奇瑞汽车震撼推出一体化压铸底盘
近日,全球首件全尺寸整体车身一体化压铸件下线仪式,在力劲集团压铸机生产基地隆重举行。此举也意味着万吨双压射整体底盘技术进入可量产阶段。
这也是车身工艺又一突破,车身由小尺寸压铸发展到前舱及后地板等一体压铸,再到如今的整车一体压铸。
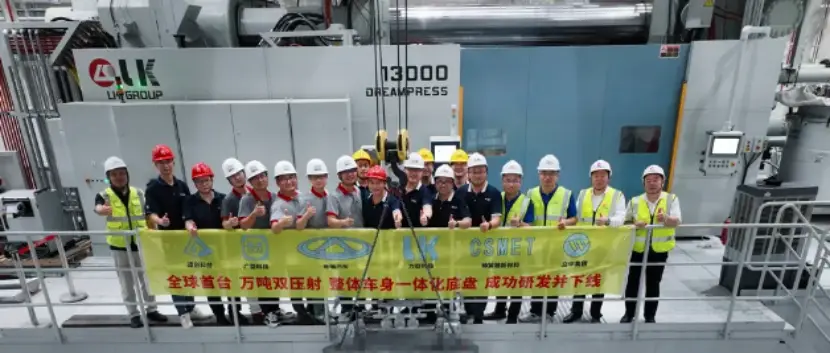
▲ 图1 后纵臂总成装配图
力劲集团与奇瑞汽车在安徽芜湖联合举办“全球首个超万吨双压射成型工艺暨技术签约仪式”,正式揭密双压射工艺与设备的技术原理及先进性。
双压射技术,顾名思义就是由“单个锁模机构+两个平行布置的压射系统”组成的一套压射系统,这一技术创造性地解决了因填充最大距离限制所导致的一系列问题。双压射系统有望实现车身超大型一体压铸结构件减重20%,成本33-35元/kg的阶段性目标。
未来会不会有三压射或者四压射呢?会不会发展上车身的一体压铸呢?技术的突破相信一切皆有可能。
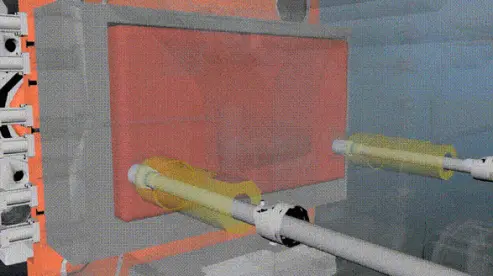
随着压铸吨位的不断突破,超大一体压铸的集成化越来越高,压铸件体积越来越大,单压射系统的局限性不断凸显,力劲集团与奇瑞汽车联合开发了这套超万吨双压射系统,成功解决了由此产生的一系列问题,更为未来更大的一体化压铸提供了无限可能。
肖总工表示,这一成功的背后,是技术团队在三方面取得的技术突破。
1 首先,针对零部件体积庞大、流动行程过长的问题,团队经过严格的试验和筛选,最终选用了高硅的铝合金材料路线,以确保合金材料的高流动性。
2 其次,双压射系统面临两个压射端同步性的挑战。采用铸造模流软件的双料筒异步仿真技术分析表明,20毫秒以内的双压射偏差,不会影响铸件成型汇流。经过前期的反复测试和调试,技术团队成功地将800吨双压射压铸机的同步偏差控制在目标范围内,而13000T双压射压铸机的偏差也达到了目标值,从而确保了压射过程的稳定性和一致性。
3 最后,为了项目的顺利实施,适创科技在其模流分析软件“智铸超云”的基础上,专门开发了双料筒异步仿真模块。这一创新为采用双压射工艺的前期模流分析提供了强有力的支持,确保了模具设计和工艺参数的准确性和可行性。
可见技术突破的背后是无数人的努力及技术的不断尝试与探索。
全尺寸整车一体底盘压铸优缺点
优势
顾名思义,整个下车身由传统的几百个零件集成为一个零件,在生产工艺中,可大大降低节拍、工人数量、生产场地、工装、模具、夹具、紧固件连接数量。对车身的成本将会有较大的提升。整个下车身钢材转化为铝材,对车身的轻量化及燃油经济性具有较大提升。
劣势
整个下车身一体化,对碰撞维修性的成本大大提高,零件的可调节可变性有一定下降,如车身进行加长加宽,零件无法具有延续性。
为应对碰撞的结构设计,通过下图可见,前后防撞梁及吸能盒等并不在集成范围,前舱在前纵梁位置停止,后部在后纵梁位置截止,猜测会设计三段式碰撞区域,通过防撞梁、吸能盒及小纵梁来实现碰撞吸能。
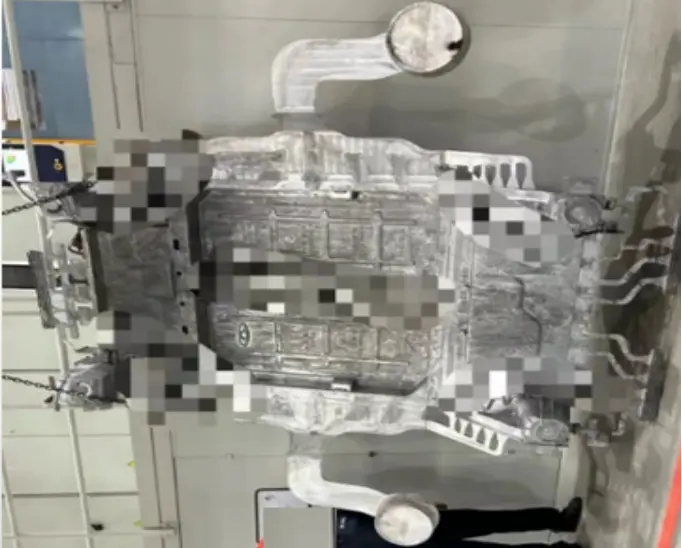
全尺寸整车一体化底盘压铸将会对车身设计带来更宽广的思路,而根据近几年的压铸发展趋势,整车一体压铸工艺可能是未来的趋势,其对生产工艺、成本、轻量化、性能等都是进一步的突破。
-
旭化成旗下旭塑洁螺杆清洗剂即将推出新品,探索
2025-04-08 -
重磅剧透!首批参展商名单曝光——这些数字化解
2025-04-01 -
从4S店到修理厂:FLIR ONE Pro USB-C版赋能全场
2025-03-28 -
电装中国:以“技术+生态”双引擎驱动汽车供应
2025-03-24
最新资讯
-
全球产业链聚沪 共探双碳新路径 SNEC
2025-04-18 18:05
-
柯马签订具有约束力的协议收购 Autom
2025-04-17 13:01
-
高效协同新范式:比亚迪叉车领创智能
2025-04-17 10:04
-
埃马克德国总部迎来中国社科院工业经
2025-04-15 09:40
-
埃马克这项全新应用即将在CIMT惊艳首
2025-04-15 09:37