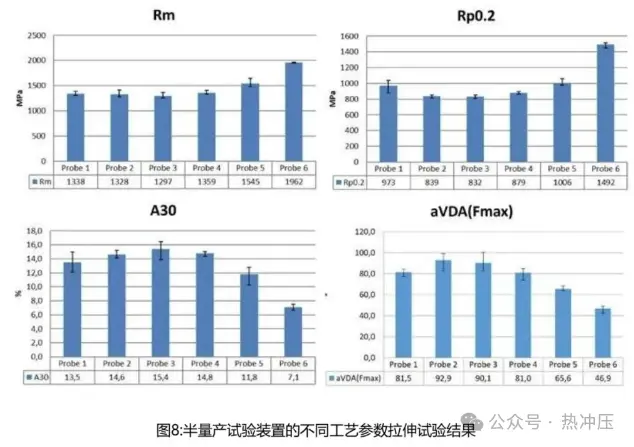
因此,贝氏体短时效时间显示出更高的强度水平和更好的可成形性。在较长贝氏体化的情况下,整体(断裂伸长率)和局部延展性(弯曲角)增加。对于长贝氏体化时间,B柱法兰的一侧出现单一裂纹。因此,必须进一步研究贝氏体钢板的温成形行为。必须指出的是,现有的模具并没有针对贝氏体热冲压成形进行优化,例如,与AS涂层相比,氧化硅层显示出更高的摩擦值。下一步的重要工作是进一步研究Q&P级钢的可焊性和批量生产。
4、结论和展望
通过添加硅以在淬火和分配(Q&P-)路线中稳定残余奥氏体(RA),可以提高延展性。在新开发的贝氏体化、淬火和分配(BQP-)工艺中产生的多相结构中,观察到了更高的强度和更好的延展性。由于“BQP-”工艺只有在成本经济的工艺条件和大规模生产的特性下才能成功,因此引入了一个在应用层面上进行进一步研究的试验装置。零件级的进一步系列测试将有助于“BQP”工艺适应现有的热成形生产线。所提出的“Sibora”合金设计显示,随着贝氏体化参数的变化,可能出现广泛的强度-延展性组合。硅合金钢的工业化试验以及用于碰撞试验的半批量生产示范工装的制造是下一步工作。
参考资料
[1] Hatscher, A. et al: A new steel roadmap for future car body applications.In: 5thinternational Conference on Steels in Cars and Trucks, June 18-22,Amsterdam-Schiphol, 2017.
[2]Hatscher, A. et al: Neue Leichtbaustudie als Basis zukünftigerStahlwerkstoffe für den Einsatz in der Karosserie. Stahl und Eisen 137(2017)No.11,pp.158-165
[3] Speer, J.G. et al: Carbon partitioning into austenite after martensitetransformation.In: Acta Materialia 51 (2017)No.9, pp.2611-2622
[4]linke,B. et al: lmpact of Silicon on Microstructure and MechanicalProperties of 22MnB5 Hot Stamping Steel Treated by Quenching &Partitioning (Q&P). In:metallurgical and Materials Transactions A, November 2017
[5] Arribas, M. et al.: Elonhotstamp, New Hot Stamping Steel with lmprovedElongation, Final Project Report, Grand Agreement No. RFSR-CT-2013-00010.
[6]Hatscher, A: Design and potential analysis of a new ultra high strengthsteel(1900MPa) with Q&P processes for car body applications, In: 7thInternational Conference on Hot Sheet metal Forming of HighPerformance Steel (CHS2), 2-5 June 2019, Luleà Sweden
[7]Graul, M:Nachhaltige Karosseriebauweisen -Volkswagen Way tZero,Hamburger Karosseriebautage, 30.Sept.-1.Aug., Hamburg Germany
[8]Diekmann,U. et a.: Development and characterization of new lowalloyed ultra-high strength steel for structural body components, to bepresented at the6th Int. Conf. Steels in Cars and Trucks, Milan, ltaly, Jun21,2022.
-
冲压技术在电机叠片制造的应用
2024-09-06 -
车身零部件包边质量控制要点
2024-09-05 -
轻量化技术——热汽胀形工艺技术解析
2024-09-04 -
高强板车身件冲压技术
2024-09-02
最新资讯
-
全球产业链聚沪 共探双碳新路径 SNEC
2025-04-18 18:05
-
柯马签订具有约束力的协议收购 Autom
2025-04-17 13:01
-
高效协同新范式:比亚迪叉车领创智能
2025-04-17 10:04
-
埃马克德国总部迎来中国社科院工业经
2025-04-15 09:40
-
埃马克这项全新应用即将在CIMT惊艳首
2025-04-15 09:37