汽车高强钢发展现状及国内外典型钢制轻量化车身开发案例
1 汽车高强钢发展现状和趋势
应用于汽车领域的高强钢根据强化机理的不同,可分为普通高强钢(HighSpeedSteels,HSS)、先进高强钢(AdvancedHighStrengthSteel,AHSS)和超高强钢(UltraHighStrengthSteel,UHSS),相关钢材类别及其强度分布如图1所示。其中,先进高强钢、超高强钢具备较高的强度和成形性,是实现车身轻量化和保证安全性的重要材料。近几十年来,汽车用先进高强钢是材料的研发重点,世界钢协根据研发历史及其特点,将其分为3代:第1代以铁素体为基的AHSS钢的强塑积为10~20GPa·%;第2代以奥氏体为基的AHSS钢的强塑积为50~60GPa·%,其合金含量高和生产工艺控制困难导致成本高;第3代AHSS钢以提高第1代AHSS钢强度、塑性和降低第2代AHSS合金含量、生产成本2方面为目标进行研发,第3代多相AHSS钢通过多相、亚稳和多尺度的组织精细调控,其强塑积为30~70GPa·%。目前,国内钢厂已经具备DP、CP、TRIP、TWIP、Q&P、MS等先进高强钢的生产能力,分别用于内外覆盖件、各种结构件和梁类等汽车零部件。其力学性能覆盖面非常宽,满足汽车对强度、刚度、碰撞吸能安全性、舒适性和可加工性的要求,给汽车用材与选材提供了更多的选择。
目前,国际主流车型的高强钢占车身的比例已超过70%,其中自主品牌中高强钢的应用已达45%。中国是高强度钢应用最普遍的国家,车身使用比例接近50%,预计未来将达到60%~65%,但是超高强钢和先进高强钢使用比例大幅落后,目前仅有5%,预计未来有3倍提升空间。业内专家认为在抗碰撞性能、加工工艺和成本方面,先进高强钢与超高强钢比铝镁合金具有明显的优势,能够满足减轻汽车质量和提高碰撞安全性能的双重技术需要,甚至从成本与性能角度来看,是目前满足车身轻量化、提高碰撞安全性的最佳材料。
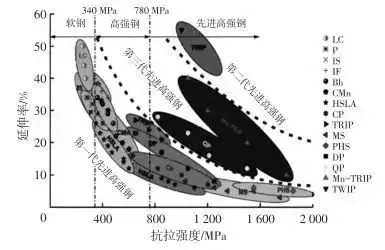
图 1 先进高强汽车用类别及强度分布
对近年来“欧洲车身会议”和“中国轻量化车身会议”展示车型相关用材数据进行了统计分析,我国乘用车高强钢的应用水平已经达到世界先进水平(图2),欧洲车身会议展示产品的高强钢用量平均为56.7%,最高为73%,中国轻量化车身会议展示产品的高强钢用量平均为62%,最高为70.4%。因此,高强钢在车身上的应用方面,中国处于领先地位,显示了我国汽车企业高强钢的应用水平大幅度提升,从材料生产到零件加工生产体系的日臻完善。
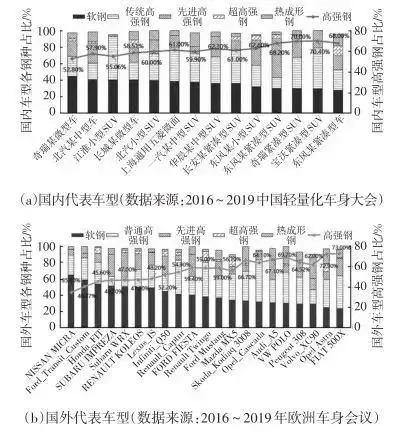
图 2 全球典型钢制车身的高强度钢应用情况
从国际上看,尽管已经有了许多铝合金和碳纤维等材料应用的成功案例,但高强钢仍然在企业用材策略中占据重要地位。从图 2 可知,各大主机厂在车身用材选择和成形工艺选择方面存在不同,而决定其高强钢用材策略的关键因素是钢铁企业的产品规格、性能、价格以及供应链的支撑能力。
综合以上分析,随着我国高强钢生产技术的不断发展,在汽车钢品种和强度级别等方面已经与发达国家基本相当,我国在具有高强度、高塑性特征的第 3 代钢开发和生产方面具有的世界领先优势为世界所公认,也为我国进一步推动高强钢的应用提供有力支撑,以高强钢相关的一批团体标准的颁布及汽车用钢上下游产业链 EVI 领域的持续发展,将为车企扩大高强钢应用提供技术依据和材料保障。相信随着“高强钢回弹”“延迟断裂”等核心技术问题的认知与解决,将为高强钢在我国新能源汽车产业内的进一步应用开拓更大的空间。
2 国内外典型钢制轻量化车身开发案例
为提升自身整车EVI技术水平,增强企业选材和提供钢铁轻量化综合解决方案的能力,近十年来国内外主要钢铁公司先后开展了多款钢制轻量化车身与综合解决方案项目,典型的有浦项PBC-EV、蒂森In-car、安米S-inmotion、宝钢BCB系列和马钢MCEV等。
2.1 浦项 PBC-EV 和 eAutopos 项目
2010~2012年,浦项开发了首款PBC-EV(POS⁃COBodyConcept-ElectricVehicle)纯电动概念白车身(图3)。PBC-EV车身采用了先进高强钢及热成形、变截面柔性辊压成形、液压成形、激光拼焊等先进成形技术,实现轻量化的同时提高了安全性。PBC-EV白车身高强钢比例达到65%(其中超高强钢超过40%),车身质量由296kg降低至218kg,在成本小幅增加的同时能够实现质量降低26%;从制造到报废回收后的LCA全生命周期评价中温室气体排放量减少约50%。
图 3 浦项 PBC-EV 白车身
2021年,浦项发布了其新的生态友好型电动汽车(含纯电动汽车和燃料电池汽车)综合解决方案eAutopos(eco-friendly,ElectrifiedAutomotiveSo⁃lutionofPOSCO),主要产品包括车身和底盘用高强汽车板、电池包专用钢材、驱动电机用节能高效电工钢、氢能电动汽车用金属双极板和二次电池用正负极材料等(图4)。针对白车身,eAutopos解决方案为使用多种先进超高强钢增强车身强度和碰撞安全性。例如,对于吸收车辆前部冲击力的前纵梁采用了980XF钢,座椅横梁和仪表板横梁外侧件则采用了MS1500等超高强度冷轧板,前侧围延伸件采用了1500MPa热成型钢。经过轻量化设计后,白车身质量降低至207kg,降低30%。针对悬架系统,eAutopos解决方案为采用其研制的高性能轴承钢、悬架弹簧、轮胎帘线钢等,在实现轻量化的同时保证了部件良好的加工和使用性能。
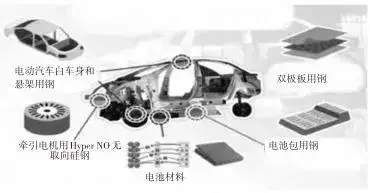
图 4 eAutopos 电动车综合解决方案
2.2 蒂森 In-car 项目
2009年,蒂森启动了面向汽车生产商的创新项目“In-car”。项目聚焦轻量化、降本、减排和提高性能,并引入生命周期分析(LifeCycleAssess⁃ment,LCA)理念,开发出了30多种车身、底盘及动力系统的创新解决方案,使整车质量减轻一半的同时成本降低20%(表1),在汽车整个生命周期可减少CO2排放量1.6t。
In-car项目是蒂森的菜单式轻量化解决方案,它对车身、悬架、动力总成3大系统的16个主要部件均进行了轻量化设计,每个部件给出了1种以上的解决方案,且每种解决方案提供了对标车和In-car解决方案的用材、质量、成本和排放情况,用户可以根据应用目的、生产和工艺条件选择不同的解决方案。
2.3安米S-inmotion项目
从2010年开始,安米陆续开发了S-inmotion系列车型(包括燃油车、电动车、轿车、SUV、商用车)轻量化解决方案(图5),主要通过先进高强钢的轻量化设计应用,为用户提供安全、轻量化、低成本、满足可持续发展的全面解决方案。
以2015年北美市场典型SUV和中高级轿车为例,通过S-inmotion解决方案,SUV可实现车身质量降低112kg(比例为21%),高强钢比例由33%提升到51%;轿车有望实现车身质量降低100kg(比例为28%),高强钢比例由68%提升到74%,全生产周期碳排放减少13.5%。
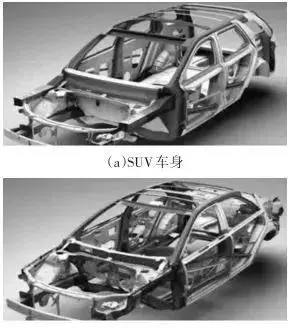
图 5 S-in motion 轻量化方案
2020年,安米推出了全新的S-inmotion纯电动汽车钢制电池包解决方案(图6)。该方案应用多种高强钢,其中关键部位(骨架、底部)使用先进高强钢(包括2GPa铝硅镀层热成形钢和500MPa马氏体钢),在满足性能的前提下有效控制电池包质量,电池盒结构仅占总电池包质量的20%。通过对零件的截面设计优化,大大降低了模具的成本投入;梁结构采用辊压成形工艺,底盖板等采用方板件设计及简单的浅冲压或开孔工艺,使得电池包整体材料利用率达到90%以上,可有效控制成本。
2.4 宝钢 BCB 系列项目
2015年,宝钢推出了首款超轻型概念白车身BCB(BaosteelCarBody),是国内钢铁企业首次按照汽车设计流程和规则,整合新材料、新工艺和新结构优化技术而完成的白车身,在安全性、舒适性和轻量化方面达到国际先进水平(图7、表2)。
BCB白车身质量为284kg,车身大量应用3代汽车用钢,包括MS1500、B1800HS、TWIP950、QP1180等新材料,高强钢应用比例为77%;在成形工艺方面,应用了热冲压成形、液压成形、辊压成形、VRB板成形和激光拼焊板成形等先进成形技术。通过高强减薄轻量化设计,保证整车性能的同时,实车轻量化系数达到2.7。
图 6 轻量化钢制电池包方案(S-in motion)
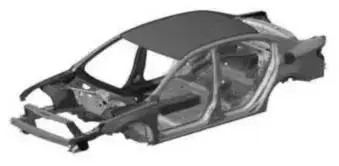
图 7 宝钢 BCB 白车身
表 2 宝钢 BCB 白车身设计指标
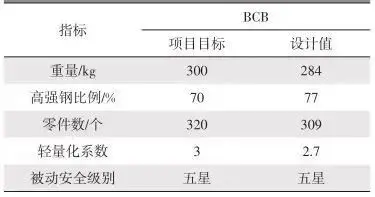
2021年,宝钢向全球发布了超轻型纯电动高安全车身BCB-EV(BaosteelCarBodyElectricVehi⁃cle)。BCB-EV以先进材料、成熟工艺和结构优化为创新点,打造了以吉帕钢为主的超轻型高安全纯电动车身(图8)。BCB-EV白车身吉帕钢比例超50%,电池包框架吉帕钢100%,最高强度热成形材料用到2000MPa级别,冷成型材料应用到1700MPa级别;先进高强钢与7种先进成形、不等厚轧制、拼焊工艺相结合,实现白车身质量达到303kg(质量降低57kg,降低比例10%~20%),轻量化系数达到2.13,满足整车C-NCAP2021五星碰撞安全、25%小偏置碰GOOD性能要求,实现钢板生产环节CO2减排200kg,电动车使用环节CO2减排296kg。
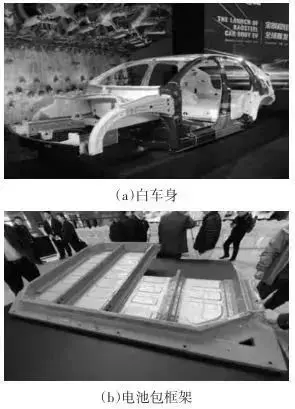
图 8 宝钢 BCB-EV
2.5 马钢 MCEV 超轻型电动概念车开发
为了积极响应汽车行业轻量化需求,充分展示利用钢铁的设计灵活性以及使用高强钢来解决新能源汽车轻量化面临的难题,2018年马钢联合中国汽研、中信金属等启动了马钢电动概念车(MasteelConceptElectricVehicle,MCEV)电动概念车开发项目。项目选取一款全球先进的电动车为标杆,并结合行业电动车先进技术水平,开发一款基于马钢汽车钢体系的轻量化、高性能、高安全、经济型A级电动概念车(图9)。 MCEV设计车采用全钢车身设计,用钢布局讲究“将合理的材料应用于合理的部位”原则,进一步提升高强钢的比例,达到轻量化效果。其中前横梁、顶盖中横梁、外门环、门槛梁外板等安全部件采用马钢1500MPa级、1800MPa薄镀层、高冷弯、抗延迟开裂热成形钢。MCEV设计车采用了48.08%高强钢、22.33%先进高强钢、13.22%热成形钢,高强钢占比达83.63%(其中含Nb高强钢比例61%),如图10所示。
图 9 MCEV 新能源概念车
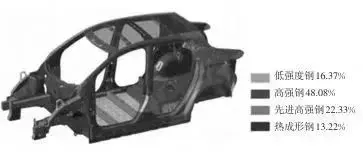
图 10 MCEV 白车身用材比例
在车身设计上,通过CAD/CAE/SE等计算机技术对白车身的结构和布局进行优化分析,通过采用传力路径优化设计、结构截面优化设计等,在实现轻量化的同时进一步提升了车身的安全性。MCEV设计车前防撞梁加长、增加副吸能盒,在MPDB工况下,可使碰撞力的传递更加均衡,在小偏置碰撞工况下,抗撞性能有所提高,如图11、图12所示。MCEV设计车上纵梁延伸到纵梁前端板形成闭环环状结构,有效提升抵抗小偏置碰撞的能力;前舱横梁的拉通横梁结构提升了抵抗变形能力,分散传力路径,增强安全性能,提高扭转刚度;贯穿式的高强钢座椅横梁与B柱、顶盖中横梁形成环状结构,提高局部刚度性能和抗变形能力,有效实现载荷分流,极大增强整车刚度,如图12所示。 经轻量化设计,MCEV白车身质量为265kg,质量降低10.9%,轻量化系数为2.62;整车正面100%碰撞、柱碰、MPDB的性能达到C-NCAP五星水平,25%小偏置碰、顶压性能达到中保研汽车碰撞安全指数(C-IASI)优秀水平,白车身(带玻璃)扭转刚度≥23000N·m/(°)、弯曲刚度≥15000N/mm,白车身(带玻璃)扭转模态≥36Hz、弯曲模态≥52Hz,具有较高安全性。
图 11 MCEV 设计车碰撞传力路径
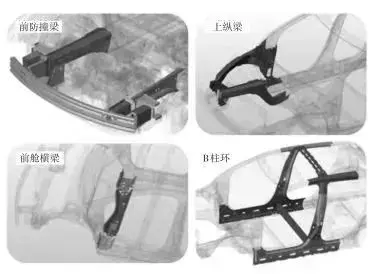
图 12 MCEV 设计车前防撞梁、上纵梁、前舱横梁、B 柱环
MCEV设计车的主要技术性能指标与其它新能源车型对比如表3所示。MCEV概念车不论在轻量化(质量)、安全性能(扭转刚度)、高强钢占比等方面的技术指标水平均优于标杆车,达到国际先进水平。
表 3 多款新能源车的高强钢占比、车身质量、扭转刚度、轻量化系数
3 结束语
轻量化是以电为核心的新能源化是汽车节能减排的有效途径,也是未来全球汽车工业发展的必然趋势。高强钢由于其高承载安全性、高工艺适应性、高性价比综合优势,可预见未来至少15年甚至更长时间内依旧是全球节能和新能源汽车材料行业的最重要发展方向之一。未来随着汽车产业的电动化这一大势所趋,节能减排、“碳达峰、碳中和”政策的实施,以及先进高强钢性能和应用技术愈发成熟,其必将在汽车轻量化领域发挥更大的作用。基于新时代的EVI理念,协同上下游产业链,以国家行业发展政策及终端用户市场共性及个性化需求为牵引,打通不同类别汽车用钢之于终端车型产品的应用瓶颈链,为终端用户提供汽车钢成套应用技术解决方案,达成在车型上的集成应用是目前全球汽车钢业界的热点、焦点领域。近十年来国内外主要钢铁公司先后开展的多款钢制轻量化车身项目,展示了不同优秀钢制轻量化解决方案的实践案例,大大促进了全球各类钢制车型领域的整体轻量化技术水平,尤其促进了各类先进汽车高强钢的持续推广应用。 相对于传统的燃油汽车,新能源汽车在钢材应用总体层面不存在本质差异性,但是还是会体现出一定的个性化。首先,新能源汽车基于三电系统的存在,其对轻量化和安全性的要求更高,尤其随着近年来中保研汽车碰撞安全指数(C-IASI)等更苛刻碰撞安全性能评价方法标准的逐步推广,强度级更高的钢种将集成应用于新能源汽车车身和底盘系统。其次,新能源汽车将增加对高品质电机用硅钢片的消耗。
上述新能源车的结构特性将会对钢企的产品发展策略产生影响。近年来国内如热成形薄铝硅镀层板、DH钢等单一品种汽车钢的研发及推广及以马钢MCEV项目为代表的超轻质、高性能、低成本,满足市场需求的新能源汽车用钢集成技术解决方案,均是国内汽车钢业界走出中国特色发展之路的重要探索。综上所述,推进中国汽车钢产业链的协同、又好又快的发展,这显然不是钢铁行业一个领域的事情,必须进一步加强汽车用钢上下游产业链EVI合作力度,不断基于新能源汽车产业的发展涌现出的新需求,研发出对口的新钢种,不断合作突破更多的产业链技术瓶颈,推进我国汽车钢事业迈向新的发展阶段,为中国制造业早日实现“强国梦”,达成“双碳”宏伟目标注入强劲的科技动力。
- 下一篇:汽车生产制造流程图
- 上一篇:汽车智能底盘:未来技术趋势
-
埃马克德国总部迎来中国社科院工业经济研究所代
2025-04-15 -
埃马克这项全新应用即将在CIMT惊艳首秀!
2025-04-15 -
[转载] 机床巨头埃马克:百年跌宕再出发
2025-03-31 -
赋能电动未来,埃马克重庆技术日展示尖端制造技
2025-03-03
编辑推荐
最新资讯
-
全球产业链聚沪 共探双碳新路径 SNEC
2025-04-18 18:05
-
柯马签订具有约束力的协议收购 Autom
2025-04-17 13:01
-
高效协同新范式:比亚迪叉车领创智能
2025-04-17 10:04
-
埃马克德国总部迎来中国社科院工业经
2025-04-15 09:40
-
埃马克这项全新应用即将在CIMT惊艳首
2025-04-15 09:37