超高强度钢在汽车轻量化中的应用及研究进展
摘要:新一代汽车对使用的超高强度钢材料提出了更高的要求,需要兼顾轻量化和更好的安全性能,材料的强韧性匹配是实现这一 目标的重要途径 。钢铁材料的强度越高,越容易发生脆性断裂 。通过成分设计优化和合理的热处理工艺匹配可以有效提高材料的 强韧性,减少事故发生 。本文综述了热冲压成形钢、淬火延性钢和冷成形马氏体钢的研究发展,总结了近年来超高强度钢的研究现 状,为高强度、高塑性的先进钢铁材料的研制开发提供参考,并针对超高强度钢的优化控制思路提出介绍和建议 。最后,从超高强 度钢的生产应用、开发现状等方面对超高强度钢的发展趋势进行了展望。
关键词:汽车轻量化;超高强度钢;合金化;热处理;显微组织;力学性能
超高强度钢是指在室温下,抗拉强度高于 1470 MPa、 屈服强度高于 1380 MPa 的合金钢[1] 。汽车零部件使用超高强度钢可实现轻量化,从而提高汽车燃油经济性,减少碳排放 。使用超高强度钢来使汽车减重,满足 汽车轻量化要求,同时提升汽车耐撞性及安全使用性 能 。在 20 世纪 90 年代,北美试制出一种超轻钢汽车车身样品[2] , 车体 90% 采用高强度钢板,减重达 30% , 汽车在弯曲刚性与扭曲刚性方面提高了 1 倍左右,证明了钢材作为未来车辆的结构材料仍具有较大潜力。
乘用车自 身 质 量 每 下 降 10% , 油 耗 降 低 6% ~ 8% , 尾气排放降低 4% [3] 。近 10 年燃油乘用车的整 车轻量化系数总体呈下降趋势,均值由 2010 年的 3. 47 降 低至 2020 年的 2. 39 , 降幅达 30% [4] 。随着汽车工业 的发展,油耗、雾霾、安全等问题随之产生,以及国家安 全法律法规的日趋严格,汽车节能减排和提高安全性 能已刻不容缓,汽车轻量化的技术要求不断提升。
迄今为止,高强度钢的发展已经经历了第一代到 第三代的演变,如图 1 所示 。第一代高强度钢的强塑 积为 10 ~ 20 GPa ·% , 主要包括双相钢、多相钢和相 变诱导塑性钢等;第二代为 50 GPa ·% 以上,主要包 括奥 氏 体 孪 晶 诱 导 塑 性 钢、诱 导 塑 性 轻 钢 和 硼 钢 等 [5] 。第三代高强度钢以马氏体为基体组织,采用微 合金化的手段,通过热处理工艺对组织的调控,利用沉淀硬化、细晶强化等强化机制来获取高强塑积、高硬 度、低成本等优异性能的钢种,已经成为国内外轻量化 汽车用钢的研究重点,但是新型超高强度钢的开发面 临强韧性平衡的难题。

鉴于钢铁材料强度高、塑性不足的问题,国内外研究学者从超高强度钢的工艺⁃组织⁃性能方面进行了一系列试验,为超高强度钢的强塑积研究提供参考 。本文对当前应用在汽车上的 1500 ~ 1700 MPa 强度级热 成形马氏体钢( PH 钢)、淬火延性钢( QP 钢)和低合金 马氏体超高强度钢( M 钢)的合金成分、热处理工艺、 组织性能及超高强度钢的最新研究内容和成果进行了 综述。
01 PH 钢、QP 钢和 M 钢的发展
关于超高强度钢的研究开发,国内外钢厂都进行 了大量的工作 。 日本新日铁、JEF、神户制钢、韩国浦项、瑞典 SSAB 和巴西 ArcelorMittal 等钢铁公司已开发 出各自的超高强度钢产品,并在汽车行业得到应用。 上述当前应用在汽车上的 1500 ~ 1700 MPa 超高强度 钢有热成形钢( PH 钢)、淬火延性钢( QP 钢)、低合金 马氏体超高强度钢( M 钢),如表 1 所示。
热成形钢的研发减小了产品的回弹、开裂问题,技 术路线如图 2( a) 所示 。最开始的热成形钢并未应用 在汽车上,主要用于制造锯片和割草机的刀片[6] 。直到 1975 年,瑞典科学家率先提出了采用热冲压成形工艺制造复杂且易变形的车身安全件和结构件[7] , 直到 1984 年,瑞典 SSAB 汽车公司最先运用该技术制造出 汽车车身零部件门内防撞杆[8] 。1991 年,第一件热成形保险杠用于福特汽车[9] 。 目前应用在汽车上强度为 1500 MPa 级 PH 钢为 Mn ⁃B、Mn ⁃B ⁃Nb、Mn ⁃B ⁃V、Mn ⁃B ⁃Nb⁃V 等系列[10] , 主要应用在后保险杠、A 柱、B 柱、中通道、门内防撞梁、车顶加强梁、纵梁、中通道、门槛 加强梁等构件。
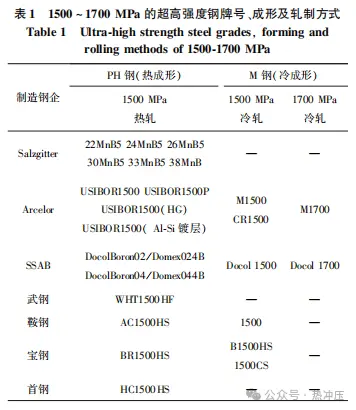
QP 钢的工艺原理可追溯到 Matas 和 Hehemann[11] 最 先发现了钢中碳原子可由马氏体配分至残留奥氏体的 现象,后来 Thomas 等 [12] 通过试验指出,在淬火过程 中,马氏体板条间的残留奥氏体会增碳( 碳由马氏体 板条内向板条界的残留奥氏体扩散)。1983 年,H su 和徐祖耀等[13] 通过计算发现,低碳马氏体形成的同时 会伴随着碳原子的扩散,并且扩散的速度和马氏体形 成的速度相差不多,大约达到 10- 7 s 数量级,这一现象在当时并没有受到重视,但为淬火⁃配分( Q⁃P) 工艺提处理的概念,如图 2( b) 所示,并提出 CPE( Constrained
para⁃equilibrium) 模型 。但是 Hutgren 等 [15] 认为相变( Para⁃equilibrium) 模型,两人后来将 CPE 模型改名为学平衡的标志是碳原子在两相中的化学势相同 。后来徐祖耀院士等[16] 将 Q⁃P 工艺进行了推广,提出了淬火⁃配分⁃回火工艺(Q⁃P⁃T),跟以往的 Q⁃P 热处理工艺
抑制碳化物析出不同,在传统 QP 钢基础上,添加一定量的 Nb、V、Ti 等强碳化物形成元素,在配分(P)结束后进行回火(T),使基体析出碳化物达到弥散强化的效果,其中回火温度( TT)范围可大于、等于或小于配分温度(PT),即 TT > PT,TT = PT,TT < PT。在之后的研究中,研究人员还发现,在碳配分的过程中 A/M 界 面也会发生移动[17] 。 由于回火过程中 Fe3 C 容易析 出,研究人员发现,Si 和 Al 元素能抑制 Fe3 C 碳化物的 形成,但 是 对 其 他 碳 化 物 抑 制 作 用 较 小,因 此,Toji 等 [18] 考虑到渗碳体的析出,又保证其他碳化物的析 出,提出 CCEθ 模型。
当前应用在汽车上的 1500 MPa 级 QP 钢最开始由宝钢生产,现在,鞍钢、河钢等钢铁企业也具备了 1500 MPa 级 QP 钢的生产能力,国内钢铁企业在 QP 钢生产处于 国际领先地位,主要应用在 A、B 柱和加强件。
马氏体最先由德国冶金学家 Martens 于 19 世纪在一种硬矿物中发现[19] , 为了纪念这位著名的冶金学 家,将钢淬火得到的高硬度相称为马氏体 。为了解决 汽车复杂零部件的成形问题,生产了微合金马氏体钢, 其组织以板条马氏体为主,含有极少量的残留奥氏体, 工艺路线如图 2( c ) 所示 。M 钢的成形方式为冷成形 (如辊弯成形),相比热成形,辊弯成形的效率高、成本 低、回弹开裂的趋向性更小 。主要用于 A、B 柱,保险 杠、门槛加强板、侧内门的防撞杆等零部件。
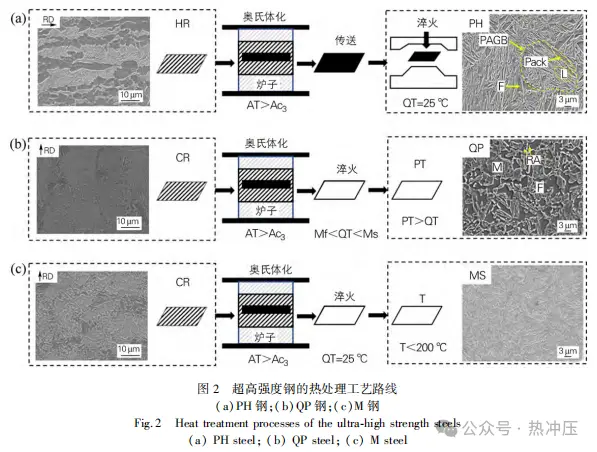
02 PH、QP、M 超高强度钢的研究进展
2. 1 PH 钢
2. 1 . 1 1500 MPa 级 PH 钢的合金成分设计
微合金化对 PH 钢的零件制造极其重要,是实现 高弯曲角度、抗氢脆断裂、高韧性、高淬透性等性能的 必要手段,对纳米级第二相析出、晶粒细化、碰撞安全 性能、断裂失效性能有着重要的作用 。表 2 为当前各 生产商 1500 MPa 级 PH 钢的合金成分体系。
2.1.2 PH 钢组织性能调控
热成形钢的成形过程是一个热力和相变耦合的过程。因为相变与热冲压过程中的塑性变形紧密耦合, 所以热成形钢在连续冷却过程中的相变相当复杂 。近 十年来,在试验方法、动力学和性能预测等方面对热冲 压过程中的相变进行了研究 。相变动力学模型对于预 测热冲压零件的力学性能至关重要 。Liu 等 [20] 的预测 模型可对不同 C 含量下超高强度钢的抗拉强度进行 了预测,表明 C 含量每增加 0. 01wt% ,抗拉强度就增加约 30 MPa,Li 等[21] 、Kirkaldy 等[22] 、Lee 等 [23] 提出的模型 均可以预测变形连续冷却转变后最终相分数和硬度;Li 等[24] 模型预测钢在热处理过程中的显微组织变化; Åkerström 和 Oldenburg[25] 基于 Kirkaldy 等[22] 的速率方程,对基本速率方程进行了修改,预测不同冷却速率下奥氏体的分解产物;Hart⁃Rawung 等[26] 提出模型预测预应变对材料相变的影响;Hippchen 等 [27] 预测了退 火过程中铁素体、珠光体、贝氏体和马氏体的数量和分 布;Neumann 等[28] 基于(TMM) 模型,预测热冲压工艺参 数对最终形状和残留应力状态的影响;Seraj zadeh 等[29] 建 立了基于有限元法和可加性规则的数学模型,用于预测 钢冷却过程中的组织变化;Bok 等[30] 模拟结果表明奥氏 体变形对热压成形板材的最终强度和残留应力分布有很大影响。这些模型为研究不同条件下超高强度钢的拉伸 强度和相变有着重要指导作用。
研究人员通过试验方法研究热处理工艺对 PH 钢的影响 。PH 钢(0. 38C⁃1 . 58Mn ⁃1 . 48Si) 在 300 ℃ 回火时,材料获得最佳的伸长率,强度高达 2000 MPa[31] ; 在 150 ℃/s 的加热速率下,相比 1 ℃ /s 的加热速率,可使 PH 钢的塑性和成形后硬度提高 25. 7% 和 5% [32] 。高的热冲压温度易使原始奥氏体晶粒( PAGS) 粗化,淬 火后导致亚结构的尺寸变大( Lath、Packet、Block) , 从 而导致材料的韧性降低[33] ; 当模具冷速大于 60 ℃ /s 时,PH 钢为全马氏体[34] ; 当奥氏体化温度为 920 ℃ 时,钢保温 2 min 后的组织为均匀板条马氏体,其具有最 佳的综合性能[35] 。形变可加速扩散相变的发生,导致 CCT 曲线向保温时间较短的方向移动,但随着塑性应变 的增加,扩散转变的加速度迅速饱和,且较低的变形温度 和高的应变速率可提高马氏体相变的临界冷却速率[21] 。
2. 2 QP 钢
2. 2. 1 1500 MPa 级 QP 钢的合金成分设计
合金元素对 QP 钢的组织和性能影响很大,适当 加入合金元素可以推迟或促进相变、抑制铁素体生成、 细化晶粒等,提高 QP 钢的性能。各生产商 1500 MPa 级 QP 钢的合金成分体系如表 3 所示。
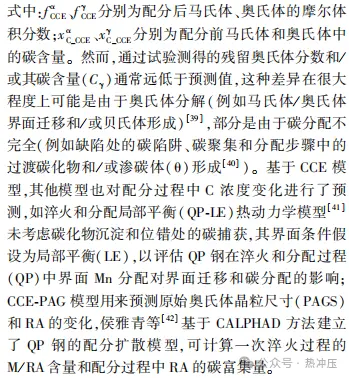
2. 2. 2 C、B、Mn、Si、Al 对 QP 钢的影响
C 含量的高低决定了马氏体晶格的畸变程度,是 影响钢强度的最主要元素;另一方面,间隙碳原子在热 处理的过程中易发生扩散,而配分过程正是利用碳容 易扩散的特性,从马氏体扩散至残留奥氏体,使得残留 奥氏体富碳,获得有利于拉伸性能的稳定残留奥氏体;B 可以显著地提高钢的淬透性,但在 PH 钢中 B 是微 量的,主要是 B 对焊接裂纹的高敏感性所致,B 可提高 钢的硬度,但会降低其冲击性能;Si 含量一般控制在 1 . 5% 左右[36] , Si 在 QP 钢中的作用是复杂的:①过多 的 Si 含量使得 QP 钢碳当量提高,增加了焊缝及周围 热影响区的强度,降低了焊接接头的塑性,导致 QP 钢 的电阻焊效果不理想;②由于 Si 是稳定奥氏体元素, Si 含量的降低将导致奥氏体稳定性下降[36] ; ③Si 能够 起到抑制马氏体中渗碳体析出的作用,在有的研究中 发现,Si 还能延长渗碳体的孕育期,抑制渗 碳 体 长 大 [37] ,使钢拥有高强度的同时保持了较好的伸长率。
M n 含量一般控制在 1 . 8% 左右[17] , M n 在 QP 钢中的 作用主要是提高奥氏体的稳定性 ,推迟珠光体、贝氏 体相变 ,避 免 钢 在 快 冷 的 过 程 中 形 成 低 强 度 相;同 时 ,M n 会降低马氏体相变开始温度 ,有助于提高组 织中残留奥氏体含量 。Al 和 Si 都有推迟渗碳体在 马氏体中形成的作用 ,类似于 TRIP 钢形成无碳化物 贝氏体的机理 ,从而形成了 QP 钢配分的工艺窗口 , 使配分时马氏体中的碳向奥氏体扩散 ,增强残留奥 氏体的稳定性 ,使室温组织中获得最大量的残留奥 氏体 。同时 Al 也是提升马氏体相变开始温度的元 素 ,在合理添加的情况下 ,能够使得 QP 钢的淬火温 度和配分温度相等[38] , 从而达到简化热处理工艺的 目的。
2. 2. 3 QP 钢组织性能调控
QP 钢通过控制快冷温度可以获得最佳残留奥氏 体含量,从而调节 QP 钢的力学性能,为了解释和预测 QP 钢成品中的奥氏体含量,指导制定 QP 钢的淬火配分工艺,Speer 等 [14] 提 出 了 CCE ( Constrained carbon paraequilibrium) 模型:
通过研究 Q⁃P ⁃T 工艺对 QP 钢显微组织的调控,发现增加退火时间,奥氏体的热稳定性降低,从而增加 了回火马氏体( TM) 的体积分数,有效地细化了生成 的微观结构[43] 。淬火和配分后的组织经 350 ℃ 回火后,形成了由马氏体基位错亚结构组成的薄膜,改善了 QP 钢的塑性[17] ; 当回火温度降低至 130 ~ 280 ℃ 时, 饱和马氏体中过量的碳会分配到未转变奥氏体中,促 进过渡碳化物( ε 和 η) 的形成[44] 。通过超快全奥氏 体化 ( 300 K/s ) , 强 塑 积 可 达 25. 7 GPa ·% [45] 。Huang 等提出一种新的贝氏体等温转变 +淬火和分配工艺( B⁃QP) , 即先在贝氏体区等温保持 3 min , 获得无碳化物贝氏体,再经过淬火和配分工艺,最终获得无碳 化物贝氏体、马氏体、薄膜状残留奥氏体的多相组织, 强塑积可达 26. 3 GPa% [46] 。通过不同的奥氏体化温 度进行试验,研究完全奥氏体化和部分奥氏体化对 QP 钢组织的影响,发现完全奥氏体化后的奥氏体晶粒主要 为薄膜状,而部分奥氏体化后则以块状奥氏体为主,且 完全奥氏体化后保留的残留奥氏体更多[47] ; 再结晶温 度以下变形时,可细化 QP 钢的原始奥氏体晶粒并降低 马氏体相变起始温度,同时影响了薄膜状 RA 的稳 定性[48] 。
2. 3 M 钢
2. 3. 1 1500 ~ 1700 MPa 级 M 钢的合金成分设计
M 钢中加入的合金元素极其微量,但实现了超高 的强度和良好的伸长率 。与其他钢的成形方式不同, M 钢采用冷成形方式,应用于汽车 A 柱/B 柱等关键 零部件 。各生产商 1500 ~ 1700 MPa 级 M 钢的合金成 分如表 4 所示。

2. 3. 2 Nb、V 对 M 钢的影响
M 钢中 Nb 元素能在奥氏体区析出碳、氮化物,如 NbC 和 NbN , 通过钉轧奥氏体晶界,抑制奥氏体再结晶 。在高温奥氏体形变的情况下,增加奥氏体的再结 晶储能、晶内点缺陷和位错密度,使得相变的铁素体形 核率更高,形成更加细小的铁素体,并钉轧铁素体的晶 界,抑制铁素体的长大,达到细晶强化的效果[49] ;V 是 一种低温析出的微合金元素,VN 的析出温度较高,也 有钉轧奥氏体晶界,抑制奥氏体再结晶的效果 。VC 的特点是到温析出,没有孕育期,析出温度相对较低, 一般在铁素体中析出[50] , 对控轧控冷的要求不高,较厚的部件中析出可起到沉淀强化的作用 。Nb 或 V 微 合金处理后,钢中马氏体板条束尺寸和板条片间距显著降低,虽然 Nb、V 的添加均能提高钢的力学性能,但 是与含 V 钢相比,含 Nb 钢的回火稳定性较差[51] 。
2. 3. 3 M 钢组织性能调控
马氏体钢的细小 PAGS 不仅能实现细晶强化,还能使相变产品被抑制并被位错马氏体所取代,且产生块状残留奥氏体[4s],对钢的淬透性、强度和冲击性能有显著影响。在 160 ℃/s 的冷却速率下,α'-M 在 MS钢中的含量增加[52],且较高的冷速会减少碳扩散,从而促进马奥岛的产生,使材料的韧性下降[53]。当水淬温度高于710 ℃时,M 钢可获得均匀的马氏体形貌和超高的抗拉强度[54。当 Block 和 Packet 的倾斜度高达-55°时,塑性变形和 TRIP 转变集中在马氏体 Block和 Packet 之间的边界上!」。当加热速率为 100 ℃/s,显微组织由马氏体(60% ) 、下贝氏体(37% ) 和残留奥 氏体(3% ) 组成[56] 。
回火处理对试验用钢的弯曲性能和冲击性能有明 显改善[57] , 但回火温度过高会造成弯曲性能和冲击性 能下降,但对织构没有影响[58] 。通常沉淀强化能提高 马氏体钢的强度及韧性,但纳米沉淀位于马氏体板条 的内部位错和板条边界上;在板条边界上时,如果通道 和边界扩散快速发生[59] ,会导致马氏体钢的沉淀强度 非常小,所以研究人员通过增加合金含量( Nb、V、C、Ti 等),来增加纳米沉淀的数量密度[60] 。但是合金含量 的增加将引发一系列问题,如析出相尺寸变大、碳当量 过高、成本更高和有害相的产生,对于获得具有弥散分 布的纳米沉淀的马氏体钢,传统的固溶时效处理可能 不是最佳选择 。最近的研究表明,通过控制位错密度 来增加基体中共格纳米沉淀的数量和细马氏体板条 数目 ,使 M 钢屈服强度提高了约 24% , 且塑性没有 明显损失[61] 。M 钢中位错促进纳米沉淀的形成过程 如图 3 所示。
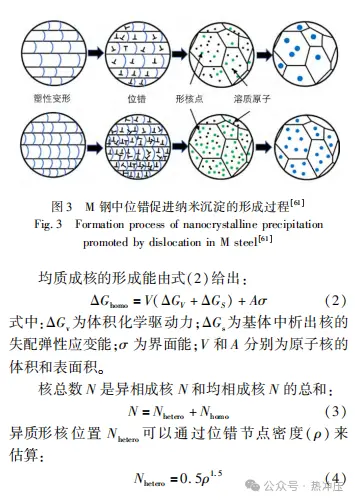
03 结语与展望
本文重点综述了 1500~1700 MPa强度级别的PH钢、0P 钢和 M 钢的发展历程、合金成分体系及组织性能调控的最新研究成果。第三代高强度低合金(HSLA)钢具有超高的强度、良好的耐蚀性和焊接性以及低成本,是汽车轻量化的有效途径。2021年,商用车已经提升总成节油和轻量化应用水平,到2022年底,实现整车材料预期减重 10%[]。鉴于钢铁发展的不断进步,汽车轻量化的要求会更高,因此,钢铁材料在汽车上的应用范围会越广。笔者对新型超高强度钢的研究开发有几点展望:
1) 在超高强度钢强塑化机理研究中,大多数工作集中在探究单一合金元素对钢的作用,多种合金元素在钢中的协同作用研究报道较少,应将计算机模拟技术、合金元素和热处理工艺结合起来调控超高强度钢的晶粒尺寸、板条厚度、残留奥氏体的含量及稳定性和纳米碳化物的弥散分布,以获得最优的综合力学性能。
2) 目前在超高强度钢的生产中,国内现有的生产线已经固定,而超高强度钢的生产需要特殊的生产线(如连续退火超快冷生产线,完全依赖进口),由于产线的价格昂贵,只有个别企业有能力进行超高强度钢的生产,且生产线也只是进行了大幅度的简化,未能充分发挥超高强度钢的最大特点,因此,开发适合超高强度钢的生产线也是必要的。
参考文献
来源/作者:金属热处理 热冲压 作者:唐远寿 , 司 宇 , 徐正萌 , 于硕硕 , 曹鹏军, 栗克建, 冯 毅 , 高 翔
-
埃马克德国总部迎来中国社科院工业经济研究所代
2025-04-15 -
埃马克这项全新应用即将在CIMT惊艳首秀!
2025-04-15 -
[转载] 机床巨头埃马克:百年跌宕再出发
2025-03-31 -
赋能电动未来,埃马克重庆技术日展示尖端制造技
2025-03-03
编辑推荐
最新资讯
-
全球产业链聚沪 共探双碳新路径 SNEC
2025-04-18 18:05
-
柯马签订具有约束力的协议收购 Autom
2025-04-17 13:01
-
高效协同新范式:比亚迪叉车领创智能
2025-04-17 10:04
-
埃马克德国总部迎来中国社科院工业经
2025-04-15 09:40
-
埃马克这项全新应用即将在CIMT惊艳首
2025-04-15 09:37