KUKA焊接机器人在十万辆面包车焊接线上的应用及存在的问题
2017-08-14 18:35:53·
随着社会的发展和科技的进步,机器人在社会各个领域得到了日益广泛的应用,而应用最多的则是工业机器人。工业机器人自60年代初问世以来,经过了40多年的发展,已广泛应用于工业领域,成为汽车制造业生产自动化中主要的机电一体化设备。制造行业应用机器人的主要目的在于削减生产人员编制、提高劳动生产率、降低劳动强度及提
随着社会的发展和科技的进步,机器人在社会各个领域得到了日益广泛的应用,而应用最多的则是工业机器人。工业机器人自60年代初问世以来,经过了40多年的发展,已广泛应用于工业领域,成为汽车制造业生产自动化中主要的机电一体化设备。
制造行业应用机器人的主要目的在于削减生产人员编制、提高劳动生产率、降低劳动强度及提高产品质量。机器人与传统的机器相比,具有两个主要优点:
1) 容易实现生产过程的完全自动化。
2) 对生产设备的高度适应能力。
焊接机器人在长安汽车股份公司的应用
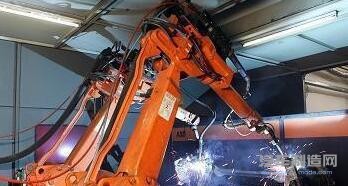
KUKA机器人在十万辆面包车焊接线上的应用
1996年,长安汽车股份公司新建十万辆SC6331系列微型面包车焊接生产线,该线首次引进德国KUKA公司的KRC32型6轴气动点焊机器人,应用在工艺要求最高的车架和成车焊接线上。在原有手工焊接线上,车架增焊工位和成车增焊工位由于焊点数量多、焊接零件结构复杂,是制约全线生产的瓶颈工位,工人作业时间长、劳动强度大、设备故障率高、焊点质量不稳定且容易造成碰压伤,严重制约了全线的生产速度,产品质量也得不到保证。
引进KUKA点焊机器人后,首先,十万辆焊接线的生产节拍大幅提高,微型面包车的单班生产数量大幅增加,达到手工焊接线产量的5倍;其次,工人的劳动强度得到大幅降低,工作时间大大缩短,工作条件得到极大改善;第三、微型面包车质量得到显著提高,车身碰压伤大为降低;第四、KUKA焊接机器人故障率极低,备件供应充足,系统稳定性高,操作维护容易,大量节约了设备维护人员,节约了人力资源。
COMAU、KUKA、OTC机器人在8万辆长安之星焊接线上的应用在成功引进KUKA 焊接机器人后,长安汽车股份公司在SC6350-“长安之星”八万辆焊接生产线上再次引进焊接机器人,其中包括意大利COMAU公司H4型伺服点焊机器人,意大利COMAU公司H1型螺柱焊机器人,日本OTC弧焊机器人,KUKA公司KRC型检测机器人。
SC6350八万辆焊接线上机器人的应用水平先进,伺服焊钳机器人、弧焊机器人、检测机器人都是目前国内汽车行业机器人应用水平最先进的代表。
其中,检测机器人采用目前国际上先进的在线检测方式,应用检测技术世界领先的德国Perceptron公司的检测设备与系统稳定性最高的德国KUKA机器人相整合,在主线(成车)焊接线的最后一个工位在线实时检测每一个“长安之星”白车身,以控制车身尺寸精度。检测系统设计白车身正常尺寸偏差±2mm,白车身尺寸超差时,生产线将要报警提示,并且检测系统中将存储每个白车身的测量数据,以供离线分析。
弧焊机器人采用日本OTC公司的DR系列七轴焊机器人,OTC机器人本体设计小巧,结构简单明了,弧焊功能齐全,特别适合于结构复杂的零部件气体保护焊接。如SC6350系列微车构架总成上的连接横梁的弧焊,由于该横梁为圆形,需要进行圆周焊接,且该部件位置较低,人工焊接劳动强度极大,气体保护焊又属于有毒作业,采用OTC弧焊机器人克服了这些严重制约生产、无法保证产品质量、损害操作者身体健康的缺点。
另一个值得关注的是高精度、高可靠性的伺服点焊机器人的引进,该型号机器人选用COMAU公司H4型点焊机器人,整合SIAKY伺服焊钳系统,焊点焊接质量稳定、定位精确。伺服焊钳与气动焊钳相比最突出的特点,是在焊接过程中,伺服焊钳的焊接质量高,焊点成形好,极大改善了白车身的焊接质量,使“长安之星”当之无愧成为中国的微车精品。
焊接机器人的应用经验
焊接机器人在长安公司汽车生产线上的应用已有七年时间,根据实际应用,以下一些经验供大家一起研究:
焊接机器人的使用,必须满足安全要求。
焊接机器人能够代替人类在危险、有害的恶劣环境中作业,同时又带来了另一种潜在的危险,即机器人伤人事故。为此,在焊接机器人在线运行时,绝对不能有人进入其运动安全范围所在区域,并且其运动区域内应该保证无干涉,这是焊接机器人安全管理的最为重要的一条原则。此外,除了通用的工业安全规程外,还要注意焊接机器人的特殊性,采取相应可靠的对策。例如现在我们正在使用的安全措施:
1)为焊接机器人及其周边设备安装安全防护栏,以防止有人进入危险区域造成意外伤害。
2)在安全护栏入口的安全门上设置插拔式电接点开关,该开关与焊接机器人的安全回电路相连接,一旦安全门打开,机器人控制器将切断机器人的驱动电源,机器人立即停止运动。
3)在距焊接机器人所在工位最近的地方,安装多个紧急停止开关,一旦发生紧急或危险情况,工作人员可以就近按下急停,让机器人停止运动。
4)示教作业时降低焊接机器人的运动速度,并由经过专业技术操作培训的人员进行示教。
5)焊接机器人安全电路与生产线安全电路联为一体,当生产线遇到紧急情况时,生产工人可以按下该线上任何工位的紧急停止开关,让机器人停止运动。
焊接机器人的控制装置
虽然焊接机器人本身拥有非常完善的控制系统,但每台焊接机器人作为一个独立的自动化设备系统,在一条生产线或一个生产系统中永远都只是一个从属的工作站,必须要有相应的外部控制装置对其进行远程控制,以适应自动化流水作业生产线上各种自动化设备之间同步、有序的生产要求。
焊接机器人常用的相关控制装置有可编程序控制器和在线监控装置。
可编程控制器对生产线上包括焊接机器人在内的各种自动化设备的工作进行协调与配合,从而有序地实现生产过程的自动化。
在线监控装置是操作者与生产系统之间的人机接口,它从生产系统中采集实时数据,并可以有条件地对生产数据进行实时修改,因而达到实时监视生产线现场情况、远程实时控制生产线运行的目的。使用在线监控装置能够方便地发出作业指令,启动或停止包括焊接机器人在内的所有自动化设备,并实时了解生产系统的状态。
长安公司8万辆长安之星焊接线上,采用西门子WINCC在线监控系统和西门子可编程控制器,所有的焊接机器人除了受自身控制系统的控制自动运行外,还必须接受可编程控制器和WINCC在线监控系统的远程控制,以保证与生产线其它自动设备的同步运行。
焊接机器人系统的扩展
为了满足长安公司八万辆“长安之星”焊接线的实际需求,COMAU公司在进行控制系统的设计时,同时考虑到了生产线系统的稳定性与白车身产品质量的稳定性,最终选用的焊接机器人具有以下扩展功能:
1)增加外部滑动轴
焊接机器人的外部滑动轴与其它6个基本轴一样,均含有伺服驱动器和伺服电机,与相应的机械传动装置相配合,可以有效扩大机器人的活动范围,并且能够在复杂或狭窄的空间内达到最佳的作业姿态,还可以通过示教来任意定位,以保持最高的定位精度。在点焊实际应用中,包含外部轴驱动的焊接机器人能够准确到达所需焊点位置,并达到最佳焊接姿态,因而点焊效果更好而无噪声和焊滴飞溅,焊接后的焊点外形美观、焊接质量高。
例如,八万辆焊接线主线730总拼工位,采用全自动的零部件装配与焊接工艺,该工位共有6台COMAU焊接机器人,要完成左/右侧围与车架的装配及整个白车身的焊接,加之工位包含了顶盖装配、车架装配及其它零件的装配,夹具、输送装置、自动焊钳等装置众多,空间极其有限,为了保证成车组焊,共有4台机器人采用了滑台式外部轴,以在狭窄的空间内,高质量、高速度、最安全地完成所有工作。
2)弧焊中的摆动焊接
弧焊机器人通过软件的正确设置,可以在沿焊缝前进的同时,焊丝尖端实现横向摆动,摆动的方式、频率及幅度等均可按工艺要求进行设定,从而达到提高弧焊质量的目的。 ^5)
3)机器人的工具自动切换
同样是在八万辆焊接线730工位,为了节约工作场地、缩短工作时间,15号(16号)焊接机器人同时要完成总拼工位白车身的焊接工作,又要负责从侧围生产线将侧围部件抓起来并放到主线与车架、顶盖组装,因而这两台焊接机器人采用了世界领先的“枪/手”自动切换技术,由可编程控制器在生产线需要时控制机器人进行伺服焊钳和抓手工具的自动切换。这样,一台机器人可以完成两台机器人需要完成的工作,既节约了成本又节约了场地。
机器人的编程
长安公司十万辆焊接线上的KUKA机器人,其编程采用WINDOWS操作系统下的APS软件,必须在WINDOWS环境下进行运动程序的上载及下载;八万辆焊接线上的COMAU机器人的编程采用任意文本编辑器,再经过编译后,用PCINT计算机仿真软件将程序下载到机器人控制器。这两种机器人编程的共同特点是均可以实现离线编程、在线示教,为生产线的设计与仿真提供了有力帮助。不同之处在于,COMAU机器人采用了类似PASCAL高级编程语言的语言结构,对于学习过计算机编程语言的人来说,可以非常快速、容易地理解,接受一些最基本的培训后,即可以编制相当完善的机器人控制程序。而KUKA机器人采用其专用的机器人编程语言,技术人员必须接受KUKA公司专业的编程培训,才能胜任编程工作。OTC机器人的控制程序编程则相对容易,基本采用简单、易懂的运动指令,意义一目了然。
伺服焊钳的成功引进
十万辆焊接线上应用的5台KUKA点焊机器人,均采用气动点焊钳进行车体焊接,由于焊钳电极帽存在磨损的问题,控制系统采用计算焊点数,对焊接电流进行递增式补偿的方法。从原理上讲,这是一种开环方式的补偿方法,并不能实际反映焊钳电极帽的真实损耗情况,因而车体焊接质量存在一定的不稳定性。
八万辆焊接线上,所有COMAU点焊机器人均采用SIAKY的伺服焊钳及控制系统。伺服焊钳作为机器人的一个外部轴存在,在机器人控制系统中增加一套驱动软件,该外部轴就与其它六个基本轴一样,完全受机器人控制器的控制。这样,该外部轴与其它六轴一起融为一体,机器人控制系统通过外部轴的驱动软件,可以实时计算该轴的真实位置。实际应用中,在完成每一个车体的焊接工作后,机器人控制系统将对这个外部轴-伺服焊钳,执行自动校正功能,通过检查该轴(伺服焊钳)的实际零点位置是否发生变化来确认电极帽是否磨损,这样确保了焊接压力的自动闭环控制,使车体焊接质量稳定性大幅提高。
应用焊接机器人实现柔性生产
长安公司微型汽车种类多、品种复杂,在以往手工生产线上,如果需要混线生产同一型号不同种类的车型,人工焊接速度因工件、工具的差别而大大降低,生产的汽车产品质量也随之呈现出不稳定性。
引进焊接机器人后,只需预先编制好适应不同车型生产所需的若干套不同的运动与焊接程序,机器人将根据生产线的工作指令,自动调用相应的工作程序与不同车体焊接所需的工具,即能自动适应生产线上车型的复杂变化,即使是八万辆焊接线上高频次、多种类车型的混线生产,也能应付自如。绝不会因为单班多种车型混线生产而产生手工线极易出现的错焊、漏焊以及误调整或不调整焊接规范等经常出现的车体焊接质量事故,生产线运转速度也丝毫不会降低。焊接机器人的广泛应用,为长安公司的汽车制造实现柔性自动化生产带来了前所未有的生机。
焊接机器人在应用中存在的问题
尽管焊接机器人在长安公司的汽车制造生产中得到广泛应用,使汽车焊接质量得到了极大改善,有效提高了企业的劳动生产效率,但仍有很多方面的问题值得我们去进一步研究和改善。
位置偏移后重新示教的问题
示教再现型焊接机器人如果发生焊接位置偏移时,必须进行在线示教然后再现运行,这个工作现在需要占用大量的生产时间。如果能够利用先进的计算机动态仿真技术对其进行离线示教和仿真,将是焊接机器人应用的一次革命性的改善。
弧焊机器人焊缝跟踪的问题
示教再现型弧焊机器人进行弧焊时,不能对焊缝进行动态跟踪反馈,因而焊缝有细微变化时,不能保证焊缝质量,如果能够应用智能技术,动态跟踪焊缝状态,就能有效保证弧焊质量的可靠性和稳定性。
目前,由于国内机器人的应用还不是非常广泛,国内机器人技术还有待于长足进步,机器人的专用部件国内还不能自行设计制造,长安公司大量应用焊接机器人后,配件问题成为机器人应用中最令人头痛的问题。因为机器人的部件多属专用部件(尤其是电器控制部分),技术水平要求相当高,因而必须从国外进口,而进口的机器人备件价格高企,国内代理公司大多不愿因大量预采购而造成资金积压,进口备件的时间周期又长,给汽车生产线造成了相当大的困难。
机器人的校轴过程占用过多时间。
长安公司所应用的KUKA、COMAU、OTC机器人,其轴的校正过程均需耗费比较长的时间,对于流水化的自动生产线来说,其停机所造成的经济损失非常巨大。如果能够应用高智能化的检测手段,使机器人在其轴的基本参数丢失或变化后,能够自动快速恢复到发生故障前的状态,将给自动化生产线带来巨大的生产效益 +&i
机器人电器控制系统的问题。
长安公司所应用的三种焊接机器人,其本体的机械可靠性及制造水平均相当高,本体出现故障(指机械故障)的概率极其微小。然而,相比之下,电气控制系统的故障率却非常高,最容易出现的部分是驱动部分的电路及元器件,另外接插件的故障频率也相当高。
当今世界上的机器人控制电路集成化程度已越来越高,控制技术的不断进步已使控制部分故障率大为降低。但对于汽车制造中的焊接作业这种环境恶劣、作业强度极大、电压波动较大的应用来说,如果能针对汽车生产的具体情况,进一步提高系统集成化程度,进一步增强系统抗干扰的能力,长安公司在未来应用大量机器人实现完全无人化生产线的理想将变为现实。
机器人与其它设备或工位上障碍物碰撞问题。
在长安公司的两条焊接线上,均出现过多次因为信号交换失误而发生机器人与机器人碰撞、机器人与其它设备或障碍物碰撞的事故。经过事后分析机器人工作程序,发现目前机器人控制系统在处理信号交换时,都采用外部I/O信号来交换彼此的工作状态,信号检测还只是以一个“点”的方式测量,即在某一运动程序行中,确认某一个交换信号是否存在来决定机器人是否继续下面的工作,而不是在一个运动区域中持续检测其它障碍物或机器人状态,这样,一旦检测过程结束而机器人的运动轨迹发生错误或信号交换不正常时,碰撞就发生了。
现在机器人的应用规模越来越大,多台机器人在狭窄空间内协同工作的场合越来越多,彼此之间信号交换已变得极其平常,如果能够在机器人的控制系统中,采用类似微软WINDOWS操作系统的后台处理方式来实时监测其它障碍物或机器人的工作状态,以决定机器人是否应该继续在有可能干涉的区域内工作,碰撞问题应能够得到有效的控制,甚至彻底解决这个问题。
综上所述,焊接机器人使汽车制造业大批量、高效率、高质量进行流水线汽车制造提供了有利保障,同时,焊接机器人在实际应用中暴露出来的问题,也促使我们不断努力学习先进技术,不断寻求更加有效的手段,让焊接机器人为中国的汽车制造业做出更大贡献。
制造行业应用机器人的主要目的在于削减生产人员编制、提高劳动生产率、降低劳动强度及提高产品质量。机器人与传统的机器相比,具有两个主要优点:
1) 容易实现生产过程的完全自动化。
2) 对生产设备的高度适应能力。
焊接机器人在长安汽车股份公司的应用
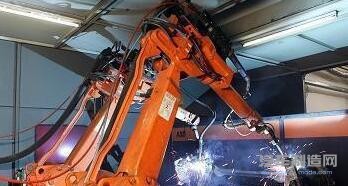
KUKA机器人在十万辆面包车焊接线上的应用
1996年,长安汽车股份公司新建十万辆SC6331系列微型面包车焊接生产线,该线首次引进德国KUKA公司的KRC32型6轴气动点焊机器人,应用在工艺要求最高的车架和成车焊接线上。在原有手工焊接线上,车架增焊工位和成车增焊工位由于焊点数量多、焊接零件结构复杂,是制约全线生产的瓶颈工位,工人作业时间长、劳动强度大、设备故障率高、焊点质量不稳定且容易造成碰压伤,严重制约了全线的生产速度,产品质量也得不到保证。
引进KUKA点焊机器人后,首先,十万辆焊接线的生产节拍大幅提高,微型面包车的单班生产数量大幅增加,达到手工焊接线产量的5倍;其次,工人的劳动强度得到大幅降低,工作时间大大缩短,工作条件得到极大改善;第三、微型面包车质量得到显著提高,车身碰压伤大为降低;第四、KUKA焊接机器人故障率极低,备件供应充足,系统稳定性高,操作维护容易,大量节约了设备维护人员,节约了人力资源。
COMAU、KUKA、OTC机器人在8万辆长安之星焊接线上的应用在成功引进KUKA 焊接机器人后,长安汽车股份公司在SC6350-“长安之星”八万辆焊接生产线上再次引进焊接机器人,其中包括意大利COMAU公司H4型伺服点焊机器人,意大利COMAU公司H1型螺柱焊机器人,日本OTC弧焊机器人,KUKA公司KRC型检测机器人。
SC6350八万辆焊接线上机器人的应用水平先进,伺服焊钳机器人、弧焊机器人、检测机器人都是目前国内汽车行业机器人应用水平最先进的代表。
其中,检测机器人采用目前国际上先进的在线检测方式,应用检测技术世界领先的德国Perceptron公司的检测设备与系统稳定性最高的德国KUKA机器人相整合,在主线(成车)焊接线的最后一个工位在线实时检测每一个“长安之星”白车身,以控制车身尺寸精度。检测系统设计白车身正常尺寸偏差±2mm,白车身尺寸超差时,生产线将要报警提示,并且检测系统中将存储每个白车身的测量数据,以供离线分析。
弧焊机器人采用日本OTC公司的DR系列七轴焊机器人,OTC机器人本体设计小巧,结构简单明了,弧焊功能齐全,特别适合于结构复杂的零部件气体保护焊接。如SC6350系列微车构架总成上的连接横梁的弧焊,由于该横梁为圆形,需要进行圆周焊接,且该部件位置较低,人工焊接劳动强度极大,气体保护焊又属于有毒作业,采用OTC弧焊机器人克服了这些严重制约生产、无法保证产品质量、损害操作者身体健康的缺点。
另一个值得关注的是高精度、高可靠性的伺服点焊机器人的引进,该型号机器人选用COMAU公司H4型点焊机器人,整合SIAKY伺服焊钳系统,焊点焊接质量稳定、定位精确。伺服焊钳与气动焊钳相比最突出的特点,是在焊接过程中,伺服焊钳的焊接质量高,焊点成形好,极大改善了白车身的焊接质量,使“长安之星”当之无愧成为中国的微车精品。
焊接机器人的应用经验
焊接机器人在长安公司汽车生产线上的应用已有七年时间,根据实际应用,以下一些经验供大家一起研究:
焊接机器人的使用,必须满足安全要求。
焊接机器人能够代替人类在危险、有害的恶劣环境中作业,同时又带来了另一种潜在的危险,即机器人伤人事故。为此,在焊接机器人在线运行时,绝对不能有人进入其运动安全范围所在区域,并且其运动区域内应该保证无干涉,这是焊接机器人安全管理的最为重要的一条原则。此外,除了通用的工业安全规程外,还要注意焊接机器人的特殊性,采取相应可靠的对策。例如现在我们正在使用的安全措施:
1)为焊接机器人及其周边设备安装安全防护栏,以防止有人进入危险区域造成意外伤害。
2)在安全护栏入口的安全门上设置插拔式电接点开关,该开关与焊接机器人的安全回电路相连接,一旦安全门打开,机器人控制器将切断机器人的驱动电源,机器人立即停止运动。
3)在距焊接机器人所在工位最近的地方,安装多个紧急停止开关,一旦发生紧急或危险情况,工作人员可以就近按下急停,让机器人停止运动。
4)示教作业时降低焊接机器人的运动速度,并由经过专业技术操作培训的人员进行示教。
5)焊接机器人安全电路与生产线安全电路联为一体,当生产线遇到紧急情况时,生产工人可以按下该线上任何工位的紧急停止开关,让机器人停止运动。
焊接机器人的控制装置
虽然焊接机器人本身拥有非常完善的控制系统,但每台焊接机器人作为一个独立的自动化设备系统,在一条生产线或一个生产系统中永远都只是一个从属的工作站,必须要有相应的外部控制装置对其进行远程控制,以适应自动化流水作业生产线上各种自动化设备之间同步、有序的生产要求。
焊接机器人常用的相关控制装置有可编程序控制器和在线监控装置。
可编程控制器对生产线上包括焊接机器人在内的各种自动化设备的工作进行协调与配合,从而有序地实现生产过程的自动化。
在线监控装置是操作者与生产系统之间的人机接口,它从生产系统中采集实时数据,并可以有条件地对生产数据进行实时修改,因而达到实时监视生产线现场情况、远程实时控制生产线运行的目的。使用在线监控装置能够方便地发出作业指令,启动或停止包括焊接机器人在内的所有自动化设备,并实时了解生产系统的状态。
长安公司8万辆长安之星焊接线上,采用西门子WINCC在线监控系统和西门子可编程控制器,所有的焊接机器人除了受自身控制系统的控制自动运行外,还必须接受可编程控制器和WINCC在线监控系统的远程控制,以保证与生产线其它自动设备的同步运行。
焊接机器人系统的扩展
为了满足长安公司八万辆“长安之星”焊接线的实际需求,COMAU公司在进行控制系统的设计时,同时考虑到了生产线系统的稳定性与白车身产品质量的稳定性,最终选用的焊接机器人具有以下扩展功能:
1)增加外部滑动轴
焊接机器人的外部滑动轴与其它6个基本轴一样,均含有伺服驱动器和伺服电机,与相应的机械传动装置相配合,可以有效扩大机器人的活动范围,并且能够在复杂或狭窄的空间内达到最佳的作业姿态,还可以通过示教来任意定位,以保持最高的定位精度。在点焊实际应用中,包含外部轴驱动的焊接机器人能够准确到达所需焊点位置,并达到最佳焊接姿态,因而点焊效果更好而无噪声和焊滴飞溅,焊接后的焊点外形美观、焊接质量高。
例如,八万辆焊接线主线730总拼工位,采用全自动的零部件装配与焊接工艺,该工位共有6台COMAU焊接机器人,要完成左/右侧围与车架的装配及整个白车身的焊接,加之工位包含了顶盖装配、车架装配及其它零件的装配,夹具、输送装置、自动焊钳等装置众多,空间极其有限,为了保证成车组焊,共有4台机器人采用了滑台式外部轴,以在狭窄的空间内,高质量、高速度、最安全地完成所有工作。
2)弧焊中的摆动焊接
弧焊机器人通过软件的正确设置,可以在沿焊缝前进的同时,焊丝尖端实现横向摆动,摆动的方式、频率及幅度等均可按工艺要求进行设定,从而达到提高弧焊质量的目的。 ^5)
3)机器人的工具自动切换
同样是在八万辆焊接线730工位,为了节约工作场地、缩短工作时间,15号(16号)焊接机器人同时要完成总拼工位白车身的焊接工作,又要负责从侧围生产线将侧围部件抓起来并放到主线与车架、顶盖组装,因而这两台焊接机器人采用了世界领先的“枪/手”自动切换技术,由可编程控制器在生产线需要时控制机器人进行伺服焊钳和抓手工具的自动切换。这样,一台机器人可以完成两台机器人需要完成的工作,既节约了成本又节约了场地。
机器人的编程
长安公司十万辆焊接线上的KUKA机器人,其编程采用WINDOWS操作系统下的APS软件,必须在WINDOWS环境下进行运动程序的上载及下载;八万辆焊接线上的COMAU机器人的编程采用任意文本编辑器,再经过编译后,用PCINT计算机仿真软件将程序下载到机器人控制器。这两种机器人编程的共同特点是均可以实现离线编程、在线示教,为生产线的设计与仿真提供了有力帮助。不同之处在于,COMAU机器人采用了类似PASCAL高级编程语言的语言结构,对于学习过计算机编程语言的人来说,可以非常快速、容易地理解,接受一些最基本的培训后,即可以编制相当完善的机器人控制程序。而KUKA机器人采用其专用的机器人编程语言,技术人员必须接受KUKA公司专业的编程培训,才能胜任编程工作。OTC机器人的控制程序编程则相对容易,基本采用简单、易懂的运动指令,意义一目了然。
伺服焊钳的成功引进
十万辆焊接线上应用的5台KUKA点焊机器人,均采用气动点焊钳进行车体焊接,由于焊钳电极帽存在磨损的问题,控制系统采用计算焊点数,对焊接电流进行递增式补偿的方法。从原理上讲,这是一种开环方式的补偿方法,并不能实际反映焊钳电极帽的真实损耗情况,因而车体焊接质量存在一定的不稳定性。
八万辆焊接线上,所有COMAU点焊机器人均采用SIAKY的伺服焊钳及控制系统。伺服焊钳作为机器人的一个外部轴存在,在机器人控制系统中增加一套驱动软件,该外部轴就与其它六个基本轴一样,完全受机器人控制器的控制。这样,该外部轴与其它六轴一起融为一体,机器人控制系统通过外部轴的驱动软件,可以实时计算该轴的真实位置。实际应用中,在完成每一个车体的焊接工作后,机器人控制系统将对这个外部轴-伺服焊钳,执行自动校正功能,通过检查该轴(伺服焊钳)的实际零点位置是否发生变化来确认电极帽是否磨损,这样确保了焊接压力的自动闭环控制,使车体焊接质量稳定性大幅提高。
应用焊接机器人实现柔性生产
长安公司微型汽车种类多、品种复杂,在以往手工生产线上,如果需要混线生产同一型号不同种类的车型,人工焊接速度因工件、工具的差别而大大降低,生产的汽车产品质量也随之呈现出不稳定性。
引进焊接机器人后,只需预先编制好适应不同车型生产所需的若干套不同的运动与焊接程序,机器人将根据生产线的工作指令,自动调用相应的工作程序与不同车体焊接所需的工具,即能自动适应生产线上车型的复杂变化,即使是八万辆焊接线上高频次、多种类车型的混线生产,也能应付自如。绝不会因为单班多种车型混线生产而产生手工线极易出现的错焊、漏焊以及误调整或不调整焊接规范等经常出现的车体焊接质量事故,生产线运转速度也丝毫不会降低。焊接机器人的广泛应用,为长安公司的汽车制造实现柔性自动化生产带来了前所未有的生机。
焊接机器人在应用中存在的问题
尽管焊接机器人在长安公司的汽车制造生产中得到广泛应用,使汽车焊接质量得到了极大改善,有效提高了企业的劳动生产效率,但仍有很多方面的问题值得我们去进一步研究和改善。
位置偏移后重新示教的问题
示教再现型焊接机器人如果发生焊接位置偏移时,必须进行在线示教然后再现运行,这个工作现在需要占用大量的生产时间。如果能够利用先进的计算机动态仿真技术对其进行离线示教和仿真,将是焊接机器人应用的一次革命性的改善。
弧焊机器人焊缝跟踪的问题
示教再现型弧焊机器人进行弧焊时,不能对焊缝进行动态跟踪反馈,因而焊缝有细微变化时,不能保证焊缝质量,如果能够应用智能技术,动态跟踪焊缝状态,就能有效保证弧焊质量的可靠性和稳定性。
目前,由于国内机器人的应用还不是非常广泛,国内机器人技术还有待于长足进步,机器人的专用部件国内还不能自行设计制造,长安公司大量应用焊接机器人后,配件问题成为机器人应用中最令人头痛的问题。因为机器人的部件多属专用部件(尤其是电器控制部分),技术水平要求相当高,因而必须从国外进口,而进口的机器人备件价格高企,国内代理公司大多不愿因大量预采购而造成资金积压,进口备件的时间周期又长,给汽车生产线造成了相当大的困难。
机器人的校轴过程占用过多时间。
长安公司所应用的KUKA、COMAU、OTC机器人,其轴的校正过程均需耗费比较长的时间,对于流水化的自动生产线来说,其停机所造成的经济损失非常巨大。如果能够应用高智能化的检测手段,使机器人在其轴的基本参数丢失或变化后,能够自动快速恢复到发生故障前的状态,将给自动化生产线带来巨大的生产效益 +&i
机器人电器控制系统的问题。
长安公司所应用的三种焊接机器人,其本体的机械可靠性及制造水平均相当高,本体出现故障(指机械故障)的概率极其微小。然而,相比之下,电气控制系统的故障率却非常高,最容易出现的部分是驱动部分的电路及元器件,另外接插件的故障频率也相当高。
当今世界上的机器人控制电路集成化程度已越来越高,控制技术的不断进步已使控制部分故障率大为降低。但对于汽车制造中的焊接作业这种环境恶劣、作业强度极大、电压波动较大的应用来说,如果能针对汽车生产的具体情况,进一步提高系统集成化程度,进一步增强系统抗干扰的能力,长安公司在未来应用大量机器人实现完全无人化生产线的理想将变为现实。
机器人与其它设备或工位上障碍物碰撞问题。
在长安公司的两条焊接线上,均出现过多次因为信号交换失误而发生机器人与机器人碰撞、机器人与其它设备或障碍物碰撞的事故。经过事后分析机器人工作程序,发现目前机器人控制系统在处理信号交换时,都采用外部I/O信号来交换彼此的工作状态,信号检测还只是以一个“点”的方式测量,即在某一运动程序行中,确认某一个交换信号是否存在来决定机器人是否继续下面的工作,而不是在一个运动区域中持续检测其它障碍物或机器人状态,这样,一旦检测过程结束而机器人的运动轨迹发生错误或信号交换不正常时,碰撞就发生了。
现在机器人的应用规模越来越大,多台机器人在狭窄空间内协同工作的场合越来越多,彼此之间信号交换已变得极其平常,如果能够在机器人的控制系统中,采用类似微软WINDOWS操作系统的后台处理方式来实时监测其它障碍物或机器人的工作状态,以决定机器人是否应该继续在有可能干涉的区域内工作,碰撞问题应能够得到有效的控制,甚至彻底解决这个问题。
综上所述,焊接机器人使汽车制造业大批量、高效率、高质量进行流水线汽车制造提供了有利保障,同时,焊接机器人在实际应用中暴露出来的问题,也促使我们不断努力学习先进技术,不断寻求更加有效的手段,让焊接机器人为中国的汽车制造业做出更大贡献。
举报 0
收藏 0
分享 139
-
熟背铝合金焊接口诀,秒杀一切焊接难题
2024-07-25 -
激光焊接技术
2024-07-10 -
创想焊缝跟踪系统适配研华宝元机器人自动化焊接
2024-05-23 -
焊装生产线规划及布置概述
2024-05-22
编辑推荐
最新资讯
-
全球产业链聚沪 共探双碳新路径 SNEC
2025-04-18 18:05
-
柯马签订具有约束力的协议收购 Autom
2025-04-17 13:01
-
高效协同新范式:比亚迪叉车领创智能
2025-04-17 10:04
-
埃马克德国总部迎来中国社科院工业经
2025-04-15 09:40
-
埃马克这项全新应用即将在CIMT惊艳首
2025-04-15 09:37