长安福特热成型数字化车间“煅造”之路
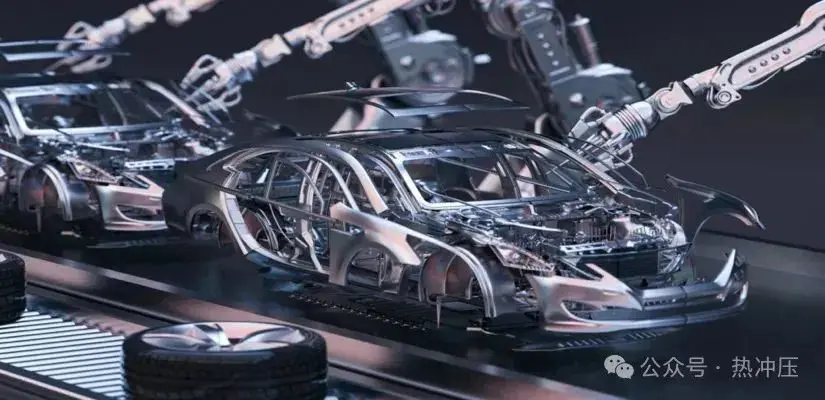
长安福特汽车有限公司热成型车间位于北部新区黄茅坪,总占地面积170亩,总投资约1.04亿美元。包括板料存放、模具/设备维修、热成型生产线、激光切割单元、检具存放、夹具存放、油品存放区域、半成品/成品库房、能源供应、辅房等区域。设计年产能380万件零件,该项目2015年12月动工,2017年10月开始设备安装,2018年5月建设完成,8月开始量产。目前主要为C519/C482/C483/CD542等车型提供热成型零件,共计38种零件。
01 总体架构
热成型车间主要生产设备包括2条热成型生产线和8台激光切割机,蓝光检测单元用于产品和检具的质量检测和控制,Maximo系统用于设备维护计划和维护工单的管理,重要故障的记录和跟踪改善等。通过MES系统将所有的生产设备和来料、半成品、成品、交付等全部集成为一个完整的生产系统,收集相关的数据用于生产组织并生成需要的报表。Maximo系统用于设备、模具、夹具的维护计划和工单的管理,确保设备和工装维护满足生产需要。
车间布局图如下:
根据交付需求由MES系统生成热成型生成计划,由生产计划生成板料需求并通知供应商供应材料,材料到厂后,由热成型生产线生产出半成品零件并入库,扫描下线半成品货箱上的RFID标签生成半成品库存,MES系统根据半成品/成品库存和交付需求生成激光切割生产计划,激光切割机对半成品切边和切孔生产出成品零件并入库,扫描下线成品货箱上的RFID标签生成成品库存。MES系统根据成品库存安排交付。车间数字化装备及网络拓扑图如图。
热成型数字化车间制造过程框图如下。车间从物流系统得到零件的交付需求后,制造系统判断成品库存不足需要生产时,先检查半成品库存,如还是不足,则自动生成热成型生产计划,当半成品库存足够后,再生成激光切割生成计划,当成品库存足够后就可以正常交付。生产计划全自动完成,生产和物流团队按系统的生产计划执行。
02 建设方案
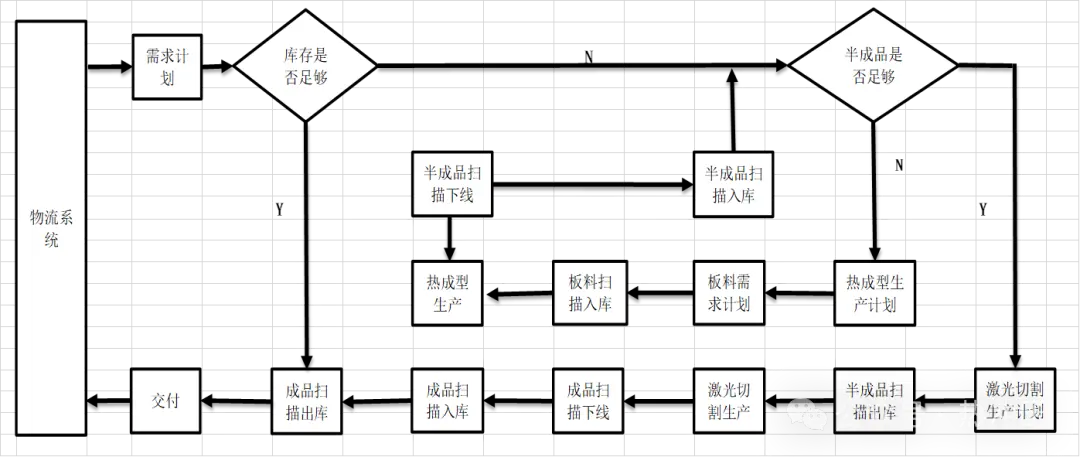
热成型生产线
热成型生产线由西班牙Loire SAFE公司集成,设计速度10~15秒/冲次,每条生产线包含ABB机器人(两台)、Schwartz加热炉、 Strothmann上下料机械手、Loire伺服液压机、线尾传送带等。主要特点:
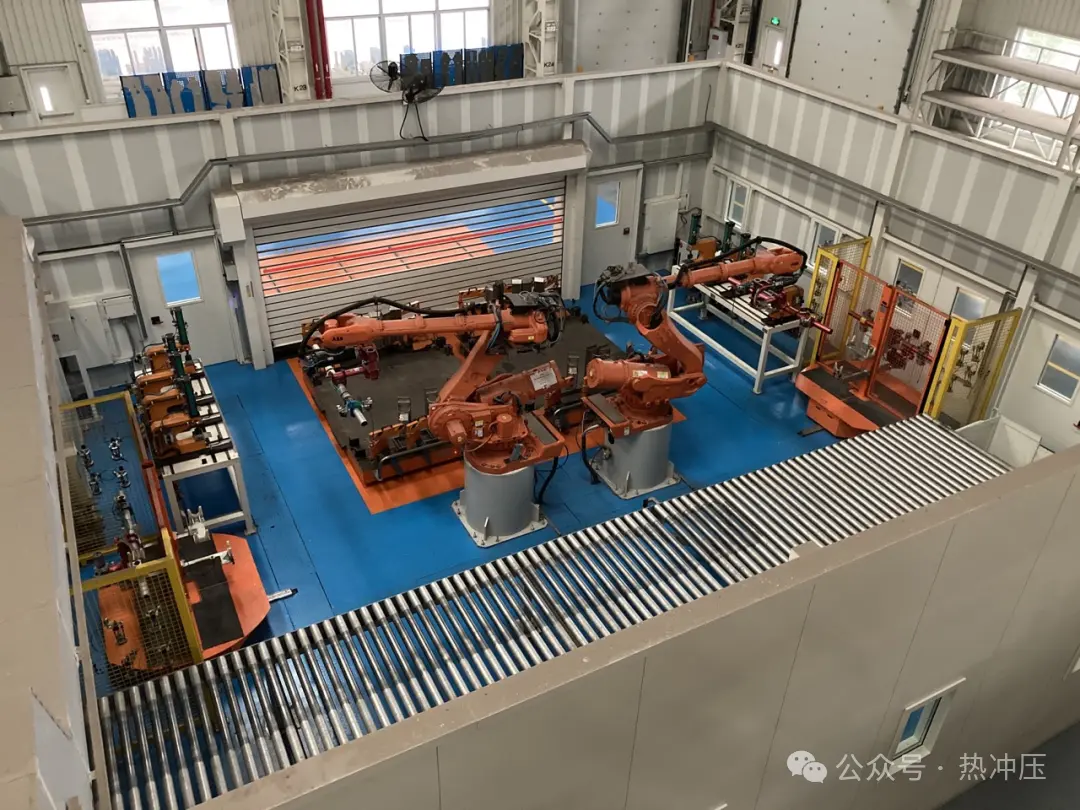
用Profinet网络将整个生产线的各个设备连接起来实现实时通讯和控制,材料上线后,生产线自动完成拆垛、打标、放料、加热、传输、对中、上料、冲压、下料等生产全过程,任何一台设备出现异常,生产线会自动做出响应,避免不合格零件产生,操作者能通过主操作屏看到异常信息,并采取对应的行动。
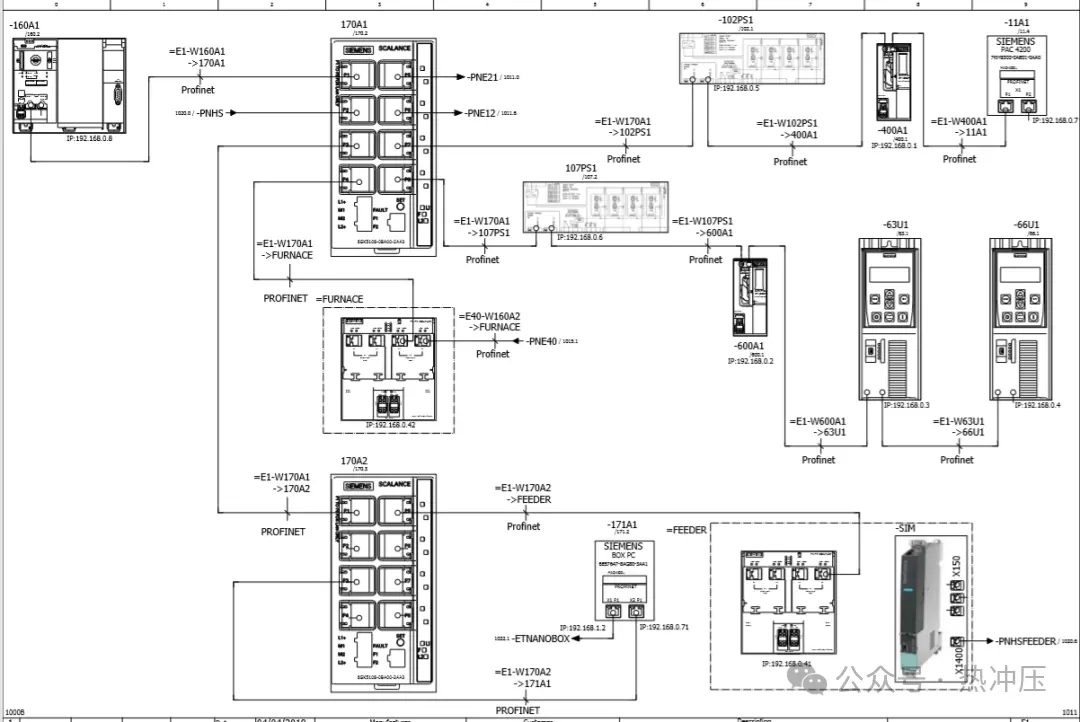
每条生产线都安装有一套高清摄像监控系统对生产线的各个关键生产过程进行监控,用于异常情况的调查和分析。
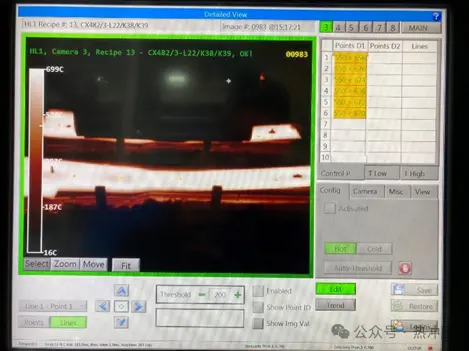
压机上下料过程有一套视觉系统监控板料出炉温度、放料位置、零件下线温度,一旦发现异常立即停止生产,确保产品质量合格。
一键启动全自动换模,生产的零件需要更换时,生产线可自动交换拆垛端拾器、上下料端拾器、模具,拆垛站、加热炉、压机等设备的工艺参数也同步自动交换,换模时间不超过20分钟就可以生产出新的零件。
激光切割单元
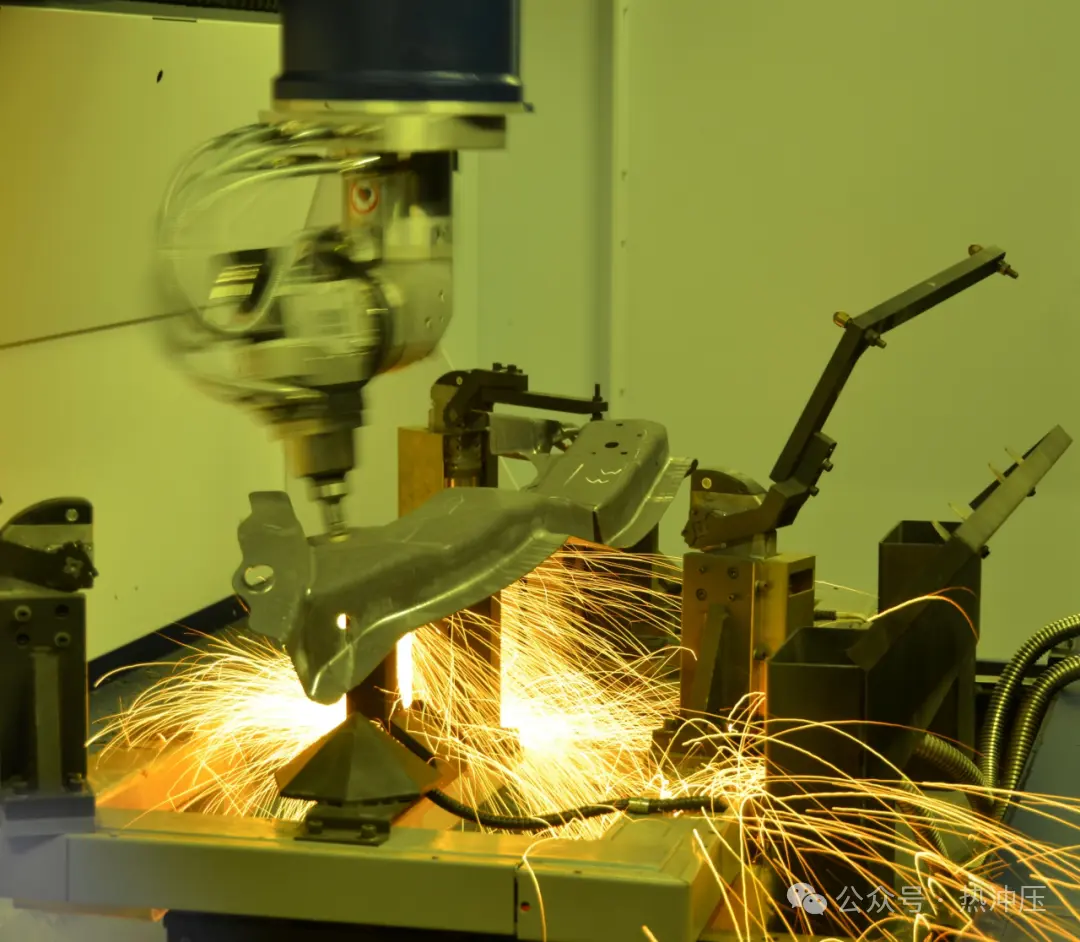
采用TRUMPF(通快)8030激光切割单元,共计8套。该设备是5轴联动数控机床,激光功率3KW,最大切割速度20米/分钟。用激光束对高强度的半成品零件进行孔和边缘的高速切割,该单元采用双转台设计,可以一边切割,一边进行上下料。使用三维仿真软件,根据零件的数模自动生成切割程序,并模拟测试,减少在线编程和调试时间。每台切割机仓内安装有高清摄像头,每4台的摄像系统汇总到一起,可以在线观察切割情况,也可通过回放调查异常情况。
蓝光检测单元
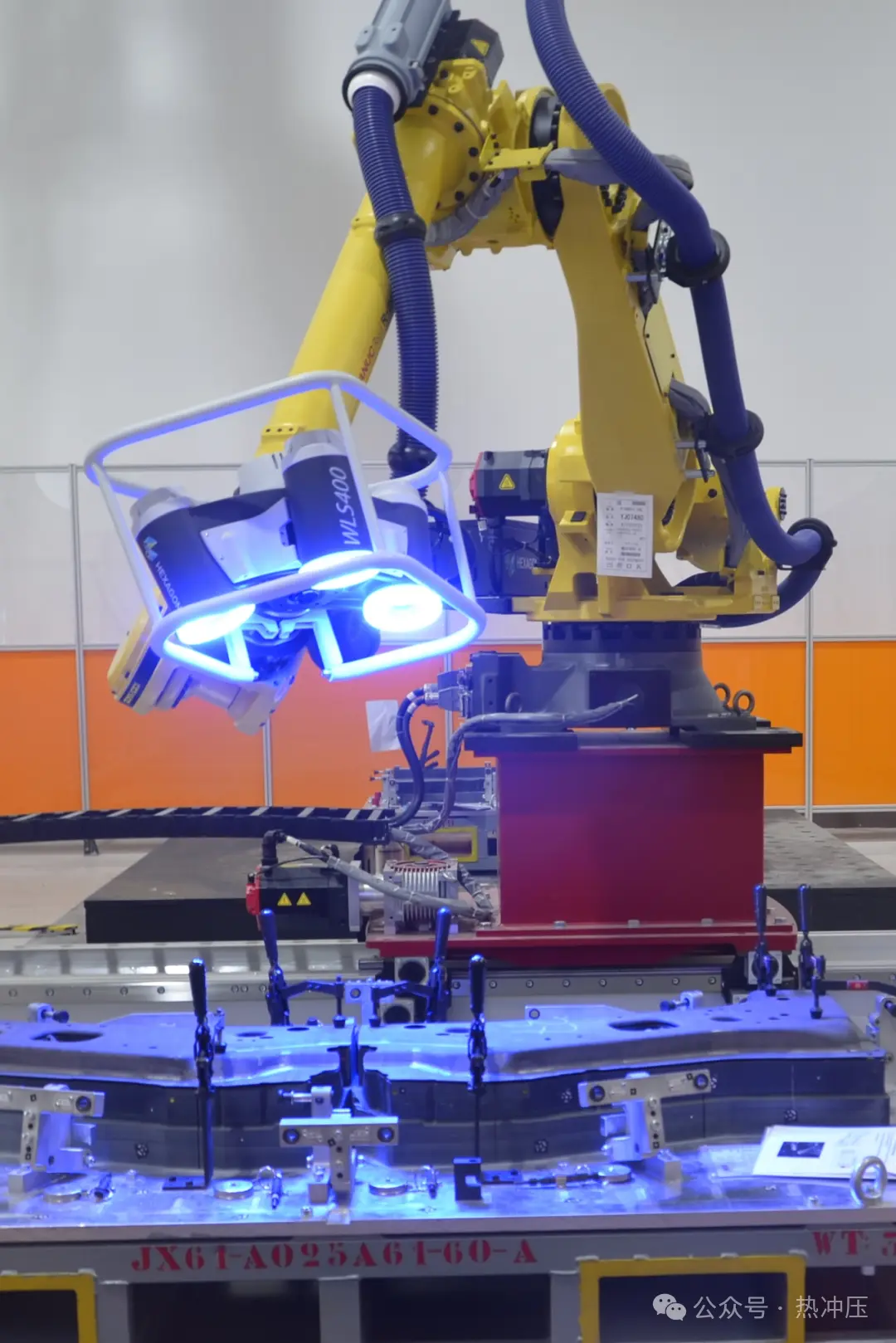
该单元由海克斯康公司集成,主要用于检具的测量(标定)、零件三维全尺寸测量,确保检具使用前的精度,每批次抽检零件进行全尺寸测量,确保零件尺寸合格。
采用FANUC通用6轴关节式机器人,搭载海克斯康蓝光扫描检测系统,双转台设计,可以一边测量,另外一边进行新测量夹具/零件的安装。
使用三维仿真软件,根据测量对象的数模自动生成测量程序,并模拟测试,减少在线编程和调试时间。
根据测量数据统计分析生成报告,用于产品质量的控制和优化。
Maximo系统
该系统为福特公司采用的设备维护系统,用于设备/模具/夹具的维护计划、维护工单的管理、故障分析、事件管理。每周自动生成维护工单,依据工单进行设备维护;出现预定标准的故障时间,进行故障分析并将故障报告录入系统。
生产管理系统(MES)
车间的主要生产设备独立使用无法发挥最大效益,需要一套生产管理系统集成为一个整体,公司授权人员通过办公电脑就可以实时读取所有设备的运行状态,查看需要的生产数据,实现统一的生产管理。热成型车间生产管理系统由重庆微标科技股份有限公司集成。该系统包含以下部分:
车间设备联网与数据采集情况
根据长安福特网络标准,MES系统搭建CPN 网络架构,通过CPN网络连接压机生产线,切割机生产线,质量检测系统,RFID绑定系统,广播大屏,实现私有网络的生产设备互联,实现自动化数据收集,保障系统安全。
获取冲压线、激光切割机生产产量数据,模具数据,夹具数据,进行生产跟踪,可跟踪到各零件模具并进行设备事件识别和维护,并对生产计划统计显示生产绩效,KPI包括:HPH(小时产能)、EO(有效输出)、冲次数、ADCT(平均换模时间)、PPH(小时零件数)、FTT(一次下线合格率)、Throughout To Potential (潜力)、Availability (可用率)、性能效率、OEE(设备综合效率)、设备停线率趋势图、设备停线分布饼图。生产绩效用于用户获知、分析生产过程中问题,指导以后的生产。统计绩效需可按不同生产周期(日、周、月、季、年)、不同生产线、不同班别人员、不同模具统计,并可以以图形导出到Excel文件中或热成型冲压工厂指定格式图形、图表。
生产过程执行情况
车间计划与调度情况:根据当前物料库存、车间消耗计划以及车间排班规则,并结合生产拉动点和零件安全库存信息进行计划排产,系统执行计划与实际生产计划同步。实时监控设备状态,自动切换系统生成计划,保证下线绑定零件信息和生产信息的准确性。在切换期间系统有可靠的放错、防呆措施。
工艺执行情况:自动拉动与e-看板零件拉动类似。根据零件库存,自动结合拉动条件,拉动材料配送计划,并自动用邮件形式发布新计划和计划的变更信息。材料拉动可支持手动拉动,对未自动维护库存的零件材料或系统零件库存不准确的零件材料也能进行计划排产。对材料计划,除自动发布方式外,也支持手动发布。提供生产工单/订单数据导入、拉动点位调整、排产计划调整等功能。
质量管理与追溯情况:覆盖热冲压产线、激光切割机、测量室、实验室以及库存管理全过程,进行质量数据采集、分析,提供正反向追溯等功能;通过蓝光扫描进行全尺寸测量,超出公差的异常情况进行异常提醒并由人员进行异常处理;通过MES系统、RFID系统数据进行零件质量反向追溯;通过MES系统生产计划号对应相应的批次、件号、货架进行绑定,并统一进行管理。
设备管理情况:通过MAXIMO系统进行设备管理、维护工单管理、故障分析、事件管理;每周自动生成维护工单,依据工单进行设备维护;出现预定标准的故障时间,进行故障分析并将4D报告录入系统。
物料配送自动化情况
通过RFID系统实现下线数据的收集,实现冲压零件的下线装箱恭维装箱信息的自动写入,如车型、零件名称、装箱数量、生产日期、生产班次、货架上线下线时间等。通过RFID绑定,管理出入库数据及时间数据,运输车辆及货架进出库房自动读取和计算,并在系统中记录和查询。
根据排产计划、库存管理及物料管理的协同功能,实现对板材和零件的物料拉动。
03 技术难点与创新点
热成型生产在行业内应用的数字化程度不高,在实际生产中存在一些困难,长安福特热成型车间采用了以下先进技术解决了这些困难:
热成型生产线包括多个工序和过程,而1个操作者无法实时监控各个工序的运行情况,我们采用高清摄像监控系统对生产线的每个关键生产过程进行监控,一旦发生异常,可以立即调取录像确认异常情况的过程和原因分析,尤其是用于拆垛过程异常、对中异常、板料入模异常等问题的调查和改善作用巨大。
热成型生产时板料出炉后温度高达930°C,无法用传统的传感器检测板料是否精确放入模具内正确的位置,零件是否从模具内被取走。我们采用热成像系统监控板料的传输,一旦板料未能准确放入模具,或者板料的入模温度、零件的出模温度异常,生产线立即报警停机,避免生产出不合格零件或设备模具的损坏。
由于板料的形状和大小差异很大,每套模具需要采用不同的端拾器,在换模时一般采用人工交换的方式,生产时间损失比较大,我们在拆垛区采用了自动化端拾器交换设计,可以离线安装端拾器,换模时自动交换。对中台阻挡器在换模时,一般采用手动交换,浪费时间且精度不高,我们采用了阻挡器自动调节位置、自动排废料的设计。换模时,模具交换和端拾器交换同步自动进行等先进技术,总的换模时间每次节约10分钟,生产线单班人员配置由5人减为4人。
激光切割机我们采用了动态调节切割头技术,对零件的不稳定有更大的适应能力。切割采用飞行穿刺,减少不必要的空运行时间。自动除尘装置确保车间生产更加环保。
使用蓝光扫描对零件、检具进行定期检测,扫描数据长期保存,可以长期跟踪产品的质量以及产品质量问题的追溯。
其他公司的热成型车间一般没有采用生产制造系统,生产组织运行全靠人工,生产效率低,人工成本高,无法有效的利用所有的硬件资源。我们采用生产制造系统将主要生产设备结合起来,制造过程管理更加快捷灵活,充分发挥了生产设备的性能,大大提高了生产效率,降低了管理成本。
04 解决的重大问题
板料的加热是热成型的关键过程,加热不足或过度都会导致产品不合格,不合理的加热还将导致加热炉传输辊严重损坏,行业内一般采用经验设计加热参数。但我们发现凭经验加热参数很容易导致产品性能不良或不合格,而且导致设备维护成本非常高。
我们将炉温跟踪仪及传感器随板料一起进入加热炉,测量板料在加热炉内的升温过程,收集到大量的数据,并建立数学模型对这些数据进行分析,得到最优化的加热参数。
新的加热参数投入使用以来,加热炉辊子成本从4.68元/冲次降低到0.32元/冲次,成本降低93%。产品的性能指标长期保持稳定,保障了产品的质量。该项技术目前处于国际领先水平。
05 实施效果及效益分析
长安福特热成型车间由于采用了大量先进的自动化技术,各种先进的传感器技术,和数字化技术,整个车间的数字化程度非常高,在国内外都处于领先水平。让我们的制造水平和生产绩效远远好于行业平均水平。
长安福特热成型车间在初期建设时就采用了比较先进的,自动化程度很高的生产设备,主要生产设备100%数控/机器人化。设备安装完成后,再次开启了生产制造系统项目,利用生产制造系统将主要设备集成在一起,实现智能制造,包括车间计划排产、零件库存管理和生产数据采集维护等功能。以看板拉动生产为基础模型,结合以太网、即时通讯技术在热成型冲压车间范围内实现系统化的管理生产数据、设备信息、模具信息、冲压零件和货箱数据等信息,达到管理精细化,提高工作效率、降低生产成本。
通过在热成型冲压车间实施生产制造系统,一方面为企业建立起了生产制造执行管理方面的信息平台,使相关生产制造人员能够适时监控生产现场,实时发现问题,及时处理问题,实现精确生产和控制管理的可视信息化,确保了生产效率及产品的品质稳定。
长安福特热成型车间完成数字化建设后,制造水平大幅度提高,小时产能、有效时间利用率、不良品率、人均产出、运营成本、单位能耗等关键指标都有大幅度的优化,详见下表。
06 下一步进行智能化改造提升的计划和思路
长安福特热成型车间2020年制造成本中,人工成本占总成本的63%,因此进一步提高车间的自动化和数字化程度,降低人工成本,是提高车间经营业绩的主要方向,目前可以考虑的主要方向有:
在线质量检测和自动化装箱:目前生产线每班4人,其中2人从事装箱和在线质量检查,这两人的劳动强度很大,考虑采用扫描的方式进行在线质量检查,然后用下料手直接装箱。当前的难点是在线质量检查的精度能否保证需要论证,在线质量检测系统的成本较高,自动装箱需要对生产线做较大的改造,需要做投资收益分析确定改善其必要性。
立体仓库和智能物料配送:目前半成品下线由叉车转运到半成品区,切割时再由叉车查到对应的激光切割单元进行切割,切割完成后再转运到成品仓库。随着生产的零件种类的增加,半成品、成品数量和种类、夹具、检具数量也大幅度增加,库房需求增加,需要考虑采用立体仓库及相应的智能物流配送。该改善投资较高,需要做投资收益分析确定其必要性。
- 下一篇:曝本田在华将关停两家工厂!广汽本田回应
- 上一篇:全国飞行汽车体验网络再添一站!
-
柯马签订具有约束力的协议收购 Automha
2025-04-17 -
高效协同新范式:比亚迪叉车领创智能搬运革新
2025-04-17 -
高歌猛进,奔赴“双碳”——比亚迪叉车助力轮胎
2025-04-10 -
果栗智造磁悬浮技术赋能汽车制造:破解行业痛点
2025-04-03
编辑推荐
最新资讯
-
全球产业链聚沪 共探双碳新路径 SNEC
2025-04-18 18:05
-
柯马签订具有约束力的协议收购 Autom
2025-04-17 13:01
-
高效协同新范式:比亚迪叉车领创智能
2025-04-17 10:04
-
埃马克德国总部迎来中国社科院工业经
2025-04-15 09:40
-
埃马克这项全新应用即将在CIMT惊艳首
2025-04-15 09:37