齿轮类零件变形影响因素及热处理工艺
2017-11-03 15:34:44· 来源:杨扬 锻压世界
摘要:对齿轮热处理变形的各种影响因素做了一定的分析,指出齿轮类零件的热处理变形主要受零件结构、材料、锻造、机加工、热处理工艺与设备等多方面因素的影响。
作者:杨扬,海侠女,王元栋
单位:陕西法士特汽车传动工程研究院
来源:《金属加工(热加工)》杂志
摘要:对齿轮热处理变形的各种影响因素做了一定的分析,指出齿轮类零件的热处理变形主要受零件结构、材料、锻造、机加工、热处理工艺与设备等多方面因素的影响。
一、渗碳热处理简介
汽车中常用的轴和齿轮需经过锻造、正火、机加工后,进行渗碳淬火和回火等工艺热处理,得到浅表层为硬度较高的渗碳层、心部为具有良好综合力学性能的组织,这些组织以及淬火后产生的残余应力对轴和齿轮的力学性能有着决定性的作用。目前,渗碳热处理在我公司应用普遍,也是较为成熟的一种热处理工艺。渗碳的目的是为了得到高碳表面层,以及低碳的心部,以保证心部高塑性高韧性,表层高硬度,提高工件的硬度、耐磨性和疲劳强度。
二、热处理变形浅析
1.影响热处理变形的因素
在零件进行热处理的同时,必然伴随着形状与尺寸的改变,这是组织应力、热应力及重力的共同作用结果。组织应力与热应力均为热处理应力,组织应力是指热处理过程各部位冷却的不同时性引起的各部位组织转变不同时所产生的应力,热应力是由于工件各部分的温度差异,导致热胀冷缩不均匀而引起的应力。淬火时,零件主要发生两种变形:几何形状的变形,主要为尺寸及形状的变形,由淬火应力引起;体积的变形,主要为工件体积按比例胀大或缩小,是由相变时的比体积变化引起。
影响零件热处理变形的因素很多,淬火过程只是释放了零件的变形潜在应力,而这些变形潜在应力是整个零件加工过程中不断累积的,可概括为材料的化学成分,锻造过程中的锻造温度、锻后冷却速度,机械加工过程中的进给速率、进刀量、切削速度、装夹方式,热处理过程中的加热速度、冷却速度、加热温度等各个方面的因素。热处理工序作为最后工序,其上游所有工序都会为零件热处理变形埋下种子,因此研究热处理变形不能单一地研究热处理工艺本身,而应该着眼于零件结构、材料以及零件的所有加工工序。
2.退火工艺
将偏离平衡状态的金属加热至较高温度,保持一定时间,然后缓慢冷却,以得到接近于平衡状态组织的各种工艺方法,统称为退火。退火的目的在于均匀化学成分、改善力学性能及工艺性能、消除或减小内应力,并为零件最终热处理提供合适的内部组织。
3.完全淬火工艺
将亚共析钢或其制件加热到Ac3点以上温度,保温后以大于临界冷却速度的冷速冷却,得到马氏体组织,以提高强度、硬度及耐磨性的热处理称为完全淬火。
三、零件热处理变形试验实例
我公司生产一种齿轮类零件,简图及热后机加工位置见图1。该零件的工艺流程为下料→锻造→正火→精车→滚齿→插内花键→剃齿→渗碳→淬火→回火→抛丸→磨棱→车端面及内孔。材料为8620RH,热处理技术要求为:淬硬层深0.84~1.34mm,表面硬度58~63HRC,心部硬度30~45HRC,金相组织符合TES-003标准。
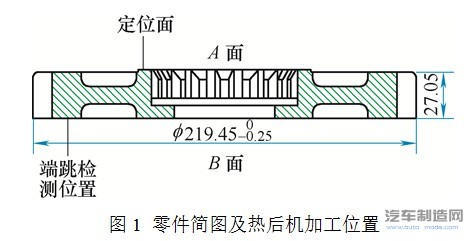
零件产量较大,采用串放式备料,其直径大(219.2~219.45mm),壁厚较薄(27.05mm),且结构为不完全对称,即B端面侧为直径小的内孔,而A端面侧为直径大的内花键,导致该类结构零件两端面(A和B端面)的热变形存在趋势不一致的特点。
2016年底,该零件成品突发热处理后B端面的跳动超差(工艺要求热后端面跳动值≤0.06mm)的情况,进而造成鼓形量与齿向角度超差。对该批次中剩余的已完成锻造、热前机加工序的零件,通过在热处理工序环节,进行临时试验、微调工艺,以最大程度控制热变形量、减小零件不合格率。
1.零件原热处理工艺
零件原先使用的热处理设备为AICHELIN42工位环形转底连续炉,集预氧化、渗碳、淬火、清洗、回火于一体。渗碳采用氮气、甲醇为基础气氛,丙酮作为富化剂,按照氮—甲醇气氛理论,供给比例为甲醇:氮气=1L/h:1.1m3/h,CO含量值仪表设定20%。原热处理工艺为:预氧化→渗碳→油淬→清洗、回火,工艺过程见图2,原淬火工艺见表1。
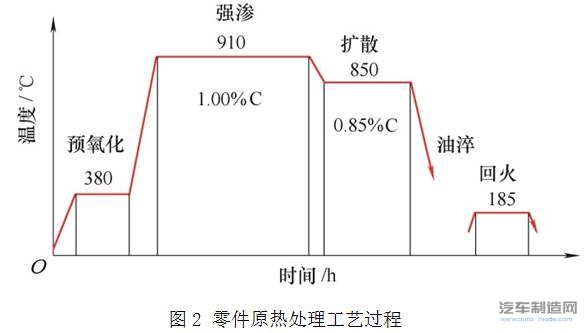
表1 原淬火油搅拌工艺参数
2.热处理工序环节的临时试验、微调工艺及结果分析
(1)增加退火工序及结果分析
采用高温回火炉退火,退火工艺设定为400℃保温2h,随炉冷却至350℃后空冷,再进行渗碳淬火。对热前和热后的端跳值进行一一对应测量。
由图3可知,退火渗碳零件端跳值的平均热变形量为0.033mm,但是因试验数据过少,仅作参考。
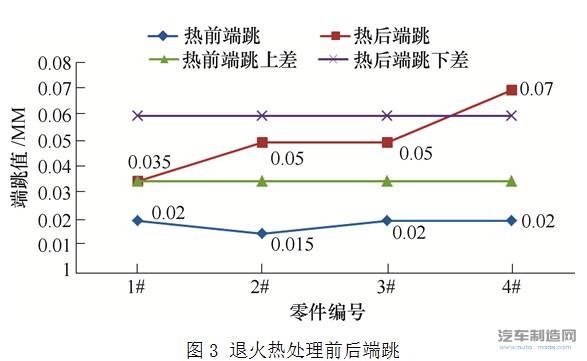
(2)调整淬火搅拌参数及结果分析
微调热处理工艺参数的前提条件是确保零件达到图样要求的各项热处理技术指标。对于一般的淬火工艺来说,最理想的状态为零件在快搅速度的设定时间内完成马氏体相变,而在接下来慢搅速度的设定时间内降低冷却速度以减少其热胀冷缩产生的变形,这样才能在保证完成热处理技术指标的同时最大程度地减小零件的热变形量。将淬火快搅时间降至45s,淬火慢搅速度降至700r/min,调整后的淬火搅拌参数见表2。
调整搅拌后,零件热处理前后端跳测量结果如图4所示,可知,零件使用调整淬火搅拌参数后的平均热变形端跳量为0.057mm,小于使用原淬火搅拌参数的平均热变形端跳量0.085mm。但是其大部分热后端跳值超出工艺要求上差,其热后端跳值标准偏差为0.015。
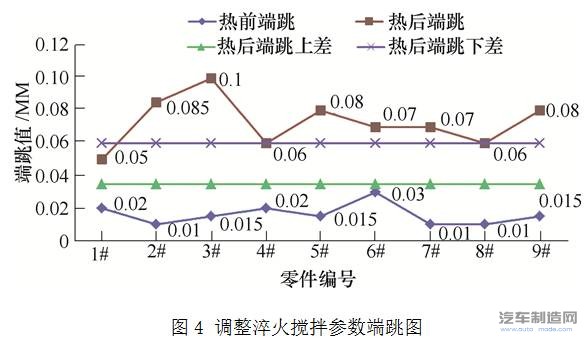
(3)增加退火工序+调整淬火搅拌参数及分析
基于上述两种试验(增加退火工序后热变形端跳量小(0.033),而调整淬火搅拌参数热后变形端跳量大(0.057)、离散性小(0.015)),将此两种方法同时用于该批次零件,即零件先进行退火,后使用调整后的搅拌参数进行渗碳淬火,观察零件的端跳热变形量。
第一,使用高温回火炉进行退火工序+调整淬火搅拌参数:使用高温回火炉进行退火工序,然后采用调整淬火搅拌参数进行渗碳淬火工序,零件热处理前后端跳测量结果如图5所示,可知热后端跳符合工艺要求,平均热变形端跳量为0.034mm,热后端跳标准偏差为0.018。
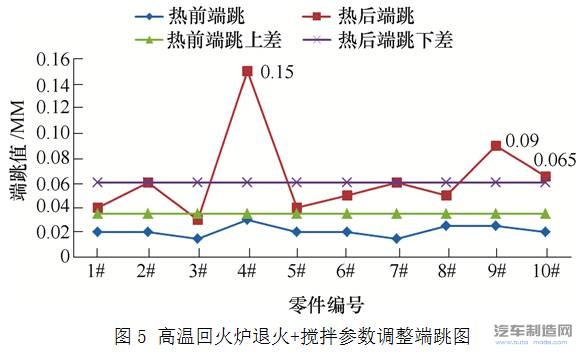
第二,使用环形炉进行退火工序+调整淬火搅拌参数:考虑到物流转运问题,进一步优化热处理工序,在环形炉预氧化区进行退火工序,按照退火工艺要求,在400℃保温2h后进入主炉渗碳,同时调整搅拌参数。零件热处理前后端跳测量结果如图6所示,可知热后端跳符合工艺要求,平均热变形端跳值为0.036mm,热后端跳标准偏差为0.017。
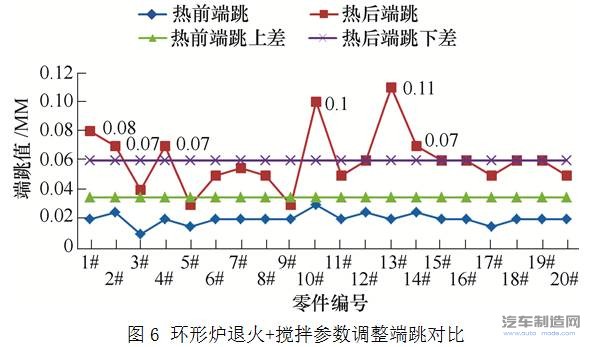
对以上4种微调工艺与原工艺及其热变形结果进行对比,可知仅调整淬火搅拌参数补救工艺的热后端跳值较大,大于增加退火+调整淬火搅拌参数的工艺类型,选用后类补救工艺类型,从生产现场的可行性考虑,环形炉预氧化区退火+搅拌参数调整的工艺类型优于高温回火炉退火+搅拌参数调整的工艺类型,如表3所示。
采用最优化补救工艺:环形炉预氧化区退火+搅拌参数调整,对该批次剩余零件进行生产,零件的不合格率由突发时的30%降至6%,大幅度降低了不合格率,为公司有效地降低了经济损失。
四、结语
机加后渗碳淬火前增加退火工序、配合调整淬火搅拌参数能有效改善零件的热处理变形,为之后类似问题提供了可行的补救工艺。但零件的热处理变形并不是只靠热处理工艺调整就能完全解决,热前各工序对最终热处理的变形都会造成一定的影响,最终产品符合性需要各工序共同协调,相互配合,寻找合适的工艺,以提高零件的合格率,保证产品质量。
单位:陕西法士特汽车传动工程研究院
来源:《金属加工(热加工)》杂志
摘要:对齿轮热处理变形的各种影响因素做了一定的分析,指出齿轮类零件的热处理变形主要受零件结构、材料、锻造、机加工、热处理工艺与设备等多方面因素的影响。
一、渗碳热处理简介
汽车中常用的轴和齿轮需经过锻造、正火、机加工后,进行渗碳淬火和回火等工艺热处理,得到浅表层为硬度较高的渗碳层、心部为具有良好综合力学性能的组织,这些组织以及淬火后产生的残余应力对轴和齿轮的力学性能有着决定性的作用。目前,渗碳热处理在我公司应用普遍,也是较为成熟的一种热处理工艺。渗碳的目的是为了得到高碳表面层,以及低碳的心部,以保证心部高塑性高韧性,表层高硬度,提高工件的硬度、耐磨性和疲劳强度。
二、热处理变形浅析
1.影响热处理变形的因素
在零件进行热处理的同时,必然伴随着形状与尺寸的改变,这是组织应力、热应力及重力的共同作用结果。组织应力与热应力均为热处理应力,组织应力是指热处理过程各部位冷却的不同时性引起的各部位组织转变不同时所产生的应力,热应力是由于工件各部分的温度差异,导致热胀冷缩不均匀而引起的应力。淬火时,零件主要发生两种变形:几何形状的变形,主要为尺寸及形状的变形,由淬火应力引起;体积的变形,主要为工件体积按比例胀大或缩小,是由相变时的比体积变化引起。
影响零件热处理变形的因素很多,淬火过程只是释放了零件的变形潜在应力,而这些变形潜在应力是整个零件加工过程中不断累积的,可概括为材料的化学成分,锻造过程中的锻造温度、锻后冷却速度,机械加工过程中的进给速率、进刀量、切削速度、装夹方式,热处理过程中的加热速度、冷却速度、加热温度等各个方面的因素。热处理工序作为最后工序,其上游所有工序都会为零件热处理变形埋下种子,因此研究热处理变形不能单一地研究热处理工艺本身,而应该着眼于零件结构、材料以及零件的所有加工工序。
2.退火工艺
将偏离平衡状态的金属加热至较高温度,保持一定时间,然后缓慢冷却,以得到接近于平衡状态组织的各种工艺方法,统称为退火。退火的目的在于均匀化学成分、改善力学性能及工艺性能、消除或减小内应力,并为零件最终热处理提供合适的内部组织。
3.完全淬火工艺
将亚共析钢或其制件加热到Ac3点以上温度,保温后以大于临界冷却速度的冷速冷却,得到马氏体组织,以提高强度、硬度及耐磨性的热处理称为完全淬火。
三、零件热处理变形试验实例
我公司生产一种齿轮类零件,简图及热后机加工位置见图1。该零件的工艺流程为下料→锻造→正火→精车→滚齿→插内花键→剃齿→渗碳→淬火→回火→抛丸→磨棱→车端面及内孔。材料为8620RH,热处理技术要求为:淬硬层深0.84~1.34mm,表面硬度58~63HRC,心部硬度30~45HRC,金相组织符合TES-003标准。
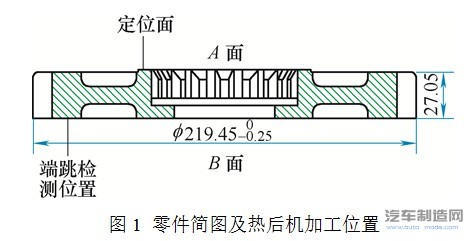
零件产量较大,采用串放式备料,其直径大(219.2~219.45mm),壁厚较薄(27.05mm),且结构为不完全对称,即B端面侧为直径小的内孔,而A端面侧为直径大的内花键,导致该类结构零件两端面(A和B端面)的热变形存在趋势不一致的特点。
2016年底,该零件成品突发热处理后B端面的跳动超差(工艺要求热后端面跳动值≤0.06mm)的情况,进而造成鼓形量与齿向角度超差。对该批次中剩余的已完成锻造、热前机加工序的零件,通过在热处理工序环节,进行临时试验、微调工艺,以最大程度控制热变形量、减小零件不合格率。
1.零件原热处理工艺
零件原先使用的热处理设备为AICHELIN42工位环形转底连续炉,集预氧化、渗碳、淬火、清洗、回火于一体。渗碳采用氮气、甲醇为基础气氛,丙酮作为富化剂,按照氮—甲醇气氛理论,供给比例为甲醇:氮气=1L/h:1.1m3/h,CO含量值仪表设定20%。原热处理工艺为:预氧化→渗碳→油淬→清洗、回火,工艺过程见图2,原淬火工艺见表1。
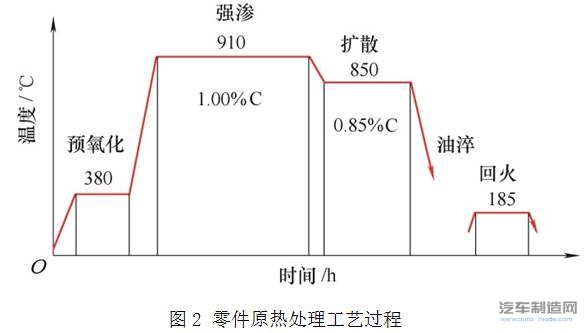
表1 原淬火油搅拌工艺参数
快搅速度/r·min-1
|
快搅时间/s
|
慢搅速度/r·min-1
|
淬火总时间/s
|
1100
|
240
|
1100
|
239
|
2.热处理工序环节的临时试验、微调工艺及结果分析
(1)增加退火工序及结果分析
采用高温回火炉退火,退火工艺设定为400℃保温2h,随炉冷却至350℃后空冷,再进行渗碳淬火。对热前和热后的端跳值进行一一对应测量。
由图3可知,退火渗碳零件端跳值的平均热变形量为0.033mm,但是因试验数据过少,仅作参考。
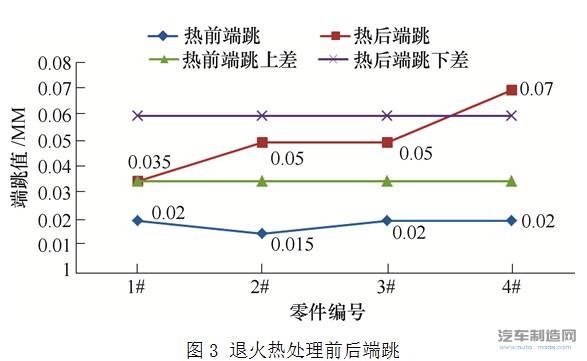
(2)调整淬火搅拌参数及结果分析
微调热处理工艺参数的前提条件是确保零件达到图样要求的各项热处理技术指标。对于一般的淬火工艺来说,最理想的状态为零件在快搅速度的设定时间内完成马氏体相变,而在接下来慢搅速度的设定时间内降低冷却速度以减少其热胀冷缩产生的变形,这样才能在保证完成热处理技术指标的同时最大程度地减小零件的热变形量。将淬火快搅时间降至45s,淬火慢搅速度降至700r/min,调整后的淬火搅拌参数见表2。
表2 调整后的淬火搅拌参数
快搅速度/ r·min-1
|
快搅时间/s
|
慢搅速度/ r·min-1
|
淬火总时间/s
|
1100
|
45
|
700
|
239
|
调整搅拌后,零件热处理前后端跳测量结果如图4所示,可知,零件使用调整淬火搅拌参数后的平均热变形端跳量为0.057mm,小于使用原淬火搅拌参数的平均热变形端跳量0.085mm。但是其大部分热后端跳值超出工艺要求上差,其热后端跳值标准偏差为0.015。
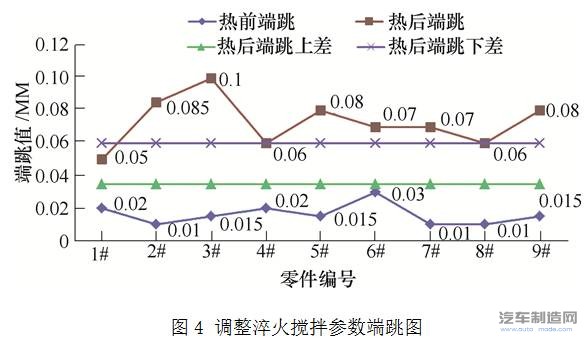
(3)增加退火工序+调整淬火搅拌参数及分析
基于上述两种试验(增加退火工序后热变形端跳量小(0.033),而调整淬火搅拌参数热后变形端跳量大(0.057)、离散性小(0.015)),将此两种方法同时用于该批次零件,即零件先进行退火,后使用调整后的搅拌参数进行渗碳淬火,观察零件的端跳热变形量。
第一,使用高温回火炉进行退火工序+调整淬火搅拌参数:使用高温回火炉进行退火工序,然后采用调整淬火搅拌参数进行渗碳淬火工序,零件热处理前后端跳测量结果如图5所示,可知热后端跳符合工艺要求,平均热变形端跳量为0.034mm,热后端跳标准偏差为0.018。
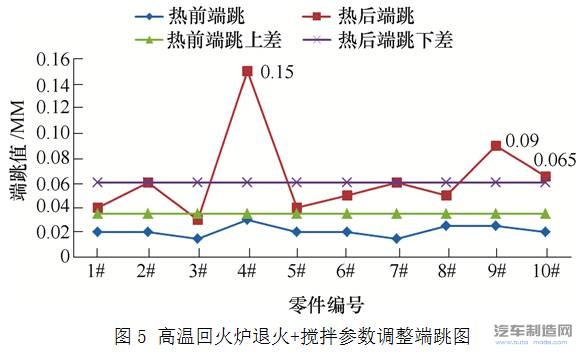
第二,使用环形炉进行退火工序+调整淬火搅拌参数:考虑到物流转运问题,进一步优化热处理工序,在环形炉预氧化区进行退火工序,按照退火工艺要求,在400℃保温2h后进入主炉渗碳,同时调整搅拌参数。零件热处理前后端跳测量结果如图6所示,可知热后端跳符合工艺要求,平均热变形端跳值为0.036mm,热后端跳标准偏差为0.017。
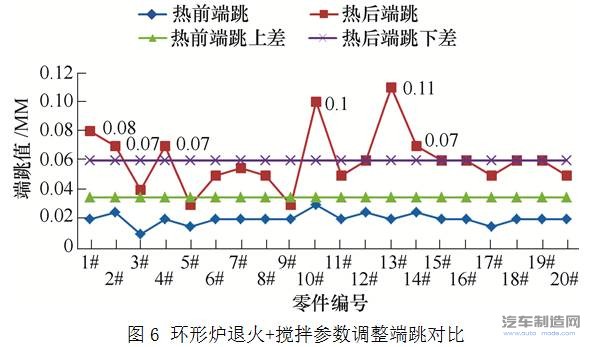
对以上4种微调工艺与原工艺及其热变形结果进行对比,可知仅调整淬火搅拌参数补救工艺的热后端跳值较大,大于增加退火+调整淬火搅拌参数的工艺类型,选用后类补救工艺类型,从生产现场的可行性考虑,环形炉预氧化区退火+搅拌参数调整的工艺类型优于高温回火炉退火+搅拌参数调整的工艺类型,如表3所示。
采用最优化补救工艺:环形炉预氧化区退火+搅拌参数调整,对该批次剩余零件进行生产,零件的不合格率由突发时的30%降至6%,大幅度降低了不合格率,为公司有效地降低了经济损失。
表3 试验工艺较原工艺对生产情况的影响
工艺调整类型
|
增加时间/h
|
增加工序
|
备注
|
退火(回火炉)
|
6
|
转运、备料
|
需占用回火炉
|
调整搅拌工艺
|
0
|
无
|
—
|
退火(回火炉)+调整搅拌工艺
|
6
|
转运、备料
|
需占用回火炉
|
退火(环形炉)+调整搅拌工艺
|
3
|
无
|
产生部分空位
|
四、结语
机加后渗碳淬火前增加退火工序、配合调整淬火搅拌参数能有效改善零件的热处理变形,为之后类似问题提供了可行的补救工艺。但零件的热处理变形并不是只靠热处理工艺调整就能完全解决,热前各工序对最终热处理的变形都会造成一定的影响,最终产品符合性需要各工序共同协调,相互配合,寻找合适的工艺,以提高零件的合格率,保证产品质量。
- 下一篇:TORNOS高效ACB断屑循环
- 上一篇:摩尔定律被终结?是挑战也是机遇
编辑推荐
最新资讯
-
全球产业链聚沪 共探双碳新路径 SNEC
2025-04-18 18:05
-
柯马签订具有约束力的协议收购 Autom
2025-04-17 13:01
-
高效协同新范式:比亚迪叉车领创智能
2025-04-17 10:04
-
埃马克德国总部迎来中国社科院工业经
2025-04-15 09:40
-
埃马克这项全新应用即将在CIMT惊艳首
2025-04-15 09:37