多车型共线生产的现在与未来
2017-08-01 10:05:24· 来源:KUKA柔性系统
汽车工业是一个典型的资本技术密集型产业,也是目前自动化程度最高的行业,推陈出新的频率日益增高。十年前,需要4年开发周期的汽车产品,现在只需要2年就可以完成。不少汽车厂家从以前的每年推出1~2款新车,到现在每年推出5~6款新车。这种高频次的推陈出新率不仅仅是充分发掘市场需求的结果,更需要强有力的制造技术来配合
汽车工业是一个典型的资本技术密集型产业,也是目前自动化程度最高的行业,推陈出新的频率日益增高。
十年前,需要4年开发周期的汽车产品,现在只需要2年就可以完成。不少汽车厂家从以前的每年推出1~2款新车,到现在每年推出5~6款新车。这种高频次的推陈出新率不仅仅是充分发掘市场需求的结果,更需要强有力的制造技术来配合生产。
为了满足目前急剧增加的新车型生产,整车厂对多车型共线生产有了更高的需求。多车型共线生产的重点在于顺利切换侧围夹具,共线的车型越多,所需的侧围夹具也越多。在现有场地面积下,实现低成本的多车型生产成为汽车整车厂商面临的重大挑战。
随着共线生产车型数量的增加,对于侧围总拼工位的设计要求也越来越严格。目前行业线体供应商对于总拼工位流行的设置有4种,分别是并排式、转毂式、转台式,以及康采恩式(空中竖直式)。其中并排放置设计,优点是造价较低,缺点是总拼工位占地面积过大,对于工厂场地要求高;康采恩式的占地面积比较小,但是空中占很大的面积,同时会影响空中输送系统的布置;转毂式生产缺点是造价相对高,但是能极大地减少客户场地使用面积;转台式的总拼缺点是占地面积较大,优点是历史悠久,技术相对成熟。
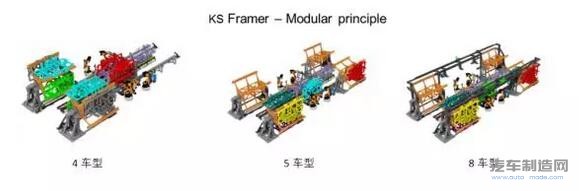
其中技术难度较高的是多车型转毂式生产,车型越多,越需要提高夹具切换时间,以便降低生产节拍损失。业内侧围夹具的切换时间一般为18 s,而库卡通过在转毂上方增加侧围夹具的空中返回轨道,任意侧围夹具的切换时间最快可达15 s,可以显著地减少车型切换的节拍损失。库卡转毂式生产设计每一个转毂可储存4个夹具,总拼工位占地面积最低可达宽13 m×长23.6 m,而行业上能实现的占地面积一般在宽18 m×长25 m左右。
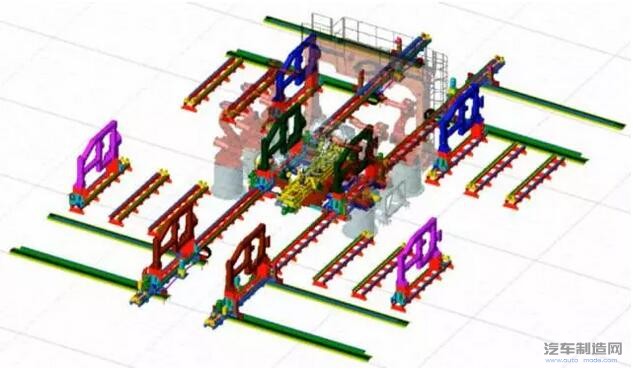
并列式放置
转毂上方的轨道是一种更换装置,用于不同转毂之间侧围夹具的更换,具有多个可控、可转动夹具存储库和夹具传送装置,在夹具库之间传输夹具并将其运送到工作站的操作位置的功能。这种技术为安装和更换不同的、典型的夹具提供了更高的灵活度,并且能够在更换车型类型和相应的车身件时更快地更换夹具。夹具传输装置为所属的夹具库提供了多种并行联接的可能性,可以在地面更换夹具的同时空中轨道也在传送另一个车型的侧围夹具。优选并行配置的夹具传输装置允许相对于夹具传送装置独立地在不同夹具库之间更换夹具,由此可以在夹具库之间实现夹具的循环传送。
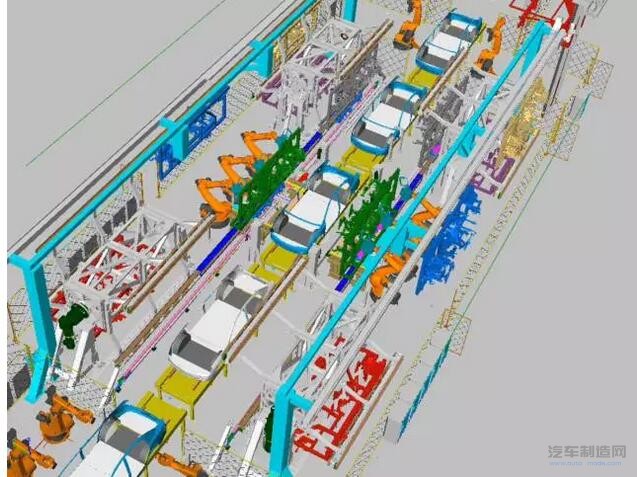
转毂式生产仿真图
此项技术还有一个优点是拥有临时夹具存储位置,在为其中一个车型安装车身件的时候,另一个夹具可先移动到存储位置待命,以便更快地切换。
通过空中轨道快速切换侧围夹具是目前库卡系统的专利技术,其关键部件由库卡系统德国总部研发生产,采用德国进口部件,可以保证较长的使用寿命以及长久的运行稳定性,故障率较低。车身进入工位时,采用精定位钢结构保证车身精度,精确地将偏差控制在很小的范围内,对于多车型生产的顺利实现有着非常重大的作用。
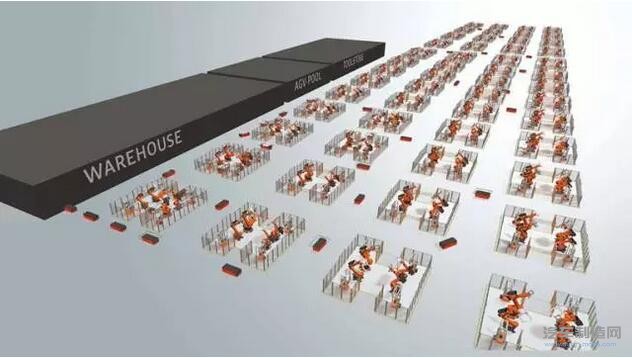
KUKA矩阵式生产
未来新产品的开发周期不断缩短,成本也不断降低。随着汽车技术水平的提升和制造技术的变革,伴随着日趋激烈的市场竞争,多品种生产最大限度满足市场的多样化需要,直到满足每一位用户的需要。“多品种、小批量”的定制生产方式开始进入人们的视野。基于成熟的技术以及丰富的经验,结合对“工业4.0”概念的理解和探索,一种独有的矩阵化生产解决方案被率先提出。变线为站,同时完成多种加工,利于实现个性化生产;降低库存,提高设备利用率和缩短加工周期,提升中国客户在市场上的竞争优势。
十年前,需要4年开发周期的汽车产品,现在只需要2年就可以完成。不少汽车厂家从以前的每年推出1~2款新车,到现在每年推出5~6款新车。这种高频次的推陈出新率不仅仅是充分发掘市场需求的结果,更需要强有力的制造技术来配合生产。
为了满足目前急剧增加的新车型生产,整车厂对多车型共线生产有了更高的需求。多车型共线生产的重点在于顺利切换侧围夹具,共线的车型越多,所需的侧围夹具也越多。在现有场地面积下,实现低成本的多车型生产成为汽车整车厂商面临的重大挑战。
随着共线生产车型数量的增加,对于侧围总拼工位的设计要求也越来越严格。目前行业线体供应商对于总拼工位流行的设置有4种,分别是并排式、转毂式、转台式,以及康采恩式(空中竖直式)。其中并排放置设计,优点是造价较低,缺点是总拼工位占地面积过大,对于工厂场地要求高;康采恩式的占地面积比较小,但是空中占很大的面积,同时会影响空中输送系统的布置;转毂式生产缺点是造价相对高,但是能极大地减少客户场地使用面积;转台式的总拼缺点是占地面积较大,优点是历史悠久,技术相对成熟。
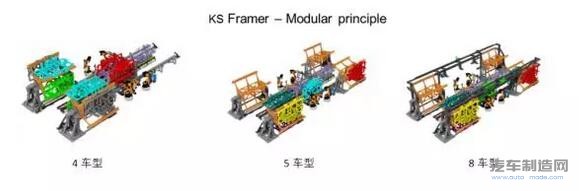
其中技术难度较高的是多车型转毂式生产,车型越多,越需要提高夹具切换时间,以便降低生产节拍损失。业内侧围夹具的切换时间一般为18 s,而库卡通过在转毂上方增加侧围夹具的空中返回轨道,任意侧围夹具的切换时间最快可达15 s,可以显著地减少车型切换的节拍损失。库卡转毂式生产设计每一个转毂可储存4个夹具,总拼工位占地面积最低可达宽13 m×长23.6 m,而行业上能实现的占地面积一般在宽18 m×长25 m左右。
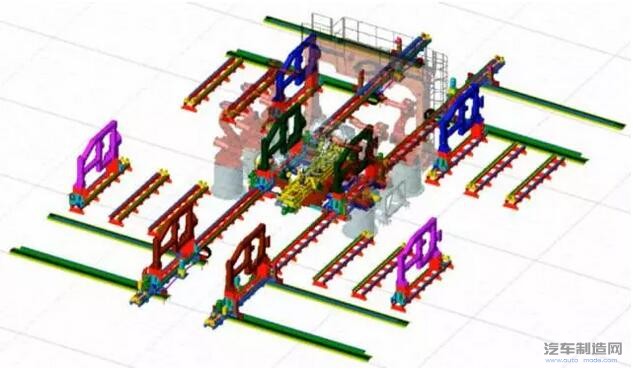
并列式放置
转毂上方的轨道是一种更换装置,用于不同转毂之间侧围夹具的更换,具有多个可控、可转动夹具存储库和夹具传送装置,在夹具库之间传输夹具并将其运送到工作站的操作位置的功能。这种技术为安装和更换不同的、典型的夹具提供了更高的灵活度,并且能够在更换车型类型和相应的车身件时更快地更换夹具。夹具传输装置为所属的夹具库提供了多种并行联接的可能性,可以在地面更换夹具的同时空中轨道也在传送另一个车型的侧围夹具。优选并行配置的夹具传输装置允许相对于夹具传送装置独立地在不同夹具库之间更换夹具,由此可以在夹具库之间实现夹具的循环传送。
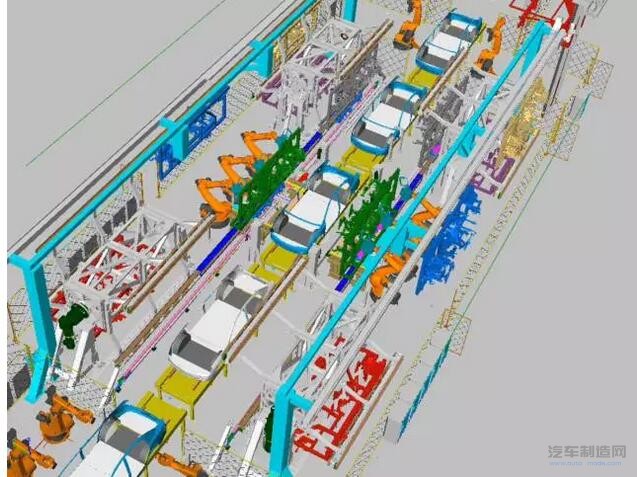
转毂式生产仿真图
此项技术还有一个优点是拥有临时夹具存储位置,在为其中一个车型安装车身件的时候,另一个夹具可先移动到存储位置待命,以便更快地切换。
通过空中轨道快速切换侧围夹具是目前库卡系统的专利技术,其关键部件由库卡系统德国总部研发生产,采用德国进口部件,可以保证较长的使用寿命以及长久的运行稳定性,故障率较低。车身进入工位时,采用精定位钢结构保证车身精度,精确地将偏差控制在很小的范围内,对于多车型生产的顺利实现有着非常重大的作用。
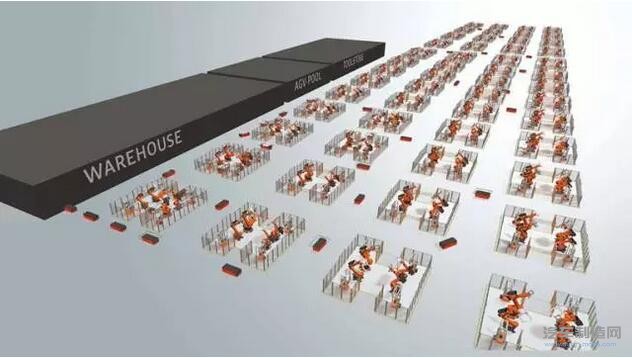
KUKA矩阵式生产
未来新产品的开发周期不断缩短,成本也不断降低。随着汽车技术水平的提升和制造技术的变革,伴随着日趋激烈的市场竞争,多品种生产最大限度满足市场的多样化需要,直到满足每一位用户的需要。“多品种、小批量”的定制生产方式开始进入人们的视野。基于成熟的技术以及丰富的经验,结合对“工业4.0”概念的理解和探索,一种独有的矩阵化生产解决方案被率先提出。变线为站,同时完成多种加工,利于实现个性化生产;降低库存,提高设备利用率和缩短加工周期,提升中国客户在市场上的竞争优势。
举报 0
收藏 0
分享 220
-
埃马克德国总部迎来中国社科院工业经济研究所代
2025-04-15 -
埃马克这项全新应用即将在CIMT惊艳首秀!
2025-04-15 -
[转载] 机床巨头埃马克:百年跌宕再出发
2025-03-31 -
赋能电动未来,埃马克重庆技术日展示尖端制造技
2025-03-03
编辑推荐
最新资讯
-
全球产业链聚沪 共探双碳新路径 SNEC
2025-04-18 18:05
-
柯马签订具有约束力的协议收购 Autom
2025-04-17 13:01
-
高效协同新范式:比亚迪叉车领创智能
2025-04-17 10:04
-
埃马克德国总部迎来中国社科院工业经
2025-04-15 09:40
-
埃马克这项全新应用即将在CIMT惊艳首
2025-04-15 09:37