全球各大材企在车用热塑性材料方面的研发方向及进展
2017-08-22 22:44:13·
盖世汽车讯 据外媒报道,热塑性塑料(thermoplastics)材质的创新型汽车应用不断涌现,除车辆内饰、发动机罩及外饰外,该材料还被用于动力总成、底盘等部件。如今,众多材料供应商都在大力研发汽车应用材料,其中最为引人注目的无疑是对热塑性材料的研发。汽车业为提升车辆的燃油经济性,纷纷聚焦汽车轻量化,但在进行具体
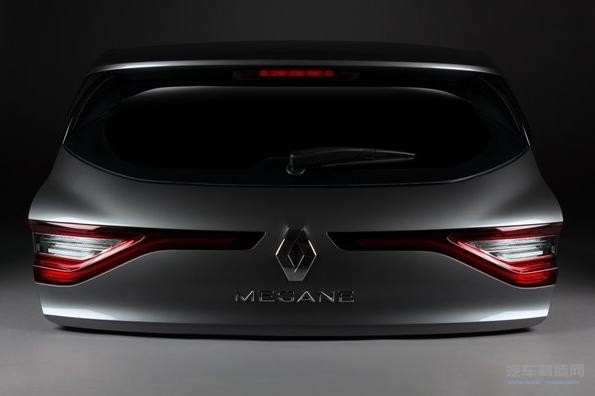
盖世汽车讯 据外媒报道,热塑性塑料(thermoplastics)材质的创新型汽车应用不断涌现,除车辆内饰、发动机罩及外饰外,该材料还被用于动力总成、底盘等部件。如今,众多材料供应商都在大力研发汽车应用材料,其中最为引人注目的无疑是对热塑性材料的研发。
汽车业为提升车辆的燃油经济性,纷纷聚焦汽车轻量化,但在进行具体的材料研发时,各大供应商势必还要考虑其他因素,如:材料耐热性、耐磨损、耐日光性、对燃油及化学物的耐腐性。小编为各位整理了全球各大材料的研发方向及进展,并将其划分为以下五大应用类别:
内饰与环境照明(Ambient Lighting)
据盛禧奥(Trinseo)新业务开发经理Jerry Majur透露,内饰与环境照明领域的个产品能否满足高档汽车内饰的整体要求。他指出,随着LED技术的面世与成熟,照明产品呈现出多样性。由于LEDs大幅提高了设计的灵活性,塑料件的应用使得制造商从上述技术中获益。
据盛禧奥汽车团队预计,消费者对内饰与环境照明设备的产品需求将会提高。他表示:“事实上,公司拥有一支专业的照明设计团队,为公司高性能塑料/消费品等重要市场业务提供支持,该团队与各大照明原始设备制造商有过合作,积累了丰富的专业知识与技术经验。”
美国舒曼公司(A. Schulman)的Frank Roederer点评道:“目前的产品趋势正朝着反射镜的前照明技术(forward-lighting technology)发展,LED技术的重要性较为明显。在过去,技术驱动源自于对车头灯反射镜(headlight reflectors)所用耐热材料的需求,然而,如今的需求都集中在尺寸稳定性(dimensional stabilities)上,因为这类反射镜的尺寸越来越小。多年来,舒曼一直提供镀ABS及耐热型ASA车灯外壳。”
Roederer表示:“公司主要供应车尾组合灯(rear combination lamp,RCL)、中置高位制动灯(center high mount stop lamp,CHMSL)、车牌卡片灯(pocket light )的外壳。”他还提到了新款散射光耐候性聚合物材料(light diffuse weatherable polymer)——Transparent Weatherable Polymer ASA TWP502,该材料可被用于LED照明设备,可被用于电镀、喷漆及焊接等二次加工。
据首席执行官Patrick Muezers透露,在透照镜研发方面,公司正在研发新款混合物,其由聚甲基丙烯酸甲酯(PMMA)、20%+的Xiran SMA共聚物(copolymer)组成,可被用于制作耐热性较好的PMMA车用LED灯应用,如:后灯片(rear-light lenses)及内饰导光板(interior light guides)。此类混合物能够很好地满足上述应用的需求,其优点包括:成本较低、提升了PMMA的流量,提升光效性能,设计自由度更高。
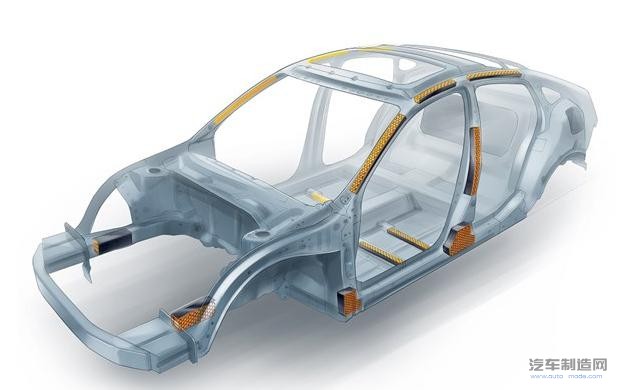
轻量化
据朗盛公司(LANXESS Corporation)的技术负责人Jose Chirino透露:“Tepex连续纤维复合层板(continuous fiber composite laminates)是一款创新型产品,其将连续纤维与热塑性塑料相结合,使材料的强度及刚度极高,可同时将零部件的重量降低极低的水平。目前,本田Clarity的后保险杠及车门模组托架(door-module carriers)就采用了该材料。”
据沙特基础工业公司(SABIC)汽车事业部全球负责人Scott Fallon透露,混合材料方案的应用正呈现上升趋势。展望未来,预计该行业将产生各类基于混合材料方案的应用,亦或是采用热塑性塑料及金属等多种材料。在量产型车辆中,Jeep Renegade车型汽车底板的槛板加强件(floor rocker reinforcement)就采用多种材料,用其替代多个钢制冲压件,该加强件能满足车辆侧面碰撞的材料规格及安全性要求。此外,相较于全钢结构的零部件,该加强件可实现减重50%。
改款Noryl GTX PPE采用了热塑性蜂窝设计,配有金属法兰,该零件可执行E涂层操作,且易于装配。而A/B/C柱及车底板横杆(floor cross-bars)等其他白车身(body-in-white,BIW)部件可实现减重5-8千克(11-18磅),且无需牺牲部件的结构防撞性(structural crashworthiness)。
PlastiComp公司位于美国明尼苏达州威诺纳(Winona, Minn.),该公司正定位结构件,其材料选用长丝碳纤维(long-carbon-fiber,LCF)热塑化合物、公司采用其独有的混合型颗粒物,其原材料分别为长玻璃纤维(LGF)及长丝碳纤维。公司的业务开发经理Steve Ouendag表示:“该混合颗粒物目前被用于尼龙66、聚丙烯(PP)及热塑性聚氨酯(TPU)。公司已与多家全球供应商合作,旨在采用LCF-PP与尼龙材料,用其替代发动机舱及动力总成装配件内的金属件。在更换铝质或金属铸件后,可实现最大减重50%。”
据塞拉尼斯工程材料公司(Celanese Engineered Materials)全球汽车OEM企业客户总监Jeffrey Helms透露,由于电池技术的技术改进已达到停滞状态,各大电动车制造商正大力寻找新技术方案,旨在为车辆减重,攻克电动车的续航里程受限这一技术难题,避免用户因上述难题而对电动车持忧虑的态度。
为实现电动车部件的超薄壁设计(ultra-thin-wall designs),选择正确的材料及模具能力(mold capability),其中就涉及到蓄电池盖及蓄电池托架等部件,最终实现车辆的减重。塞拉尼斯采用了高流量长纤维热塑技术(high-flow long-fiber thermoplastic technology),欲借助薄壁设计来降低原材料成本。除实现减重20-30%外,该设计使生产周期缩短了12%以上,该技术可持续增强模塑件玻璃纤维的长度,进而提升材料的强度及耐冲击性(impact resistance)。
巴斯夫分散体与树脂部(dispersions & resins division)新业务开发兼创意管理部(new business development and idea management)经理Henning Karbstein提出了热塑性塑料版的Acrodur丙烯酸粘合剂系统(acrylic binder systems)。该款粘合剂呈水溶液及乳胶离散剂的形式。他表示,该款产品对浸渍中纤维(impregnating fibers)的粘性较低,在室温状态下可实现预浸料坯(prepregs)的制作。这类半成品在固化前可展现其热塑性塑料的特性,在高温下,其受热后变形,然后固化为热固性复合材料(thermoset composites)。在整个过程中,唯一的副产品是水。
Karbstein指出,轻量化、高性能成为汽车行业对材料的两大需求趋势。部分注塑件(Injection molded)已被压塑非织造复合物(compression molded nonwoven composites)所替代,该工艺变动主要适用于呈扁平面的大型零部件,如:车门内面板或门架。Acrodur树脂的复合物纤维含量达到75%或更高。对于复杂零部件设计而言,相较于挤塑件,注塑件仍是其选择。
他表示:“公司采用二次成型技术(overmolding),完美结合了可持续天然纤维复合物的轻量化特性及注塑工艺的设计自由度两大优点。在执行该复合工艺时,将非织造复合物嵌入到大型扁平面内的注塑凹槽内,该操作步骤与传统的注塑的操作一致。随后,再注入热塑性塑料颗粒,通过削减零部件扁平区域的厚度,并将其替换为天然纤维复合物,进而实现了轻量化的效果,并为传统注塑设计提供了一定的自由度。”
他补充道,压塑及注塑聚丙烯材料的混用在业内并非什么秘密,因为该技术的应用已经有段时间了。然而,相较于聚丙烯, Ultramid尼龙可提升材料的机械性能,不仅能实现轻量化目标,还能改变应用的温度范围。此外,Acrodur还可被用作为纤维复合材料及非织造物嵌入件的粘合剂。

电气化
据苏威特种塑料公司(Solvay Specialty Polymers)全球汽车业务开发经理Brian Balen透露,对汽车业而言,Amodel苯丙醇胺(PPA)及Ryton聚苯硫醚(PPS)等高性能聚合物的需求在不断提升,该类产品被用于牵引电机、逆变器及48V技术的电子件。目前还采用上述两类树脂产品研发连接器、旋转变压器(resolvers)、汇流母线(bus-bars)、传感器及螺线管(solenoids)。
Amodell PPA产品系列中的AE-1XXX、AE-4XXX及AE-8XXX均采用了玻璃纤维增强件,其性能提升幅度从30%-60%。Amodel PPA则替换了传统的尼龙,根据新的材料规格要求,在高温下,要求提升电压并保留介电性能(dielectric properties)。
通常,当对材料的温度、尺寸稳定性、阻燃性(flame retardance)等诸多因素均有要求时,企业会选用Ryton PPS材料。目前,公司正采用该材料,用其替换这类电气元器件内的热固性材料及金属材料。苏威可提供各类PPS材料,其含有玻璃纤维或矿物填料(mineral filler)与玻璃纤维的混合物,具体的材料选用因视操作环境而定。
聚碳酸酯车用玻璃/车窗
沙特基础工业公司的Fallon表示,玻璃制作、涂层及制造技术上的进步不断,使得基于聚碳酸酯的车窗的制作成为可能,别克GL车型的后窗(rear-quarter window)就采用了该类车窗,这是一项显著的技术发展。
内饰——仪表盘托架(Instrument Panel Carriers)
荷兰公司Polyscope的首席执行官Patrick Muezers表示,公司正在研发混合材料,将以Xiloy品牌的名义对外出售,产品价格相对较低。该公司提出了一种创新方法,可兼容Xiran SMA及聚丙烯产品。目前,该公司内部正采用该材塑料生产零部件,旨在对产品及其性能进行优化。该公司定位仪表盘托架产品,相较于聚丙烯,SMA材料的温度范围较大,从-35℃-120℃(约合-31℉-248℉)。Muezers指出,该市场对该领域的侧重较大。他指出,相较于热稳定性能更强的非晶材料(amorphous material),聚丙烯的性能就存在不足,例如:低温下的性能不如前者优异,尤其是将其用于安全气囊时,表现尤为明显。
举报 0
收藏 0
分享 118
-
旭化成首战全球供应链管理大赛斩获佳绩
2025-03-03 -
旭化成授权斯尔邦高纯度碳酸盐生产技术,助力二
2024-12-13 -
华为尊界S800的座椅会有什么亮点?
2024-11-27 -
博世最新宣布裁员7000人
2024-11-06
编辑推荐
最新资讯
-
柯马签订具有约束力的协议收购 Autom
2025-04-17 13:01
-
高效协同新范式:比亚迪叉车领创智能
2025-04-17 10:04
-
埃马克德国总部迎来中国社科院工业经
2025-04-15 09:40
-
埃马克这项全新应用即将在CIMT惊艳首
2025-04-15 09:37
-
展会预告 | 2025CIMT中国国际机床展
2025-04-11 14:44