简单分析激光切割参数对切割质量影响
2017-12-14 14:58:39· 来源:金属加工
北京汽车制造厂有限公司用功率为500W的激光器切割各种车身及车架零件。本文结合实际生产中发生的切割质量不良零件状态确定试验项目,重点从激光功率、切割速度、气体压力、零件间距、零件材质五个工艺参数及切割误差入手,对常用材料进行模拟环境切割试验。
1. 概述
目前,在汽车制造领域,激光切割技术都已经获得广泛应用。北京汽车制造厂有限公司用功率为500W的激光器切割各种车身及车架零件。本文结合实际生产中发生的切割质量不良零件状态确定试验项目,重点从激光功率、切割速度、气体压力、零件间距、零件材质五个工艺参数及切割误差入手,对常用材料进行模拟环境切割试验。通过对比激光切割光束形态及切割质量,研究激光切割参数对零件切割质量的影响,得出大概结论后再通过实际零件切割分析产生不良原因及解决措施并最终避免不良问题的发生。
2. 试验研究
(1)确定试验材料及零件 结合生产计划确定试验钢板材料:DC01/SS400碳钢(t=1.0mm、2.0mm、3.0mm、5.0mm)、劣质SS400/t=3.0mm。
结合不良零件确定试验零件为勇士车型车架零件:绞盘支架补强板(B1210616AA,SS400/t=3.0mm)、前保险杠支架(B1210713AA,SS400/t=5.0mm)。
(2)试验设备 切割设备:3D机器人光纤激光切割机(型号:TH-RCF2010S-500, 史陶比尔机器人为载体)。测量设备:游标卡尺、钢板尺、三坐标测量仪、ATOS扫描仪。
(3)确定试验项目 试验共测试五个工艺参数及切割误差以及两种勇士车型零件,利用多种板材在各种既定环境下进行切割,通过观察激光切割光束形态及零件切割质量作为后续分析数据依据。具体测试项目及方法如表1所示。
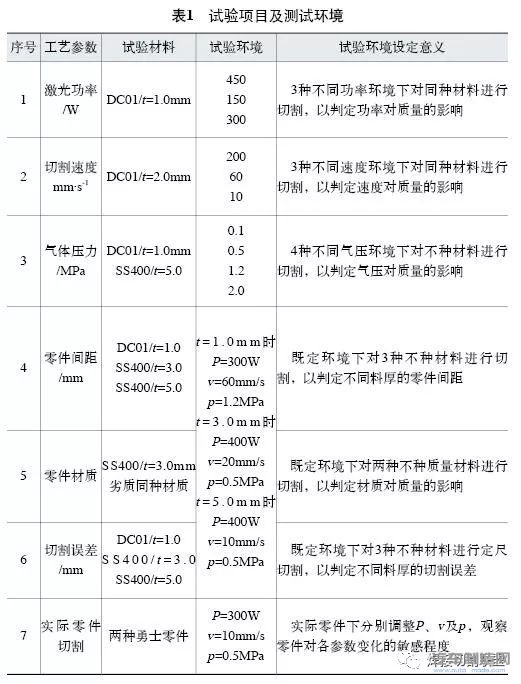
(4)确定零件切割质量判定标准 零件切割质量可通过目测切割过程中光束形态及测量零件来进行判定,其中光束形态通过光束形状及飞溅两个方面进行目测;零件质量通过从断面质量、表面质量、批次状态、零件尺寸、零件变形及焊瘤大小六个方面进行判定。具体检验方法及判定标准如表2、表3所示。
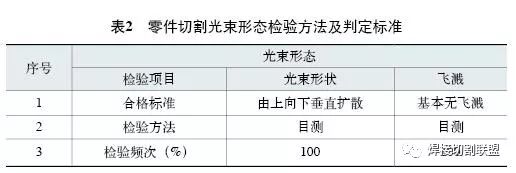
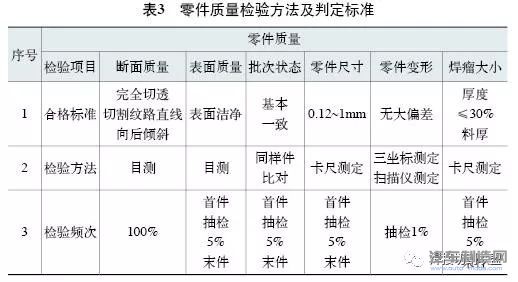
3. 试验过程及结果分析
(1)激光功率 试验中对同种材料进行3种不同激光功率环境的切割,具体结果如下。
首先,激光功率设定过大时(450W),整个切割面熔化,切缝过大,得不到良好的切割质量,如图1a所示。
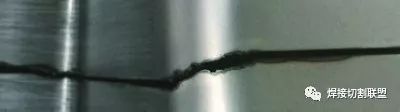
图1a
其次,激光功率设定不足时(150W),产生切割熔渣,切割断面上产生焊瘤,如图1b所示。
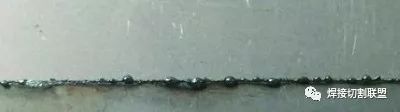
图1b
最后,激光功率设定中等时(300W),切割质量达到标准。
通过此试验得知激光功率过大或过小都无法得到良好的切割断面,因此需设定适当的激光功率,配合适当的切割气体压力及速度,才能得到良好的切割质量,保证无熔渣产生。
(2)切割速度 试验中对同种材料进行3种不同切割速度环境的切割,试验中发现切割速度不同切割火花形态及断面质量(切割断面纹路)均不同,具体结果如下。
首先,正常速度(60mm/s)的火花是由上往下扩散的, 断面纹路直线并稍向后倾斜,表面光洁无熔渣产生,如图2a、图2d所示。
其次,速度过快(200mm/s)时火花向后倾斜, 切割断面粗糙且纹路呈大角度向后倾斜弯曲,零件下方产生熔渣,断面有些区域能切断有些区域则不能,如图2b、图2e所示。
最后,速度过慢(10mm/s)时火花少且不扩散,板材过烧,切割断面粗糙,切缝变宽,小转角部位整个区域熔化,如图2c、图2f所示。
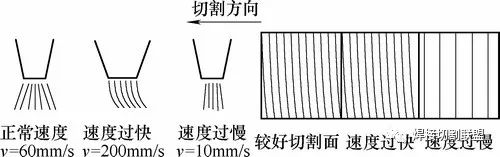
图2 切割火花及断面效果
因此得知选择适当的切割速度,可使火花形态良好,切割断面呈现较平稳线条,且零件下方没有熔渣,不会出现切不断或板材过烧,区域熔化的现象。可见不同的切割速度对激光品质有重大影响,如切缝宽度和断面质量。
(3)气体压力 试验设备配备液态氧气作为切割气体,先测试DC01/t=1.0mm在0.1MPa、1.2MPa、2.0MPa下切割,后测试SS400/t=5.0mm在0.1MPa、0.5MPa、2.0MPa下切割,不同环境下综合分析如下。
首先,气体压力不足时(0.1MPa),会产生焊瘤,直接影响切割速度。
其次,气体压力过高时(2.0MPa)会造成断面粗糙,切缝较宽,断面部分熔化,无法达到良好的切割质量。
最后,气体压力适中时(1.2MPa/0.5MPa),质量合格。
试验发现气体压力对切割作用很大,切割气体有助于散热、助燃、吹走残渣。同时发现,对薄板件切孔采用较高的气体压力且效率高、质量良好,如图3a所示;而对厚板件切孔则采用较低的气体压力且效率低质量较差,如图3b所示。因此建议采用特定的打孔方式(如钻孔),以提高工作效率。
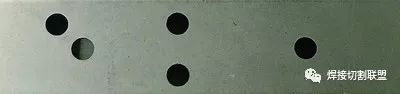
(a)
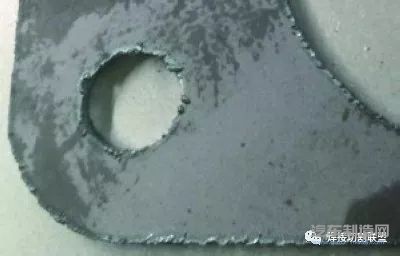
(b)
图3 薄板与厚板切割对比
(4)零件间距 试验中对3种料厚板材进行测试,重点从最小孔径进行测试,具体如下。
首先,DC01/t=1.0mm时,1mm直径圆孔无法保证质量(切割引线无法预留),2mm直径圆孔质量过关。
其次,SS400/t=3.0mm时3mm圆孔质量达标,2mm无法实现。
最后,SS400/t=5.0mm时5mm圆孔质量达标,4mm无法实现。
得知最小孔径一般大于等于板材料厚,如执意加工小于板厚的小孔则不能保证切割断面质量,可能会因零件质量不良而造成报废。实际生产中考虑到浮头的正常工作以及热影响,切割板材边缘、零件间最小间距及最小切割孔径一般最少预留10mm距离,以保证正常加工。
(5)零件材质 激光切割对加工零件材质有较高要求,不同碳含量材质加工出的零件质量会大不相同。
试验中两种不同质量的SS400/t=3.0mm进行切割对比,其中劣质材料在切割时产生爆点(正常切割中到一部位突然爆炸,如图4所示)。经分析得知,产生爆点的主要原因是材料内部杂质较多,分布不均造成。
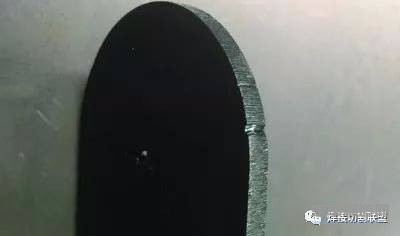
图4 爆点
因此为得到高质量零件同时为保护镜片,一般建议采用高品质板材(如宝钢)进行激光切割。
(6)切割误差 试验中通过对3种不同料厚材料进行切割,每种料厚各进行四次切割误差测量,测量数据如表4所示。将各数据描点形成散点图,各散点连线得知各误差值上下浮动范围在±0.1mm之间,且随材料厚度增加而增大,如图5所示。
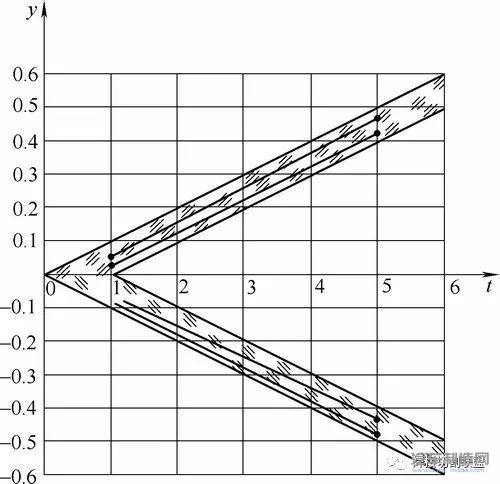
图5 材料厚度t与切割误差y关系
激光加工过程中除去切缝材料被去除外,由于受热切缝附近材料也会受影响,零件存在着不完全可控的热变形,因此会存在一定的切割误差。鉴于误差值的存在,需要编程人员与现场操作者非常了解该误差值,并通过采取一些措施尽量避免误差的出现。分析得知,注意以下事项可使误差值减小:①切割加工时必须使用合适的刀具补偿。②测量误差值时应该选择在无切割焊渣且无变形的位置进行测量。③选择合适的切割料片大小,即切割成型零件时尽量以单料片1~2件零件为佳,切割平面料片时尽量以单料片5~10件零件为佳。④良好的光路元件及光路调试是控制误差的必然。
(7)实际零件切割 通过上述试验分析发现以上因素中零件材质及间距属于可控制因素,可通过控制其他因素进行控制;切割误差虽难以避免但是可根据经验控制在一定误差范围内;其余激光功率、切割速度、气体压力三个工艺参数在实际切割中均需进行参数的设定。鉴于此,重点从后面三个工艺参数入手进行调整,以分析此三个工艺参数对切割质量的敏感程度。
针对不良零件(前保险杠支架,SS400/t=5.0mm,如图6a所示)分析产生不良的原因,得知原因可能为以下三个:切割速度不足、切割速度过快或气体压力不足。试验中分别单独调整以上3个工艺参数,调整量分别为P=xW±50W、v=xmm/s±10mm/s及p=xMPa±0.1MPa,当调整至P=300W、v=10mm/s、p=0.5MPa时切割质量达到最佳。在调整过程中通过观察各工艺参数对切割质量的敏感度得出三者敏感程度排序:气体压力>切割速度过快>切割速度不足。得出此结论后为确定其准确性,再切割不同料厚勇士零件(绞盘支架补强板,SS400/t=3.0mm,如图6b所示)进行二次确认,得出同样的结论。
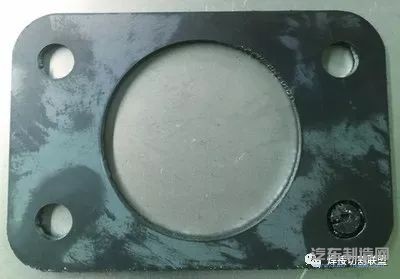
(a)前保险杠支架
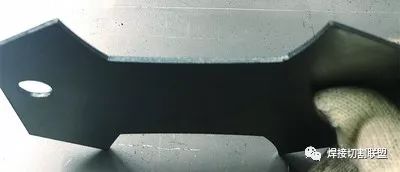
(b)绞盘支架补强板
图6 勇士零件切割
通过此激光切割试验,将四个工艺参数(除零件材质)及切割误差的试验结论数据汇总,如表5所示。
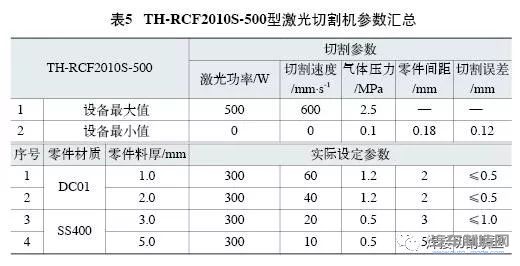
4. 总结
本文对不同厚度碳钢及实际零件在不同测试环境下切割,通过观察激光火花的形态及零件切割质量对各参数进行分析,结论如下:
(1)试验所述工艺参数及切割误差均会不同程度影响激光切割质量,不同切割环境下影响程度大不相同,为提高切割质量必须综合考虑各因素,控制各因素间的关系,以使切割质量达到最优。
(2)在调整切割参数时,气体压力对零件质量的敏感程度最大,切割速度次之,激光功率最小。
目前,在汽车制造领域,激光切割技术都已经获得广泛应用。北京汽车制造厂有限公司用功率为500W的激光器切割各种车身及车架零件。本文结合实际生产中发生的切割质量不良零件状态确定试验项目,重点从激光功率、切割速度、气体压力、零件间距、零件材质五个工艺参数及切割误差入手,对常用材料进行模拟环境切割试验。通过对比激光切割光束形态及切割质量,研究激光切割参数对零件切割质量的影响,得出大概结论后再通过实际零件切割分析产生不良原因及解决措施并最终避免不良问题的发生。
2. 试验研究
(1)确定试验材料及零件 结合生产计划确定试验钢板材料:DC01/SS400碳钢(t=1.0mm、2.0mm、3.0mm、5.0mm)、劣质SS400/t=3.0mm。
结合不良零件确定试验零件为勇士车型车架零件:绞盘支架补强板(B1210616AA,SS400/t=3.0mm)、前保险杠支架(B1210713AA,SS400/t=5.0mm)。
(2)试验设备 切割设备:3D机器人光纤激光切割机(型号:TH-RCF2010S-500, 史陶比尔机器人为载体)。测量设备:游标卡尺、钢板尺、三坐标测量仪、ATOS扫描仪。
(3)确定试验项目 试验共测试五个工艺参数及切割误差以及两种勇士车型零件,利用多种板材在各种既定环境下进行切割,通过观察激光切割光束形态及零件切割质量作为后续分析数据依据。具体测试项目及方法如表1所示。
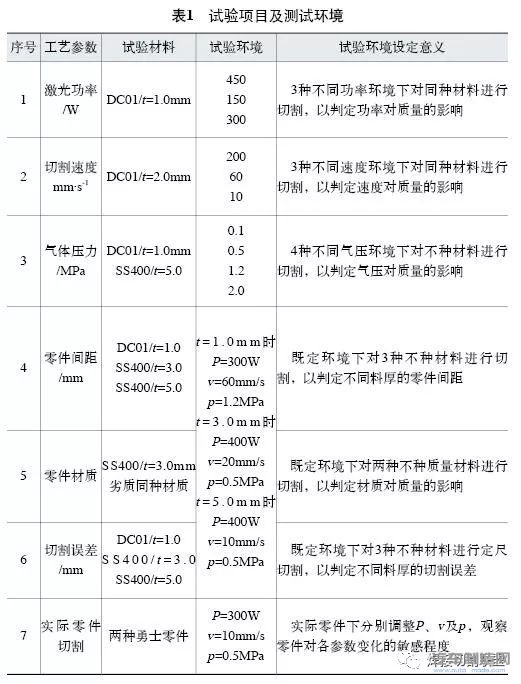
(4)确定零件切割质量判定标准 零件切割质量可通过目测切割过程中光束形态及测量零件来进行判定,其中光束形态通过光束形状及飞溅两个方面进行目测;零件质量通过从断面质量、表面质量、批次状态、零件尺寸、零件变形及焊瘤大小六个方面进行判定。具体检验方法及判定标准如表2、表3所示。
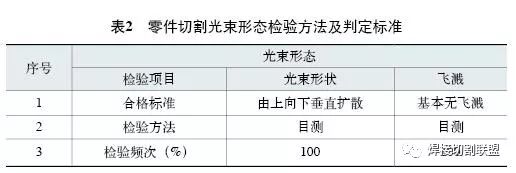
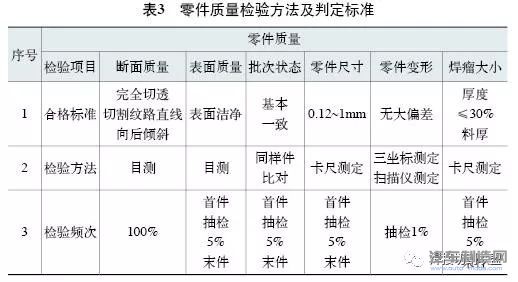
3. 试验过程及结果分析
(1)激光功率 试验中对同种材料进行3种不同激光功率环境的切割,具体结果如下。
首先,激光功率设定过大时(450W),整个切割面熔化,切缝过大,得不到良好的切割质量,如图1a所示。
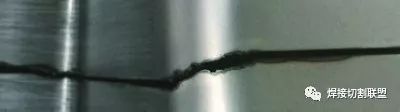
图1a
其次,激光功率设定不足时(150W),产生切割熔渣,切割断面上产生焊瘤,如图1b所示。
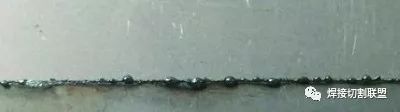
图1b
最后,激光功率设定中等时(300W),切割质量达到标准。
通过此试验得知激光功率过大或过小都无法得到良好的切割断面,因此需设定适当的激光功率,配合适当的切割气体压力及速度,才能得到良好的切割质量,保证无熔渣产生。
(2)切割速度 试验中对同种材料进行3种不同切割速度环境的切割,试验中发现切割速度不同切割火花形态及断面质量(切割断面纹路)均不同,具体结果如下。
首先,正常速度(60mm/s)的火花是由上往下扩散的, 断面纹路直线并稍向后倾斜,表面光洁无熔渣产生,如图2a、图2d所示。
其次,速度过快(200mm/s)时火花向后倾斜, 切割断面粗糙且纹路呈大角度向后倾斜弯曲,零件下方产生熔渣,断面有些区域能切断有些区域则不能,如图2b、图2e所示。
最后,速度过慢(10mm/s)时火花少且不扩散,板材过烧,切割断面粗糙,切缝变宽,小转角部位整个区域熔化,如图2c、图2f所示。
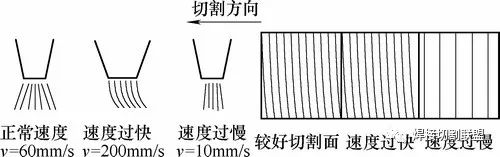
图2 切割火花及断面效果
因此得知选择适当的切割速度,可使火花形态良好,切割断面呈现较平稳线条,且零件下方没有熔渣,不会出现切不断或板材过烧,区域熔化的现象。可见不同的切割速度对激光品质有重大影响,如切缝宽度和断面质量。
(3)气体压力 试验设备配备液态氧气作为切割气体,先测试DC01/t=1.0mm在0.1MPa、1.2MPa、2.0MPa下切割,后测试SS400/t=5.0mm在0.1MPa、0.5MPa、2.0MPa下切割,不同环境下综合分析如下。
首先,气体压力不足时(0.1MPa),会产生焊瘤,直接影响切割速度。
其次,气体压力过高时(2.0MPa)会造成断面粗糙,切缝较宽,断面部分熔化,无法达到良好的切割质量。
最后,气体压力适中时(1.2MPa/0.5MPa),质量合格。
试验发现气体压力对切割作用很大,切割气体有助于散热、助燃、吹走残渣。同时发现,对薄板件切孔采用较高的气体压力且效率高、质量良好,如图3a所示;而对厚板件切孔则采用较低的气体压力且效率低质量较差,如图3b所示。因此建议采用特定的打孔方式(如钻孔),以提高工作效率。
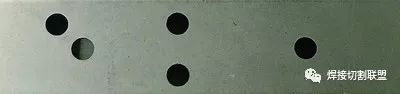
(a)
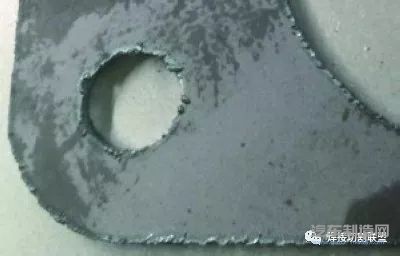
(b)
图3 薄板与厚板切割对比
(4)零件间距 试验中对3种料厚板材进行测试,重点从最小孔径进行测试,具体如下。
首先,DC01/t=1.0mm时,1mm直径圆孔无法保证质量(切割引线无法预留),2mm直径圆孔质量过关。
其次,SS400/t=3.0mm时3mm圆孔质量达标,2mm无法实现。
最后,SS400/t=5.0mm时5mm圆孔质量达标,4mm无法实现。
得知最小孔径一般大于等于板材料厚,如执意加工小于板厚的小孔则不能保证切割断面质量,可能会因零件质量不良而造成报废。实际生产中考虑到浮头的正常工作以及热影响,切割板材边缘、零件间最小间距及最小切割孔径一般最少预留10mm距离,以保证正常加工。
(5)零件材质 激光切割对加工零件材质有较高要求,不同碳含量材质加工出的零件质量会大不相同。
试验中两种不同质量的SS400/t=3.0mm进行切割对比,其中劣质材料在切割时产生爆点(正常切割中到一部位突然爆炸,如图4所示)。经分析得知,产生爆点的主要原因是材料内部杂质较多,分布不均造成。
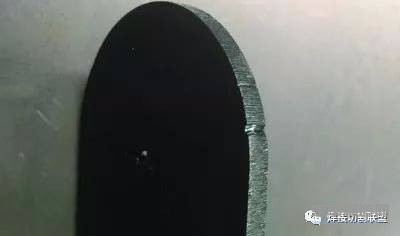
图4 爆点
因此为得到高质量零件同时为保护镜片,一般建议采用高品质板材(如宝钢)进行激光切割。
(6)切割误差 试验中通过对3种不同料厚材料进行切割,每种料厚各进行四次切割误差测量,测量数据如表4所示。将各数据描点形成散点图,各散点连线得知各误差值上下浮动范围在±0.1mm之间,且随材料厚度增加而增大,如图5所示。
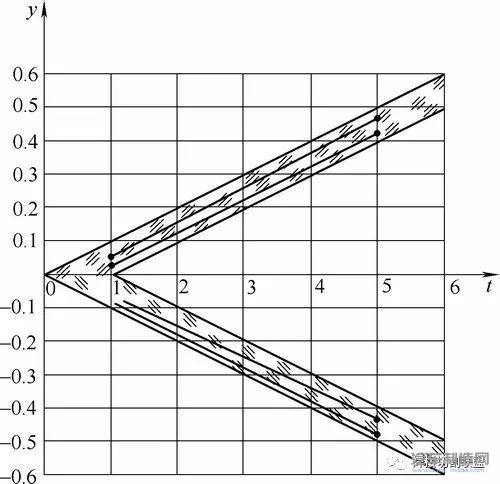
图5 材料厚度t与切割误差y关系
激光加工过程中除去切缝材料被去除外,由于受热切缝附近材料也会受影响,零件存在着不完全可控的热变形,因此会存在一定的切割误差。鉴于误差值的存在,需要编程人员与现场操作者非常了解该误差值,并通过采取一些措施尽量避免误差的出现。分析得知,注意以下事项可使误差值减小:①切割加工时必须使用合适的刀具补偿。②测量误差值时应该选择在无切割焊渣且无变形的位置进行测量。③选择合适的切割料片大小,即切割成型零件时尽量以单料片1~2件零件为佳,切割平面料片时尽量以单料片5~10件零件为佳。④良好的光路元件及光路调试是控制误差的必然。
(7)实际零件切割 通过上述试验分析发现以上因素中零件材质及间距属于可控制因素,可通过控制其他因素进行控制;切割误差虽难以避免但是可根据经验控制在一定误差范围内;其余激光功率、切割速度、气体压力三个工艺参数在实际切割中均需进行参数的设定。鉴于此,重点从后面三个工艺参数入手进行调整,以分析此三个工艺参数对切割质量的敏感程度。
针对不良零件(前保险杠支架,SS400/t=5.0mm,如图6a所示)分析产生不良的原因,得知原因可能为以下三个:切割速度不足、切割速度过快或气体压力不足。试验中分别单独调整以上3个工艺参数,调整量分别为P=xW±50W、v=xmm/s±10mm/s及p=xMPa±0.1MPa,当调整至P=300W、v=10mm/s、p=0.5MPa时切割质量达到最佳。在调整过程中通过观察各工艺参数对切割质量的敏感度得出三者敏感程度排序:气体压力>切割速度过快>切割速度不足。得出此结论后为确定其准确性,再切割不同料厚勇士零件(绞盘支架补强板,SS400/t=3.0mm,如图6b所示)进行二次确认,得出同样的结论。
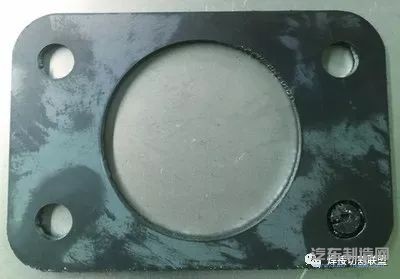
(a)前保险杠支架
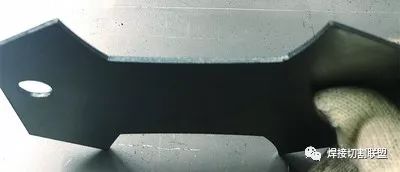
(b)绞盘支架补强板
图6 勇士零件切割
通过此激光切割试验,将四个工艺参数(除零件材质)及切割误差的试验结论数据汇总,如表5所示。
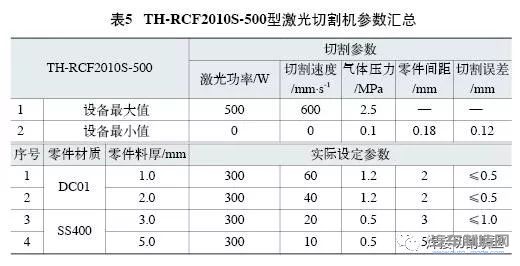
4. 总结
本文对不同厚度碳钢及实际零件在不同测试环境下切割,通过观察激光火花的形态及零件切割质量对各参数进行分析,结论如下:
(1)试验所述工艺参数及切割误差均会不同程度影响激光切割质量,不同切割环境下影响程度大不相同,为提高切割质量必须综合考虑各因素,控制各因素间的关系,以使切割质量达到最优。
(2)在调整切割参数时,气体压力对零件质量的敏感程度最大,切割速度次之,激光功率最小。
- 下一篇:巴斯夫在上海开设汽车涂料新工厂
- 上一篇:软铝料冲压要重点注意哪些?
编辑推荐
最新资讯
-
2025上海国际汽车成形制造产业对话会
2025-04-26 19:14
-
旭化成微电子开始批量生产用于环保发
2025-04-24 16:00
-
华为、地平线、大众、东风、起亚等引
2025-04-24 08:27
-
全球产业链聚沪 共探双碳新路径 SNEC
2025-04-18 18:05
-
柯马签订具有约束力的协议收购 Autom
2025-04-17 13:01