用于焊接机器人应用的创新
2017-06-20 11:30:27·
根据国际机器人联合会,世界上有50%的机器人用于焊接。此外,BCC Research最近的一份报告显示,2021年全球自动化/焊接机器人配件部门将达到28亿美元,高于2016年的20亿美元,五年复合增长率为6.9%。为什么这些数字如此令人印象深刻,只需看一下典型的汽车厂。例如,在本田的英国斯温顿制造工厂,超过300台机器人可以帮助
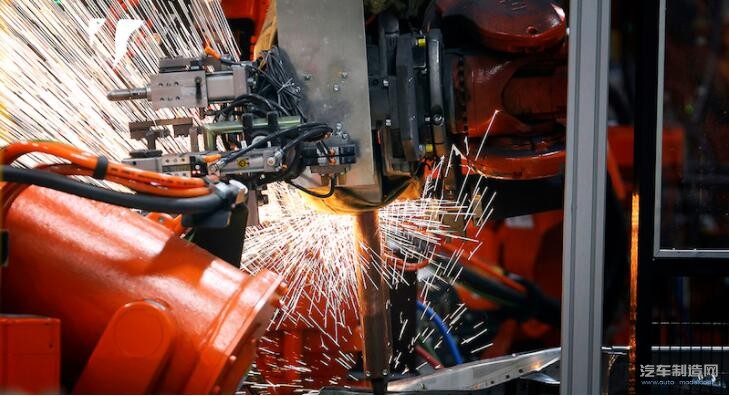
根据国际机器人联合会,世界上有50%的机器人用于焊接。此外,BCC Research最近的一份报告显示,2021年全球自动化/焊接机器人配件部门将达到28亿美元,高于2016年的20亿美元,五年复合增长率为6.9%。
为什么这些数字如此令人印象深刻,只需看一下典型的汽车厂。例如,在本田的英国斯温顿制造工厂,超过300台机器人可以帮助每个车身提供2200个点焊。每85秒生产一辆车身,每转换650只白身(BIW)。
本田的过程开始于右侧和左侧车轮房屋被焊接到下面的仪表板和前部舱壁上,形成完整的发动机舱。然后将其与前后地板组件组合以完成地板。
右侧面板和左侧板被分组并转移到“通用焊机”(GW)。这是该部门的核心部分,在各个地区(侧面板,地板,屋顶,上面和后面的包裹托盘)上生产的部件聚集在一起,由GW焊接以生产完整的机体。
BIW机器人
的大订单这样一个过程的要求显然需要效率和重复性,随着机器人在这两个方面的交付,重大的订单继续被放置。例如,ABB最近向Valmet Automotive交付了250台机器人,用于芬兰Uusikaupunki的梅赛德斯 - 奔驰GLC SUV车身车间。这项投资是芬兰最大的工业机器人合同,将Valmet Automotive公司的ABB机器人总数翻了一番,达到500多台。
新生产线由主线和子组装电池组成。据ABB介绍,额外的机器人将提升汽车供应商的灵活制造能力,通过提高生产率和缩短交货期来提升运营水平。
该订单包括IRB 6700系列机器人,ABB表示更强大,节能15%,并需要比前代更简化的维护。此外,IRB 8700系列机器人也是订单的一部分; 这些距离达到3.5米,能够处理高达800公斤的有效载荷。
对于BIW生产,无障碍,高速运行是圣杯。然而,这些属性必须与灵活性相匹配,这是适当设计和配置的输送机系统可以帮助的。
Kuka的KS PULSE(推进使用线性同步能源)是一种基于托盘的运输系统,可以通过BIW焊接和装配线的各个工作站移动各种主体部件,从而减少非生产性停机时间。系统的主要部件是机箱。使用各种运输平台,称为滑行装置,该托架通过线性同步电动机沿着线路移动单个主体部件。
由于运动部件数量很少,系统对故障的敏感性低,而在循环时间方面,滑轨是可以互换的,可以在同一条生产线上生产多个型号。
在其他地方,塔塔钢铁公司在其在日内瓦的汽车中心推出了新的机器人焊接生产线,据说这是在英国最大的。该系统使该网站能够为汽车门板生产定制焊接坯料。基于ABB机器人技术,每小时可以焊接超过一千辆汽车零件,钢铁运往英国的汽车制造商,目前在德国,法国和荷兰获得新的订单。
焊接在一起
即使在较低的数量是规范,自动化仍然是有吸引力的。例如,以商业车辆专家Meiller的捷克Slaný设备为例。Meiller作为自卸车车身和拖车的设计师和制造商。
通过与HGV制造商的紧密合作,底盘和车身必须得到最佳匹配。为了有助于实现这一目标,Meiller公司共运营六台自动化系统,其中包括八个焊接机器人和由Cloos提供的300多个焊接电源。最新的系统使用Cloos'Tandem Weld焊接工艺来焊接侧倾体。

Kuka已经快速采取了工业4.0考虑其摩擦焊机
在串联焊接中,两根内联线同时进料并熔化成两个弧。由于两个电路的分离,可以严格控制电弧。据说,高效率,低热输入,良好的焊缝质量和高沉积速率是主要优点。
据该公司介绍,该工艺在商业车辆结构中焊接薄,轻质部件时实现了特别高的速度。这种类型的部件正在日益增加的需求,因为有效载荷优化的货车可以运输更多的运费,节省燃料和减少运输网络的负担。
MeillerSlaný工厂的程序员和设计师Andrej Stary表示:“在Meiller,我们越来越多地使用轻量级组件。“我们的自卸车车身侧板由2.5mm细粒钢制成。此外,该组件以前由三个单独的元件组成,而今天的侧板由单件形成,使得每侧仅需要焊接一个接缝。由于焊接数量的减少,组件比以前轻得多,这给我们的铲车带来了巨大的好处。“
防止连接机器人
的停机时间机器人在BIW中产生质量差的焊缝的问题对于最终组装可能是灾难性的,当工作人员解决问题时停止输出。然而,现在可以使用实时状态监视和诊断来防止意外停机。
思科表示,它已与Fanuc和罗克韦尔自动化公司合作,为五个国家的27家通用汽车工厂创造了数千台机器人解决方案。Fanuc被称为“零停机时间”(ZDT),该解决方案在发生问题之前向工作人员提供警报,以便他们可以在计划停机窗口中安排维护。思科公司说,除了诊断和主动维护计划之外,这种远程监控功能通过'1 + 1 + 1> 3'集成了每个公司带来的功能和专业知识。
“通过Fanuc ZDT解决方案,机器人通过网络和工厂内的思科数据采集器连接到思科云,所有这些都产生了强大而安全的端到端解决方案,”高级总监Bryan Tantzen说,思科IoT垂直。“通过将设备数据传输到基于云的平台,我们正在建立一个制造数据公路,使通用汽车能够与其大型设备供应商合作,更轻松地执行预防性分析和优化。
Fanuc America董事长兼首席执行官Rick Schneider补充说:“从机器人收集数据并在云中分析数据的能力 - 在停机发生之前预测潜在的设备问题 - 使我们能够主动满足客户需求。通过ZDT,我们还可以利用从机器人收集到的数据,通过降低能耗和延长设备使用寿命以及改善周期时间和质量来优化通用汽车的制造系统。通过ZDT减少停机时间已经证明对通用汽车的性能有直接和积极的影响。“
创造摩擦
“摩擦焊接有时会过时,”Kuka Industries先进焊接解决方案部门负责人Walter Weh说。“然而,技术只不过是在Kuka,我们以市场需求为指导,与时俱进。”
例如,Kuka已经很快地采用“工业4.0”来考虑其摩擦焊机。将机器完全集成到生产网络中可以实现更高的生产率。由于采用数字化网络流程,因此可以制造具有更高灵活性,节能和定制的产品,同时减少对资源的影响。
来自Kuka PCD(过程控制和文档)控制器的所有过程数据进行数字监控和电子存档。然后,此信息可用于在基于云的系统中进一步分析,例如,这也有助于确保可追溯的质量和数据透明度。考虑到这一点,安全地处理大量数据的能力起着基本的作用,就像系统接口上的统一标准一样。据Kuka介绍,这一原则的实施不仅限于新产品和解决方案; 已经在运行的机器人,小区和系统也可以以相同的方式联网。
- 下一篇:KUKA亮相 2017FE柏林站
- 上一篇:双用途激光
编辑推荐
最新资讯
-
[转载] 机床巨头埃马克:百年跌宕再
2025-03-31 12:42
-
从4S店到修理厂:FLIR ONE Pro USB-C
2025-03-28 16:05
-
比亚迪发布2024年ESG报告 以技术创新
2025-03-26 16:44
-
电装中国:以“技术+生态”双引擎驱
2025-03-24 19:07
-
杜尔中国海外项目-Stellantis 集团摩
2025-03-20 11:59