保守和安全的方法是采取两个步骤,首先在单独的阶段转换铝,稳定过程,然后移动到所有锆转化涂层。这是福特汽车公司在推出100%铝制F-150皮卡时采用的方法。
传统的磷酸锌工艺包括以下步骤:
1.清洁
2.水漂洗
3.表面调节
4.磷酸盐转化涂层
5.水漂洗
6.后处理 -(可选)
7.最终去离子或反渗透水冲洗。
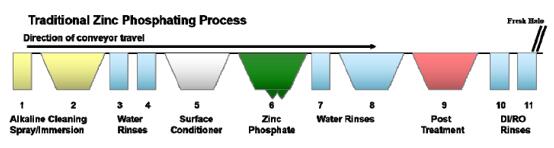
图1是传统的磷酸锌工艺如何在工厂中布局
只要预处理供应商设定的所有参数都能有效地维持系统
加工冷轧和镀锌钢以及少量铝的金属混合物。 结果是在所有基底上形成紧密均匀的微晶转化涂层。
扫描显微照片 - 传统磷酸锌(1000X)
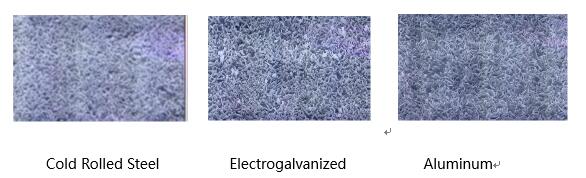
为了确保在铝上均匀涂覆,预处理公司向预处理浴中引入了游离氟化物源,以确保所有基材上的转化涂层的完整性。如果铝含量增加,则需要额外的游离氟化物,事实上传统工艺可以处理高达30%的铝,只要该工艺保持在控制状态并且有足够的游离氟化物来源。需要游离氟化物(F-)来吸收任何游离的铝金属离子,如果允许其在转化涂层浴中积聚,将关闭所有基材上的涂层机制。去除游离铝金属离子的机制也可在浴中产生污泥。铝金属离子与浴中的游离氟化物一起与钠和钾反应,以除去作为污泥的铝。以下等式显示了污泥如何形成和沉淀:

在等式1中,游离铝金属离子与游离氟化物结合形成氟化铝络合物。在方程式2和3中显示,该复合物然后与钠,钠和钾,钾结合形成冰晶石,方程式2和elpasolite,方程式3.两种化合物均沉淀,但冰晶石在浴中与铝离子达到平衡。为了将所有铝金属从工作浴中取出,还添加钾以形成沸石,其在操作pH下不溶,从而沉淀所有铝。
可以通过常规操作参数控制铝含量在30%以下,并保持特定量的游离氟化物。将游离氟化物值控制为附加参数。
一旦铝含量超过30%,保持浴化学性质并确保在所有基材上均匀的转化涂层变得极其困难。
设计的两步金属预处理工艺允许通过生产线处理更多的铝,而不会对操作参数进行任何重大改变。该方法的工作方式是将涂层的沉积分成两个阶段和两个不同的转化涂层。首先,改进传统的磷酸锌浴化学物质以蚀刻铝表面,但防止磷酸锌涂层沉积在表面上。将常规涂层施加到穿过浴槽的所有其他铁和锌表面。然后,主体通过第二转化涂层阶段,其中锆转化涂层沉积在铝表面上。该转化涂层阶段用作其他基材的后处理,因此涂层完整性不会丧失。流程序列如图2所示:
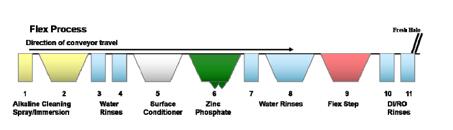
图2:
与传统系统相比,运行两步法具有多种优势,特别是随着铝含量的增加。一些优点是:
1.通过系统处理高达80%的铝
2.存放两个单独的转化涂层:
传统磷酸锌在冷轧钢电镀和热浸镀锌和镀锌。
铝上的锆转化膜
3.减少磷酸锌浴中游离氟化物的添加量
4.减少污泥形成减少对废物处理的影响
5.减少维护-减少过滤介质的更换和煮沸。
两步法在实验室中测试了福特的WSS M3P38 A高铝规格。
加工面板符合规范要求。 其中一项测试是循环腐蚀,结果如图3所示。
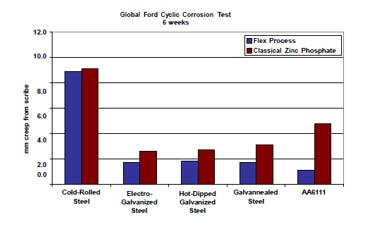
图3:Flex预处理工艺 - 循环腐蚀试验结果
随着铝含量的增加,2步工艺符合F-150生产的要求。该工艺提供了增加铝含量的灵活性,而没有传统工艺中出现的工艺问题。随着全铝F-150被引入生产线,这是福特汽车在迪尔伯恩装配厂从传统的磷酸锌工艺转变为两步金属预处理系统的第一步。这是一个可以接受的解决方案,因为全铝F-150的初始生产运行率在一年内不会达到100%水平,直到2015年全铝车型将推出并且迪尔伯恩的唯一车辆运行并且 堪萨斯城装配厂。IHS Automotive Insight在2015年发布的F-150预计产量为658,000辆,2016年为724,000辆。
在转换为两步法之后,完全生产之前的下一步是确定锆工艺是否也能够满足性能要求并能够在具有100%铝体拾取器的生产工厂中成功运行。验证锆工艺的第一步是详细的实验设计(DOE),以确定应建立哪些操作参数以确保性能。在建立操作参数之后,根据WSS M10P13-A指南设计并测试面板矩阵。
由于锆工艺中的阶段较少,因此也需要对现有工艺进行设备改造。如图4所示,与2步或传统的锌磷化系统相比,新的生产线布局仅具有清洁和转化涂层阶段。对于锆工艺,锆预处理后的所有阶段都转化为水冲洗,并且在排水之前将水从阶段11至阶段7级联回来,从而最大化水的再利用。
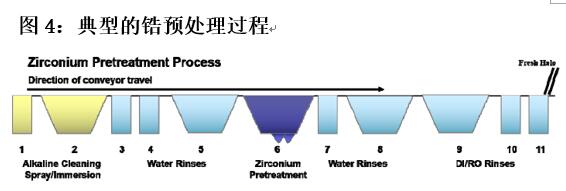
图4:典型的锆预处理过程
与传统和/或两步系统相比,锆预处理工艺的最大优势在于新工艺的可持续性。与其他系统相比,能源,水和废物处理成本显着降低。
在转换之前,根据工厂信息整理了一个商业案例,以确定投入所有这些时间和精力是否是一个良好的决策,在财务和环境方面?使用表1和表2中的基本信息,开发了下面图5所示的图表。从下图可以看出,通过从两步系统转换为锆工艺,生产工厂估计每年可将处理成本降低近342,000美元或23.4%。