浅谈江淮汽车动力总成制造工艺的发展
2017-05-18 17:46:22·
近年来,随着自身产品的不断变化升级,以及工业4.0 的发展推广,以自动化和数字化为基础的智能制造、以节能环保为基础的绿色制造的迫切需求,促使江淮汽车进行工艺设计思路的转变和工艺技术应用的深化。淮汽车动力总成生产线近年来主要的工艺设计思路以及未来的发展趋势。
江淮汽车的第一条发动机生产线于2004 年建成并进入投产。经过十多年的发展,江淮汽车已先后建立了4GA、4GB、4GC、4DA、4DB 和DCT 共五大平台发动机生产线和变速器生产线,形成了一套动力总成工厂规划设计理念。近年来,随着自身产品的不断变化升级,以及工业4.0 的发展推广,以自动化和数字化为基础的智能制造、以节能环保为基础的绿色制造的迫切需求,促使江淮汽车进行工艺设计思路的转变和工艺技术应用的深化。本文对以上内容做了简要的介绍。
加工线布局规划
近年来,我们在工艺流程的设计思路上做了一些转变,尤其是对加工设备的布局,逐渐由原来一个流的直线布置(见图1)向模块化、成组加工的岛状工艺布置(见图2)转变。一个流布置的工序状态多、重复定位多和单机故障的出现会影响到整条加工线的生产,而采用模块化布置避免了这些现象。从实际的生产情况来看,由于工序状态少,更有利于自动化的实现;工序集中,同时使精度更容易控制,进一步提升了产品质量。随着同平台产品
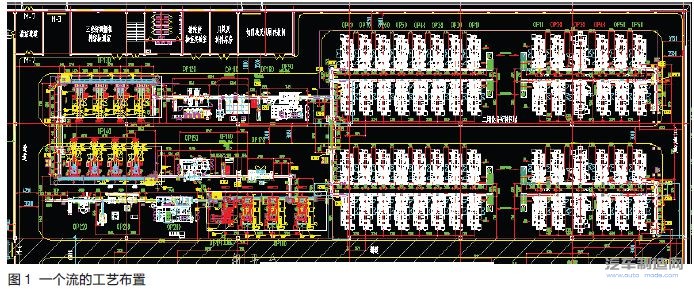
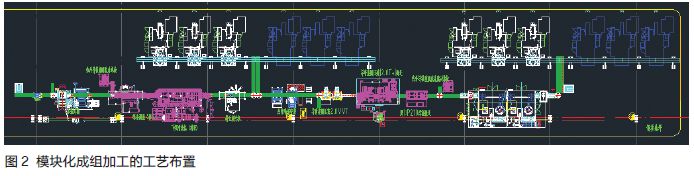
种类的不断增多,小批量、多品种的生产模式是当下生产的趋势所在,这让生产线对于多品种产品柔性、共线生产以及精益投资、分期投入的要求也越来越强烈,显然,模块化布线更适合今后的发展需要。
同时,按照轻资产、重质量的思想,江淮汽车将进一步加大粗加工的外协内容,集中力量控制好精加工和装配的质量。
柔性化生产线建设
如上所述,柔性化生产是发展的必然趋势,这就要求我们做出相应的调整。
1. 由精加工采用专机向采用加工中心转变
专机的优势在于设备精度好、效率高。其缺点是:一次性投入大;柔性差,不利于新产品共线;占地空间大。加工中心的优势是:一次性投资低,可分期投入;柔性好,产品切换方便;空间布置约束小。其缺点是效率较低。而随着加工中心本身精度的不断提升和在线自动补偿技术的发展,其替代专机完成精加工内容已逐渐成为趋势。
2. 传统步进式常压清洗机向机器人高压清洗转变
传统清洗机的优点是投资经济。缺点在于:柔性差,不利于产品切换;输送定位精度不高,影响清洗和吹干效果;设备长度大。而机器人高压清洗的优点在于:柔性好,适合多品种清洗;定位精准,适合高压清洗和去毛刺;设备长度紧凑。缺点为投资较高。由于对质量要求的精益求精,对清洁度要求的不断提高,机器人高压清洗已逐步取代传统方式。
3. 从传统的非标设备向工业机器人的广泛应用转变
这种转变可以通过机器人卡爪的快换来满足生产线产品的快速换型。
自动化程度大幅提高
机器人的大量应用也是自动化程度提升的重要体现,其取代了传统的输送、翻转和上下料机构,并与清洗、检测等设备相结合,提升生产线的自动化。如果设计合理,一台机器人可以在多个工位进行应用,生产线成本并没有增加。
图3 所示为机器人在活塞连杆安装工位的应用。机器人从工位1 将缸体抓取后翻转180°,移动到工位2 进行自动缸孔喷油;将缸体翻转放至线外转台上进行活塞连杆的装配;将装配好活塞连杆的缸体自动翻转后放置到工位3 的托盘;连杆拧紧后,在工位4 将缸体由倒立姿态翻转为正立姿态。这样,一台机器人完成工件的3 次姿态转换,取代了传统的3 台翻转机构。
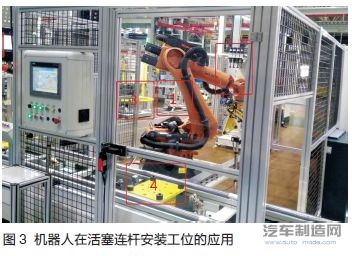
同时,我们也在着手进行原有生产线的自动化改造,对之前的手动装配工位,进行自动化手段替代。如图4 所示,油封压装、气门弹簧安装、缸垫安装、缸盖合装、燃油泵涂胶以及链轮室盖螺栓送料等部位,都可以通过优化进行自动化升级。
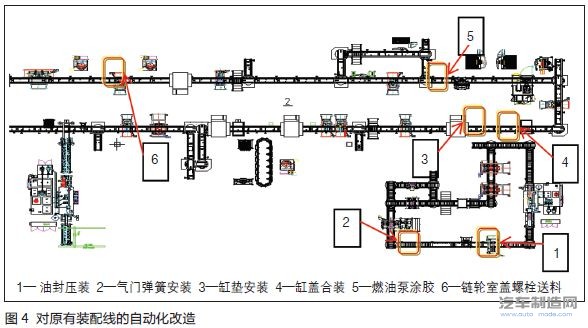
数字化生产的深化应用
十二五期间, 我们完成了从采用流水号、二维码向全线RFID 质量追溯的转变,即从简易信息系统向MES 系统深层次应用的转变。加工线采用螺栓式载码体,安装于缸体、缸盖本体上,将身份识别及质量追溯相结合;装配线托盘载码体,集成工位覆盖率达到70%,进一步增加了数据的可追溯性。
目前,江淮汽车动力总成生产线与数字化系统已经有了较高的集成度,从动力总成跟踪系统、车间监控系统、物流安灯系统、质量数据采集、SPC 分析系统以及质量门与返修管理等多个方面提升了生产的信息化建设。
对于MES 系统下一步的发展,将是其与工艺、电控和生产的融合度得到进一步的提升,将MES 系统建设成为智能工厂的指挥官,整个生产过程实现可追溯性和可视化。对加工中心、刀具的集成、工艺流程和生产管理的标准化以及信息化下的全供应链物流管理,将是可能的发展方向。
绿色制造技术应用实例
1. 切削液
对切削液的处理,我们根据使用环境的不同采取了三种方式:
(1)对于加工设备比较少的情况(主要用于试制车间),我们采用在液箱上配备简易的抽吸装置,可以在短时间内除去表面浮油。
(2)对于少量加工设备组成的集中过滤系统,我们给净液箱配备三相离心分离机,可以对集中收集后的切削液进行除油和除屑处理。
(3)对于整线加工设备组成的集中过滤,我们配置功能比较齐全的切削液集中处理系统。该系统将各设备的切削液连同铁屑一起,通过泵和管路返回到专门的处理设备,经过粗、精两级过滤进行处理。粗过滤排出的铁屑集中后进行压块处理后直接回收;精过滤后的切削液再经过离心处理通过泵组返回加工设备进行循环利用。此系统对整线的切削液进行恒温控制,保证切削液的质量,一次换液的使用寿命可以达到三年以上。
2.车间油雾处理
对于加工车间油雾的处理随着环保等级的不断提升,我们从最初的单机过滤后直接排放到厂内,到单机过滤后通过管路集中排到厂外,最后发展为通过管路收集后在车间内进行集中过滤处理后再排放(见图5)。
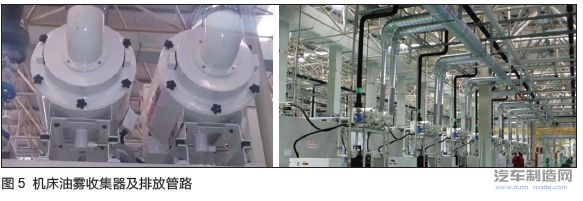
3.改进工艺
冷热试结合,不断降低热试比例,也是节能降耗的有效手段。装配线采用冷试(汽油机、柴油机)全检、热试抽检的工艺方式可保证产品质量(热试抽检比例控制到50%以内),同时大大节约了燃油损耗量,也降低了热试排放对环境造成的污染。而对热试台架的尾气采用“电加热系统+DOC+SCR+DPF”串联工艺系统(见图6),净化处理后的有害气体成分去除率≥ 75%,颗粒物去除率≥ 90%,有效降低了大气污染及雾霾危害。
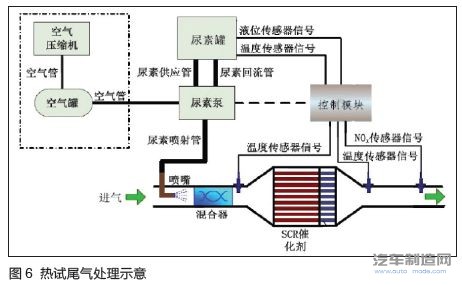
由于缸内直喷发动机的燃油系统压力(35 MPa)远大于传统发动机,如这个部位密封性不好,将存在重大质量风险。因此,可以在燃油系统管路装配完成后的工位增加氦检测试,并配置人机协作机器人与氦检探头进行集成。同时,对发动机采用电检,也可以在热试之前提前发现电气元件的故障。
结语
历经多年的发展, 江淮汽车在工艺技术上积累了丰富的经验,动力总成生产线的质量控制正努力保持着国内领先的水平,精致工艺仍在持续提升之中。江淮汽车正从工艺规划、制造水平和工艺装备等方面全方位朝着世界先进水平迈进,为打造世界一流产品而不断努力。
编辑推荐
最新资讯
-
全球产业链聚沪 共探双碳新路径 SNEC
2025-04-18 18:05
-
柯马签订具有约束力的协议收购 Autom
2025-04-17 13:01
-
高效协同新范式:比亚迪叉车领创智能
2025-04-17 10:04
-
埃马克德国总部迎来中国社科院工业经
2025-04-15 09:40
-
埃马克这项全新应用即将在CIMT惊艳首
2025-04-15 09:37