基于多部件集成的热冲压成形技术研究进展
摘 要:高性能金属板料热冲压成形技术对汽车轻量化极其重要,目前已被广泛应用。随着超高强钢热冲压成形技术的进步,热冲压成形技术从简单的零件成形正逐步向复杂结构成形发展。以轻量化车身结构件的碰撞能量分布载荷路径为基础,选择不同板厚和强度级别的板料进行激光拼焊,经过一体化热冲压成形后,获得高强塑性区域合理分布的多部件集成热冲压轻量化车身部件。激光拼焊工艺和高效激光加工自动化装备保证了其关键技术的实现。在降低碳排放、提高生产效率、减少材料用量及满足车身结构优化等诸多方面具有突出的优越性和实用价值。
关键词:车身轻量化;多部件集成;激光拼焊;热冲压;工业4.0
多部件集成(Multi Part Integration,MPI)技术的核心是超高强钢激光拼焊技术与一体式热冲压技术的完美结合。通过使用激光拼焊技术将材料的强度和厚度进行合理组合,使车身结构刚度大大改善,优化整车的振动特性,使汽车振动和噪声降低,提高了整车的舒适性。材料强度和厚度的可变性保证了某些重要位置的碰撞强化要求,实现了材料性能的充分利用。
01 汽车车身结构件的高强钢热冲压
超高强钢和热冲压技术于1977年获得专利,1990年在车身结构件上获得初步应用,2009年后得到快速发展[1]。用于热冲压的超高强钢从开始单一的强度级别逐步发展到1000、1500、1800和2000 MPa多种强度级别,同时也开发了适应热冲压技术的500~700 MPa强度级别的热成形钢,如图1所示[2]。热冲压技术也发展到变强度(Tailored Temperature Properties,TTP)热冲压[3-4]、变厚度(Tailor Rolled Blank,TRB)热冲压和激光拼焊板(Laser Tailor Welded Blank,LWB)热冲压;虽然一度受到激光去镀层相关技术的限制,但是当瓶颈突破后,国内的车体零部件热冲压成形从单一零件的热冲压发展到基于激光拼焊板的多零件集成的一体式热冲压。
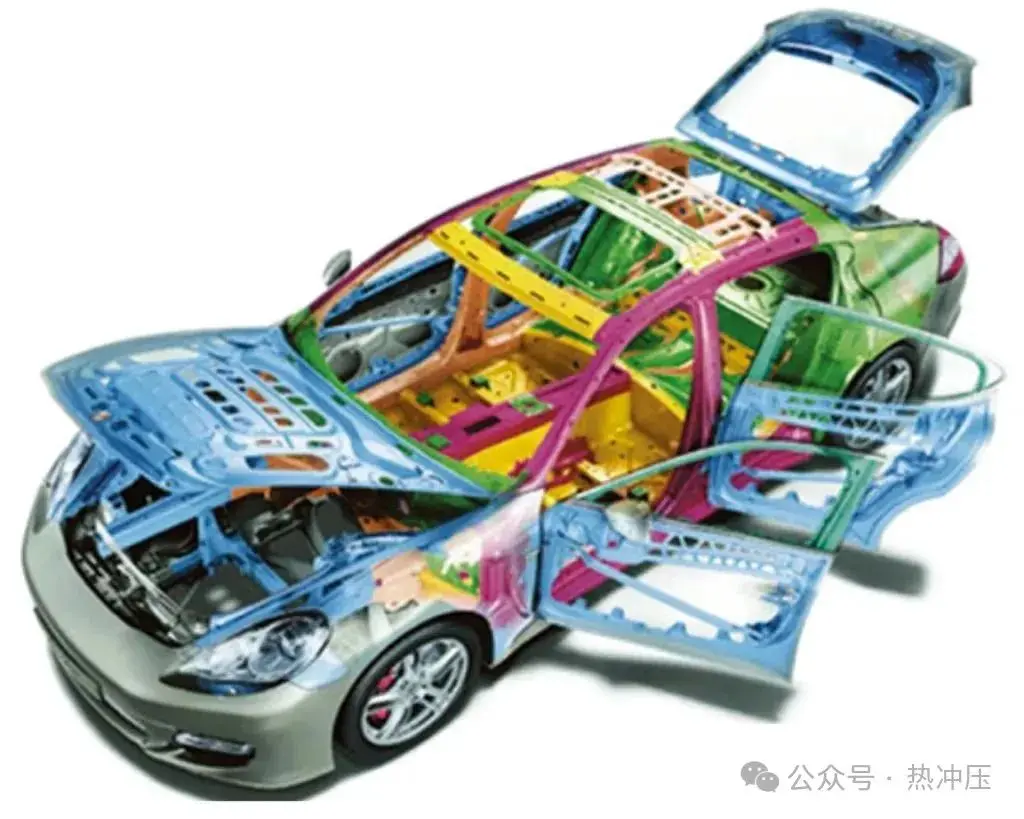
图1 多种材料定制化成形技术[2]
1.1 多部件集成热冲压一体成形
高强钢的最佳连接工艺是激光拼焊,即将不同材质、厚度和形状的板材焊接成一整块毛坯板材,再通过热冲压成形。ArcelorMittal公司与本田公司在2014年合作研发了世界上第一款超高强钢拼焊板制造的门环[5],2018年又以Acura RDX为平台推出了世界上第一款超高强钢内-外门环,如图2所示。2021年ArcelorMittal公司在多年技术发展的基础上提出了MPI概念[6],MPI技术结合了超高强钢激光拼焊技术与热冲压技术的优点,其和特斯拉公司的铝合金一体式压铸具有异曲同工之妙,但明显前者具有投资小、技术较为成熟、性能可定制、尺寸精度高以及维修成本低等优点。
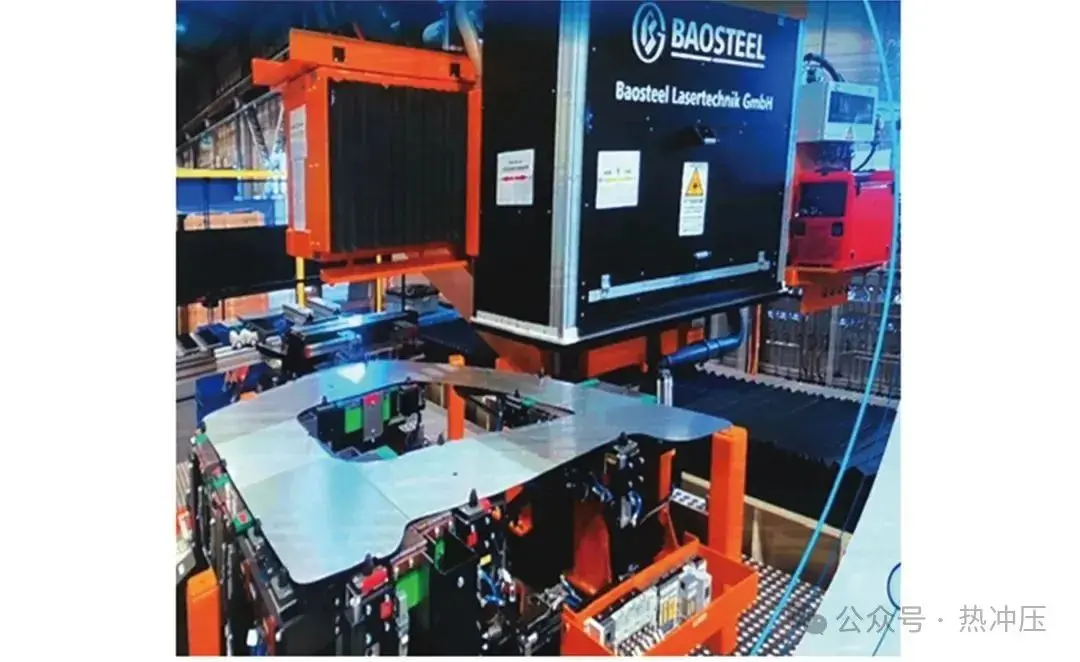
图2 MPI门环的热冲压成形
1.2 关键技术
激光拼焊原理是将材料的强韧性和厚度进行合理组合,从而改善车身结构刚度和强度(图3[7])。其中,刚度优化可以降低汽车振动和噪声,提高整车舒适性。材料强韧性和厚度的可变性保证了碰撞强化和吸能要求,实现材料性能的充分利用,提高车身的安全性,增加产品设计的灵活性。由于不同零部件在成形前通过激光焊接在一起,因而提高了零部件的尺寸精度,降低了零部件的制造及装配公差,同时减少了生产设备和简化了制造工艺,提高了生产效率,降低了成本。
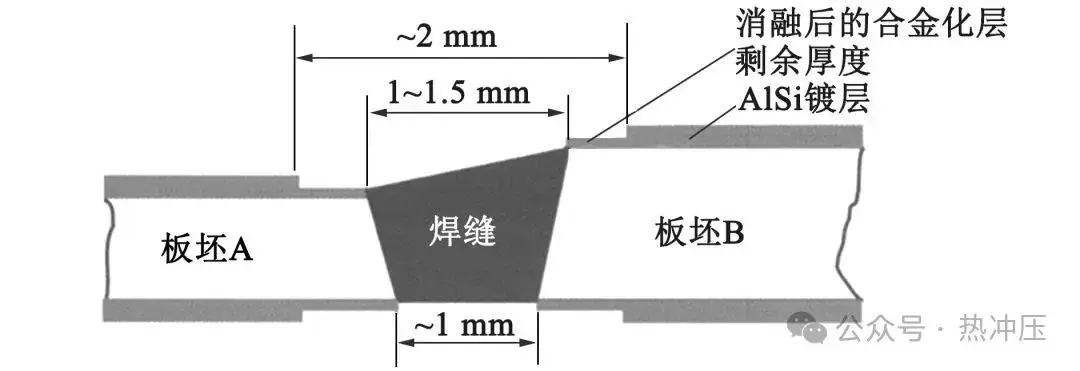
图3 激光拼焊板技术原理[7]
02 多部件集成技术
2.1 多部件集成的结构设计优化
目前,大部分汽车车身零件制造采用的是分离成形方法,即利用不同的模具分别成形单个零件,然后将各个零件焊接起来组成目标部件。这种方法虽然提高了材料选择的灵活性,但同时也增加了冲压、加工和装配成本以及形状配合问题,且点焊时的材料重叠也增加了车身重量。
为实现车身结构轻量化,车身材料需要逐渐高强化,特别是车身安全结构件,往往使用强度性能很高的先进高强钢。此外还可将不同性能的高强钢连接起来,从单一材料向多种材料混合使用转变[8],从而实现汽车轻量化。因此,焊接工艺十分重要,保证焊缝的稳定结实、不易发生断裂失效等缺陷是基本要求。
与传统燃油车相比,新能源汽车的结构发生了重大变化。由于车身没有中央通道的存在,故纯电动平台可以实现贯穿式车身底部横梁设计,以保证乘员舱真正形成一个截面闭环的框架结构,提高整个车身刚性和侧向安全强度。在此情况下,多部件集成的一体式热冲压件具有更大的安全优势,其设计路线如下:
(1) 以汽车载荷传递路径设计为基础,对包含一体式拼焊部件在内的车身结构进行分析(图4[9]),实现了车身结构刚度、承载体扭转刚度、车身结构振动特性以及碰撞能量分散与吸收的设计优化,确定不同强度和厚度组合的拼焊板结构性能分配。
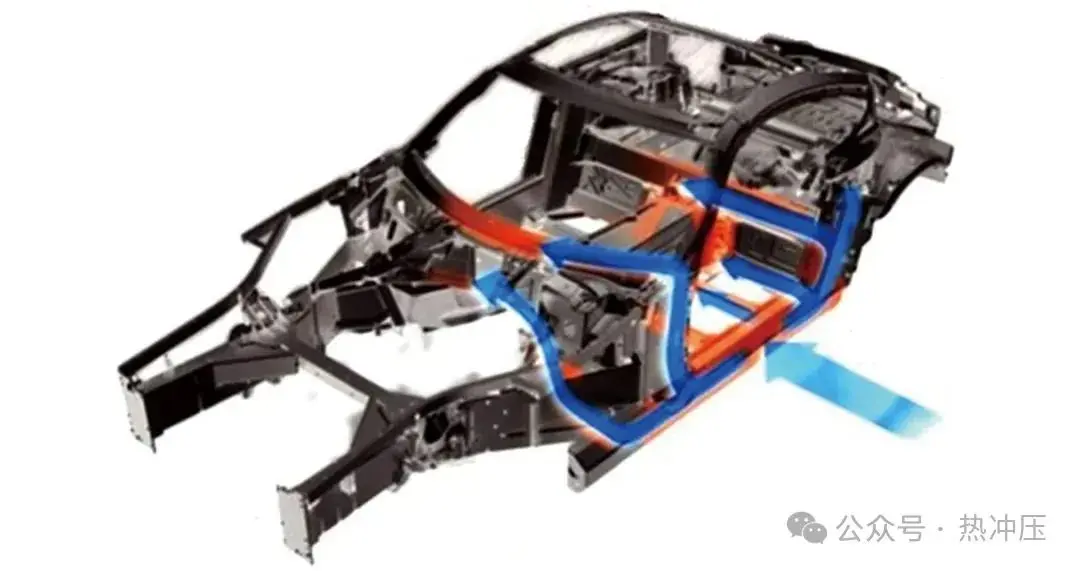
图4 车身载荷传递路径分析[9]
(2) 拼焊板部件的尺寸优化。基于特定结构的材料性质、类型、几何尺寸和布局关系,通过特定的数学模型优化算法对结构的截面尺寸参数进行优化,从而实现结构的质量、体积达到最小值,材料利用率提高,成本降到最低,由本团队研发的实际案例如图5和图6所示,A~F表示部件。在优化过程中,必须满足热冲压工艺(如最小圆角半径和侧壁角度、局部成形深度与宽度比以及热冲压不能二次成形等)的要求。
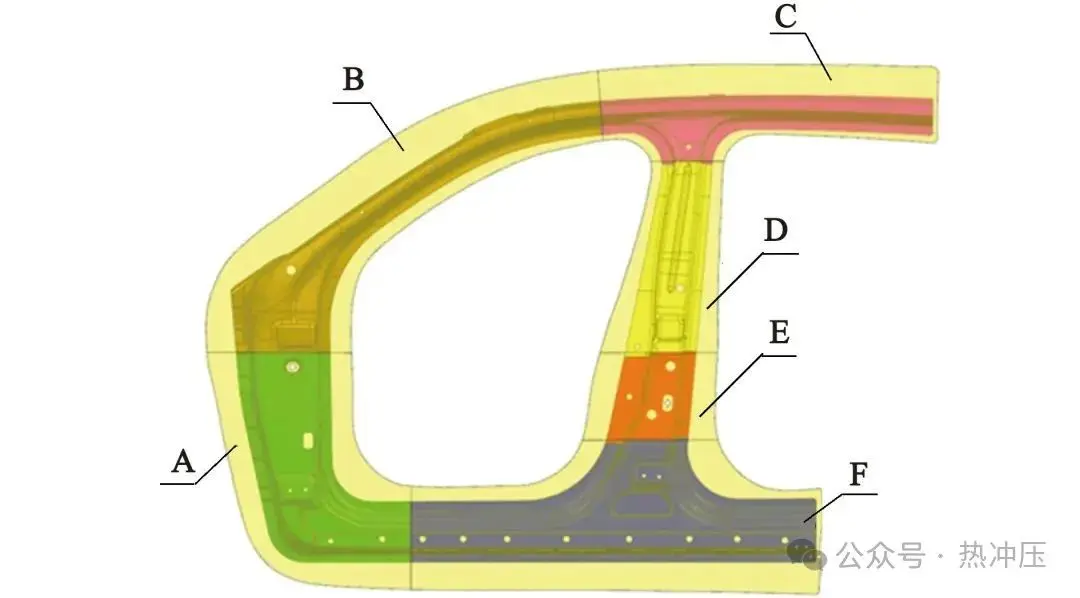
图5 拼焊板部件的尺寸优化
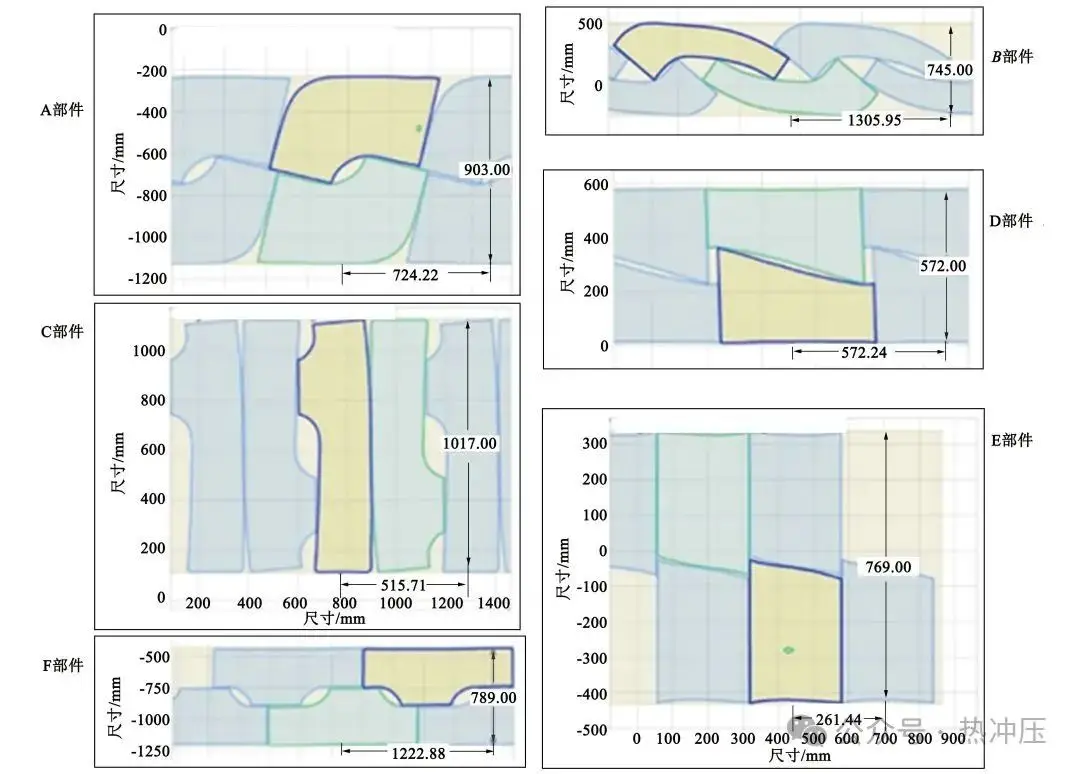
图6 拼焊板的落料工艺对材料利用率的影响
(3) 拼焊板部件的形状优化。设计人员先进行模型结构拓扑布局、材料特性等形状参数的确定,然后通过改变结构边界形状来实现优化结构设计,属于可动边界问题。作为一体化成形方式,不同材料的连接方式从电焊变成了激光焊接,为满足车身结构服役要求,必须修改边界形状以避免缺陷出现。
(4) 采用高速拉伸试验获得不同拼焊板的高速动态特性。在此基础上,实现车身结构的碰撞仿真,优化车身结构。
2.2 不同强度和厚度的激光拼焊工艺
通过激光拼焊板制成的成形件不仅具有多种厚度,甚至可以具有多种性能各异的材料,从而可在不同部位采用具有针对性的材料,如在变形量较大的部位采用成形性较好的软钢,而变形量较小或者需承受较大载荷的地方采用性能强度更好的高强钢。同时激光焊接工艺保证了焊缝的性能,使得焊缝强度不低于母材强度[10]。
自2007年ArcelorMitittal公司推出半消融铝硅镀层板激光拼焊技术以来,铝硅镀层热成形激光拼焊板最大程度上发挥了激光拼焊板和热冲压工艺[11-12]轻量化的优点。该方案在现今汽车行业主要应用有:等强差厚热冲压激光拼焊板、差强等厚热冲压激光拼焊板和差强差厚热冲压激光拼焊板的设计方案。国内的铝硅镀层激光拼焊板在2019年之前一直被ArcelorMitittal公司垄断供应,直至2020年宝钢提出了填丝激光拼焊工艺才打破了其垄断地位。
在填丝激光拼焊工艺基础上,目前应用项目的相关研究内容主要为:
(1)采用激光拼焊技术将不同强度级别、材料和厚度的钢板拼焊在一起,研究了异种材料焊接过程中的组织转变规律。测量焊接接头的显微硬度,得到接头显微硬度与不同材料的关系。
(2)开展了多种拉伸试验,得到了激光拼焊板的应力-应变曲线,分析了焊接工艺对拼焊板的变形规律的影响;开展了杯突试验,得到了拼焊板的成形极限。通过研究焊缝组织的力学性能,最终获得了激光焊接工艺参数对异种材料焊接组织和力学性能的影响。
(3)由于采用填丝焊接,焊缝组织中会有少量镀层融入,因此需要研究不同镀层组织和填丝材料之间的作用关系及对最终力学性能的影响,为选择合适的填丝材料提供帮助[13]。
2.3 激光拼焊板的热冲压工艺及模具
由于激光拼焊板是由不同或相同厚度、强度和材质的钢板拼焊而成的毛坯件,在制定热冲压工艺时,除了要考虑不同材质、强度和厚度对工艺过程的影响,避免成形缺陷的产生,还需要考虑不同基板的热冲压特性而制定工艺参数区间。具体研究如下:
(1)由于激光焊缝受两侧材料的强度和厚度的影响,在热冲压成形过程中存在焊缝偏移的现象。较薄的一侧变形量大,强度较低的一侧变形量大,减薄严重,容易导致破裂,因此对冲压工艺参数对焊缝偏移的规律展开了研究。
(2)热冲压钢目前有1500、1800和2000 MPa等级别,其热冲压的工艺窗口较为明确,需要综合考虑相变特性对材料的影响,获得合适的工艺窗口[14]。
(3)多部件集成的热冲压件使用的材料多样化,需要从材料热冲压特性、焊缝偏移规律、工艺窗口的融合等方面优化工艺[15]。
(4)建立多部件集成的激光拼焊板热冲压材料本构模型,研究热冲压过程的相变转化模型、传热模型及激光拼焊板的热力学模型。通过热冲压成形试验,进行厚度分布分析及微观组织测试,通过与数值模拟结果的对比验证了材料模型的可靠性[16]。
(5)热冲压后的快速冷却保证了材料相变得到所需组织。但在实际热冲压过程中,焊缝的移动、薄侧起皱和过量减薄等都会影响淬火的效率。需要在模具设计时考虑这些流动现象的影响,从而使模具结构设计合理[17]。
2.4 多部件集成一体式热冲压技术的应用
车体门环是典型的多部件集成,并能够实现一次完成热冲压成形-强化。采用激光拼焊的方法将多段不同材料、厚度和性能的高强钢坯料焊接起来,再通过热冲压成形技术改变其形状和性能,得到整体的高性能强度的门环结构。由于门环不同部位的性能要求不同,往往在选择材料时,针对不同位置,适配不同强度和厚度的材料,实现整体的门环结构性能达到最合理、最优异的状态,不仅使得材料运用更合理,大大节约了模具成本、简化了生产工艺,同时实现了材料轻量化设计。热冲压成形的门环尺寸精度更精准,力学性能更优秀,大幅提高了乘用车白车身的强度以及侧围的抗碰撞能力,使得车身结构的安全性更高,有效提升了乘用车白车身的静态刚度。
高强钢热成形板分为带表面镀层(一般是AlSi镀层或锌基镀层)的镀层板和不带镀层的非镀层板(或裸板),因其成本较低且来源广泛,在世界上应用广泛。
最新研究中,集成部件采用中锰钢或者高强不锈钢板能够集成强度合理的轻量化一体部件,并可满足更多的材料特性(如更高的伸长率和抗腐蚀性),这些应用研究已经在试验评估过程中。
无涂层免喷丸热成形钢是一种新开发的抗氧化热成形钢板,采用特殊的表面改性技术在钢板表面直接预生成Fe3O4的表面氧化物层结构,使得坯料板在加热过程中无法生成FeO亚层,可以有效地改善和解决氧化皮脱落现象,提高加热和成形过程中材料的表面质量,抑制热冲压工艺氧化皮脱落,为提高材料的使用特性开辟新的途径[18]。
03 多部件集成的技术装备
3.1 激光拼焊板生产线
根据激光拼焊板生产线的自动化程度可以分为手工焊缝拼焊、半自动机器人连续焊接线和全自动龙门式连续焊接线。典型的手工焊缝拼焊生产线需要人工装载料片,并依靠手工布置和定位料片,焊接完成后也需要通过手工卸载拼焊板成品,手工焊缝拼焊生产线需要5名左右操作人员。半自动机器人连续焊接线需要手动或自动加载预材料,并通过精密剪切机进行剪切落料,人工拼对后进行自动连接,然后手动或自动卸载焊接坯料,需要3名直接操作人员。全自动龙门式连续焊接线可以实现材料自动加载、坯料的自动连接和定位,焊接坯料自动卸载,需要1名直接操作人员。
而专用的门环拼焊全自动线,其生产效率比传统的半自动拼焊线的效率高很多,如图7所示[19]。宝钢激光拼焊国际有限公司的新一代生产效率是传统拼焊板生产线的2~3倍[19]。
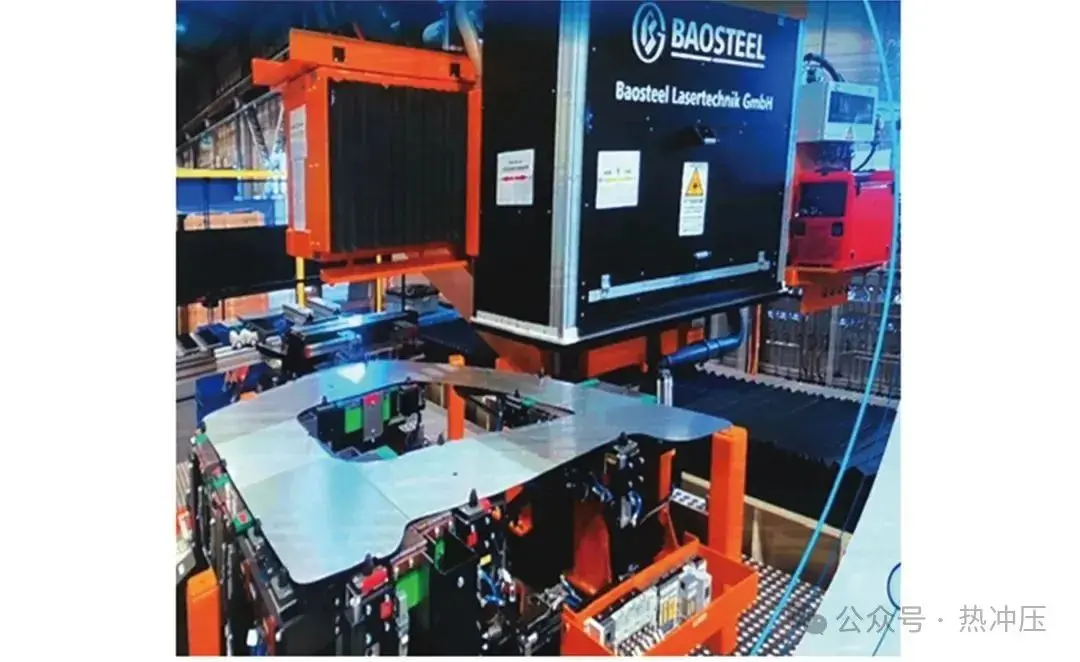
图7 高效专用门环坯料拼焊板设备[19]
3.2 热冲压车间与激光加工数字化车间
由于热冲压生产线节拍与拼焊线节拍不同步,单条热成形生产线要与多台专用激光拼焊设备(如门环专用拼焊系统)匹配,方能满足整体产能需求。热冲压生产节拍基本不受零件大小的影响,而激光拼焊生产线的节拍受焊接路径长短和焊缝数量的影响,拼焊的时间也有所不同。由于激光加工设备是数字化激光设备,可以根据数字化热冲压车间的生产节拍需要,及时调整拼焊生产线的任务,进行动态调整,有助于提高生产效率和设备利用率。
传统的热冲压生产线流程是:开卷校平-切割落料-热冲压成形-三维五轴激光切割-抛丸清理(对于非镀层板)。而在新一代数字化车间的工序流程中,增加了更多的激光加工工序,其流程是:开卷校平-激光切割落料-激光拼焊-热冲压成形-三维五轴激光切割-热冲压件(某些特殊要求)局部激光软化加工或者激光组件焊接[20]。
本课题组基于工业4.0概念的数字化热冲压与激光加工数字化车间[21-22]的规划如图8所示。在新的数字化车间的体系架构中,由相对独立的数字化制造单元组成系统,单元之间使用工业互联网连接,由于嵌入式环境系统出现越来越多的交叉,形成了所谓的系统体系(System of System,SoS),即在热成形生产情境下,由多个分散自主系统组成的更大、更复杂的系统。要理解SoS系统的复杂性,就需要理解子系统的单独特征和相互交互产生的涌现特征。在实现热冲压数字化车间工业4.0的实践目标的过程中,也为金属板料热冲压成形行业引入了智能制造的课题[23]。
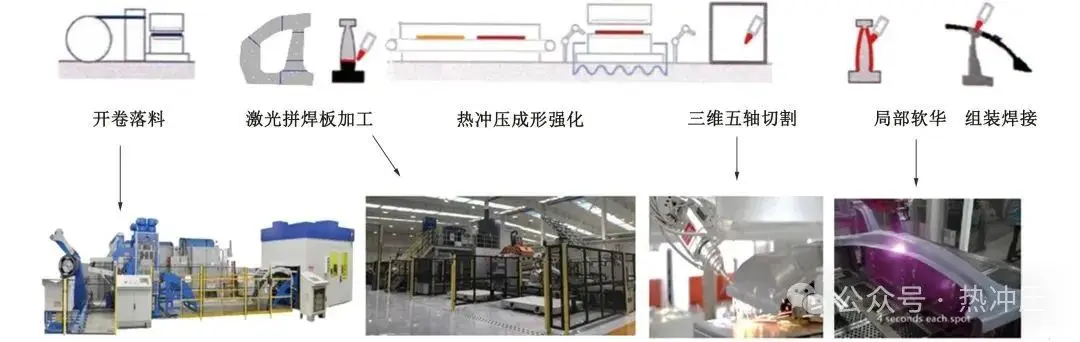
图8 热冲压与激光加工数字化车间示意图
3.3 多部件集成热冲压生产过程中的CO2减排
多部件集成热冲压生产的最突出优势为:车身零件的总用材量减少,拼焊板落料的材料利用率和加工效率提高。同时多部件集成冲压创新的零件重量减小、冲压模具数量减少,零部件装配的装配车间的占地面积也大大减少,总体收益明显增加。
以某车型的热成形激光拼焊一体式后车体骨架为例(图9[6])。传统的集成方法中,该组件由5个零件和10个隔板成形,装配零件为15件,装配点焊90个,需要多套冲压模具和多级组装。组装后的重量为11.02 kg,坯料重17.75 kg,材料利用率为62%。多部件拼焊板集成设计中,采用5个零件集成为1个组件和6个独立的隔板,装配零件为7件,组装后的重量8.34 kg,坯料重11.24 kg,每辆车减重2.68 kg,材料利用率为74%。
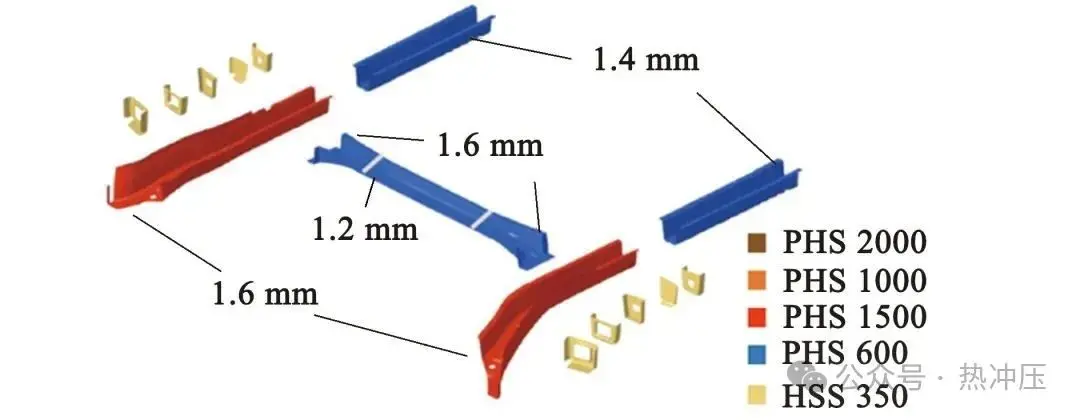
图9 传统组件方案与多部件集成方案对比[6]
对该部件而言,CO2当量排放由传统方案的24.29 kg减少到15.53 kg,在汽车生产阶段,每辆车的CO2当排放量为8.76 kg量,节省了36%。
多部件集成一体化热冲压成形解决方案有利于绿色环保的落实。基于UCSB汽车能源和温室气体模型用户指南V5以及BEV SUV设计实施的钢材计算的CO2减排报告可知,该零件生产10年内的CO2减排量相当于减少了200万辆汽车的运行排量[24]。在生产和车辆使用生命周期中减少17000 t的CO2当量,相当于4座风力发电站,为3000个家庭提供的用电量。
04 结论
(1)多部件集成热冲压,是激光拼焊板与热冲压成形的综合技术。应用多部件集成高强钢热冲压技术可以实现复杂几何形状的轻量化车体成形。该方法适用于不同车辆动力系统的解决方案,包括电动汽车。有利于产品质量的提升和材料利用率的优化。
(2)与多部件独立设计成形传统技术相比,一体成形技术总成本更低,可以满足国际市场的所有相关安全要求。由于该技术的零部件集成度和材料利用率高,目前已经成为车身轻量化的一种可持续发展的解决方案。
参考文献:
[1] 张宜生,王子健,王梁.高强钢热冲压成形工艺及装备进展[J].塑性工程学报,2018,25(5):11-23.
[2] MESCHUT G,JANZEN V,OLFERMANN T. Olfermann innovative and highly productive joining technologies for multi-material lightweight car body structures[J]. Journal of Materials Engineering and Performance,2014,23:1515-1523.
[3] 王子健,刘晓龙,张宜生,等.高强钢热冲压成形变强度工艺研究[J].热加工工艺,2018,47(13):33-36.
[4] 喻苗. 高强钢变强度成形的综合目标实现方法研究[D].武汉:华中科技大学,2014.
[5] MALLEN R Z.RIGGSBY J. 2014 acura MDX one-piece hot stamp door ring development[R]. Global Powertrain Congress,2013.
[6] ACHIKET G.Mulit part integration (MPI)concepts using press hardening sheet laser concepts using press hardening steel laser welded blanks[EB/OL].(2022-06-01)[2022-12-11]. https://www.steel.org/wp-content/uploads/2022/06/Track-2-Session-3-Gokhale-ArcelorMittal-TWB-r2.pdf.
[7] YOON T J,OH M H,SHIN H J,et al.Comparison of microstructure and phase transformation of laser-welded joints in Al-10wt%Si-coated boron steel before and after hot stamping[J].Materials Characterization,2017,128:195-202.
[8] 朱彬,刘旺,刘勇,等.高强钢/碳纤维增强复合材料热冲压-连接一体化工艺可行性及试样弯曲性能研究[J].中国机械工程,2021,32(24):2975 -2980.
[9] GAGAN T. Integrated battery occupant protection body-in-white concept using tailored blanks[EB/OL]. (2021-06-01)[2022-12-11]. https://www.steel.org/wp-content/uploads/2021/06/GDIS-2021_Track-3_01_Tandon_Tailored-Blanks.pdf.
[10] 景财年,范吉超,倪晓梅,等.激光焊接不等厚异种钢接头组织与性能研究[J].中国激光,2014,41(8):97-102.
[11] 王凯,朱彬,王义林,等.热冲压钢Al-Si镀层形貌动态演化及形变开裂特征[J].塑性工程学报,2020,27 (9):181-185.
[12] LIANG W,DUAN J,WANG Q,et al. Influence of multi-step heating methods on properties of Al-Si coating boron steel sheet[J].Coatings,2021,11(2):164-178.
[13] PAN H,DING K,GAO Y L,et al. Performance evaluation and application of the laser welded joint with filler wire for Al-Si coated press-hardened steels[C]//Advanced High Strength Steel and Press Hardening Proceedings of the 6th International Conference (ICHSU 2022). Wuhan,2022:161-169.
[14] 唐炳涛,原政军,张保仪,等.高强钢B340LA与B1500HS钢激光拼焊板热冲压淬火性能[J].材料热处理学报,2013,34(2):62-66.
[15] 龚志辉,赵树武.差厚拼焊板零件焊缝线偏移的控制方法[J].中国机械工程,2019,30(6):742-747.
[16] 于恒星.差厚板热冲压的成形工艺和组织演变规律研究[D].沈阳:东北大学,2019.
[17] 王子健. 高强钢板料变强度热冲压成形研究及应用[D].武汉:华中科技大学,2016.
[18] LIU H L,HU Y,GAO H G,et al. Application research on antioxidant hot formed phs1500a steel[C]//Advanced High Strength Steel and Press Hardening Proceedings of the 3rd International Conference (ICHSU2016). Xi′an,2016:31-35.
[19] LIU J B. Green technology of laser welding and equipment for hot forming steel[C]//Advanced High Strength Steel and Press Hardening of the 6th International Conference(ICHSU 2022). Wuhan,2022:161-164.
[20] FREY A,KOHLLÖFFEL R,MAIER D M,et al. Improvements in laser processing of door rings with laser machines[C]//Advanced High Strength Steel and Press Hardening of the 5th International Conference (ICHSU2020). Shanghai,2020:387-394.
[21] EBNER F. Intelligent process optimization for highly efficient productions[C]//Hot Sheet metal Forming of High-Performance Steel (CHS2). Lulea,2019:759-766.
[22] WANG L,WANG K,LI S,et al. Long period intelligent control in hot stamping production[C]//Hot Sheet metal Forming of High-Performance Steel (CHS2). Lulea,2019:767-772.
[23] SVEN F,THOMAS D,SEBASTIAN W,et al.Towards sustainable systems recon-figuration by an iot-driven system of systems engineering lifecycle approach[J]. CIRP,2022,(105):654-659.
[24] WILSIUS J,LUTTENSCHLAGER K. Multi part integration approach for body structure using breakthrough hot stamped laser welded blanks solutions[C]//Hot Sheet metal Forming of High-Performance Steel (CHS2). Barcelona,2022:221-218.
-
冲压技术在电机叠片制造的应用
2024-09-06 -
车身零部件包边质量控制要点
2024-09-05 -
轻量化技术——热汽胀形工艺技术解析
2024-09-04 -
高强板车身件冲压技术
2024-09-02
最新资讯
-
重磅剧透!首批参展商名单曝光——这
2025-04-01 20:48
-
施耐德电气发布新一代Harmony XVB7模
2025-04-01 18:51
-
[转载] 机床巨头埃马克:百年跌宕再
2025-03-31 12:42
-
从4S店到修理厂:FLIR ONE Pro USB-C
2025-03-28 16:05
-
比亚迪发布2024年ESG报告 以技术创新
2025-03-26 16:44