美、欧、日、中汽车轻量化技术路线分析
美国:以材料进步为驱动
美国汽车轻量化路线,以材料进步为驱动,综合衡量材料成本、性能、可回收性及用量。
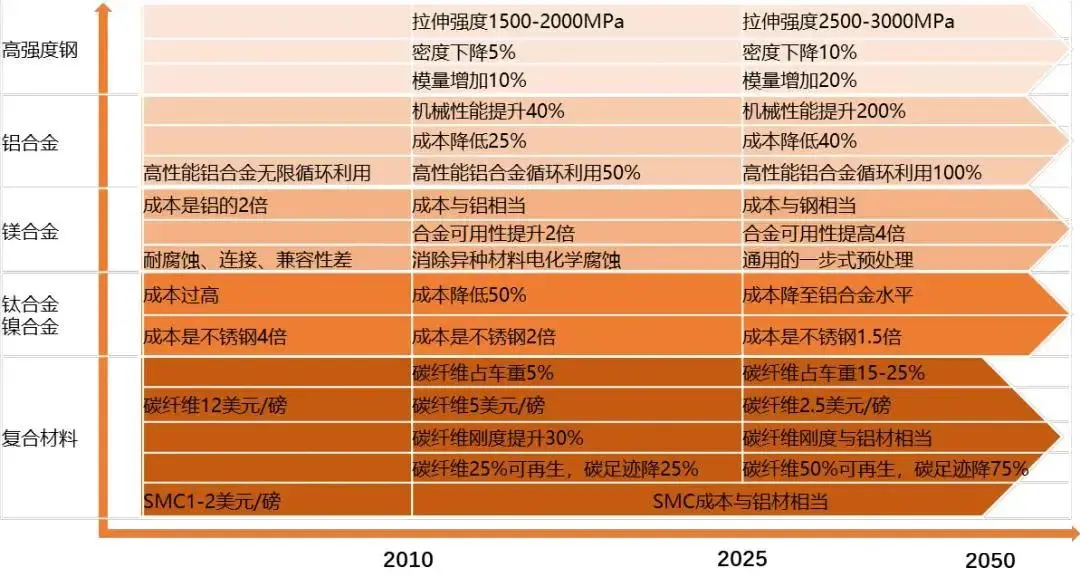
表1 美国汽车轻量化路线
2010-2025年高强度钢拉伸强度1500~2000MPa,密度下降5%,模量增加10%;铝合金机械性能提升40%,成本降低25%,高性能铝循环利用50%;镁合金成本下降至与铝相当,可用性提升2倍,消除异种材料电化学腐蚀;钛合金、镍合金成本降低50%,成本是不锈钢2倍;碳纤维占车重5%,单价5美元/磅,刚度提升30%,25%可再生,碳足迹降25%。
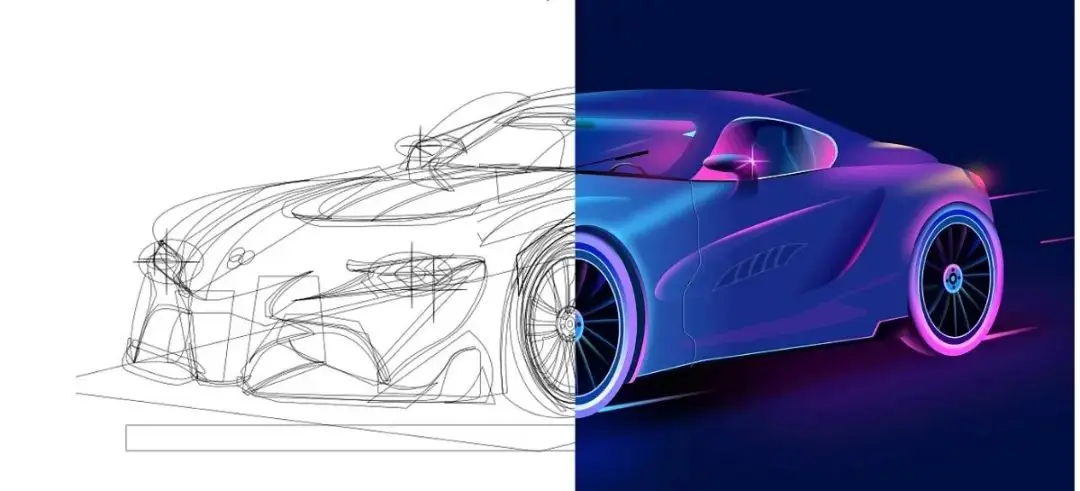
2025-2050年高强度钢拉伸强度2500~3000MPa,密度下降10%,模量增加20%;铝合金机械性能提升200%,成本降低40%,高性能铝循环利用100%;镁合金成本与钢相当,可用性提升4倍,采取通用的一步式预处理;钛合金、镍合金成本降低至铝合金水平,成本是不锈钢1.5倍;碳纤维占车重15%~25%,单价2.5美元/磅,刚度与铝材相当,50%可再生,碳足迹降75%。
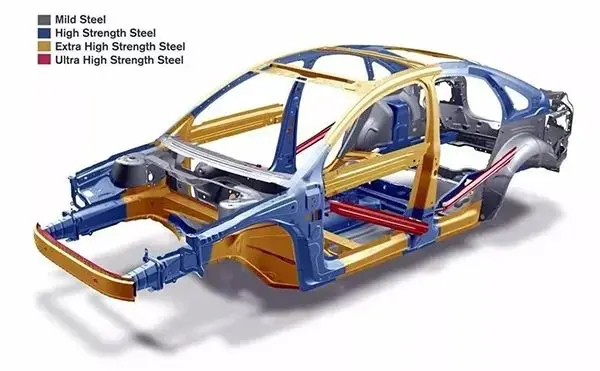
美国的轻量化路线以材料降本与性能优化贯穿其中,美国汽车零部件制造的特点是综合考虑不同材料的性价比在汽车的不同部位得到应用。
欧洲:瞄准多材料应用技术
欧洲汽车轻量化路线,以先进的钢铁材料、轻金属镁铝、碳纤维强化复合材料三类先进轻量化材料应用为出发点,目标瞄准多材料应用技术。
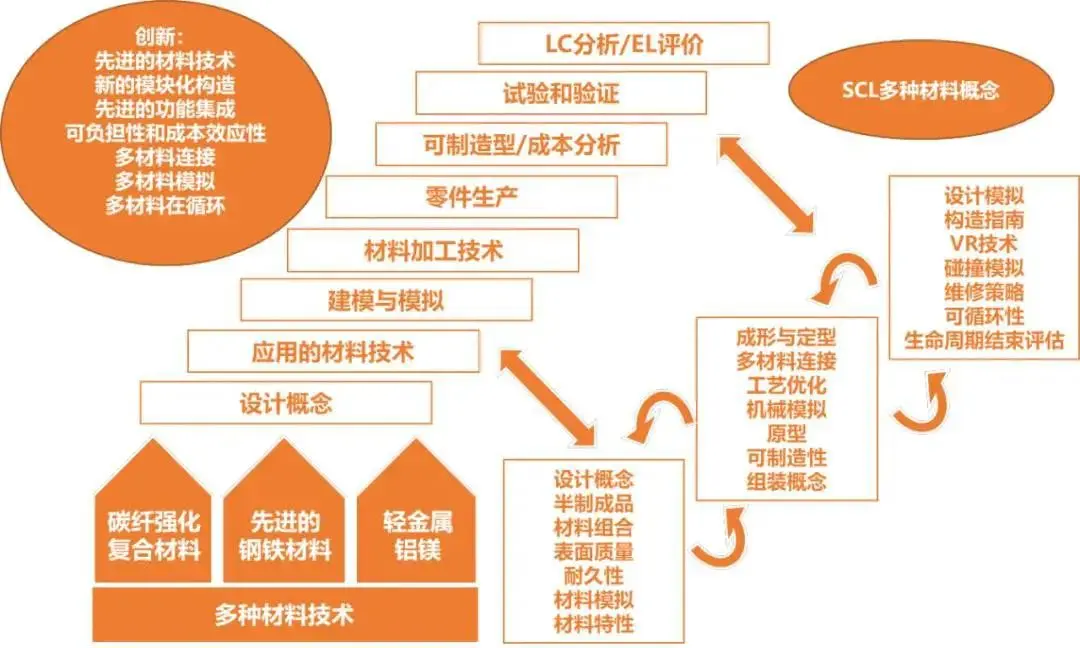
表2 欧洲汽车轻量化路线
欧洲汽车轻量化的发展路径以创新为驱动,围绕先进的材料技术,新的模块化构造,先进的功能集成,可负担性和成本效应性,多材料连接,多材料模拟,多材料再循环。材料的开发与应用过程包括:设计概念,应用材料技术,建模与模拟,材料加工技术,零件生产,可制造性和成本分析,试验和验证,LC分析与EL评价。欧洲的汽车轻量化路线充分结合材料特性与成本、制造工艺和结构设计,多层次多角度协调实现轻量化的目标。
日本:材料和工艺实用化
日本汽车轻量化路线,以材料和工艺的基础研究突破为实用化出发点,材料进步驱动轻量化。
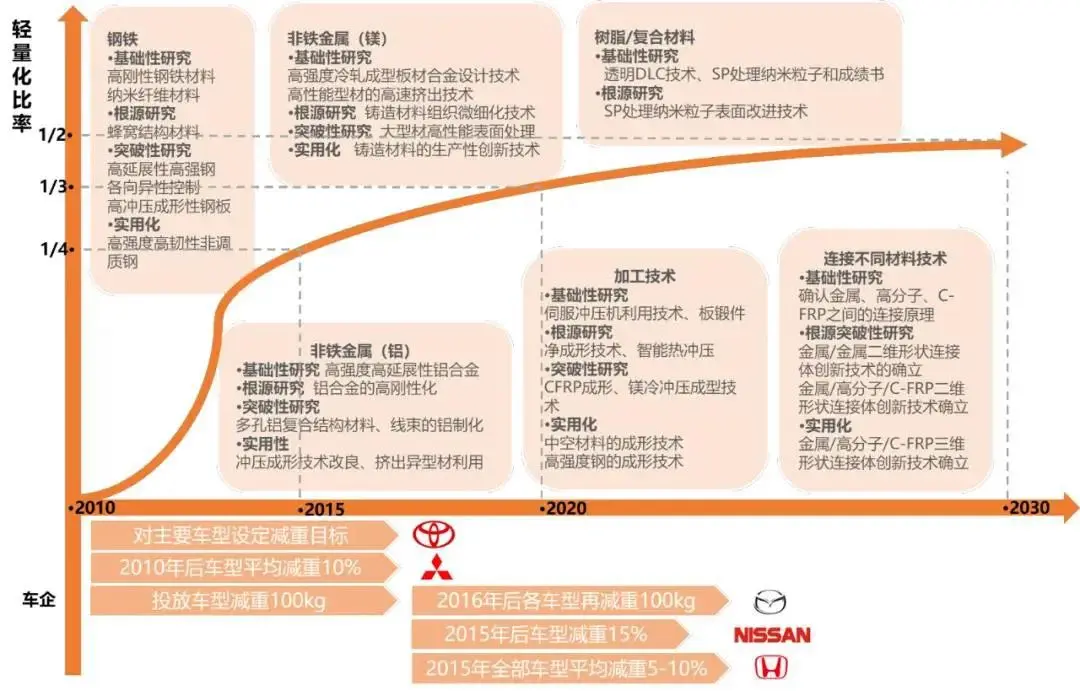
表3 日本汽车轻量化路线
钢铁以高刚度钢铁材料、纳米纤维材料为基础性研究,以蜂窝结构材料为根源研究,以高延展性高强度钢、各向异性控制、高冲压成形性钢板进行突破性研究,开发出高强度高韧性非调质钢。
铝以高强度高延展性铝合金为基础性研究,以铝合金的刚强性化为根源研究,以多孔铝复合结构材料、线束的铝制化进行突破性研究,实现冲压成形技术改良、挤出异型材利用。
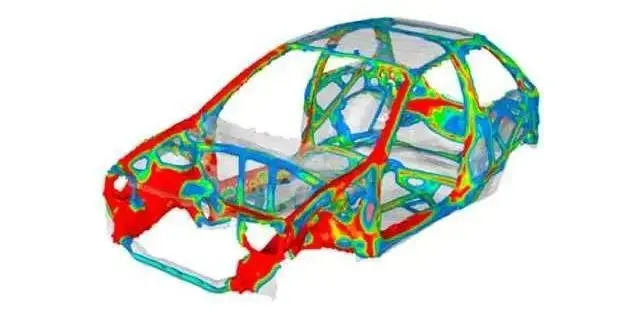
镁以高强度冷轧成型板材合金设计技术、高性能型材的高速挤出技术为基础性研究,以铸造材料组织微细化技术为根源研究,以大型材高性能表面处理进行突破性研究,实现铸造材料的生产性创新技术。
复合材料以透明DLC技术、SP处理纳米粒子和成绩书为基础性研究,实现SP处理纳米粒子表面改进技术。
加工技术以伺服冲压机利用技术、板锻件为基础性研究,以净成形技术、智能热冲压为根源研究,以CFRP成形、镁冷冲压成型技术进行突破性研究,开发出中空材料的成形技术、高强度钢的成形技术。连接不同材料技术经过基础性和根源突破性研究,确立了金属/高分子/C-FRP三维形状连接体创新技术。
2010年以来,日系整车厂商也相继提出轻量化目标,本田对主要车型设定减重目标,三菱各车型平均减重10%,马自达连续两个5年实现投放车型减重100kg,尼桑2015年后车型减重15%,丰田2015年全部车型平均减重5%~10%。预计自2010开始, 2015年、2020年、2030年分别实现轻量化比率1/4、1/3、1/2。
中国:材料-设计-工艺协同发展
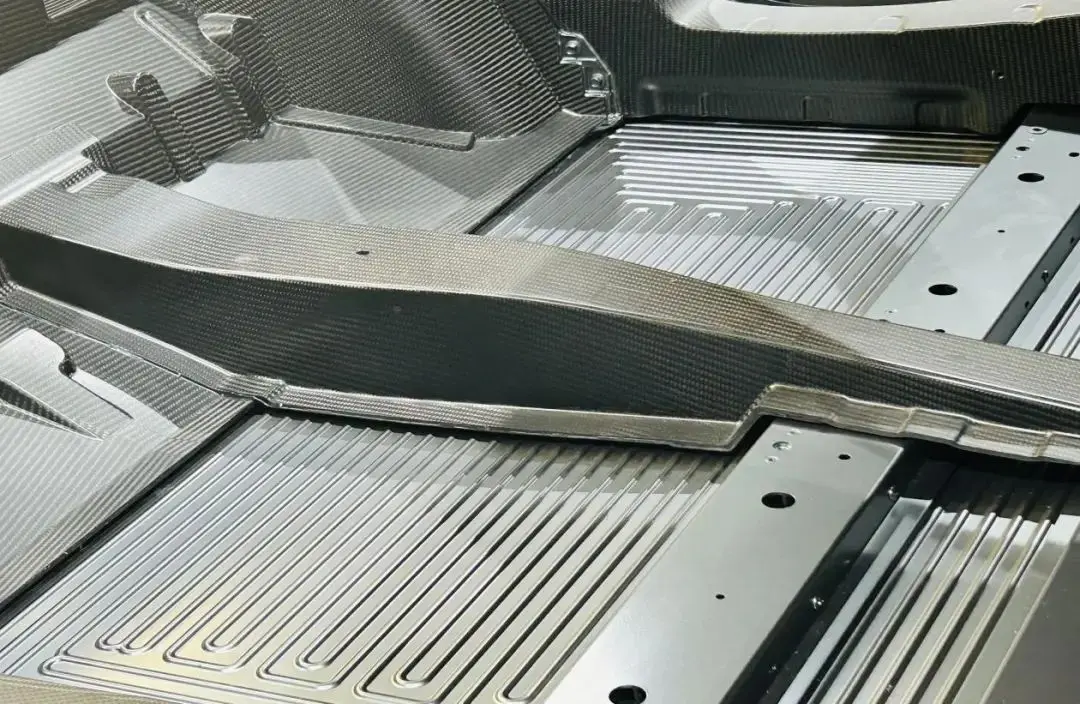
表4 中国汽车轻量化路线
根据中国汽车工程学会发布的《节能与新能源汽车技术路线图》,中国汽车轻量化自2015年到2020年实现减重18%,适量应用铝、镁合金及碳纤维增强复合材料,根据材料特性和性能要求进行优化设计,工艺以冷成形为主,热成形、辊压成形、激光拼焊为辅。
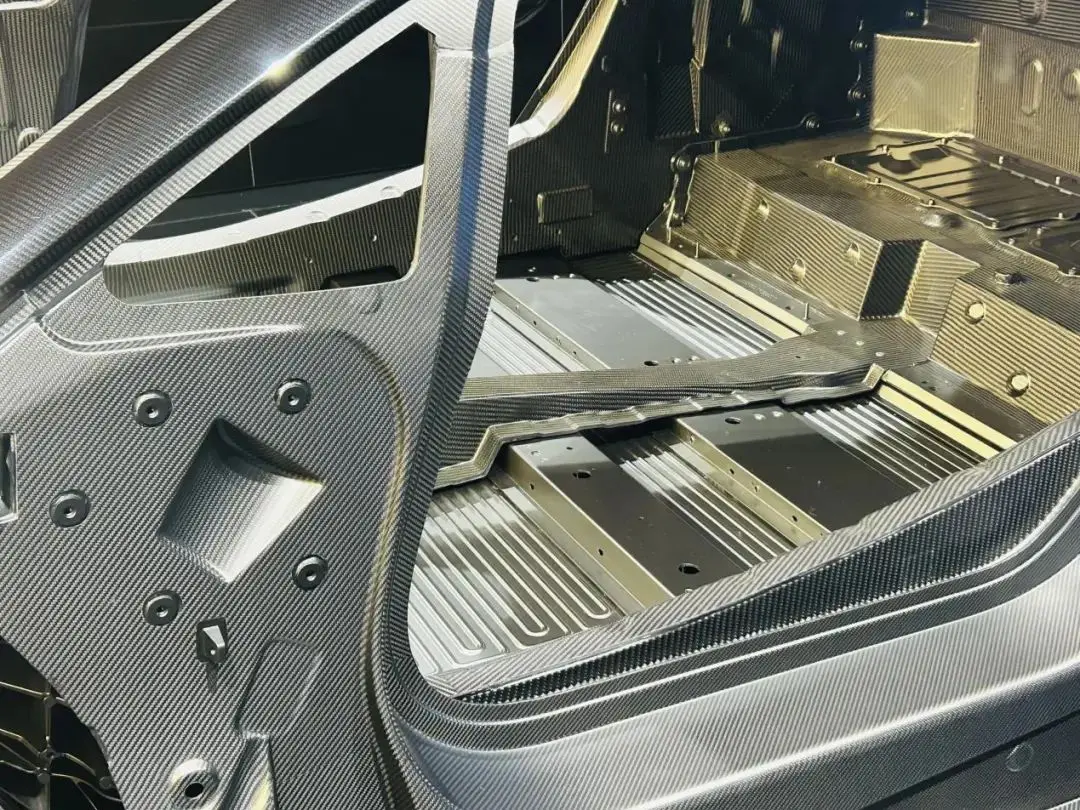
到2025年实现减重30%,扩大铝、镁合金与碳纤维增强复合材料在车身上的应用,采用结构-材料-性能一体化轻量化多目标协同优化设计,工艺以热成形、温成形、内高压成形为主,挤压成形、弯曲成形及热固性纤维材料成形为辅。
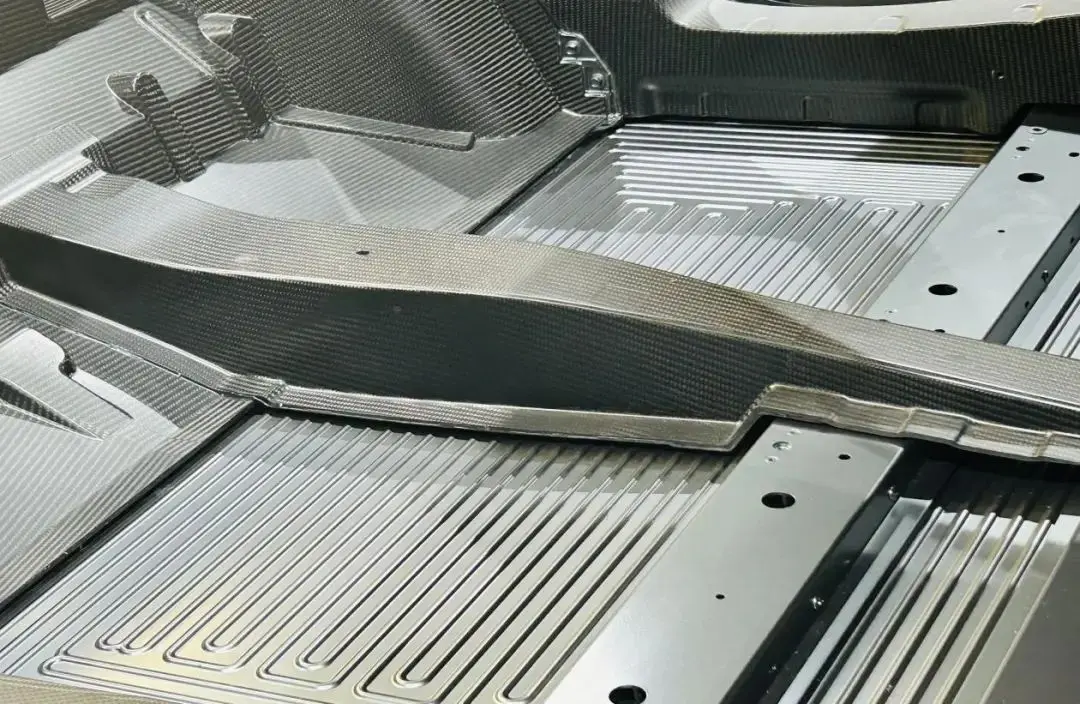
到2030年以纤维复合材料为主、轻合金和高强度钢为辅,结合制造工艺和成本控制要求进行集成化设计,以热塑性纤维材料成形及挤压成形、弯曲成形为主,温成形、热成形为辅。在政策的驱动,对轻量化的迫切需求下,铝合金压铸市场容量有望扩大,有较强材料制备、设计能力并且掌握先进工艺的铝合金压铸企业发展潜力大。
- 下一篇:汽车电动座椅电机供应商20强
- 上一篇:热塑性复合材料在汽车车身面板中的应用与创新
-
旭化成首战全球供应链管理大赛斩获佳绩
2025-03-03 -
旭化成授权斯尔邦高纯度碳酸盐生产技术,助力二
2024-12-13 -
华为尊界S800的座椅会有什么亮点?
2024-11-27 -
博世最新宣布裁员7000人
2024-11-06
编辑推荐
最新资讯
-
[转载] 机床巨头埃马克:百年跌宕再
2025-03-31 12:42
-
从4S店到修理厂:FLIR ONE Pro USB-C
2025-03-28 16:05
-
比亚迪发布2024年ESG报告 以技术创新
2025-03-26 16:44
-
电装中国:以“技术+生态”双引擎驱
2025-03-24 19:07
-
杜尔中国海外项目-Stellantis 集团摩
2025-03-20 11:59